Avanço da manufatura aditiva para explorar a anisotropia
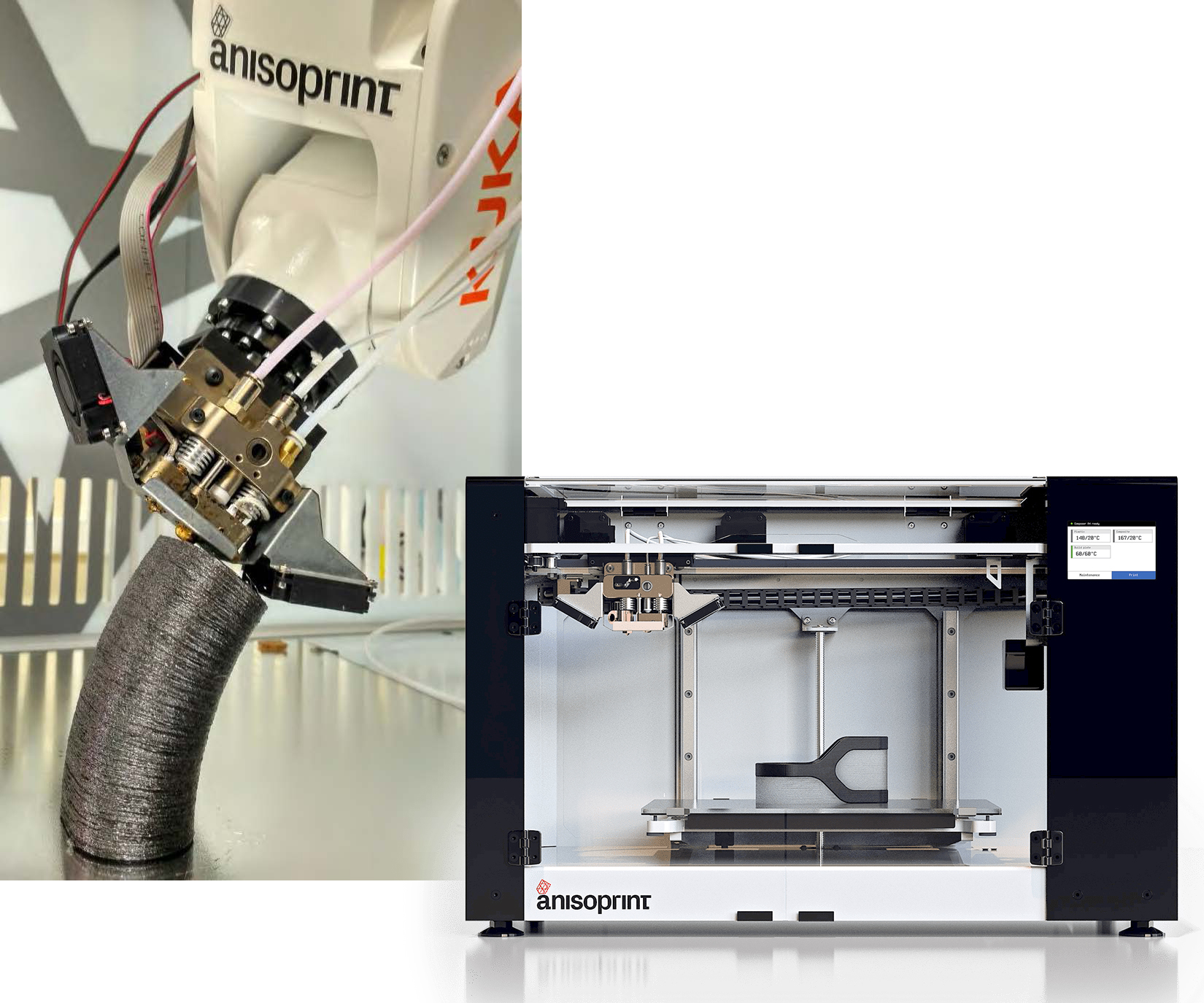
Fundada em 2014 pelo CEO Fedor Antonov, a Anisoprint (Esch-sur-Alzette, Luxemburgo) é uma entre um número crescente de empresas de tecnologia que estão promovendo a impressão 3D de compósitos com fibra contínua . Ela prefere, no entanto, ser conhecida como a pioneira em afastar a manufatura aditiva (AM) dos metais para compósitos.
“As propriedades direcionais dos compósitos são uma vantagem, não uma desvantagem”, diz Antonov. “Os compostos de fibra de carbono unidirecional são mais fortes e leves do que os metais. A manufatura convencional e a AM baseada em metais consideram a anisotropia direcional dos compósitos como uma desvantagem que precisa ser mitigada. Mas a abordagem da Anisoprint explora essa anisotropia, orientando e posicionando as fibras para atender com precisão às cargas estruturais, reduzindo significativamente o peso da peça, mantendo alta resistência e rigidez. ”
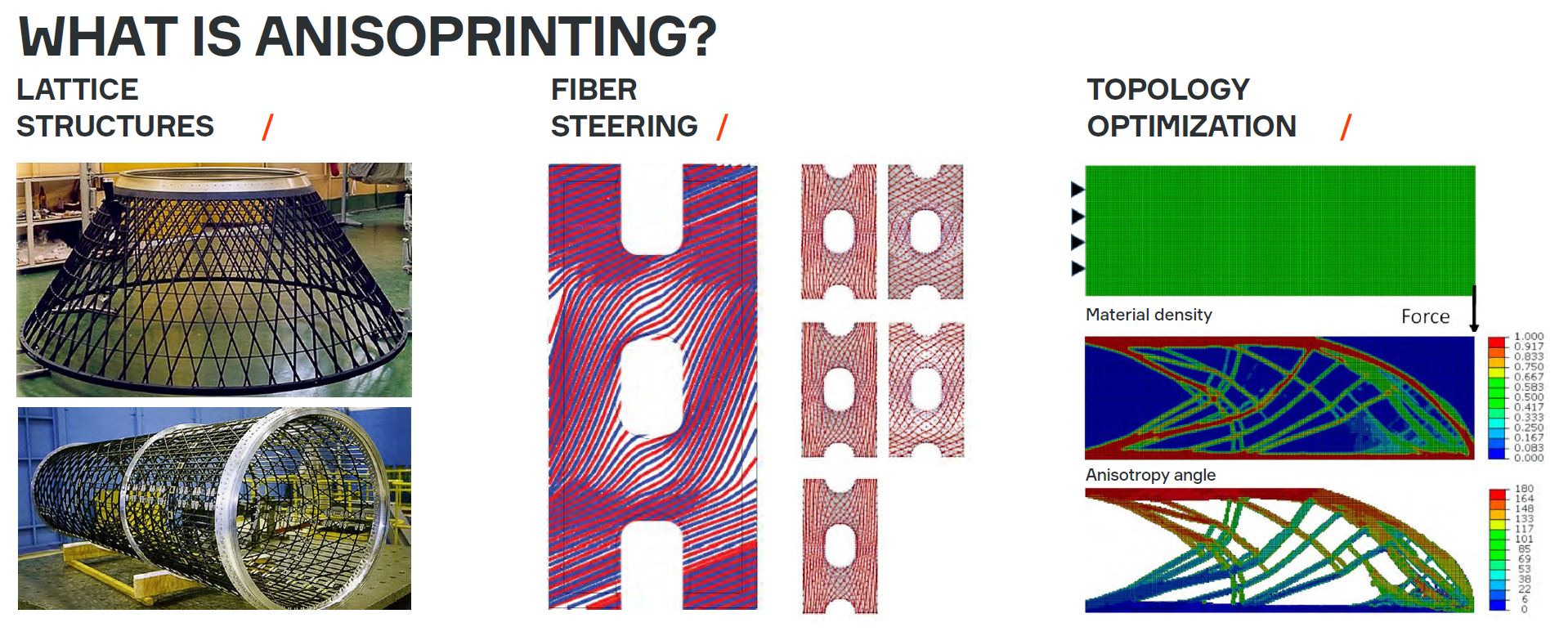
Ativando composições mais eficientes
Antonov aponta que a fabricação de compósitos convencionais normalmente usa práticas da indústria de metais, incluindo laminados quase isotrópicos, furos de perfuração e fixadores mecânicos. “Estes anulam as vantagens de peso e desempenho de compósitos ”, diz Antonov. “A tecnologia de anisimpressão fornece um método automatizado de produção muito mais rápido e flexível.” Também oferece uma maneira de obter estruturas mais eficientes agora produzidas por otimização de topologia e design gerador Programas.
