Eletrônicos de consumo:tampas compostas híbridas
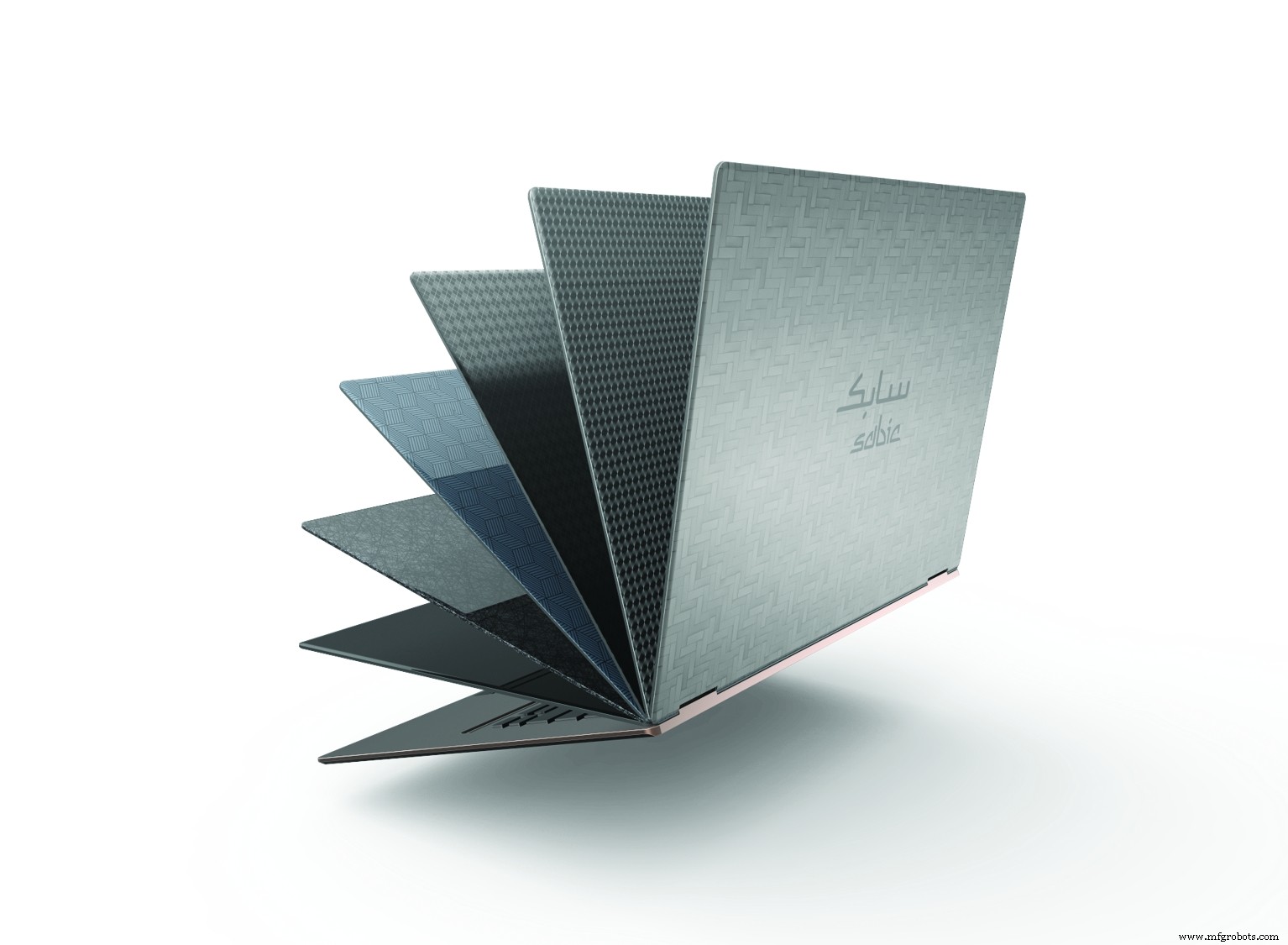
A SABIC demonstrou em um estudo recente que uma capa de 1 milímetro de espessura pode atender a todas as especificações relevantes de desempenho da indústria para notebooks ou tablets muito finos. Fonte, todas as imagens | SABIC
A eletrônica de consumo é um mercado dinâmico com tempos de ciclo bastante curtos entre as gerações de produtos. De seus smartphones, smartwatches, tablets e notebooks / laptops, os consumidores desejam velocidades operacionais mais rápidas, baterias mais duráveis, maior durabilidade e mais recursos com menor custo e peso. Para atender à demanda do consumidor, os OEMs pedem aos fornecedores materiais com alta estética e liberdade de design, excelente resistência ao impacto e alta rigidez - o que denota qualidade neste mercado - em seções de baixo peso e paredes finas. Eles também desejam métodos de processamento econômicos e altamente repetíveis que atendam à demanda de produção global de dezenas de milhões de unidades anualmente. Essas pressões empurraram o mercado primeiro para metais leves para tampas / caixas e armações, e agora estão direcionando-o para soluções de metal / composto e totalmente composto.
