Nova tecnologia impulsiona o crescimento da soldagem robótica
É o momento certo para automatizar sua operação de soldagem? Preocupado com quanto tempo você pode manter seus soldadores experientes? Precisa aumentar seu rendimento, mas não vê como com a força de trabalho disponível? Desafiado por materiais mais resistentes? Uma variedade de avanços técnicos torna relativamente fácil resolver esses problemas automatizando sua operação de soldagem, com um retorno surpreendentemente rápido.
Três vezes mais rápido
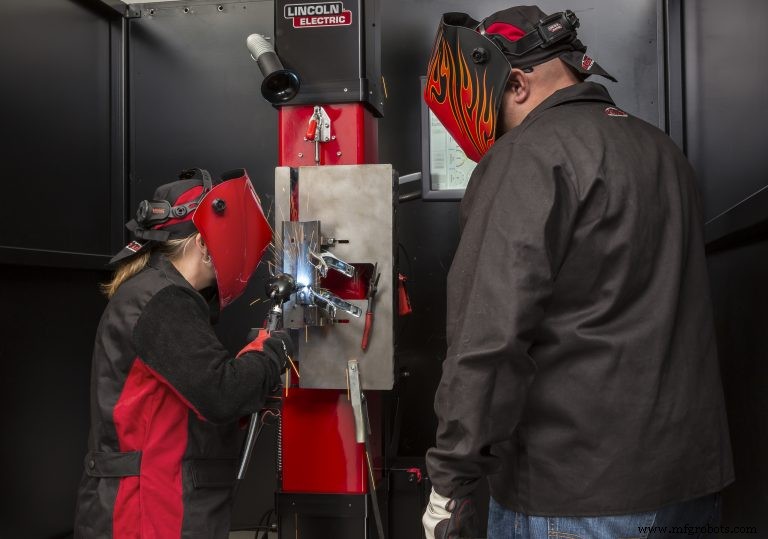
Existem duas grandes categorias de soldagem automatizada, a chamada automação “fixa” e soldagem “flexível” (ou robótica). A automação fixa geralmente é específica para a aplicação e é melhor quando a geometria da peça e a solda são muito simples. Por exemplo, geralmente é a melhor solução para soldagem de tubos. Mas para a maioria das aplicações industriais e qualquer coisa complexa, a soldagem robótica é ideal e é o foco deste artigo.
Como Jason Lange, gerente de vendas internas da Lincoln Electric Co. (Cleveland), explicou:“O principal objetivo de um robô é ajudar na repetibilidade de uma solda. O número dois é reduzir o abuso no soldador. Mover peças durante todo o dia e rastejar sob diferentes acessórios é desgastante para um ser humano. Os robôs ajudam na ergonomia.”
É duplamente importante facilitar os soldadores porque eles estão se tornando mais difíceis de encontrar. “Existem muitas escolas de tecnologia em todo o país investindo em programas de soldagem para tentar ajudar a preencher essa lacuna”, continuou Lange. “Mas em qualquer dia, o número de pessoas que se aposentam excede as substituições recebidas, criando um vazio. A soldagem robótica ajuda a preencher esse vazio.”
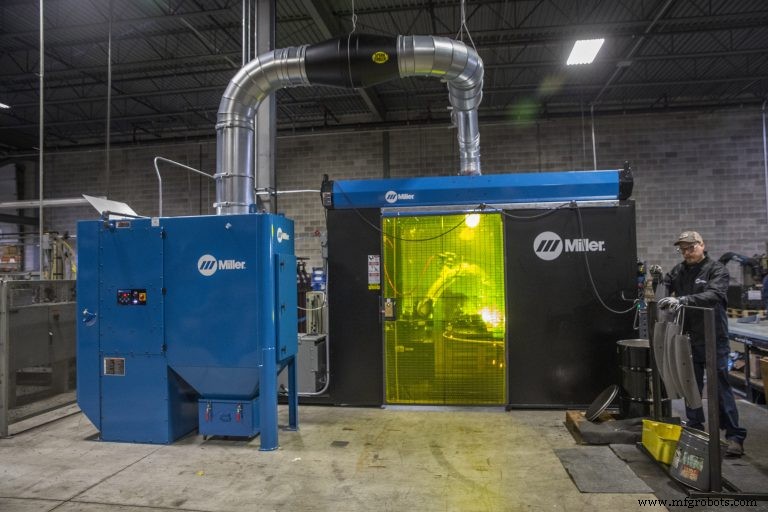
Ao mesmo tempo, “o retorno de um sistema robótico é tipicamente muito melhor do que você imagina”, explicou Erik Miller, gerente de desenvolvimento de negócios – grupo de laser da Miller Electric Mfg. Co. (Appleton, WI). “Um sistema de robô fará tantas peças quanto três soldadores. Você está economizando dois salários por turno e o custo médio das células pré-projetadas é de US$ 100.000 a US$ 120.000. Ele se paga em cerca de um ano. Normalmente, se você pode automatizar um processo e obter retorno em menos de um ano, isso é algo que você faz imediatamente. Se forem dois anos, é algo que você deve considerar seriamente.”