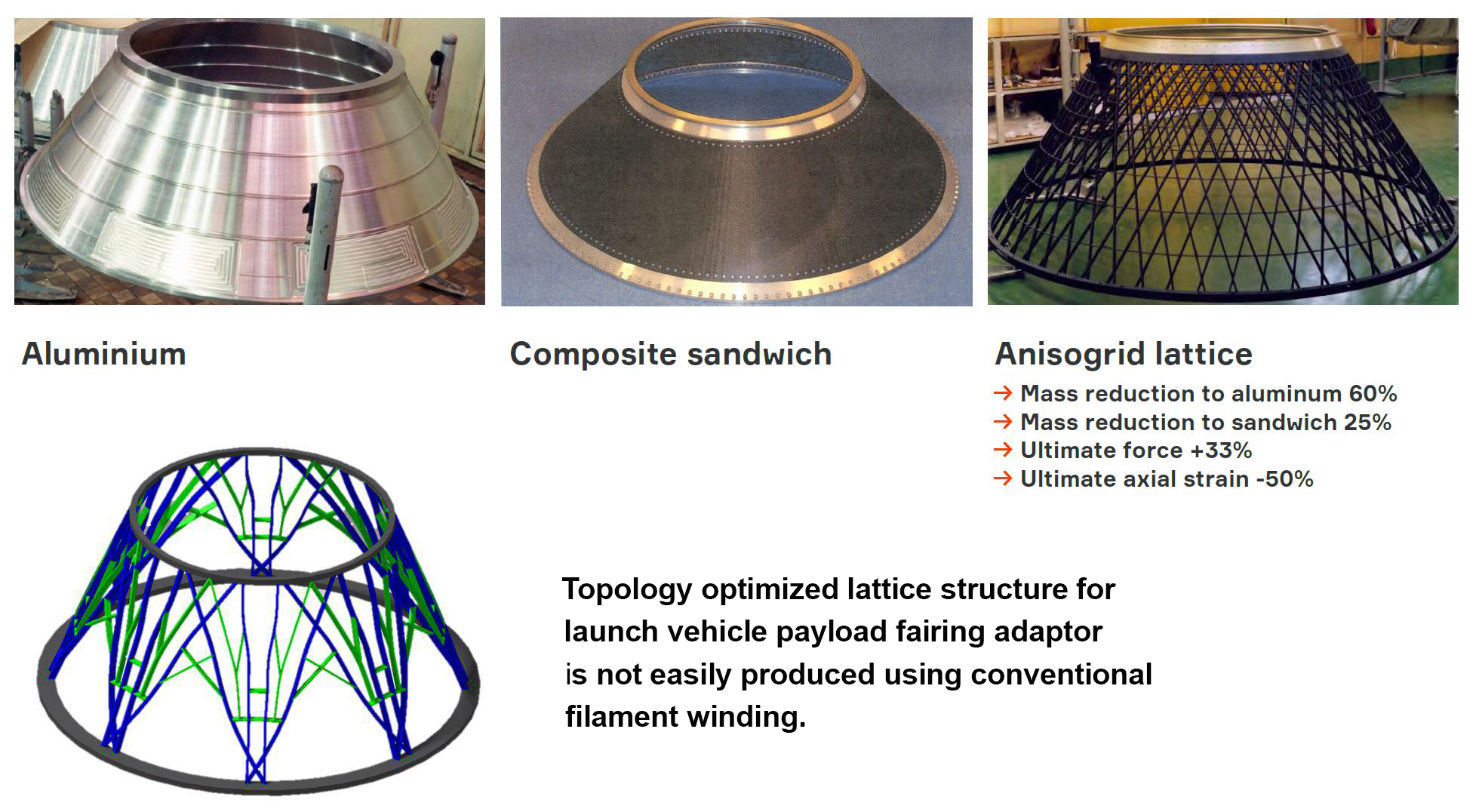
“As estruturas mais eficientes da natureza, como árvores e ossos, exploram as propriedades direcionais, orientando o material de transporte de carga principalmente ao longo dos caminhos de carga”, afirma Antonov. No entanto, esses tipos de estruturas otimizadas de topologia são difíceis de produzir. Por exemplo, estruturas treliçadas que permitiram adaptadores de carenagem de carga útil fortes e leves para espaçonaves são normalmente produzidas usando enrolamento de filamento. No entanto, uma versão com topologia otimizada , oferecendo uma economia de peso adicional de 30% , não é mais fácil de produzir com processos de compósitos convencionais, nem com a colocação automatizada de fibra (AFP) mais recente.
“Estruturas de filamento anisogrid convencionais são obtidas usando ranhuras na ferramenta, e uma fração de volume de fibra relativamente baixa nas costelas permite cruzá-las”, diz Antonov. “Esses tipos de estruturas anisogrid eram nosso objetivo original. Mas isso não funciona usando AFP porque seu conteúdo de volume de fibra é sempre constante e costelas de interseção sem cortar as fibras ou variações locais de espessura não é possível. ”
(Observação:para obter mais estudos sobre isso, consulte https://www.researchgate.net/publication/321081593_Anisogrid_Payload_Adaptor_Structure_for_Vega_Launcher)
Direcionamento de fibra
O direcionamento de fibra é uma técnica aplicada atualmente à produção de compostos usando AFP, que permite que as fibras sejam aplicadas em caminhos curvilíneos - o AFP tradicionalmente usa caminhos lineares retos. O direcionamento da fibra permite que o caminho da fibra e, portanto, a resposta mecânica do painel composto, seja otimizado para exibir um desempenho superior do que com os laminados convencionais. Em um exemplo, esta abordagem produz um painel de substrato composto para uma matriz solar de nave espacial que tem uma primeira frequência natural 44% maior (minimiza a amplitude das vibrações e permite um amortecimento mais rápido) do que um painel convencional equivalente com caminhos de fibra retos e a mesma massa. Alternativamente, um painel de peso mais baixo pode ser obtido para o mesmo desempenho de frequência.
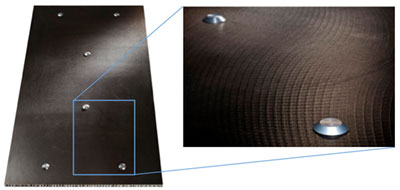
A direção de fibra permite o projeto e a fabricação de peças como painéis estruturais para satélites ou componentes de máquinas de alta velocidade com um desempenho muito alto. É um processo repetível, alcançando uma qualidade elevada e consistente e permite novos designs inovadores. Também pode ser usado para reduzir o peso para o mesmo desenho geométrico. FONTE | “Tecnologia de direção de fibra para painéis compostos avançados” (link original é fornecido aqui, mas não está mais disponível através do servidor esa-tec:http://www.esa-tec.eu/space-technologies/from-space/fibre-steering -tecnologia-para-painéis-compósitos avançados /)
“Anisoprinting é uma combinação de estruturas treliçadas e direcionamento de fibra que é usado para obter peças otimizadas de topologia”, diz Antonov. “Esta é uma tecnologia chave para compósitos impressos. Por exemplo, como você constrói um painel da fuselagem para uma aeronave comercial com recortes ou orifícios?
