Cobre
Antecedentes
O cobre é um dos elementos químicos básicos. Em seu estado quase puro, o cobre é um metal laranja-avermelhado conhecido por sua alta condutividade térmica e elétrica. É comumente usado para produzir uma ampla variedade de produtos, incluindo fios elétricos, panelas e frigideiras, canos e tubos, radiadores de automóveis e muitos outros. O cobre também é usado como pigmento e conservante para papel, tinta, têxteis e madeira. É combinado com zinco para produzir latão e com estanho para produzir bronze.
O cobre foi usado pela primeira vez há 10.000 anos. Um pendente de cobre de cerca de 8700 a.C. foi encontrado onde hoje é o norte do Iraque. Há evidências de que por volta de 6400 a.C. cobre estava sendo derretido e fundido em objetos na área hoje conhecida como Turquia. Por volta de 4500
Em cerca de 3.000 a.C. , grandes depósitos de minério de cobre foram encontrados na ilha de Chipre, no Mar Mediterrâneo. Quando os romanos conquistaram Chipre, deram ao metal o nome latino aes cyprium, que costumava ser abreviado para ciprium. Mais tarde, foi corrompido para cuprum, de onde derivam a palavra inglesa cobre e o símbolo químico Cu.
Na América do Sul, objetos de cobre eram produzidos ao longo da costa norte do Peru já em 500 a.C. , e o desenvolvimento da metalurgia do cobre estava bem avançado na época em que o império inca caiu nas mãos dos soldados espanhóis conquistadores nos anos 1500.
Nos Estados Unidos, a primeira mina de cobre foi aberta em Branby, Connecticut, em 1705, seguida por uma em Lancaster, Pensilvânia, em 1732. Apesar dessa produção inicial, a maior parte do cobre usado nos Estados Unidos foi importado do Chile até 1844, quando começou a mineração de grandes depósitos de minério de cobre de alto teor em torno do Lago Superior. O desenvolvimento de técnicas de processamento mais eficientes no final dos anos 1800 permitiu a mineração de minérios de cobre de baixo teor em enormes minas a céu aberto no oeste dos Estados Unidos.
Hoje, os Estados Unidos e o Chile são os dois maiores produtores mundiais de cobre, seguidos pela Rússia, Canadá e China.
Matérias-primas
O cobre puro raramente é encontrado na natureza, mas geralmente é combinado com outros produtos químicos na forma de minérios de cobre. Existem cerca de 15 minérios de cobre extraídos comercialmente em 40 países ao redor do mundo. Os mais comuns são conhecidos como minérios de sulfeto, nos quais o cobre é quimicamente ligado ao enxofre. Outros são conhecidos como minérios de óxido, minérios de carbonato ou minérios mistos, dependendo dos produtos químicos presentes. Muitos minérios de cobre também contêm quantidades significativas de ouro, prata, níquel e outros metais valiosos, bem como grandes quantidades de material comercialmente inútil. A maioria dos minérios de cobre extraídos nos Estados Unidos contém apenas cerca de 1,2-1,6% de cobre em peso.
O minério de sulfeto mais comum é calcopirita, CuFeS 2 , também conhecido como pirita de cobre ou minério de cobre amarelo. Calcocita, Cu 2 S, é outro minério de sulfeto.
Cuprita, ou minério de cobre vermelho, Cu 2 O, é um minério de óxido. Malaquita, ou minério de cobre verde, Cu (OH) 2 • CuCO 3 , é um importante minério de carbonato, como a azurita, ou carbonato de cobre azul, Cu (OH) 2 • 2CuCO 3 .
Outros minérios incluem tennantita, boronita, crisocola e atacamita.
Além dos próprios minérios, vários outros produtos químicos são freqüentemente usados para processar e refinar o cobre. Isso inclui ácido sulfúrico, oxigênio, ferro, sílica e vários compostos orgânicos, dependendo do processo usado.
