Peças híbridas sobremoldadas abrem novos mercados de compósitos
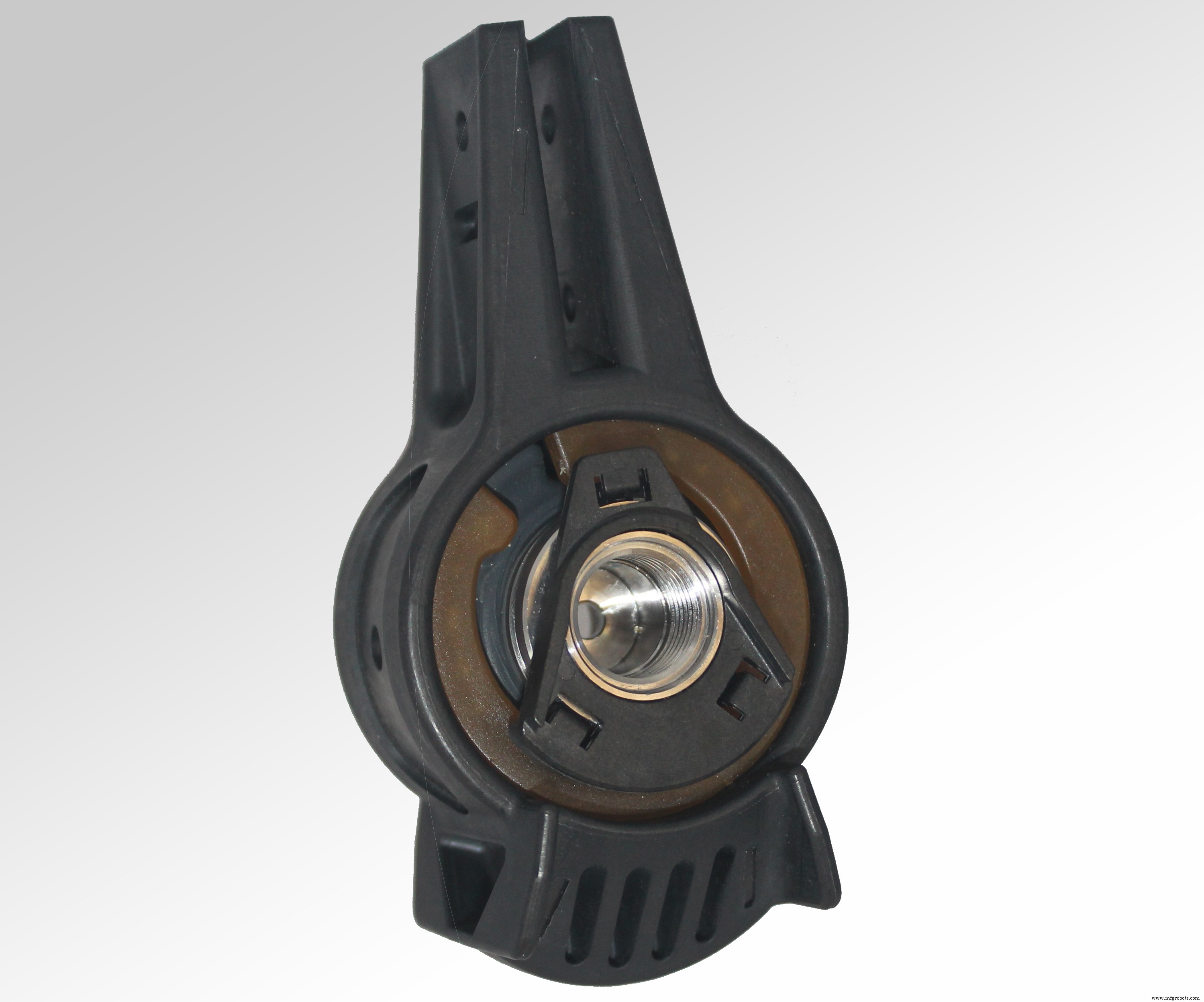
Complexidade e força. Componentes como o suporte B para caixas de armazenamento de aeronaves exibem alta complexidade e um requisito de alta resistência - uma combinação para a qual a técnica de sobremoldagem híbrida é especialmente adequada. Fonte, todas as imagens | TxV Aero Composites
Muitas vezes, no mercado aeroespacial, um OEM está disposto a pagar mais por um componente composto, sabendo que o investimento retornará dividendos em economia de combustível devido ao peso do componente, uma vida mais longa devido a menos desgaste ou outras reduções operacionais e custos de manutenção. Essa visão do “ciclo de vida do produto” abriu muitos mercados e aplicativos para compostos. Mais incomum é um componente composto cujo custo de aquisição é menor do que o da versão de metal. Mas isso está mudando. Alguns novos processos de fabricação de compósitos automatizados estão começando a inclinar a escala em favor dos compósitos, e entre eles está um processo de sobremoldagem híbrido desenvolvido pela TxV Aero Composites (Bristol, R.I., U.S.).
Uma joint venture da Tri-Mack Plastics Manufacturing (Bristol, R.I., EUA) e da Victrex (Thornton Cleveleys, Reino Unido), a TxV avançou sua técnica de sobremoldagem híbrida ao ponto do status de produção comercial. A empresa fez parceria com a SFS intec Aircraft Components (Althengstett, Alemanha) para reprojetar e produzir comercialmente um suporte de compartimento de armazenamento de aeronaves anteriormente feito de alumínio de grau aeroespacial. Uma história de sucesso própria, o suporte também demonstra o potencial de sobremoldagem híbrida e fita unidirecional de fibra de carbono / poliariletercetona (PAEK) VICTREX AE 250 para peso valioso e economia de custos em várias aplicações aeroespaciais - vantagens alcançadas pela substituição de um processo de usinagem de metal subtrativo por um processo de compósitos no qual o material é adicionado, não subtraído.
Da subtração à adição
Os maquinistas e as oficinas que produzem componentes de metal em máquinas CNC se autodenominaram "fabricantes de chips", pela razão óbvia de que seus processos cortam o material desnecessário das chapas de metal para fazer os componentes, criando aparas de metal. Esses cavacos representam um aspecto caro da usinagem de metal, sejam eles descartados, enviados para uma recicladora ou reprocessados internamente. No caso do suporte do compartimento superior de armazenamento da SFS intec, 60 a 70% do alumínio se torna sucata durante as várias etapas de fresagem necessárias para usiná-lo.
