Compósitos termoplásticos reciclados para produção
A capacidade de reciclagem tem sido um benefício prometido há muito tempo com o uso de compósitos termoplásticos (TPCs). Mas ainda não foi usado comercialmente em grande escala. O fornecedor de materiais TenCate Advanced Composites e o ThermoPlastic composites Research Center (TPRC) fizeram parceria com o fabricante Tier 1 GKN Fokker para demonstrar tal processo em 2016. A equipe desenvolveu um painel de porta de acesso usando sucata TenCate Cetex TC1100 tecido de fibra de carbono / sulfeto de polifenileno (CF / PPS) material da produção da GKN Fokker do elevador e leme Gulfstream G650. Os resíduos da produção foram picados e, em seguida, moldados por compressão usando um processo e molde projetados pela TPRC. O painel da porta de acesso apresentava nervuras de reforço moldadas, variações de espessura e orifícios moldados com saliências. (Uma saliência é um recurso saliente que orienta um fixador para dentro do furo). O uso do material recuperado possibilitou uma peça leve com maior funcionalidade moldada enquanto formava um processo de fabricação em malha fechada, visto que o painel da porta de acesso foi então usado na borda de ataque do leme Gulfstream G650. O projeto ganhou o Prêmio JEC de Inovação em 2016.
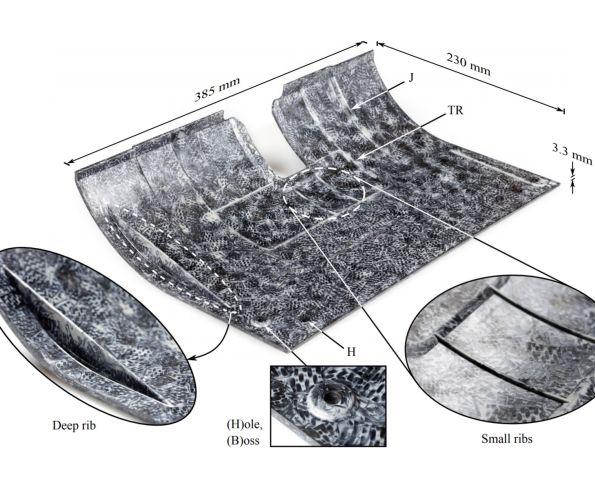
Painel da porta de acesso demonstrado em 2016 é feito de sucata de material Cetex CF / PPS e apresenta reforços de reforço e orifícios moldados com ressaltos. FONTE | TPRC.
Desde essa pesquisa, uma nova organização foi estabelecida, o ThermoPlastic composites Applications Center (TPAC). “O TPRC foi formado há dez anos e trabalha principalmente em pesquisas fundamentais de TPC para a indústria aeroespacial”, explica Thomas de Bruijn, pesquisador em estruturas leves da TPAC. “O TPAC foi formado aproximadamente dois anos atrás, e tem uma forma mais aplicada de trabalhar. Está ligada à Saxion University e também a PME. Nosso foco é reduzir os custos, desenvolvendo processos mais econômicos. Juntos, esses dois grupos formam a TPC NL, uma indústria inteligente, hub de inovação digital para a tecnologia TPC. ”
O envolvimento da TPAC e também da P&D contínua da TenCate demonstraram que este tipo de fabricação em circuito fechado não só é possível, mas economicamente benéfico. O foco, inicialmente, está em materiais CF / PPS, e a pesquisa está em colaboração com parceiros da indústria para ajudar a implementar esta produção de peças otimizada para reciclagem TPC.
No entanto, os processos reais desenvolvidos são diferentes. TenCate tem se concentrado em materiais de fibra mais curtos usados como uma camada de fluxo para adicionar recursos geométricos moldados e funcionalidade a peças de fibra contínua. Enquanto isso, o TPRC e o TPAC têm procurado manter um comprimento de fibra maior, criando um material semelhante a uma massa que pode ser moldado por compressão em peças com propriedades mecânicas mais altas do que é possível com os compostos de fibra curta tradicionais.
