União automatizada de estruturas compostas híbridas metal-termoplásticas
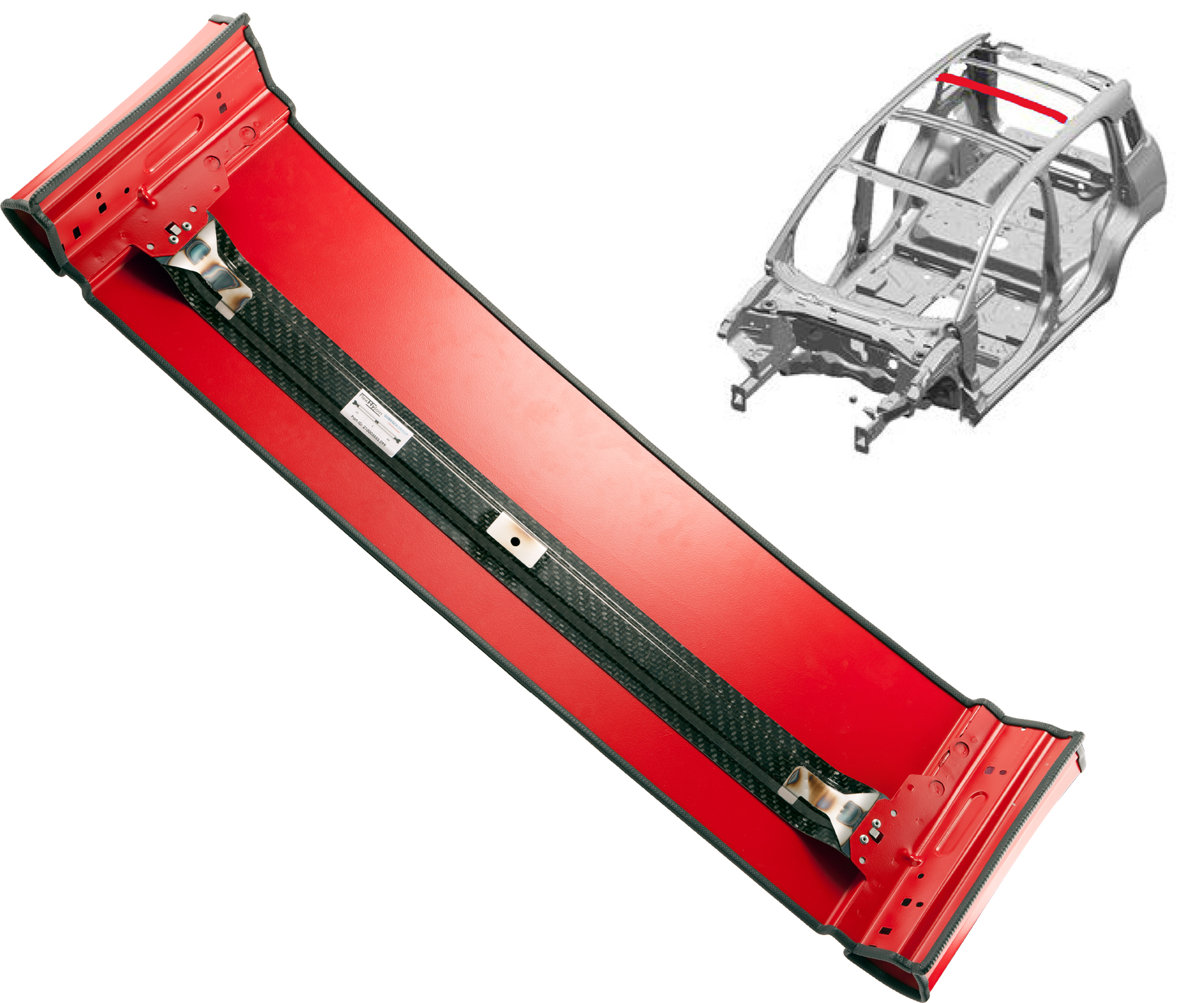
Ativando a união híbrida em escala industrial
FlexHyJoin demonstra um processo de produção em massa para a produção de um reforço de telhado composto termoplástico com suportes de metal soldados para montagem em um corpo de metal branco, como o caso de uso do projeto, o Fiat Panda carro da cidade. Fonte | IVW
Estruturas híbridas de metal-composto continuam a ser de interesse para aplicações automotivas e aeroespaciais, oferecendo peso reduzido e desempenho aprimorado ao colocar “o material certo no lugar certo”. Compósitos termoplásticos (TPCs) são atraentes para tais estruturas multimateriais devido ao seu rápido processamento, incluindo a capacidade de serem soldados e termoformados. No entanto, a união de compósitos a metais tem, até agora, contado principalmente com fixadores mecânicos, que exigem furos que danificam as fibras de suporte. A união adesiva também tem sido usada, mas vários termoplásticos são difíceis de unir dessa maneira; além disso, os adesivos adicionam material e peso. Por exemplo, o BMW i3 , que usa um chassi de plástico reforçado com fibra de carbono (CFRP) e painéis de plástico da carroceria, usa 16 kg de adesivo, o que neutraliza parcialmente o potencial de redução de peso dos compostos.
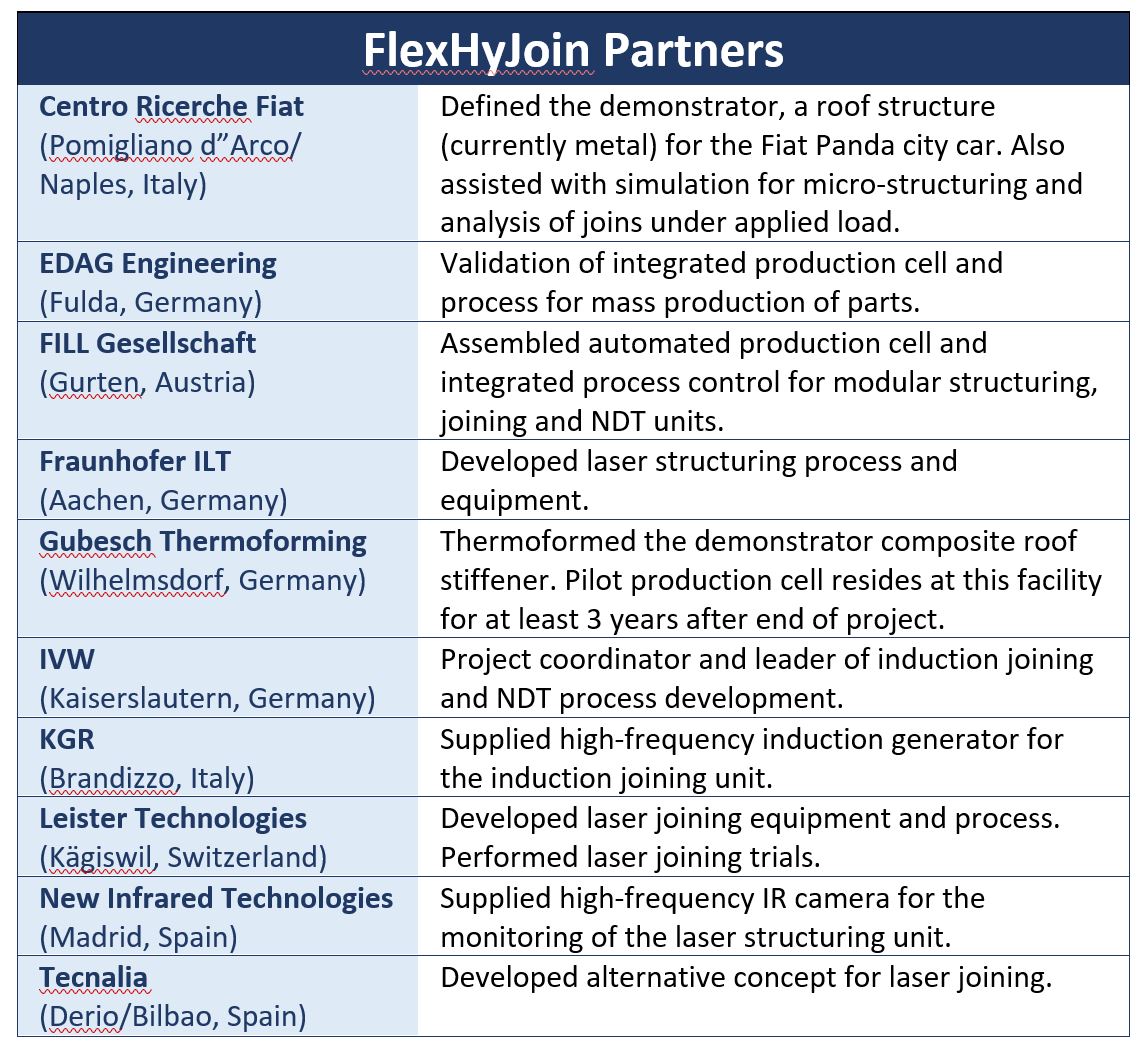
FlexHyJoin é um projeto financiado pelo programa de pesquisa e inovação Horizon 2020 da União Europeia, conduzido de outubro de 2015 a dezembro de 2018, que buscou enfrentar os desafios de unir TPC e peças de metal. Coordenado pelo Institut für Verbundwerkstoffe (IVW) - uma instituição de pesquisa sem fins lucrativos do estado da Renânia-Palatinado e da Universidade Técnica de Kaiserslautern, Alemanha - FlexHyJoin reuniu 10 parceiros de toda a Europa para desenvolver um processo automatizado permitindo um teto automotivo TPC estrutura a ser montada em um corpo metálico em branco (BIW). A estratégia era produzir uma junção neutra de peso e de alta resistência - sem adesivos ou fixadores - por pré-tratamento a laser dos suportes de metal e fixando-os ao reforço do telhado por indução e junção a laser. Isso foi alcançado em uma única célula de produção automatizada com controle de processo integrado e teste não destrutivo em linha (NDT).