Essa alta taxa de refugo torna o custo da matéria-prima para uma versão composta de formato líquido ou quase líquido do suporte potencialmente menor do que o custo do material de metal. “Podemos competir com o alumínio mais barato (por libra) por causa dos chips; se a proporção de compra e venda for de 8:1, a maior parte do alumínio comprado se transforma em sucata ”, observa Jonathan Sourkes, gerente de contas sênior da TxV. “Outro fator é o tempo que cada componente leva para ser fresado. Podemos fazer peças [compostas] em minutos, não horas. ”
Além dos custos de matéria-prima, as versões compostas de componentes como o suporte - apresentando uma geometria complexa e exigindo alto desempenho de suporte de carga - não eram economicamente viáveis usando as opções de fabricação disponíveis historicamente. Por outro lado, se os componentes fossem feitos com reforço de fibra picada de baixo custo em um processo de alta velocidade e baixo toque como a moldagem por injeção, o componente não alcançaria desempenho de suporte de carga suficiente. Por outro lado, se fosse feito com maior carga de reforço de fibra contínua por meio de um processo de baixa velocidade e alto toque, normalmente envolvendo algum layup manual, a produção seria muito lenta e / ou imporia custos de fabricação que tornariam o produto final muito caro.
Por causa desses obstáculos para novas aplicações de compósitos deste tipo, a indústria de compósitos como um todo tem dedicado recursos significativos ao desenvolvimento de processos automatizados que podem produzir tais componentes em taxas de produção adequadamente altas e com capacidade de carga suficiente para atender às necessidades e especificações dos clientes aeroespaciais . Visando a produção comercial de tais componentes compostos, o TxV surgiu em 2017 especificamente para acelerar a adoção comercial de processos de fabricação inovadores para aplicações de compostos baseados em policetona em toda a indústria aeroespacial.
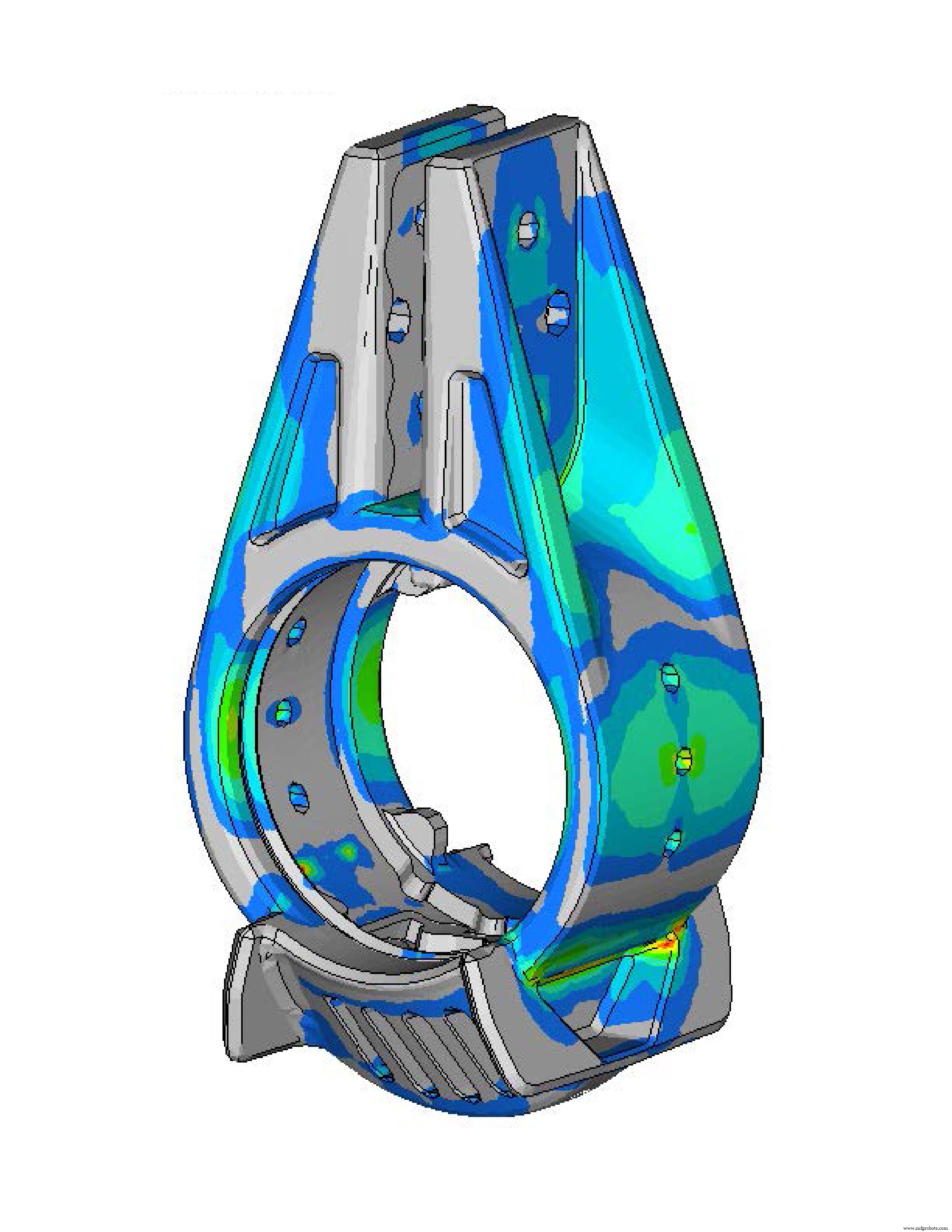
Prototipagem virtual. Usando dados proprietários desenvolvidos para caracterizar a relação entre o laminado e a sobremoldagem, o TxV iterou os layups e as orientações das camadas sem ter que fabricar e testar um protótipo físico. As iterações continuam até que as tensões visíveis, conforme representadas aqui, estejam dentro da faixa de casos de carga fornecidos.
A solução híbrida sobremoldada da TxV incorpora dois avanços importantes para o estado da arte na fabricação de componentes compostos. Primeiro, ele automatiza a produção das partes do componente que requerem a resistência ou rigidez do reforço de fibra contínuo. Em segundo lugar, ele aproveita a velocidade da moldagem por injeção para completar as geometrias complexas do componente. Mais especificamente, ele produz um laminado sob medida para lidar com cargas, que é então moldado para funcionalizar e criar geometrias de peças finais. A técnica híbrida, de acordo com Sascha Costabel, chefe de inovação da SFS intec Aircraft Components, “é uma boa opção para componentes que devem suportar altos níveis de tensão mecânica e geometrias que requerem várias etapas de processamento onde a usinagem convencional é usada”.
A parceria com a SFS intec tem sido uma ótima escolha, diz Sourkes. “Como líder global em anexos de sistema, a SFS está sempre fazendo algo realmente interessante. São muito inovadores e dispostos a investir em novas tecnologias ”, observa. A SFS intec também tem um forte relacionamento com seus clientes de aeronaves, acrescenta, e eles possuem a capacidade de realizar processos de qualificação - chave para a adoção de um componente reprojetado pela indústria aeroespacial.