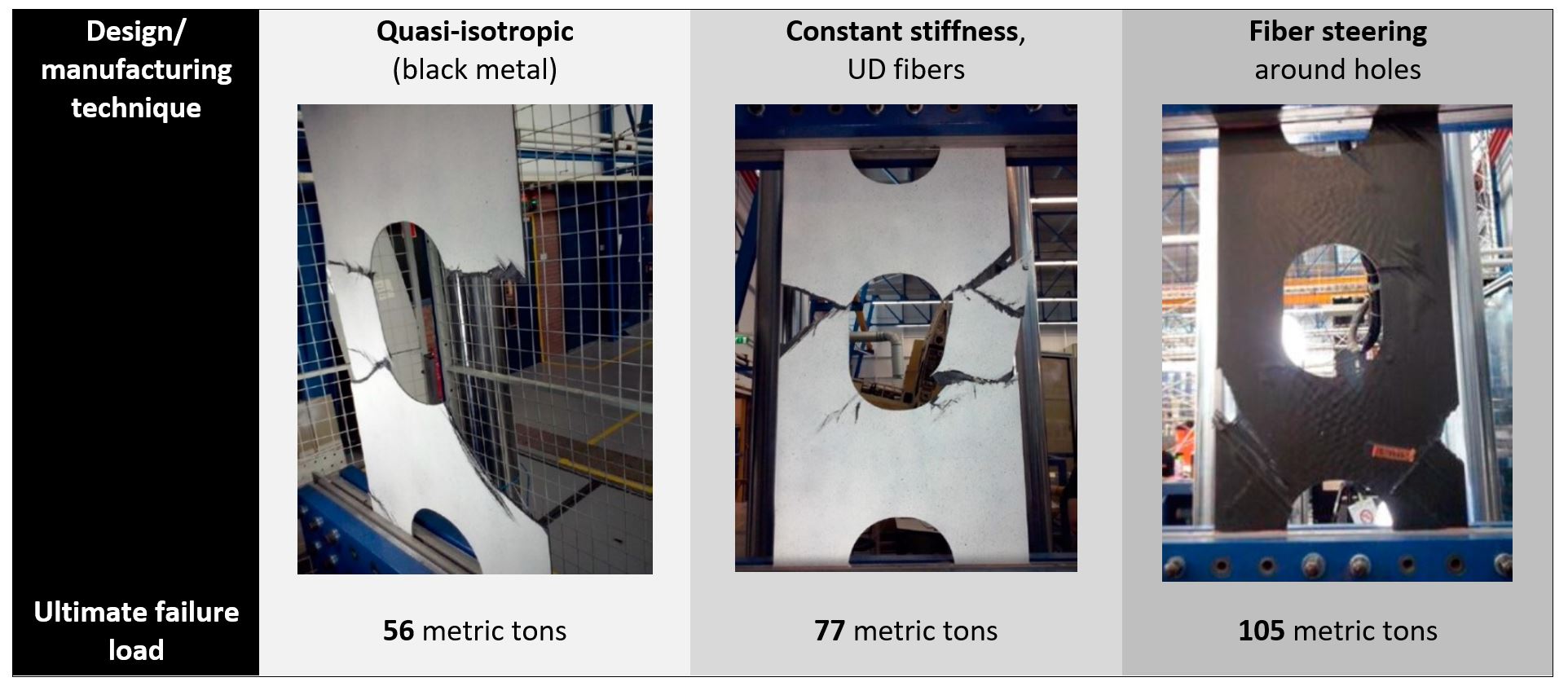
Ele dá três técnicas diferentes, que são usadas para produzir amostras compostas da mesma espessura e peso, cada uma com furos usinados CNC (ver tabela abaixo). Ele observa que, no teste de compressão, a amostra feita com fibra de direcionamento tem uma carga de compressão final duas vezes maior que a de um composto quase isotrópico (“alumínio preto”) e 30% maior em comparação com um laminado UD de rigidez constante. “Portanto, o direcionamento por fibra é uma ferramenta poderosa”, diz Antonov. “A anisimpressão se moverá em direção ao direcionamento de fibra AFP conforme aumentamos o volume e a produtividade da fibra, e o AFP se moverá em nossa direção com mais flexibilidade.
A “flexibilidade” a que Anotov se refere é uma medida de quanto é possível colocar uma fibra ao longo de qualquer caminho no espaço tridimensional. A Arevo, outra empresa que comercializa impressão 3D em fibra contínua, afirma ter esse tipo de flexibilidade. “A tecnologia da Arevo não é muito diferente em comparação com empresas AFP como Coriolis, Automated Dynamics, Electroimpact, etc.,” diz Antonov. “Eles simplesmente o miniaturizaram e em vez de usar uma fita fina e larga, eles usam uma grossa e estreita com um cabeçote AFP a laser. É tudo a mesma coisa." Observe que a tecnologia de impressão 3D da Arevo foi baseada em robôs desde o início. Como a tecnologia da Anisoprint mudará conforme ela se move para plataformas robóticas?
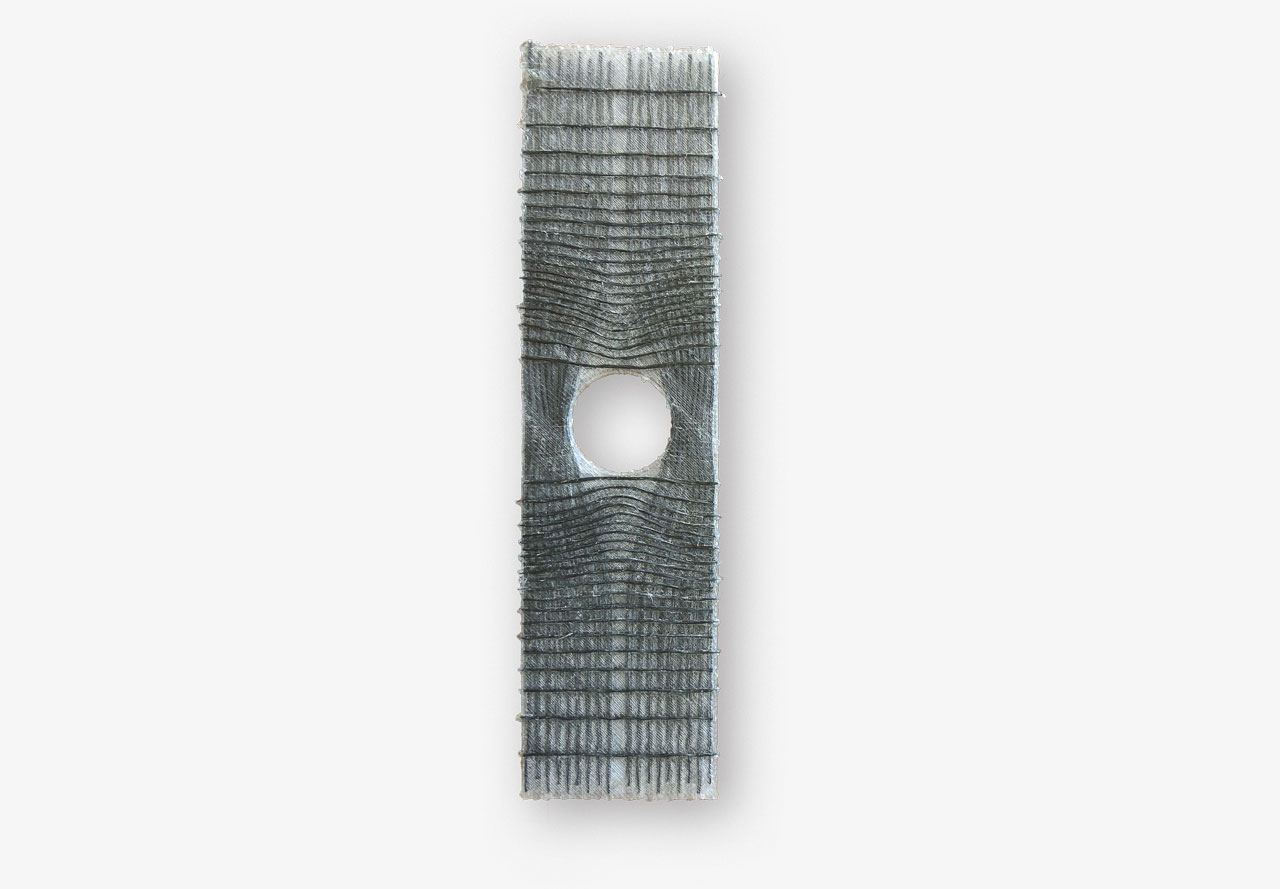
Exemplo de uma amostra composta impressa em 3D Anisoprint usando direcionamento de fibra.