TenCate - partes de organosheet aprimoradas com camada de fluxo
“Três anos atrás, começamos a investir mais de nosso orçamento de P&D na reciclagem”, disse Frank ten Napel, gerente de produto TenCate para termoplásticos. “Não se trata apenas de obter um‘ rótulo verde ’. Estamos convencidos de que incorporar material reciclado em sua peça oferece benefícios econômicos e de construção muito reais. Podemos aplicar um nível de geometria a uma peça que não poderíamos alcançar de outra forma. Ao aplicar uma camada de fluxo de material reciclado, podemos moldar nervuras de enrijecimento e espessura variável em toda a peça, bem como saliências ao redor dos orifícios, que distribuem as cargas induzidas pelos fixadores. Tudo isso permite o uso de material de fibra menos contínuo, para peças mais finas, leves e econômicas em vez de apenas usar material virgem. ” Ele observa que essas características moldadas são difíceis de alcançar com materiais de fibra contínua, “mas combinando tanto a fibra contínua com a sobremoldagem localizada, você obtém mais liberdade de design”.
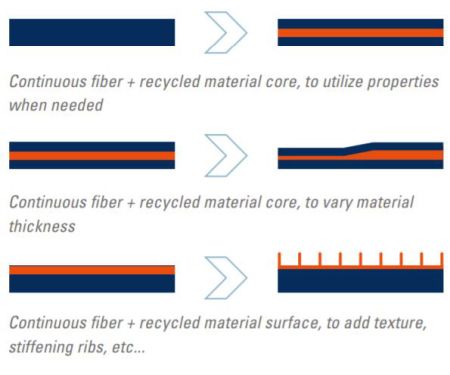

Este demonstrador tipo colchete mostra os dois lados da mesma peça, destacando uma camada de folha orgânica tecida convencional e uma camada de fluxo TPC reciclado. Este último apresenta reforços e ressaltos para as pastilhas. FONTE | TenCate
Projeto do Ciclo TPC
Este projeto de quatro anos começou em setembro de 2015 e inclui parceiros de toda a cadeia de fornecimento de compósitos termoplásticos (TPC):
- TenCate Advanced Composites (Toray Group) - materiais
- GKN Fokker Aerostructures - Tier 1 design e fabricação de estruturas aeroespaciais e conjuntos
- Componentes termoplásticos holandeses (DTC) - projeto e fabricação de pequenas e médias empresas de nervuras aeroespaciais, longarinas, suportes, clipes, caixas
- Cato Composites - PMEs fabricação e design de peças para os mercados aeronáutico, automotivo, de defesa, esportivo e de consumo
- Nido RecyclingTechniek (NRT) - tecnologia para trituração e redução do tamanho dos materiais / peças a serem reciclados
O TPC-Cycle é facilitado pela TPAC e pela Saxion University of Applied Sciences, particularmente seu grupo de pesquisa de estruturas leves, e financiado por Regieorgaan SIA, parte da Organização Holandesa de Pesquisa Científica (NWO).
Thomas de Bruijn é gerente de projeto do TPC-Cycle e pesquisador em estruturas leves na Saxion / TPAC. Ele explica que houve muitos motivadores para iniciar o projeto TPC-Cycle. “Pudemos ver um aumento no uso de TPCs de fibra contínua, principalmente para a formação de estampas, como em clipes e suportes. Com esse aumento, o volume de resíduos pós-industriais torna-se expressivo. Portanto, a reciclagem era necessária, tanto para o meio ambiente quanto economicamente, e também para atender às regulamentações. Por exemplo, a legislação europeia de fim de vida exige que 95% do material usado nos automóveis seja reciclado. ” Ele observa que a Airbus também definiu metas de reciclagem e fim da vida útil, e as comunicou a seus fornecedores. “A cadeia de abastecimento não deve apenas dizer que pode cumprir esses objetivos, mas também provar essa capacidade com os demonstradores”, acrescenta de Bruijn.
