Hitachi Powdered Metals adota a automação robótica, aumenta o volume em 400% no mercado de trabalho apertado
Metalurgia em pó (PM), ou sinterização, é o processo de compactação de misturas personalizadas de pós elementares ou de ligas em matrizes pré-fabricadas para fazer peças de máquinas de complexidade variável com eficiência. Uma vez compactadas, as formas são aquecidas em um forno de atmosfera controlada para unir as partículas e endurecer as peças.
Também conhecido como compactação verde, o processo produz componentes quase líquidos que normalmente usam mais de 97% da matéria-prima inicial na peça acabada. As misturas de ligas de pó personalizadas fornecem a capacidade de produzir peças complexas e até intrincadas que atendem às especificações de resistência e tolerância exigidas para aplicações altamente exigentes.
A fábrica da Hitachi Powdered Metal (EUA) Inc. em Greensburg, Indiana, é uma das nove instalações da Hitachi em todo o mundo. É especializada na produção de componentes de trem de válvulas e transmissão para fornecedores automotivos de nível nos EUA, com uma presença crescente entre os fabricantes de motocicletas e equipamentos paisagísticos.
Motivação inicial
A Hitachi Powdered Metals (HPM) iniciou um investimento gradual em robôs industriais na fábrica de Greensburg em 2005, impulsionado pelo surgimento de um mercado de trabalho apertado e pela oportunidade de produzir um produto extremamente frágil.
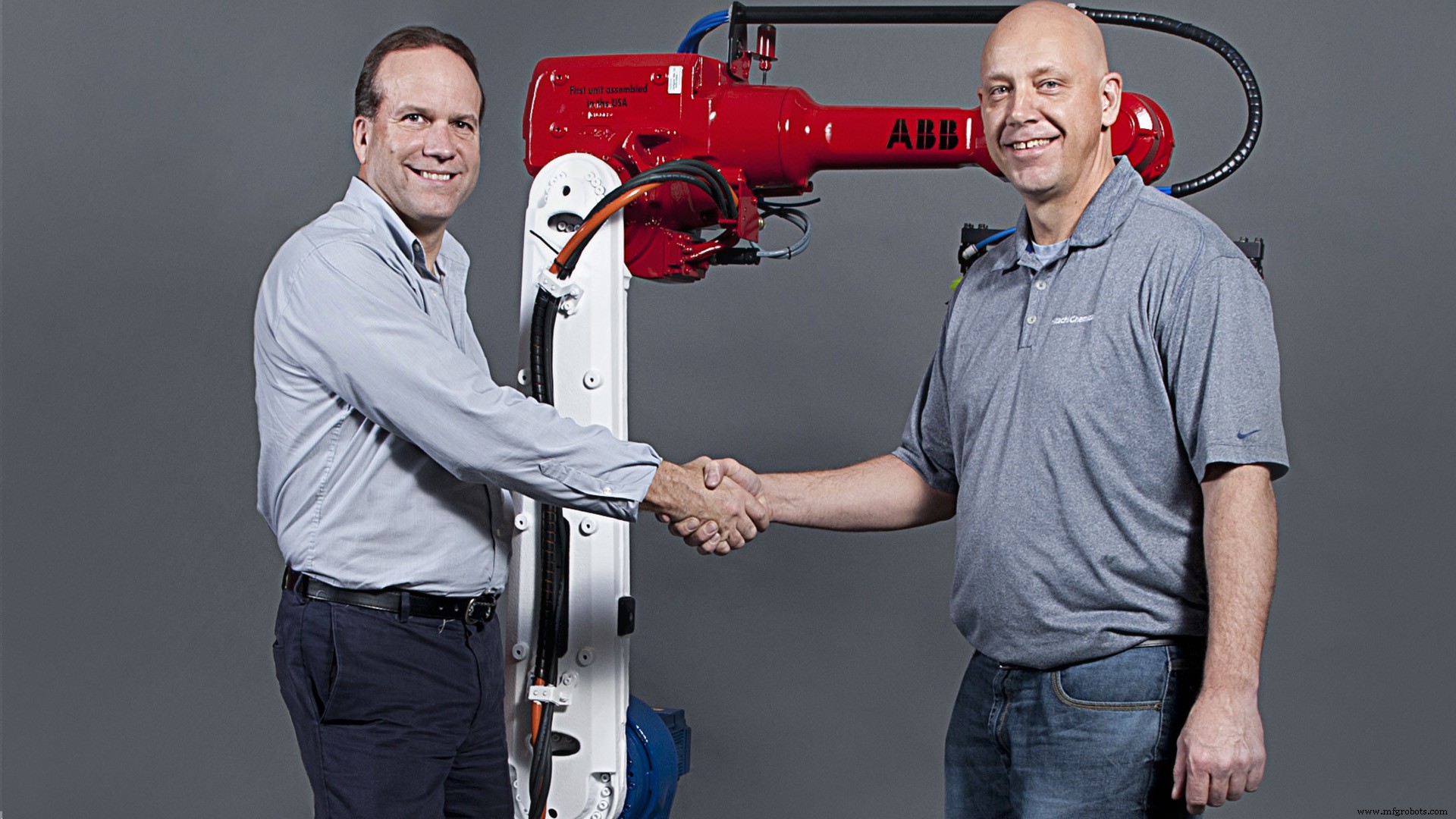
“Começamos com robôs porque tínhamos uma peça para fazer para um cliente que tinha dentes pequenos e frágeis que não podiam ser manuseados manualmente e, naquela época, todas as nossas prensas compactadoras eram cuidadas manualmente”, disse Gregory Owens, presidente da a planta HPM Greensburg. “Reduzir os custos de mão de obra também foi um fator, mas logo após a primeira instalação, um grande OEM automotivo abriu uma fábrica na cidade e nosso problema de custo de mão de obra passou para um problema de disponibilidade de mão de obra, pois ficou extremamente difícil contratar e reter funcionários.”
