Fabricação de compósitos digitais baseados em solução
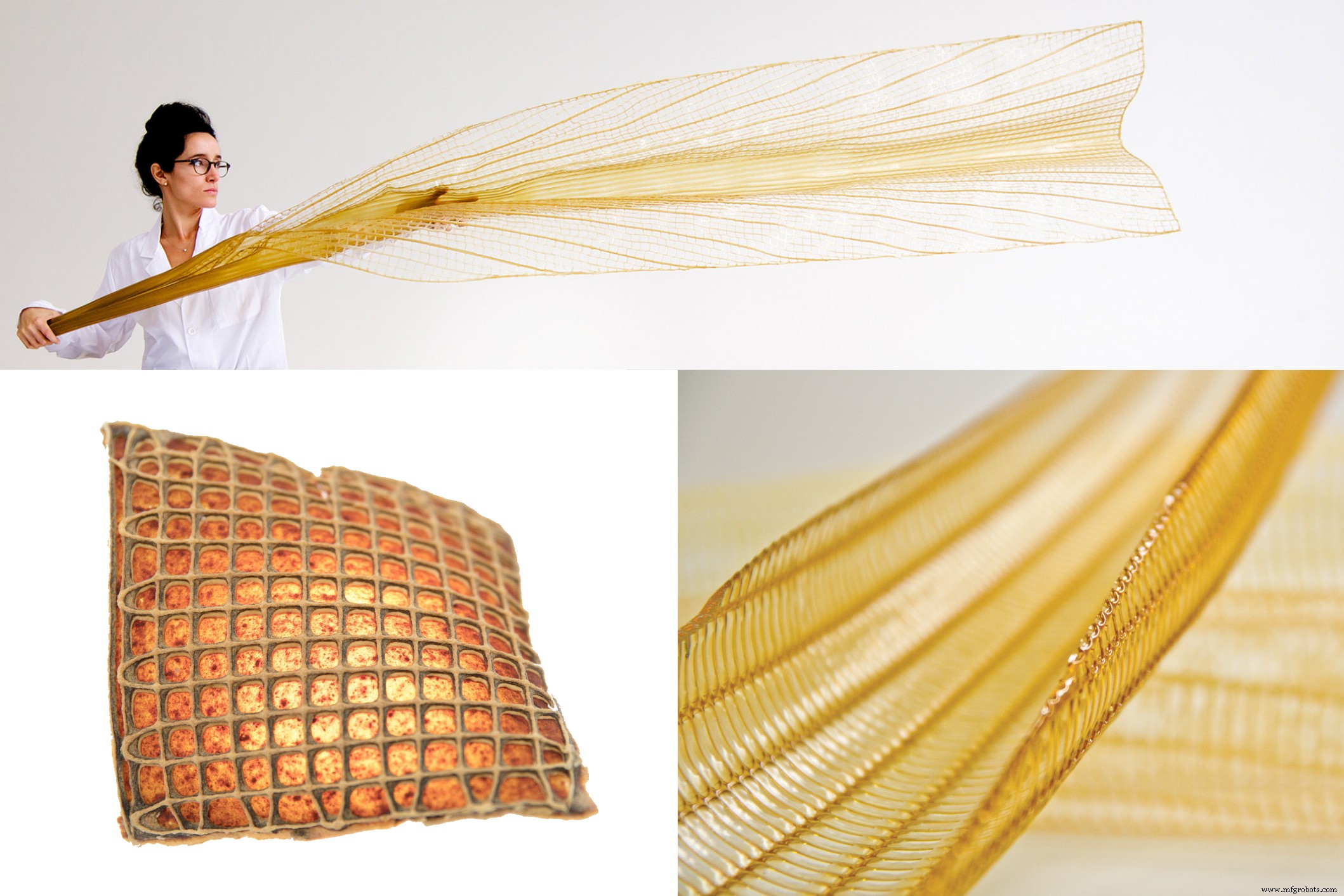
A natureza constrói estruturas que são incrivelmente fortes, versáteis e adaptáveis, crescendo e funcionando em resposta ao ambiente - pense em árvores, ossos e quitina. O último forma ambas as camadas rígidas e articulações flexíveis de crustáceos. As construções da natureza produzem pouco ou nenhum desperdício, requerem muito pouca energia e são recicladas no final de sua vida funcional. Em contraste, as construções feitas pelo homem são tipicamente prescritivas, consomem grandes quantidades de energia, geram lixo tóxico e, em sua maioria, não são recicladas. De acordo com dados de 2018 da Agência de Proteção Ambiental dos EUA, o percentual de materiais reciclados é de apenas 9% para plásticos (sem alteração desde 2010), 25% para vidro e 33% para metais (ambos abaixo de 2010). Embora o design e a fabricação digital estejam avançando rapidamente e permitindo a produção de estruturas e componentes multifuncionais sofisticados, essas tecnologias ainda não fizeram os mesmos avanços em sustentabilidade.
