RTM de compressão para produção de aeroestruturas futuras
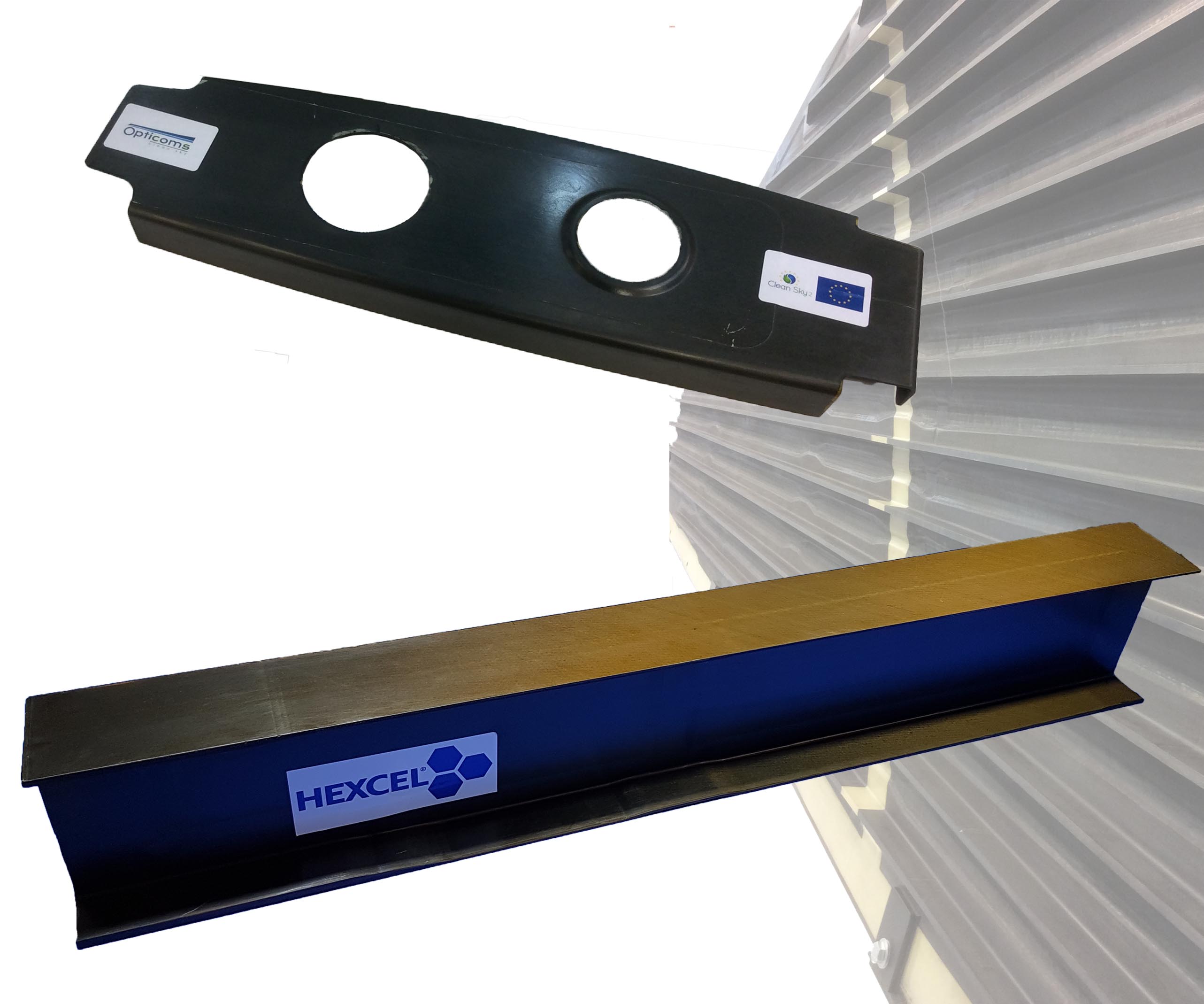
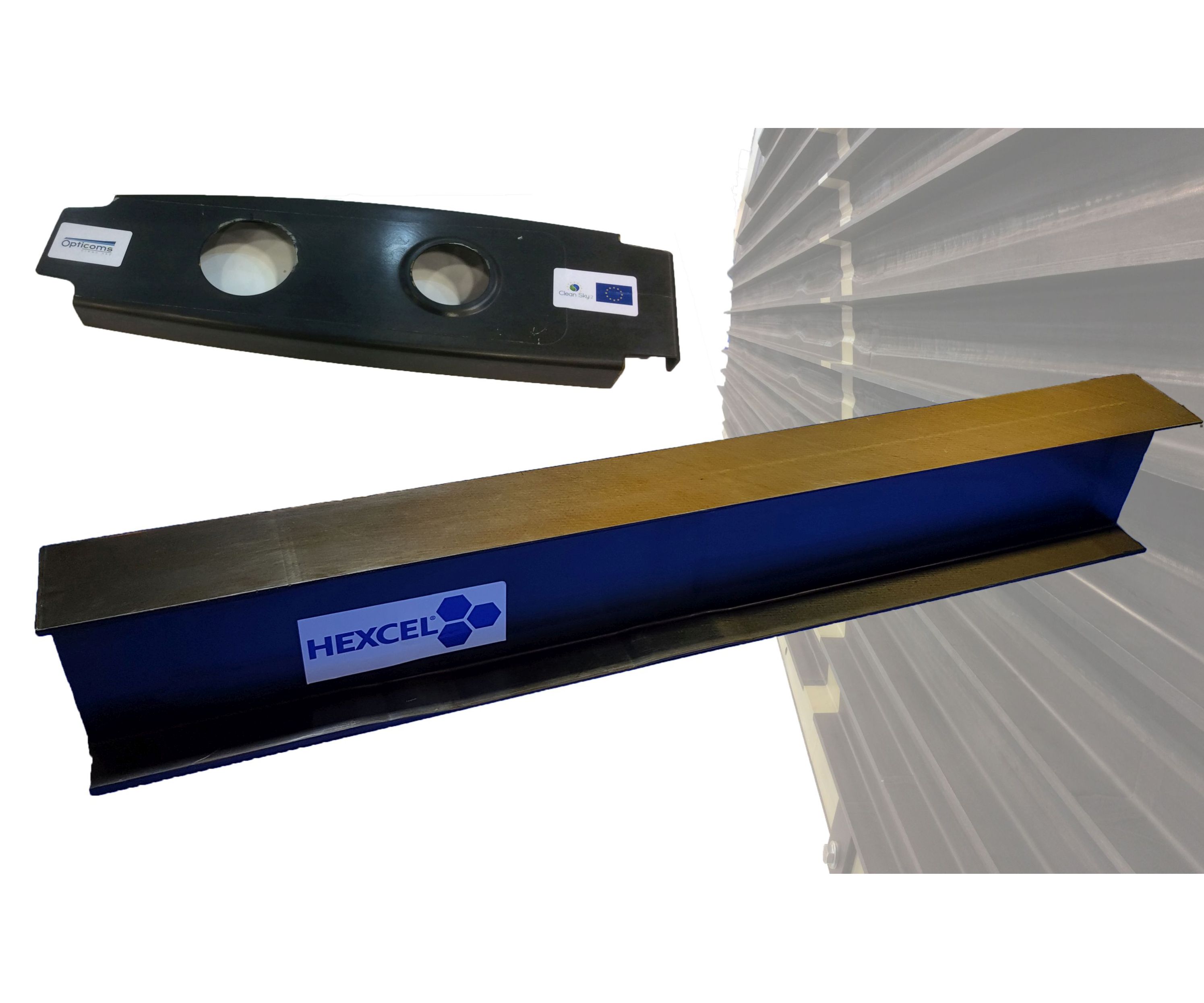
Os compósitos garantiram um lugar permanente nas fuselagens de aviões comerciais porque permitem estruturas leves e de alta resistência que fornecem custos de manutenção mais baixos em comparação com o metal. As projeções atuais para a próxima geração de aeronaves de fuselagem larga e estreita mostram um crescimento contínuo em fuselagens compostas, mas apenas se os materiais e processos puderem atender às metas desafiadoras de baixo custo e altas taxas de produção. Embora o pré-impregnado de epóxi curado por autoclave tenha reinado supremo em fuselagens de polímero reforçado com fibra de carbono (CFRP) até o momento, os desenvolvedores de aeronaves de próxima geração estão buscando agressivamente tecnologias fora de autoclave (OOA) com automação integrada e inspeção em linha como facilitadores principais para futura produção da Indústria 4.0.