Em um esforço para manter os custos baixos e minimizar qualquer exposição durante o período de teste inicial, a HPM comprou um robô ABB S3 usado, vintage de 1993 da CIM Systems Inc. nas proximidades de Noblesville, Ind. James Adams, que havia se juntado à HPM vários anos antes como um engenheiro de desenvolvimento de fabricação, estava familiarizado com o CIM, o ABB Robotics Value Provider (ou seja, integrador de sistemas) mais antigo nos EUA, devido ao seu trabalho com robôs em seu empregador anterior.
“A CIM tinha um robô usado que nos permitiria facilitar nosso caminho para a automação robótica, limitando nossa exposição inicial caso não funcionasse como pretendido”, disse Adams. “Eles também nos forneceram um suporte muito necessário com a programação e integração do sistema na operação existente.”
Redução de sucata, melhor alocação de mão de obra
Quando as peças de metal em pó saem da prensa, antes de serem endurecidas no forno, elas podem desmoronar facilmente com o mais leve toque. Com o robô recém-instalado, com uma garra magnética elétrica para manusear a peça, a taxa de sucata do novo produto passou de 11% enquanto manualmente tendia para 0,5%.
“Quando as peças estavam sendo retiradas manualmente da prensa, houve danos consideráveis de manuseio. A peça pode estar imperceptivelmente deformada, mas você não saberia até que ela saísse do forno cinco horas depois. Devidamente programados e equipados, os robôs são muito mais gentis no manuseio das peças”, disse Adams.
O novo sistema permitiu à HPM mover vários manipuladores de máquinas manuais para posições menos mundanas na planta, reduzindo o estresse de uma tarefa repetitiva e realocando a mão de obra de maneira mais eficiente.
A produção aumenta 400%
No ano seguinte, a HPM adicionou mais cinco robôs S3 usados, aplicando o que aprendeu com o sistema inicial para automatizar outras prensas compactas. Após 18 meses, a HPM economizou o suficiente em sucata e mão de obra para investir em seu primeiro novo robô.