O suporte do compartimento de armazenamento da aeronave, especificamente referido como “suporte B”, foi escolhido como o primeiro componente de fixação para reprojeto de compósitos porque é representativo de componentes que são desafiadores para projetar e produzir. Seguindo a engenharia colaborativa, a conceituação e design de peças e a modelagem de desempenho por meio de uma ferramenta de análise de elementos finitos (FEA) Altair (Troy, Mich., EUA), a equipe do projeto iterou desde o primeiro artigo para validar, testar e provar o modelo. O projeto para a manufatura foi fundamental para o desenvolvimento do suporte composto, que aproveita as vantagens de fabricação de colocação de fita automatizada para os elementos reforçados com fibra contínua e moldagem por injeção de alta velocidade para os elementos reforçados com fibra picada.
Construção de colchetes B
Um aspecto chave do processo de sobremoldagem híbrida é o uso de polímeros distintos da mesma classe. PAEK serve como a resina de matriz para as porções de compósito de fibra contínua do braquete, enquanto a polieteretercetona (PEEK) é usada nas áreas sobremoldadas. VICTREX PAEK e PEEK apresentam resistência superior à fadiga, química e corrosão; excelente resistência a fumaça, chama e toxicidade; formabilidade rápida; e soldabilidade. VICTREX AE 250, um PAEK de baixo ponto de fusão (LM PAEK), oferece uma temperatura de fusão de 40 graus C menor do que PEEK. “Quando o PEEK fundido flui sobre a superfície do compósito LM PAEK, a temperatura de fusão mais baixa permite uma fixação forte”, explica Sourkes.
As matérias-primas específicas para o suporte B são a fita PAEK reforçada com fibra de carbono unidirecional VICTREX AE 250 (58% de fibra de carbono) em larguras de duas polegadas; e VICTREX PEEK 150CA30 com fibra de carbono curta (30% de fibra de carbono). Esses materiais alimentam as células de trabalho de produção de sobremoldagem híbrida, que criam os suportes por meio do seguinte processo de várias etapas.
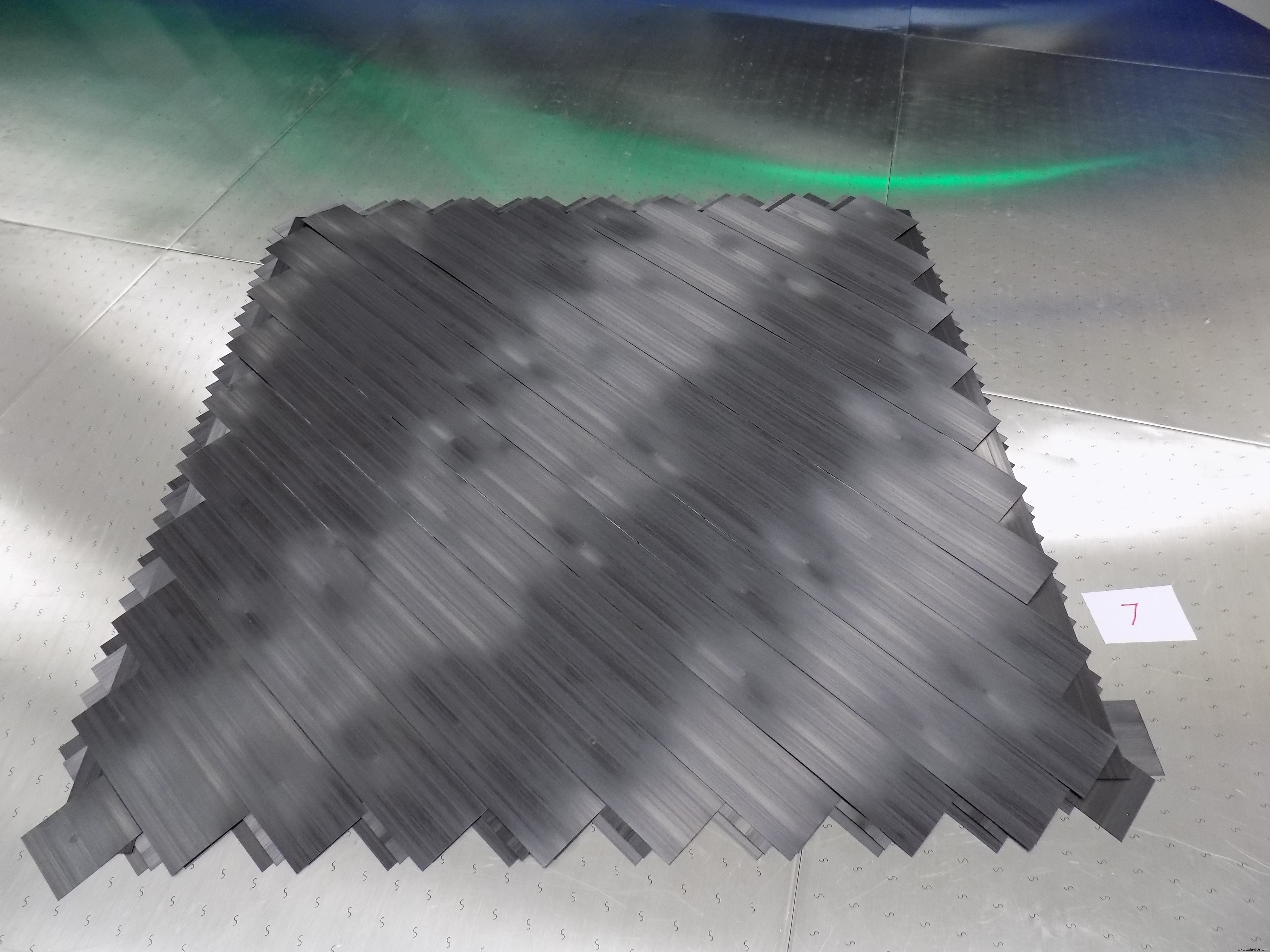
Etapa 1. Um sistema automatizado de colocação de fita Dieffenbacher Fiberforge 2000 produz blanks laminados sob medida.