Demonstrador híbrido em 140 segundos
O parceiro do projeto Centro Ricerche Fiat (Pomigliano d'Arco / Nápoles, Itália) forneceu especificações para a parte do demonstrador - um reforço de teto para o Fiat Panda carro urbano que atualmente é fabricado em aço. Para FlexHyJoin, a peça foi termoformada a partir de compósito termoplástico (Fig. 1) por Gubesch Thermoforming (Wilhelmsdorf, Alemanha) usando 1,5 milímetros de espessura de Tepex Dynalite 102 tecido de fibra de vidro / poliamida 6 (PA6) organosheet fornecida por Bond-Laminates (Brilon, Alemanha). A fim de juntar este reforçador de telhado TPC no Panda BIW de aço, um conjunto de suportes laterais (esquerdo e direito) feito de aço DC04 de 0,7 mm de espessura foram unidos a laser nas extremidades. Um suporte central feito do mesmo material foi fixado por meio de união por indução. FlexHyJoin mostrou que ambos os métodos de união podem ser usados para a produção de estruturas híbridas industriais.
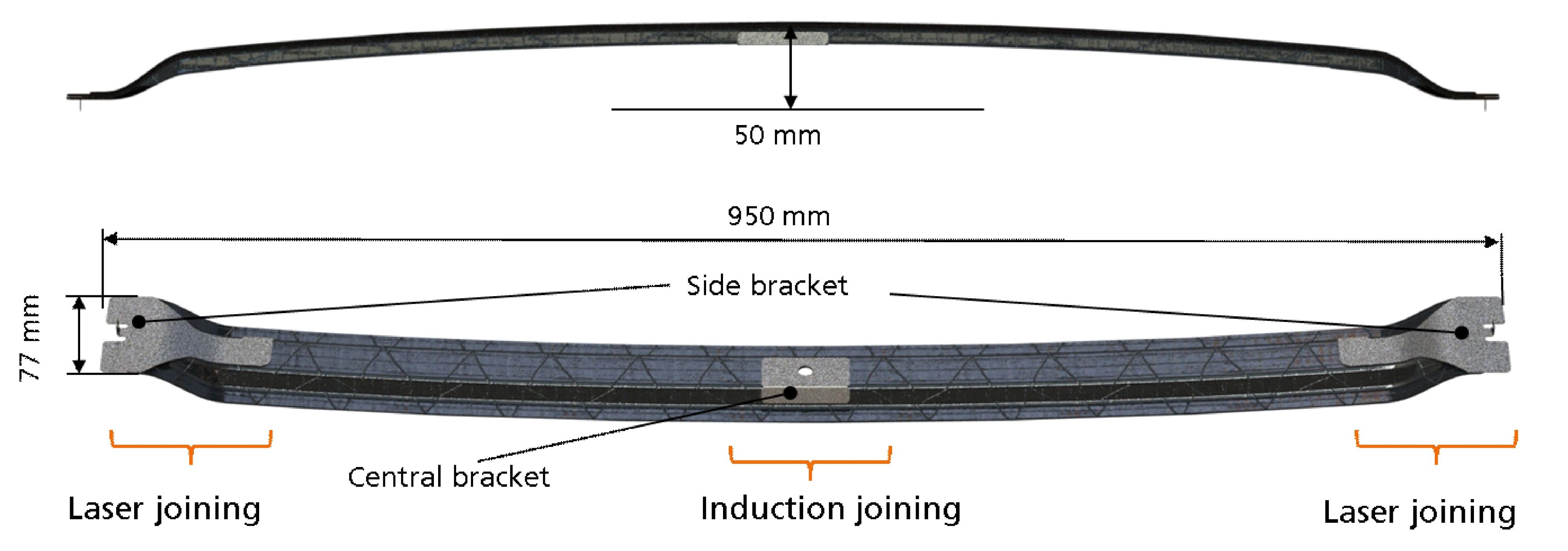
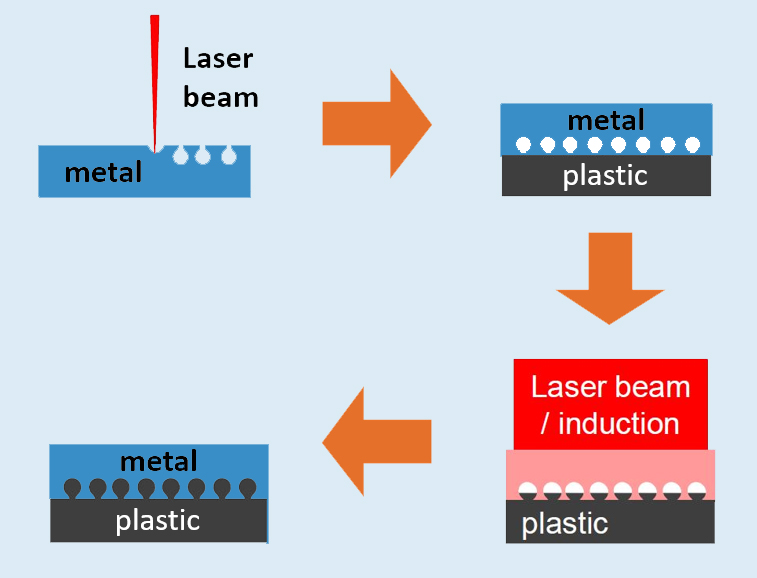
Fig. 1 Estruturação de superfície para união híbrida
FlexHyJoin demonstra laser e união por indução de suportes de aço a um reforço de telhado GF / PA6 estampado ( topo ) Essas juntas híbridas contam com o tratamento de superfície dos suportes de metal para criar recortes, que são preenchidos com plástico derretido durante as etapas do processo de junção ( parte inferior )
Fonte | IVW
Simplesmente derreter a matriz PA6 nos suportes de aço não produziria uma junção com resistência suficiente para atender aos requisitos estruturais. Portanto, um tratamento de superfície a laser foi necessário antes da união. “A superfície dos suportes foi estruturada por um laser para criar rebaixos”, explica Johannes Voithofer, gerente de projeto da Fill Gesellschaft (Gurten, Áustria), que foi encarregada de montar e integrar a célula de produção automatizada. “Os braquetes tratados são colocados na peça composta. Calor e pressão são então aplicados durante a união, fazendo com que a matriz PA6 do composto flua para os recortes induzidos por laser [ver Fig. 1]. ” O processo de estruturação foi desenvolvido por outro parceiro, o Fraunhofer Institute for Laser Technology (ILT, Aachen, Alemanha), e resulta em uma junção de metal compósito que combina adesão de material e travamento mecânico.
As peças unidas são então transferidas para uma estação NDT, onde são escaneadas em busca de defeitos usando um tipo de termografia. “Holofotes de halogênio são usados para aquecimento modulado da superfície do composto”, explica Vitalij Popow, pesquisador associado da IVW e líder no desenvolvimento do FlexHyJoin NDT e controle de processo. “Isso leva a um campo de temperatura oscilante dentro da estrutura composta. Analisamos a resposta térmica na superfície ao longo do tempo e identificamos defeitos nas juntas. ” O teste totalmente automatizado é concluído dentro da célula de produção para cada componente fabricado. A validação do processo foi realizada em cerca de 400 juntas.
A célula de produção automatizada FlexHyJoin, conforme configurada atualmente, executa estruturação, junção e NDT em paralelo com tempos de ciclo de 81 segundos, 98-108 segundos e 100 segundos, respectivamente, não incluindo o tempo de transferência robótica de peças entre as estações. Voithofer afirma que o tempo de ciclo por peça híbrida concluída é de aproximadamente 140 segundos.