Avanço rápido para 2019. Agora com mais de 200 robôs instalados, a instalação de Greensburg tem o mesmo número de funcionários de 10 anos atrás, mas produz quatro vezes o volume, entregando facilmente mais peças com menos pessoas do que qualquer uma das fábricas globais de PM da Hitachi .
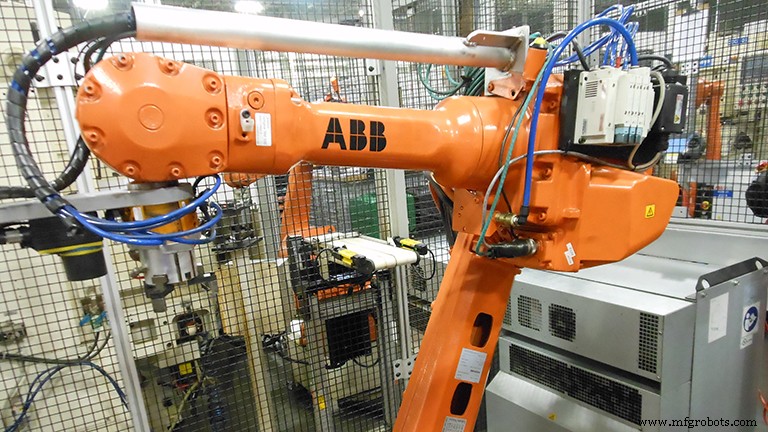
“Uma vez que o primeiro robô foi instalado para a parte frágil, ficou muito óbvio que poderíamos realmente tirar proveito de outros robôs autômatos”, disse Owens. “Os robôs superaram em muito nossas expectativas iniciais e, com a escassez de mão de obra que continuamos enfrentando, francamente, acredito que os robôs nos salvaram de potencialmente não existir.”
Com o sucesso do primeiro robô, o ritmo das instalações subsequentes foi constante. Demorou dez anos para atingir 100 robôs instalados e, à medida que os negócios e a economia continuaram a melhorar, apenas mais quatro anos para atingir os 200 th recém-instalados robô.
Quando surgiram as oportunidades, a HPM continuou a comprar robôs ABB usados em boas condições, embora mais e mais robôs novos fossem adicionados à frota. Na verdade, todos os robôs adicionados desde o número 147 em 2015 são novos.
A base de instalação da HPM inclui uma variedade de robôs de seis eixos de pequeno e médio porte da ABB, um robô Delta e vários modelos SCARA adicionados recentemente. Juntamente com 350 funcionários, o investimento em automação é bem utilizado, funcionando em três turnos de cinco a seis dias por semana.
“Nossa sede corporativa fica no Japão”, disse Adams. “Uma vez que eles viram o desempenho dos robôs e o rápido retorno do investimento, eles apoiaram muito nossa agenda robótica.”
Alguns dos robôs, novos e usados, são ABB Foundry Prime da ABB Robotics, Auburn Hills, Michigan. Eles são modelos com classificação IP67 que possuem conexões bem vedadas que protegem o funcionamento interno dos robôs do metal fino e afiado pós que flutuam pela atmosfera da planta. Os muitos modelos de robô padrão com classificação IP65 no piso da HPM são robustos e têm sido capazes de suportar o ambiente empoeirado.
Expansão contínua
A proliferação de robôs na HPM foi apoiada pela replicação de aplicativos existentes e pela expansão da automação para outras funções nas instalações.
Após a instalação do primeiro robô encarregado da prensa compacta para o produto mais frágil, Adams e sua equipe automatizaram sequencialmente a remoção dos compactos de outras prensas. Parte desse processo consistia em colocar cada peça em uma escala para verificar sua integridade. Uma vez verificada, a peça foi colocada em uma esteira que conduzia ao forno.
Eficiências de mão de obra adicionais resultaram e, com o toque hábil do robô, a taxa de sucata das peças menos frágeis passou de 7% para os mesmos 0,5% da peça inicial.
Ao final do transportador as peças são colocadas em bandejas de sinterização que, ao serem preenchidas, são colocadas em fornos para o processo de endurecimento. Este processo de carregamento do forno tornou-se a segunda função principal a ser automatizada.