Um estudo de viabilidade conduzido pela SABIC (Bergen op Zoom, Holanda) envolveu o uso de dois tipos de compostos termoplásticos para produzir uma capa para notebook / tablet com 1 mm de espessura. O estudo mostrou que o projeto de composto termoplástico híbrido pode ser uma solução viável para o desafiador mercado de eletrônicos de consumo.
Caso de teste
Desde 2012, a SABIC fez uma série de investimentos para desenvolver suas próprias fitas compostas termoplásticas reforçadas com fibra unidirecional (UD) (consulte "Evoluindo para reforços de fibra contínua"), que estendeu a competência central da empresa em injeção de fibra curta e longa materiais termoplásticos de fibra (LFT) e permitiram que a SABIC se expandisse para compósitos termoplásticos de alto desempenho. Em 2015, a empresa adquiriu participação majoritária na fabricante de fitas Fiber Reinforced Thermoplastics BV (FRT, Lelystad, Holanda) e em 2017 fez parceria e tornou-se um investidor minoritário na Airborne (Haia, Holanda), uma fabricante de máquinas e desenvolvedora de processamento de compósitos linhas.
Como a SABIC e a Airborne projetaram e desenvolveram tecnologia para produzir de forma rápida e econômica laminados à base de fita termoplástica de alta qualidade para mercados de volume verdadeiramente alto (consulte "Fabricação de compósitos termoplásticos de alta velocidade e alta taxa"), a equipe começou a procurar um caso de teste. Este demonstrador seria uma importante ferramenta de marketing para provar os conceitos de projeto para laminados compostos termoplásticos produzidos a partir de fitas compostas sobremoldadas com compostos reforçados com fibra descontínua. Também seria importante testar as ferramentas de engenharia preditiva que a equipe desenvolveu para ambas as tecnologias de materiais e mostrar o processo de fabricação de alta velocidade em evolução na Holanda.
“Decidimos nos especializar em aplicações de eletrônicos de consumo”, explica Gino Francato, líder global de compostos da SABIC. “Esse mercado é muito interessante porque existe uma ambição real de mudar para materiais leves para tornar nossos telefones celulares e notebooks mais leves e finos. E como eles fazem milhões e milhões deles, decidimos aceitar o desafio que esse mercado oferecia. ”
“Decidimos começar com algo que era razoavelmente complexo, mas não muito complexo ”, explica Scott Davis, tecnologia de aplicação global de cientistas da equipe da SABIC. A capa superior de um notebook muito fino ou até mesmo de um tablet - que a equipe esperava que acabasse sendo traduzido em componentes de smartphone - parecia um bom lugar para começar. “Estávamos trabalhando com uma geometria geral simples, um retângulo, que ainda precisava manter uma alta estética e oferecer muita complexidade em seu lado B, incluindo recursos de fixação”, continua Davis. “Tivemos que manter a tampa muito fina, mas ainda assim atender aos desafiadores requisitos de deflexão comuns na indústria. E, claro, tivemos que entregar um produto muito consistente por meio de um novo processo de fabricação complexo. ”
Como eles não estavam trabalhando com um projeto real do cliente e estavam apenas criando a capa protetora para uma tela, eles usaram uma geometria genérica. Na verdade, Davis observa, quando eles começaram a cortar ferramentas de injeção para desenvolvimento interno, eles não tinham certeza se fariam uma capa para tablet ou notebook, então a capa foi projetada para funcionar para ambos. “Havia muitos desafios para preparar uma solução composta para produção de alto volume”, acrescenta Davis. “Na verdade, havia muita coisa acontecendo simultaneamente - desenvolvimento de fita, desenvolvimento de laminado e desenvolvimento de processo - e não podíamos esperar até que todas essas coisas estivessem finalizadas para começar nosso ferramental, que é como terminamos com esse design.” Com o projeto básico concluído, a equipe se concentrou em outros detalhes, como a melhor forma de passagem, que tipos de sobreposições eram necessárias entre a pastilha laminada e o composto de sobremoldagem, como lidar com a colocação automatizada dentro da ferramenta, como lidar com o coeficiente de ( linear) incompatibilidade de expansão térmica (CLTE ou CTE) entre os dois compostos e como criar uma peça facilmente repetível.