Essa foi a inspiração e o objetivo do projeto Water-Based Digital Fabrication desenvolvido pelo Mediated Matter Group do Massachusetts Institute of Technology (MIT, Cambridge, Mass., EUA) Media Lab, iniciado em 2013. Essa iniciativa desenvolveu uma nova manufatura digital tecnologia que combina os materiais naturais mais abundantes da Terra com um sistema de extrusão de múltiplas câmaras, controlado por robôs, que deposita várias concentrações de soluções de biocompósitos - a primeira foi a quitina das cascas de crustáceos e ácido acético - para criar estruturas com propriedades anisotrópicas. Os gradientes nas propriedades mecânicas, químicas e ópticas são produzidos em escalas de comprimento de milímetros a metros, alcançando não apenas geometrias exclusivas e multifuncionalidade, mas também o potencial para automontagem estrutural. Por exemplo, as deposições úmidas podem ser projetadas para formar formas (por exemplo, cilindro) à medida que secam, em resposta a tensões de evaporação direcional dentro dos compósitos de multicamadas.
Essa fabricação digital baseada em solução foi concebida como uma ponte entre os ambientes biológico e construído, com aplicações potenciais em painéis arquitetônicos sustentáveis, embalagens recicláveis e bens de consumo ou peças automotivas leves e biodegradáveis. O MIT acabou explorando compósitos usando microfibras de celulose, pectina, algas e nanoplacas de cerâmica. Mas e se você pudesse combinar esta deposição digital à base de água com as tecnologias de extrusão aditiva reforçada com fibra curta e contínua que avançam rapidamente nos compósitos impressos em 3D de hoje?
Por que solução de quitosana?
Os experimentos iniciais no projeto de Fabricação Digital à Base de Água usaram quitosana, derivada da quitina. O segundo polímero natural mais abundante na terra depois da celulose, a quitina tem uma estrutura química semelhante à celulose e compreende não apenas as conchas de alto módulo e alta resistência dos crustáceos e insetos, mas também o tecido forte, porém flexível, encontrado em suas articulações. Materiais naturais - especialmente polímeros e polissacarídeos como quitina e celulose - fornecem um vasto recurso renovável produzido a taxas muito mais altas do que os polímeros sintéticos feitos pelo homem, explica Laia Mogas-Soldevila, uma das principais pesquisadoras do MIT neste projeto. Ela afirma que os derivados de polissacarídeos podem substituir os polímeros de base petroquímica existentes, fornecendo novas combinações de propriedades e permitindo uma fabricação mais sustentável.
