5 maneiras que a impressão 3D complementa a manufatura tradicional
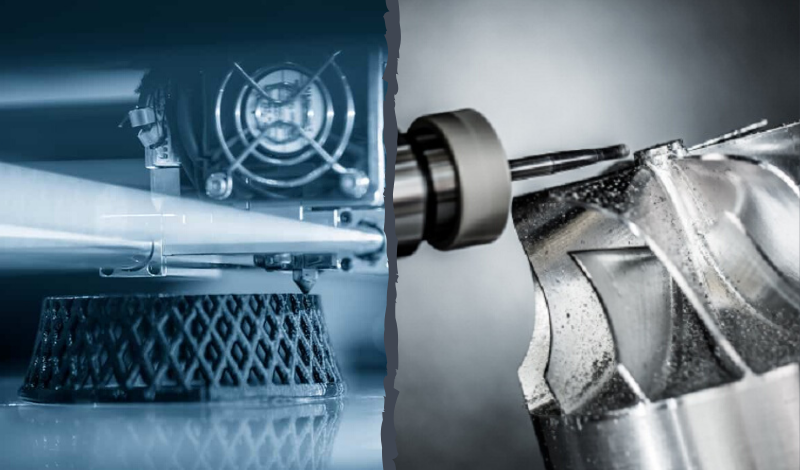
A impressão 3D foi prevista para substituir as tecnologias de manufatura tradicionais. No entanto, o verdadeiro poder da tecnologia pode residir não em competir com, mas em complementar e aumentar os métodos convencionais de fabricação.
Para apoiar esta afirmação, a seguir estamos explorando 5 maneiras principais de como a impressão 3D pode apoiar a manufatura tradicional.
1. Impressão 3D de moldes de injeção de melhor desempenho
A moldagem por injeção envolve o processo de derreter e injetar material plástico em uma ferramenta de molde especial, com a forma do objeto desejado. Quando o plástico endurece, ele assume a forma da cavidade do molde. A moldagem por injeção é a melhor maneira de produzir em massa produtos e peças complexas e altamente precisas.
No entanto, o processo também apresenta alguns desafios. Por exemplo, as peças moldadas por injeção são resfriadas pela construção de canais - essencialmente, passagens localizadas perto da superfície do molde - ao longo dos moldes. Esses canais são normalmente linhas retas, o que às vezes pode resultar em resfriamento desigual, aumentando o risco de deformação da peça. O resfriamento eficiente pode ser alcançado com canais de resfriamento conformados, que estão em conformidade com a forma da peça. No entanto, esses tipos de canais são difíceis de produzir usando métodos convencionais, tornando a impressão 3D uma alternativa atraente para a criação de moldes de injeção. A criação de moldes com canais de resfriamento conformados não só ajuda a aumentar a qualidade das peças moldadas, mas também ajuda a reduzir significativamente o tempo de resfriamento.
A impressão 3D ajuda a otimizar a linha de moldagem por injeção
Um caso em questão é a Alfred Kärcher GmbH &Co. KG, uma empresa que vende milhões de suas lavadoras de alta pressão K2 em todo o mundo, todos os anos. Ao tentar atender a essa demanda, a empresa enfrentou um gargalo na produção, sendo necessário aumentar a produção das carcaças das lavadoras.
Em vez de adquirir mais máquinas de moldagem por injeção, a Kärcher começou a buscar maneiras de aumentar a produtividade das máquinas existentes. A empresa encontrou a solução na impressão 3D de metal.
Kärcher recorreu à LBC Engineering, parte da Renishaw GmbH, que descobriu que o tempo do ciclo de moldagem era afetado pela ineficiência do processo de resfriamento. Os moldes de revestimento apresentavam sistemas de resfriamento tradicionais, perfurados em linhas retas, criando pontos quentes que aumentavam o tempo de ciclo.
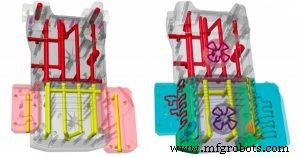
A LBC Engineering modificou o design do molde criando dois núcleos impressos em 3D para fornecer resfriamento conformado nos pontos de acesso identificados.
Canais de resfriamento conformados impressos em 3D ajudaram a reduzir a temperatura da parede nos moldes de 100 ° C para 70 ° C, encurtando o tempo de resfriamento de 22 para 10 segundos, uma redução de 55 por cento.