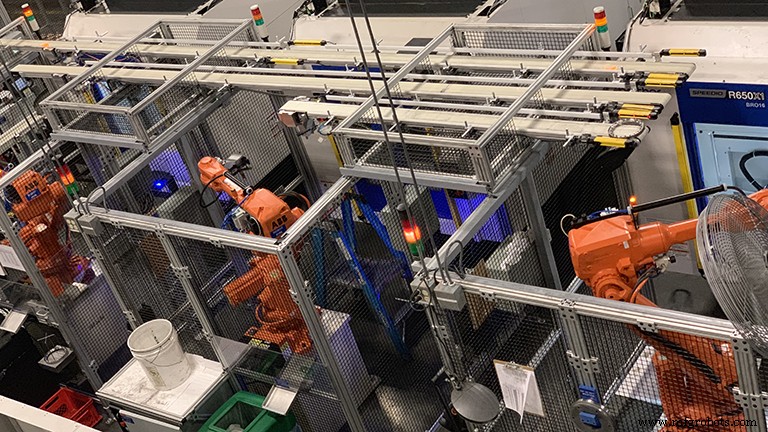
Continuando a um ritmo medido, foram instalados robôs para retirar as peças das bandejas e colocá-las em paletes, além de inserir divisórias entre cada camada de paletes.
“À medida que nos familiarizamos com os robôs, pegamos o que aprendemos e duplicamos os aplicativos nas instalações”, disse Adams. “A programação ficou muito mais fácil e, no último dia de instalação da linha, ajustamos os programas existentes, copiamos e colamos e estávamos funcionando em algumas horas.”
RobotStudio, o software de simulação e programação offline da ABB, tornou-se uma ferramenta valiosa para acelerar a adoção crescente da tecnologia robótica pela HPM. Construído no ABB VirtualController, uma cópia exata do software real que executa os robôs em produção, o RobotStudio realiza simulações realistas, usando programas de robôs e arquivos de configuração idênticos aos usados no chão de fábrica. Com o RobotStudio, Adams conseguiu projetar o layout ideal da célula e verificar seu desempenho antes de integrar os robôs em uma operação específica.
“É o melhor software já desenvolvido”, disse Adams. “Economiza tempo e dinheiro tanto na criação de sistemas para novos aplicativos quanto na replicação daqueles que já havíamos instalados em outras áreas da planta.”
Introdução da Visão
A relativa simplicidade de replicação existe somente depois que um determinado aplicativo foi instalado e refinado no chão de fábrica. Novas aplicações costumam ser mais desafiadoras. Após 18 meses e a integração bem-sucedida de seis robôs de impressão, a HPM teve a confiança necessária para adotar a tecnologia habilitada para visão, em sua infância na época (2006), para automatizar roboticamente a complexa operação de cunhagem ou repressão.
Depois que as peças saem do forno, elas geralmente podem deformar, o que exige que elas sejam colocadas em uma prensa que as cunha de volta para serem retas ou planas. Muitas peças têm rasgos de chaveta ou dentes que precisam ser colocados no molde com todos os aspectos alinhados com precisão. Antes da chegada dos robôs, as peças cunhadas eram tratadas por um sistema de automação rígido que, com muitas variações de produtos diferentes, exigia trocas frequentes e demoradas. As trocas foram tão longas que backups de 250 lotes de produtos, cada um com aproximadamente 100 peças, eram comuns.