Atendendo a requisitos desafiadores
O objetivo era desenvolver uma cobertura superior de 1 milímetro de espessura que fornecesse alta rigidez e passasse em todos os requisitos de desempenho e estéticos - especialmente no teste de deflexão do ponto central aplicado regularmente a tampas de laptop para avaliar as cargas necessárias para danificar a tela subjacente. Os requisitos de carga / deflexão variam por OEM, dispositivo e modelo, mas normalmente não mais do que 3-5 milímetros de deflexão são permitidos sob 40-120 Newtons de pressão - uma situação que simula as cargas exercidas por um dedo ou cotovelo pressionado na tampa como um usuário humano se levanta. Em muitas indústrias, a estratégia para passar em tais testes seria aumentar a espessura da seção, mas este mercado valoriza projetos mais finos que liberam espaço para baterias maiores e outros componentes sem aumentar o tamanho ou peso do dispositivo. Portanto, a equipe precisava usar uma estratégia de projeto diferente para evitar danos à tela - ou seja, selecionar materiais mais rígidos (por meio de uma inserção de laminado) e usar a geometria (por exemplo, nervuras por sobremoldagem por injeção). Mas, primeiro, eles tiveram que especificar os materiais.
Um desses materiais, o policarbonato (PC), já é amplamente utilizado nesta indústria para coberturas e outros componentes, devido à sua excelente estética e elevada resistência ao impacto. Os maiores pontos fracos do polímero são a resistência química e arranhões na superfície, mas o revestimento, tinta ou combinações de ambos aplicados à maioria das coberturas geralmente superam esses problemas potenciais.
“Como os computadores ultraleves são muito finos, o espaço interno da embalagem é muito valioso, então os desvios e a mecânica tornam-se realmente críticos”, destaca Francato. “Embora você queira usar vidro [reforço] do ponto de vista de custo, tivemos que usar carbono [fibra] para obter a rigidez de que precisávamos.” Como resultado, todos os laminados baseados em fita avaliados eram variações do policarbonato reforçado com fibra de carbono - graus então em desenvolvimento com a subsidiária FRT da SABIC.