Portanto, a automação robótica é uma grande ajuda para aumentar o rendimento. Mas as fontes entrevistadas para este artigo enfatizaram que não é um substituto para mão de obra qualificada. “Você ainda precisa de um soldador de qualidade para operar esse robô”, como disse Lange.
Alterar materiais é outro motivo para automatizar
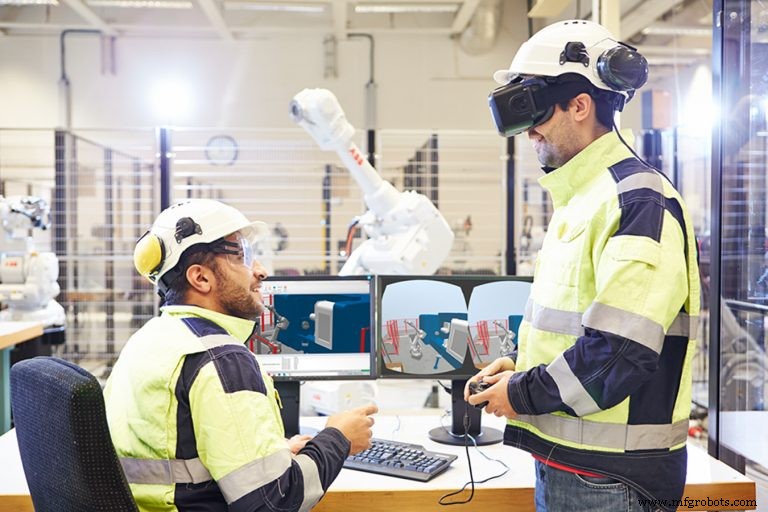
As mudanças nos materiais de trabalho nos últimos dez anos levaram a melhorias na soldagem, muitas das quais são impossíveis de aplicar manualmente, como a soldagem a laser, de acordo com Erwin DiMalanta, diretor da linha de negócios de soldagem e corte da ABB Robotics (Auburn Hills, MI) . “Os fabricantes de tudo, de veículos de mineração a automóveis, estão usando materiais diferentes para reduzir custo e peso e acomodar diferentes soluções de trem de força”, disse ele. “Os fabricantes automotivos mudaram para aços de alta resistência e ultra-alta resistência, que possuem propriedades metalúrgicas tornando-os mais fortes, mais leves e mais resistentes à corrosão, mas com alta conformabilidade e soldabilidade. Isso está mudando drasticamente a forma como as estruturas metálicas são projetadas, formadas e montadas.” Enquanto os fabricantes podem ter usado matrizes de estampagem tradicionais para cortar recursos na peça, agora eles estão usando processos de estampagem a quente e tecnologias automatizadas de laser para formar e cortar as peças.
“Outro exemplo é a mudança para o alumínio para mais aplicações”, disse DiMalanta. “Dependendo do carro, até 90% da carroceria pode ser de alumínio agora. Devido à sua maior condutividade, você precisa de mais corrente elétrica para soldar alumínio e corrente é sinônimo de calor. No entanto, vamos usar materiais de calibre mais finos. Em alguns veículos, os materiais têm cerca de 1 mm de espessura. Então, como você lida com essas tendências que estão indo em direções opostas?”
A resposta é tecnologia aprimorada para controle eletrônico e mecânico de soldagem a arco e aumento do uso de soldagem a laser. Para soldagem a arco, DiMalanta disse que “as fontes de energia agora são extremamente avançadas e controladas eletronicamente. A deposição de material em uma poça de fusão é cuidadosamente controlada, com formas de onda personalizadas.” Miller acrescentou que essas formas de onda especiais “controlam a entrada de calor nas peças, o que pode reduzir a distorção e também melhorar a aparência cosmética das soldas”.
