Revolucionando o paradigma de custo de compósitos, Parte 2:Formação
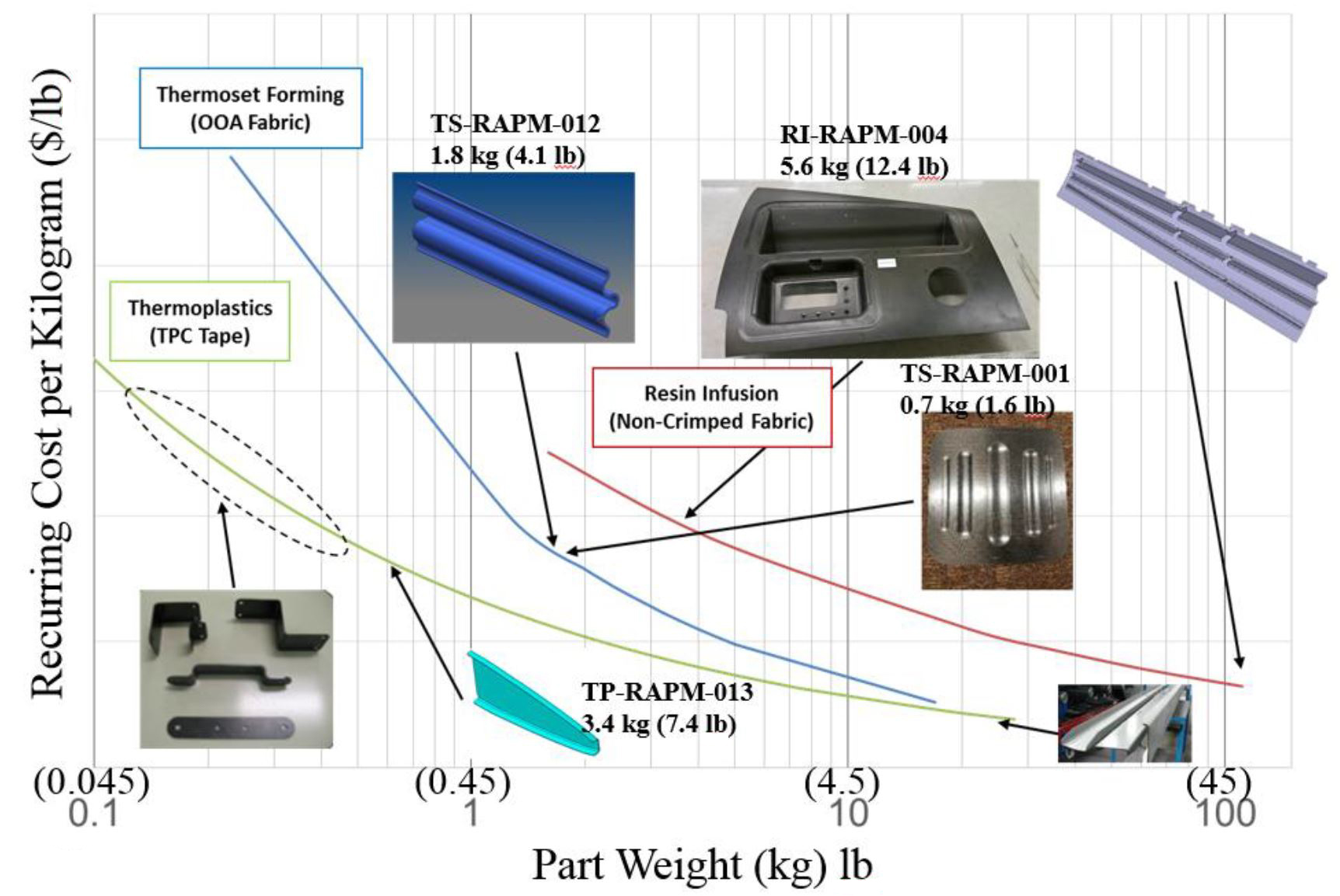
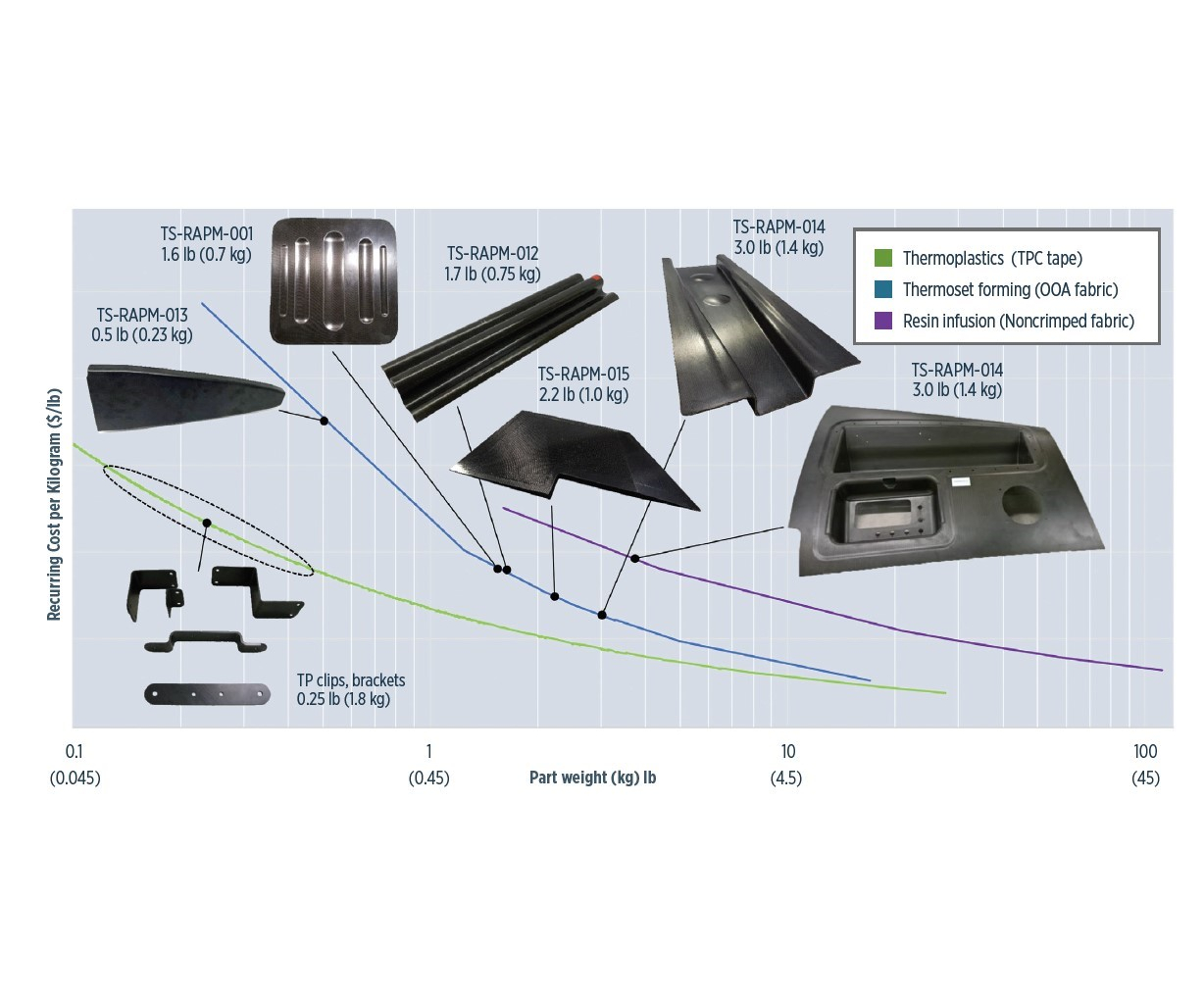
O subprograma RAPM dentro do programa Tailorable Feedstock and Forming (TFF) da DARPA compilou dados analíticos da produção atual / passada, bem como dados empíricos de seus próprios testes de formação para várias peças para gerar essas curvas. O objetivo é compreender melhor o espaço comercial para peças e processos compostos.