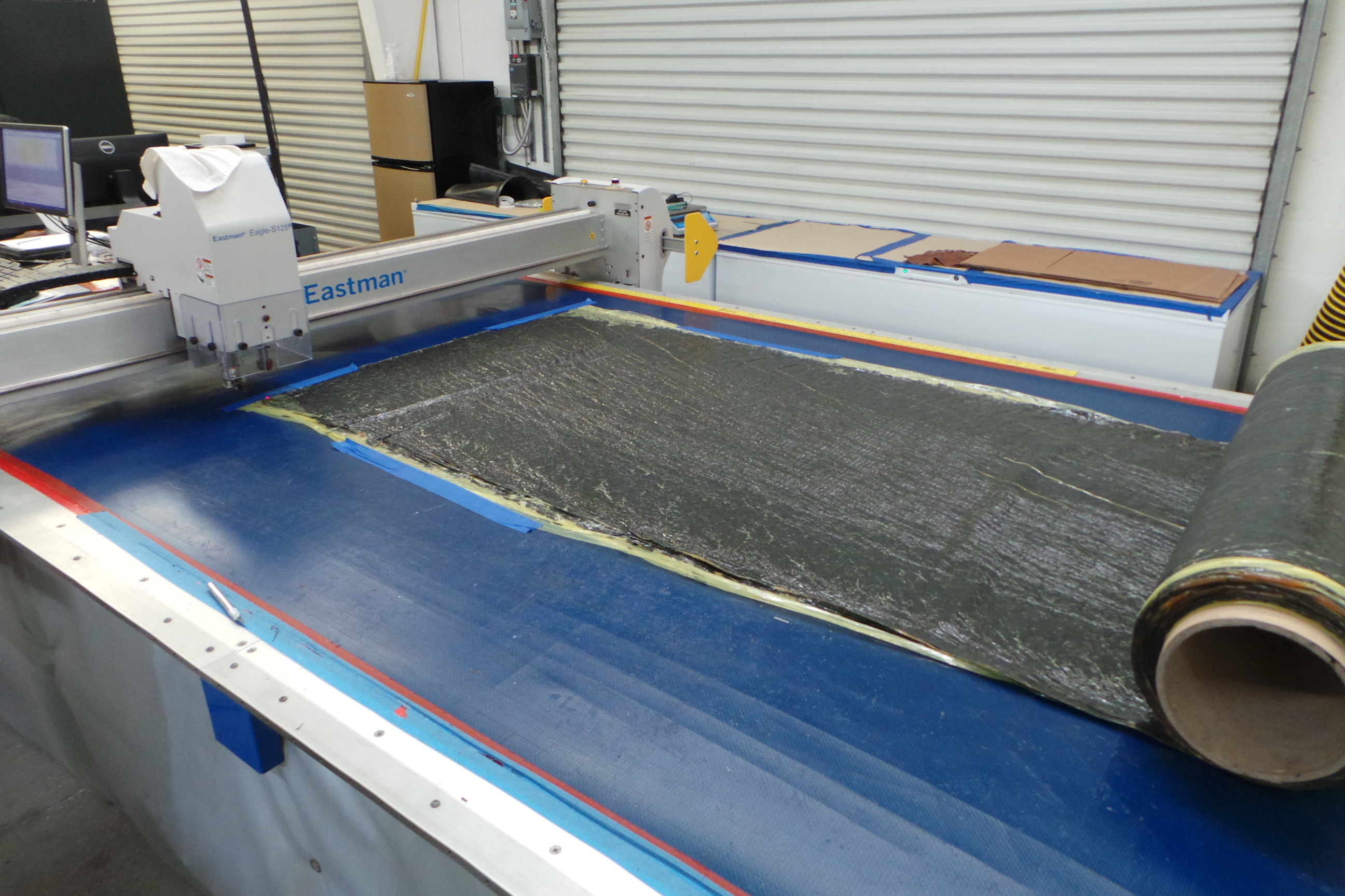
O fornecedor de equipamentos e automação Techni-Modul Engineering (Coudes, França) e sua subsidiária americana Composite Alliance Corp. (Dallas, Texas, EUA) fizeram parceria com as unidades de negócios do Reino Unido e da França do fornecedor de materiais avançados Hexcel (Stamford, Conn., EUA) para demonstrar a produção OOA automatizada de costelas e longarinas de CFRP. As peças são feitas com pré-formação automatizada de reforços de fibra de carbono seca Hexcel e um processo de moldagem por transferência de resina de compressão (C-RTM) que oferece infiltração rápida de resina epóxi líquida Hexcel HexFlow RTM6 para produzir peças com 60% de volume de fibra e menos de 1% de vazios em um ciclo de 2,5 a 3,0 horas que pode ser dimensionado para produzir várias peças para produção de alta taxa.
Desenvolvimento de reforços secos
“Vemos a moldagem de compósito líquido (LCM) como uma resposta ao desafio triplo de reduzir custos, estar pronto para a taxa e fornecer desempenho de estrutura primária”, explica Rémy Pagnac, Engenheiro de suporte técnico da Hexcel para moldagem de compostos líquidos. A Hexcel desenvolveu seu tecido não frisado HiMax (NCF) e materiais de fibra de carbono HiTape unidirecional (UD) para atender às necessidades de desempenho da estrutura primária ao usar processos LCM. HiMax permite que estruturas grandes e planas, como lonas de asas, sejam colocadas rapidamente, enquanto HiTape permite layups personalizados para estruturas grandes e complexas com desperdício mínimo. “Podemos alcançar propriedades iguais aos pré-impregnados UD de última geração”, acrescenta Pagnac.
A Hexcel trabalhou para reduzir o volume e melhorar a elasticidade com HiMax NCF, incluindo um fio de ponto fino de 20 dTex. Os materiais HiMax são feitos nas instalações anteriores da Formax em Leicester, Reino Unido, que a Hexcel adquiriu em 2016. Os multiaxiais leves e estendidos produzidos nesta instalação já tinham uma longa história de fornecimento de soluções para aplicações exigentes, como iates de corrida, supercarros e Fórmula 1 carro de corrida. Agora os materiais NCF foram usados em um projeto de demonstração de asa concluído pela Airbus Defence and Space (Airbus DS, Cadiz, Espanha) e Danobat (Elgoibar, Espanha) usando a tecnologia de Colocação Automatizada de Material Seco (ADMP) - um tipo de colocação automática de fibra (AFP) para NCF (consulte "Provando viabilidade para infusão de tecidos secos para grandes aeroestruturas") - e no projeto ZAero patrocinado pela Airbus para estruturas de CFRP com defeito zero, como lonas endurecidas com longarina (consulte "Fabricação com defeito zero de peças compostas ”).
Com HiMax e HiTape, Hexcel integra camadas de véu de filamento termoplástico fino e de baixo peso que agem como um aglutinante, eliminando a necessidade de aglutinantes de pó historicamente usados em materiais secos para pré-formação e moldagem líquida. Para HiMax, este véu é intercalado entre camadas NCF; para HiTape, o véu é aplicado em ambos os lados da fita unitária de fibra de carbono. “Com isso, você não precisa usar aglutinante em pó para segurar as camadas UD no lugar”, explica Pagnac. “HiTape é calibrado e não é uma fita cortada, então não há fuzz e há menos variação na largura para um processamento AFP aprimorado. O véu termoplástico também adiciona resistência ao laminado final, e demonstramos que podemos atingir altas taxas de deposição de material com a próxima geração de máquinas AFP. ” Em um artigo SAMPE de maio de 2015, Hexcel descreve uma pré-forma de curvatura única fabricada usando HiTape de 0,25 polegada de largura aplicada com uma máquina Coriolis Composites equipada a laser (Quéven, França) AFP a uma velocidade de layup de 1 metro / segundo. Também trabalhou com equipamento AFP Electroimpact (Mukilteo, Wash., U.S.) para demonstrar taxas de deposição de até 150 quilogramas / hora para uma aeroestrutura de longarina de tamanho real.
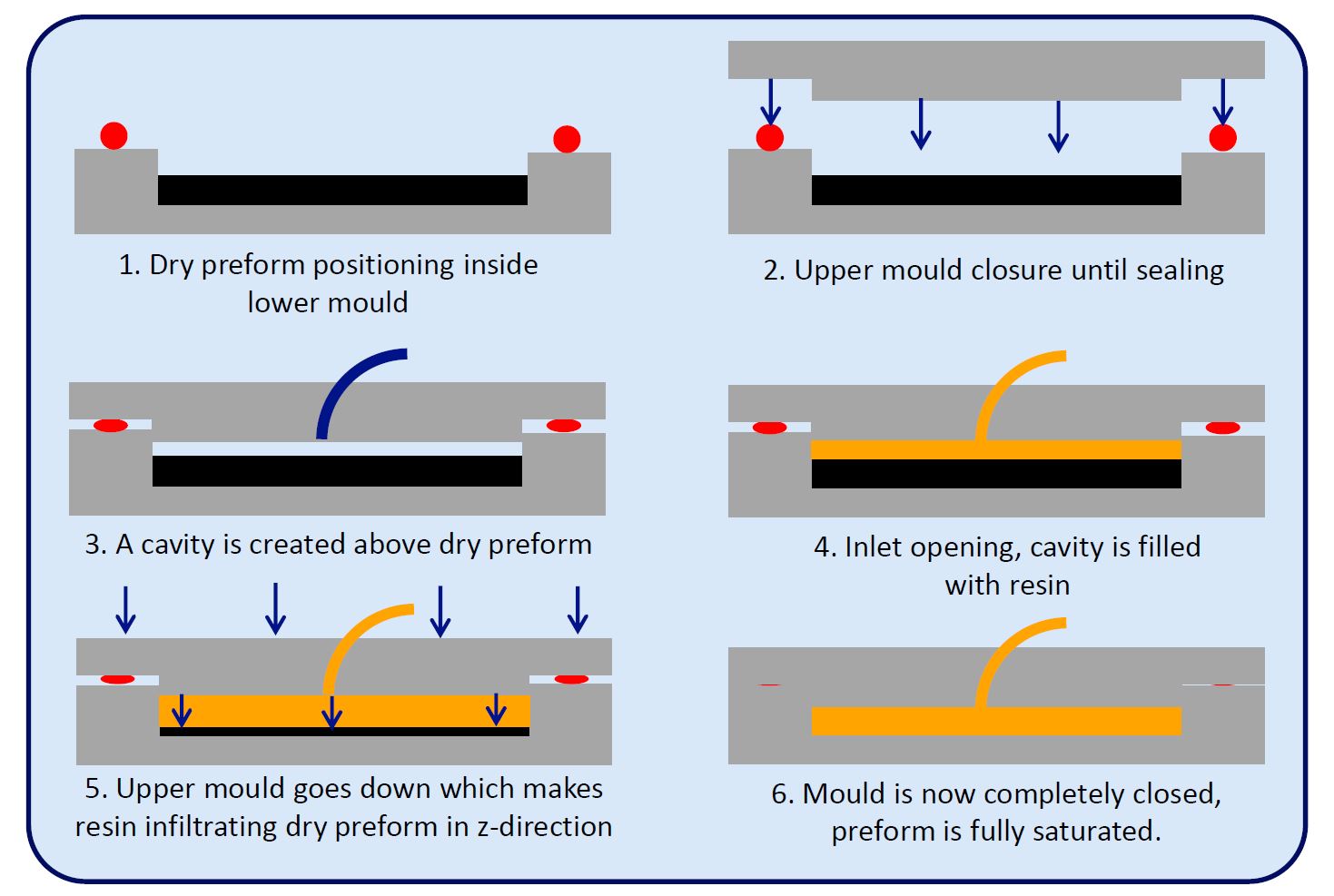
Fig. 1 RTM de compressão
No C-RTM, a pré-forma seca é colocada em um molde RTM, mas o molde é apenas parcialmente fechada, deixando uma lacuna entre a pré-forma seca e a superfície superior do molde. O vácuo é então aplicado, a resina é injetada e a prensa fecha a lacuna no molde, empurrando a resina líquida para dentro da pré-forma na direção z em toda a parte. Fonte | Hexcel

Adaptando C-RTM para aeroespacial
O C-RTM foi introduzido pela primeira vez com o RTM de alta pressão (HP-RTM) para compósitos automotivos. Assim como acontece com o RTM convencional, o C-RTM envolve a colocação de uma pré-forma de fibra seca em um molde de metal combinado, injetando resina líquida na pré-forma e, em seguida, aplicando calor e pressão usando uma prensa atuada. No C-RTM, no entanto, o molde é apenas parcialmente fechada, deixando uma lacuna entre a pré-forma seca e a superfície superior do molde (Fig. 1). O vácuo é então aplicado, uma dose precisa de resina misturada é injetada e a prensa fecha a lacuna no molde, forçando a resina líquida para dentro da pré-forma na direção z em toda a parte. “Isso é muito mais rápido do que injetar a resina no plano através da peça”, explica o engenheiro de processo da Techni-Modul Engineering, Thomas Chevallet.