O processo de fabricação
O processo de extração do cobre do minério de cobre varia de acordo com o tipo de minério e a pureza desejada do produto final. Cada processo consiste em várias etapas nas quais os materiais indesejados são removidos física ou quimicamente e a concentração de cobre é aumentada progressivamente. Algumas dessas etapas são conduzidas no próprio local da mina, enquanto outras podem ser conduzidas em instalações separadas.
Aqui estão as etapas usadas para processar os minérios de sulfeto comumente encontrados no oeste dos Estados Unidos.
Mineração
- 1 A maioria dos minérios de sulfeto é extraída de enormes minas a céu aberto por meio de perfuração e detonação com explosivos. Nesse tipo de mineração, o material localizado acima do minério, chamado de estéril, é removido primeiro para expor o depósito de minério enterrado. Isso produz um poço aberto que pode chegar a ter uma milha ou mais de diâmetro. Uma estrada para permitir o acesso às espirais dos equipamentos pelas encostas internas do poço.
- 2 O minério exposto é coletado por grandes escavadeiras capazes de carregar 500-900 pés cúbicos (15-25 metros cúbicos) em uma única mordida. O minério é carregado em caminhões basculantes gigantes, chamados caminhões de transporte, e transportado para cima e para fora da mina.
Concentração
O minério de cobre geralmente contém uma grande quantidade de sujeira, argila e uma variedade de minerais não contendo cobre. O primeiro passo é remover alguns desses resíduos. Esse processo é chamado de concentração e geralmente é feito pelo método de flotação.
- 3 O minério é britado em uma série de trituradores de cone. Um britador de cone consiste em um cone de moagem interno que gira em um eixo vertical excêntrico dentro de um cone externo fixo. Conforme o minério é alimentado no topo do britador, ele é espremido entre os dois cones e quebrado em pedaços menores.
- 4 O minério triturado é então moído ainda menor por uma série de moinhos. Primeiro, ele é misturado com água e colocado em um moinho de barras, que consiste em um grande recipiente cilíndrico cheio de vários pedaços curtos de barra de aço. Conforme o cilindro gira em seu eixo horizontal, as hastes de aço tombam e quebram o minério em pedaços de cerca de 0,13 pol. (3 mm) de diâmetro. A mistura de minério e água é posteriormente quebrada em dois moinhos de bolas, que são como um moinho de barras, exceto que bolas de aço são usadas em vez de barras. A lama de minério finamente moído que emerge do moinho de bolas final contém partículas de cerca de 0,01 pol. (0,25 mm) de diâmetro.
- 5 A pasta é misturada com vários reagentes químicos, que revestem as partículas de cobre. Um líquido, denominado espumante, também é adicionado. Óleo de pinho ou álcool de cadeia longa são freqüentemente usados como espumantes. Essa mistura é bombeada para tanques retangulares, chamados de células de flotação, onde o ar é injetado na lama pelo fundo dos tanques. Os reagentes químicos fazem com que as partículas de cobre se agarrem às bolhas à medida que sobem para a superfície. O espumante forma uma espessa camada de bolhas, que transborda dos tanques e é coletada em cochos. As bolhas condensam-se e a água é drenada. A mistura resultante, chamada de concentrado de cobre, contém cerca de 25-35% de cobre junto com vários sulfetos de cobre e ferro, além de concentrações menores de ouro, prata e outros materiais. Os materiais restantes no tanque são chamados de ganga ou rejeitos. Eles são bombeados para tanques de decantação e deixados para secar.