Fonte para todas as imagens:The Boeing Co., DARPA
O programa Tailorable Feedstock and Forming (TFF) foi lançado pela Defense Advanced Research Projects Agency (DARPA, Arlington, Va., EUA) em 2015 para permitir a fabricação rápida, de baixo custo e ágil de pequenas peças compostas de formato complexo para defesa aeronaves. Este programa de 48 meses teve como objetivo aumentar a competitividade de custos dos compósitos, a fim de explorar sua economia de peso e resistência à corrosão e rachaduras em relação ao alumínio usinado. Na Parte 1 desta série, CW explorou a visão da TFF e seu subprograma Tailorable Universal Feedstock for Forming (TuFF), que desenvolveu um material de folha de fibra curta com altas propriedades mecânicas e formabilidade semelhante à de metal.
Neste artigo, o foco muda da matéria-prima para a formação com o segundo subprograma da TFF:Fabricação de alto desempenho RApid (RAPM, pronuncia-se "wrap-em") liderado pela The Boeing Co. (Chicago, Illinois, EUA). O programa começou em julho de 2016 e apresentou seus resultados em várias publicações, incluindo 6 artigos e duas apresentações no SAMPE 2019. O objetivo do RAPM, conforme explicado pelos pesquisadores técnicos da Boeing e principais investigadores Gail Hahn e Tom Tsotsis, é "revolucionar o paradigma de custo para pequenas peças compostas, permitindo o uso generalizado em aplicações de defesa. ”
“Começamos com essa visão de alcançar desempenho aeroespacial com eficiência automotiva”, diz Hahn. O programa trabalhou com materiais compostos automotivos e fabricantes de peças, incluindo Solvay Composite Materials (Alpharetta, Ga., EUA) e SGL Composites (Ried e Ort im Innkreis, Áustria), mas alcançar propriedades aeroespaciais nem sempre foi fácil. “Embora os epóxis de baixa temperatura e cura rápida estejam prontamente disponíveis para aplicações automotivas, eles não chegam perto de atender aos requisitos aeroespaciais”, diz Tsotsis. O RAPM usou novos epóxis de duas partes, de cura rápida, voltados para peças de infusão de resina de grau aeroespacial. Porém, inicialmente, o sistema de moldagem da SGL não podia ultrapassar 130 ° C, o que impedia atingir a meta de 30 minutos de tempo na ferramenta.
“Nosso objetivo era atingir o tempo máximo de 30 minutos na ferramenta para permitir o uso de uma célula de trabalho de alta taxa para reduzir os custos de nível de sistema para ser competitivo em termos de custos com o alumínio usinado”, diz Tsotsis. “Na Boeing, decidimos que isso iria satisfazer tudo o que víamos para aplicações de defesa”, acrescenta Hahn. “Por que definir aqui quando podemos obter 2 a 6 minutos com termoplásticos? Porque os termoplásticos exigem processamento em temperaturas ainda mais altas com restrições de ferramentas correspondentes, e nosso objetivo é dar à nossa cadeia de suprimentos muitas opções. ”
À medida que o programa avançava, ele se abria para materiais e fabricantes aeroespaciais e até mesmo sistemas experimentais, como o XEP-2750 da Solvay. “Originalmente, pensamos que seríamos capazes de avaliar totalmente este sistema, como fizemos com o CYCOM 5320-1 em nosso trabalho com o programa DARPA‘ Non-Autoclave Manufacturing Technology ’de 2007 a 2012”, disse Hahn. Embora o mesmo grau de avaliação não fosse possível, o XEP-2750 agora foi comercializado pela Solvay como CYCOM EP-2750 (consulte a barra lateral online “Novo pré-impregnado para moldagem por compressão em RAPM ”) E se beneficiou dos inúmeros testes de peças RAPM e lições aprendidas.
“Tudo que eu quero são alguns processos para pequenas peças compostas que podem vencer o alumínio em um estudo comercial”, disse Jeff Hendrix, consultor da indústria de compostos e do programa da TFF, sobre seus objetivos para o RAPM. Então, o RAPM foi bem-sucedido? CW explora os esforços do programa para fabricar centenas de peças, comparando mais de uma dúzia de configurações de peças aeroespaciais por meio de vários materiais e processos, enquanto busca métodos para reduzir tempo e custo.
Estrutura do programa
Trabalhando com os principais parceiros da indústria, o RAPM testou peças em três linhas principais:
- Infusão de resina com HITCO Carbon Composites (Gardena, Califórnia, EUA) e SGL Composites
- Prepreg termofixo formação com Solvay Composite Materials (Heanor, U.K. e Anaheim, Califórnia, EUA), Fiber Dynamics (Wichita, Kan., EUA) e Reinhold Industries (Santa Fe Springs, Califórnia, EUA)
- Enformação termoplástica com ATC Manufacturing Inc. (Post Falls, Idaho, EUA) e TxV Aero (Bristol, R.I., EUA)
Os testes de formação foram concluídos em duas fases:uma fase inicial de "Desenvolvimento de Fabricação" (Fig. 1) seguida por peças subsequentes de "Desafio e Transição" (C&T) (Fig. 2) para desafio desenvolvimentos iniciais e transição candidatos com potencial para vencer o alumínio usinado.