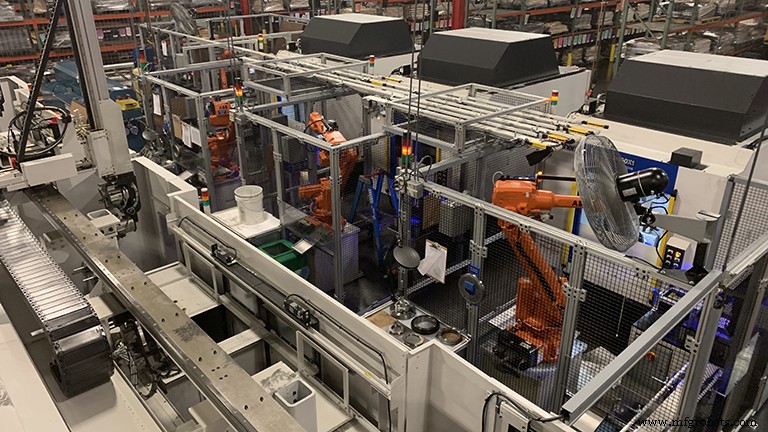
Com o robô habilitado para visão, não há tempo de inatividade. O robô é capaz de identificar a peça de um grupo de muitas peças diferentes, pegá-la, orientá-la radialmente e posicioná-la com precisão na repressão.
Como o sistema de visão precisava interagir com a mais recente tecnologia robótica, este foi o primeiro novo robô da ABB instalado nas instalações de Greensburg. Logo após a operação, mais dois novos robôs foram adquiridos para a mesma aplicação.
“Antes da instalação do robô da estação de cunhagem, a equipe de repressão trabalhava todos os dias”, disse Adams. “Seis meses após a instalação do primeiro robô de visão, não havia mais backups e a equipe teve seus fins de semana de folga!”
Visão Adicional
A HPM usou a visão novamente no último dos principais processos a serem automatizados, a despaletização de peças que foram enviadas para tratamento térmico especializado. Embora as peças sejam enviadas ordenadamente posicionadas em camadas em camadas em um palete, elas voltam em relativa desordem e são difíceis de desempilhar. Um robô ABB com visão integrada é capaz de encontrar as peças e agarrá-las com segurança para que possam ser despaletizadas com segurança.
“Essa é uma das capacidades exclusivas dos robôs da ABB”, disse Dave Fox, presidente da CIM Systems, que ajudou a integrar os vários sistemas de visão. “As peças estão realmente desorientadas nos patins, não em fileiras uniformes, com algumas de cabeça para baixo. Um robô típico de seis eixos teria todos os tipos de problemas de singularidade, chegando a uma posição em que não pode mais se mover. Mas o robô da ABB usando a prevenção avançada de singularidade é capaz de encontrar as peças, agarrá-las e colocá-las com segurança em um transportador sem perder o ritmo.”
Robôs SCARA para inspeção de qualidade
Não surpreendentemente, uma busca recente por um sistema mais eficiente para inspecionar guias de válvulas levou de volta aos robôs, neste caso um grupo de modelos ABB SCARA (Selective Compliance Assembly Robot Arm), que são normalmente usados para montagem de peças pequenas e manuseio de materiais.
O protocolo HPM exige 100% de inspeção de todas as guias de válvula, o que é um grande empreendimento, dada a variedade de peças que devem ser testadas:30 variações de tamanho diferentes e 16 pontos de detecção para cada peça. Com o sistema de testes de automação rígido predominante incapaz de acompanhar suficientemente o volume, Adams começou a procurar um sistema melhor.
