O design Liftgate coloca o enrolamento de filamento modificado em teste
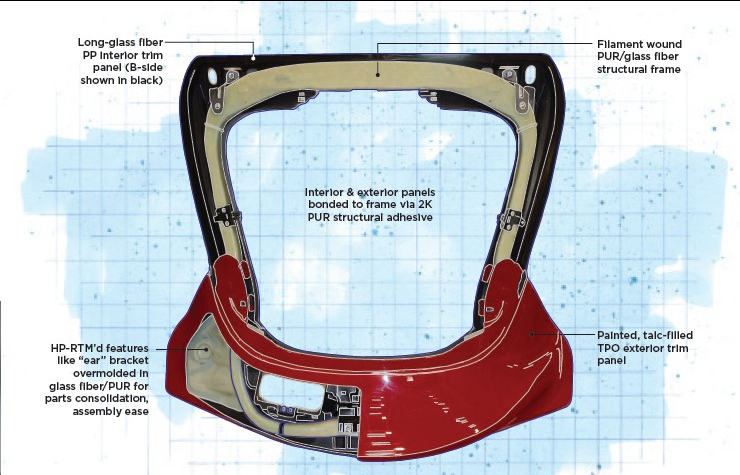
As portas elevatórias automotivas, ou portas traseiras, estão lentamente mudando de metais para materiais compostos por décadas. Embora não tenha sido até 2013 que a primeira porta elevatória totalmente de plástico / composto, sem estrutura de suporte de metal, foi comercializada, a maioria das portas elevatórias de hoje ainda apresenta este componente de suporte no qual revestimentos externos e painéis internos são fixados, especialmente em equipamentos esportivos maiores e mais pesados. veículos utilitários (SUVs) e veículos utilitários crossover (CUVs) com portas traseiras maiores.
No entanto, o que pode muito bem ser a próxima evolução em portas elevatórias compostas estreou em 2019 no Toyota Supra carro esporte da Toyota Motor Corp. (Toyota City, Japão). Uma estrutura composta de filamento enrolado substituiu uma estrutura metálica e é dito que oferece maior rigidez e resistência com menor peso do que as estruturas de metal tradicionais, com maior flexibilidade de design, especialmente em espaços de embalagem apertados. Alegadamente, o processo de enrolamento do filamento foi modificado a tal ponto que, conforme o interesse cresce e as aplicações proliferam, ele pode atender às metas de velocidade e custo da produção de veículos de alto volume. É assim que o design e a tecnologia surgiram.
Fabricação trilateral
Magna International Inc. (Aurora, Ontário, Canadá) é um integrador Tier 1 na América do Norte, mas na Europa, sua subsidiária Magna Steyr AG &Co. KG (Graz, Áustria) também projeta e monta carros completos para OEMs que precisam de fabricação extra capacidade.
Recentemente, a Magna participou de um programa interessante envolvendo as montadoras Toyota e BMW AG (Munique, Alemanha), que trabalharam cooperativamente em projetos de design e fabricação desde 2013. Para seu esforço mais recente, a Toyota estava tentando reviver seu Supra placa de identificação e fez parceria com a BMW para fornecer design e ajuste para o veículo e um carro irmão, o BMW de 2 lugares Z4 . Os dois veículos compartilham sistemas de motor, suspensão e direção. Magna Steyr montaria os dois carros em Graz, bem como forneceria o Supra com assentos, painéis da carroceria, travas das portas e portas elevatórias. Embora haja muita inovação em ambos os carros, a tampa do compartimento de bagagens incorporada no Supra é onde a inovação em design de compósitos é mais aparente.