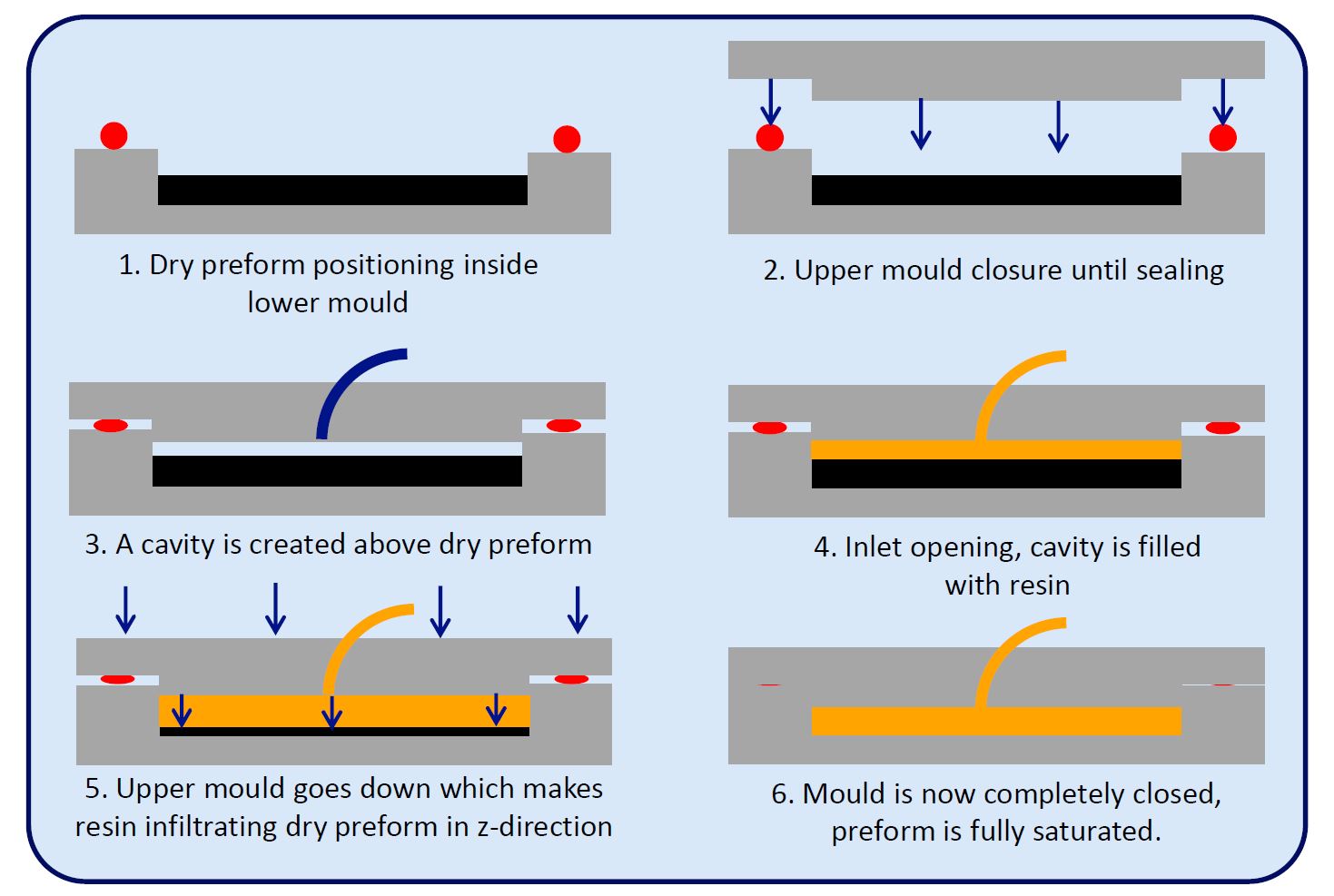
A Techni-Modul Engineering viu uma oportunidade para adaptar o C-RTM para a indústria aeroespacial durante seu papel como um parceiro no projeto Clean Sky 2 “Estruturas compostas otimizadas” (OPTICOMS). Organizado dentro do Pacote de Trabalho B-1.2 ("Estruturas compostas mais acessíveis"), o OPTICOMS visa reduzir os custos de produção de aeronaves pequenas (por exemplo, jato regional) por meio de estruturas integradas e fabricação automatizada, explorando métodos de pré-impregnação e resina líquida. A OPTICOMS projetou um demonstrador de asa composto que compreende uma pele de asa superior com três longarinas, produzida como uma estrutura integrada em um processo único. A asa em escala real (Fig. 2) é parte de um AIRFRAME Innovative Technology Demonstrator (ITD) para avaliar e amadurecer tecnologias em direção ao nível de preparação de tecnologia (TRL) 6 para aeronaves de próxima geração em produção de 2025 em diante. A Israel Aerospace Industries (Lod, Israel) foi selecionada como coordenadora da OPTICOMS em julho de 2016. O consórcio também inclui pequenas aeronaves OEM Piaggio Aerospace (Savona, Itália), Techni-Modul Engineering e fornecedores de equipamentos AFP Coriolis Composites e Danobat.
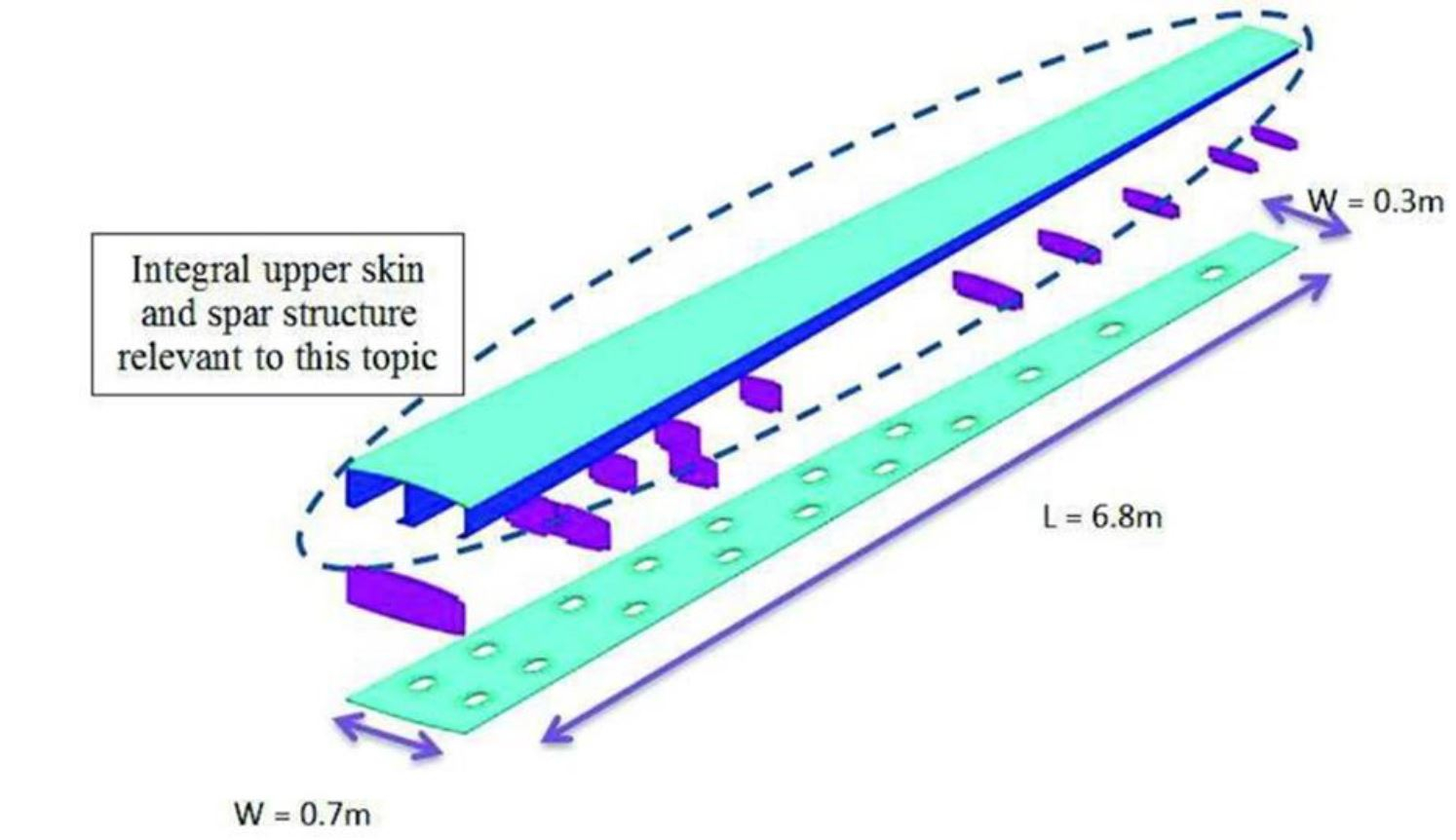
Fig. 2 Clean Sky 2 OPTICOMS rib
A Techni-Modul é parceira do projeto Clean Sky 2 “Optimized Composite Structures” (OPTICOMS), que projetou um demonstrador de asa composta que compreende uma pele de asa inferior, múltiplas costelas e uma pele de asa superior com três longarinas. Este último é produzido como uma estrutura integrada em um processo único. O demonstrador será avaliado para aeronaves de próxima geração em produção de 2025 em diante. Fonte | Clean Sky 2
“O C-RTM era bem conhecido na indústria”, explica Chevallet, “mas com o HP-RTM, uma grande impressora ainda é necessária. Nosso desenvolvimento foi adaptar o C-RTM para injeção rápida usando pressões mais baixas, permitindo a produção menos dispendiosa de peças aeroespaciais com requisitos muito rígidos para alto volume de fibra, alinhamento de fibra e baixos vazios. O tempo de injeção para a costela da asa de 0,7 metros de comprimento por 0,2 metros de largura no projeto OPTICOMS foi reduzido de 40 para cinco minutos. Em um programa de teste separado para uma longarina de viga I medindo 900 milímetros de comprimento e 150 milímetros de altura, o tempo de injeção foi reduzido de uma hora para menos de cinco minutos.

