Moldes CFRP de impressão 3D para flaperon RTM, exoesqueletos e mais
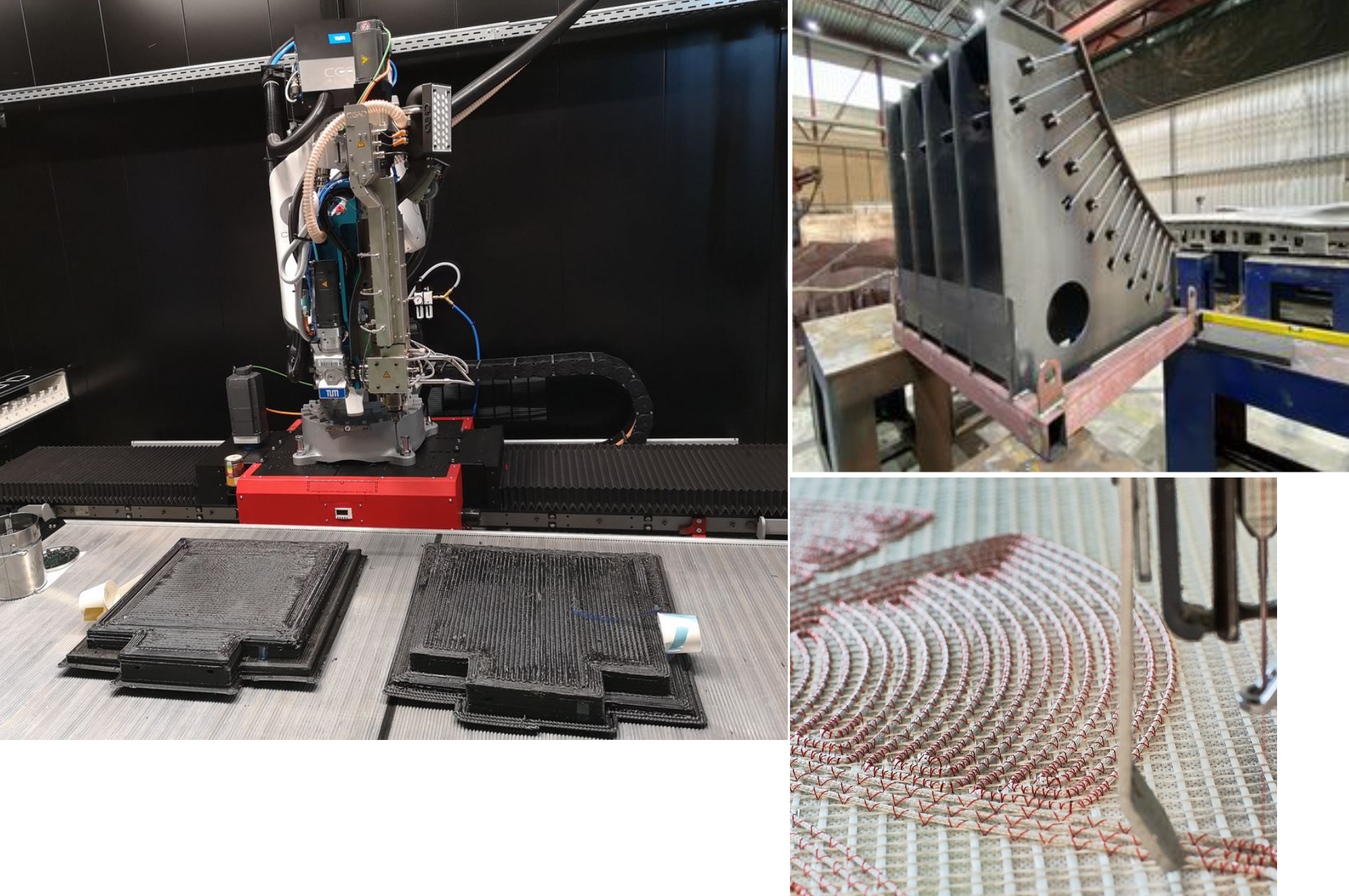
A Cátedra de Compostos de Carbono (Lehrstuhl für Carbon Composites ou LCC) foi criada em 2009 no departamento de Engenharia Mecânica da Universidade Técnica de Munique (TUM, Munique, Alemanha) com financiamento da SGL Carbon (Wiesbaden, Alemanha). Sua missão é realizar P&D em materiais, processos e aplicações de polímero reforçado com fibra de carbono (CFRP), incluindo projetos de simulação e testes. Uma “cadeira” no sistema universitário alemão é a menor unidade composta por um professor e sua equipe. A equipe do LCC é liderada pelo Prof. Dr. -Ing. Klaus Drechsler e atualmente emprega 30 pesquisadores em tempo integral. Embora o financiamento da SGL tenha chegado ao fim em 2016, o LCC continuou sua liderança em P&D de compósitos, que inclui a construção do molde para a metade inferior do Demonstrador de Fuselagem Multifuncional (MFFD), veja a barra lateral abaixo, e agora também inclui impressão 3D / aditivo fabricação.