História da Anisoprint e abordagem TS-TP
Antonov e seus cofundadores (Andrey Azarov, Alexey Khaziev, Mikhail Golubev e Zafer Gürdal) estavam em uma nova universidade na parte oeste de Moscou chamada Instituto Skolkovo de Ciência e Tecnologia (Skoltech), que foi estabelecido em 2011. Em 2014, Antonov estava trabalhando para construir o novo centro de tecnologia de compósitos da Skoltech e começou a desenvolver a impressão 3D. O diretor do centro de compósitos na época era Zafer Gürdal, que saiu em 2015, voltando para o McNair Center da University of South Carolina. Este último agora é conhecido por sua P&D em compósitos e impressão 3D de fibra contínua.
“Decidimos nos separar da Skoltech quando Zafer Gürdal saiu”, explica Antonov. “Desenvolvemos um protótipo de cabeça de impressão CFC no verão de 2015. Nosso próximo objetivo era desenvolver uma impressora de mesa.”
A Anisoprint lançou sua impressora de mesa Composer em 2017. Semelhante às impressoras de fibra contínua Markforged, o Composer da Anisoprint usa dois bicos de impressão:um para o reforço de fibra contínua e outro para a matriz de plástico. Alojado dentro de uma câmara de impressão de vidro, o leito de impressão de vidro do Composer pode ser aquecido até 120 ° C, o que permite minimizar os efeitos do encolhimento. Atualmente está disponível em dois tamanhos:
- A3 (420 por 297 por 210 milímetros)
- A4 (297 por 210 por 147 milímetros)
Com um diâmetro de bico padrão de 0,4 milímetros, a velocidade de impressão do Composer é citada como 10-80 milímetros / segundo sem reforço e 1-20 milímetros / segundo com reforço de fibra contínuo. Anisoprint pode extrudir muitos plásticos, incluindo PLA, PETG, ABS, nylon e PC. Ela pode reforçá-los com seus materiais de fibra de carbono composta (CCF) e recentemente lançou um material de impressão de fibra de basalto composto (CBF).
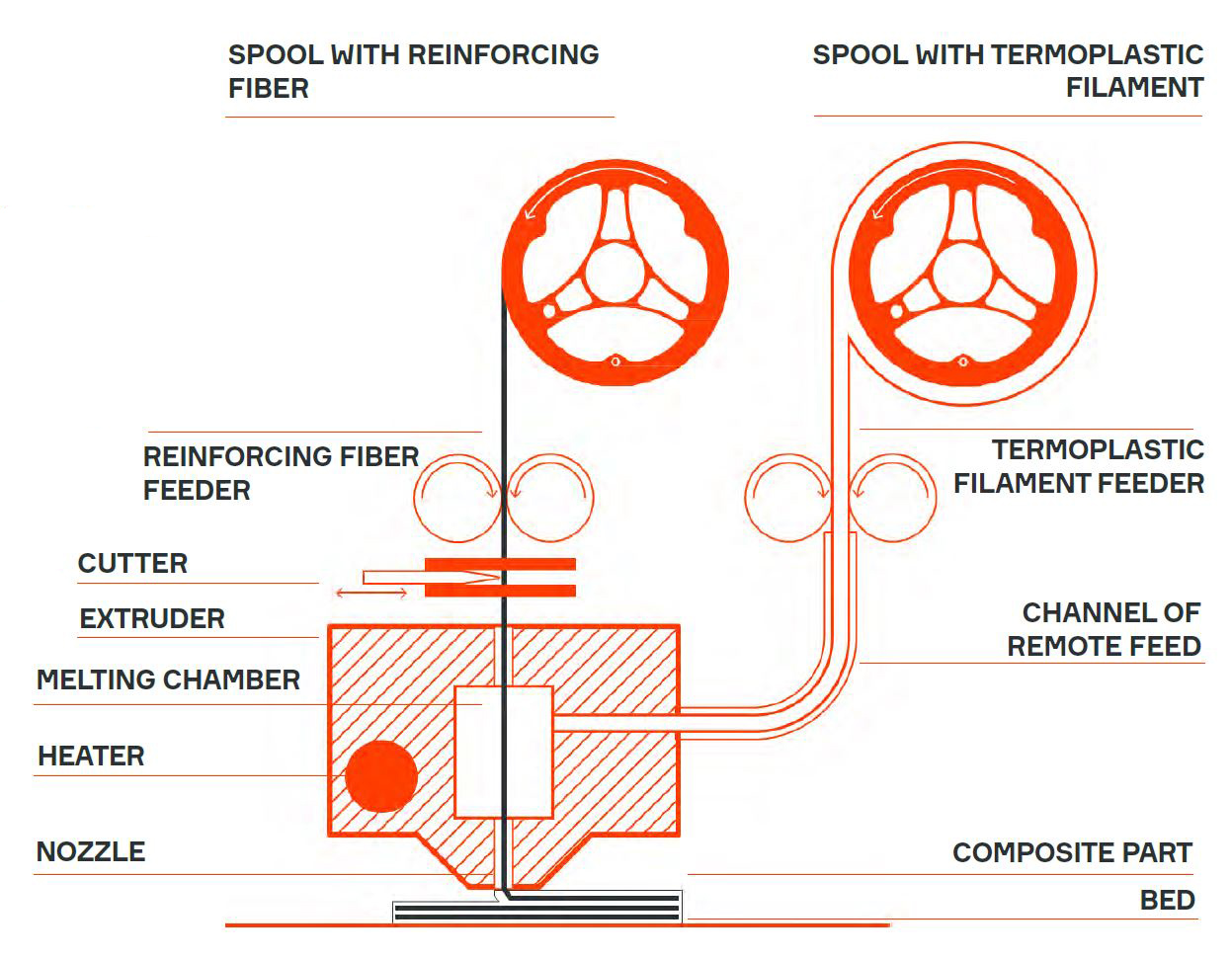
No entanto, o Anisoprint é bastante diferente de outras tecnologias de impressão 3D de fibra contínua porque primeiro impregna o reforço de fibra contínua com um termofixo polímero e, em seguida, expulsa este no filamento termoplástico derretido durante a impressão. “Esta abordagem de duas matrizes garante baixa porosidade, boa adesão da fibra ao polímero e excelentes propriedades mecânicas,” Antonov afirma.
Ele continua, “O inventor da anisogrelha enrolada com filamento para o adaptador de carga útil do iniciador Proton M, V.V. Vasiliev, que está em nosso conselho consultivo, mostrou que essa ideia de usar termoplástico termofixo de matriz dupla Os materiais (TS-TP) têm benefícios em relação ao uso de uma única matriz termofixa ou termoplástica. Os materiais de matriz termofixa têm problemas de fragilidade, de modo que a matriz começa a rachar muito mais cedo do que a fibra falha. Vasiliev provou que poderia mitigar isso com a abordagem de matriz dupla. ”
O termoendurecível que o Anisoprint usa é um epóxi multicomponente e os laminados impressos finais têm um conteúdo de fibra de até 45%, conforme testado pela Universidade Técnica de Munique (TUM).