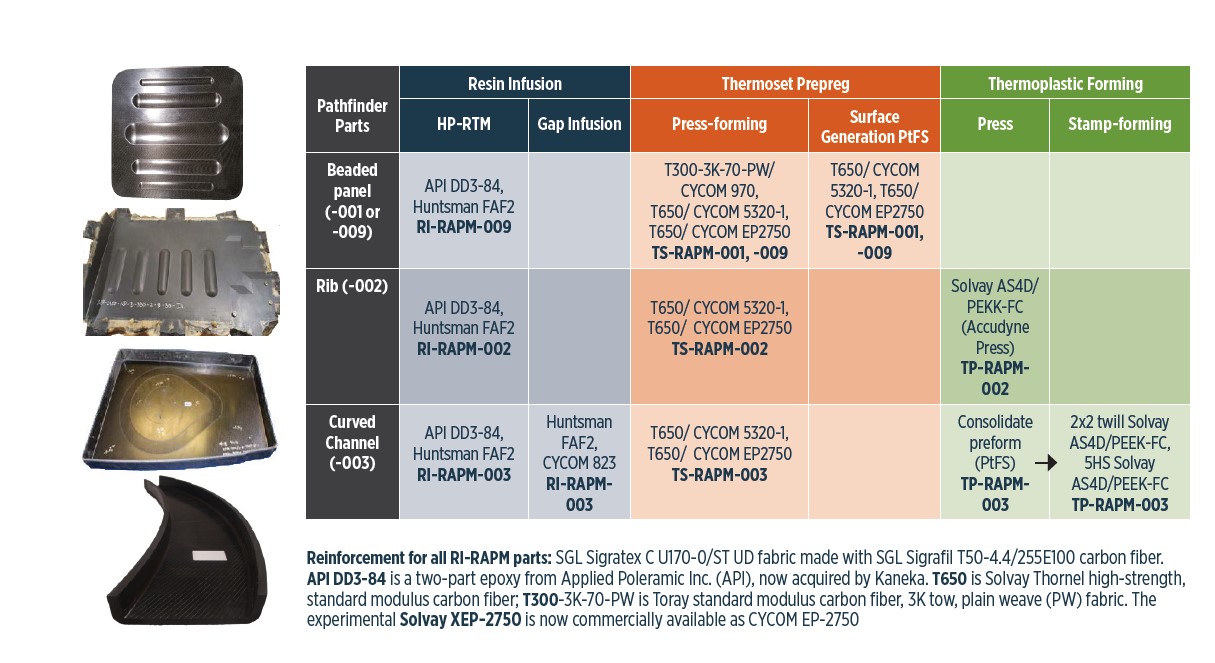
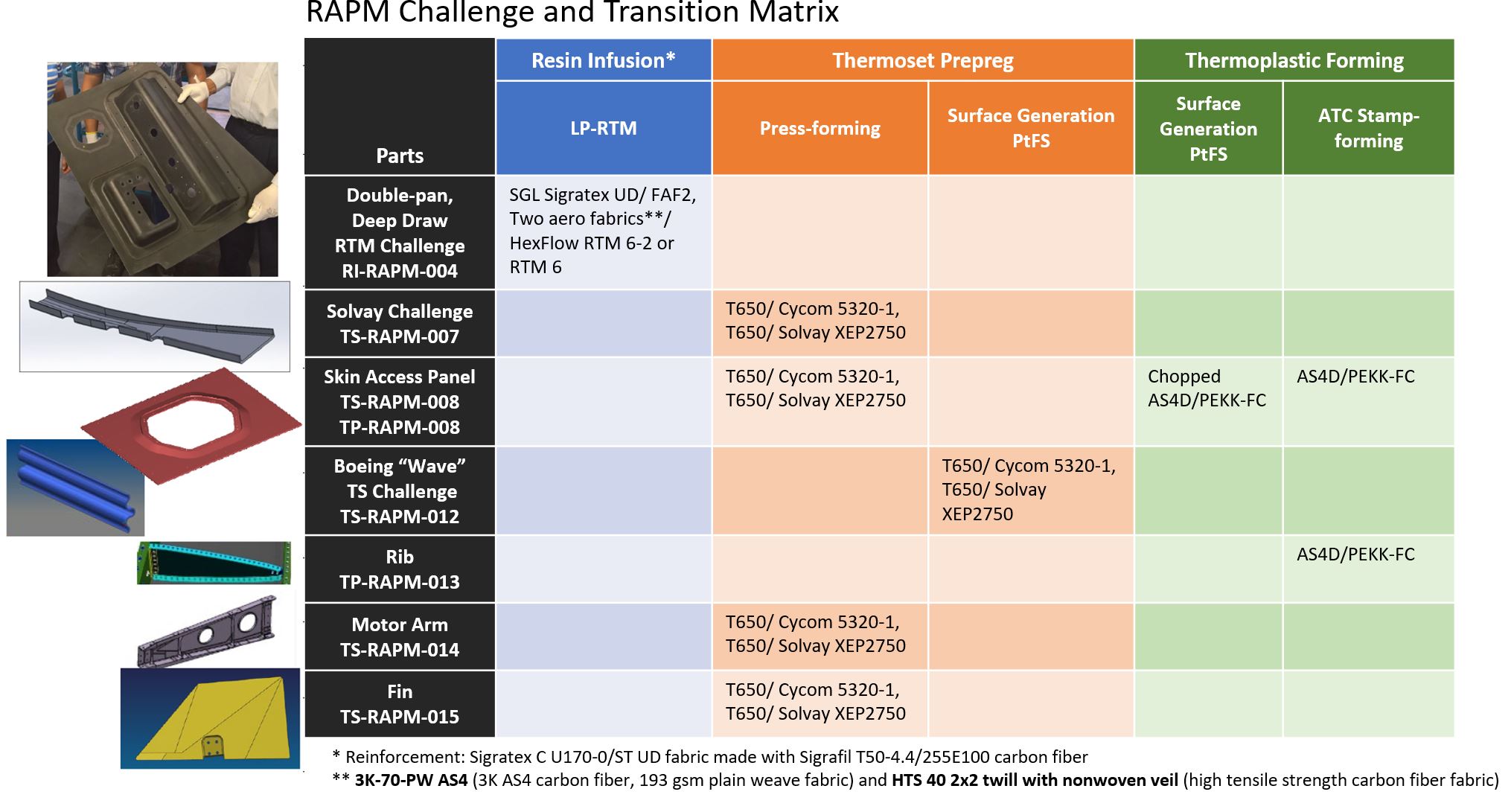
Desenvolvimento de manufatura os testes usaram três configurações de peças principais:painéis com cercadura (havia dois tipos), uma nervura com acolchoamentos (camadas de camadas) e um canal C curvo. Esses recursos incorporados comuns às peças aeroespaciais que podem causar desafios de fabricação:o painel frisado tinha vários recursos fora do plano, além de almofadas, almofadas e uma borda vertical; o painel de nervuras tinha um acolchoamento com várias bordas de 90 graus, bem como uma saliência em uma das bordas; e o canal C tinha um raio interno e externo diferente, curvatura variável nos flanges e quedas significativas de camada na alma.
O objetivo era desenvolver diretrizes de design e fabricação para cada uma das três linhas. “Não parecia sexy fazer essas primeiras experiências”, lembra Hahn. “Mas eles ajudaram a determinar raios aceitáveis e geometrias de peças que produziriam peças sem distorção de fibra indesejada, bem como combinações ideais de parâmetros, como tensão aplicada, temperatura, pressão e tempo na ferramenta.”
Todos os três materiais RAPM e trilhas de processo incluíram testes usando um sistema de ferramentas e controle de aquecimento pixelado de Geração de Superfície (Rutland, Reino Unido) Produção para Especificação Funcional (PtFS) (consulte a barra lateral online “ Desenvolvimento RAPM com PtFS ”), Localizado na Boeing R&T em St. Louis, Missouri, EUA“ Isso aconteceu porque estávamos procurando uma célula de trabalho que pudesse acomodar todos os três tipos de materiais / processos em um ambiente de taxa flexível ”, diz Hahn. “Pudemos explorar diferentes abordagens e custos de controle de temperatura.” A célula Boeing PtFS tem uma temperatura máxima de 440 ° C, uma força de aperto de 150 toneladas e um volume efetivo de 750 por 750 por 100 milímetros.