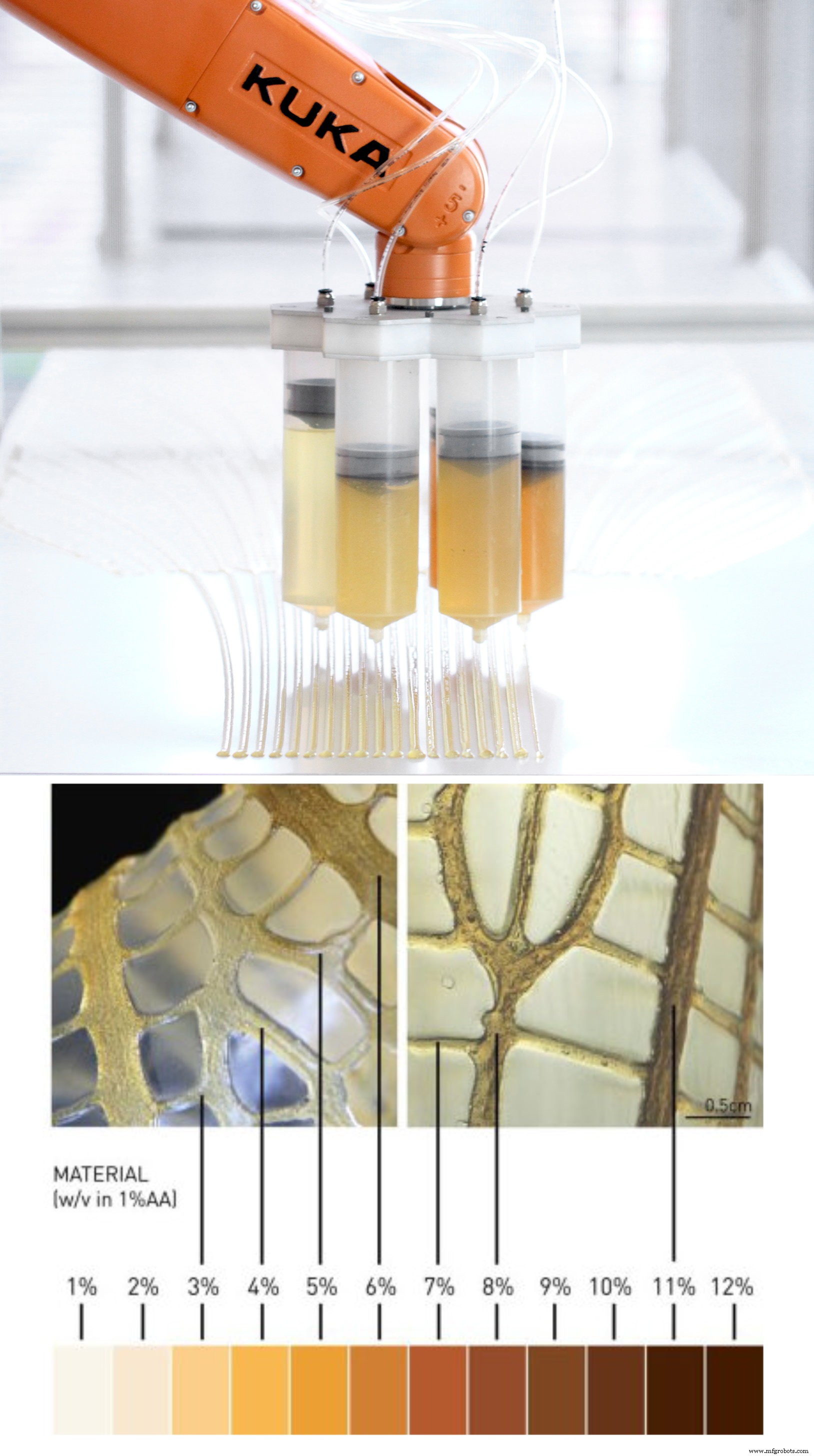
Mogas-Soldevila oferece uma excelente visão geral do desenvolvimento da tecnologia do MIT em sua tese de 2015, “Design e fabricação digital à base de água:Explorações de materiais, produtos e arquitetura na impressão de quitosana e seus compostos”. Ela explica que a ideia de usar fabricação digital baseada em solução veio do estudo de métodos de biofabricação com base em jato de tinta e bico para produzir materiais macios como suportes para o crescimento do tecido.
