Como o Lean Manufacturing é aplicado em uma oficina CNC
Muitas oficinas mecânicas estão surgindo continuamente à medida que o mercado de peças personalizadas cresce exponencialmente e isso nos deixa com muitas oficinas CNC para escolher. Claro, todos nós queremos obter a melhor qualidade para nossas peças, então se eu escolher uma oficina de máquinas CNC perto de mim, eu procuraria aquela com uma vantagem competitiva que oferece o maior valor pelo meu investimento. Isso inclui alta qualidade de mão de obra, tempo de resposta rápido e entrega no prazo. Para uma instalação alcançar essa vantagem competitiva entre outras, ela tem que incorporar eficiência em seus processos, e uma das formas mais estabelecidas e eficazes para isso é através da aplicação dos princípios da manufatura enxuta.
Adaptando os Princípios de Manufatura Enxuta em uma Oficina CNC
O que é manufatura enxuta em uma oficina CNC?
Em primeiro lugar, quando falamos de manufatura enxuta, estamos nos referindo à maximização da produção de uma oficina CNC, minimizando os desperdícios incorridos durante o processo produtivo. Essa metodologia vem das melhores práticas empregadas pela Toyota em sua linha de produção na década de 1930, cujo principal objetivo é eliminar desperdícios em sua operação.
Através da evolução desse método desde sua descoberta, especialistas do setor identificam as 8 principais categorias de resíduos industriais, e isso pode ser abreviado como DOWNTIME:Defeitos, Superprodução, Espera, Não utilização de talentos, Transporte, Excesso de estoque, Desperdício de movimento e Processamento excessivo.
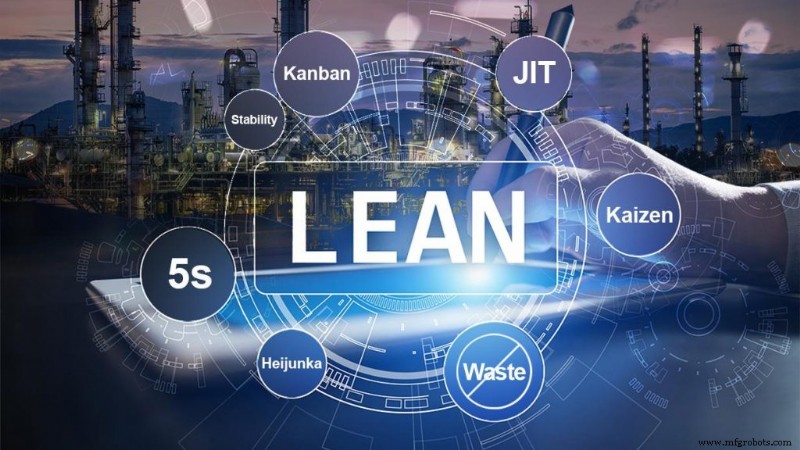
1. Defeitos
Em uma oficina mecânica CNC, isso pode incluir peças sucateadas devido à imprecisão dimensional, acabamento superficial indesejado e quaisquer outros defeitos na peça usinada. Esses defeitos geralmente são causados por diferentes fatores, como parâmetros de usinagem ruins, mau funcionamento da máquina, ferramentas de baixa qualidade, instrumentos não calibrados e processos de usinagem mal planejados.
2. Superprodução
Esse desperdício industrial advém do excesso de oferta devido à produção cega de peças de tal forma que as peças produzidas superam a demanda. Isso às vezes se origina de um planejamento inadequado e pedidos de peças descoordenados.
3. Tempo de espera
Isso é um desperdício devido ao tempo não utilizado que pode ser usado para etapas de produção valiosas. Alguns exemplos incluem a paragem da produção devido à indisponibilidade de materiais e devido à avaria da máquina. Os tempos de espera na produção podem ser causados por planejamento inadequado, tempo de inatividade imprevisto da máquina e muito mais.
4. Não utilização de talentos
Isso inclui a falha em usar o talento e as habilidades de um funcionário de forma eficaz.
5. Transporte
Este é um tipo de resíduo caracterizado pelo transporte excessivo de um processo para outro. Em outras palavras, os resíduos de transporte são as etapas irracionais de um processo que podem ser eliminados ou melhorados em troca de uma etapa mais eficiente.
6. Excesso de estoque
Nas instalações de usinagem CNC, esse desperdício vem ao lado da superprodução, em que o excesso de estoque pode causar perdas para uma oficina CNC. Lembre-se que as peças produzidas que ficam presas em um armazém não geram retorno para a empresa e por isso são considerados resíduos industriais.
7. Resíduos de movimento
Isso se estende à movimentação desnecessária de qualquer recurso que não agregue valor ao produto como um todo. Em uma oficina CNC, isso inclui a colocação não estratégica de diferentes ferramentas, materiais e estações de trabalho.