Ele também apontou para um método mecânico chamado Active Wire da Panasonic. “É uma alimentação de arame bidirecional em que o arame avança para criar o curto e depois inverte para fora da poça, repetindo essa ação do tipo máquina de costura a 120 Hertz. Isso reduz a entrada de calor e também reduz bastante os respingos. Também melhora a consistência do arco em cada solda. É muito popular para soldagem de alumínio e para soldagem de chapas finas.”
Quanto mais leve o componente, mais avançados os materiais devem se tornar para permitir estruturas complexas, mantendo a resistência, disse DiMalanta. “Os robôs e seus sistemas de software avançados ajudam a conectar os processos de manuseio desses materiais com o caminho do robô.”
Soldagem a laser uma opção atraente
Com sua capacidade ultrarrápida de soldar uma ampla variedade de materiais (incluindo materiais diferentes), o laser é provavelmente a maior coisa que aconteceu na soldagem em décadas. E como diz Masoud Harooni, engenheiro sênior de tecnologia avançada de soldagem a laser da Trumpf Inc. (Hoffman Estates, IL), “a maior novidade na soldagem a laser nos últimos anos é a queda nos preços do laser.
“Os sistemas de soldagem a laser são mais fáceis de controlar”, continuou Harooni. “Você seleciona uma potência e uma velocidade. Uma vez ajustado, você processa a peça inteira com poucos respingos. Na soldagem a arco, você deve manter o arco e os parâmetros de soldagem são sensíveis a qualquer alteração na distância entre a tocha e a peça de trabalho. Diferentes partes da [peça de trabalho] requerem mais corrente, ou menos corrente, e isso causa menos estabilidade do processo. Embora os circuitos de feedback nos sistemas modernos de soldagem a arco sejam muito bons, esses sistemas nunca são perfeitamente ajustados. Os componentes soldados a laser requerem muito menos pós-processamento do que os componentes soldados a arco, que geralmente precisam ser retificados. Você também tem o problema de lidar com os respingos e precisar limpar o bico em sistemas de soldagem a arco.”
Talvez mais importante, a soldagem a laser pode obter uma solda mais profunda sem danos causados pelo calor, mesmo em materiais como alumínio e magnésio que seriam suscetíveis a rachaduras ou porosidade com soldagem a arco. Harooni explicou que isso ocorre porque o laser pode atingir uma densidade de potência de 108 watts por centímetro quadrado. Isso gera um buraco de fechadura, uma área oca profunda criada pela vaporização do metal da peça de trabalho. À medida que o feixe de laser se move ao longo da peça, ele mantém esse minúsculo buraco de fechadura cercado por uma poça derretida, enquanto o material por trás se solidifica.
“Você obtém uma solda forte e profunda sem entrada de calor extremo na peça”, disse ele. “A soldagem a arco não tem a densidade de potência, então a única maneira de obter uma solda mais profunda é aumentar a entrada de calor. As propriedades mecânicas das peças soldadas que têm menor aporte de calor e menos distorção são muito melhores do que as peças com maior aporte de calor.”
Miller afirmou que “o impacto inicial da soldagem a laser foi na soldagem automotiva, devido ao alto volume e [vantagens técnicas]. Os fabricantes de chapas metálicas também devem considerar a soldagem a laser. Os benefícios reais estão na substituição da soldagem por pontos de resistência, que pode ser um desafio para a fabricação de médio a baixo volume. A fixação pode ser difícil, pois o acesso é necessário para o lado superior e inferior da peça, enquanto a soldagem a laser requer apenas acesso pelo lado superior, por isso é mais fácil de automatizar. Você também pode usar um robô de carga útil menor para soldagem a laser, juntamente com uma óptica fixa simples.”
Comparado a um grande robô de carga útil com um braço forte carregando uma grande ferramenta com dois eletrodos, os fabricantes agora podem usar um robô de oito kg mais seguro, montar um cabeçote de processo nele e automatizar a soldagem por pontos de resistência com relativa facilidade.
“A outra área em chapas metálicas onde a soldagem a laser é benéfica é na fabricação de caixas”, disse ele. “As soldas de cantos externos que exigem uma aparência cosmética e que exigem pouco ou nenhum acabamento metálico posterior são uma área em que vimos muito interesse.”