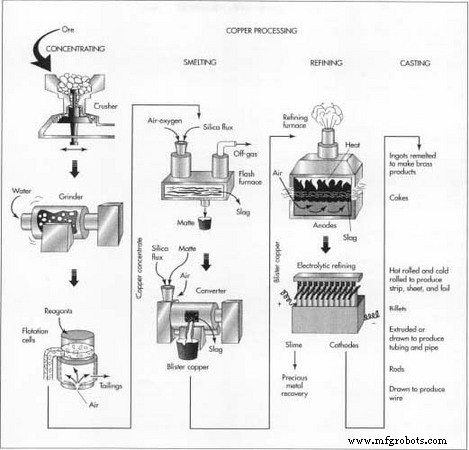
Fundição
Uma vez que os resíduos tenham sido fisicamente removidos do minério, o concentrado de cobre restante deve passar por várias reações químicas para remover o ferro e o enxofre. Este processo é chamado de fundição e tradicionalmente envolve dois fornos, conforme descrito a seguir. Algumas fábricas modernas utilizam um único forno, que combina as duas operações.
- 6 O concentrado de cobre é alimentado em um forno junto com um material de sílica, denominado fluxo. A maioria das fundições de cobre utiliza fornalhas flash enriquecidas com oxigênio, nas quais o ar pré-aquecido e enriquecido com oxigênio é forçado a entrar na fornalha para entrar em combustão com óleo combustível. O concentrado de cobre e o fundente fundem e são coletados no fundo do forno. Muito do ferro no concentrado combina quimicamente com o fluxo para formar uma escória, que é removida da superfície do material fundido. Muito do enxofre no concentrado se combina com o oxigênio para formar dióxido de enxofre, que é exaurido da fornalha como gás e posteriormente tratado em uma planta de ácido para produzir ácido sulfúrico. O material derretido restante no fundo do forno é chamado de fosco. É uma mistura de sulfuretos de cobre e sulfuretos de ferro e contém cerca de 60% de cobre em peso.
- 7 O fosco derretido é retirado do forno e colocado em um segundo forno denominado conversor. Fluxo de sílica adicional é adicionado e oxigênio é soprado através do material fundido. As reações químicas no conversor são semelhantes às do forno flash. O fluxo de sílica reage com o ferro restante para formar uma escória e o oxigênio reage com o enxofre restante para formar dióxido de enxofre. A escória pode ser realimentada no forno flash para atuar como um fluxo, e o dióxido de enxofre é processado através da planta de ácido. Depois que a escória é removida, uma injeção final de oxigênio remove tudo, exceto um traço de enxofre. O material fundido resultante é chamado de bolha e contém cerca de 99% de cobre em peso.
Refino
Embora a bolha de cobre seja 99% cobre puro, ela ainda contém níveis altos o suficiente de enxofre, oxigênio e outras impurezas para dificultar o refinamento posterior. Para remover ou ajustar os níveis desses materiais, o cobre blister é primeiro refinado a fogo antes de ser enviado para o processo final de eletrorrefinação.
- 8 O cobre blister é aquecido em um forno de refino, que é semelhante a um conversor descrito acima. O ar é soprado na bolha derretida para oxidar algumas impurezas. Um fluxo de carbonato de sódio pode ser adicionado para remover vestígios de arsênio e antimônio. Uma amostra do material fundido é retirada e um operador experiente determina quando as impurezas atingiram um nível aceitável. O cobre fundido, que é cerca de 99,5% puro, é então despejado em moldes para formar grandes ânodos elétricos, que atuam como terminais positivos para o processo de eletrorrefinação.
- 9 Cada ânodo de cobre é colocado em um tanque individual, ou célula, feito de concreto polimérico. Pode haver até 1.250 tanques em operação ao mesmo tempo. Uma folha de cobre é colocada na extremidade oposta do tanque para atuar como o cátodo, ou terminal negativo. Os tanques são preenchidos com uma solução ácida de sulfato de cobre, que atua como um condutor elétrico entre o ânodo e o cátodo. Quando uma corrente elétrica passa por cada tanque, o cobre é removido do ânodo e é depositado no cátodo. A maior parte das impurezas restantes caem da solução de sulfato de cobre e formam uma lama no fundo do tanque. Após cerca de 9-15 dias, a corrente é desligada e os cátodos são removidos. Os cátodos agora pesam cerca de 136 kg (300 lb) e são 99,95-99,99% de cobre puro.