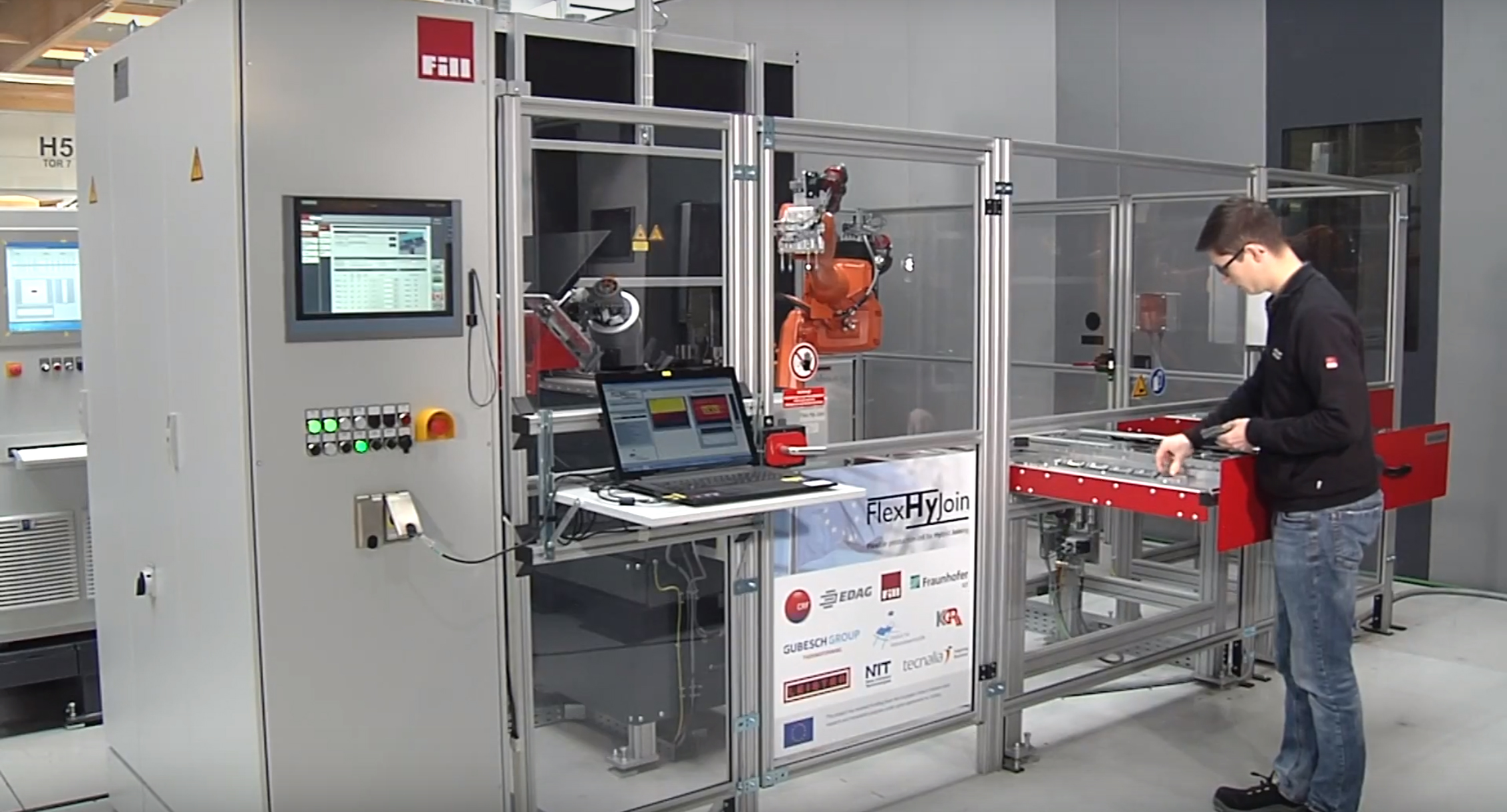
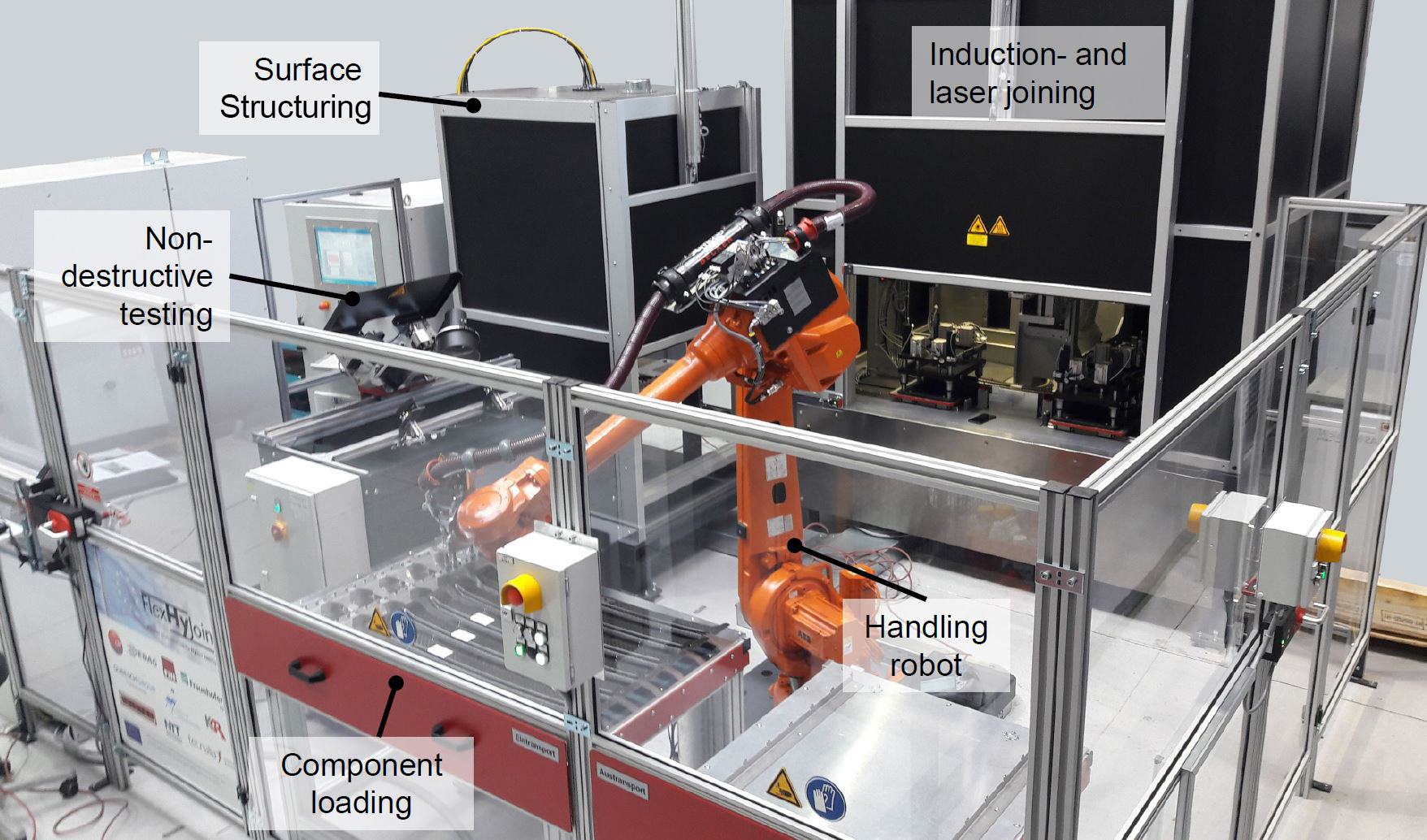
Fig. 2 Habilitando a união híbrida em escala industrial
A célula de produção piloto FlexHyJoin apresenta três estações modulares para estruturação de superfície, junção e NDT. O único robô de manuseio da célula transfere componentes da gaveta de carregamento para cada uma dessas estações, colocando as peças híbridas acabadas em uma gaveta adjacente. Fonte | IVW e Preencher
Estruturação de laser
O processo de estruturação a laser produz linhas com geometrias rebaixadas na superfície de união dos suportes de metal. Para FlexHyJoin, os cortes mediam 75 micrômetros de largura e 215 micrômetros de profundidade. Essas medidas, bem como o número de linhas e o padrão geral de linhas, podem ser ajustados e, idealmente, são combinados para atender aos requisitos de tempo de ciclo e peça.
“A posição, bem como o número de microestruturas na superfície de união podem ser adaptados ao carregamento no componente", explica Stefan Weidmann, pesquisador associado da IVW e líder da equipe de desenvolvimento da unidade de união por indução FlexHyJoin. “A distância entre as microestruturas pode ser reduzida em áreas altamente carregadas da superfície de união e aumentada em áreas menos carregadas para permitir um processo de microestruturação eficiente.”
A estruturação é obtida por ablação da superfície do suporte de metal usando um laser de fibra monomodo de alta potência fornecido pela IPG Photonics (Burbach, Alemanha). Este laser YLR-1000-WC tem uma saída máxima de 1.000 watts em um comprimento de onda de emissão de 1.070 nanômetros. “Usamos o laser de fibra monomodo para o processo de microestruturação por causa de sua alta focalização, mantendo um tamanho de ponto de aproximadamente 40 micrômetros”, explica Christoph Engelmann, líder da equipe de processamento de polímero da Fraunhofer ILT.
O laser está contido em um cabeçote ótico montado em um braço robótico ABB 1200. “Dentro da cabeça óptica, temos dois espelhos galvanométricos para desviar o feixe em um campo de trabalho de 240 por 240 milímetros”, detalha Engelmann. “Além disso, há uma lente móvel para rastrear a altura z (z-shifter). Usamos o robô apenas para posicionar a cabeça de varredura acima dos componentes de metal e, em seguida, o feixe é desviado pelos espelhos e a posição z para cada linha da microestrutura é adaptada pelo z-shifter. Assim, não há movimento da cabeça durante o processamento. Desta forma, somos capazes de tratar peças 2,5D, permanecendo na mesma posição z para cada linha discreta, mas capazes de ajustar entre as linhas. ”
“Por motivos de segurança, tanto as unidades de estruturação quanto as de junção são fechadas”, explica Voithofer, observando os gabinetes pretos na célula de produção piloto (Fig. 2). Assim, um portão / porta automatizado permanece abaixado durante as operações a laser, abrindo para retirada das peças acabadas e inserção de novas.