De acordo com Miller, o laser oferece uma boa solução em peças onde o acesso é limitado. Um laser requer apenas linha de visão para fazer a solda, enquanto em uma aplicação de soldagem a arco o robô precisa mover uma tocha volumosa dentro e ao redor das peças, o que pode ser muito difícil. “Na soldagem a laser, geralmente estamos a 500 mm de distância da peça de trabalho. É como atirar com uma arma de raios. O laser também tem velocidades de processamento muito mais altas e menor entrada de calor geral na peça, o que reduz a distorção. É uma ferramenta perfeita para soldagem autógena.”
A desvantagem da soldagem a laser, explicou Harooni, é que você “tem que garantir que praticamente não haja folga entre os componentes ou usar uma linha de fusão, que combina a soldagem a laser com a assistência do fio, na qual você derrete o fio na piscina para que você pode cobrir a lacuna. Mas a soldagem a laser é muito mais rápida que vale a pena o investimento extra na fixação. Por exemplo, se você está fazendo 50 peças por dia com soldagem a arco robótica, a soldagem robótica a laser pode produzir 300, 500 ou até milhares da mesma peça em um dia.”
Entrando na automação de soldagem
Mergulhar na automação de soldagem é mais fácil do que nunca. Primeiro, os principais players oferecem software de configuração off-line que programa o próximo trabalho em um PC com alto grau de realismo, transfere esse programa para o robô e inicia a soldagem. A ABB ainda usa técnicas de realidade virtual para permitir que os usuários “colaborem” com equipamentos de soldagem robóticos.
“Você pode literalmente pegar o robô pelo pescoço, por assim dizer, e direcioná-lo como faria com um cachorro na coleira”, explicou DiMalanta. “Isso pode ser muito mais intuitivo do que usar um teach pendant.”
Segundo, esses sistemas podem ter mecanismos que se adaptam automaticamente às mudanças de posição de uma peça para outra e monitoram a qualidade da solda.
Como explicou David Schaefer, especialista em produtos da Miller Electric, “Existem vários tipos de sensores que lidam com mudanças na localização das juntas. Um é simplesmente o sensor de toque e o outro é o rastreamento de costura através do arco. Ao usar o sensor de toque, o robô pode descer e usar seu fio de solda a arco para sondar a peça. Ele verifica o delta entre o local programado e o local real para basicamente se reprogramar.
“No rastreamento de costura através do arco, quando você tece através de uma junta, como com uma solda de filete ou uma solda de sobreposição, se for um material grosso o suficiente, ele detecta a mudança na amperagem e determina quando está na junta e quando está fora de a junta e, em seguida, segue essa solda enquanto ela está soldando”, continuou Schaefer. “Você também tem a opção de usar ótica a laser em vez de sensor de tipo de fio, mas é a mesma ideia básica.”
Lange, da Lincoln Electric, disse que “outra maneira de fazer isso é através de uma câmera que tira uma foto 2D ou 3D da peça. Podemos compensar programas e juntas de compensação com base na localização física das peças. As câmeras mais recentes não são tão afetadas pelo brilho de uma parte como as câmeras poderiam ter sido alguns anos atrás. Eles são capazes de ver mais cores e ler as definições de uma peça, distinguindo sombra e reflexos da peça.” Harooni acrescentou que “a ótica de hoje também nos dá a capacidade de verificar a qualidade da solda em tempo real sem a necessidade de testes destrutivos”.
Terceiro, todos os robôs oferecem alguma forma de detecção de colisão. Miller, da Miller Electric, disse que isso representa a melhoria mais significativa no próprio braço do robô. “Anteriormente, um cliente criava seu programa com base na posição X-Y-Z conhecida da tocha. Digamos que o robô esteja soldando metade do turno e o operador deixe um grampo aberto. O robô provavelmente iria bater no grampo, dobrando a tocha. Isso faria com que todas as soldas desse programa ficassem desalinhadas porque a extremidade da tocha foi dobrada e essa posição mudou. Hoje, se o robô atinge um objeto, mesmo em alta velocidade, ele lê o pico de corrente resultante como uma obstrução. Isso faz com que o robô entre imediatamente no modo servo flexível, o que atrasa a aplicação do freio por uma certa distância especificada para cada eixo. O robô fica 'flácido', na verdade. Isso permite que o robô dissipe o impulso, minimizando os danos à ferramenta. Isso significa que você pode ter uma colisão em alta velocidade sem dobrar a tocha.”