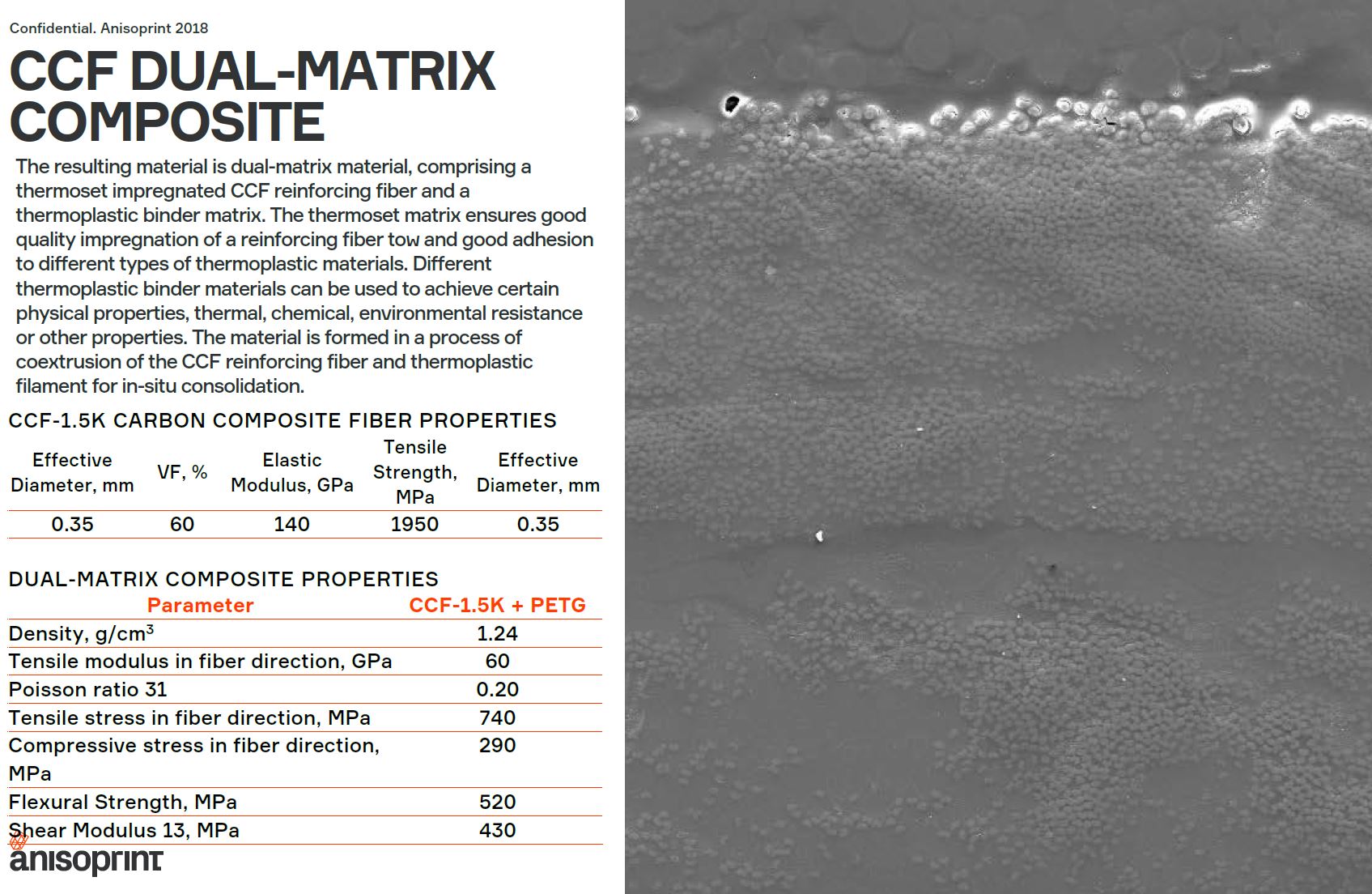
As ofertas patenteadas da Anisoprint incluem:
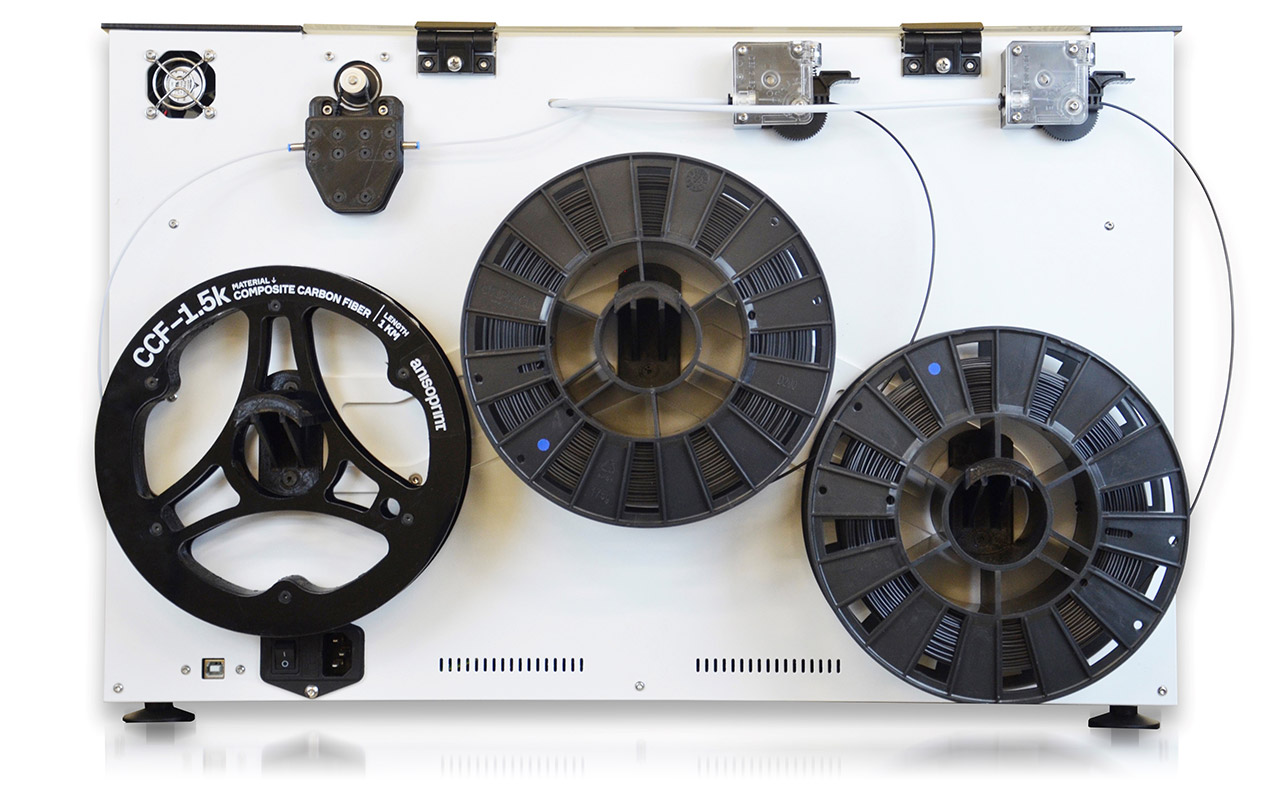
Tecnologia de coextrusão de fibra composta (CFC) para fabricação aditiva usando diferentes polímeros termoplásticos reforçados com fibras contínuas (por exemplo, carbono, basalto) que são consolidados e curados em um processo automatizado de estágio único que não requer ferramentas nem pós-processamento.