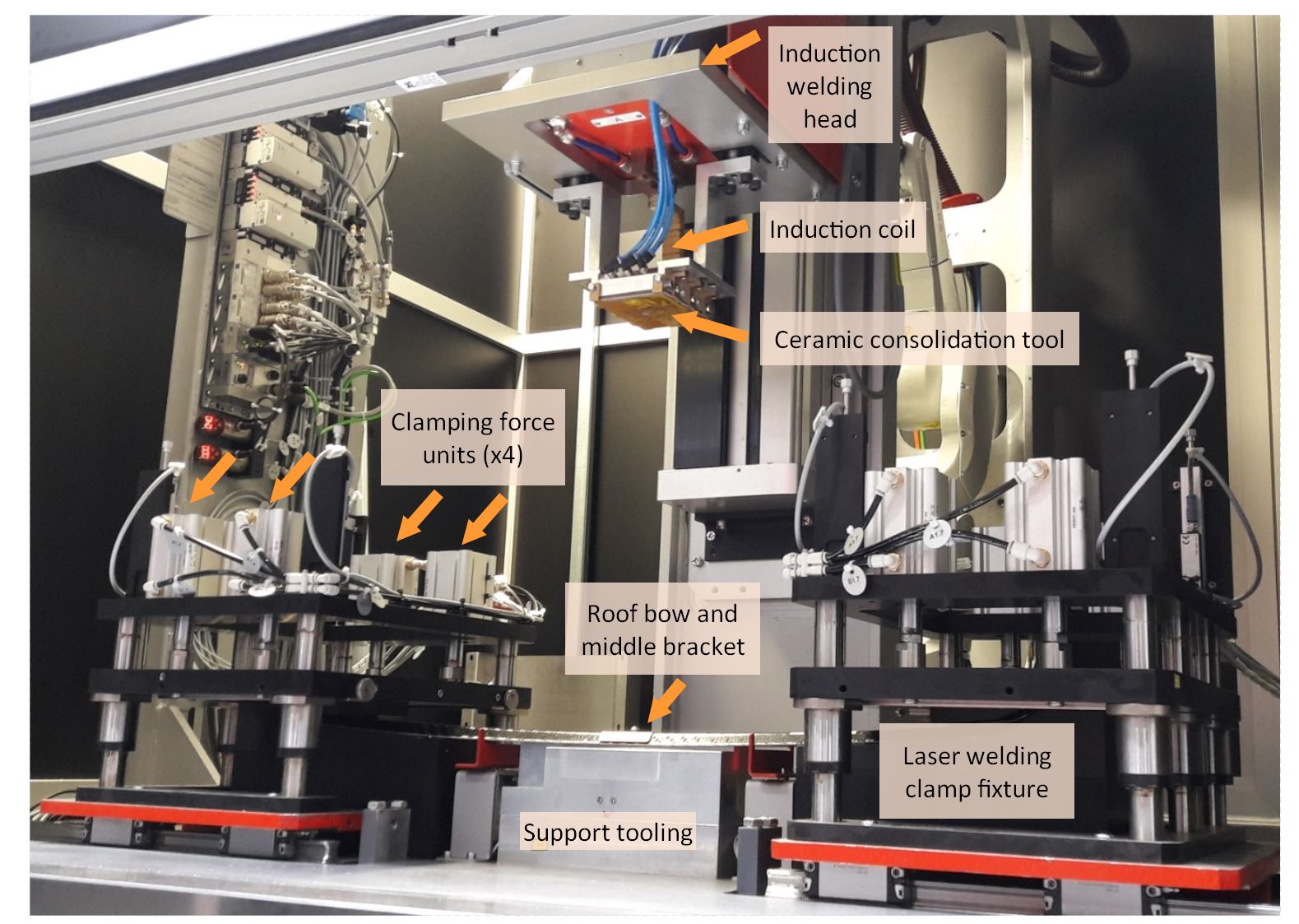
Fig. 3 Célula de indução e união a laser
Na célula de união, a união por indução é usada para prender o suporte do meio, enquanto a união a laser é usada para unir os suportes laterais em cada extremidade do arco composto do telhado. Fonte | IVW e Preencher
Indução e união a laser
Adjacente à célula estruturante está a célula de união, que compreende duas operações distintas:união por indução do suporte central e união por laser dos suportes laterais esquerdo e direito. “Para peças maiores com uma complexidade moderada, como o suporte central, a união por indução é um método de união mais adequado”, diz Weidmann. “Uma ferramenta de consolidação de cerâmica com indutor aplica pressão na área de união e é permeável ao campo eletromagnético, levando a uma entrada de energia eficiente no suporte metálico para aquecimento. Isso é conveniente para formas planas, mas é mais desafiador para formas complexas, como a geometria dos suportes laterais. Portanto, foi mais eficaz usar a junção a laser para isso. ” Weidmann acrescenta:“A união por indução é melhor para peças grandes e de complexidade moderada, enquanto a união a laser é mais adequada para peças de alta complexidade.”
Um orifício perfurado no reforço de telhado composto alinha-o no topo da ferramenta de suporte, moldado para coincidir com a curvatura do reforço termoformado. Um orifício cortado a laser no suporte central o posiciona no reforço do telhado, enquanto os suportes laterais são alinhados por sua forma que corresponde às extremidades do reforço do telhado.
“O suporte central foi unido usando descontínuo união por indução. “Esta é essencialmente uma junção de prensa quase estática”, diz Weidmann, “o que simplesmente significa que é um processo estático, alcançando uma junção de área em um lugar, mas há movimento na direção z porque a espessura do composto muda ligeiramente devido à pressão de consolidação aplicada durante a união (por indução). ”
A unidade de união por indução contém um gerador de alta frequência KGR (Brandizzo, Itália) para fornecer um campo elétrico alternado à bobina de indução. A cabeça é movida por meio de um motor elétrico e fuso (Fig. 3) para que a ferramenta de consolidação de cerâmica seja pressionada contra o suporte de metal. A bobina de indução na ferramenta de consolidação faz com que o metal aqueça, o que derrete a matriz composta e cria a junta. “A pressão é aplicada em todo o aquecimento e resfriamento”, observa Weidmann.
A união a laser dos suportes laterais começa simultaneamente à união por indução. Dois dispositivos de fixação, localizados em cada lado da ferramenta de suporte, podem aplicar 4.000 Newtons de força de fixação aos suportes laterais. “A fixação é necessária para minimizar a lacuna entre o compósito e os componentes de metal”, explica Voithofer. “Isso evita vazios na junta.” Depois que a força de fixação é aplicada, o cabeçote do laser se move para a posição. É equipado com um diodo laser LineBeam fornecido pela Leister Technologies (Kägiswil, Suíça). Johannes Eckstaedt de Leister explica que este laser tem uma potência máxima de saída de 600 watts em um comprimento de onda de emissão de 980 nanômetros. O feixe é formado em uma linha de 27 mm por 1 mm por lentes ópticas e é focado no suporte de metal. O cabeçote do laser é montado em um braço do robô que permite que ele se mova ao longo da superfície moldada do suporte. “Definimos velocidades diferentes para cada área dos suportes para atingir uma temperatura de união homogênea, reduzindo o estresse térmico para os melhores resultados de união”, diz Eckstaedt.
Em geral, a união a laser pode usar união por transmissão ou por condução de calor. Para a união de transmissão de laser, o composto que está sendo unido deve ser transparente para o comprimento de onda selecionado do laser. O laser então passa pelo compósito, atinge a superfície metálica do suporte e o aquece. No entanto, este método não foi usado no demonstrador FlexHyJoin porque o laminado de folha orgânica do reforçador de telhado não era transparente a laser. Em vez disso, o método alternativo de união por condução de calor foi usado. Isso simplesmente aplica o laser diretamente na superfície do metal, que conduz calor através do material de base de metal para o compósito, derretendo a matriz PA6 a 220-300ºC e criando a junta. “Devido à alta condutividade térmica dos suportes de aço, o calor do laser se espalha rapidamente, unindo-se aos suportes laterais de maneira eficiente”, diz Voithofer.