“Essa redução no tempo de injeção oferecida pelo C-RTM seria ainda maior para peças grandes, como asas inteiras ou lâminas de rotor de helicóptero”, acrescenta Chevallet. Ele observa que o C-RTM também permite a injeção de resinas de alta viscosidade, bem como sistemas de injeção de baixa pressão e prensas de baixa tonelagem, o que reduz custos. “A pressão do molde durante o C-RTM é de apenas 6 bar, muito mais baixa do que a usada no HP-RTM”, explica Chevallet. “O processo atinge compósitos com qualidade aeroespacial, mas funciona bem para peças grandes e finas e peças menores de formato complexo.”
Pré-formação automatizada
Embora a injeção de resina mais rápida e de baixo custo e a moldagem OOA sejam partes essenciais dessa abordagem para a produção de aerocompósitos mais acessíveis, a cadeia do processo ainda requer várias etapas para corte e disposição de materiais e pré-formação. “Para nós, OPTICOMS também significa automação”, diz Chevallet. A Techni-Modul Engineering forneceu não apenas um sistema de injeção C-RTM para o projeto OPTICOMS, mas também um robô pick-and-place e uma máquina de moldagem a quente (HDF), todos integrados em uma célula de produção totalmente automatizada.
Pouco depois do início da OPTICOMS em 2016, a subsidiária da Techni-Modul Engineering CAC ganhou o prêmio ACE Equipment and Tooling Innovation na categoria de manufatura por sua célula de pré-formação 3D automatizada no CAMX 2016 (26-29 de setembro, Anaheim, Califórnia, EUA). Capaz de produzir pré-formas 3D a partir de fibra seca ou pré-impregnado, a célula usava garras de sucção a vácuo para coletar, colocar e dobrar as camadas cortadas em um molde de pré-forma aquecido. A Techni-Modul Engineering e a CAC desenvolveram um software para preparar as camadas cortadas de materiais 2D para moldar em superfícies complexas e reveláveis. Esta célula foi posteriormente desenvolvida no OPTICOMS e no projeto de teste de feixe em I.
Etapa 1
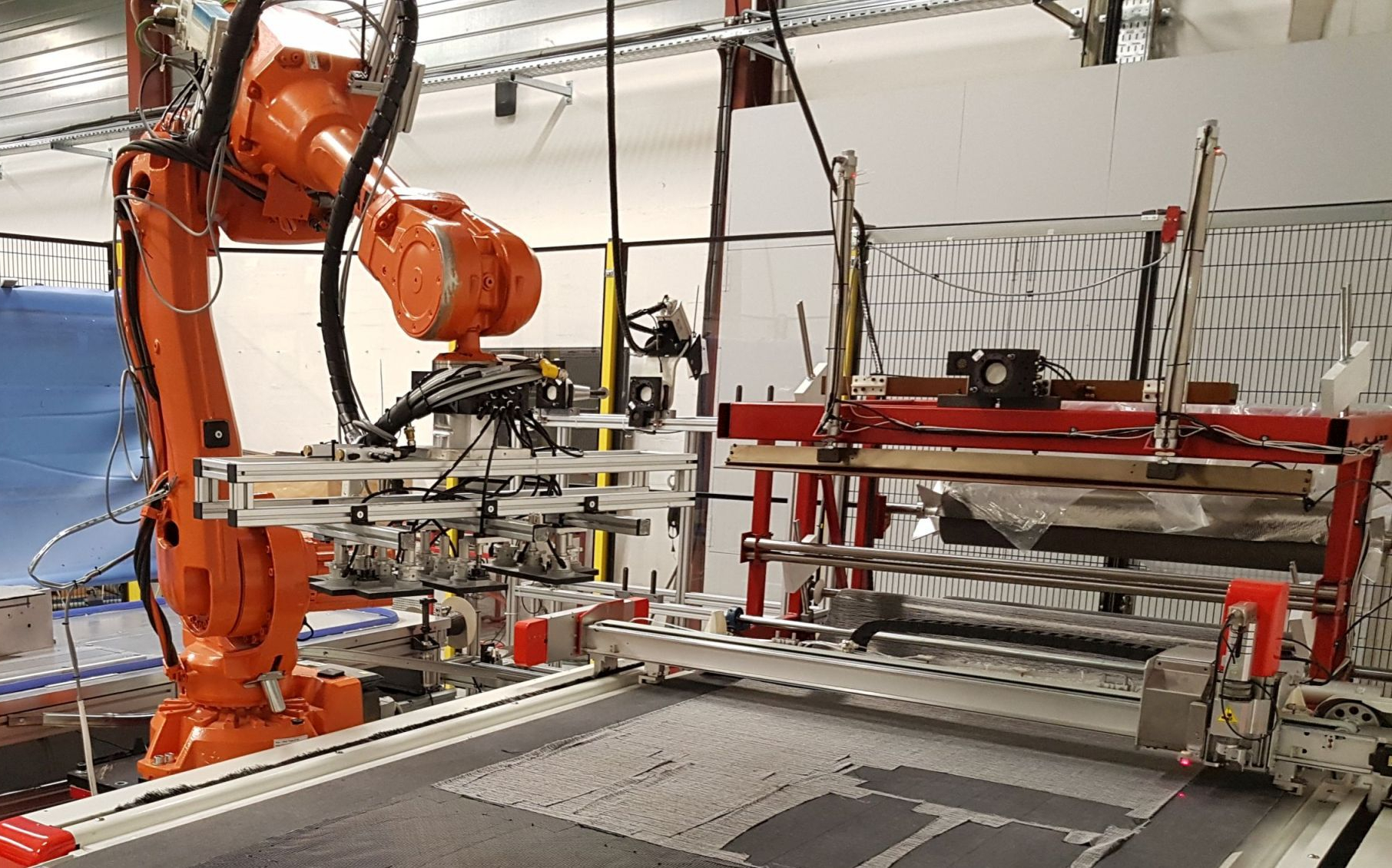
Fonte, todas as imagens da etapa | Engenharia Techni-Modul
Dentro da célula automatizada Techni-Modul Engineering, um robô pick-and-place remove as camadas de um cortador automatizado e as aplica a uma ferramenta de pré-formação aquecida.
Etapa 2

As ferramentas de pré-formação ficam em uma mesa de compactação com uma membrana de vácuo reutilizável articulada (azul, à esquerda) usada para completar uma despressurização aquecida a cada 5-8 camadas durante o layup.