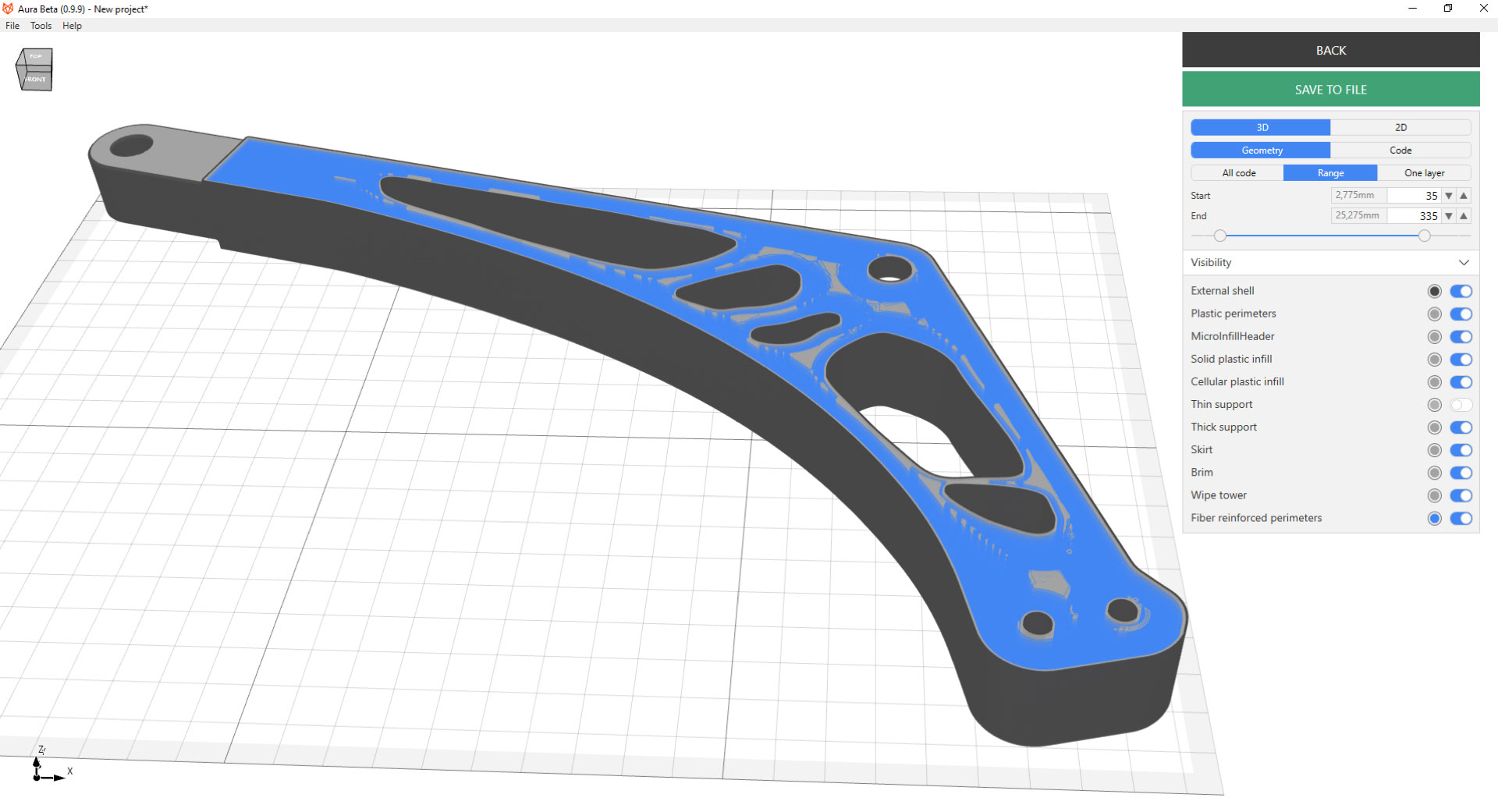
O software Aura Slicer que prepara modelos 3D para peças de fabricação usando a impressora Composer CFC, bem como impressoras FFF convencionais.
Impressora 3D de mesa Composer disponível em três tamanhos (A4, A3, A2).
PROM família de sistemas de impressão industrial com opções de robô e pórtico, disponíveis comercialmente a partir de 2020.
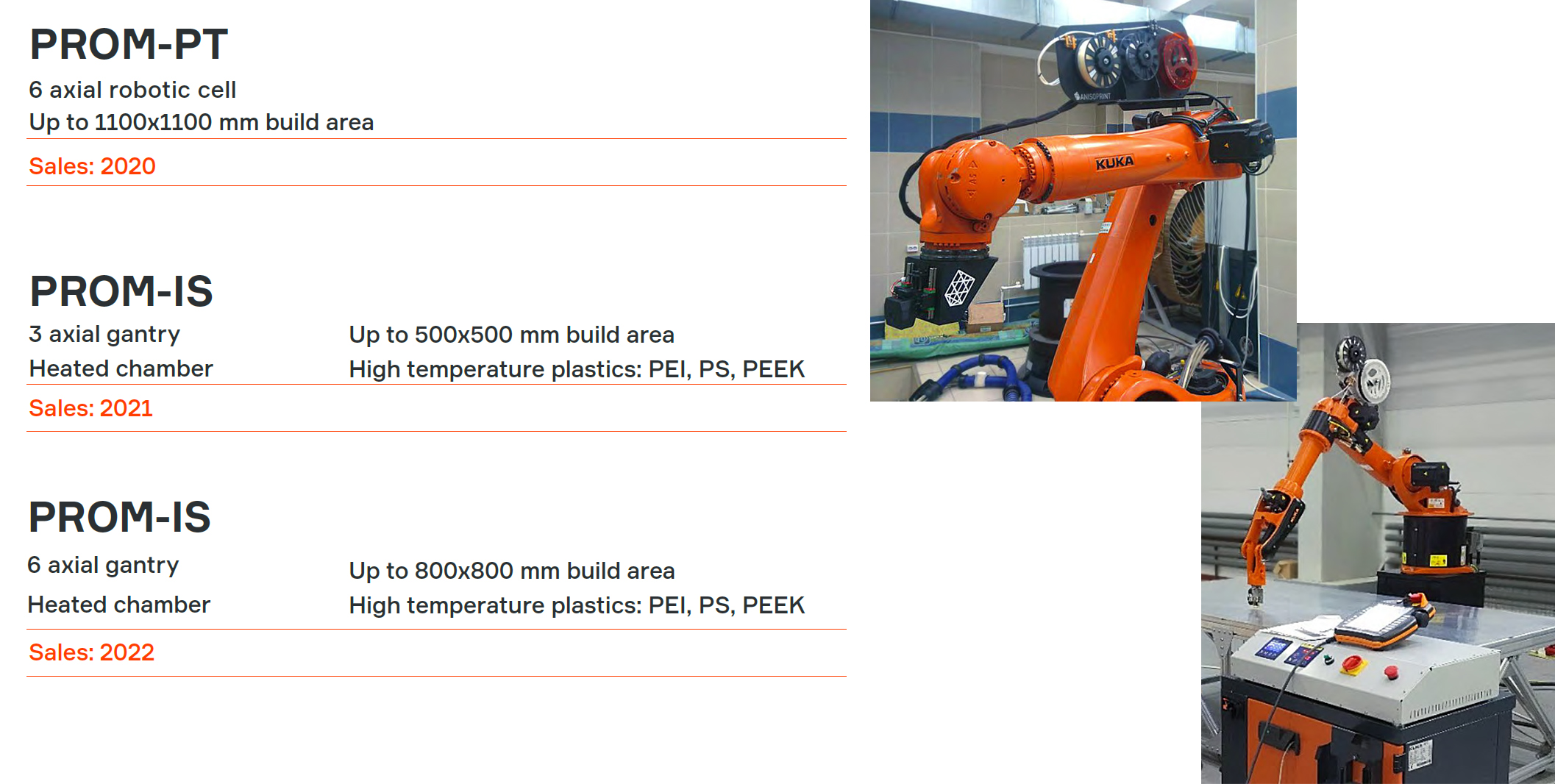
Desenvolvimento de robôs vs. desktop
“O robô tem um cabeçote de impressão diferente porque você precisa mover o cabeçote para caber e alcançar espaços restritos durante a impressão”, explica Antonov. “Em um plano 2D, isso não é um problema. Mas no espaço 3D, você precisa colocar fibra onde já existe alguma estrutura. A acessibilidade ideal é conseguida com agulha. Portanto, precisamos de um meio-termo, um cabeçote de impressão mais parecido com uma agulha. ”
Ele observa outras diferenças, como controles industriais. “As impressoras de mesa são baseadas em eletrônicos de consumo, como o Arduino. Mas para sistemas robóticos maiores, você precisa de controle de movimento industrial e interfaces e todos os tipos de garantia de qualidade in-situ, como medição a laser, que a Markforged tem em sua máquina maior. Você também precisa modificar os sensores e controles de aquecimento / resfriamento. ” Ele acrescenta que tudo isso leva tempo e recursos, e sua prioridade nos últimos dois anos foi desenvolver a máquina desktop, mas agora eles estão trabalhando nos sistemas robóticos também. ”
Software:Aura
Antonov descreve o software da Anisoprint como flexível, permitindo tanto usuários iniciantes quanto avançados. “O software é fácil de usar, mas é importante que os laboratórios de P&D tenham a capacidade de alterar os parâmetros de impressão”, explica ele. De fato, os clientes incluem o instituto de pesquisa MFPA (Weimar, Alemanha), Brightlands Materials Center (Geleen, Holanda) e a Universidade Técnica de Munique, bem como fabricantes como Schunk Carbon Technology, Airbus e BMW.