Este blog começou quando o CEAD (Delft, Holanda) me informou que a LCC havia comprado um de seus sistemas AM flexbot baseados em extrusora para impressão 3D usando um braço de robô. Minha entrevista subsequente com o pesquisador do LCC, Patrick Consul, no entanto, revelou um tesouro de projetos, incluindo COMBO3D, dentro do Clean Sky 2, para imprimir em 3D um molde RTM de composto termoplástico para a produção de um flaperon composto de termofixo e EMOTION para produzir a ferramenta para moldar a metade inferior do Demonstrador de Fuselagem Multifuncional (MFFD) composto termoplástico da Clean Sky 2, bem como uma ferramenta parcial secundária para demonstrar como a mesma fuselagem pode ser produzida por consolidação direta in situ (fora da autoclave). Achei interessante toda a discussão de como o TUM chegou a este ponto e para onde está se dirigindo.
Metade inferior do molde MMFD
Veja meu blog de fevereiro de 2020:“Provando soldagem LM PAEK para Demonstrador de Fuselagem Multifuncional”. Esta barra lateral foi retirada do artigo de fevereiro de 2020, “Desenvolvimento de um Demonstrador de Fuselagem Multifuncional”, de Bas Veldman, gerente de programa do MFFD na GKN Fokker (Hoogeveen, Holanda).
O invólucro da metade inferior do MFFD consiste em uma película termoplástica, endurecida com longarinas soldadas, clipes e armações. O processo de fabricação a ser demonstrado compreende três etapas principais:
- A fita pré-impregnada para a grande pele do demonstrador é colocada em uma mesa plana inclinada pela máquina AFP a laser existente da NLR.
- Layups são transportados roboticamente com ventosas para um molde de consolidação feminino e colocados nele sem aquecimento.
- Após o ensacamento a vácuo, a pele é consolidada em uma autoclave.
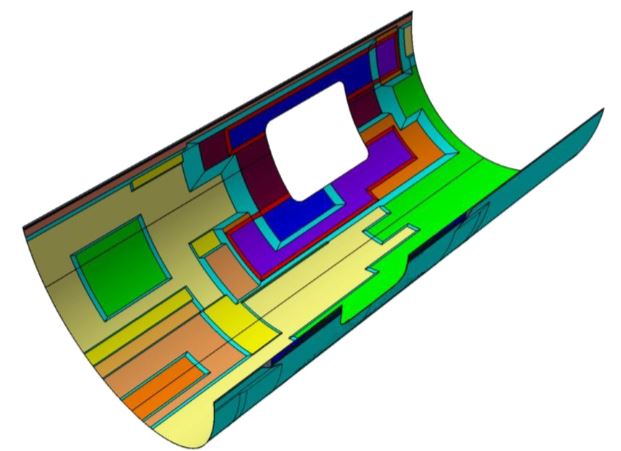
O uso de um molde de consolidação fêmea oferece uma superfície muito mais simples (plana) do que para uma ferramenta macho, ao mesmo tempo que controla diretamente as restrições aerodinâmicas na qualidade da superfície externa da pele.
O projeto MFFD também exige fora da autoclave processos a serem investigados - começando em paralelo ao grande demonstrador multifuncional da fuselagem - em um subsequente demonstrador de menor porte. Em particular, compósito termoplástico in-situ a fabricação em que a consolidação é obtida durante o lay-up, será considerada, uma vez que pode eliminar completamente a etapa de autoclave e, portanto, reduzir a fabricação a um procedimento de uma única etapa.
Molde aprimorado para fuselagem termoplástica dentro e fora da consolidação de autoclave, ou EMOÇÃO (https://cordis.europa.eu/project/id/864474), é o projeto Clean Sky 2 para a produção de ferramentas de revestimento inferior MFFD. “Parece simples”, diz Patrick Consul do coordenador do projeto, TU Munich, “mas na verdade é bastante desafiador, pois precisa ser aquecido a 400 ° C. Isso está bem acima da faixa de temperatura em que Invar36 não tem um CTE significativo [coeficiente de expansão térmica]. ” Invar é comumente usado para ferramentas de moldagem de compósitos devido à sua baixa expansão durante os ciclos de cura em alta temperatura. No entanto, o CTE do Invar aumenta com a temperatura. “O desafio”, observa Consul, “será controlar a expansão térmica durante o aquecimento e resfriamento para o molde de 8 por 4 metros e a pele da fuselagem durante a cura”.
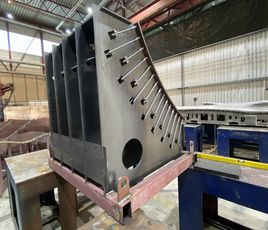
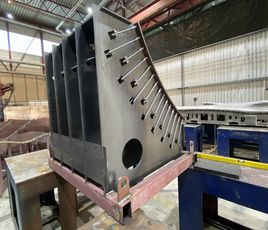
Progressão na manufatura aditiva
“Somos 8-9 pessoas trabalhando na manufatura aditiva dentro do LCC”, diz Consul. Ele começa a história deste trabalho com a compra pela LCC de uma máquina de colocação de fita composta termoplástica assistida por laser da AFPT (Dörth, Alemanha) em 2012. Mais tarde, ela adicionou uma máquina Coriolis Composites (Quéven, França) para permitir a colocação automática de fibra (AFP ) de prepregs termofixos. As primeiras impressoras desktop baseadas em filamento foram adquiridas em 2017. “Também entrei em 2017 para ajudar no desenvolvimento de novos aplicativos e projetos de pesquisa, incluindo a redação de propostas, por exemplo, para a Clean Sky 2.” Ele explica que os projetos do Clean Sky 2 são premiados com base em propostas enviadas aos gerentes de tópicos em resposta a Chamadas de Propostas (CFP) divulgadas publicamente. A LCC teve sucesso em suas propostas para o projeto CFP08 COMBO3D e o projeto CFP09 EMOTION. Ambos são discutidos abaixo.