Foi decidido tentar a deposição 3D baseada em bico usando pó de quitosana processado em um gel em concentrações de peso para volume (p / v) de 1-12% usando ácido acético a 4% p / v em solução aquosa. Esses hidrogéis variaram de um líquido translúcido com viscosidade como mel aquoso na concentração de 3%, a um material opaco com consistência de borracha natural na concentração de 12% (Fig. 1). Resultados iniciais de depositado e seco os filmes de quitosana mostraram uma resistência à tração final de 40 megapascais, que Mogas-Soldevila descreveu como comparável ao polímero de náilon ou madeira na direção da fibra. As estruturas foram fabricadas e curadas em temperatura ambiente.
Nova plataforma de manufatura digital
A plataforma de fabricação de aditivos robóticos personalizados que o MIT projetou para depositar os géis de quitosana combinou um braço robótico de seis eixos Agilus KR1100 KUKA (Augsburg, Alemanha) (uma plataforma de 54 quilogramas com carga útil de 10 quilogramas e repetibilidade / precisão de ± 0,03 milímetros) com um efetor final baseado em extrusão. O novo efetor final continha seis barris para os hidrogéis de quitosana conectados a um sistema de pressão de ar controlado por computador que incluía pressão de ar positiva (tanque de ar comprimido) e negativa (bomba de vácuo) com um regulador PSI digital e motores de passo duplo para controlar a extrusão.
Este efetor final pesava 4 kg, incluindo seringas carregadas e material de deposição. As taxas de fluxo típicas variaram de 8-4.000 milímetros cúbicos por segundo usando bicos com um diâmetro interno medindo 0,5-8 milímetros. O movimento linear do sistema variou de 10-50 milímetros por segundo. A área de deposição era de 1.000 milímetros de comprimento por 500 milímetros de largura; no entanto, as limitações de comprimento foram posteriormente removidas por meio de uma cama de impressão deslizante.
Os motores de passo, o sistema pneumático e o braço robótico foram controlados digitalmente para coordenar as relações de alimentação / velocidade, permitir relações de mistura e taxas de extrusão variáveis e ajustar a pressão de deposição e velocidade em tempo real com base nas geometrias de extrusão desejadas e propriedades do material. O movimento robótico e a extrusão não foram explicitamente ligados - ou seja, ambas as funções eram independentes uma da outra - o que permitiu o controle independente de cada seringa motorizada, bem como o deslocamento do efetor final do braço robótico. O sistema produziu com sucesso formas 3D em grande escala sem moldes e alcançou uma ampla gama de formas geométricas com propriedades estruturais variáveis.
Design digital para deposição
Os testes iniciais de fabricação foram baseados em estruturas biológicas como folhas e asas de libélula. Uma estrutura longitudinal principal forneceu forma global, feita com depósitos de diâmetro mais espesso e concentrações de material mais altas para rigidez. Estruturas secundárias foram então formadas por redes depositadas de materiais de menor diâmetro e menor concentração. O sistema de manufatura usou várias técnicas para construir essas estruturas:aplicação de diferentes soluções de concentração ao longo de certos caminhos, controle digital da pressão durante a deposição para controlar a largura e altura do material e repetindo a estratificação. Essas estratégias foram codificadas nas instruções de posição, velocidade, pressão e material enviadas em tempo real para o robô KUKA (posicionamento) e efetor final de extrusão (deposição).
Para começar, as estruturas foram modeladas em um programa CAD e, em seguida, um software de fatiamento personalizado converteu em camadas impressas. O sistema de controle digital testou e otimizou os caminhos de deposição. Caminhos de ferramentas geométricas que fornecem controle e operação do sistema de extrusão foram projetados com o software de modelagem Rhino3D (Robert McNeel and Associates, EUA) e seu plugin de script Grasshopper.