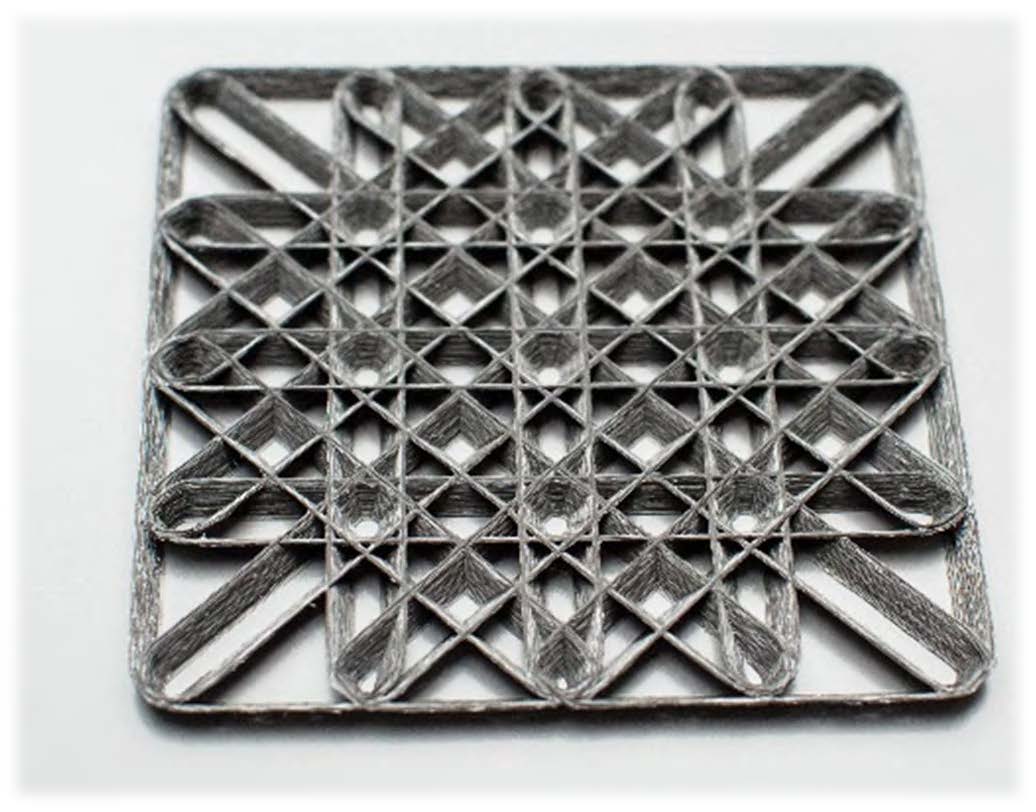
O Anisoprint possui peças de microssatélites compostas impressas em 3D com até 45% de redução de peso em comparação com metais leves.
Parcerias para soluções contínuas
A Anisoprint, que se autodenomina uma plataforma de materiais abertos, também está procurando desenvolver mais parcerias para novos materiais de impressão e peças. Em junho, ela anunciou um acordo com a Thought3D, sediada em Malta, para usar os adesivos Magigoo desta última. Eles grudam a primeira camada de impressão na base de impressão, evitando que a parte se solte. “A má adesão da primeira camada é um dos problemas mais comuns que podem arruinar as peças impressas, e não necessariamente no início da construção”, explica Antonov. “Isso é especialmente importante para nosso sistema de materiais abertos, onde o cliente pode escolher entre diferentes tipos de termoplásticos. Cada um requer parâmetros de impressão diferentes e é por isso que introduzimos várias configurações de primeira camada em nosso software de segmentação Aura. É também por isso que incluiremos varas Magigoo em cada caixa do Composer para garantir que nossos clientes tenham uma solução adequada em mãos para uma boa adesão da primeira camada. ”
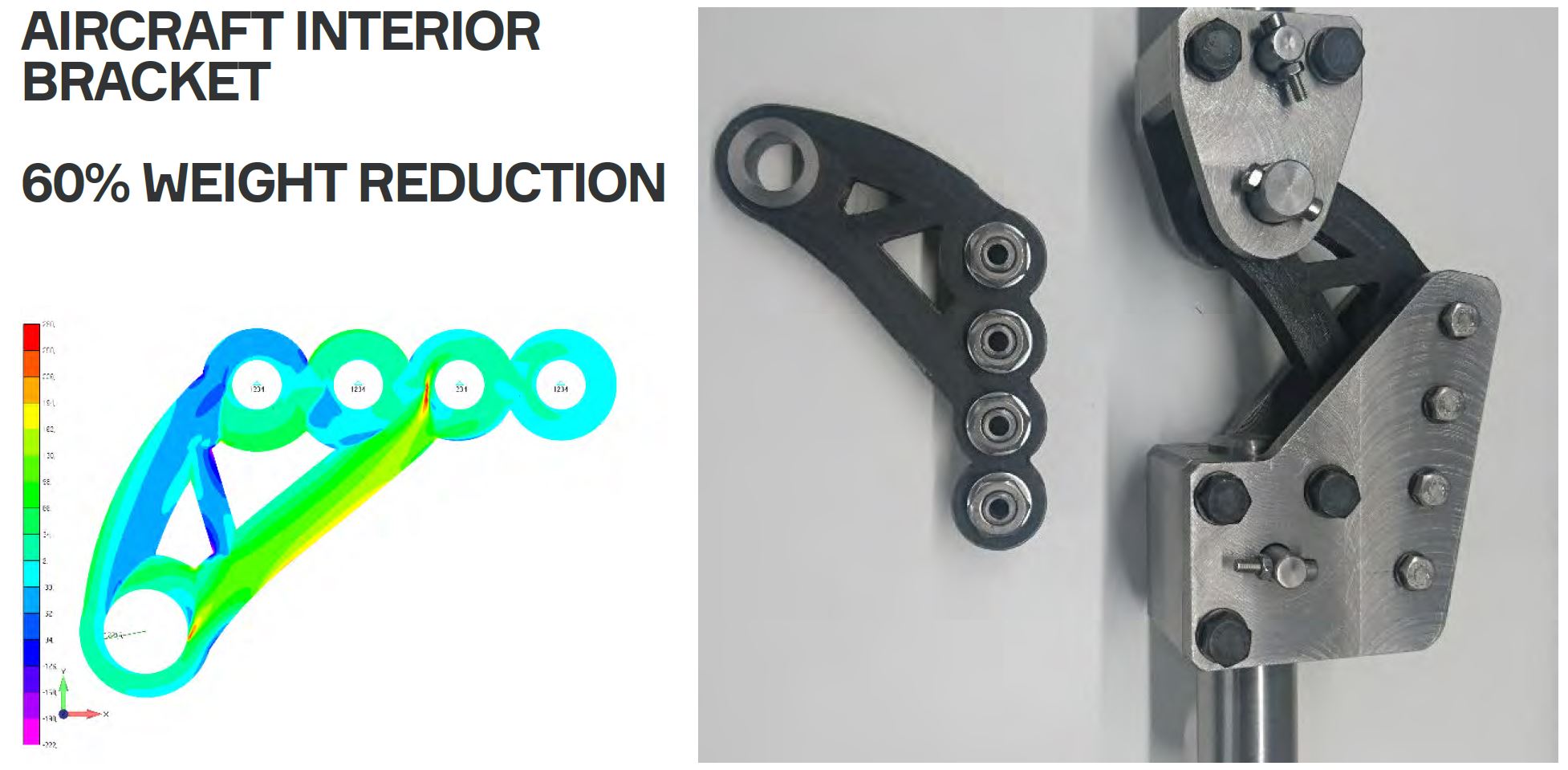
Aplicativos de anisimpressão
A Anisoprint afirma que sua tecnologia pode ser aplicada em muitos campos, desde a indústria aeroespacial até produtos de consumo e saúde. Um exemplo é um suporte de assento de aeronave que suporta 1,5 toneladas de carga com redução de peso de 40% em comparação com o alumínio. Com 100 desses acessórios em um avião de passageiros médio de corredor único, essa redução de peso pode representar uma economia significativa de combustível e custos operacionais gerais.