Etapa 3
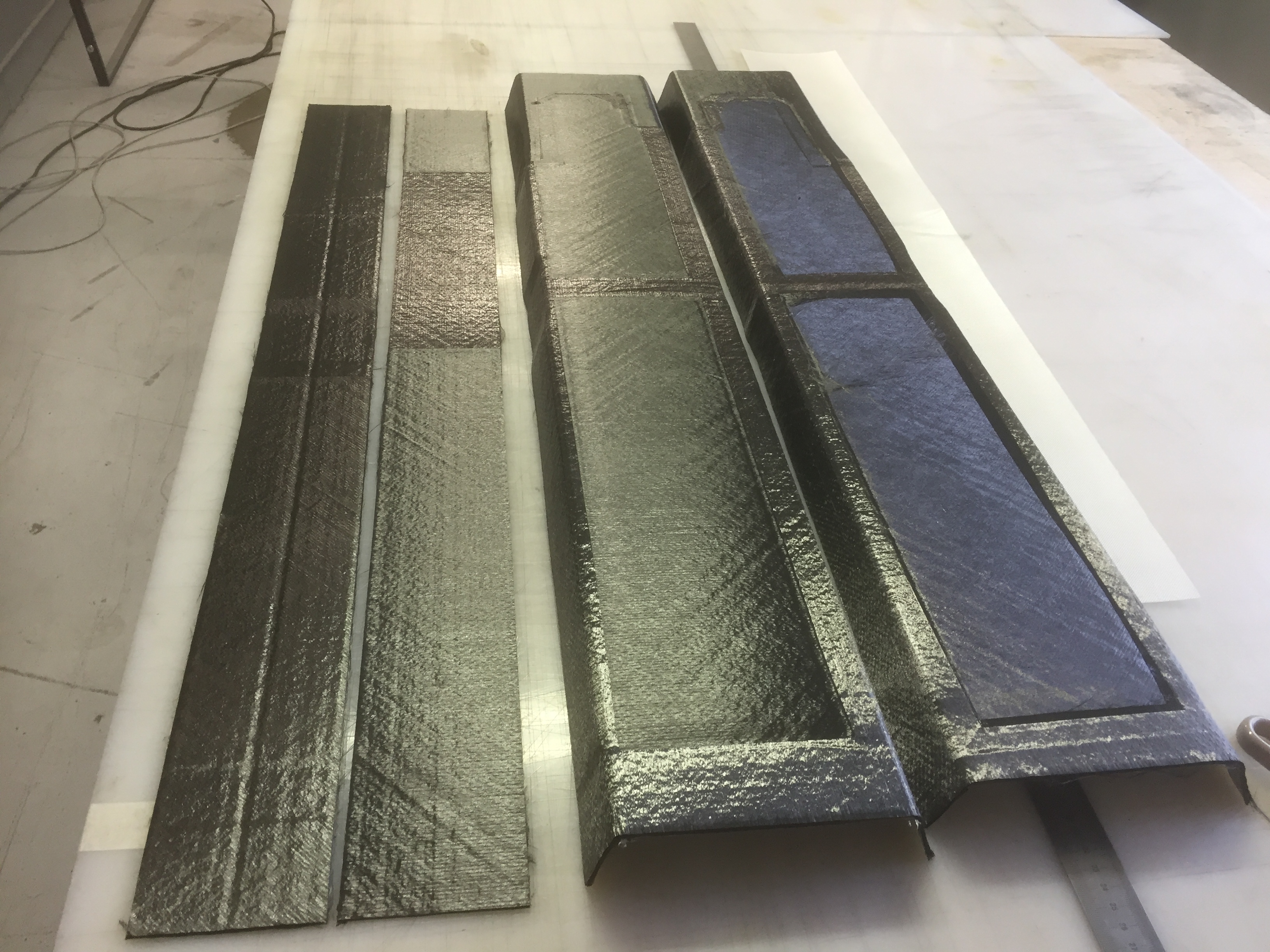
Cada ciclo de pré-formação de longarina produz uma pré-forma de viga C (duas compreendem a teia de viga I) e uma pré-forma de flange plana. Dois conjuntos necessários para cada longarina em I são mostrados aqui.
Etapa 4
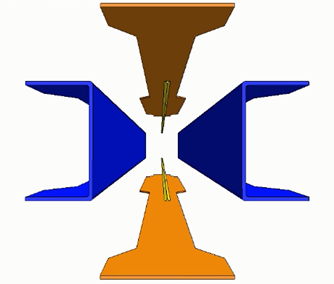
As quatro pré-formas de viga em I são colocadas no molde RTM, o vácuo é aplicado e a injeção de resina é concluída em 5 minutos.
Etapa 5
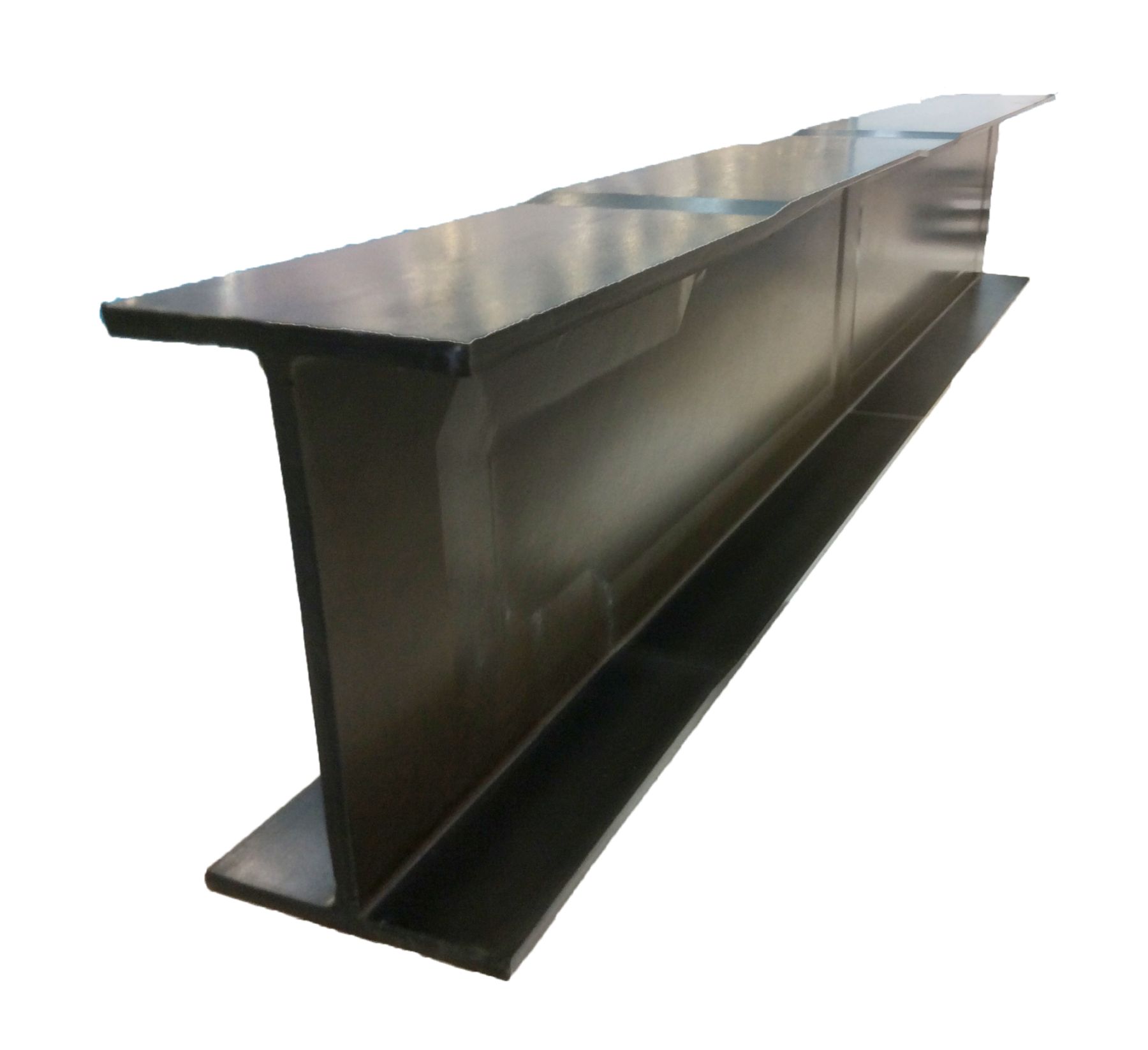
Após uma cura de 90 minutos, a longarina é desmoldada e o flash de resina é aparado para um ciclo parcial completo de 4,5 horas.

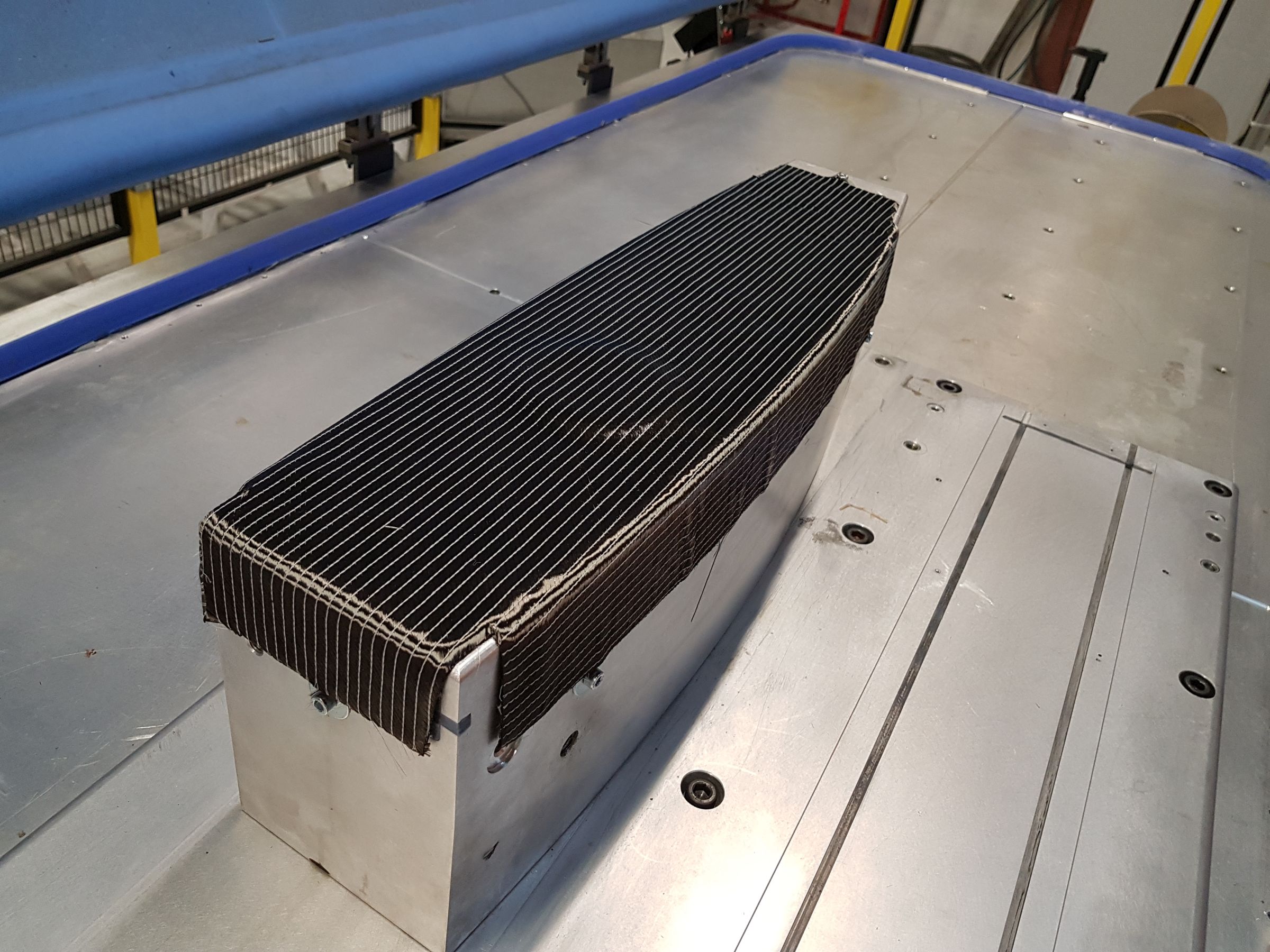
Um robô coloca lonas cortadas na ferramenta de pré-forma aquecida. A cada 5-8 camadas, um desbastador aquecido é concluído para compactar a pré-forma.