Junto com alguns ajustes nos componentes periféricos, como o sistema de alimentação e manuseio de material, o tempo de ciclo para tripas caiu de 52 para 37 segundos. A impressão 3D proporcionou a maior parte dessa redução, permitindo que a Kärcher aumentasse a produtividade de sua linha e atingisse as metas de produção de invólucros. Em outro exemplo, o profissional de moldagem por injeção, Pat Zaffino, desenvolveu uma tecnologia de deposição robótica multicamadas que imprime canais de resfriamento conformados na superfície de moldes de injeção em 3D.
No início deste ano, Zaffino lançou uma nova empresa, Conformal Cooling Solutions Inc. (CCS), para promover as vantagens do uso de canais de resfriamento conformados.
'Criação de canais de resfriamento conformados que seguem a forma da cavidade e do núcleo promovem uniformidade de temperatura nos materiais plásticos que estão sendo moldados, e os moldadores que usam essa tecnologia estão obtendo resultados surpreendentes:tempos de ciclo reduzidos, qualidade aprimorada das peças de plástico e - acima de tudo - redução de custos ', disse ele em uma entrevista com canplastics.com.
Conforme a tecnologia se torna mais barata e fácil de adotar, os moldes com canais de resfriamento conformados impressos em 3D podem se tornar um novo padrão na indústria.
2. Padrões de impressão 3D para fundição de investimento
Fundição de investimento usa padrões de cera descartáveis e conchas de cerâmica para criar projetos de peças complexos e detalhados. Tradicionalmente, esses padrões são moldados por injeção. No entanto, o custo dos moldes de injeção pode chegar a vários milhares de dólares, com prazos de entrega que variam de uma a quatro semanas. Isso torna o processo proibitivo para pessoas que podem não ter tanto capital ou prazos curtos para entregar as peças.
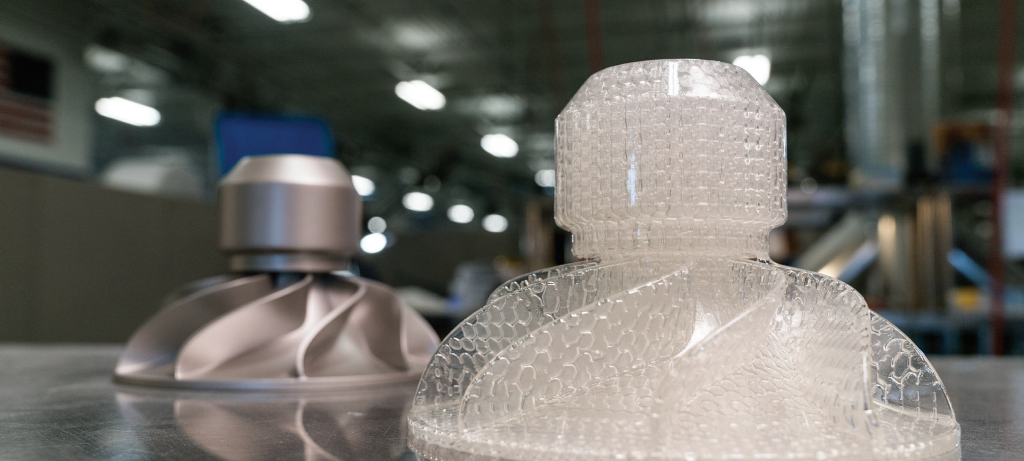
Por este motivo, as empresas podem optar por padrões de impressão 3D em um material adequado para fundição de investimento. Muitos fabricantes de impressoras 3D desenvolveram materiais imprimíveis 3D especificamente para fundição, incluindo cera, resinas fundíveis e alguns termoplásticos, com base em PLA e ABS.
Esses materiais são normalmente usados com Estereolitografia (resinas) e FDM ( plásticos), criando padrões altamente precisos com excelentes características de queima.
Outra vantagem desta abordagem é o risco relativamente baixo envolvido em experimentá-la. Os padrões podem ser impressos em 3D usando impressoras 3D de mesa profissionais, que custam menos de US $ 5.000, uma fração do custo de um equipamento de impressão 3D industrial mais caro.
Acelerando os prazos de entrega de peças fundidas com impressão 3D
Padrões de fundição de investimento impressos em 3D são cada vez mais usados para criar joias personalizadas com designs complexos e prazos de entrega mais curtos. Em um exemplo, a empresa canadense de joalheria Vowsmith - especializada em anéis personalizados - conseguiu reduzir seus tempos de produção e entrega em 50% ao integrar as impressoras 3D de cera da 3D Systems em seu fluxo de trabalho. Em uma única impressão, a empresa produziu entre 35 e 40 padrões de anéis personalizados, prontos para fundição.