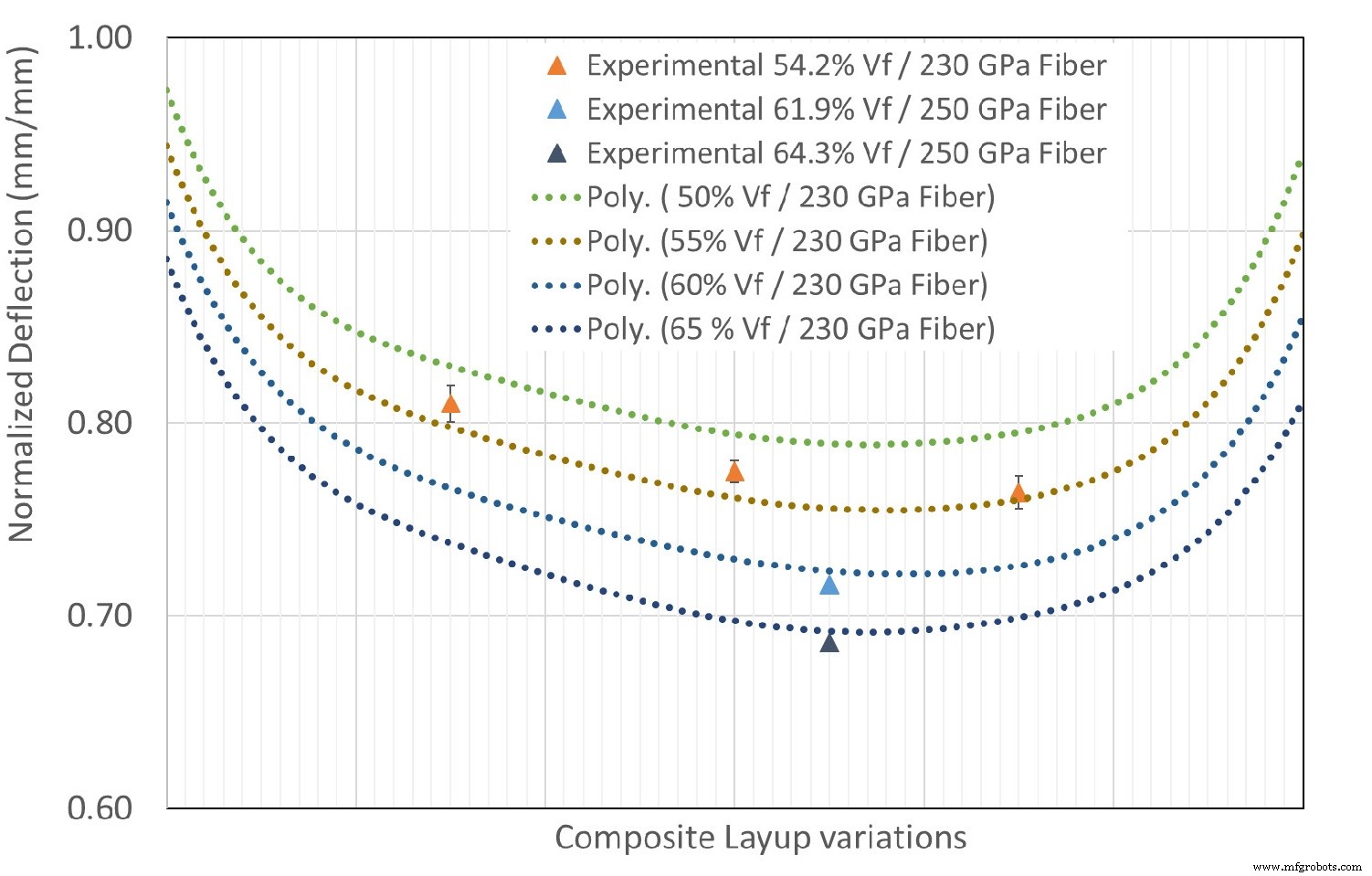
A SABIC desenvolveu modelos preditivos para simular o tipo e a arquitetura do laminado (com e sem compostos de sobremoldagem) versus o desempenho da peça moldada e relata que foi alcançada uma forte correlação entre as previsões e os resultados experimentais. As ferramentas de engenharia preditiva aceleram o desenvolvimento de materiais.
O composto de sobremoldagem exigia uma abordagem diferente. Inicialmente, a estratégia era usar um composto LFT de fibra mais longa, mas por uma série de razões - incluindo altos requisitos estéticos, tamanho da peça e estratégia de passagem - os compostos de fibra curta atenderam melhor aos requisitos do projeto. Outro problema era o tipo de fibra a ser usada. “Compostos de injeção de carbono curto são realmente difíceis de trabalhar e ainda assim obtêm alta estética”, continua Francato, “então, para nosso material de sobremoldagem, olhamos para grades reforçadas com vidro curto”. A subsidiária da SABIC, LNP Engineering Plastics, Inc. (Exton, Pa., EUA), oferece muitos tipos de fibra de vidro / PC com boa estética e rigidez que são populares entre os OEMs de dispositivos, então a equipe se concentrou neles.