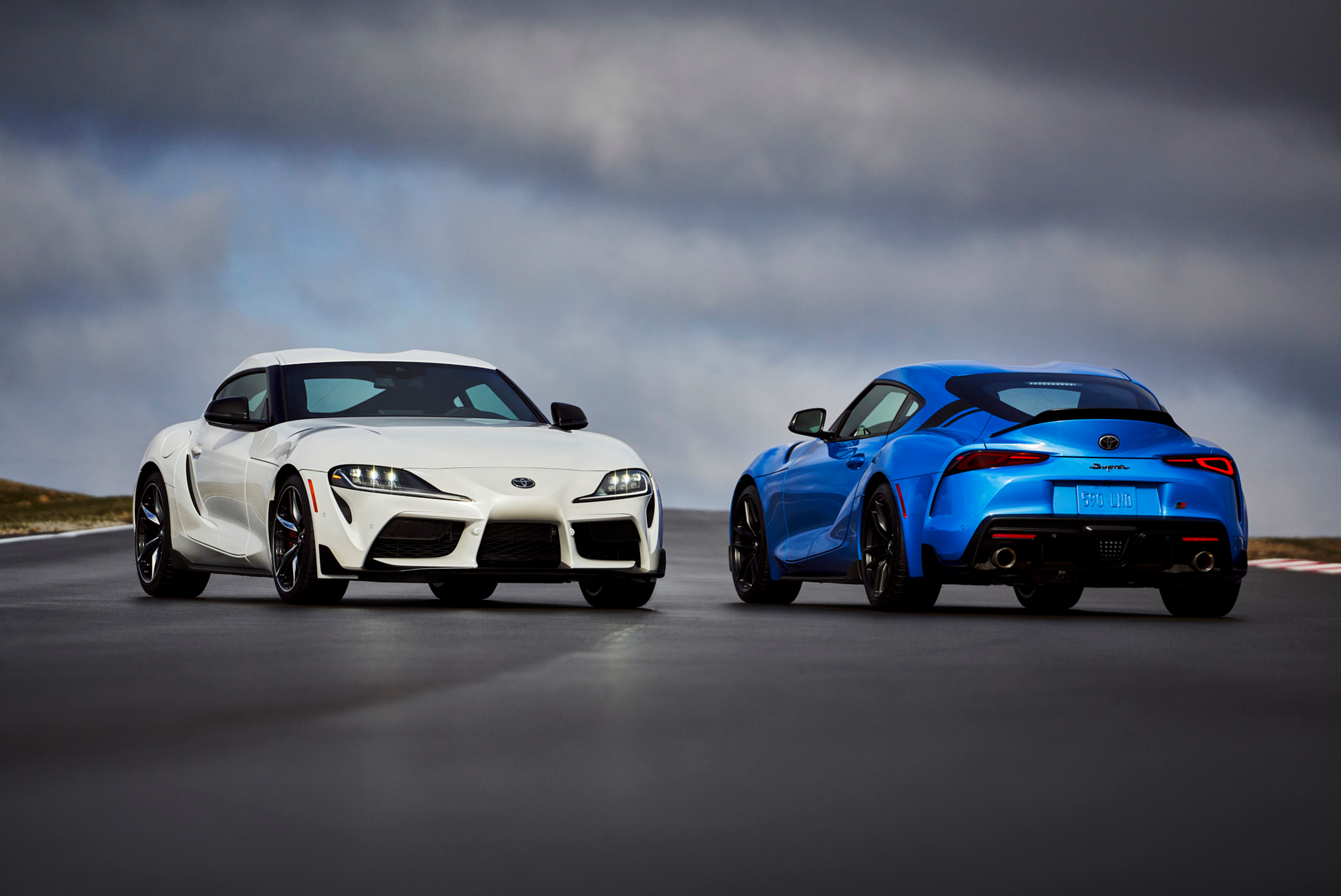
Manchester da Boêmia
Anos antes do envolvimento da Magna com 2020 ano do modelo Supra
“Concluímos que precisávamos de um produto termofixo com alta estabilidade térmica e dimensional”, lembra Riad Chaaya, diretor da linha de produtos globais da Magna - portas elevatórias compostas. “Também sabíamos que precisávamos de uma forma fechada com a capacidade de produzir seções transversais de formatos e espessuras variáveis - necessárias para otimizar o desempenho mecânico, espaço da embalagem, massa e custo - que pudesse ser produzida em um processo capaz de fazer 150.000 peças anualmente. Examinamos muitas tecnologias, incluindo moldagem por sopro, trança e enrolamento de filamento, mas nenhuma atendeu às nossas necessidades. Depois de muitos testes, selecionamos o enrolamento de filamento como a melhor combinação para o que queríamos, uma vez que nos deu o controle das orientações e do número de filamentos para extrair o módulo mais alto com o peso mais baixo. ”
Apesar dos muitos benefícios, havia a preocupação de que o enrolamento de filamento pudesse ser muito lento para a produção automotiva convencional. Além disso, a equipe precisava de um método para iniciar e terminar o processo de enrolamento a fim de criar uma estrutura de formato fechado. Felizmente, embora a equipe não tivesse histórico com enrolamento de filamento, o legado de Liberec na fabricação de têxteis significava que a comunidade local estava cheia de especialistas em enrolamento e enrolamento de filamentos.