“Também vimos TPCs crescendo fora da indústria aeroespacial, em aplicações como engradados de alimentos, móveis e componentes industriais, porque eles oferecem tempos de ciclo mais baixos, estruturas leves e mais inteligentes”, diz de Bruijn.
Ele continua, “Queríamos provar uma cadeia de processo de reciclagem comercialmente viável, mas não apenas moagem, que é a reciclagem. Queríamos alto desempenho. Portanto, escolhemos uma abordagem de mistura de baixo cisalhamento para reter o comprimento da fibra de 0,5-1,0 polegadas. Para obter rigidez, você só precisa de alguns mm de comprimento. Mas para força e resistência ao impacto, você precisa de mais de 0,5 polegada de comprimento. ” Além de manter o comprimento da fibra, outro desafio importante era conseguir uma boa homogeneidade na mistura dos materiais e no produto reciclado final.
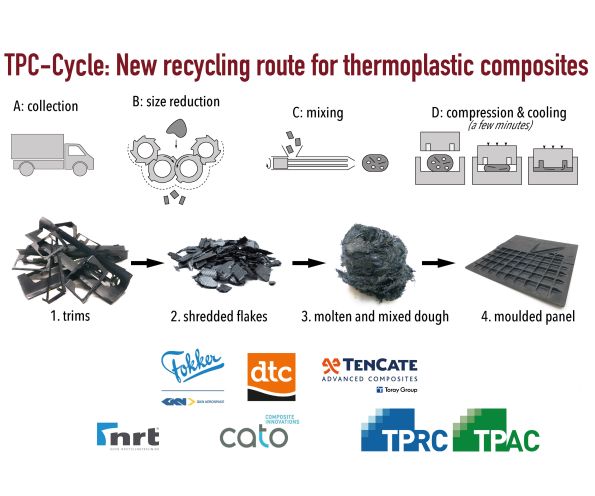
“O objetivo é coletar os resíduos, triturá-los em flocos de 0,5-1,0 polegadas e transformá-los em uma massa homogênea, que é extrusada e diretamente transferida para uma prensa de moldagem por compressão”, explica o pesquisador e Ph.D. do TPRC. aluno Guillaume Vincent. “O processamento da massa é feito através da alimentação de flocos e grânulos de polímero virgem em um misturador de baixo cisalhamento, reduzindo a fração de peso da fibra para 25-40%.” Ele observa que o processo é muito semelhante à composição direta de termoplásticos de fibra longa (D-LFT), comum no setor automotivo. “No entanto, os processos D-LFT requerem milhões de dólares de investimento, por isso são usados apenas na produção de alta série. Modificamos nossa abordagem usando máquinas menores, mas obtemos resultados semelhantes. Nossos volumes são baixos em comparação aos processos D-LFT. ”
Vincent descreve um exemplo de onde a inclusão da cadeia de valor de reciclagem completa compensa:“A NRT ajudou a nos conectar com fabricantes de máquinas de trituração maiores, como a Untha.” Esta é uma parte fundamental do dimensionamento do processo de produção de peças em série.
A primeira cadeia de processo em desenvolvimento é para CF / PPS. Vincent diz que a TPC-Cycle construiu modelos de simulação e métodos de análise para caracterizar o comprimento e a distribuição das fibras no material reciclado. “Também estamos entendendo como essas características do material se transferem para as propriedades da peça moldada”, observa. Este é, de fato, o foco de seu doutorado. tese, que será publicada até o final de 2019.