Embora o PC totalmente amorfo seja menos sujeito a empenamento do que os polímeros semicristalinos, a equipe ainda se preocupava com as diferenças CLTE entre as fitas de fibra de carbono UD altamente reforçadas e anisotrópicas e os graus de sobremoldagem de fibra de vidro curta mais isotrópica e descontínua com cargas de fibra mais baixas. “Em paredes tão finas, há muito pouco espaço para erros, então as pequenas diferenças no CLT foram coisas que tivemos que considerar cuidadosamente”, explica Davis. “E isso nem sequer toca em todos os problemas normais com os quais você está preocupado durante a moldagem por injeção, como locais de passagem, padrões de preenchimento, pressões de embalagem e linhas de malha. Todos esses fatores foram simulados e verificados com testes físicos. ”
Uma vez que os materiais foram escolhidos, os engenheiros da SABIC conduziram várias iterações de enchimento do molde, análise estrutural e simulação de empenamento para avaliar a disposição do laminado, geometria e combinações de materiais para otimizar a rigidez para o teste de carga / deflexão, além de outros requisitos de desempenho e custo. A empresa diz que desenvolveu ferramentas de modelagem de compostos abrangentes e precisas (disponíveis para os clientes e executando em códigos estruturais e de processamento comuns) que podem modelar e simular rapidamente a arquitetura do laminado, composição do composto de sobremoldagem e várias opções de processamento e ferramentas em comparação com o desempenho da peça moldada. Diz-se que essas ferramentas alcançam uma forte correlação entre as previsões e o desempenho medido e são ideais para acelerar o desenvolvimento de materiais personalizados.