“Para nossa sorte, esses especialistas tiveram a paixão de ressuscitar seu know-how tradicional para nos ajudar a aplicá-lo de novas maneiras para atender às necessidades automotivas de alto volume”, acrescenta Dr.-Ing. Josef Půta, líder de tecnologia da Magna Exteriors - República Tcheca.
“Como o enrolamento de filamento tradicional era muito lento para nossas necessidades, nós e nossos parceiros buscamos muitas maneiras de fazê-lo funcionar mais rápido”, lembra Lukáš Strouhal, chefe de industrialização da Magna Liberec. “Nós consideramos maneiras de acelerar cada etapa do processo, bem como fazer as coisas de forma bastante diferente. Embora não possamos dizer muito sobre como fizemos isso, podemos dizer que alcançamos grandes melhorias na velocidade, de modo que nosso processo modificado pudesse se tornar ‘digno automotivo’ ”.
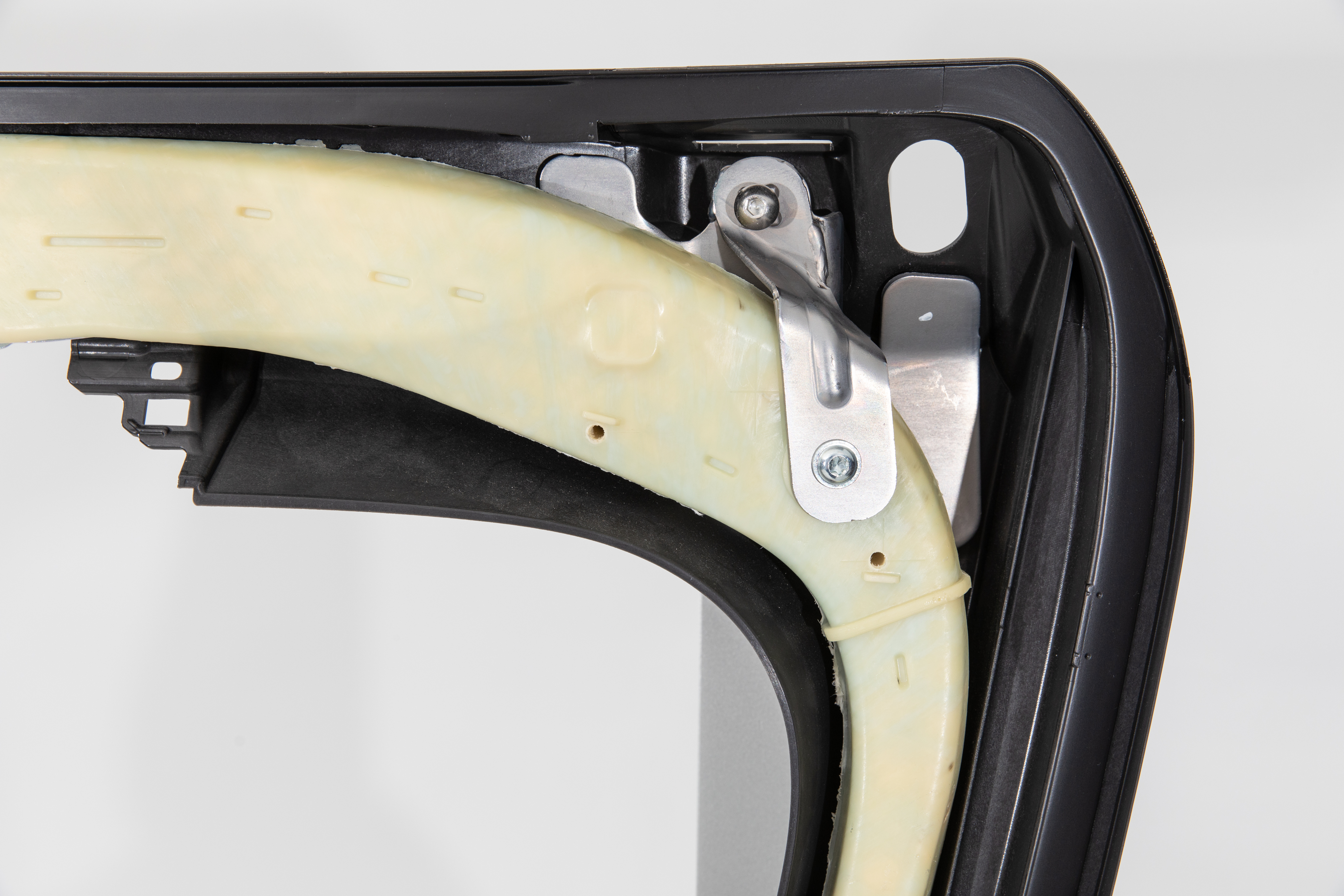
Magna e seus parceiros exploraram muitos sistemas de resina, incluindo epóxi, poliuretano (PUR) e uma mistura de PUR / vinil éster, além de uma variedade de reforços, de vidro a carbono e fibras de basalto. O sistema final apresenta PUR e fibras de vidro, que oferecem o melhor equilíbrio entre eficiência de fibra, desempenho, custo e velocidade de produção.