8. Processamento excessivo
Na fabricação de peças usinadas, o processamento excessivo inclui a execução de processos desnecessários que não são significativos para os requisitos do cliente. Isso geralmente é resultado de um processo de usinagem mal projetado.
Esses diferentes desperdícios nos levaram à base principal que pode ser utilizada pelas oficinas mecânicas na implementação da manufatura enxuta e são:
- Estabelecer as expectativas e os requisitos do cliente para suas peças
- Mapeamento do fluxo de valor de uma oficina CNC
- Criação de um fluxo eficiente
- Estabelecer uma atração efetiva
- Buscando a excelência contínua
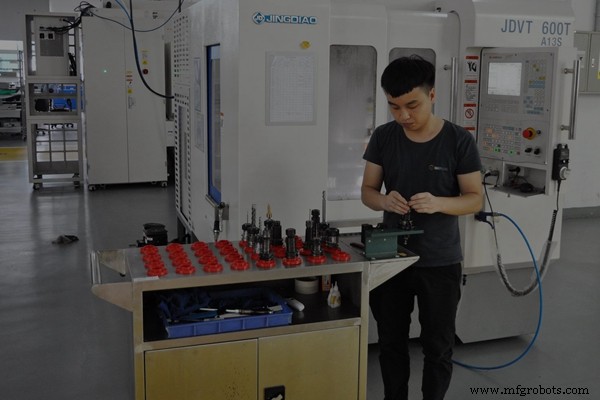
7 maneiras como uma oficina CNC pode implementar os princípios Lean
1. Maximizando a eficiência de ferramentas (seleção de ferramentas)
A eficiência do ferramental é um fator crítico para uma oficina mecânica porque esse único fator pode fazer ou quebrar a qualidade das peças produzidas por qualquer máquina CNC. É essencial escolher as ferramentas certas para garantir uma alta qualidade de corte e, por sua vez, minimizar as peças defeituosas devido à má utilização das ferramentas.
2. Ser inteligente com parâmetros de usinagem e processos de usinagem
Os engenheiros de fabricação planejam cuidadosamente seus parâmetros (por exemplo, taxa de avanço, velocidade de corte, profundidade de corte, etc.) de forma que obtenham o máximo valor da máquina CNC, do material e das ferramentas. Além dos parâmetros, é importante projetar o arranjo mais eficaz para os diferentes processos de usinagem. Fazer isso minimizará os desperdícios relacionados a defeitos, movimento e processamento excessivo.
3. Implementação consistente de manutenção periódica e preventiva
Os tempos de inatividade das máquinas são, de longe, uma das principais razões para paradas desnecessárias de produção na linha de fabricação, e é por isso que o cumprimento diligente da manutenção programada é uma obrigação. Os tempos de paragem imprevistos são significativamente reduzidos com manutenções e verificações regulares dos diferentes equipamentos, o que leva à redução de desperdícios relativos a esperas, defeitos e talentos não utilizados.
4. Produção Just-in-time (JIT)
O JIT é alcançado por meio de planejamento e programação inteligentes para vários recursos. Outra causa importante para a espera desnecessária em uma oficina CNC é a indisponibilidade de matérias-primas para trabalhar. Para evitar que isso aconteça, os planejadores planejam os métodos mais eficazes em relação ao fluxo de entrada, processamento e saída de diferentes recursos.
5. Organização para produtividade
É importante planejar a organização e colocação de diferentes instrumentos necessários na produção de peças CNC. Tão simples quanto aplicar o 5S (Classificar, Definir em ordem, Brilhar, Padronizar e Sustentar) em um ambiente de trabalho pode fazer uma diferença significativa na organização de um fluxo de trabalho. Isso elimina desperdícios relacionados ao movimento e recursos não utilizados.
6. Layout Estratégico da Planta
Em uma oficina mecânica CNC, o layout da planta é um dos pontos essenciais a serem levados a sério para evitar desperdícios desnecessários trazidos pelo excesso de transporte. Cenários de exemplo seriam:racks para matérias-primas devem ser colocados perto das operações de blanking, máquinas são dispostas para transportar facilmente a peça para o próximo processo de usinagem, equipamentos de acabamento são colocados perto da área de embalagem.
7. Iniciativas de melhoria contínua
Por último está a sustentação das melhores práticas da oficina CNC. A longo prazo, as oficinas CNC que melhoram continuamente seus processos são aquelas capazes de entregar peças da mais alta qualidade com compromissos de entrega promissores.
Máquina cnc
- história das máquinas CNC
- es de Máquinas CNC
- re para comprar peças CNC
- ter em uma oficina mecânica:como a temperatura afeta o desempenho do CNC
- Como as máquinas CNC mudaram a fabricação moderna?
- Como as máquinas CNC mudaram de fabricação
- Como as máquinas CNC impactaram a fabricação?
- Como escolher uma oficina de usinagem CNC confiável para peças CNC
- Como retomar a manufatura enxuta
- Manufatura Aeroespacial – Como Alcançamos a Qualidade