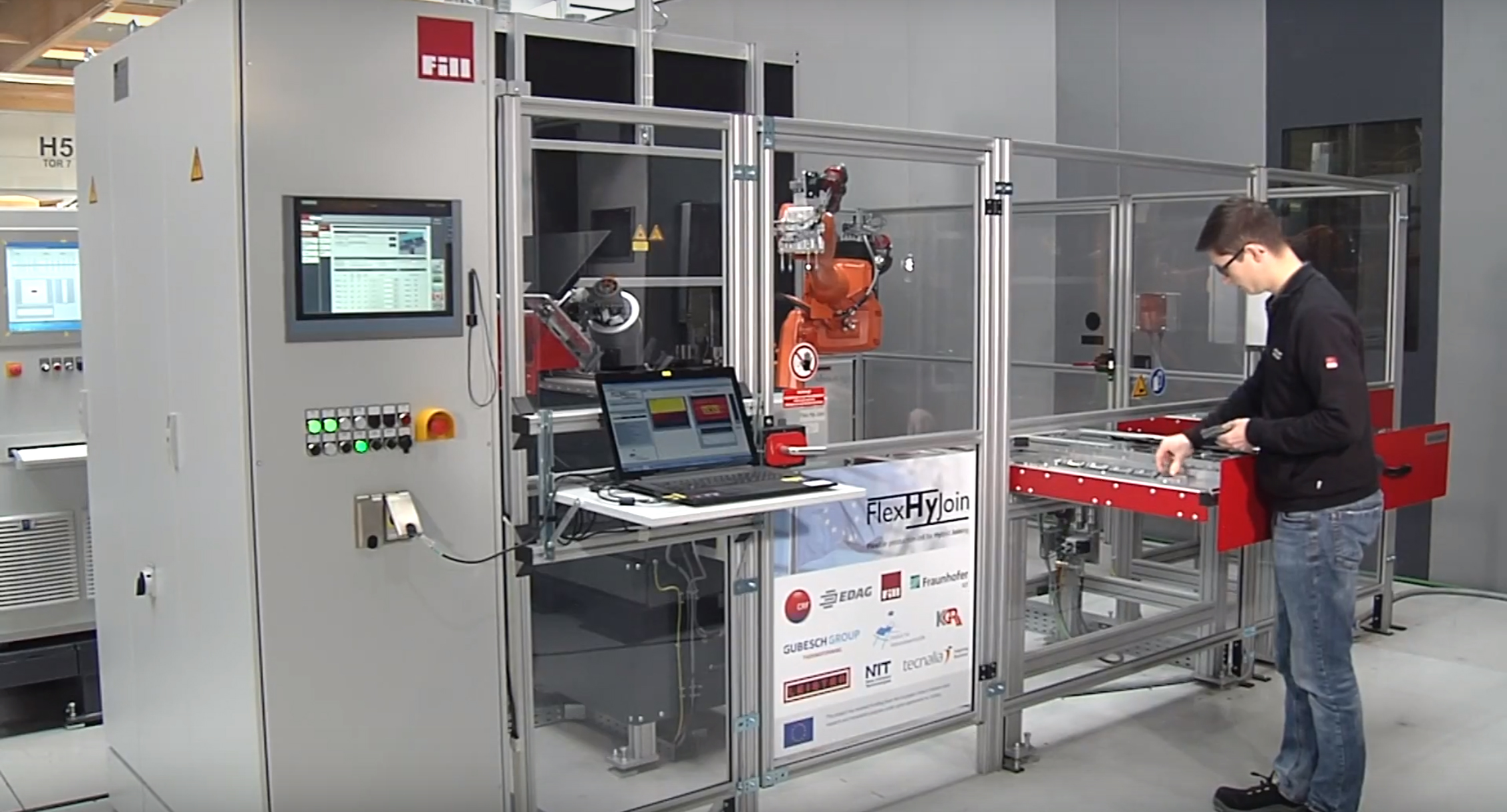
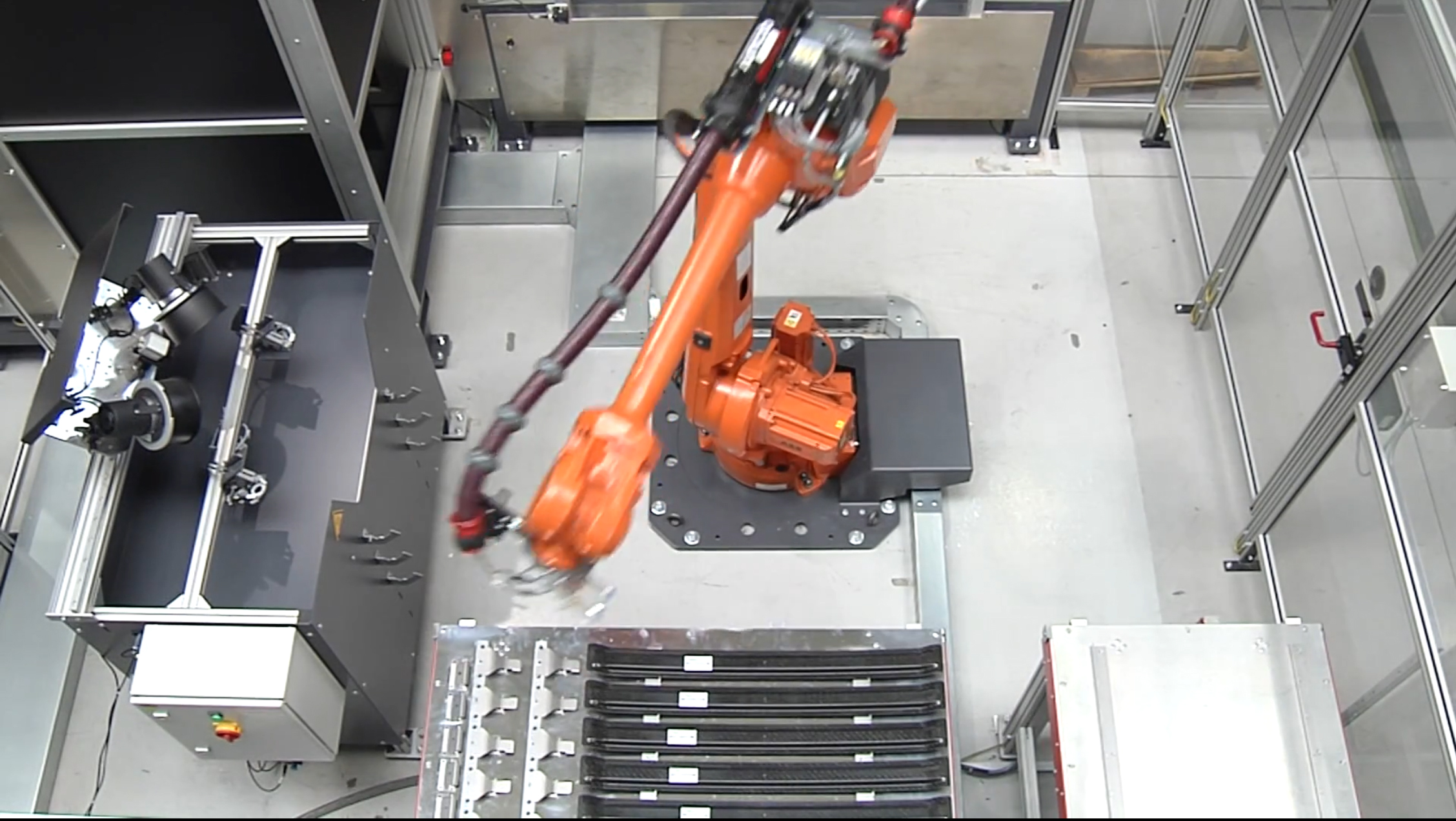
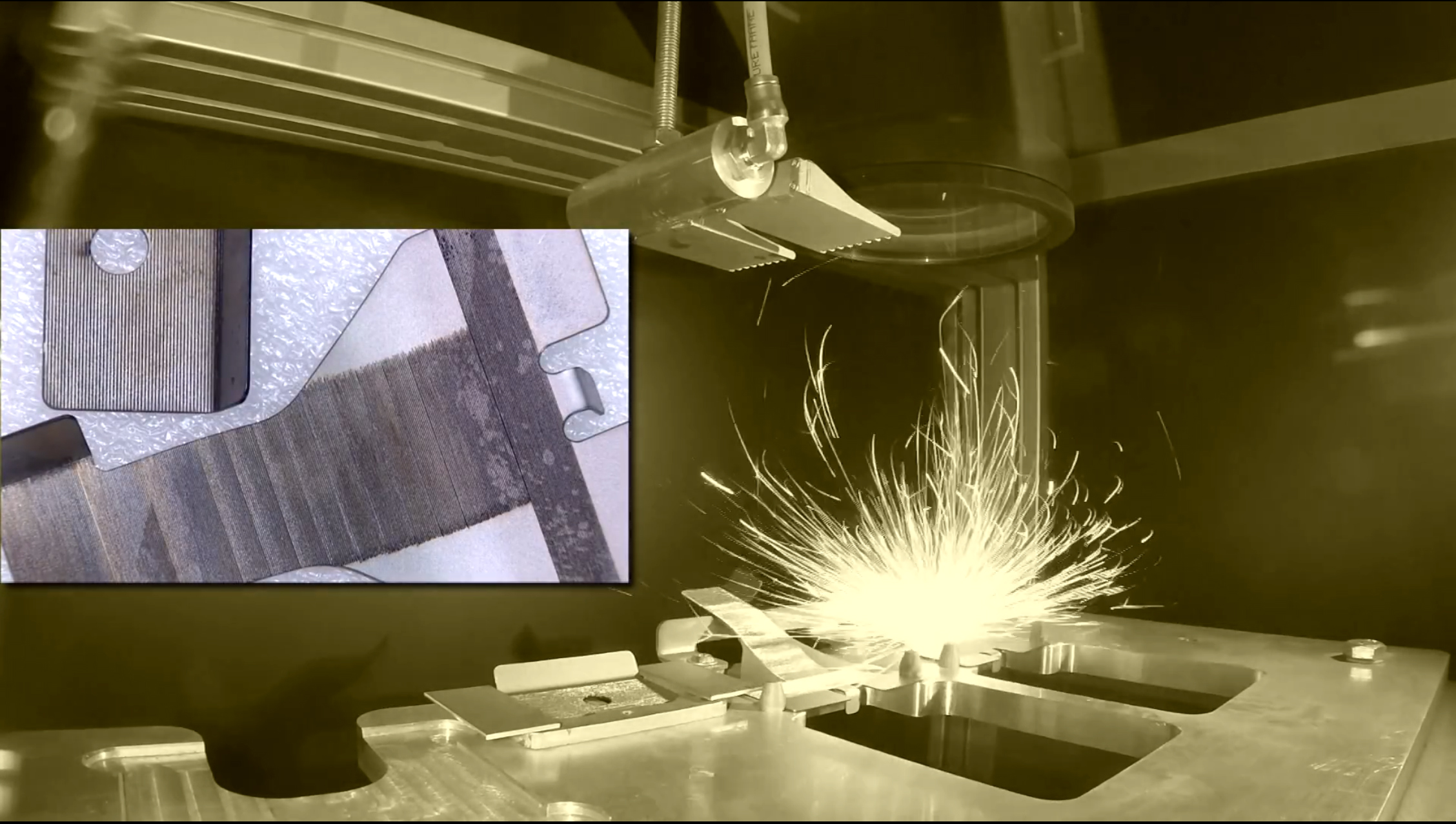
Etapa 3. Dentro da célula de estruturação, um laser de fibra de alta potência cria rebaixos na superfície do suporte a serem unidos no reforço de telhado composto.