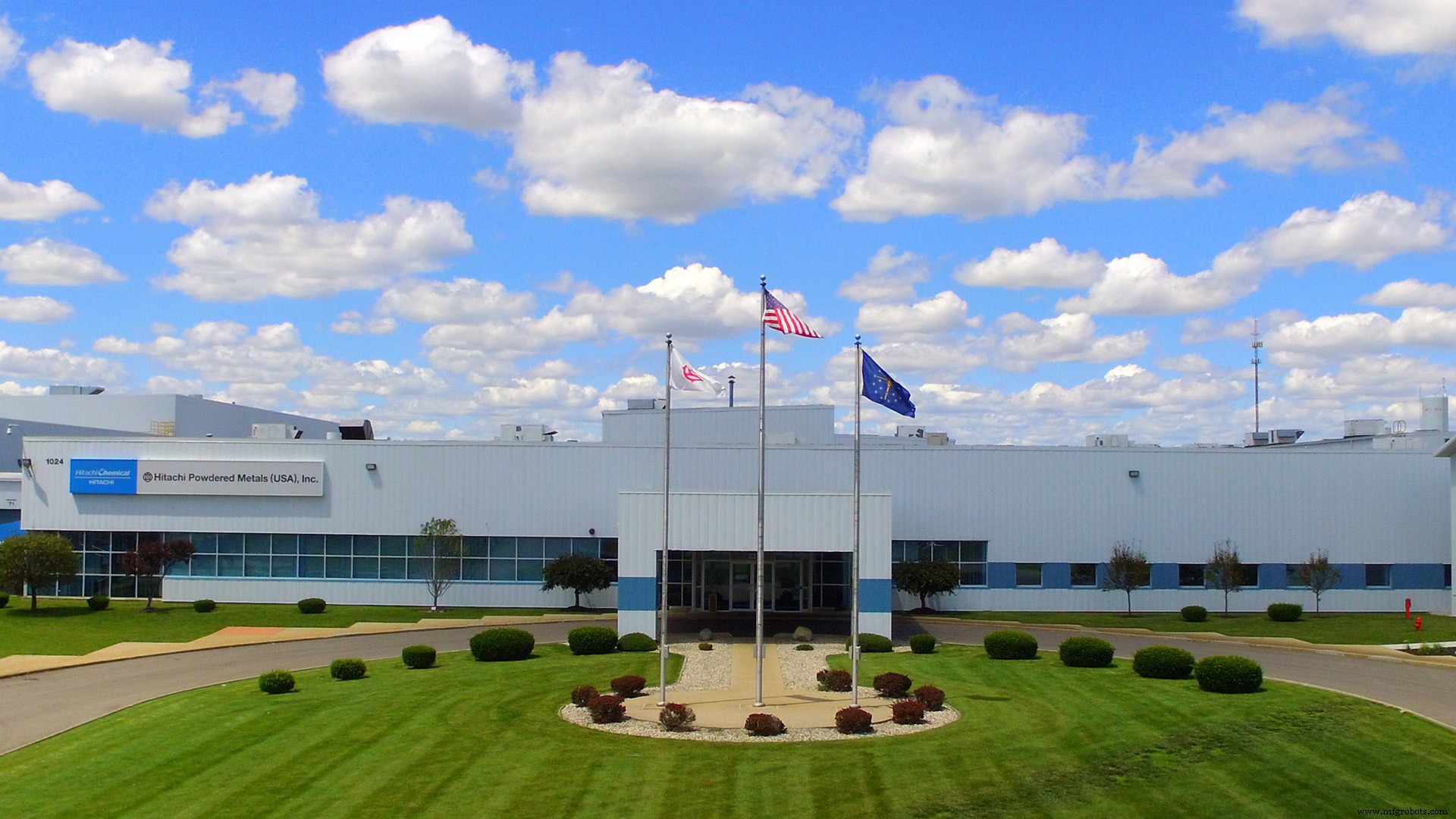
Depois de analisar várias opções, todas com muitas partes móveis e exigindo engenharia complexa, Fox sugeriu projetar um sistema em torno dos robôs SCARA, que a ABB adicionou ao seu portfólio em 2016. Eles certamente eram rápidos o suficiente, com grande repetibilidade e tinham uma pegada pequena e uma forma de montagem sem impedimentos que se encaixam em um espaço confinado.
Um sistema relativamente simples foi projetado com três robôs SCARA pegando guias de válvula individuais de um transportador de tremonha e apresentando-os a câmeras de visão e um “comparador” estacionário nos vários ângulos necessários para acessar os 16 pontos de detecção. As peças que passaram foram colocadas em um transportador e as que não passaram foram colocadas em caixas de rejeição.
Com a flexibilidade de lidar habilmente com cada variação de peça diferente com facilidade semelhante, o sistema é capaz de inspecionar uma peça a cada dois segundos, 30% mais rápido do que o método anterior. Como os movimentos estão confinados a uma curta distância e as peças são muito leves, um robô de seis eixos não funcionaria tão efetivamente quanto o elegante SCARA de alcance limitado.