- 10 O lodo que se acumula no fundo do tanque contém ouro, prata, selênio e telúrio. Ele é coletado e processado para recuperar esses metais preciosos.
Elenco
- 11 Após o refino, os cátodos de cobre são derretidos e fundidos em lingotes, bolos, tarugos ou barras, dependendo da aplicação final. Lingotes são tijolos retangulares ou trapezoidais, que são fundidos novamente junto com outros metais para fazer latão e bronze. Bolos são placas retangulares com cerca de 20 cm de espessura e 8,5 m de comprimento. Eles são laminados para fazer chapas, tiras, folhas e produtos de folha de cobre. Tarugos são toras cilíndricas com cerca de 20 cm de diâmetro e vários pés (metros) de comprimento. Eles são extrudados ou estirados para fazer tubos e canos de cobre. As hastes têm uma seção transversal redonda de cerca de 0,5 pol. (1,3 cm) de diâmetro. Eles geralmente são fundidos em comprimentos muito longos, que são enrolados. Este material enrolado é então puxado ainda mais para baixo para fazer fio de cobre.
Controle de qualidade
Como as aplicações elétricas exigem um nível muito baixo de impurezas, o cobre é um dos poucos metais comuns que são refinados até quase 100% de pureza. Foi comprovado que o processo descrito acima produz cobre de altíssima pureza. Para garantir essa pureza, as amostras são analisadas em várias etapas para determinar se algum ajuste do processo é necessário.
Subprodutos / resíduos
A recuperação de ácido sulfúrico do processo de fundição de cobre não só fornece um subproduto lucrativo, mas também reduz significativamente a poluição do ar causada pela exaustão do forno. Ouro, prata e outros metais preciosos também são subprodutos importantes.
Os produtos residuais incluem o estéril da operação de mineração, os rejeitos da operação de concentração e a escória da operação de fundição. Esses resíduos podem conter concentrações significativas de arsênio, chumbo e outros produtos químicos, que representam um perigo potencial para a saúde na área circundante. Nos Estados Unidos, a Agência de Proteção Ambiental (EPA) regulamenta o armazenamento de tais resíduos e a remediação da área após o término das operações de mineração e processamento. O grande volume do material envolvido - em alguns casos, bilhões de toneladas de resíduos - torna essa tarefa formidável, mas também apresenta algumas oportunidades potencialmente lucrativas para recuperar os materiais utilizáveis contidos nesses resíduos.
O Futuro
A demanda por cobre deve permanecer alta, especialmente nas indústrias elétrica e eletrônica. As tendências atuais no processamento do cobre são para métodos e equipamentos que usam menos energia e produzem menos poluição do ar e resíduos sólidos. Nos Estados Unidos, esta é uma tarefa difícil devido aos rígidos controles ambientais e aos minérios de cobre de baixíssima concentração disponíveis. Em alguns casos, os custos de produção podem aumentar significativamente.
Uma tendência encorajadora é o aumento do uso de cobre reciclado. Atualmente, mais da metade do cobre produzido nos Estados Unidos vem de cobre reciclado. Cinquenta e cinco por cento do cobre reciclado vem de operações de usinagem de cobre, como a formação de parafusos, e 45% vem da recuperação de produtos de cobre usados, como fios elétricos e radiadores de automóveis. A porcentagem de cobre reciclado deve crescer à medida que aumentam os custos do novo processamento de cobre.
Processo de manufatura
- Tabela de calibre de fio de cobre
- Tabela de Ampacidade de Fio de Cobre
- Defeitos de interconexão (ICDs)
- Guia para materiais de liga de cobre
- As propriedades antimicrobianas do cobre
- Cobre Berílio (BECOL-25) TB00
- Cobre Berílio (BECOL-25) TD04
- Cobre Berílio (BECOL-25) TH04
- Liga de Cobre COLSIBRO®
- Tratamento térmico de cobre e ligas de cobre