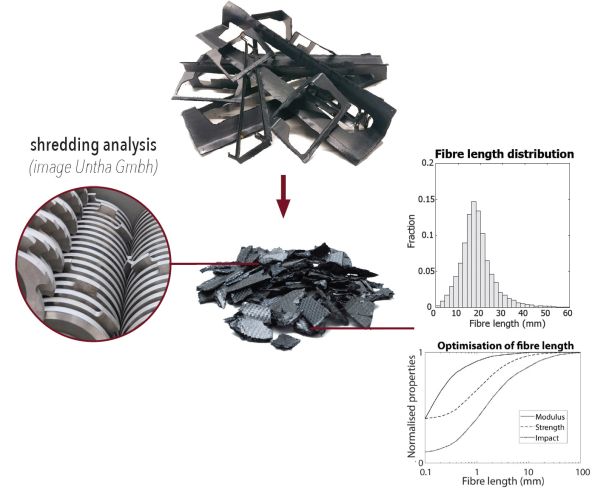
O TPC- O projeto Cycled desenvolveu uma cadeia de processo completa para a reciclagem de compósitos termoplásticos, incluindo trituração econômica e caracterização do comprimento e distribuição da fibra. FONTE | TPRC / TPAC.
Essa massa reciclada é às vezes chamada de composto de moldagem em massa (BMC). Historicamente, o BMC era uma mistura semelhante a uma massa de fibra de vidro curta (<25 mm), pasta de resina termofixa e cargas moldadas por compressão em peças compostas. Com menos volume de fibra e mais fluxo em relação ao composto de moldagem de folha (SMC), ele também oferece propriedades mecânicas ligeiramente inferiores. TenCate vendeu termofixos e termoplásticos BMC há anos, embora o último seja um processo em que fitas pré-impregnadas unidirecionais cortadas são espalhadas em um molde e prensadas. “Nosso produto é bastante diferente”, afirma Vincent. “Com o termoplástico convencional BMC, geralmente não há mistura e requer um longo ciclo de aquecimento e consolidação. Descobrimos que com a mistura você obtém um produto mais homogêneo e menos concentrações de tensão na peça, portanto, propriedades mais altas. Com o termoplástico BMC convencional, você obtém flocos mais grossos que possuem regiões ricas em matriz nas extremidades que produzem concentrações de tensão no laminado composto. ”
O processo de mistura de baixo cisalhamento desembaraça os flocos em camadas e, em seguida, separa as camadas em feixes e os feixes em fibras soltas. O polímero também é misturado para diminuir o conteúdo de fibra a fim de obter melhores propriedades de fluxo, de modo que o material seja mais fácil de processar em formas.
“A massa é extrudada e então roboticamente colocada em um molde de compressão aberto e isotérmico [aquecido]”, explica de Bruijn. “Após a mistura, as fibras da massa são orientadas aleatoriamente. Mas durante a prensagem, o fluxo de material reorienta as fibras. Esta orientação é menor em comparação com misturas que usam fibras mais curtas que são moldadas por injeção, mas é semelhante de parte a parte. Este é um dos nossos tópicos de estudo contínuo. ”
Custo
A cadeia de processo TPC-Cycle desenvolvida até agora parece economicamente vantajosa. “Esperamos responder o quanto podemos reduzir os custos das peças até o final de 2019”, diz de Bruijn. “Mas isso é complexo porque você precisa de um mercado e tem que vender o material reciclado.” Ele observa que existem muitos fatores econômicos. Por exemplo, a maioria dos fabricantes hoje está simplesmente jogando fora os resíduos da produção. O custo local para disposição em aterro é de € 80 por tonelada ($ 90). “Mas esse material jogado fora tem valor”, diz de Bruijn. “Além disso, você deve contabilizar os custos para coletar os resíduos, triturá-los, misturá-los e, em seguida, moldar a compressão em novas peças. No entanto, este também é um processo quase final com tempos de ciclo curtos devido ao molde isotérmico. ” Em outras palavras, deve haver uma redução drástica ou eliminação do acabamento secundário e da usinagem. De Bruin diz que a TPC-Cycle está agora procurando concluir a análise de custos e a análise do ciclo de vida.