Pronto para o horário nobre
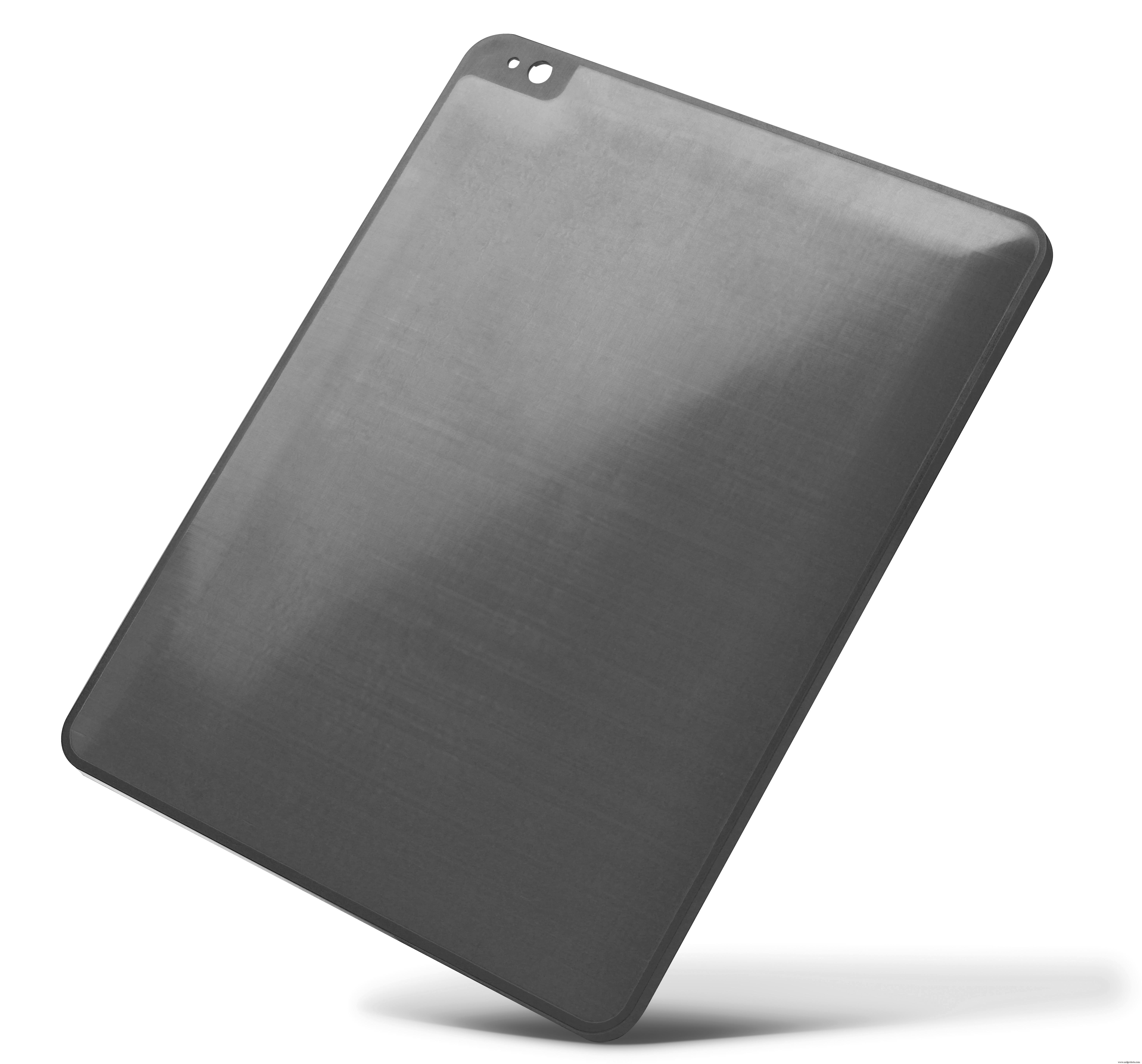
Parte frontal da tampa final do laptop / tablet, que foi produzida usando um inserto laminado à base de fita de policarbonato reforçado com fibra de carbono sobremoldado com composto de vidro curto / copolímero de policarbonato, uma combinação que atendeu a todos os requisitos mecânicos e estéticos relevantes em um 1- parte milimetrada de espessura.
O demonstrador final apresenta uma inserção laminada produzida a partir de sete camadas de fibra de carbono UDMAX / fitas de PC (fração de volume de fibra de 55%), então consolidada, aparada, pré-formada e aparada novamente para a forma líquida final, antes de ser moldada por injeção com 40% de fibra fração de peso THERMOCOMP D452 fibra de vidro curta / copolímero de PC (um grau otimizado para alto fluxo e alta estética e já amplamente utilizado neste segmento). A combinação produz uma cobertura com alta rigidez e resistência em baixa massa e espessura de seção, enquanto inclui vários detalhes de design 3D, recursos de fixação e boa estética, aproveitando assim o melhor de cada material. A capa supostamente passou em todos os testes de requisitos da indústria e atualmente está sendo avaliada por OEMs de dispositivos.
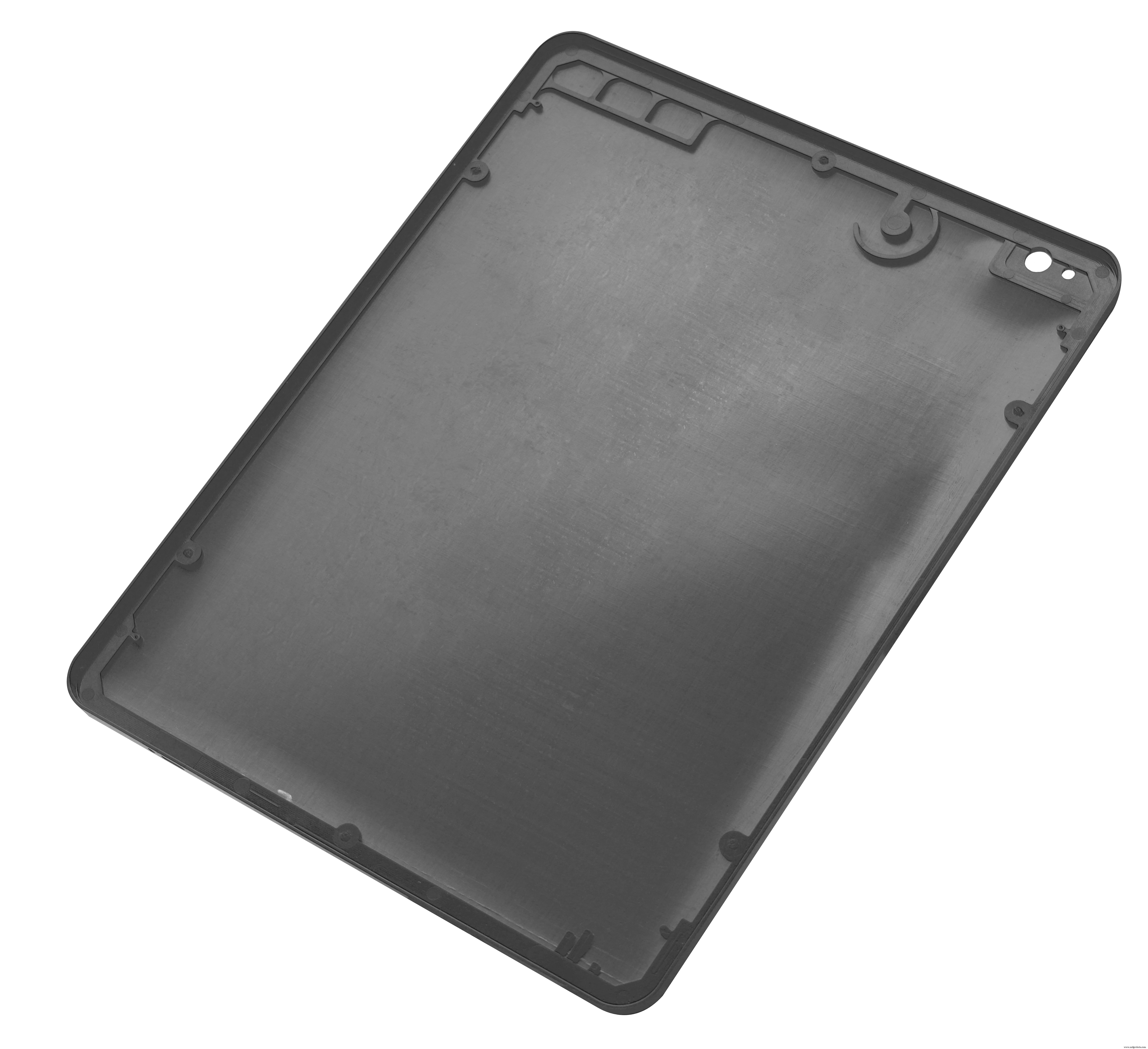
Verso da capa acabada.