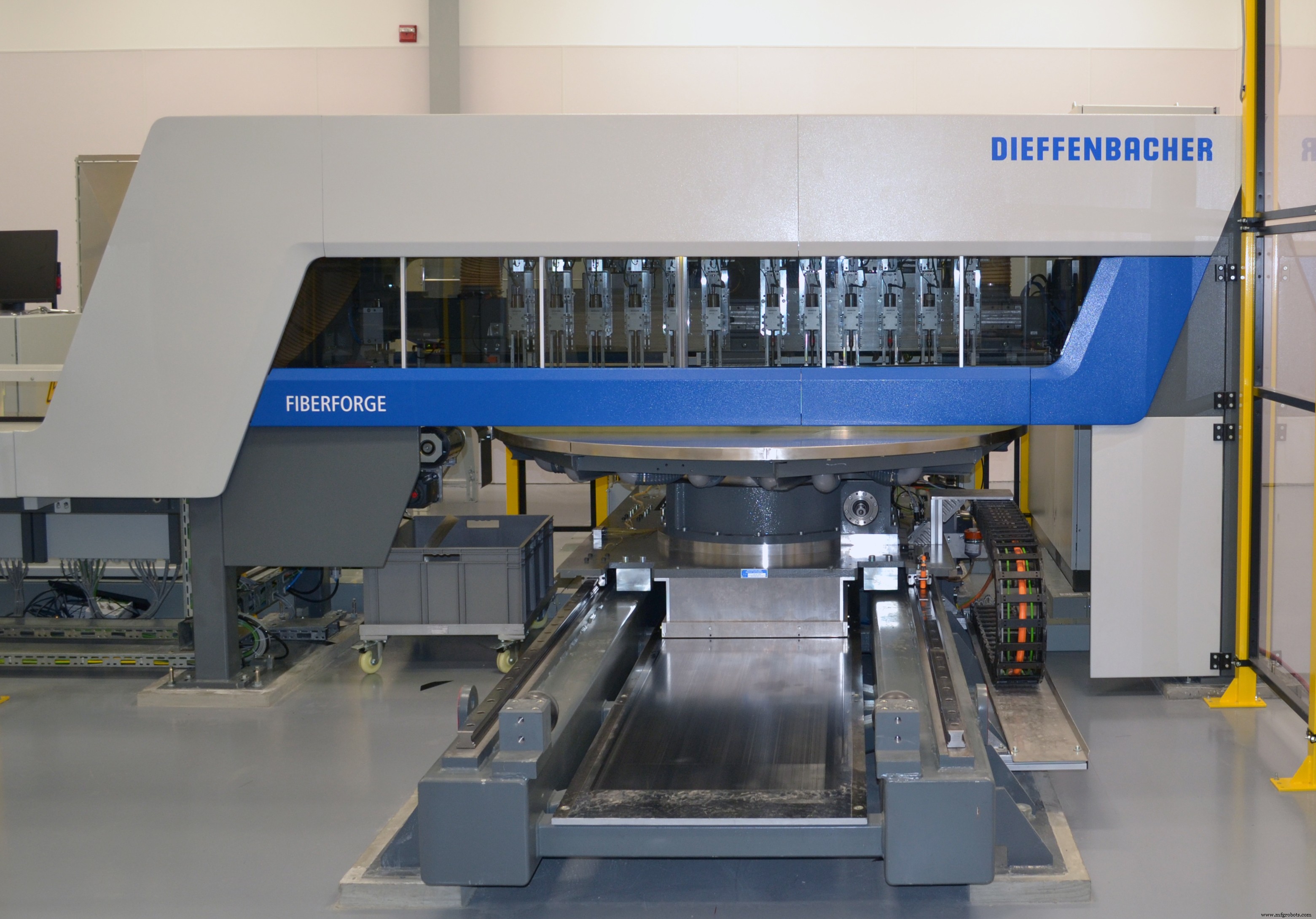
Em primeiro lugar, as fitas de fibra de carbono / PAEK são dispostas em um molde personalizado usando um sistema de colocação de fita Dieffenbacher (Eppingen, Alemanha) Fiberforge 2000. “Esta máquina é atualmente um dos sistemas de colocação de fita mais rápidos do mundo”, atesta Sourkes. É equipado com robôs para carregar e recarregar carretéis de fita, de modo que possa funcionar sem interrupções, minimizando o tempo de toque manual. Layup é projetado para que as lacunas entre as fitas sejam minimizadas. Cada folha da peça bruta ajustada do suporte B é inspecionada antes que a próxima folha seja colocada. O processo é realizado em uma área com controle ambiental para minimizar o potencial de objetos estranhos e detritos (FOD).
Os blanks personalizados são então consolidados em uma célula automatizada sob medida que requer um mínimo de manuseio manual para carregar e descarregar os laminados. Na célula, prensas aquecidas combinadas consolidam um painel, eliminando espaços vazios. Pratos frios combinados, em seguida, esfriam o painel. Os dois conjuntos de prensas, mantidos em temperatura, são muito mais eficientes do que uma prensa estática com um conjunto de prensas. “O resultado é um tempo de ciclo drasticamente reduzido medido em minutos versus horas”, diz Sourkes.
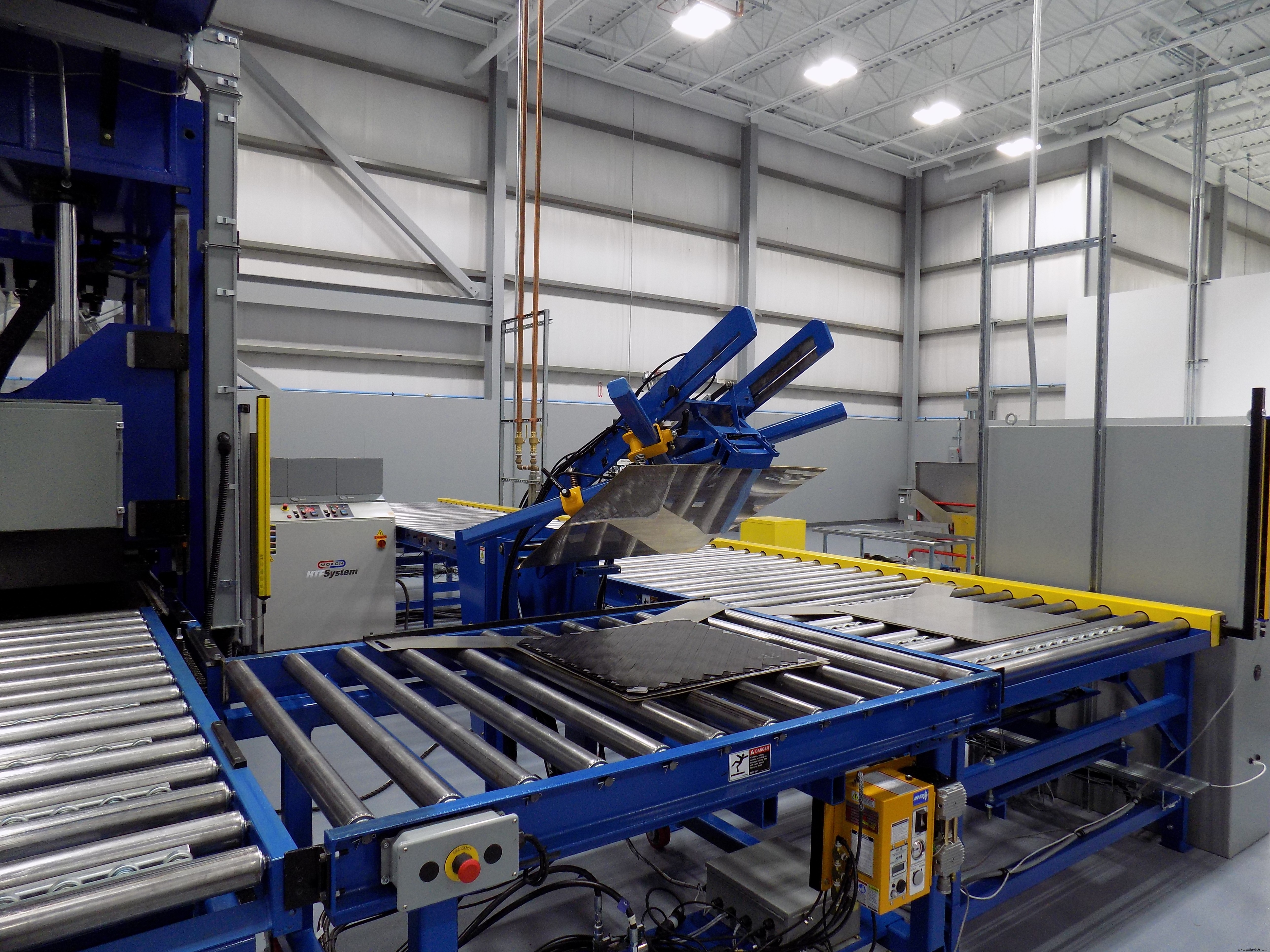
Etapa 2. Os blanks personalizados são consolidados em uma célula de consolidação automatizada sob medida, que apresenta dois conjuntos de placas que são mantidas em temperatura (uma quente, uma fria) para acelerar esta etapa.