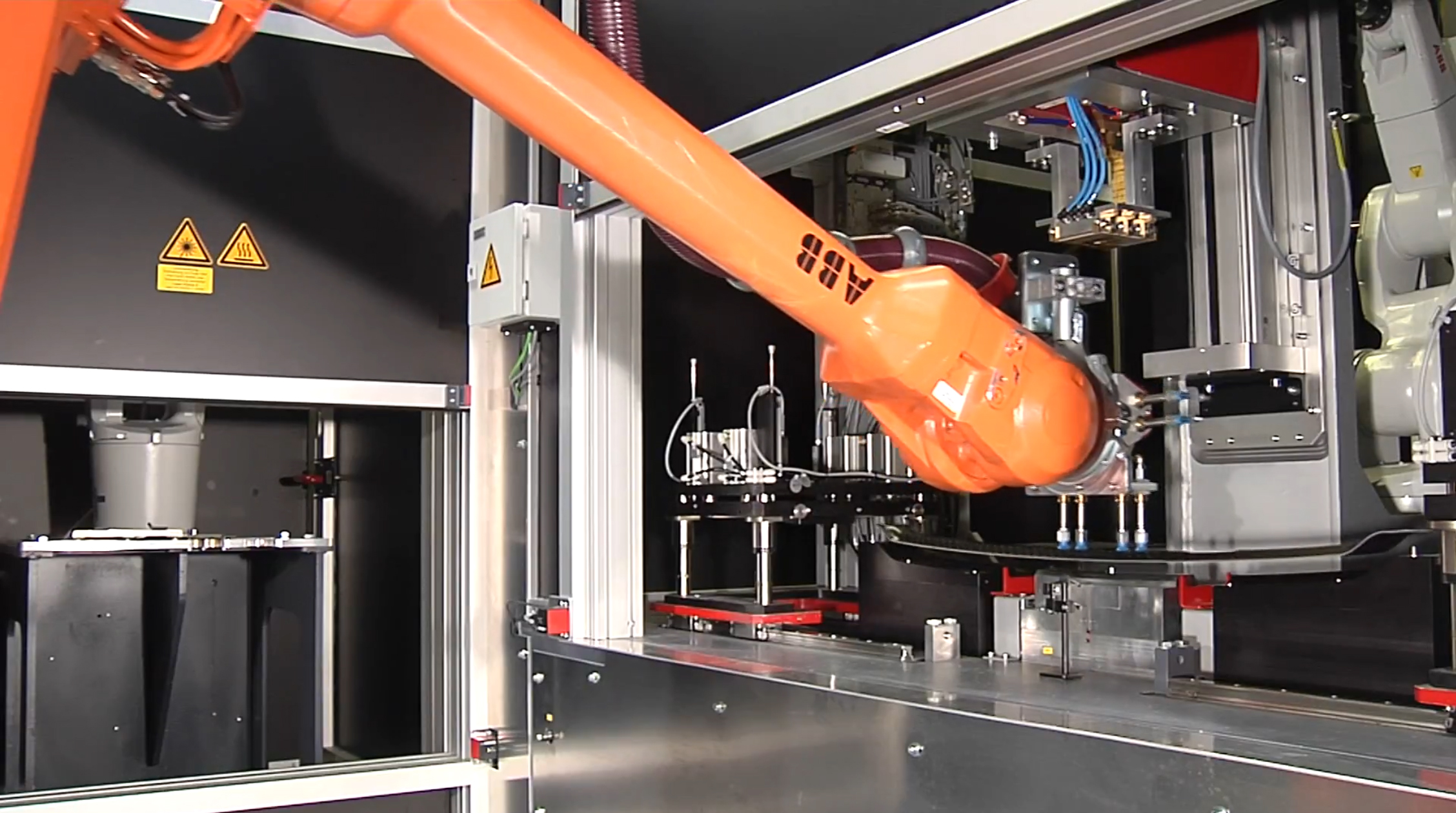
Etapa 4. Enquanto os suportes são tratados a laser, o robô pega um arco de telhado TPC da gaveta de peças e o coloca na célula de união, à direita da célula estruturante.
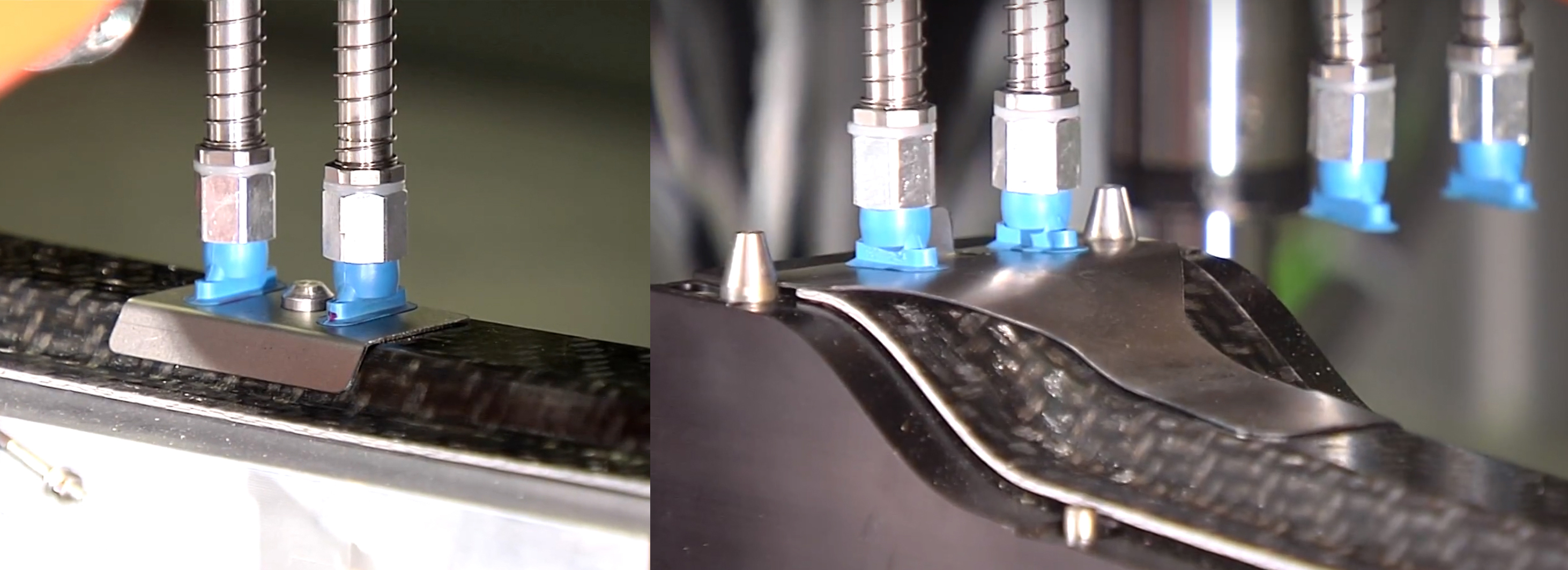
Etapa 5. O robô volta para a célula estruturante, pega os braquetes tratados e os coloca, com o lado estruturado para baixo, na proa do telhado do TPC.
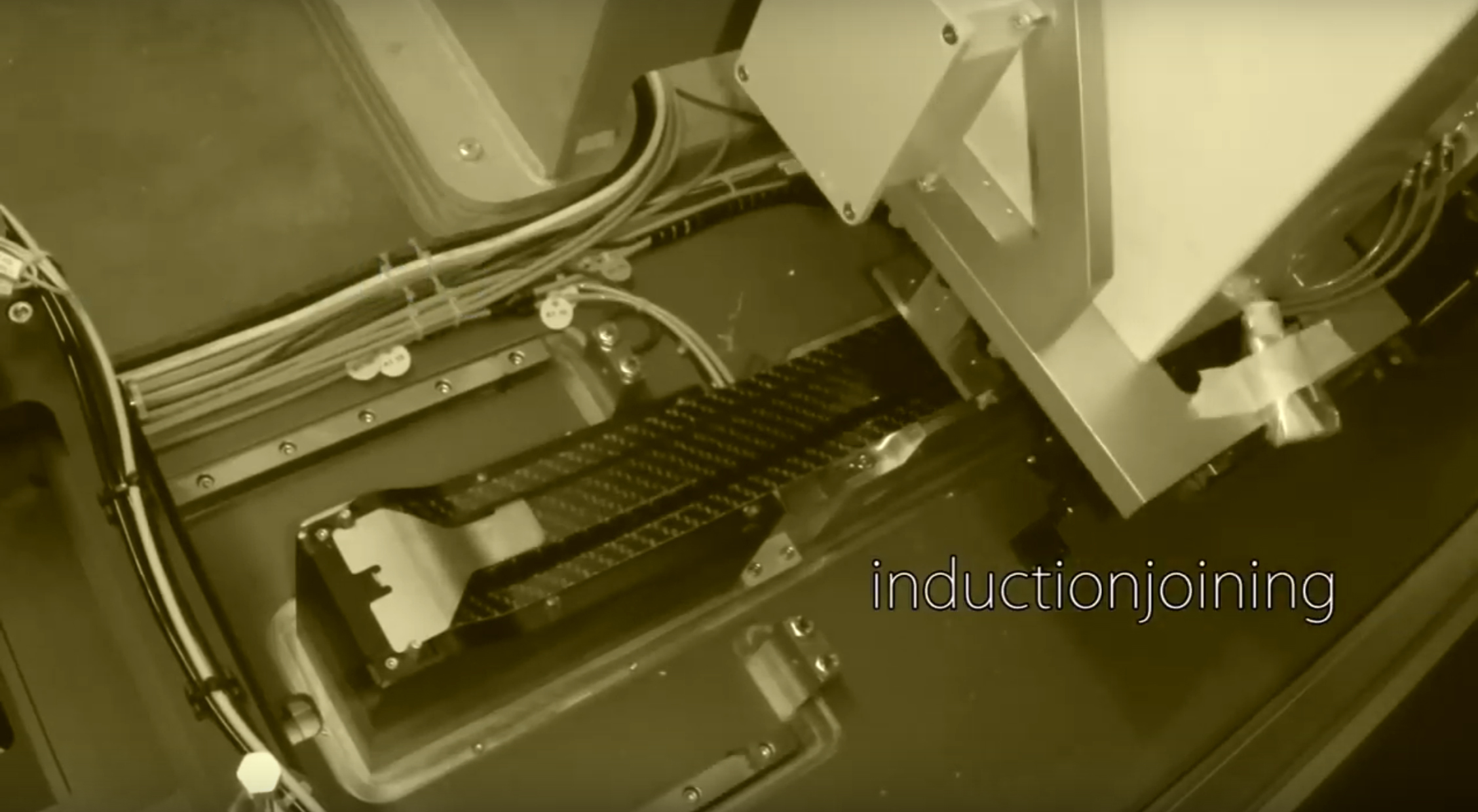
Etapa 6. O robô então coloca as unidades de fixação nos três suportes. A unidade de união por indução desce para o suporte central. A bobina de indução faz com que o suporte de metal aqueça, derretendo a matriz PA6 do compósito subjacente.