A tecnologia também é cada vez mais aplicada em fundições, para criar padrões complexos para uma ampla gama de aplicações industriais. Por exemplo, a Invest Cast, Inc. integrou recentemente a nova solução de fundição digital da 3D Systems em sua produção de moldes.
A capacidade de fazer peças fundidas finais sem usinar um molde deu aos clientes da Invest Cast a liberdade de teste várias iterações de forma rápida e econômica, permitindo, em última análise, que cheguem a melhores peças finais.
De acordo com a Invest Cast, a impressora 3D ProJet MJP 2500 IC da 3D Systems reduziu significativamente o processo de fundição de investimento. . A tecnologia permite que a empresa passe do modelo ao metal em 2 a 5 dias, o que é inferior ao prazo médio de aproximadamente 6 a 12 semanas com os moldes de fundição de investimento.
3. Aumentando a produtividade com ferramentas de corte impressas em 3D
A impressão 3D pode ser usada para criar ferramentas de corte - pequenas pastilhas feitas de metal duro que removem o material do caminho da ferramenta programado. Alguns materiais de alto desempenho, como aços de ultra-alta resistência, titânio e ligas de níquel, podem ser difíceis de usinar e podem causar o desgaste rápido da ferramenta. Ferramentas de impressão 3D com geometrias personalizadas, com canais de resfriamento embutidos que podem efetivamente remover o excesso de calor gerado perto da zona de corte durante a usinagem, podem aumentar a vida útil e o desempenho da ferramenta.
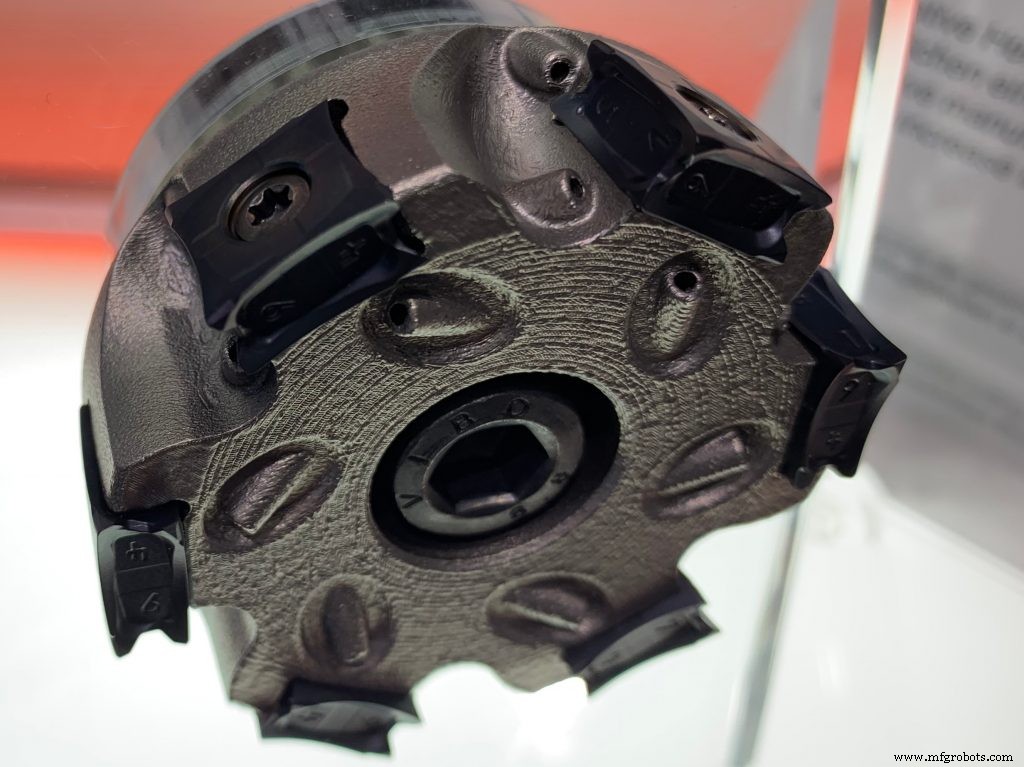
O especialista em ferramentas, LMT Tools Inc., usou a tecnologia para criar passagens internas de refrigeração em um corpo de ferramenta de fresamento, anteriormente com furos retos. A liberdade da impressão 3D de fornecer canais curvos permite que a ferramenta de fresamento da LMT forneça refrigerante precisamente onde é necessário. A LMT diz que o corte de teste mostrou uma melhoria na vida útil da ferramenta de 50 por cento no fresamento de titânio, graças a essa mudança de projeto.