Quatro, todos os principais players oferecem células robóticas pré-projetadas com tudo o que você precisa em um palete (ou vários). “Uma célula de trabalho seria uma unidade totalmente projetada com todas as proteções em vigor”, disse Lange. “Você normalmente vê cercas ou paredes de aço, geralmente scanners de segurança, luzes, botões para permitir que o robô vá, chaves de intertravamento e algum tipo de dispositivo de posicionamento na frente do robô, como uma plataforma giratória ou uma roda gigante. Esses dispositivos trazem a peça para a zona de trabalho enquanto o operador carrega peças adicionais no lado oposto. Ou você pode ter apenas uma mesa fixa onde o robô irá processar. Também haveria uma fonte de energia de soldagem, a tocha e alguns alargadores para limpar as brocas, se necessário. Você só precisa conectá-lo à eletricidade e a uma fonte de gás.” E se uma das soluções prontas não funcionar, estão disponíveis soluções personalizadas prontas para uso.
Então, com o que se preocupar?
“Quando consultamos um cliente em potencial sobre automação de soldagem, analisamos sua fabricação a montante”, explicou Schaefer da Miller Electric. “Se eles estiverem usando lasers e equipamentos CNC para dobrar, frear e cortar o material, eles terão muito mais sucesso em soldá-lo roboticamente do que se estivessem cortando manualmente ou usando uma serra. Essas oficinas podem se safar agora porque, quando soldam as peças à mão, os soldadores podem ajustar de acordo, mas o robô não.” Miller acrescentou que a soldagem geralmente é a última coisa que é automatizada em uma instalação, porque os processos a montante devem ser precisos primeiro. “As peças precisam ser cortadas com precisão e depois dobradas com precisão. Então você pode soldá-los”, disse ele.
Além de garantir que as peças sejam repetíveis, é necessária uma fixação que limite ou elimine as folgas, como explicou Schaefer:“Você não pode soldar ar. Um operador humano pode ver uma lacuna e reagir de acordo, geralmente aumentando o stickout do fio para reduzir a amperagem, o que reduz o calor e a penetração, e então começa a tecer para preencher a lacuna. Um robô não fará isso. Vai queimar”.
Por outro lado, Lange disse que alguns clientes gastaram milhares ou centenas de milhares de dólares em alguns casos em ferramentas para segurar peças quando poderiam reduzir esse preço pela metade melhorando os processos de upstream. Isso fornece a repetibilidade necessária a jusante, o que, em última análise, reduz o custo do ferramental e diminui a quantidade de retrabalho e refugo.
Depois da qualidade e repetibilidade da peça, a próxima preocupação mais importante é “conhecer e entender o processo de soldagem no que se relaciona para se soldar e soldar através do dispositivo automatizado”, disse Lange.
Então, quem você deve treinar para executar a soldagem automatizada? Seja um soldador experiente ou alguém que esteja ansioso para aprender soldagem (o que leva semanas) e automação de soldagem.
Schaefer advertiu que “Você precisa da cultura certa na instalação. Pessoas com empregos podem se sentir ameaçadas pela automação entrando nas instalações. Eu seria muito franco com meu pessoal sobre os benefícios, como isso tornará a empresa mais eficiente, ajudá-la a crescer e ser mais competitiva e, finalmente, contratar mais pessoas.”
Finalmente, os tamanhos dos lotes devem ser grandes o suficiente para automação. Como Lange colocou, “O tempo que leva para fazer a programação off-line, colocar o robô e fazer uma configuração rápida definitivamente produz um bom retorno se os tamanhos dos lotes durarem aproximadamente um dia ou um dia e meio. Se você estiver alterando uma peça a cada hora, pode não ser tão eficaz no ROI.”
Sistema de controle de automação
- Nova tecnologia sem fio 2015
- NPE2018 Foco da Nova Tecnologia:A Revolução ‘4.0’
- Novo Centro de Tecnologia de Saúde da Hahn Automation
- Sistemas de automação robótica inovam em novas instalações
- 4 maneiras de melhorar o desempenho da soldagem robótica
- Estudantes constroem sistema robótico de triagem de lixo usando tecnologia B&R
- Acieta lança nova célula de carregamento de máquina robótica
- Robotiq lança nova solução robótica de coleta de lixo
- AMRC impulsiona inovação em tecnologia e economia circular
- Avanço robótico feito pelo Centro de Tecnologia de Fabricação