“Temos alguns outros projetos, alguns voltados para impressão 3D com reforços de fibra contínua”, diz Consul. “Outros usam um cabeçote de impressão integrado a laser para pré-aquecer o substrato composto para imprimir em peças CFRP já consolidadas ou para aumentar a resistência ao cisalhamento interlaminar (ILSS) entre as camadas impressas. Outro projeto explora aplicações de ferramentas, por exemplo, onde você tem um baixo número de peças compostas especializadas. ”
“Esses projetos são continuamente suportados por simulações numéricas para prever o comportamento das peças manufaturadas dos aditivos durante e após o processo de impressão”, continua. “O LCC também está envolvido em um projeto com o Imperial College of London que visa fabricar exoesqueletos usando CFRP impresso em 3D. Outro projeto pesquisa estruturas reticuladas para otimizar as propriedades das peças impressas em 3D no que diz respeito à rigidez, resistência ou absorção de energia. ”
Progressão em impressoras

“Começamos usando uma impressora 3D simples baseada em FDM (modelagem de deposição fundida) da Apium (Karlsruhe, Alemanha) para imprimir acessórios de teste especializados que precisam de alta rigidez”, explica Consul. “A impressora tinha 3 metros de comprimento por 1 metro de largura com uma alta produção de material para reduzir o tempo de impressão. Embora não pudesse usar fibra contínua, foi bem projetada para impressão com PEEK, PEKK e PEEK reforçado com fibra de carbono picada. Não só utilizava um leito aquecido, mas também uma placa aquecida ao redor da cabeça de impressão, o que ajudava a produzir uma distribuição homogênea da temperatura nas impressões, reduzindo o estresse térmico e garantindo a cristalização ”.
“Também tivemos uma impressora Markforged (Cambridge, Massachusetts, EUA) por um tempo e, em seguida, adquirimos uma Anisoprint [Esch-sur-Alzette, Luxemburgo]”, diz Consul. Embora a impressora Markforged habilitasse o FDM com fibra contínua, a equipe da LCC optou por não mantê-la. “O problema que tínhamos era que o sistema era muito fechado”, explica Consul. “O software fatiador da Markforged era muito difícil de usar para pesquisa porque limitava severamente o que podíamos fazer. Só pudemos imprimir uma camada de material de fibra contínua e, em seguida, uma camada de filamento termoplástico reforçado com fibra curta na parte superior. O divisor que gera o código não aceitaria o código G de nós. Portanto, não havia como dizer à máquina para imprimir da maneira que queríamos com fibra contínua em cada camada, etc. ”
Quando questionado sobre isso, Markforged explica que seus sistemas nunca foram planejados para serem usados para pesquisa, mas sim projetados para serem simples e robustos para uso generalizado na fabricação de peças, utilizando caminhos de fibra baseados em regras e exigindo pouco esforço e tempo para configurar o fatiador . É O software Eiger permite que os usuários configurem camadas individualmente, e o Markforged aceita comentários e prioriza a melhoria da experiência do usuário para seus clientes.