O trabalho entre a Airborne e a SABIC também rendeu frutos para os objetivos do mercado de eletrônicos de consumo da SABIC. A parceria foi anunciada em 2018, e este ano foram fornecidos mais detalhes sobre o que ambas as empresas chamam de Linha de Fabricação de Compósitos Digitais, que pode produzir quatro inserções laminadas consolidadas de formato líquido a partir de fitas compostas termoplásticas por minuto ou 1,5 milhão de laminados por ano a partir de uma única linha de produção. O sistema é considerado flexível (em termos de arquitetura e materiais layup) e rápido. A partir de 2020, a Airborne usará a linha para fabricar laminados para uso comercial em produtos eletrônicos de consumo, tornando-se um recurso que ambas as empresas esperam que aumente muito a penetração de compósitos termoplásticos neste segmento altamente competitivo e acelerado.
fibra
- Materiais:Grafite Flexível de Camada Única para Eletrônicos de Consumo
- Solvay Expande a Capacidade do Composto Termoplástico
- Roda termoplástica faz o caminho difícil
- Fraunhofer encomenda células de produção Engel automatizadas para P&D de compósitos termoplásticos
- Fitas termoplásticas continuam a mostrar potencial para aeroestruturas compostas
- Avient lança compósito termoplástico de fibra longa de náilon resistente à umidade
- INEOS Styrolution para construir local de produção para compósito termoplástico StyLight
- Xenia apresenta compostos termoplásticos de CF / PP
- Composto termoplástico TenCate qualificado NIARs NCAMP
- Composto + metal:tecnologia híbrida de perfil oco