Embora a visão original fosse usar materiais de folha de fibra curta TuFF, porque eles não estavam disponíveis no início, o RAPM continuou com materiais substitutos. Isso é realmente benéfico para a indústria de compósitos porque os substitutos abrangem materiais que refletem mais o que está sendo usado e desenvolvido fora deste projeto:organofolhas automotivas e pré-impregnados qualificados aeroespacial, epóxis experimentais, termoplásticos semicristalinos e compostos pré-impregnados picados. Assim, os resultados e descobertas referem-se a todos os tipos de fabricantes de compósitos, não apenas aos de defesa.
Faixa 1:Infusão de resina / fabricação RTM
Os testes de desenvolvimento de manufatura nesta trilha começaram com materiais e processos do tipo automotivo. As peças foram feitas pela SGL Composites usando moldagem por transferência de resina de alta pressão (HP-RTM, 300 bar) e módulo padrão C T50, tecidos não crimpados de fibra de carbono 50K (SGL Carbon em Wackersdorf, Alemanha) em configurações de três partes:RI-RAPM-009 , RI-RAPM-002, RI-RAPM-003 (Fig. 1). Eles foram usados para identificar os parâmetros de pré-forma necessários para peças acabadas de alta qualidade. A infusão de lacuna (RTM de compressão ou C-RTM) também foi testada para RI-RAPM-003 pela Boeing St. Louis usando seu sistema PtFS.
A modelagem de fluxo computacional foi usada para entender melhor como infundir essas peças, analisando o comportamento do processo para otimizar materiais e parâmetros de processo e para avaliar cenários de injeção.
As abordagens de ferramentas foram avaliadas para saber como e quando aplicar tensão a diferentes tipos de geometrias de pré-forma para minimizar a distorção da fibra. Essas mudanças de projeto foram validadas para uma geometria modificada do canal C, seguida por análises de tomografia computadorizada (TC). As lições aprendidas foram aplicadas na fase C&T subsequente, passando para RTM de baixa pressão (LP-RTM) para reduzir custos.
Dentro desses testes de peças do Pathfinder, delaminações foram encontradas em vários dos raios de profundidade. Tsotsis acredita que isso foi causado por uma combinação de cura inicial insuficiente da resina na ferramenta - porque o sistema de aquecimento a vapor da SGL restringia as temperaturas na ferramenta a 130 ° C - e tensões térmicas / mecânicas fora do plano durante a remoção da peça. “Como a resistência da resina ainda não havia sido desenvolvida o suficiente, essas anomalias provavelmente poderiam ter sido eliminadas com a cura total na ferramenta, sugere ele. “SGL não conseguiu cumprir o tempo na ferramenta e propriedades aeroespaciais até o aquecimento do óleo (versus apenas vapor) ser adicionado à ferramenta, permitindo a cura acima de 130 ° C ”, observa Hahn. Isso foi adicionado após os testes de desenvolvimento de fabricação.
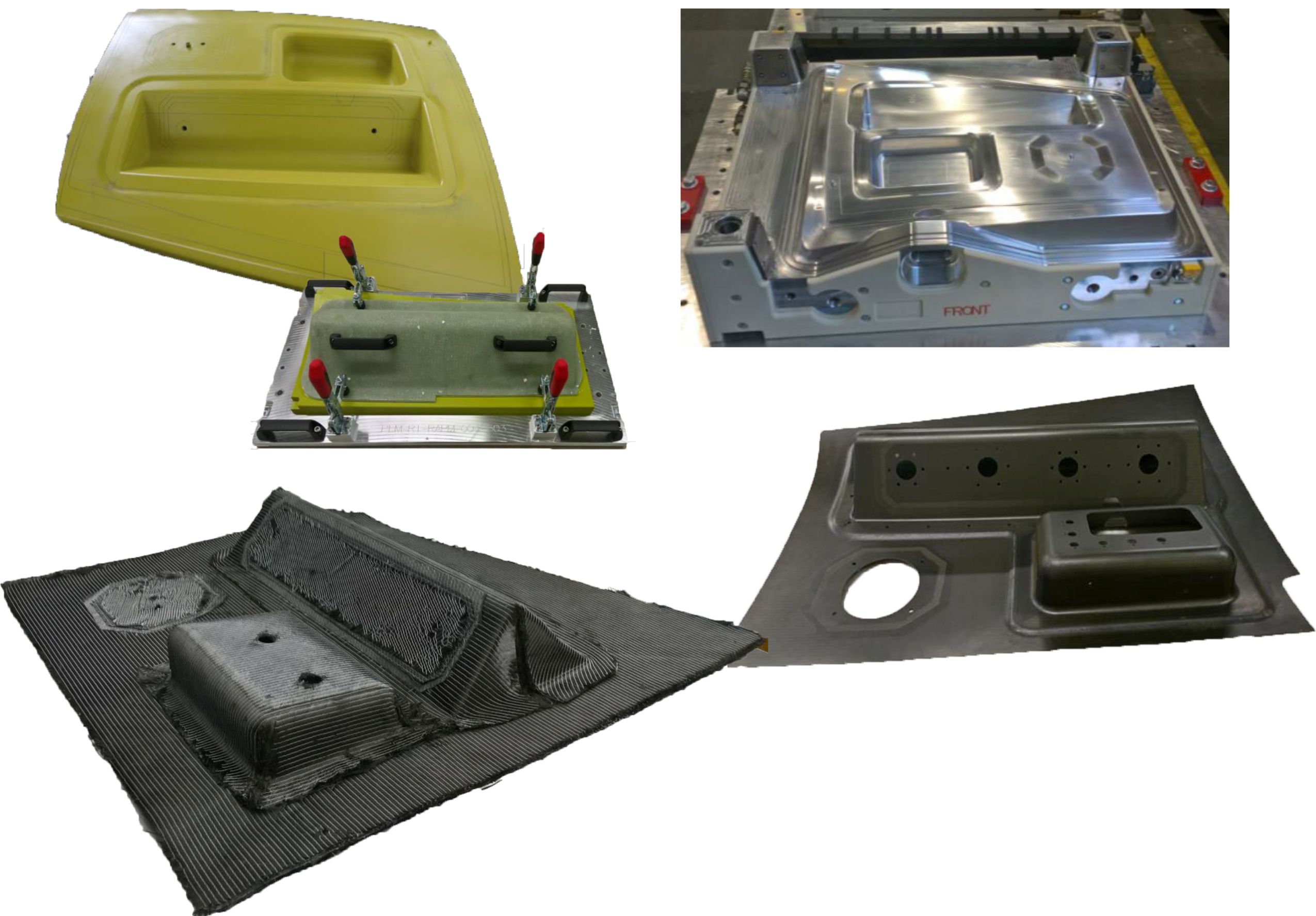
Parte do desafio em profundidade
Os resultados dos testes de desenvolvimento de fabricação foram então usados para desenvolver testes de desafio e transição. A modelagem também foi concluída para a parte do desafio de repuxo profundo RI-RAPM-004 (Fig. 3), que apresenta dois rebatimentos profundos:uma região retangular de 5 centímetros e uma região de 10 centímetros que faz a transição de retangular para uma forma de V. Inspirado por uma montagem de bandeja de produção, sua geometria complexa garantiu um caminho de fluxo de resina não uniforme. Huntsman (Basel, Suíça) realizou a modelagem de fluxo com o software PAM RTM (ESI Group, Paris, França) para um processo LP-RTM usando FAF2 epóxi de duas partes (Huntsman, The Woodlands, Tex., EUA) e SGL Carbon NCF 150 -gramas por metro quadrado biaxial e 190 gramas por metro quadrado de reforços unidirecionais (UD).