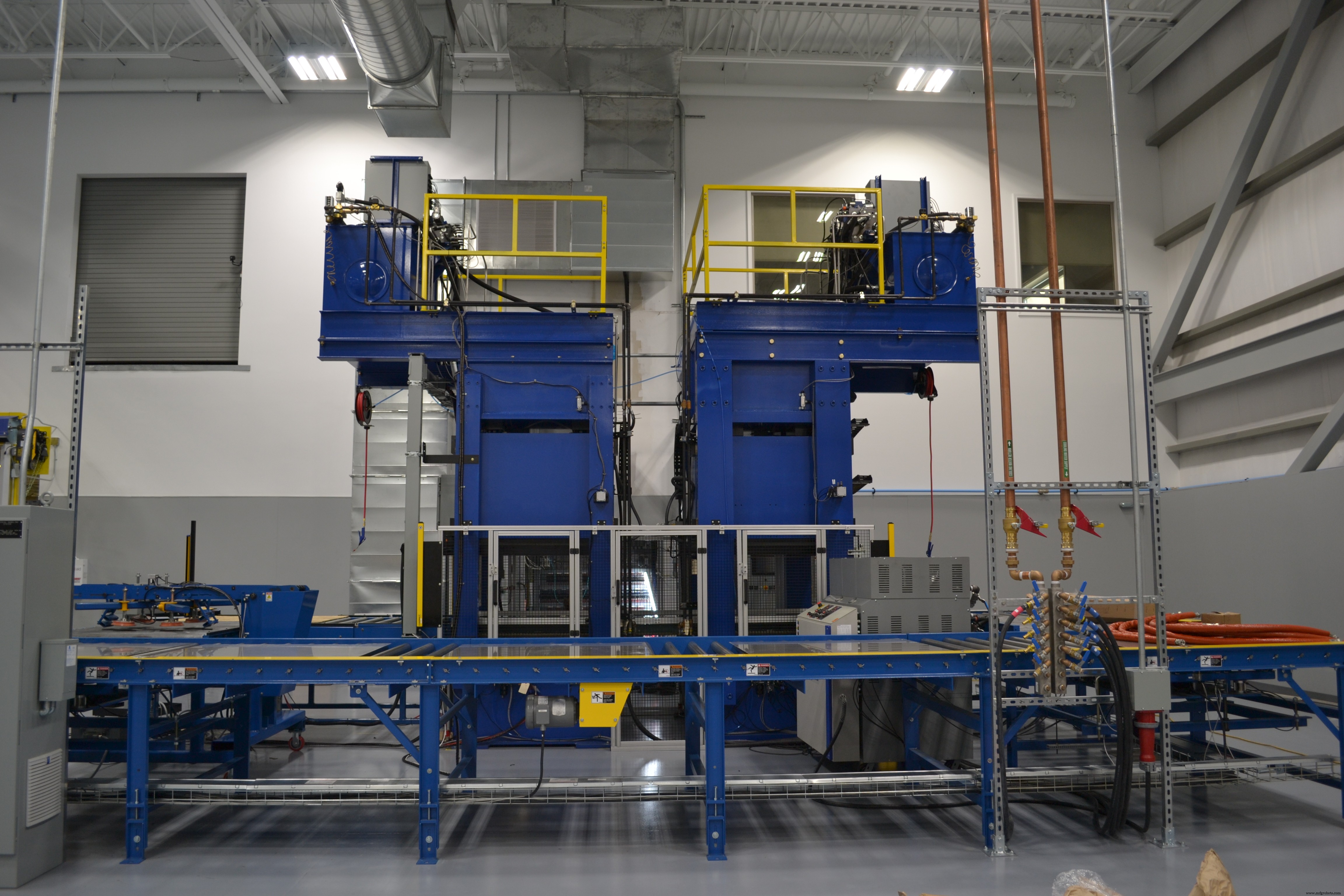
As pré-formas laminadas consolidadas são então processadas em uma célula de trabalho proprietária para formar a forma primária do suporte (Etapa 3). As inserções finais de fibra de carbono / PAEK são então cortadas dos espaços em branco usando um cortador de jato de água Flow International (Kent, Wash., EUA) (Etapa 4)
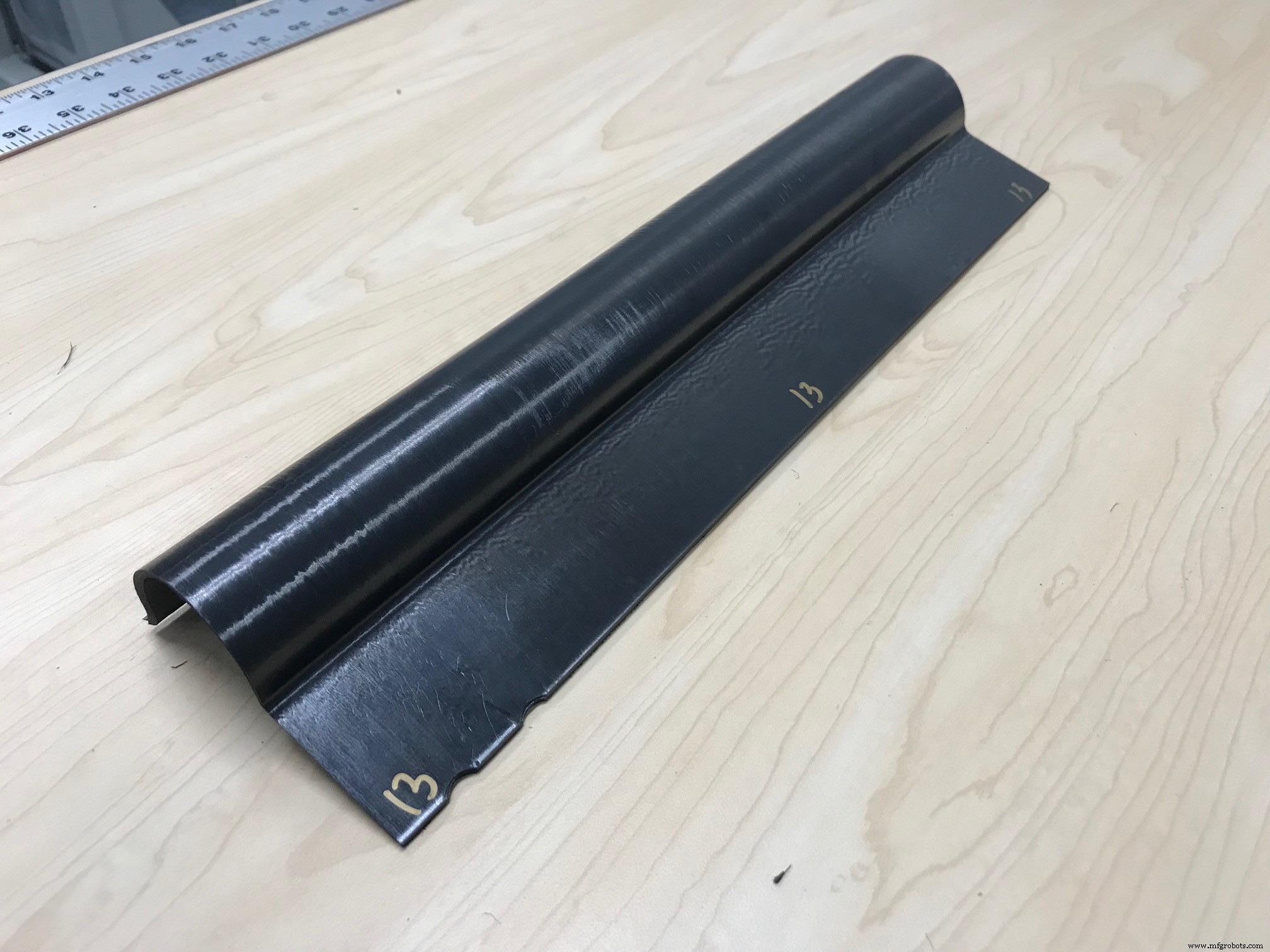
Etapa 3. Uma célula de trabalho proprietária forma a forma primária do suporte.
Ao determinar o tamanho do espaço em branco sob medida, Sourkes aponta que uma compensação deve ser deliberada para cada projeto. “Podemos dimensionar o laminado de modo que possamos retirar três ou quatro retângulos de um único bloco quadrado. Ao preparar uma peça bruta o maior que puder e, em seguida, cortá-la em pré-formas, você maximiza a proporção entre compra e venda; mas cortar as pré-formas significa mais tempo para operações de corte por jato de água. ” No projeto do suporte B, cada laminado consolidado é cortado em várias pré-formas