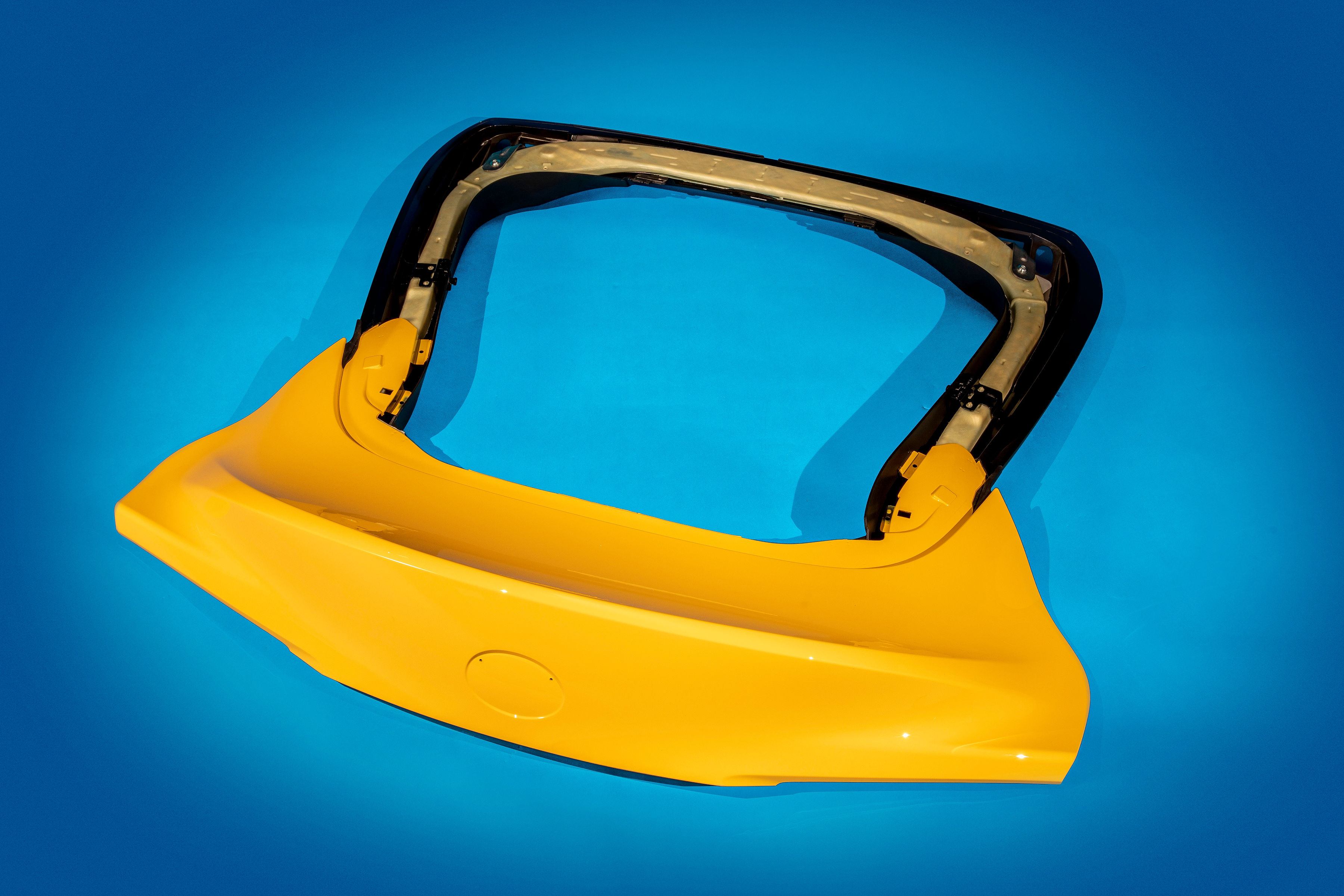
A estrutura do espaço enrolado de filamento genérico da Magna é produzida em três etapas, cada uma cuidadosamente otimizada para velocidade. Primeiro, um núcleo de PUR celular rígido é produzido por meio de moldagem por injeção de reação (RIM); segundo, esse núcleo, que funciona como um mandril, é enrolado com fibra de vidro; e terceiro, essa estrutura da ferida é então infundida com PUR e consolidada no processo de moldagem por transferência de resina de alta pressão (HP-RTM). É tomado cuidado para garantir que o núcleo não entre em colapso durante a infusão / consolidação. Půta explica que muito trabalho foi feito para especificar os tipos de mechas, gomas e resinas utilizadas - exigindo um trabalho próximo com os fornecedores nas modificações do material - além de determinar o número de enrolamentos e a orientação dos filamentos em cada camada. Não é de surpreender que a empresa tenha recebido várias patentes cobrindo tudo, desde o design e a produção do núcleo até a bobinadeira de filamento, além de segredos comerciais adicionais que mantêm em segredo.
“Fizemos várias inovações em cada etapa do processo e produto”, explica Strouhal. “Você poderia rasgar uma de nossas armações, ver as formas e geometrias usadas e ainda se perguntaria por que e como fizemos isso.”
Embora a equipe da Magna Liberec não tivesse desenvolvido sua tecnologia de estrutura espacial para uma aplicação específica, eles estavam prestes a obter uma oportunidade interessante de usá-la.
Plataforma desafiadora
A Magna tem uma longa história de produção de portas elevatórias para veículos de passageiros. A empresa supostamente construiu as primeiras portas elevatórias totalmente em olefinas na América do Norte e na Europa para o BMW i3 2013 carro elétrico urbano, e projetou e construiu uma plataforma elevatória de última geração totalmente em olefina para o jipe 2019 Cherokee da FCA NA LLC (Auburn Hills, Michigan, EUA) SUVs. Dado que a produção da porta traseira foi um resultado para o Supra No programa, a Magna não se baseou apenas no trabalho realizado em Liberec, mas também em sua longa história de conversão de estruturas metálicas de porta traseira em compósitos e plásticos.