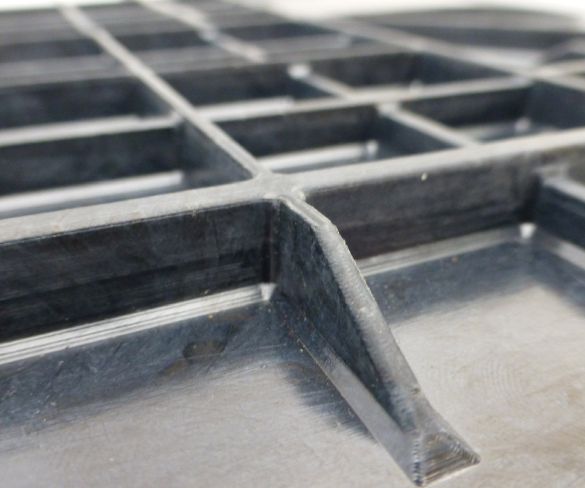
FONTE | TPRC / TPAC
Clean Sky RESET
Um terceiro projeto que reitera a importância do trabalho realizado pela TenCate e também no projeto do Ciclo TPC é o projeto RESET, que decorreu de janeiro de 2016 a dezembro de 2017 e foi coordenado pelo Instituto Tecnológico Leitat de Barcelona, Espanha. Parece que o RESET foi iniciado no Clean Sky (2008-2016) e concluído durante o Clean Sky 2 (2017-2021).
Os programas Clean Sky e Clean Sky 2 são organizados em uma camada superior de Programas de Demonstração de Aeronaves Inovadoras (consulte IADPs de Veículos na imagem abaixo) e uma camada inferior de Demonstradores de Tecnologia Inovadora (consulte ITDs de Grande Sistema na imagem abaixo). O RESET foi concluído como parte do Airframe ITD, especificamente Work Package (WP) A-3.4 Eco-Design for Airframe.
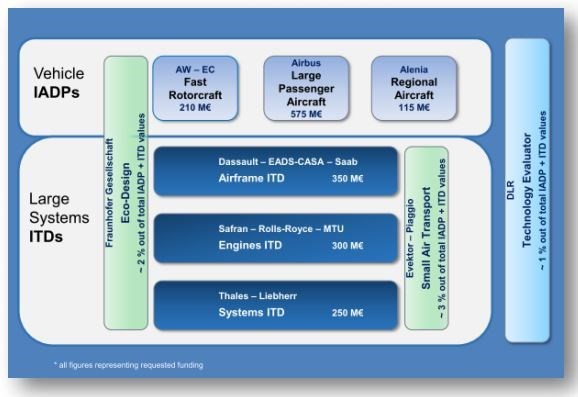
FONTE:Limpar Sky 2 Joint Technical Proposta
Para mais detalhes, veja “Demonstradores de composto termoplástico - Roteiro da UE para fuselagens futuras”
De acordo com a diretora de projeto da Clean Sky, Elena Pedone, a equipe RESET da Leitat desenvolveu um processo para reciclar o material composto de aeronaves usado anteriormente e usá-lo para fabricar novas peças. Eles compararam essas peças recicladas com as feitas comercialmente e descobriram que tinham características mecânicas semelhantes. “A tecnologia desenvolvida neste projeto poderá ser comercializada de forma realista no setor aeronáutico nos próximos anos e possivelmente se espalhar para outros setores da economia”, diz Pedone.
Durante o projeto RESET, o trabalho foi concluído para investigar os efeitos dos materiais de matriz termoplástica PEEK e PPS e a natureza química do reforço de fibra de carbono. A forma do reforço foi estudada, incluindo comprimento da fibra e tecido versus não tecido. O efeito do conteúdo de fibra (relação polímero para fibra) também foi estudado.