A seguir vem a etapa de sobremoldagem, que é realizada com uma máquina de moldagem por injeção de alta temperatura Engel (Schwertberg, Áustria) (Etapa 5). As inserções são colocadas em uma cavidade de moldagem por injeção que é então preenchida com PEEK fundido. As inserções são colocadas em uma cavidade de moldagem por injeção que é preenchida com PEEK fundido, que funde a camada superior dos laminados VICTREX AE 250 para criar um forte componente fundido.
Quando necessário, um componente é acabado por meio de usinagem em forma líquida. “Embora seja nosso objetivo moldar peças quase definitivas”, admite Sourkes, “muitas vezes é necessário algum nível mínimo de usinagem após o fato para limpar a geometria do processo”. A usinagem pode ser realizada com jato de água ou usinagem CNC.
Resultados inovadores
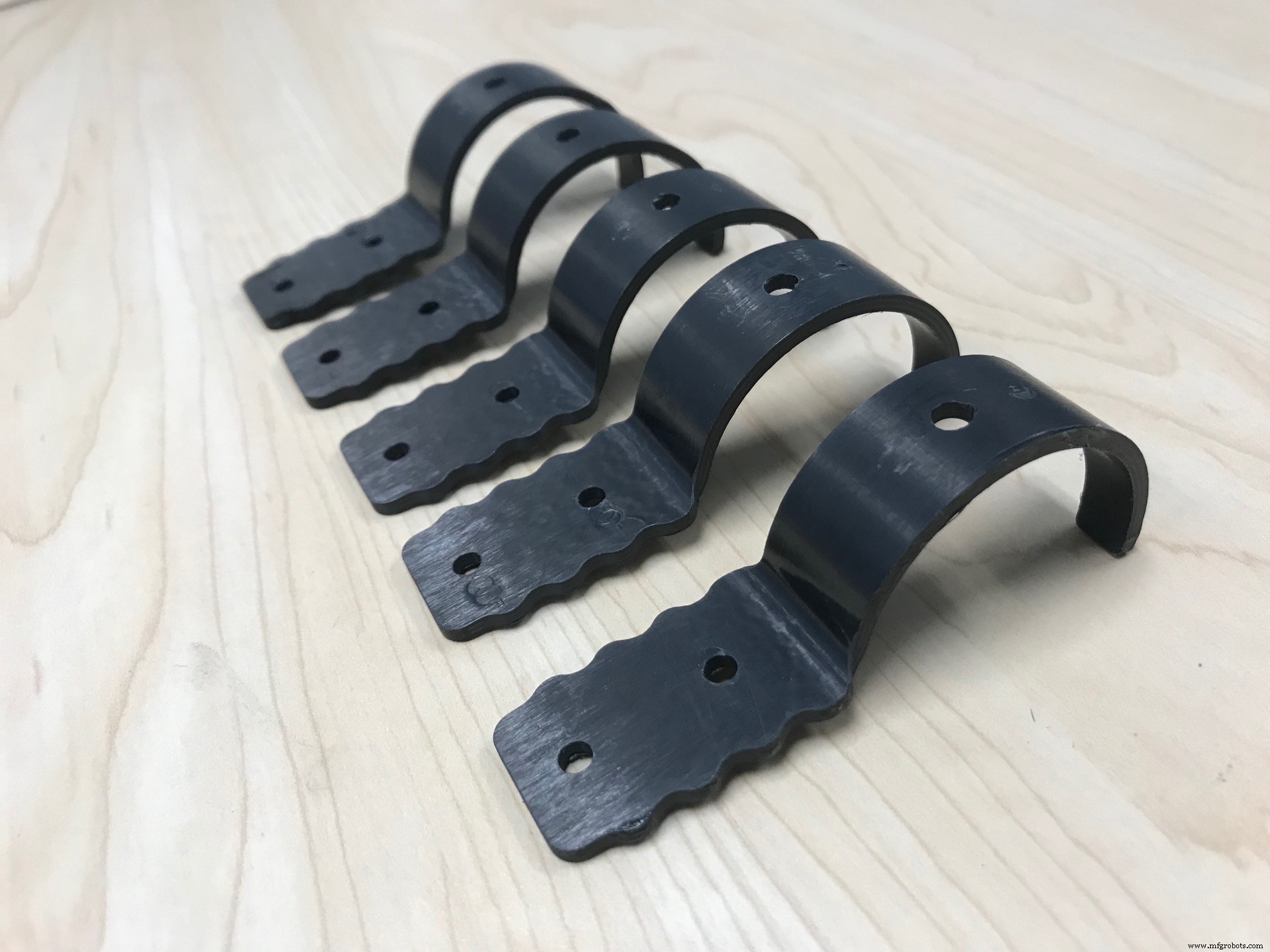
Etapa 4. Um cortador por jato de água da Flow International corta os insertos de fibra de carbono / PAEK dos blocos formados. Duas dessas inserções são usadas em cada suporte.