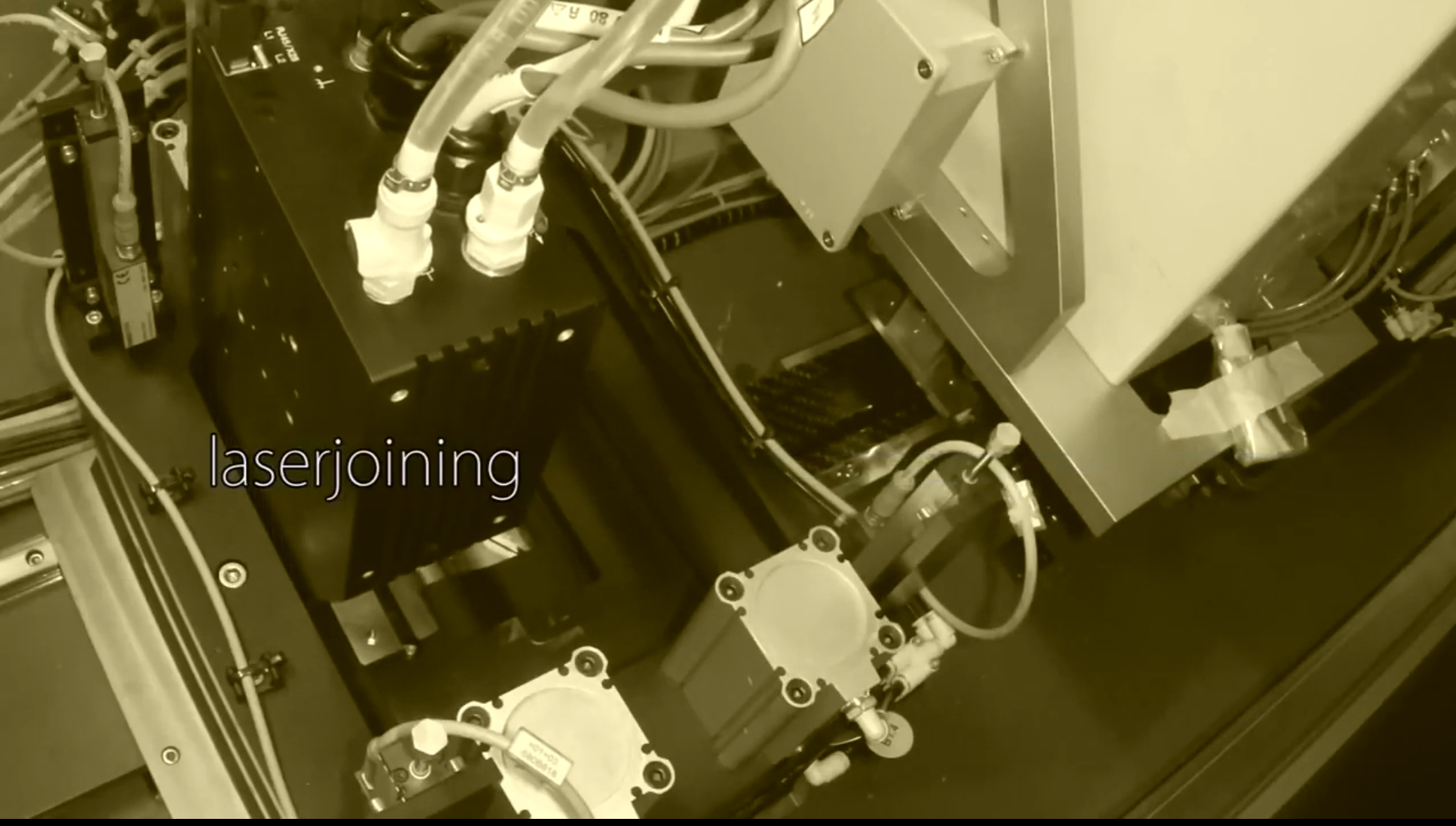
Etapa 7. Enquanto a união por indução é concluída, a unidade de união a laser é abaixada para unir os suportes esquerdo e direito. O laser aquece o metal, fazendo com que a matriz PA6 subjacente derreta nos recortes, criando uma junção de alta resistência.
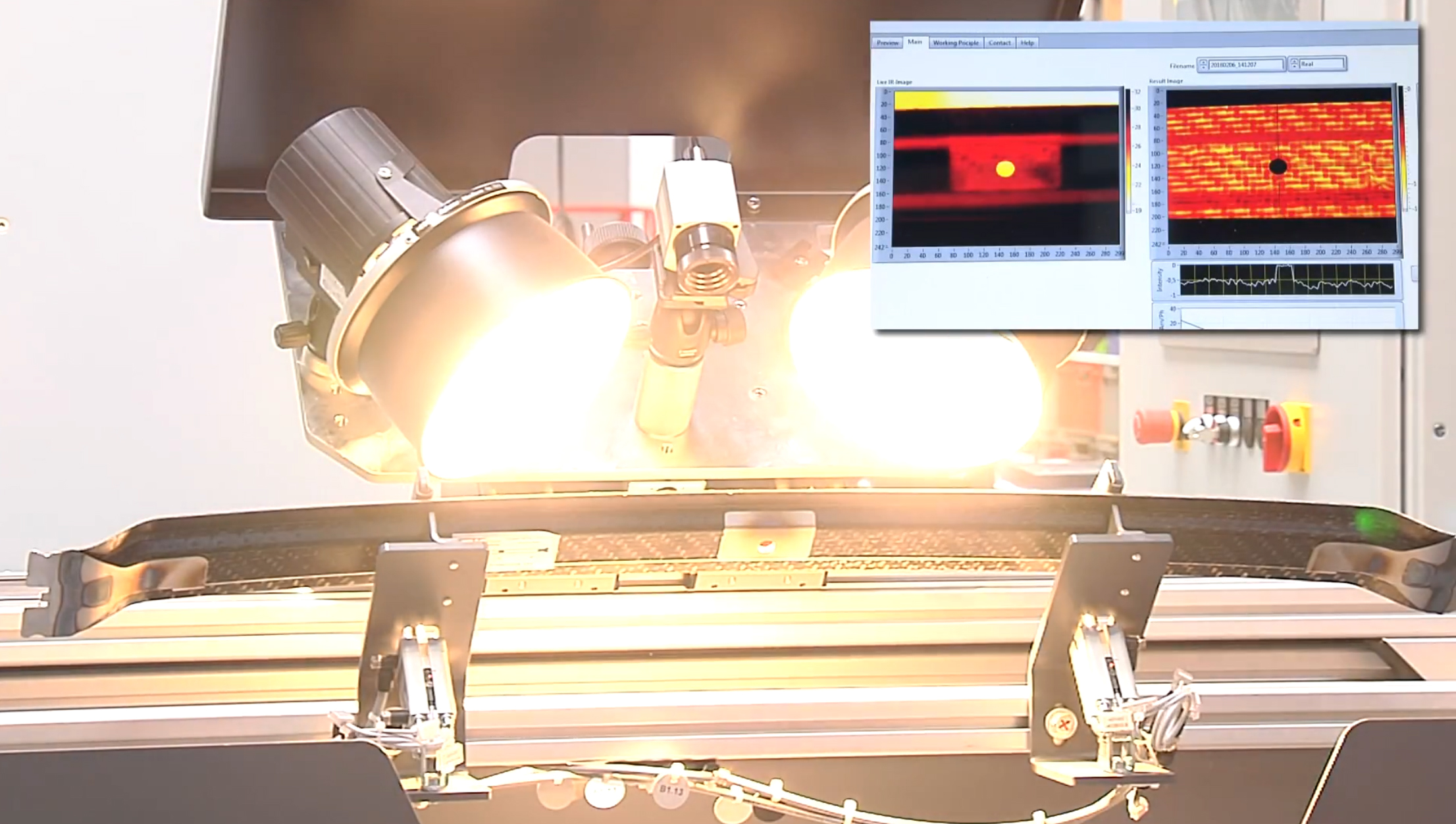
Ingressando no controle do processo
O método básico para controlar os dois processos de união é medir a temperatura e o tempo em relação a um conjunto de parâmetros otimizados que foram definidos por meio de testes. “Portanto, produzimos a união de amostras de teste com diferentes parâmetros e realizamos testes mecânicos para cada conjunto de parâmetros usando configurações de teste especiais. Para o suporte lateral, uma combinação de um teste de cisalhamento e um teste de remoção foi desenvolvida, e para o suporte central usamos um teste de carga de pressão, comparável a um teste de cisalhamento de volta, mas você empurra em vez de puxar, a fim de obter uma carga de cisalhamento na área de união ”, diz Popow. A configuração destes testes especiais foi desenhada em conjunto com a EDAG Engineering GmbH (EDAG, Fulda, Alemanha), que também fez a análise dos resultados dos testes. Seguindo este procedimento, o melhor conjunto de parâmetros para os processos de união foi identificado e então utilizado na célula de produção piloto.