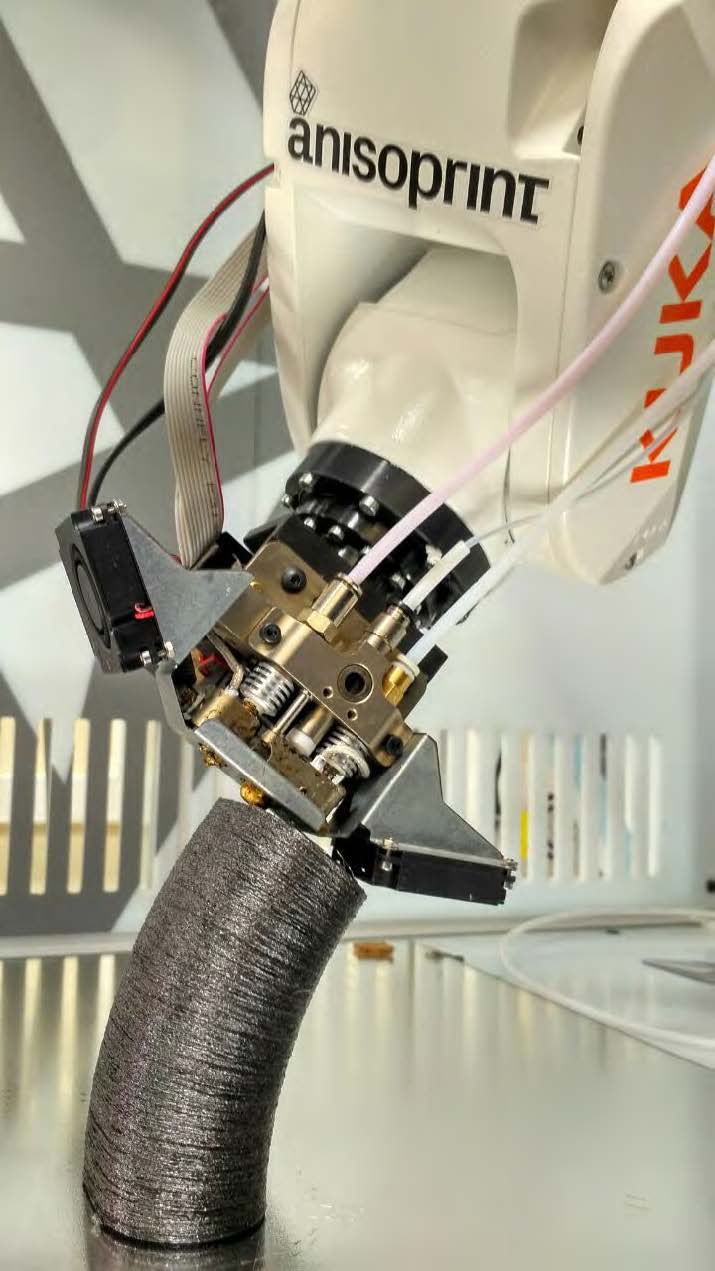
“O Anisoprint, que usa um fatiador de código G totalmente aberto, nos deu mais acesso ao processo”, diz Consul. “Também é capaz de imprimir fibra de carbono contínua e não apenas em camadas 2D, mas também fora do plano, em curvas 3D. Temos uma cabeça de impressão Anisoprint para um pequeno robô Kuka, capaz de produzir peças de 1 metro por 1 metro, que é maior do que a maioria dos desktops, mas pequena para um sistema de robô. "
Mas e quanto à matriz dupla da Anisoprint materiais termoplásticos termofixos (TS-TP)? Conforme explicado em meu blog de 2019 no Anisoprint “... primeiro impregna o reforço de fibra contínua com um termofixo polímero e, em seguida, extrude isso no filamento termoplástico derretido durante a impressão. ” A Consul responde que a adesão entre o filamento de TS e o TP é muito boa. “Em nossos primeiros testes, pudemos obter um conteúdo de volume de fibra maior em comparação com a impressora Markforged, mas isso ocorreu porque pudemos modificar o código G. O cabeçote de impressão Anisoprint empurra o filamento TS para o TP e o coloca. Estamos planejando usar essa impressora para peças de exoesqueleto. É uma maneira fácil de integrar fibras de maior resistência. "
Impressoras de pellets extrudados
A próxima progressão foi para uma impressora em grande escala, primeiro com TP reforçado com fibra curta e, em seguida, TP com fibra contínua. “Primeiro desenvolvemos uma extrusora montada em um robô e, em seguida, nosso interesse pela máquina CEAD surgiu rapidamente. Esperamos integrar fibra contínua em ambos os sistemas no próximo ano ”.
Mas por que você precisou da máquina CEAD se já tinha uma extrusora em um braço de robô? “A extrusora inicial era a versão beta de uma extrusora de pellets Dyze Pulsar, que produz no máximo cerca de 2 kg / h e cerca de 1 kg / h com PAEKs, mas luta com mais de 20% de carregamento de fibra de carbono”, diz Consul. “No entanto, a produção média é menor porque o robô acelera e desacelera frequentemente durante a impressão. Para o COMBO3D, as metades iniciais do molde em pequena escala já exigiam pelo menos 36 kg, portanto, precisávamos de cerca de 48 horas para imprimir uma única metade. Também tínhamos que ter alguém sempre com ele, porque erros, como uma linha de alimentação de material bloqueada ou empenamento de peças, podem acontecer a qualquer momento. ”
Como o demonstrador final COMBO3D é cerca de 10 vezes maior do que as peças iniciais em pequena escala, imprimi-lo usando este primeiro sistema de extrusora não era viável, diz Consul. “Além disso, alguns dos materiais que a Victrex nos forneceu tinham uma viscosidade mais alta e esta primeira extrusora não podia fornecer torque suficiente para extrudir esses polímeros. Com a impressora CEAD, temos uma produção máxima de cerca de 12,5 kg / h e, após algumas horas de testes, obtivemos uma produção média estável de cerca de 5-6 kg / h. Isso nos permitiu imprimir a metade do molde em pequena escala em menos de 8 horas e nos permite usar um maior teor de fibra para reduzir o empenamento, tornando o processo geral mais fácil de controlar. ”
“Portanto, embora o Pulsar já nos permitisse usar pellets, obter uma alta produção de material e tirar proveito dos graus de liberdade de um robô”, continua ele, “a impressora CEAD estende nossas capacidades para peças maiores, maior conteúdo de fibra e uma gama mais ampla de polímeros . O Pulsar preenche a lacuna entre nossas impressoras baseadas em filamentos e o CEAD, não apenas na produção, mas também no tamanho do bico e nos detalhes resultantes das impressões ”.