Antes da redução de volume, o filme de liberação azul é aplicado.
O respirador é usado para extrair o ar através da pré-forma.
Após o debulk final, a pré-forma é resfriada na ferramenta e os recortes são aparados (abaixo).
“Automatizamos o empilhamento manual clássico de camadas usando a escolha e colocação robótica”, diz Chevallet. “O robô pega camadas de um cortador automatizado e as transfere para a ferramenta de pré-forma aquecida que fica em uma mesa de compactação [Etapas 1 e 6].” Um peel ply (filme azul na Etapa 6), respirador (material branco na Etapa 6) e membrana de vácuo reutilizável articulada (azul claro à esquerda nas Etapas 2 e 6) são aplicados, seguidos de vácuo e calor para moldar e remover o ar do pilha têxtil (formação de cortina a quente, HDF) enquanto derrete os finos véus termoplásticos para criar uma pré-forma compactada.
“Quantas camadas você pode compactar de uma vez depende dos materiais e do formato da peça”, explica Chevallet. “Para peças com baixa curvatura, como uma pele de asa, então você poderia compactar a cada 50 camadas. A nervura OPTICOMS, no entanto, tem ângulos de 90 graus e a longarina de teste em I tem formas em T, portanto, você deve ter cuidado para não formar rugas nas camadas durante a pré-formação. ” Ele acrescenta que essas formas complexas podem exigir compactação a cada 5-8 camadas, mas ainda podem fazer parte de um processo industrializado de alto volume:camadas de pilha, HDF de 2 minutos compactar, reabrir e empilhar novamente, seguido por ciclos de compactação repetidos com um resfriamento final da pré-forma na ferramenta antes da transferência para o molde RTM.
“Nossa célula automatizada pode ser posicionada a uma taxa de 15 segundos por camada”, observa Chevallet. “O layup para a nervura OPTICOMS, com menos de 20 camadas no total, foi concluído em 20 minutos.” O layup para a longarina em I foi mais longo - 45 minutos devido ao seu formato complexo e pilha laminada, incluindo variações de espessura de 1,2 a 6 milímetros. “Isso ainda é muito mais rápido do que os processos manuais e reduz o risco de erro, aumenta a repetibilidade e a qualidade enquanto reduz os custos”, acrescenta.
Etapa 7
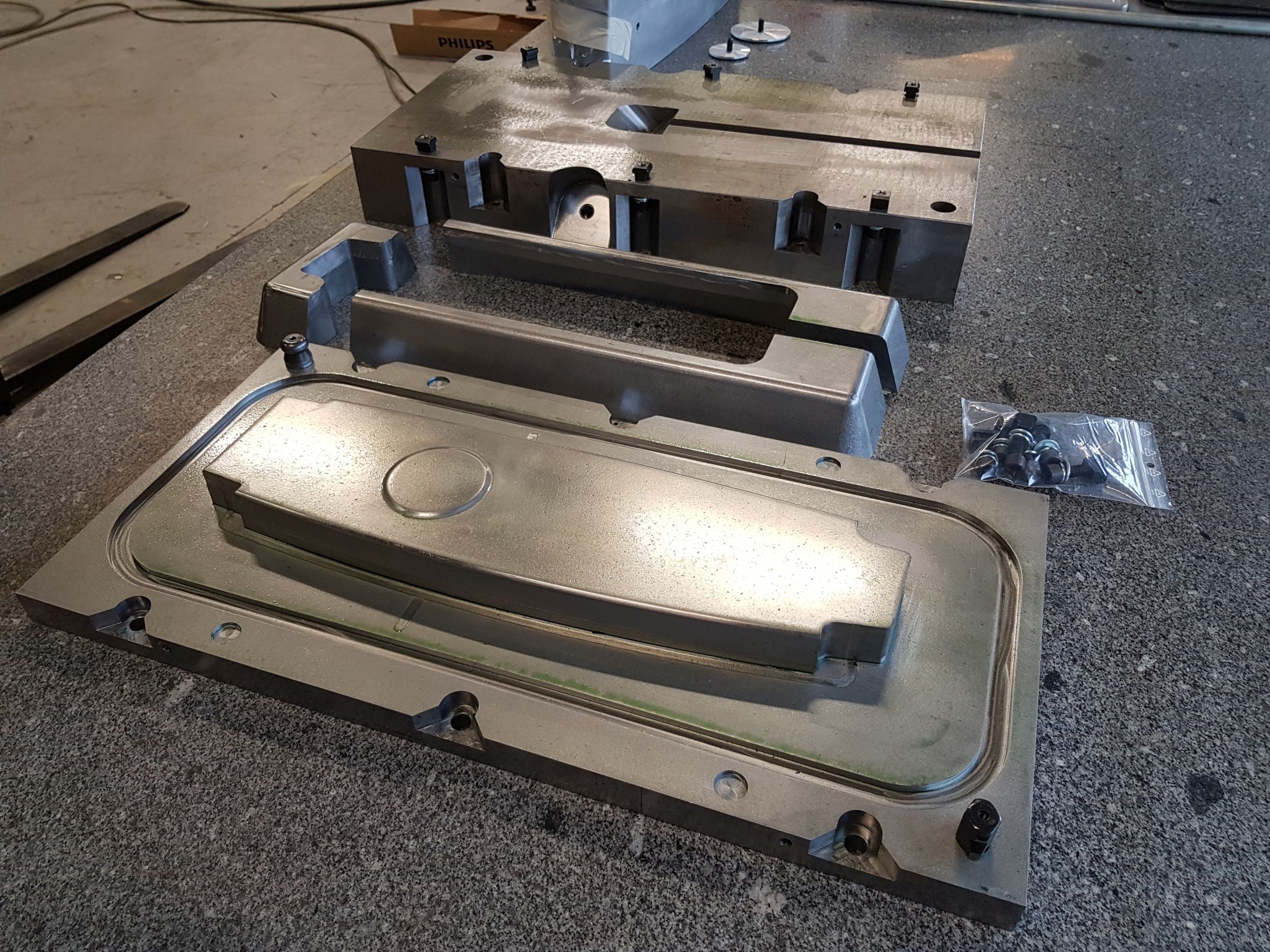
A ferramenta RTM para a nervura OPTICOMS compreende várias partes.
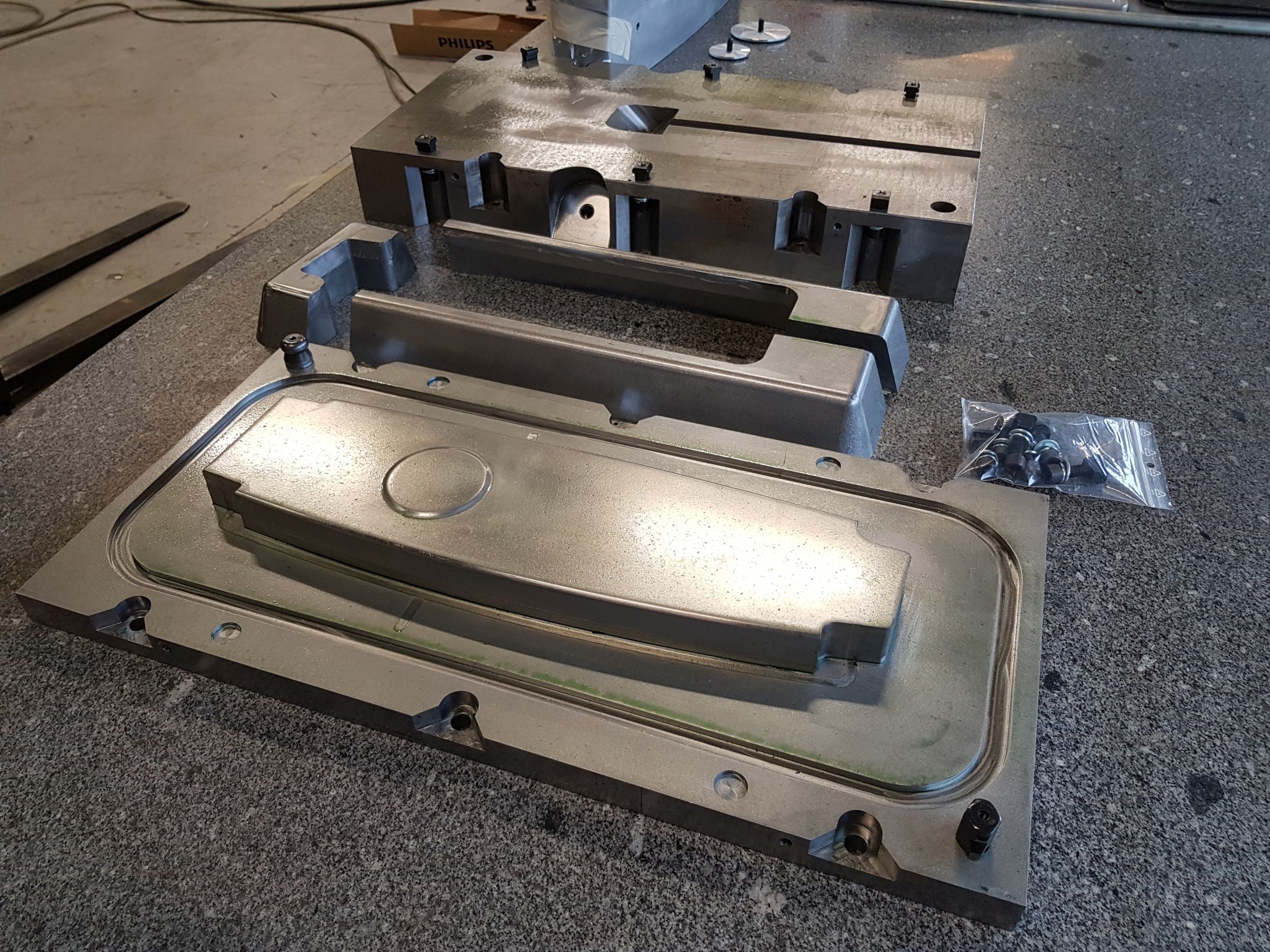
Etapa 8
A pré-forma de nervura é colocada na ferramenta RTM.