RI-RAPM-004 compreende uma pré-forma para a pele, uma para cada uma das seções de repuxo profundo, mais duas áreas de acumulação (Fig. 3). Diferentes layups foram usados para esses elementos de pré-forma para atender às espessuras de painel projetadas (consulte “ Fabricação de peças de geometria complexa de RAPM ”).
"A pré-forma de baixa pressão e LP-RTM permitiram o uso de ferramentas econômicas (em comparação ao aço):a ferramenta de pré-forma, com braçadeiras acionadas manualmente, foi feita com material Raku-Tool à base de poliuretano (RAMPF Tooling Solutions, Grafenberg, Alemanha); a ferramenta de cura foi feita com alumínio 5083.
Os testes iniciais do RI-RAPM-004 mostraram uma anomalia inesperada no fluxo perto da saída que levantou as camadas da superfície, causando distorção da fibra. Reverter a entrada e a saída resolveu o problema. Após a infusão e a cura inicial em uma ferramenta de 130 ° C, as peças foram pós-curadas a 180 ° C por 60 minutos e depois usinadas para obter a forma líquida. Dez peças de alta qualidade foram entregues à Boeing para varreduras C do sistema ultrassônico automatizado (AUSS).
As peças de desafio acabadas mostraram consolidação total, excelente alinhamento de fibra e boa qualidade. As peças exibiram uma temperatura de transição vítrea de 197 ° C e uma fração de volume de fibra (FVF) de 49,5%, típica para o NCF utilizado. A contagem de peças de layup de peças foi reduzida em mais de dois terços em relação ao processo prepreg atual e a mão de obra de toque caiu cerca de 90%. A RAPM também fez a parte do desafio com resinas e tecidos qualificados aeroespaciais - para testar a adaptabilidade das ferramentas e processos que desenvolveu - e peças fabricadas que passaram nos requisitos de produção para testes não destrutivos (NDT).
Faixa 2:formação pré-impregnada TS

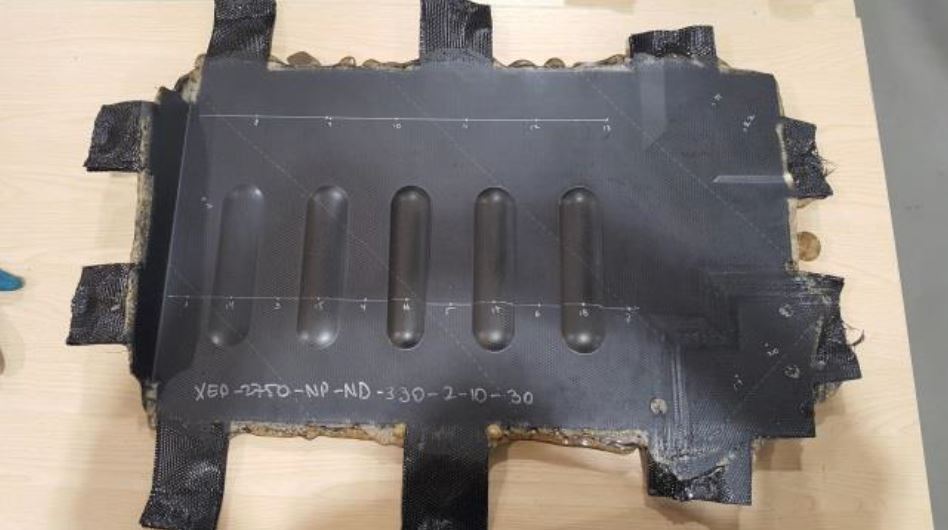
Três peças prepreg termofixo de desenvolvimento de fabricação (TS) foram fabricadas no Centro de Aplicações da Solvay em Heanor, Reino Unido, usando estampagem de estrutura de mola e / ou formação de diafragma duplo (DDF). Todas as três peças foram fabricadas usando pré-impregnados de epóxi com base em resinas Solvay, incluindo CYCOM 5320-1, CYCOM 970 e o sistema aeroespacial CYCOM EP-2750. “CYCOM 5320-1 é a nossa escolha para peças fora da autoclave (OOA), mas também é usado como um sistema qualificado para a autoclave”, diz Hahn. “CYCOM 970 é uma opção de prepreg de solvente versus hot-melt, e [CYCOM] EP-2750 é nosso sistema para conformação por prensagem porque é otimizado para a física e cinética do processo, que mostramos produz as melhores peças.”
A estampagem com mola e DDF são processos de moldagem por compressão isotérmica nos quais os pré-impregnados termofixos são cortados, agrupados e consolidados em uma pré-forma 2D. A pré-forma é então pré-aquecida, transportada em ferramentas de metal combinadas e moldada em uma prensa de cilindro hidráulica convencional. A pré-forma pode ser mantida em tensão por uma estrutura de mola (Fig. 4), que reduz o enrugamento induzido por zonas de compressão do material durante a formação. Como alternativa, o DDF ensanduicha a pré-forma entre dois diafragmas, eliminando a necessidade de limpeza e liberação do molde. A pré-forma é colada a um dos diafragmas, essencialmente mantendo-a sob tensão, embora não tão diretamente ou adaptável como com uma moldura de mola. No RAPM, o tipo de mola, os locais e as tensões foram otimizados para cada peça usando simulação, assim como a estrutura da mola. Por exemplo, o painel frisado TS-RAPM-009 utilizou uma moldura que pode atuar para cima e para baixo para ajustar a formação da carga em paralelo com o fechamento da prensa.
O RAPM minimizou o tempo peça na ferramenta removendo peças dimensionalmente estáveis após uma cura inicial de 15-30 minutos e, em seguida, pós-cura em lote para aumentar a capacidade de taxa. Famílias de peças também foram investigadas usando um único conjunto de ferramentas - por exemplo, um canal C com três ângulos de flange variados ao longo do comprimento de uma asa - para maximizar o uso da célula. Outros objetivos que orientam a abordagem RAPM TS incluem:
- Agrupamento e conformação automatizados para minimizar o trabalho manual
- Desempenho mecânico aeroespacial com cura a 177 ° C
- Ferramentas de aço com capacidade para> 1.000 peças por conjunto de ferramentas.
Desenvolvimento para a parte do desafio da “onda”
As peças de desenvolvimento de fabricação de pré-impregnado termofixo foram formadas, indexando uma variável por vez, até que a qualidade da peça suficiente fosse alcançada. Variáveis como velocidade de fechamento da prensa, posição de fechamento e pressão de fechamento foram avaliadas, com o objetivo de consolidar o material no ponto correto da curva de reologia para criar pressão hidrostática interna, minimizar o sangramento da resina e evitar que a cura avance muito, para evitar rachaduras indução. Depois que os parâmetros de formação foram definidos, três a cinco peças foram feitas para verificar a repetibilidade do processo e, em seguida, testadas quanto à qualidade. Os painéis frisados apresentaram porosidade <0,5% devido às altas pressões de consolidação (20,7 bar). Costelas repetíveis e de alta qualidade também foram produzidas.