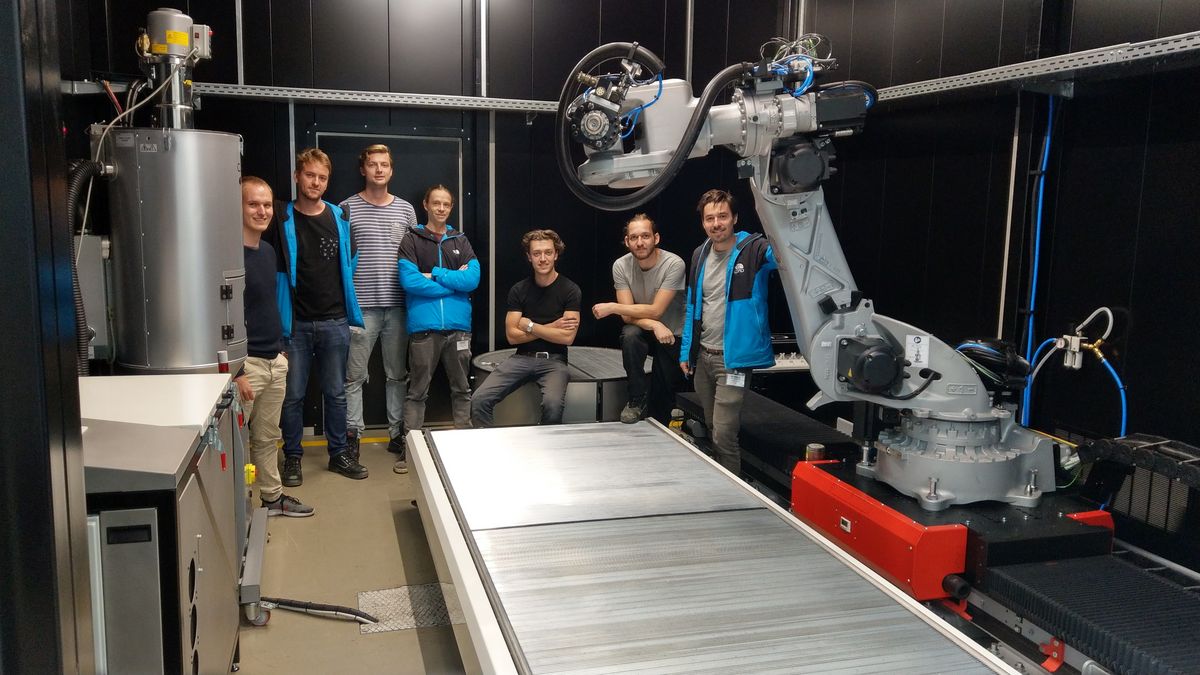
Dados técnicos do CEAD AM Flexbot:
- Dados técnicos do AM Flexbot:
- Impressões de extrusão com base em pellets de até 12,5 kg / h (sem reforço e reforçado com fibra curta)
- Processamento de materiais até 450 ° C
- Volume de construção 3000 x 1200 x 1700 milímetros
- Monte a placa em uma mesa rotativa ou plana (aquecível)
- Retrabalho por meio de uma cabeça de fresagem.
COMBO3D
O objetivo deste projeto Clean Sky 2 é imprimir em 3D um molde para produzir um flaperon composto demonstrador (1,5 por 3 metros) para uma grande aeronave de passageiros, parte do Pacote de Trabalho A-3.1:Asa multidisciplinar para alta e baixa velocidade. O objetivo do uso da manufatura aditiva é reduzir o tempo de espera para a produção de ferramentas. O projeto começou em janeiro de 2019 e terminará em março de 2021. Os parceiros incluem Alpex Technologies (Mils bei Hall, Áustria), especialista em metais leves Leichtmetallkompetenzzentrum Ranshofen (Ranshofen, Áustria) e Victrex (Thornton Cleveleys, Reino Unido), fornecedora do termoplástico de alto desempenho poliariletercetona (PAEK).