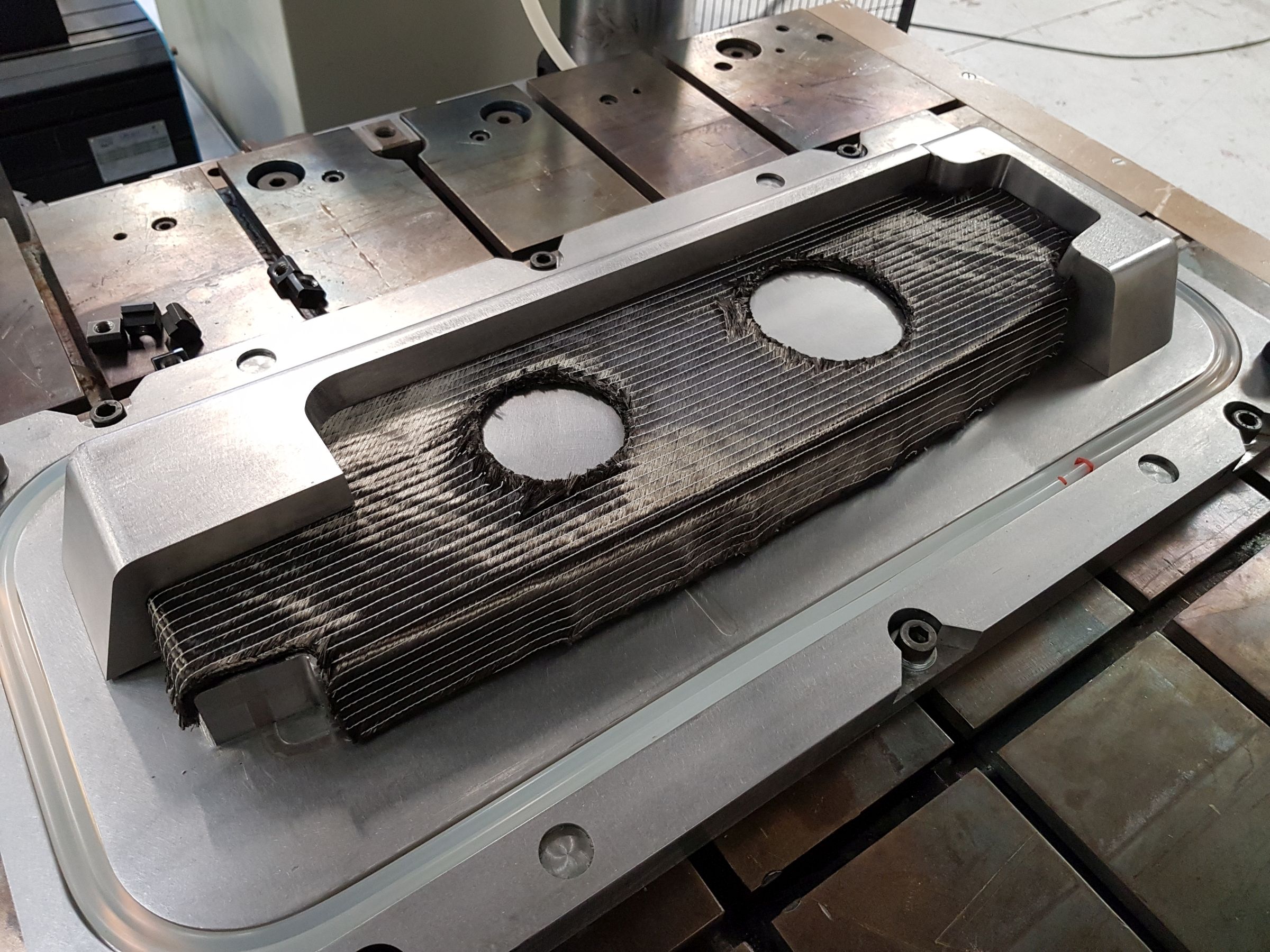
Etapa 9
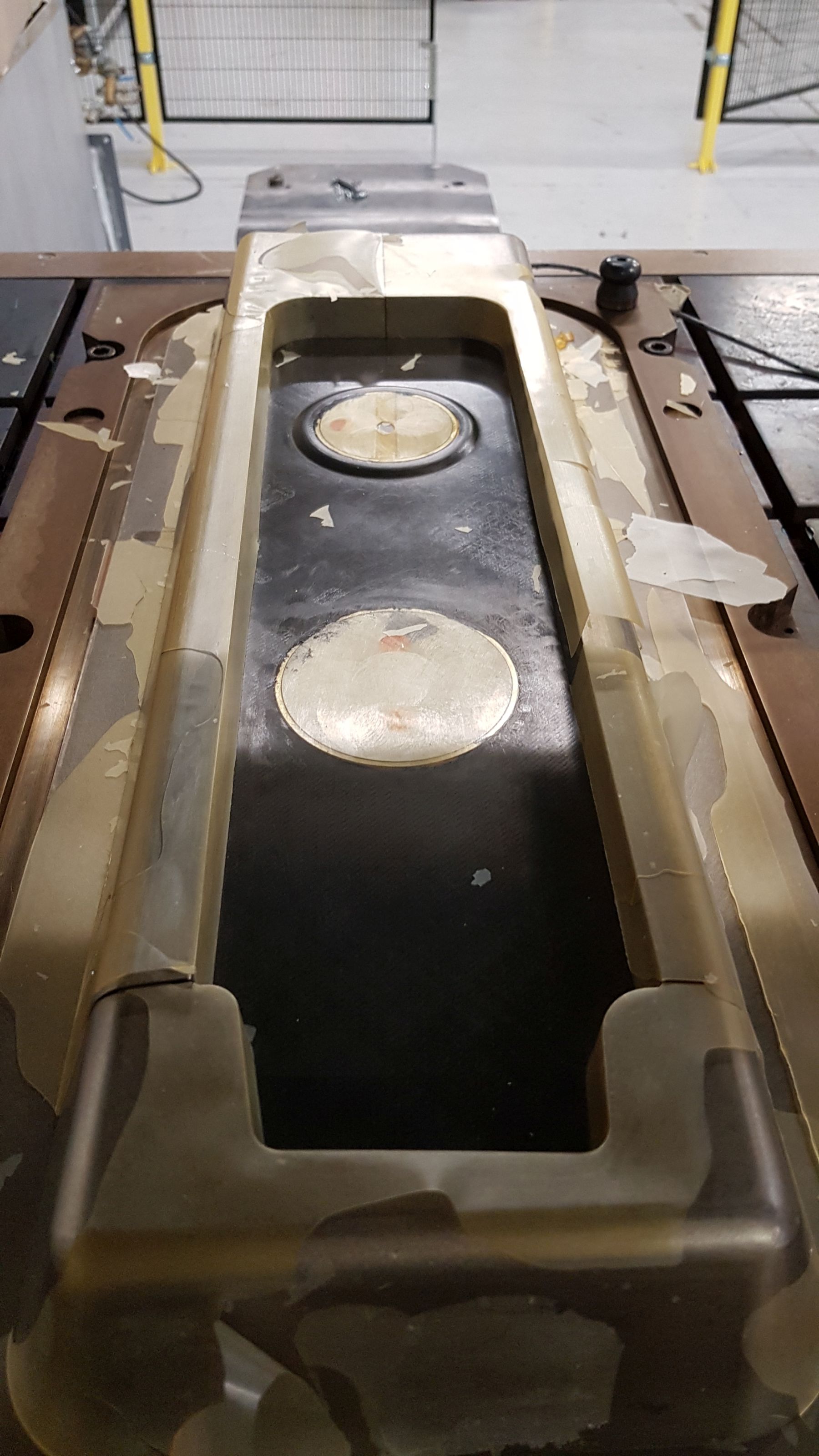
Vácuo é aplicado, resina é injetada e infiltra no pré-molde, seguido por uma cura de 90 minutos. Aqui, a prensa foi aberta para revelar a peça curada.