O sistema então codificou uma série de parâmetros independentes associados ao design digital, bem como propriedades básicas mecânicas e químicas dos materiais. Também moderou restrições dependentes da plataforma dadas pelo sistema de fabricação, como viscosidades, taxas de cisalhamento, tipos de barril, tempos de resposta de hardware e / ou tamanho do envelope. Todos esses parâmetros foram então combinados com específicos do projeto variações como tipo de bico, composição do material e mapas de pressão dependentes do tempo. Os cálculos resultantes geram as taxas de fluxo necessárias, padrões de recarga do barril e velocidades de posicionamento. Finalmente, instruções de fabricação personalizadas foram geradas, codificando comandos de movimento e extrusão para os sistemas de posicionamento e deposição, respectivamente.
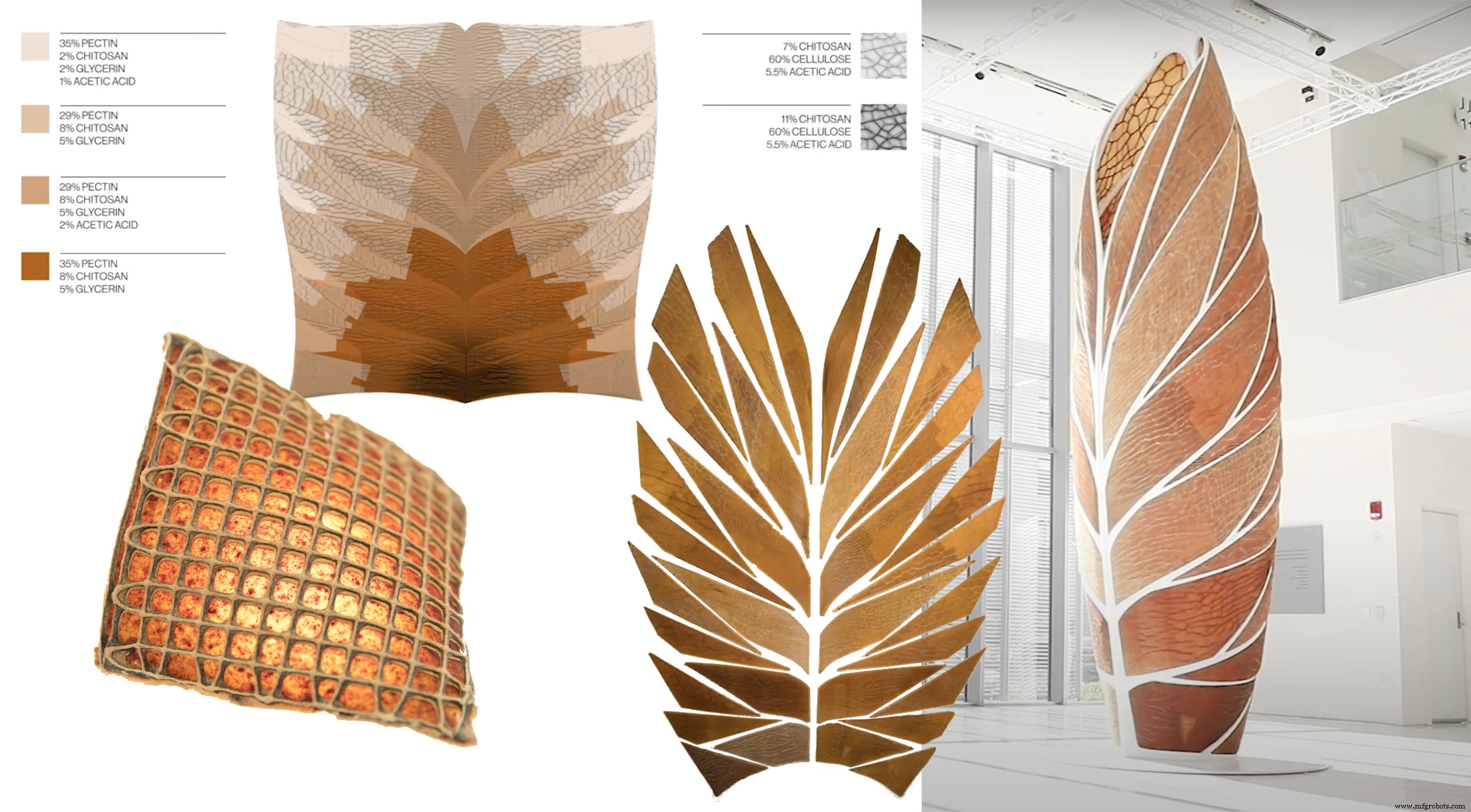
Exploração de novas estruturas
Os testes de fabricação descritos por Mogas-Soldevila incluem uma estrutura de 50 centímetros de comprimento inspirada nas asas de uma libélula. Suas “veias” estruturais foram feitas de gel de quitosana engrossado com pó de alginato de sódio natural, sobre o qual uma membrana transparente resistente à tensão de gel de quitosana a 3% foi sobreposta. Devido às características de autorreparação dos materiais, a membrana foi colada às veias durante a deposição. Este conceito foi posteriormente explorado em uma variedade de estruturas em forma de folha de até 3 metros de comprimento. Em outro exemplo, uma grade de 5 x 15 milímetros foi depositada plana usando uma solução de microfibra de celulose em gel de quitosana a 2%. À medida que secou, formou um cilindro de 50 centímetros de comprimento, usando a capacidade de projetar tensões de evaporação interna conforme discutido acima.