Na fabricação do suporte SFS intec, o processo de sobremoldagem híbrida TxV atinge tempos de ciclo de três minutos e uma relação de compra para voar de 1,06:1. “É o uso eficiente de materiais e o rápido processo de fabricação que nos permite produzir peças compostas termoplásticas de valor agregado e que possibilita a redução de custos do sistema em relação aos designs de metal existentes”, enfatiza Sourkes. “Efetivamente, estamos substituindo uma matéria-prima de baixo custo com uma alta taxa de compra para voar e um tempo de processamento significativo por uma solução de material de alta engenharia.” O resultado é uma economia de peso na faixa de 30 a 40% e economia de custos na faixa de 20 a 30% em uma substituição semelhante, ou seja, uma peça de reposição que segue as mesmas especificações geométricas e operacionais do componente existente. “A redução de peso, em particular, pode chegar a 60% quando temos a oportunidade de reprojetar completamente um sistema de peças”, observa ele.
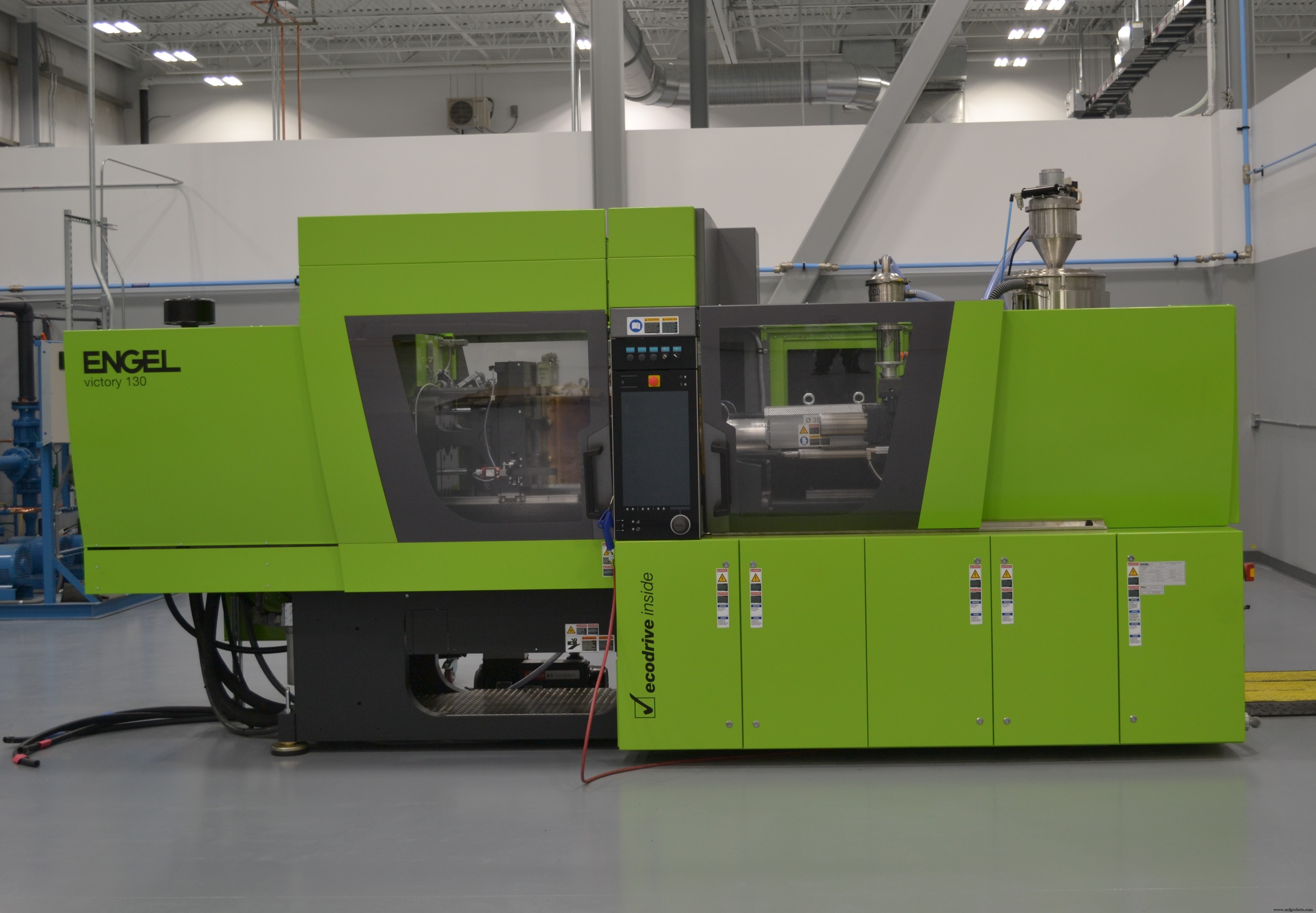
Etapa 5. Uma máquina de moldagem por injeção Engel otimizada para sobremoldagem híbrida PEEK completa a peça composta por sobremoldagem dos insertos.
O suporte de fibra de carbono / PAEK / PEEK também consolidou a contagem de peças:TxV e SFS concordaram em moldar por injeção um bico de extensão na parte inferior da peça na mesma operação usada para funcionalizar e adicionar outros recursos. Anteriormente, a ponta do spreader era feita de PEEK e então mantida no lugar por dois rebites. Assim, a consolidação resulta em uma contagem de peças reduzida e na eliminação de uma etapa de montagem.
A experiência das duas empresas que lançaram o TxV sem dúvida possibilitou o sucesso da sobremoldagem híbrida. Sourkes explica que, depois de desenvolver o material PAEK e a tecnologia de processamento, a Victrex primeiro explorou as oportunidades com os parceiros de negócios existentes. “No entanto, as empresas com experiência em moldagem por injeção não tinham experiência para trabalhar com compósitos reforçados com fibra contínua e vice-versa.” A Victrex e a Tri-Mack firmaram parceria por vários anos antes de formar a TxV em 2017 e construir o centro de excelência de composto de policetona desenvolvido para esse fim, que é altamente automatizado e projetado para produção em série de alta taxa.