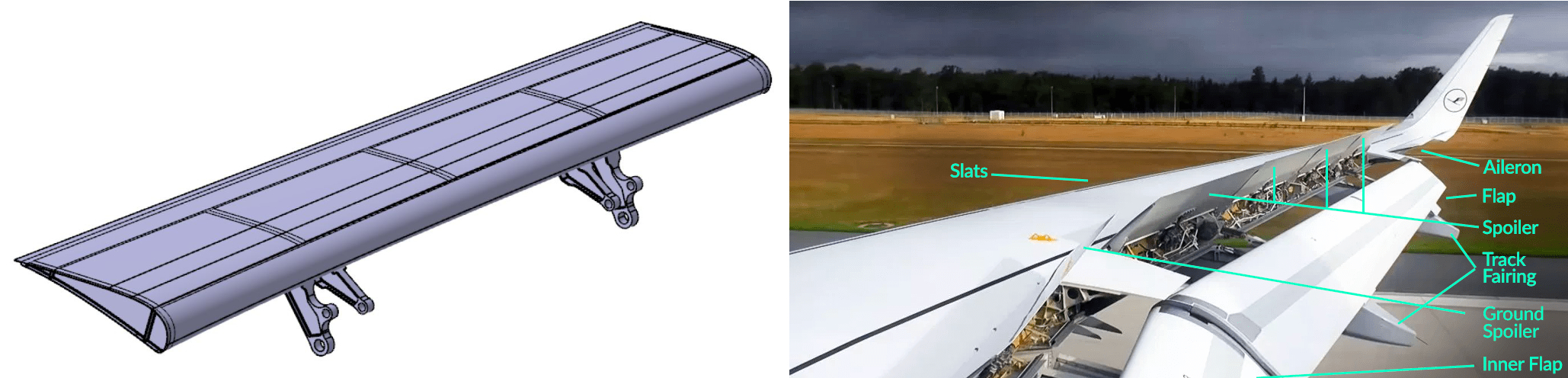
Outra parte importante do projeto é demonstrar que este flaperon de fibra de carbono / epóxi pode ser feito com moldagem por transferência de resina (RTM) em vez de pré-impregnado curado em autoclave. A peça RTM irá curar aos mesmos 180 ° C que as peças da autoclave. Para garantir a estabilidade térmica, a ferramenta será impressa com PAEK reforçado com fibra de carbono curta, que tem uma temperatura de fusão de 305 ° C.
Para encurtar o ciclo de cura, o molde impresso em 3D irá integrar o controle de temperatura ativo. “Devemos ser capazes de aquecer e resfriar o molde mais rapidamente em comparação com a autoclave”, observa Consul. “Usaremos uma malha de elementos de aquecimento elétrico 3 milímetros abaixo da superfície do molde e também integraremos canais impressos para óleo aquecido ou ar a 6 milímetros abaixo da superfície do molde. Desta forma, podemos aquecer a superfície do molde muito rapidamente, mas também usar os canais para aquecer em todo o volume da ferramenta. Nosso objetivo é uma taxa de aquecimento e resfriamento 50% mais rápida do que a autoclave e estamos confiantes de que podemos atingir uma taxa pelo menos 30% mais rápida ”.
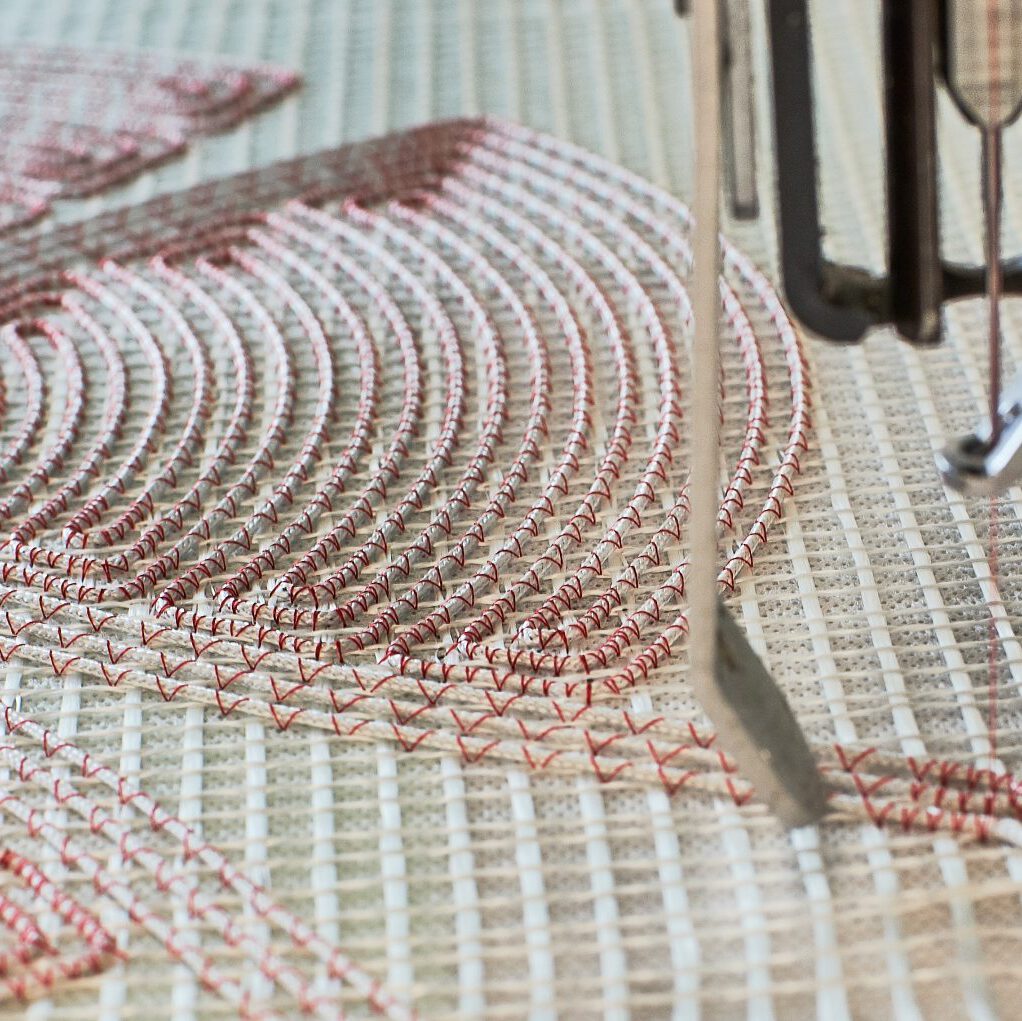
Quais são os elementos de aquecimento a serem integrados na impressão 3D? “Usamos a colocação de fibra adaptada (TFP) de mechas de carbono em um tecido de fibra de vidro como elementos de aquecimento para realizar diferentes zonas de aquecimento em um molde de CFRP para uma pá de rotor de helicóptero”, explica Consul. “Isso foi para um projeto Clean Sky 1 que concluímos trabalhando com QPoint Composite (Dresden, Alemanha). Vamos trabalhar com um conceito semelhante no molde COMBO3D. ”
Todo o desenvolvimento da ferramenta impressa é suportado por simulação. O projeto da ferramenta será otimizado pela implementação do sistema de aquecimento e resfriamento em uma simulação térmica. O processo de manufatura também será simulado, apoiando o processo de impressão, gerando conhecimento sobre a distribuição de temperatura durante a impressão e correlacionando-o com o planejamento do caminho.