Grupo Komet aumenta a produtividade da ferramenta com impressão 3D
Um dos principais fornecedores mundiais de ferramentas de corte de precisão, o Komet Group, também está aplicando a impressão 3D de metal na fabricação de ferramentas.
Usando liga de alumínio e tecnologia baseada em laser do especialista britânico Renishaw, Komet foi capaz de introduzir mais arestas de corte na ferramenta e otimizar sua geometria para aumentar a produtividade da ferramenta.
Por exemplo, os engenheiros otimizaram os canais de refrigeração da ferramenta para garantir que cada aresta de corte recebesse refrigerante precisamente por meio de um canal separado. Graças a essas melhorias no projeto, o tempo de usinagem por unidade pode ser reduzido em até 50 por cento.
AM também oferece a possibilidade de reduzir o peso do componente, uma vez que o material só pode ser usado onde for necessário para a ótima funcionalidade do componente. Também é relatado que supera os métodos de produção convencionais, em termos de tempo de entrega, para quaisquer ferramentas especiais ou experimentais necessárias para os clientes da Komet.
Impressão 3D de uma cabeça de fresagem mais eficiente
Além disso, o fabricante sueco de sistemas de ferramentas, Sandvik Coromant, lançou recentemente uma nova fresa com cabeça de metal impressa em 3D. Inédito para a empresa, o componente marca um movimento em direção ao envolvimento da empresa na impressão 3D para produção de uso final.
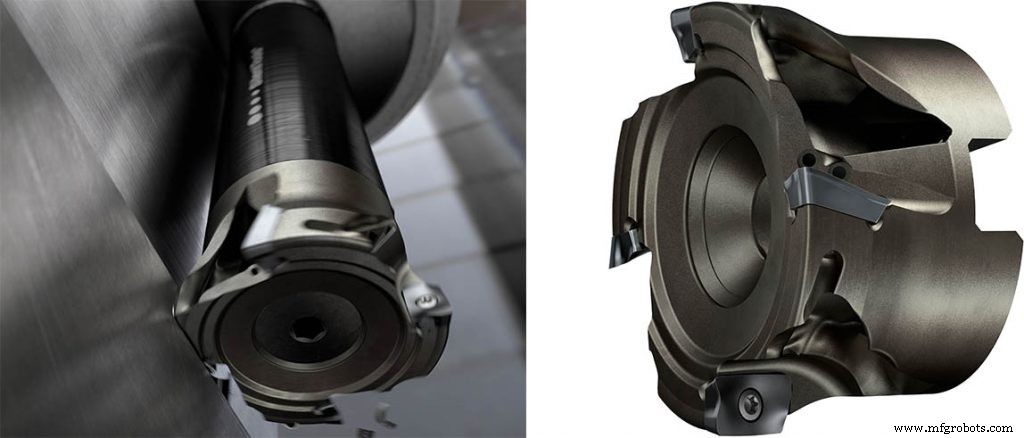
A nova CoroMill 390 leve, produzida pela Sandvik Coromant, é uma cabeça de fresamento de metal baseada no projeto da CoroMill 390. A ferramenta, produzida com o pó Osprey de liga de titânio da Sandvik, foi desenvolvida especificamente para superar os problemas de vibração durante a fresagem de metal com longos balanços.
Tais características são um requisito comum de componentes usados nas indústrias aeroespacial e de petróleo e gás. Cavidades profundas em uma peça usinada CNC podem ser comprometidas por vibração, levando a uma produção mais lenta, vida útil mais curta da ferramenta e acabamento superficial pobre. Quando usado em combinação com os adaptadores de fresamento Silent Tools da empresa, a empresa relata que a ferramenta impressa em 3D pode aumentar a produtividade de usinagem em 50 por cento.
4. Reparando ferramentas gastas e danificadas
A impressão 3D pode ser usada não apenas para criar novas ferramentas e moldes, mas também para reparar ferramentas danificadas. As empresas aeroespaciais, de construção naval e de bens industriais estão começando a usar processos de AM, como a Deposição Direta de Energia (DED), para remanufaturar componentes de volta à sua forma original.
Também conhecido como revestimento a laser, o DED usa um laser para gerar uma poça de fusão na superfície do componente. O material é então adicionado à poça de fusão na forma de pó ou arame. As partículas derretidas se fundem e solidificam, enquanto o bico é manipulado para adicionar a estrutura desejada ao componente.