“Os SCARAs são uma grande adição ao portfólio da ABB. Se não fosse por essa solução, a Hitachi provavelmente teria que buscar outra tecnologia para inspeção de peças”, disse Fox. “Foi bom poder encontrar outro aplicativo para robôs, embora essa não tenha sido a primeira opção que me veio à mente.”
Sistemas CIM sempre presentes
Uma constante que está em cena desde o primeiro robô instalado na HPM até os dias atuais, seja em primeiro plano ou em segundo plano, é a CIM Systems. Sempre disponível quando necessário, a CIM configurou o HPM com robôs novos e usados, ajudou a programar e solucionar problemas e, talvez o mais importante, ensinou a equipe do HPM a fazer muitas coisas por conta própria.
Quando a HPM integrou robôs em uma nova aplicação, com visão ou não, a CIM fez a configuração e programação, sempre pensando em compartilhar seus conhecimentos, incluindo o uso do RobotStudio. Durante a pausa ocasional na linha do tempo de aquisição de robôs da HPM, a CIM estava disponível para atualizar programas, encontrar peças de reposição indescritíveis para modelos mais antigos ou oferecer conselhos sobre como trabalhar com robôs em várias safras.
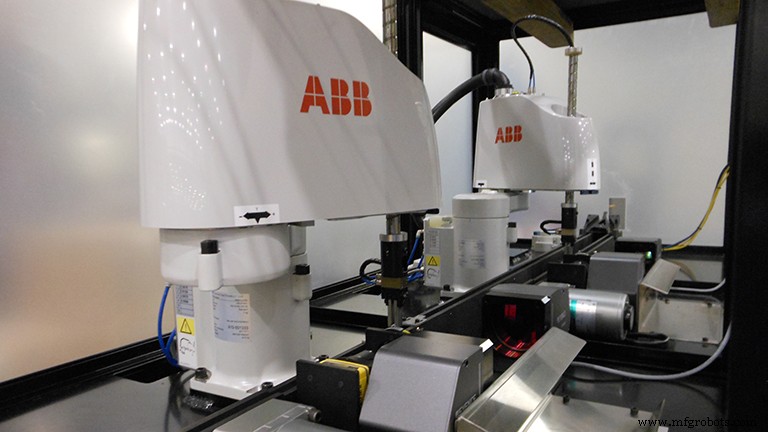
“À medida que atingimos cada um dos diferentes processos, a CIM fez a integração inicial e a programação. Assim que começamos a replicar os processos em toda a fábrica, aprendemos o suficiente para fazer muito por conta própria”, disse Adams. “Por causa de seu relacionamento próximo com a ABB, Dave Fox sempre sabe quando uma nova tecnologia está chegando e quais robôs seriam ideais para nossas diversas aplicações. O suporte que recebemos da CIM Systems e o serviço da ABB foi uma combinação ideal.”
Com um relacionamento tão duradouro, não é surpresa que, quando o primeiro robô saiu da linha de produção da ABB nos EUA em Auburn Hills em 2017, ele foi comissionado pela CIM na HPM. O robô IRB 2400 exclusivo foi pintado de vermelho, branco e azul na fábrica e está posicionado de forma destacada nas instalações da HPM, realizando tarefas de inspeção e paletização.
“Estamos entusiasmados por termos conseguido adquirir o primeiro robô fabricado nos Estados Unidos para HPM”, afirmou Fox. “É especialmente significativo porque a fábrica de Indiana possui o autômato mais flexível das muitas instalações globais da HPM.”
Suporte de outras instalações HPM
A gestão corporativa da HPM no Japão tomou conhecimento das grandes melhorias de produtividade que a equipe de Greensburg alcançou com robôs e, em 2017, designou Adams e Owens para liderar uma iniciativa “Global Robotics” para apoiar as outras fábricas de metal em pó da Hitachi em todo o mundo, expandindo seu uso de robôs .
O programa de dois anos já passou do ponto médio e as empresas afiliadas estão começando a perceber melhorias significativas de produtividade, mesmo com os custos trabalhistas mais baixos nos outros países.