Esta tecnologia foi iniciada por Jorge Duro-Royo, arquiteto e engenheiro e pesquisador principal do MIT Mediated Matter Group sob o Prof. Neri Oxman, e posteriormente desenvolvida nos projetos Aguahoja onde estruturas semelhantes a pele ("hojas") foram criadas e moldadas com soluções à base de água ("agua"). Aquahoja I incluiu um pavilhão arquitetônico de 5 metros de altura (Fig. 2) e uma biblioteca de experimentos materiais que foram exibidos em 2018 e então adquiridos pelo Museu de Arte Moderna de São Francisco (SFMOMA, Califórnia, EUA) para sua coleção permanente . Aguahoja II fez parte de uma exposição de 2019 co-organizada pelo Cube Design Museum (Kerkrade, Holanda) e pelo Cooper Hewitt, Smithsonian Design Museum (Nova York, N.Y., EUA).
A plataforma de fabricação robótica nos projetos Aguahoja evoluiu para incluir sistemas robóticos e baseados em pórticos. O pavilhão compreendia 95 segmentos individuais impressos em 3D. A lombada branca foi impressa usando um sistema de modelagem por deposição fundida F900 pronto para uso (FDM) e termoplástico de acrilonitrila estireno acrilato (ASA). Os múltiplos painéis biocompósitos foram projetados com vários graus de rigidez, flexibilidade e opacidade para criar regiões que servem como estrutura, janela e filtro ambiental. Alguns dos materiais em Aguahoja I mudam em resposta à umidade e ao calor, outros escurecem ou clareiam com a mudança das estações. Os materiais variam de frágeis e transparentes a flexíveis e semelhantes a couro, mas todos podem ser programados para se degradar na água (por exemplo, chuva), restaurando assim os blocos de construção constituintes do ecossistema natural.