Solicitado a comparar o processo e os resultados do TxV com uma abordagem de fabricação convencional, Sourkes observa que o suporte B não é compatível com as abordagens de fabricação de compósitos padrão. “Isso seria muito desafiador sem usinar o suporte de um tarugo composto - o que teria um custo proibitivo”, diz ele.
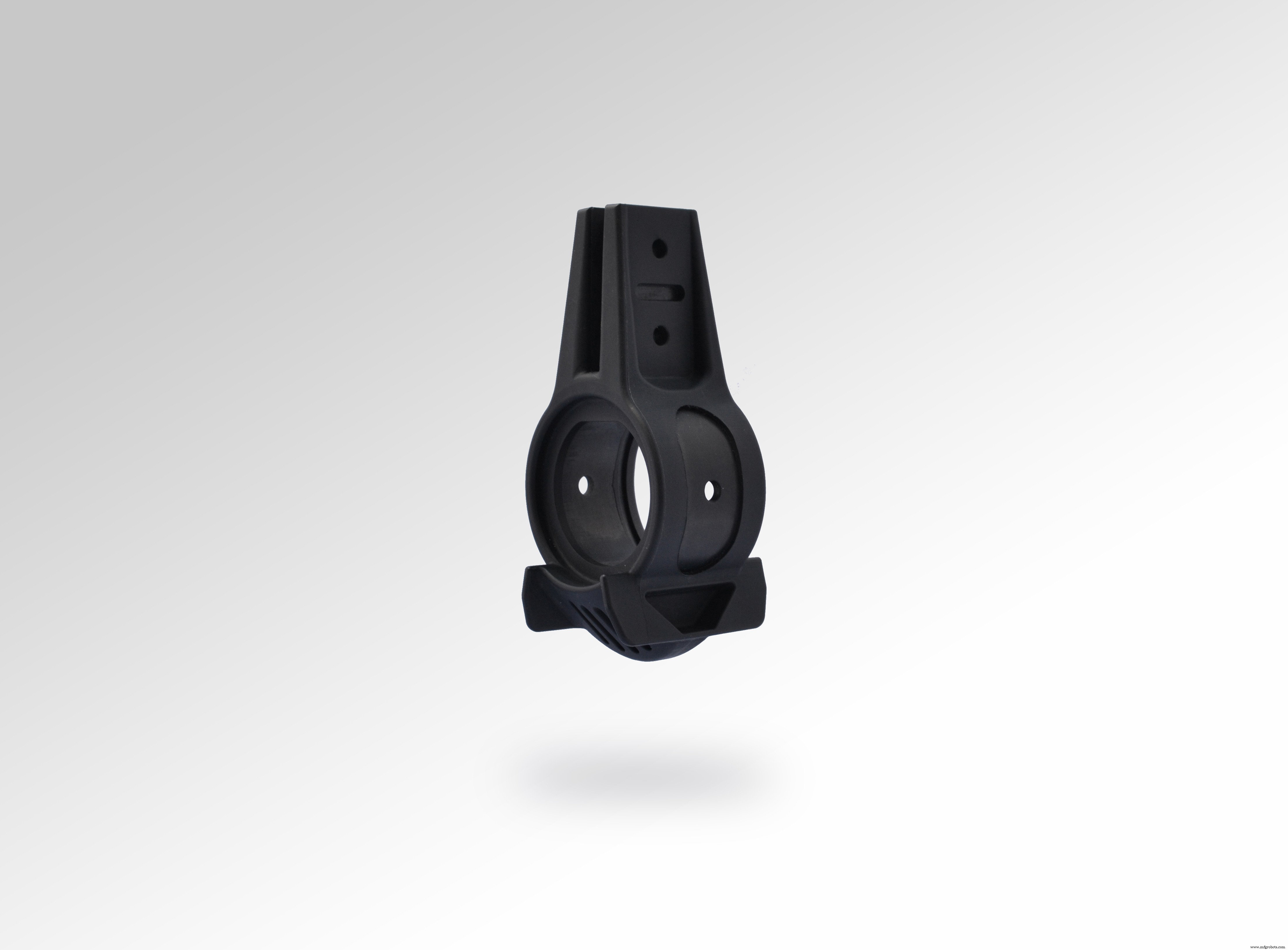
Etapa 6. O suporte B final é produzido com um tempo de ciclo de três minutos, uma proporção de compra para voar de 1,06:1 e economia de peso de 30 a 40%.
Qualifique-se e voe
Aproveitando a capacidade da SFS intec de executar a qualificação, as duas empresas procederam à certificação por meio de "design de pontos", o que significa que apenas esta geometria de peça em particular obtém a aprovação de voo. As peças foram produzidas e submetidas aos testes previstos no documento de qualificação. “Como a peça é um suporte para compartimento superior, as cargas operacionais são facilmente alcançadas”, observa Sourkes. “No entanto, os requisitos de desempenho vão além das cargas típicas e devem cobrir algumas manobras extremas de decolagem e pouso.” Como CW vai para a impressão, o pacote de qualificação foi enviado e está aguardando a aprovação final do custodiante de especificações. A TxV e a SFS intec esperam que a peça voe no início de 2020.
Assim que o suporte B for qualificado, o TxV será dimensionado para os volumes de produção. Enquanto a empresa está usando sua linha de sobremoldagem híbrida existente para produzir esses suportes, Sourkes enfatiza que a empresa tem um mandato duplo - tanto para fazer peças com a tecnologia quanto para apoiar os fabricantes da indústria interessados em adotar a tecnologia eles próprios. Em outras palavras, os fabricantes de compósitos podem adotar essa técnica de fabricação em suas próprias instalações.
Os suportes compostos, como o produto SFS intec, têm o potencial de conquistar um mercado bastante grande para esses tipos de componentes. Aeronaves comerciais usam milhares de suportes e acessórios de sistema, sendo responsáveis por custos significativos e contribuições de peso para a aeronave em geral. “Estamos convencidos de que os componentes termoplásticos terão um papel cada vez mais importante na fabricação de aeronaves”, antecipa Costabel.
fibra
- MMF # 5:Um guia para incorporar componentes em peças impressas em 3D
- Uma nova maneira revolucionária de fabricar peças de metal
- Apresentando nosso novo material Markforged:Onyx
- AT&T, Tech Mahindra colaboram na nova plataforma de IA de código aberto
- LANXESS comissiona duas novas linhas de produção para compósitos termoplásticos Tepex
- Compósitos termoplásticos de aceleração na indústria aeroespacial
- Nèos International estabelece novo HQ, instalação de compósitos no Reino Unido.
- Como fabricar componentes mecânicos de precisão
- Entendendo os componentes de alta precisão
- Acabamento de peças e componentes