As lições aprendidas foram então aplicadas à peça de desafio de "onda" corrugada, TS-RAPM-012, para demonstrar a moldagem por compressão de laminados UD espessos (espessura nominal de 6,3 milímetros) em formas com curvatura de raio estreito (12,7 milímetros). Para atender aos requisitos, a peça usou uma fita UD de fibra de carbono quase isotrópica de módulo intermediário (IM7; Hexcel; Stamford, Conn., EUA). Camadas externas de tecido de fibra de vidro estilo 108 e fibra de carbono de módulo padrão Solvay THORNEL T650 em um tecido de cetim de 8 chicotes protegem as fibras UD e evitam a corrosão galvânica no lado que se encaixa a uma peça de metal. O uso da resina epóxi Solvay CYCOM 5320-1 permitiu ciclos de cura isotérmica de menor duração (≤ 30 minutos) com uma pós-cura autônoma de 2 horas a 177 ° C.
A peça do desafio da onda foi moldada usando a célula de trabalho PtFS da Boeing e faces do molde de aço P20 com vácuo integrado e vedações de resina. A cavidade da ferramenta era mais fina do que a espessura nominal do laminado para compensar a variação no teor de resina do material, mantendo a pressão hidrostática interna para peças de alta qualidade.
Três parâmetros de processo foram testados, incluindo conformação a frio (camadas de pré-conformação sem calor), pré-consolidação de debulk a quente e pré-aquecimento da pré-forma. A conformação a frio foi rejeitada por ser demorada e ineficaz. Para a pré-consolidação, os laminados foram ensacados a vácuo em uma placa com um respirador de fibra de vidro tecido e debulked sob vácuo total em um forno a 116 ° C por 40 minutos. Embora um pré-aquecimento infravermelho automatizado seja padrão para a produção industrial, nesses testes, o pré-aquecimento consistia em colocar a pré-forma no molde quente (179 ° C) e fechar o máximo possível sem tocar por 3 minutos. A peça foi então moldada por compressão.
O ensaio 8 dos nove concluídos (# 0-8) produziu a peça da mais alta qualidade, atribuída principalmente à pré-consolidação. As amostras retiradas dele encontraram espessura (um problema com outras peças) e qualidade do laminado com um volume de fibra de 59-63% e conteúdo de vazios de 0-0,6%.
Faixa 3:costela TP formada pela bexiga e canal C
A RAPM escolheu a costela TP-RAPM-002 dos testes de desenvolvimento de fabricação para demonstrar a moldagem por compressão em uma única etapa da matéria-prima à peça complexa acabada, e o canal curvo TP-RAPM-003 para uma abordagem de duas etapas. A Boeing St. Louis moldou a nervura -002 usando uma prensa Accudyne Systems (Del., EUA) e consolidou os blanks para o canal -003 C usando o equipamento PtFS. Em uma segunda etapa, a ATC Manufacturing estampou os espaços em branco do canal C em partes.
Para a nervura -002, RAPM usou fita UD de 12 polegadas de largura fornecida pela Solvay:fibra de carbono 12K AS4D (Hexcel, Stamford, Conn., EUA) polietercetonecetona reforçada (PEKK). O canal C -003 usou tecido da Cramer Fabrics Inc. (Dover, N.H., U.S.):3K AS4 (Hexcel) fibra de carbono não dimensionada em uma sarja 2x2, revestida em pó com poliéteretercetona (PEEK); o peso da área da fibra é 250 gramas / metro quadrado; o conteúdo de resina é de 42%.
Problemas de formação de termoplásticos (TP)
Os compósitos TP processam a temperaturas mais altas do que os termofixos - por exemplo, 390 ° C para PEEK e 375 ° C para PEKK - o que apresenta uma série de problemas. Os materiais de ferramentas que podem lidar com essas altas temperaturas de processo são limitados. Além disso, o grande delta de temperatura entre o processamento e a remoção da peça torna difícil manter a temperatura uniforme da ferramenta. O remédio é absorver o calor e / ou aumentar e diminuir a velocidade, o que aumenta os tempos de ciclo.
As altas temperaturas também apresentam um desafio ao coeficiente de expansão térmica (CTE). O CTE do material da ferramenta é muitas vezes diferente daquele do laminado de TP, o que pode fazer com que o laminado de TP se retraia da ferramenta, reduzindo a pressão aplicada e evitando a consolidação total. Além disso, o laminado TP CTE é constante ao longo da fibra de carbono, mas uma curva bilineal perpendicular à fibra. Isso resulta em uma contração diferente no plano versus fora do plano, conforme o laminado TP aquece e resfria e também deve ser considerado no projeto da ferramenta.
Os laminados TP também podem encolher com o uso de ferramentas conforme o volume da resina diminui com a mudança de líquido para sólido. É durante essa fase de resfriamento, quando ocorre a cristalização crítica da matriz de resina, que o controle preciso sobre a uniformidade da temperatura e a pressão do laminado é necessário para garantir propriedades de alta qualidade na peça acabada.
Outro problema é que as ferramentas precisam ser totalmente vedadas para conter o líquido TP derretido durante a moldagem. “Vedar uma ferramenta de 375 ° C a 390 ° C é difícil, pois existem muito poucas juntas adaptáveis que podem lidar com esta temperatura e TP formando pressões de 300 a 500 psi ou mais ”, diz Hahn. “Estamos limitados a juntas metálicas ou ferramentas de metal correspondentes para fornecer os recursos de vedação. Ferramentas elastoméricas seriam incrivelmente benéficas, no entanto, todos os elastômeros atuais irão quebrar nas temperaturas de formação TP. ”
A Boeing St. Louis exigiu novas ferramentas para criar pressão horizontal nos elementos verticais da costela durante a consolidação em uma prensa hidráulica que tinha apenas atuação vertical. Sua solução foi uma bexiga de alumínio fina (um sistema semelhante foi usado para formar TP-RAPM-003, Fig. 5). Pressurizada com gás argônio inerte em altas temperaturas, a bexiga se expandiu para aplicar pressão uniforme a todas as superfícies da peça durante a consolidação.
As ferramentas superior e inferior eram feitas de aço inoxidável 410, que combinava com o CTE no plano do laminado de fibra de carbono UD / PEKK. Durante o ciclo de prensa, a ferramenta superior com a bolsa de alumínio desceu e pressionou lentamente o layup na cavidade fêmea da ferramenta inferior. A bexiga foi subdimensionada 30% da espessura da parte final para acomodar a maior parte da pré-forma de fita não consolidada neste processo de uma etapa. Esta ferramenta foi montada em uma prensa convencional com cartuchos de aquecimento elétrico, conectada em 12 zonas controladas de forma independente - mais as seis zonas principais do cilindro da prensa - para controlar a temperatura da superfície da ferramenta nos flanges da nervura e na teia.
Esses testes de conformação produziram peças compostas com resultados NDI aceitáveis. No entanto, o projeto da ferramenta de bolsa requer desenvolvimento adicional para melhorar a formação do layup nos raios internos estreitos da peça e também para manter a espessura uniforme da superfície.