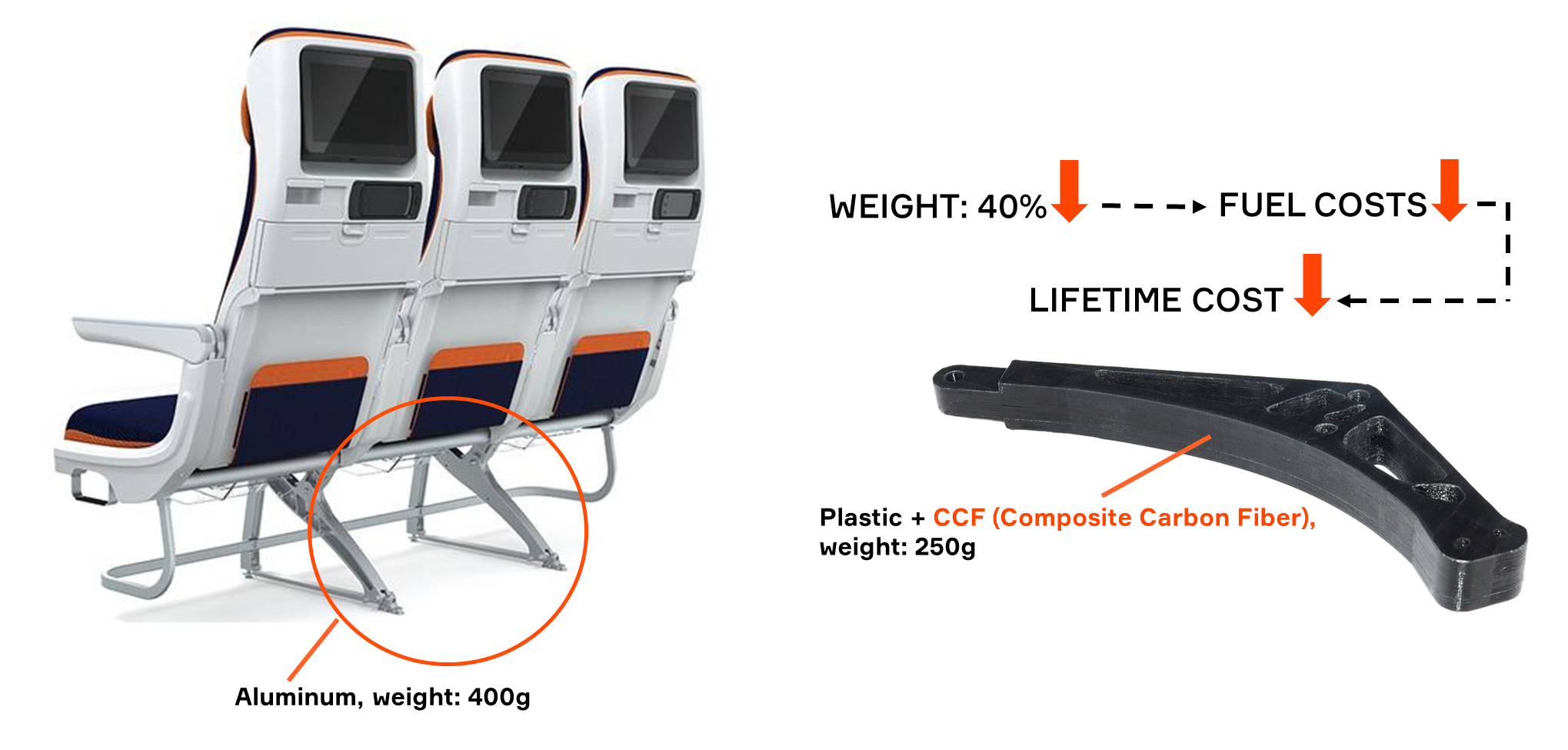
O suporte de assento de aeronave composto de impressão 3D Anisoprint atinge 40% de economia de peso em relação ao alumínio.
Outro caso é um pistão para formar potes de iogurte, utilizado em uma linha de produção de laticínios. Esses pistões são normalmente feitos de poliamida fresada, mas a substituição dessas peças quando danificadas leva três meses, com a linha de produção paralisada por enquanto. A peça impressa por um Anisoprint Composer supostamente tem uma vida útil mais longa e reduz o tempo de inatividade da linha de produção de 3 meses para 24 horas.
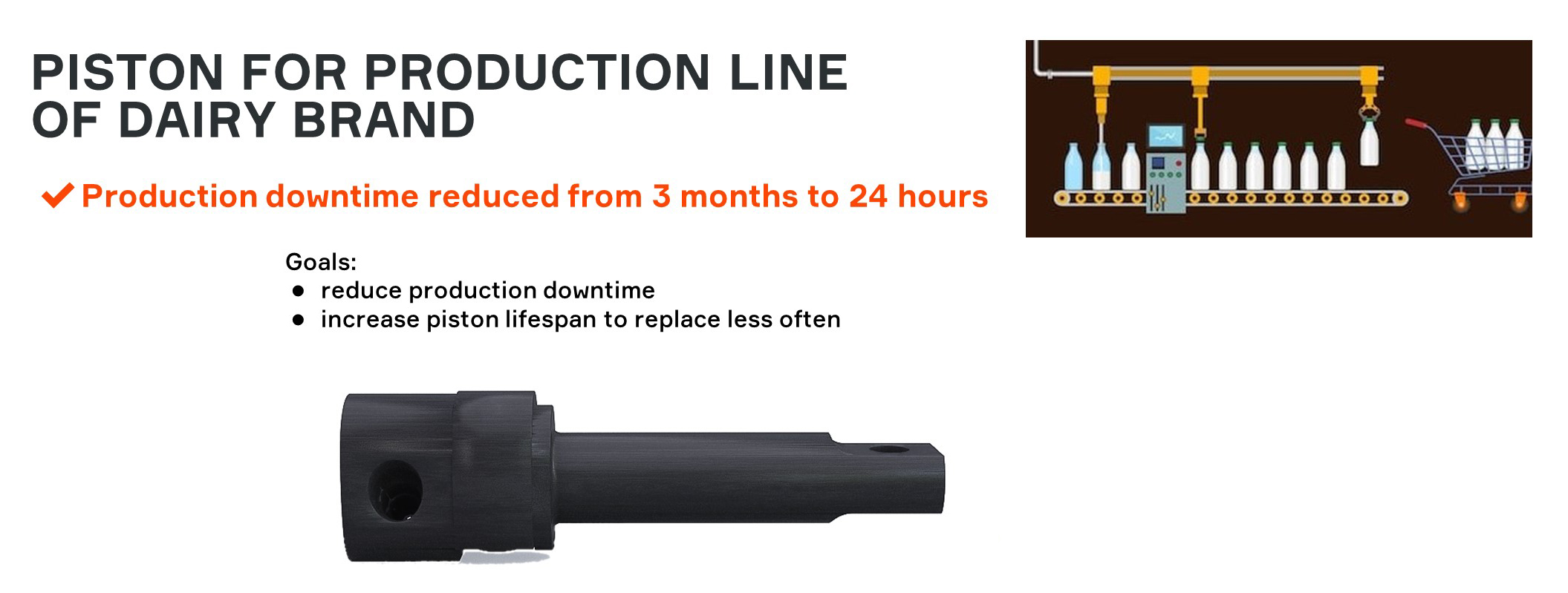
O Anisoprint atendeu aos requisitos de um componente de linha de produção de laticínios com seu pistão composto impresso em 3D, mas com um tempo de substituição drasticamente reduzido.
“A anisimpressão permite o projeto e a produção de estruturas compostas ideais por meio da coextrusão de fibras compostas”, diz Antonov. “Os polímeros termoplásticos são reforçados com fibras contínuas, consolidados e curados em um processo de estágio único, totalmente automatizado, sem necessidade de pós-processamento. Como resultado, obtemos peças que são várias vezes mais fortes, mais leves e mais baratas do que os metais e plásticos tradicionais e superiores também aos compostos convencionais. ”
Resina
- 5 Processos de Fabricação de Aditivos Comuns
- Manufatura Aditiva vs Manufatura Subtrativa
- Vantagens da fabricação de aditivos
- Uma pesquisa sobre fluxos de trabalho de manufatura aditiva
- Os 10 principais avanços na tecnologia de fabricação de compósitos
- Fabricação de compostos:A fabricação de materiais compostos
- Fabricação de aditivos com compostos na indústria aeroespacial e defesa
- Henkel oferece plataforma de materiais para fabricação de aditivos
- Manufatura Aditiva em Eletrônicos
- Manufatura Aditiva na Aeroespacial