“O processo de união por indução foi calibrado com antecedência”, diz Weidmann. “Sabemos que atingimos a temperatura de união após aproximadamente 30 segundos, mas também medimos a temperatura in-situ por razões de segurança para evitar um superaquecimento.” Um pirômetro, que mede remotamente a radiação de uma superfície, foi usado para medir um ponto quente conhecido na área de união de indução. “Mas ele não pode fornecer medições precisas da junção do laser devido ao alto nível de luz irradiada e calor in-situ”, explica ele. No entanto, os sensores de contato poderiam ser usados no lado composto das áreas de junção do laser, embora não fossem aplicáveis para o processo de junção por indução porque eles são tipicamente feitos de metal e aqueceriam por indução e distorceriam a medição.
“As áreas aquecidas de todas as juntas também são cobertas pela ferramenta de prensagem e acessórios de fixação”, observa Weidmann. “Assim, validamos a alteração da espessura do componente devido à pressão e ao calor antes e depois da união como um método de garantia de qualidade.” Esta mudança de espessura é medida por um sensor de distância integrado na ferramenta de posicionamento para o reforço do telhado (também mostrado na Fig. 3). “Quando pressionamos as peças juntas, o sensor de distância é movido”, explica ele. “Quando aplicamos calor e pressão de junção, o polímero da matriz fundida flui para as cavidades da estrutura do laser e é ligeiramente pressionado para fora da zona de junção até que a junta esfrie. Isso leva a uma mudança na espessura que é registrada pelo sensor de distância. ” Weidmann e a equipe IVW correlacionaram essa distância com a qualidade da peça. “Uma mudança de espessura - em outras palavras, uma compactação - maior que 0,1 milímetro significa que a qualidade da junta é boa”, observa Weidmann.
NDT em linha
A IVW desenvolveu outro método para garantia de qualidade - teste de termografia em linha. “Para garantir a qualidade, o objetivo principal era ver as propriedades na área de junção”, explica Popow. “Mas isso era muito difícil, então realizamos a termografia no lado do composto das juntas depois que a peça foi concluída.”
IVW escolheu uma técnica de termografia ativa chamada Termografia Lock-In porque oferece uma melhor relação sinal-ruído do que outros métodos ativos (por exemplo, termografia de fase de pulso) e também pode inspecionar para defeitos mais profundos. “A ideia básica é colocar calor no compósito, que então o conduz para a área de junção e de volta para a superfície”, diz Popow. “Com a termografia travada, o componente fica animado com uma frequência definida ao longo de vários períodos. Em seguida, analisamos essa resposta ao longo do tempo. Se você tiver áreas entre a superfície do composto e a área de junção que não são homogêneas devido a um vazio ou defeito, isso aparecerá na resposta térmica. ”
A resposta térmica é capturada como uma imagem. Os pontos que compõem essas imagens são pixels, abreviatura de elementos de imagem. Cada pixel também é um ponto de medição. Assim, o sinal de temperatura para cada pixel em toda a área de inspeção é analisado. “Como resultado, você obtém informações de amplitude e fase de cada pixel, e o software então as reconstrói em uma imagem novamente, que pode ser inspecionada visualmente”, acrescenta. Mas também forneceu grandes conjuntos de medidas para as 126 peças testadas. “Correlacionamos esses resultados de END com os resultados dos testes mecânicos realizados pela EDAG”, diz Popow. Sua equipe também testou a área de junção depois de remover os colchetes - ou seja, testes destrutivos. “Assim, correlacionamos três conjuntos de resultados de teste e agora podemos identificar áreas de ligação de baixa resistência versus alta resistência a partir da análise visual dos resultados da termografia”, diz ele.
Célula integrada para produção em massa
Uma das maiores conquistas da FlexHyJoin, diz Weidmann, é integrar todas as unidades de tecnologia, cada uma desenvolvida por um parceiro de projeto diferente, em uma linha de produção otimizada e automatizada. Voithofer, que integra o equipamento em Fill, explica que “cada conjunto de equipamento enviado para nós usava um controlador diferente. Tive que conceber um PLC mestre para controlar todas as diferentes unidades de processo. ” Isso incluiu os invólucros do laser e o robô de manuseio da célula, que foram fornecidos pela Fill. “Também era muito difícil fazer com que todas essas etapas do processo funcionassem juntas, porque elas demoravam diferentes quantidades de tempo”, acrescenta ele.
A Voithofer começou desenvolvendo uma arquitetura para cada unidade de processo e robô, considerando como posicioná-los para o melhor fluxo. “Nosso conceito era manter as três estações - estruturação, junção e NDT - modulares, em três compartimentos separados”, diz ele. “Desta forma, poderíamos extrair unidades individuais e usá-las em feiras ou outros projetos de demonstração e depois devolvê-las. Portanto, a célula de trabalho é modular, mas integrada. ”
As décadas de experiência de Fill neste tipo de integração de sistemas para produção de compósitos em série ajudaram a alcançar o que Popow vê como a maior façanha do FlexHyJoin:passar da escala de laboratório para a escala industrial. “Somos o primeiro consórcio a realizar um processo como esse, adequado para a produção em massa de compósitos unidos ao metal”, afirma. “Esse processo pode ser usado para muitas peças automotivas, como elos estabilizadores, pára-choques e portas”, observa Voithofer. “Existem muitas peças compostas que se conectam a peças de metal em um BIW leve.”
Adaptação para vários setores
No entanto, existem algumas alterações necessárias antes que a célula seja colocada em produção em série. “Não manteríamos mais a estruturação e a junção do laser em compartimentos separados, mas combiná-los em um”, diz Voithofer. “Isso eliminaria a necessidade de portas de gabinete para abrir e fechar entre esses processos, reduzindo o tempo de ciclo.” Ele também conectaria todas as estações linearmente em uma correia transportadora. A linha, portanto, funcionaria continuamente, com peças recolhidas e colocadas de volta no transportador para cada estação antes de sair da célula pronta para montagem em um BIW. Isso reduziria ainda mais o tempo do ciclo. Além disso, gavetas expandidas, capazes de alimentar centenas de peças, permitiriam que a linha passasse por turnos inteiros sem a necessidade de reabastecimento.
Embora esta célula de produção piloto tenha sido direcionada para a indústria automotiva, Popow observa que ela pode ser facilmente adaptada para aplicações aeroespaciais, esportes / bens de consumo e industriais. “Essa foi realmente uma das principais diretrizes”, diz Weidmann, “que deve ser capaz de unir diferentes geometrias e peças. A única mudança deve ser a ferramenta de compactação de união por indução, os acessórios de fixação para união a laser e as ferramentas de suporte. As partes principais da célula devem permanecer as mesmas. ” Ele observa que a IVW também demonstrou a união híbrida de titânio e aço com compósitos de folhas orgânicas de fibra de carbono / sulfeto de polifenileno (PPS) e agora está desenvolvendo demonstrações de polieteretercetona (PEEK) e polietercetonecetona (PEKK). “Isso simplesmente requer a adaptação dos processos de união para temperaturas mais altas e a redefinição dos parâmetros de processo ideais”, diz Weidmann. “A célula está aberta a uma variedade de materiais, incluindo alumínio e cobre, bem como outros sistemas de matriz de composto termoplástico, como polipropileno e polietileno.”
“Os parceiros do projeto trabalharam bem juntos e estão entusiasmados para avançar no desenvolvimento”, observa ele. “Achamos que esse tipo de produção é muito promissor e a resposta que recebemos da indústria até agora mostra que há uma variedade de empresas que também enxergam essa promessa”.
Resina
- Solvay Expande a Capacidade do Composto Termoplástico
- Síntese e Estudo das Características Óticas de Estruturas de Esfera Híbrida Ti0.91O2 / CdS
- Impedância de Superfície de Metasurfaces / Estruturas Híbridas de Grafeno
- Fraunhofer encomenda células de produção Engel automatizadas para P&D de compósitos termoplásticos
- A importância da seleção de resina
- Instituto de Estruturas e Projeto DLR aumenta a maturidade de estruturas de fuselagem de compósito termoplástico
- Kits fáceis de usar permitem o reparo interno de estruturas compostas
- Consórcio visa soluções para estruturas compostas termoplásticas de fibra de carbono
- Composto de revestimento arquitetônico revelado
- Composto + metal:tecnologia híbrida de perfil oco