Consolidação de espaços em branco de tecido PEEK
Para o canal C curvo TP-RAPM-003, o tecido de sarja PEEK 2x2 revestido com pó usado tinha um fator de volume relativamente alto. A Boeing St. Louis consolidou primeiro o layup, que caiu de 32 para 24 camadas ao longo do comprimento da peça, em um blank liso com uma seção transversal cônica e, em seguida, enviou os blanks para a ATC Manufacturing, que estampou a parte final com vertical flanges.
As with the rib, Boeing used a forming bladder and steel top and bottom tools. The bladder was changed to AZ31 magnesium, which better resists rupture versus aluminum. The C-channel tool was designed to operate within the Surface Generation PtFS forming cell to enable more rapid heating and cooling versus the conventional press with cartridge heaters used for the rib.
The C-channel tooling approach was developed to increase flexibility for multiple parts. The layup was placed onto the bottom tool, which was heated to the material’s glass transition temperature (Tg ) to maintain pliability without melting. A volume reducing frame that included a pressure-sealing gasket was placed on top of the bottom tool, leaving a cavity slightly larger than the part layup (Fig. 5). Heat and hydraulic pressure were applied from the top tool through the bladder to the layup. Once at forming temperature, argon gas was applied to the bladder, forcing it down into the frame cavity to apply pressure to the tapered blank. The tool temperature was then increased through the melt phase of the material while maintaining bladder pressure, which prevented material from flowing across the lower tool while in melt phase.
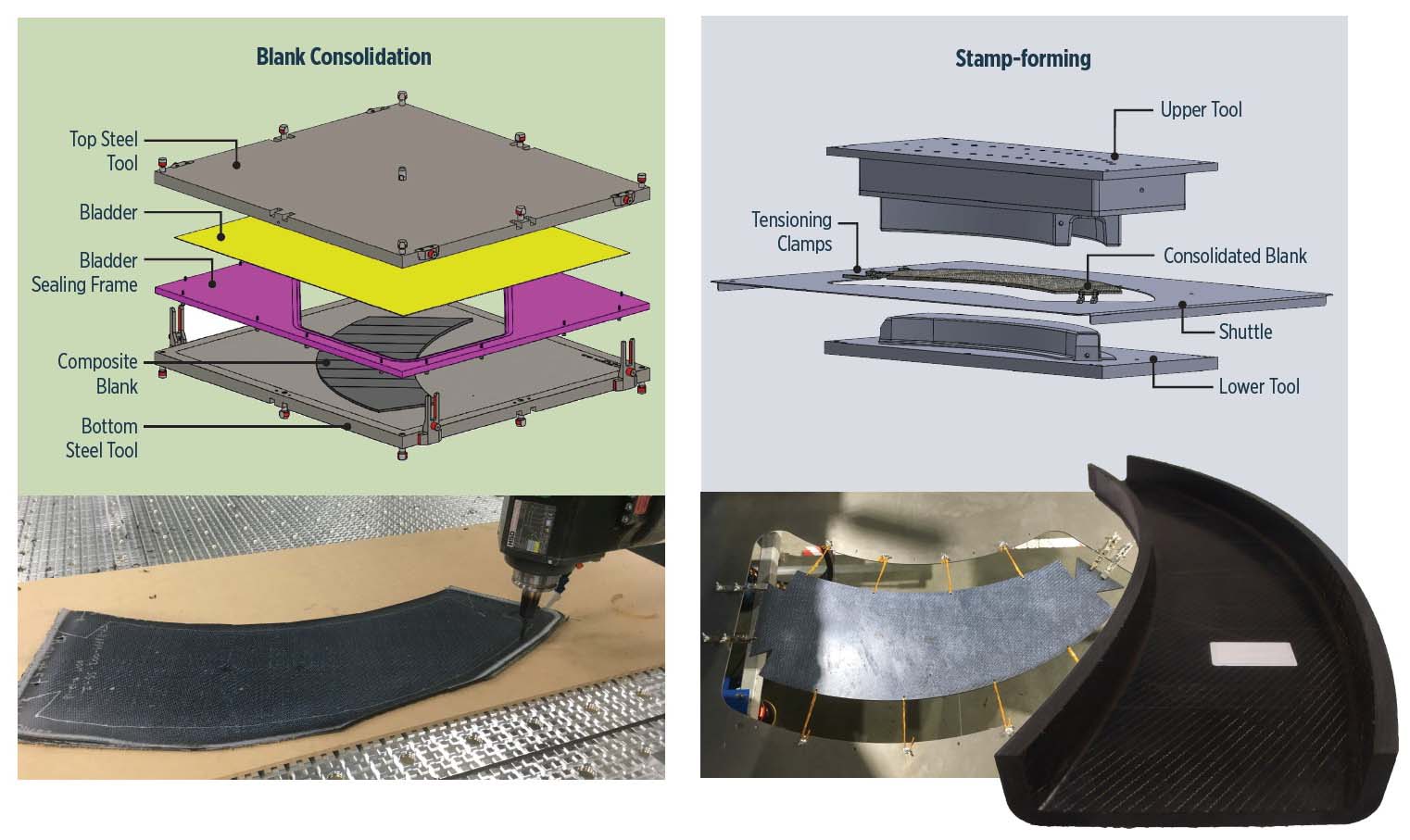
Preforming cycle time comprised 55 minutes for bladder and TP charge to reach process temperature and 30 minutes to cool below the PEEK crystallization temperature. Pressure ranged from 1.4 to 9.7 bar and was maintained manually from a high-pressure tank with a valve. With the recent incorporation of a pressclave system into the PtFS cell, autoclave-like control of vacuum and pressure (±3 psi) in the press mold cavity will be automated in the future.
TP stamp-forming
Consolidated blanks for the -003 C-channel were sent to ATC Manufacturing for stamp-forming, in which the blank is heated sufficiently above melt temperature to ensure polymer flow. It was then transferred to a rapidly closing press to form and cool the part quickly. The forming tool in the press is kept at constant temperature, enabling rapid cycle times by eliminating ramp-up and cool-down. The tool temperature must be between melt temperature and Tg to develop the required level of thermoplastic matrix crystallinity in a short time, yet ensure the part can be removed without deformation. A series of blanks with implanted thermocouples was used to validate the complete thermal cycle for stamp-forming the C-channel.
Forming simulations using Aniform software (Enschede, Netherlands) showed the highly drapable PEEK fabric blank still posed a risk of wrinkling in compression areas, namely the inner (smaller radius) flange. Thus, a tensioning system (Fig. 5) comprising shuttle plate and clips held the blank in tension as the matched metal tools closed to form it. Despite this, the flange face in compression still showed buckling as fiber was pushed inward at the inner radius. “All three RAPM tracks struggled to make this part,” Hahn contends. “Its geometry was extreme, and not so indicative of a real part, but more designed to push what we could achieve in formability.”
The manufacturing development trials led to challenge and transition parts that included multiple versions of the TP-RAPM-008 skin access panel, the TP-RAPM-013 rib with joggles on the flanges and a bladder study using three different geometries of the TP-RAPM-017 panel (Fig. 2). Boeing St. Louis produced all of these except for the TP-RAPM-013 rib, which ATC produced. “Even though this part was made with UD tape, which is typically more challenging to form versus fabric, we were able to form these parts very well,” says Trevor McCrae, R&D director for ATC Manufacturing. Overall, the TP forming trials showed that stamp-forming can produce complex geometries that might not be possible with conventional compression molding.