“O Supra A porta de embarque oferecia uma série de desafios imediatos ”, lembra Chaaya. “Em primeiro lugar, o espaço da embalagem era muito limitado, o que significa que as tolerâncias eram muito estreitas e o coeficiente dos valores de expansão térmica linear deve ser gerenciado com cuidado para manter as comportas abrindo e fechando livremente. Em segundo lugar, a forma desta porta era ainda mais desafiadora. A Toyota não queria apenas uma porta traseira mais leve, mas tinha requisitos de estilo muito específicos para a forma como a traseira do veículo era coberta. Terceiro, com os volumes de construção projetados do veículo, as ferramentas para atingir essa forma em metais seriam muito caras. Na verdade, concluímos que a estrutura da porta traseira não poderia ser produzida em uma única peça de metal e ainda atender aos requisitos de design e desempenho da Toyota. Isso significava que a estrutura do espaço tinha que ser feita de compostos e, mais especificamente, compostos termofixos. ”
O revestimento externo seria um painel de TPO reforçado com talco moldado por injeção, pintado para lidar com a forma agressiva, enquanto o painel interno seria de polipropileno de vidro longo (PP); ambos seriam unidos à estrutura com um adesivo PUR 2K estrutural. Chaaya acrescenta que muito trabalho foi feito para otimizar a estrutura do espaço e concluir a porta traseira para atender aos requisitos de carga de torção. Um desafio inicial foi encontrar uma maneira de simular com precisão as propriedades do material para obter uma correlação precisa entre os resultados previstos e medidos.
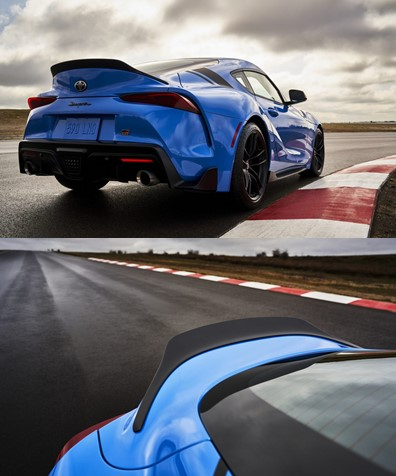
“Foi uma luta difícil conseguir uma boa correlação com nossos modelos de materiais, pois tivemos que simular cada camada do enrolamento e incorporar a forma, os raios e os próprios requisitos de enrolamento”, acrescenta. “Embora tenhamos começado com 20%, depois de muitos ajustes e determinar a melhor forma de melhorar nossa rigidez, nossas previsões finais estavam muito próximas. Em um quadro tão grande, também conseguimos manter as tolerâncias dimensionais de 1 milímetro. ”
Muitos benefícios
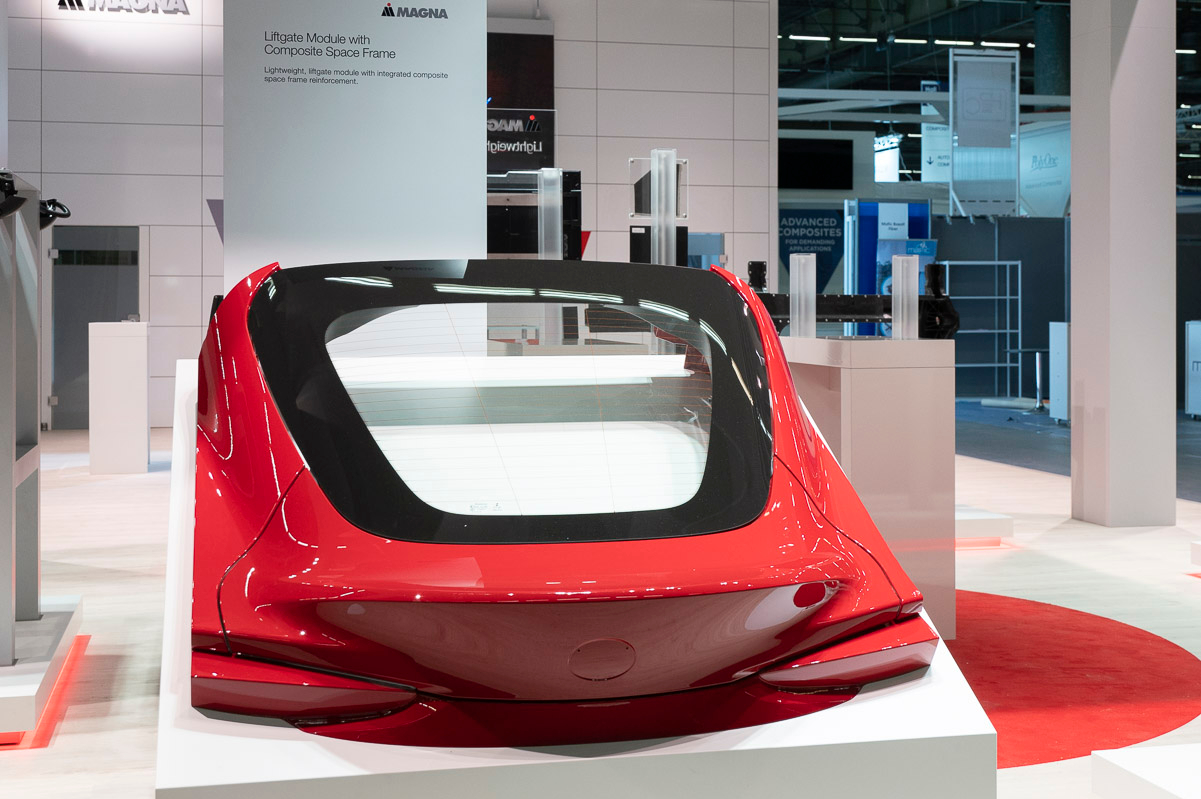