Instalação da máquina CEAD e progresso do projeto
“O sistema CEAD foi entregue muito rapidamente - do pedido à instalação durou apenas 6 meses”, diz Consul. “Nessa época, tínhamos concluído os testes de materiais, projetado o ferramental de chapa e começado a imprimir pequenas peças. Estávamos preocupados que demoraria muito para que o processo funcionasse bem com o CEAD AM Flexbot, mas funcionou bem com os primeiros testes. ”
Ferramentas de chapa? “É um molde pequeno, já integrando canais de resfriamento e elementos de aquecimento para produzir placas de CFRP para teste de cupom”, explica ele. “Este teste foi para garantir que a qualidade do nosso molde CFRP RTM impresso em 3D será comparável ao CFRP atual que a Saab produz com seu processo de autoclave.”
Infelizmente, o projeto foi interrompido pelo COVID-19, “mas agora tudo está indo bem e estamos recuperando o atraso”, diz Consul. E que tal usar o PAEK para o molde impresso em 3D? “O único problema atualmente é que a Tg [temperatura de transição vítrea] para PAEK é 130-140 ° C, que é inferior à cura de 180 ° C para a parte de demonstração”, observa Consul. “Portanto, ainda temos que ver quantos ciclos podemos completar na temperatura de cura antes que a fluência aconteça ou a superfície seja danificada.”
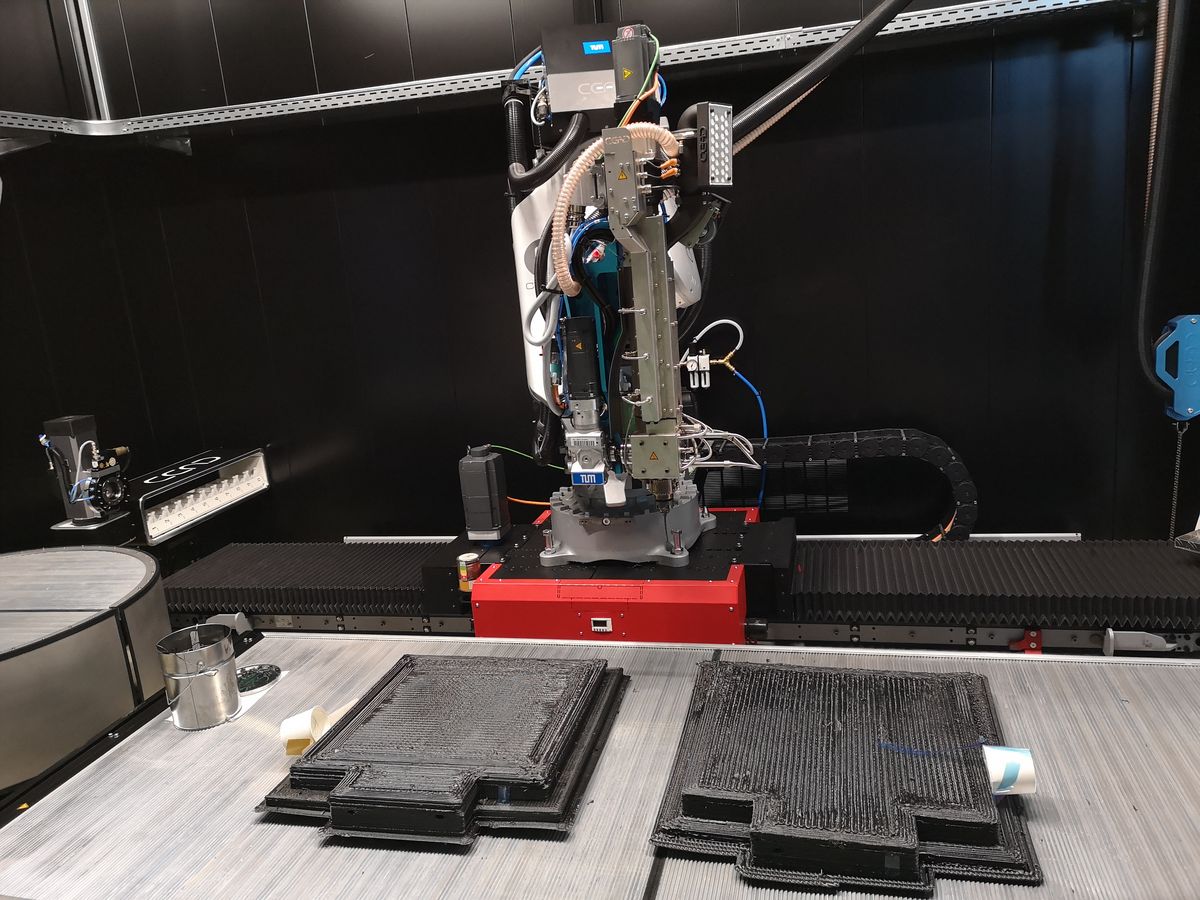
Máquina CEAD em outros projetos?