Adams configurou a função de monitoramento remoto da ABB no HPM para que ele ou membros de sua equipe possam ver como os robôs estão operando e solucionar a maioria dos problemas de qualquer lugar fora da fábrica em um laptop, tablet ou smartphone. Com os robôs mais novos, a HPM espera tirar proveito dos ABB Ability Connected Services — a oferta digital unificada, multissetorial e digital da ABB — que fornece dados em tempo real sobre o status e o desempenho do robô de qualquer local.
Planos futuros
A missão contínua da HPM inclui melhorar suas operações com automação robótica.
“Esperamos crescer 10% ao ano no futuro próximo e devemos fazer o que pudermos para nos mantermos competitivos”, disse Owens. “Estamos analisando quais peças de transmissão poderemos fabricar para veículos elétricos e focamos em penetrar em segmentos não automotivos, como equipamentos pesados, onde o metal em pó pode substituir peças feitas de outros materiais a um custo menor. .”
“Eu certamente prevejo que o ritmo das instalações de robôs permaneça estável ou até aumente”, disse Owens.
Para obter informações sobre a Hitachi Powdered Metals (USA) Inc., visite www.hitachi-pm.us ou telefone 812-663-5058. Para obter informações sobre a CIM Systems Inc., visite www.cimrobotics.com ou ligue para 317-773-5600. Para obter informações da ABB Robotics, visite www.abb.com/robotics ou ligue para 248-391-9000.
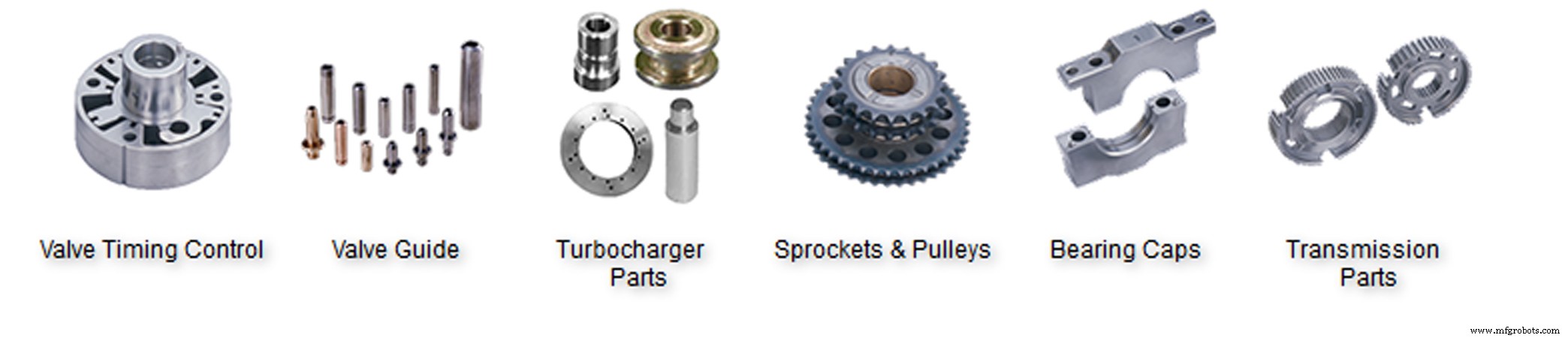
Sistema de controle de automação
- Logística e automação de armazenamento
- Mais automação =Robôs mais capazes
- NPE2018:Robôs e automação aumentam a complexidade
- Automação:Lâmina de rebarbação compatível para robôs
- A ABB prevê as principais tendências que mudarão a automação robótica em 2022
- Um novo tipo de "cérebro" robótico pode transformar fábricas modernas
- Hitachi adquire o integrador de sistemas robóticos JR Automation por US$ 1,4 bilhão
- Hitachi conclui aquisição da JR Automation
- ATI Industrial Automation lança nova lixadeira orbital para robôs
- Mercado de automação de processos robóticos para ganhar impulso da força de trabalho digital da Blue Prism e sua automação excepcionalmente segura