Desde então, Mogas-Soldevila completou um doutorado no The Silklab dentro da Tufts Biomedical Engineering (Medford, Mass., EUA), examinando como usar seda e outras fibras e materiais naturais, incluindo aqueles com os quais ela trabalhou no MIT. Ela agora é professora assistente de Arquitetura na Escola de Design Stuart Weitzman da Universidade da Pensilvânia, onde leciona e pesquisa design orientado a materiais na interseção da sustentabilidade com as ciências da vida de ponta. Alguns de seus trabalhos recentes podem ser encontrados em dumolab.com. “São materiais que vêm da natureza e são facilmente funcionalizáveis - podemos misturá-los, dopá-los e transformá-los. Na verdade, podemos ajustá-los para capacidades de fabricação específicas. Estamos analisando o que vem por aí amanhã. ”
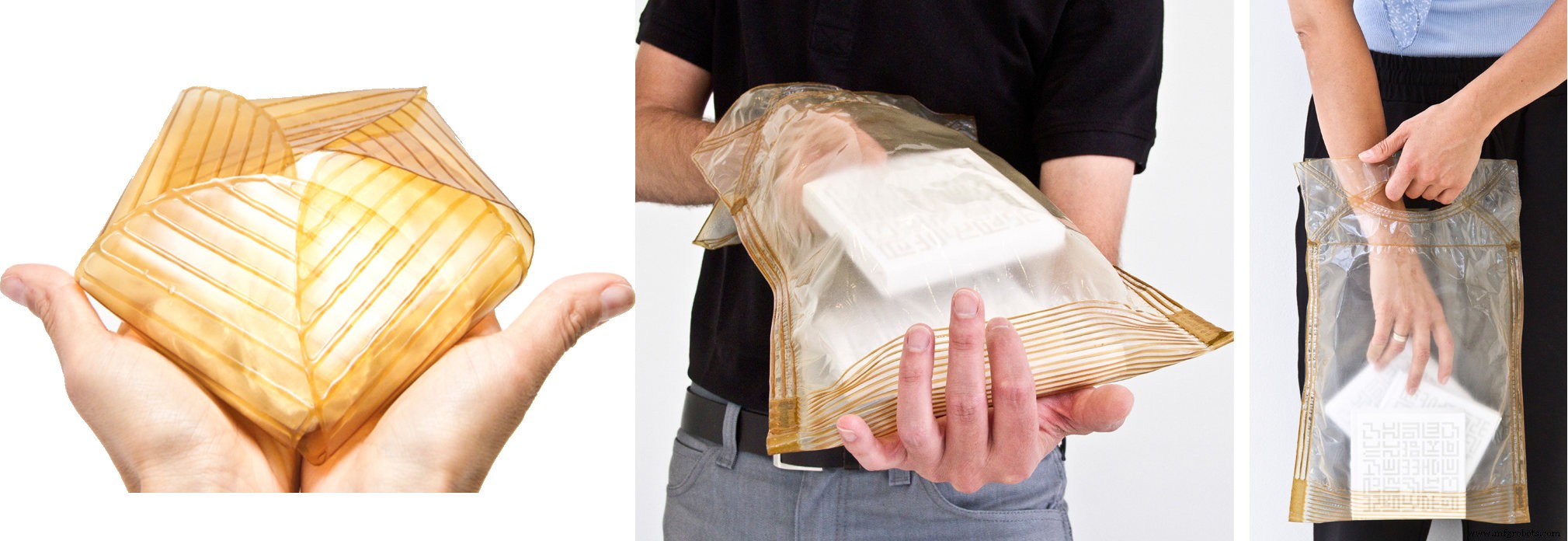
Material compósito
- Uma introdução à fabricação de metal
- Uso do voltímetro
- Por que digital?
- Propriedades de compostos termofixos em HVAC
- Ferramentas de alta qualidade para compostos termofixos
- Razões para usar compostos termofixos em seu produto
- Compósitos de fibra de carbono em um rolo em rodas automotivas
- RS Electric Boats seleciona Norco para a fabricação de compostos
- Compostos de alto desempenho em Israel
- O que é uma força de trabalho digital?