Em um segundo pacote de trabalho, o objetivo principal era o condicionamento e caracterização de CF / PPS reciclado à base de extrusão e dos compósitos moldados resultantes. Duas peças - um suporte termoplástico e uma presilha termoplástica - foram criadas por moldagem por injeção e outras duas por termoformação, explica a coordenadora científica do projeto de Leitat, Claudia Aguilar. Essas peças foram então testadas. “As propriedades mecânicas do material foram consideradas comparáveis às da contraparte comercial”, diz Aguilar.
O projeto RESET afirma ter demonstrado um processo de reciclagem que pode retirar o material residual do TPC da produção de aeronaves e usá-lo como matéria-prima para produzir novas peças para aeronaves. “Até 70% do material reciclado foi usado para produzir uma nova família de materiais compostos”, diz Aguilar. Ela acrescenta que “o processo de reciclagem do RESET permite que a aviação europeia limite a pegada ambiental e reduza os custos de produção de novas peças de aeronaves. Portanto, o projeto torna a indústria da aviação mais competitiva e mais verde. ”
Suporte (à esquerda) e presilha (à direita) feitos de material CF / PPS reciclado demonstrado pelo projeto Clean Sky RESET. FONTE | Instituto Tecnológico Leitat
O futuro do TPC começa com o design
A afirmação de TenCate e TPRC / TPAC é que esses processos de reciclagem que agora foram demonstrados não são apenas verdes, mas economicamente atraentes. Então, que tipo de investimento é necessário? “Depende do volume de produção”, diz Ten Napel, da TenCate. “As máquinas de trituração necessárias não são grandes nem caras e o processo foi desenvolvido para ser bastante simples.” O tipo de matriz afeta a reciclabilidade? “Não”, diz Ten Napel, “mas em termos de viabilidade econômica, fibra de carbono e PPS, PEEK ou PEKK são mais viáveis do que fibra de vidro e polipropileno por causa de seu valor mais alto em relação ao último.”
“Acho que se isso vai ser adotado pela indústria, deve começar com o design”, continua ele. “O maior obstáculo no momento é a mentalidade dos engenheiros. Para realmente sair e projetar com material reciclado (ou projetá-los parcialmente em um novo produto) é muito novo para eles. ”
Ten Napel admite que a TenCate não projeta nem fabrica peças comercialmente, “mas estamos tentando inspirar designers a pensar dessa forma no desenvolvimento de suas novas peças e estruturas”. Ele cita os interiores de aeronaves e os painéis de acesso e portas de acesso como uma opção mais baixa para a reutilização de material reciclado. “Se nós, como indústria, pudermos nos acostumar a reutilizar nossa própria sucata e resíduos, podemos dar o próximo passo e começar a estudar como lidar com peças em fim de vida”.
O mantra sobre a reciclagem de compósitos termoplásticos - simplesmente moagem e remoldagem - pode definitivamente ser adotado, diz Ten Napel, mas geralmente não faz muito sentido economicamente. “Demonstramos um processo melhor e que pode realmente criar peças e programas gerais mais econômicos. Optamos por disseminar este conhecimento, junto com o TPRC e TPAC, a fim de inspirar a indústria quanto ao que é totalmente possível com os compósitos termoplásticos. ” Se os compósitos termoplásticos devem ser adotados em grande escala, a reciclagem como parte inerente da produção não é mais uma opção, é uma necessidade.
Resina
- Reciclagem:Compósitos termoplásticos reforçados com fibra contínua com policarbonato reciclado
- Biomaterial termoplástico ‘Ajustado’ para aplicações médicas
- Karl Mayer lança linha de produção para fitas UD termoplásticas
- INEOS Styrolution para construir local de produção para compósito termoplástico StyLight
- Hexion apresenta solução epóxi de dois componentes para produção de compósitos aeroespaciais
- Porta termoplástica a primeira para compósitos automotivos
- LANXESS expande capacidade de produção de compósitos termoplásticos reforçados com fibra contínua
- Visualização do CAMX 2018:TenCate Advanced Composites
- Compósitos termoplásticos de soldagem
- TenCate celebra montagem de consórcio de compósitos termoplásticos no Brasil