Learning to cut cost vs. aluminum
RAPM has demonstrated novel forming capability in all three tracks and amassed numerous lessons learned, ranging from how to position pad-ups to prevent slippage during compression molding to guidelines for part geometry to maximize quality and minimize tooling cost. “Understanding the effects of out-of-plane features, radius-to-thickness ratio and distance between geometric details becomes key as you move to small parts,” Hahn observes. “Standardizing features such as radii, curves and flange angles can help mitigate cost drivers, for example, reducing tooling costs, the number of forming trials during development and the need for multiple scans during NDI (nondestructive inspection) by enabling a standard AUSS shoe for a family of parts.”
Another cost driver RAPM highlighted was the time-consuming pre-consolidation step during TS prepreg compression molding. “Low-bulk and higher resin content prepregs widen the process window and increase repeatability for high-quality parts,” Hahn explains. “Solvay has developed a patent-pending ‘transformer film’ which can be applied to lower-impregnation prepregs before compression molding as a method of guaranteeing hydrostatic pressure in the mold cavity during consolidation.”
Although RAPM won’t officially end until fall 2020, followed by additional published results, findings so far for selected parts, which are based on real defense programs, show that composites can compete with machined aluminum (Fig. 6). Though the selected resin infusion and TP parts reduce recurring costs — e.g., materials, machine time, etc. calculated over total parts per family assuming non-recurring infrastructure is in place — the TS-RAPM-012 wave assembly actually shows a 7% increase vs. machined aluminum. However, it does achieve desired weight savings, and at a premium that is actually within the margin mandated by Hendrix:“No one is going to pay 2X for the weight savings composites offer; they must cost within 10 percent of aluminum.” However, he does concede, “There are still non-recurring time and cost issues to figure out, such as tooling and the development required to successfully form the shape.”
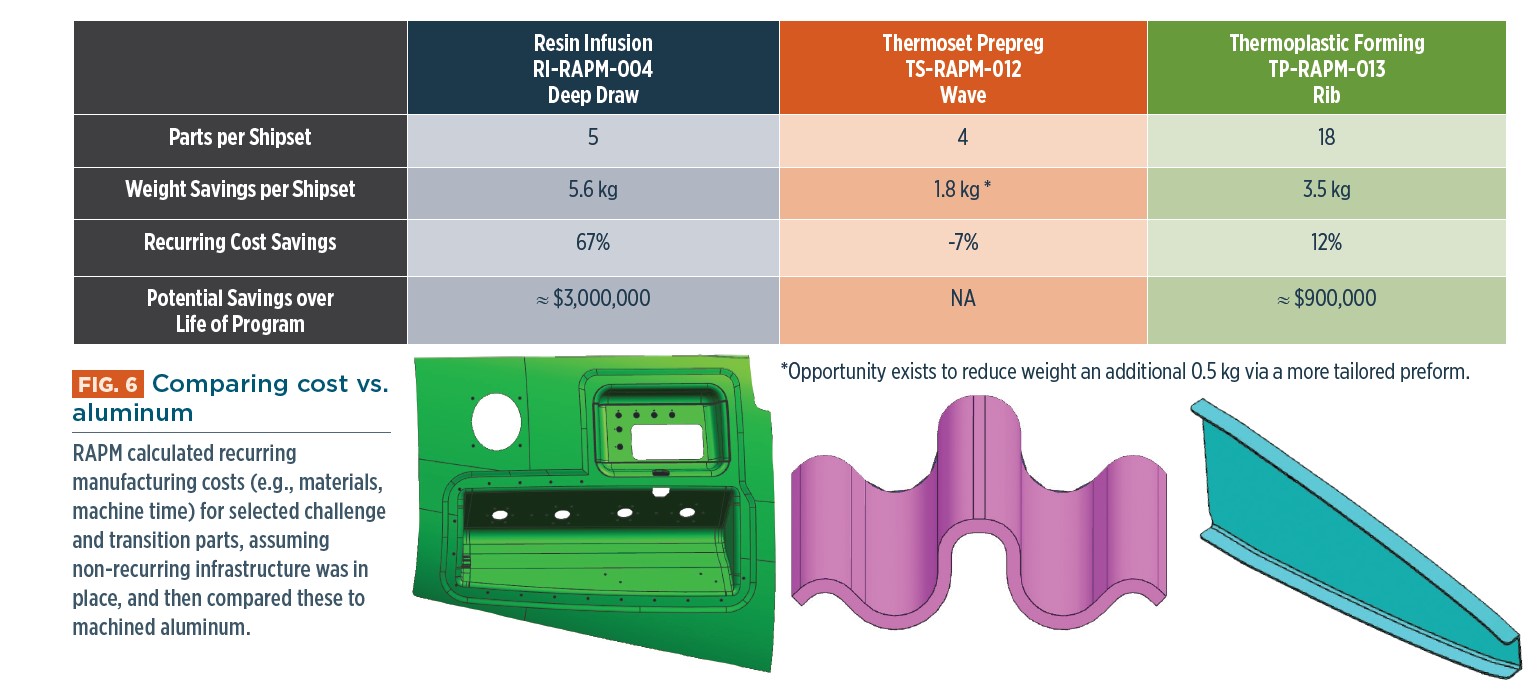
Expanding options
Although resin infusion wins for large parts, says Hahn, TS and TP stamping look pretty good for small parts. “Initial tooling cost for resin infusion is hard to overcome unless the metal parts are very complex, requiring a lot of machining,” she explains.
“Thermoplastics look good for high volume, but a subcontractor for a given program might not be set up to do thermoplastics. However, thermoset stamping might be a very good option, even for low-volume replacement parts. Because defense applications are so wide-ranging, it is important to have more than one material and process in a trade discussion.” Hahn notes that RAPM has opened up new materials and proven aerospace materials can work in automotive-type processes. “We also brought in new manufacturers.”
Hendrix agrees that RAPM’s aerospace and automotive manufacturing exchange was beneficial. Further, he was impressed with Solvay’s and SGL’s ability to form complex shapes without fiber distortion or other defects. “What it takes to make aesthetic auto parts actually has benefits,” he concedes. “You can’t have wrinkles or bad surface finish; they have to be perfect. But it still took multiple trials and significant development for them to form the RAPM parts. I’m not sure defense programs will want to invest in this non-recurring engineering if they’re dealing with small quantities. The economics will be on a case-by-case basis, but tooling and development remain issues we need to address.” Hahn adds, “We are publishing lessons learned, enabling more informed trade studies with expanded options and establishing a reasonably open basis for industry discussion.” CW will continue this discussion with an update once RAPM wraps up later this year.
Resina
- 6 maneiras de reduzir o custo da impressão 3D
- A questão da manutenção do contrato - Parte I
- Fabricação de compostos:A fabricação de materiais compostos
- A Economia da Impressão 3D
- Rastreando a História de Materiais Poliméricos, Parte 13
- As Vantagens de um Programa Corporativo de Paletes
- ACMA lança programa da Conferência de Compostos Termoplásticos em 2020
- A palestra do SAMPE 2018 olha para o futuro dos compostos
- O custo da usinagem CNC
- O valor do investimento (Parte 2)