No início deste ano, um consórcio de 7 empresas e organizações do Reino Unido lançou um projeto de £ 1,2 milhão, chamado DigiTool , para permitir o reparo de baixo custo de ferramentas e matrizes usando tecnologias AM.
Com a impressão 3D, as empresas do setor de ferramentas e matrizes podem superar os custos de substituição e reparo de matrizes, com potencial para acelerar o processo de manutenção. Isso ajudará as empresas a economizar em custos e materiais, melhorando simultaneamente sua sustentabilidade com menos desperdício.
Reparo mais rápido de uma inserção do molde
Ferramenta alemã e empresa de fabricação de moldes, HWF, usou a impressão 3D para reparar uma inserção de molde. Um dos desafios que a HWF enfrentou foi o de construir uma estrutura, medindo 300 x 20 x 20 mm, em um material de molde típico.
No passado, estruturas como esta eram construídas usando um método de revestimento manual a laser alimentado por fio para evitar os riscos de trincas, deformações e propriedades metalúrgicas alteradas. No entanto, o soldador pode levar entre 60 e 80 horas para concluir a tarefa.
Hoje, a HWF usa a tecnologia DED da OR Laser, que permite criar a mesma estrutura aplicando camadas de 250 µm de espessura, a uma taxa de 5000 mm³ por hora. O tempo de produção, portanto, pode ser reduzido para 24 horas.
Graças a este processo, o material de base também é afetado muito menos do que antes, reduzindo muito o risco de rachaduras e rebaixamento do material, muitas vezes causados por métodos de reparo convencionais.
5. Alcançando mais flexibilidade com processos híbridos
Combinar capacidades aditivas e subtrativas em um sistema híbrido é outra maneira que a AM pode complementar a manufatura tradicional. Nesse cenário, as tecnologias aditivas e subtrativas podem abrir uma gama de oportunidades para uma manufatura aprimorada e completa.
A manufatura híbrida potencializa os recursos mais valiosos de ambas as tecnologias:a complexidade geométrica de AM e a alta precisão dos métodos subtrativos. Isso significa que uma peça pode ser criada e usinada de forma aditiva em uma única operação, acelerando o processo de produção.
Vários sistemas híbridos comerciais já estão disponíveis no mercado. Por exemplo, DMG MORI combina DED com capacidade CNC de cinco eixos em seu sistema de manufatura híbrido. Enquanto isso, Matsuura e Sodick adotaram uma abordagem diferente, combinando a tecnologia Powder Bed Fusion (PBF) e a capacidade CNC em seus sistemas de manufatura híbridos. Para acompanhar a concorrência, a DMG MORI respondeu recentemente com seu próprio PBF e sistema híbrido CNC.
Além de um sistema híbrido autônomo, há também a opção de reformar um centro de usinagem CNC existente com o cabeçote de deposição a laser Ambit de alimentação de pó da Hybrid Manufacturing Technologies.
As empresas também podem adicionar uma combinação de recursos de alimentação de pó e arame a uma máquina CNC, com a tecnologia 3D Hybrid. Isso permite que um sistema subtrativo convencional seja convertido em um sistema de manufatura híbrido com custo e esforço relativamente mínimos.
Embora a promessa da manufatura híbrida seja cativante, apenas começamos a aprender como essa tecnologia pode ser aplicado de forma eficiente e viável.
Abraçando a impressão 3D como uma tecnologia complementar
A impressão 3D pode se tornar um ativo valioso para os fabricantes, que buscam otimizar seus processos de fabricação tradicionais. A tecnologia pode ser usada para produzir moldes de alto desempenho e padrões de fundição complexos, bem como aumentar a eficiência das ferramentas de usinagem. Além disso, as máquinas híbridas podem oferecer às empresas maior liberdade e flexibilidade no projeto e na fabricação.
Portanto, em vez de ver a manufatura aditiva como uma tecnologia concorrente, os fabricantes deveriam adotá-la como mais uma ferramenta na caixa de ferramentas e avançar para os benefícios que ela oferece.
impressao 3D
- 5 Benefícios da impressão 3D na manufatura
- 4 maneiras que a impressão 3D está transformando a indústria médica
- 8 maneiras que a impressão 3D industrial está transformando a manufatura
- 6 maneiras de reduzir custos de fabricação com impressão 3D
- 6 maneiras de reduzir o custo da impressão 3D
- A impressão 3D está em toda parte
- 5 maneiras pelas quais a impressão 3D está mudando a indústria automotiva
- Fabricação aditiva em medicina e odontologia
- O futuro da impressão 3D na fabricação
- A impressão 3D é o futuro da manufatura?