“Estamos nos inscrevendo para um projeto de ferramental aeroespacial que começa no próximo ano com a GKN Aerospace Deutschland (Munique) usando a máquina CEAD e polietersulfona (PESU)”, diz Consul. [Nota:GKN na Alemanha fabrica flaps de asa compostos para A330 e A350, bem como ailerons para a família de jatos executivos Bombardier Global.] “O CEAD fará parte deste responsável pelo desenvolvimento de máquinas para fibras de carbono contínuas. Também estamos planejando usar a máquina CEAD internamente para fazer moldes de protótipo para RTM que, de outra forma, teriam sido terceirizados. Isso nos dá um benefício em acelerar o trabalho. ”
Cônsul observa que PESU tem uma Tg maior que PAEK. “Também é amorfo, não semicristalino, por isso deve ser mais fácil de imprimir, embora a resistência à fluência possa ser um problema. O que estamos tentando fazer é evitar PEI (polieterimida). No passado, examinamos a questão da ligação PEI à resina epóxi. O RTM6 [epóxi para RTM] dissolve o PEI, que proporciona uma boa adesão entre os dois. Isso é exatamente o que você não quer em moldes impressos em 3D que precisam liberar as peças, não grudar nelas. ”
Compósitos impressos em 3D industriais (e voadores) do futuro
Ao discutir alguns dos outros projetos que a LCC está desenvolvendo na manufatura aditiva, pergunto à Consul o que tem retido o CFRP nos exoesqueletos. “Como os exoesqueletos precisam ser adaptados a cada usuário, as peças são especializadas para que o volume não seja grande”, responde. “Nosso projeto visa permitir a produção de componentes de exoesqueleto de membros inferiores específicos do paciente para permitir a produção de um exoesqueleto específico do paciente em menos de 24 horas. Esses exoesqueletos apoiarão a reabilitação de pacientes com AVC com base em seus perfis biofísicos e necessidades únicas de reabilitação médica. ” (Veja o artigo CW, "C-FREX exoesqueleto depende de CFRP ...")
“As pessoas têm o conceito de que a impressão 3D pode imprimir qualquer parte, mas primeiro é necessário ter experiência com impressão 3D e com composições. Por exemplo, muitas vezes existem problemas com adesão camada a camada e anisotropia que devem ser compreendidos. As peças compostas impressas em 3D não terão o mesmo design que as feitas atualmente de plástico e metal. ”
Ele observa que ainda há problemas a serem superados para o uso de compostos impressos em 3D para a produção de peças de aeronaves de alto desempenho, por exemplo:Como você projeta essas peças para manufatura aditiva? Como você identifica as peças onde a manufatura aditiva agrega valor? “As ferramentas aeroespaciais são o principal campo de aplicações que nossa equipe está examinando agora”, afirma Consul. “A impressão 3D do molde se encaixa bem. Esses moldes devem suportar todas as mesmas condições de cura que as peças, mas há menos risco associado aos moldes do que às peças voadoras. Um bom exemplo são reforçadores de nervura para asas, onde há um grande número de peças diferentes, mas não muitos ciclos por peça. Então, essa é uma boa forma de gerar experiência com a tecnologia. É muito cedo para tentar peças estruturais que voem. Faremos isso em longo prazo, mas as ferramentas de impressão nos permitirão tornar o processo de impressão 3D estável o suficiente com propriedades de alto desempenho e também desenvolver a capacidade de prever com precisão essas peças e processos em simulação ”.
Resina
- Por que a impressão 3D e o software são cruciais para a transformação digital
- Soluções de impressão 3D para empresas de petróleo e gás
- DSM e Nedcam desenvolvem novos aplicativos para impressão 3D de tamanho grande
- Masterbatches de cor de acetal para automotivo e mais com base em transportadores de baixa emissão
- Automação para IML e moldes de pilha
- Victrex e parceiro Bond para impressão 3D de peças PAEK
- Dicas para moldes de impressão 3D
- Dicas para usinagem CNC de titânio:aeroespacial e muito mais
- Formlabs para ajudar a tornar a impressão 3D mais acessível para PMEs
- SIGRABOND® Chemical CFRP para componentes e montagens