Etapa 10
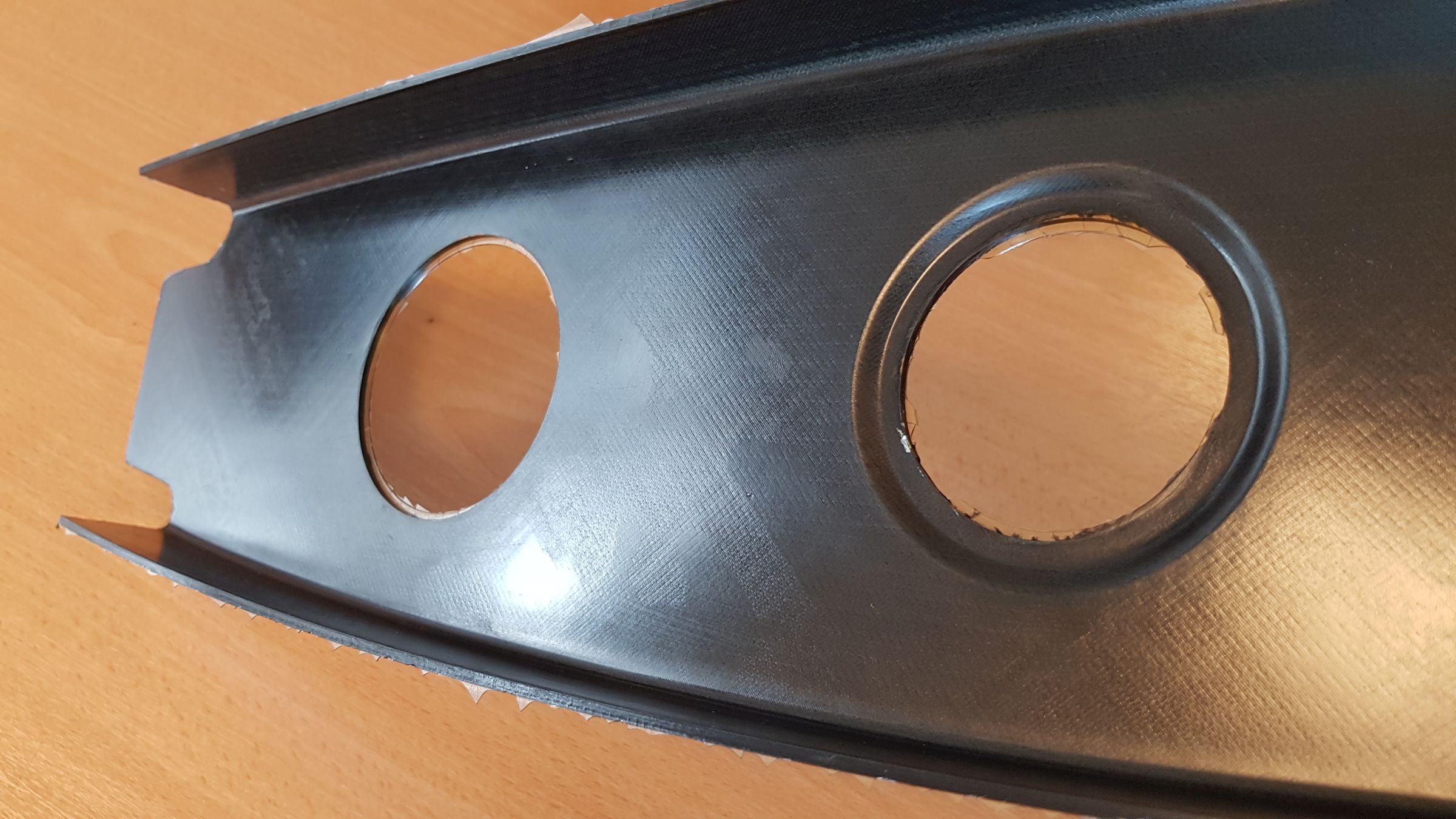
Após a desmoldagem ser concluída, o flash de resina será removido por um ciclo parcial completo de 4 horas.
Controle inteligente
Outra característica importante da célula de pré-formação automatizada da Techni-Modul Engineering é seu sistema de controle integrado. Chamado de SMART CONTROL, seu backbone é um sistema de câmera e software multiuso que compara as fotos tiradas durante o processamento com o banco de dados CAD da peça, permitindo o reconhecimento da forma da preforma, controle de orientação da fibra, posicionamento da camada e detecção de defeitos e detritos de objetos estranhos (FOD ) O feedback do SMART CONTROL instrui o robô como pegar e colocar as camadas na sequência e no tempo corretos, mas também alerta o operador da célula quando detecta erros. “O sistema pode ser configurado para que o operador remova manualmente a camada e reinicie o sistema para substituí-la”, explica Chevallet, “ou podemos trabalhar com o cliente para criar uma solução automatizada para remover camadas defeituosas e corrigir erros”.
As mesmas imagens ópticas usadas para detectar bordas e contornos das camadas também são usadas para controlar a orientação da fibra. Chevallet admite que se a parte for muito grande (por exemplo, 2 metros de comprimento em comparação com 200 por 200 milímetros), "você pode precisar de uma câmera tirando fotos [de uma] posição vertical mais alta para detectar as bordas das camadas e, em seguida, aproxime-se de a parte para verificar a orientação da fibra. Você calibra essa sequência para cada tipo de peça. Para detectar rugas e FOD, existe um banco de dados de diferentes defeitos e você pode adicioná-lo, de forma que o algoritmo de aprendizado profundo melhore com o tempo. A ideia é ter um sistema que seja adaptável. ”
Tempo de ciclo e produção futura
As pré-formas para a nervura OPTICOMS foram feitas usando HiMax, e a longarina I-beam usou HiTape. O sistema de resina para ambos era o epóxi líquido HexFlow RTM6 de um componente (1K) da Hexcel, que tem um ciclo de cura de 90 a 120 minutos a 180 ° C. Esta cura é a etapa mais longa nos tempos de ciclo da peça tanto para a nervura OPTICOMS quanto para a longarina de teste em I, como pode ser visto na Tabela 1.
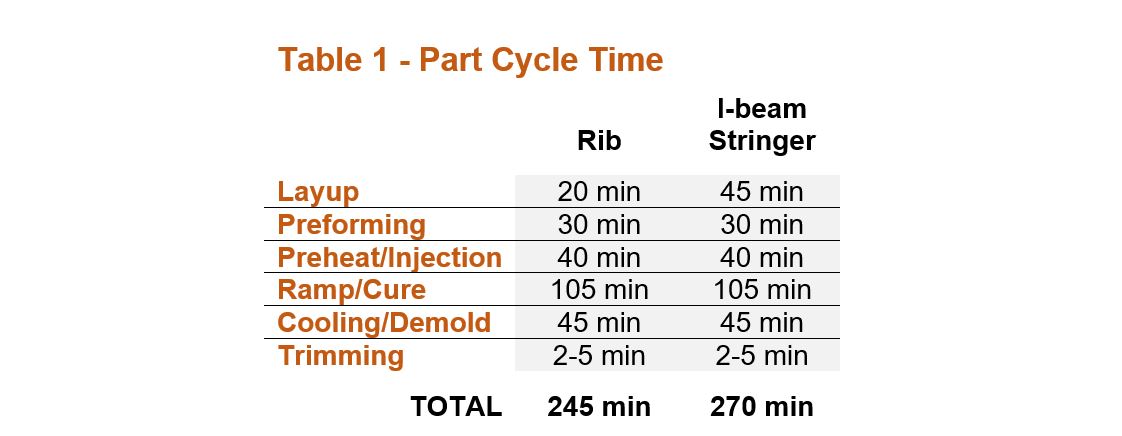
Fonte | Engenharia Techni-Modul
Até o momento, este foi o único epóxi qualificado para RTM de estruturas aeroespaciais. No entanto, está crescendo o interesse na qualificação de sistemas de dois componentes que são misturados no cabeçote de injeção, oferecendo maior flexibilidade do ciclo de cura e eliminando a necessidade de transporte e armazenamento refrigerados necessários para evitar a reação prematura do RTM6 pré-misturado.
A Airbus Helicopters (Donauworth, Alemanha) trabalhou com a Alpex Technologies (Mils, Áustria) no projeto SPARTA para demonstrar um processo HP-RTM usando uma versão de dois componentes do HexFlow RTM6 para atingir curas de 30 minutos a 180 ° C para uma porta A350 frame, que é uma estrutura primária de formato complexo medindo 2 metros de altura, 200-250 milímetros de largura e 8-10 milímetros de espessura (consulte “HP-RTM para produção em série de aeroestruturas CFRP econômicas”). A Airbus também demonstrou uma costela CFRP de 1,5 metros por 0,5 metros feita usando HP-RTM por sua subsidiária do Composite Technology Center (CTC, Stade, Alemanha), alcançando ciclos de moldagem de 20 minutos para peças com volume de fibra de 60% e menos de 2 % voids. No ano passado, a CTC trabalhou com vários fornecedores de nível para fazer a transição de peças pré-impregnadas de layup manual para HP-RTM para o A320. No entanto, os sistemas de resina 2K devem ser qualificados para a produção de aeroestruturas, e o CTC está preocupado com a capacidade de garantir continuamente a qualidade da mistura dos sistemas de resina 2K in situ. Alpex está usando sensores in-mold da Netzsch (Selb, Alemanha) e Kistler (Winterthur, Suíça) para ajudar a alcançar isso, e outras soluções estão sendo desenvolvidas (consulte “Epóxi de 2 partes para aumentar a produção de aeroestruturas compostas”).
Mesmo sem sistemas 2K, volumes de produção maiores podem ser possíveis. As molduras das portas no projeto SPARTA foram removidas após a cura inicial de 30 minutos a 180 ° C e pós-curadas fora da prensa, sob vácuo para remover o estresse térmico e garantir as propriedades mecânicas. De acordo com o chefe de P&D da Alpex, Bernhard Rittenschober, isso requer conjuntos extras de ferramentas, mas apenas uma única unidade de prensa e injeção. Ele explica que o custo extra da ferramenta é compensado pelo menor custo do processo e da prensa e pode ser recuperado rapidamente, mesmo com um baixo volume de 500-1.000 peças / ano.
“A principal conquista desses demonstradores é a capacidade de fazer aeroestruturas primárias com uma injeção curta de resina em comparação aos processos RTM aeroespaciais convencionais, onde tem sido um processo longo e difícil infiltrar resina em peças tão grandes com reforços de fibra de carbono UD”, diz Pagnac . “Estamos apenas no início do que podemos alcançar com este tipo de pré-formação automatizada inteligente e processamento C-RTM”, acrescenta Chevallet. “Ele tem o potencial de atingir a produção sustentável e mais econômica de estruturas de revestimento integradas ao reforço que está sendo idealizada para aeronaves futuras”.
Resina
- Materiais de impressão 3D para viagens espaciais?
- Três maneiras pelas quais as empresas estão usando compósitos no aeroespacial para o futuro
- Henkel oferece plataforma de materiais para fabricação de aditivos
- Materiais:Tecnologia de produção de Honeycomb leve em K 2019
- Materiais:Poliamida de alta temperatura retardante de chamas para impressão 3D
- Preparando-se para um futuro autônomo
- Trelleborg anuncia novo distribuidor de materiais de ferramentas
- Arkema Inc. constrói planta de produção U.S. PEKK
- 10 materiais mais resistentes para impressão 3D
- Materiais para componentes de Invar 36