A estrutura final em formato de donut apresenta diâmetros e espessuras de parede variáveis, mas tem um diâmetro nominal de 50-60 milímetros. Além de um pequeno suporte no canto e acessórios rígidos como travas e dobradiças, além de folha para aterrar as antenas integradas, toda a estrutura - que tem 104 x 111 centímetros - é inteiramente composta. Mesmo os suportes de “orelha”, usados para conectar o painel de acabamento interno à metade inferior da tampa do compartimento de bagagens, são compostos e fabricados via HP-RTM. Embora a estrutura composta seja 10% mais leve do que uma estrutura de metal comparável, os efeitos de descompounding em massa significam que a porta traseira completa é ~ 20-25% mais leve do que uma porta traseira metálica. Plataformas elevatórias mais leves requerem menos esforço para os consumidores abrirem / fecharem, são mais fáceis para um trabalhador instalar durante a montagem do veículo, economizam combustível durante a vida útil do veículo e fornecem o que Strouhal descreve como "um som sólido incrível" quando a porta elevatória fecha. O sistema composto também eliminou etapas como bordas de bainha e pontos / juntas de soldagem necessários com portas elevatórias de metal.
Chaaya sugere que sua empresa tem outro grande projeto automotivo de filamento enrolado em andamento. Ele também diz que Magna vê outros usos para a tecnologia além das portas elevatórias. “Portas, tampos, capôs, FEMs (módulos frontais) e até veículos autônomos - como um ônibus que é composto de uma estrutura envolta em vidro - poderia usar tal estrutura de espaço ”, acrescenta. “E nem teria que ser escondido. Se usássemos tecido de fibra de carbono, seria um sinal de prestígio deixar essa linda superfície exposta e não esconder a moldura por dentro ”.
Resina
- O Guia do Iniciante na Fabricação de Filamentos Fundidos (FFF)
- A função do design auxiliado por computador (CAD) na impressão 3D
- Os desafios do design de produto
- O Triodo
- Desenho industrial na era da IoT
- Otimizando a linha de alimentação RF no design de PCB
- Novas tecnologias e mercados no evento World of Filament Winding
- Enrolador de filamento Roth para facilitar grandes cortes de peso / custo Ariane 6
- Os benefícios da prototipagem de PCBs
- Conheça o significado da BOM no projeto de PCB