Destaque do aplicativo:suportes impressos em 3D
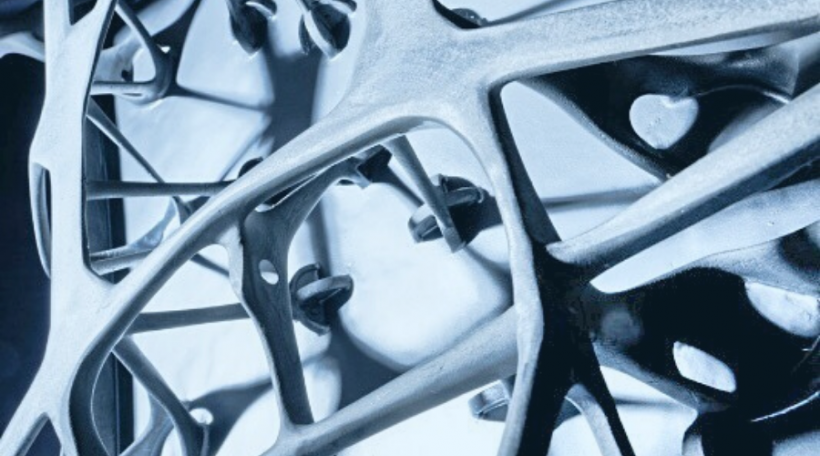
Os suportes, embora sejam partes bastante simples, são uma escolha popular para impressão 3D. Por um lado, a impressão 3D permite a otimização do suporte, ajudando a melhorar o desempenho de uma peça, bem como de uma estrutura na qual um suporte é usado.
No Application Spotlight de hoje, exploramos os principais benefícios do uso de impressão 3D para suportes, bem como mergulhamos em algumas aplicações interessantes nas indústrias aeroespacial e automotiva.
Dê uma olhada nos outros aplicativos abordados nesta série:
Impressão 3D para trocadores de calor
Impressão 3D para rolamentos
Impressão 3D para fabricação de bicicletas
Impressão 3D para Odontologia Digital e Fabricação de Alinhador Transparente
Impressão 3D para implantes médicos
Foguetes impressos em 3D e o futuro da fabricação de espaçonaves
Impressão 3D para Fabricação de Calçados
Impressão 3D para componentes eletrônicos
Impressão 3D na Indústria Ferroviária
Óculos impressos em 3D
Impressão 3D para produção de peças finais
Impressão 3D para peças de turbinas
Como a impressão 3D permite componentes hidráulicos de melhor desempenho
Como a impressão 3D apóia a inovação na indústria de energia nuclear
O que é um colchete?
Um suporte é um fixador, projetado para manter duas partes perpendiculares juntas em uma montagem e para fortalecer o ângulo.
Os suportes mantêm juntas as estruturas ao nosso redor (pense em edifícios, aviões e carros), determinando em grande parte a resistência, resiliência e integridade dessas estruturas.
Por que usar a impressão 3D para colchetes?
Os suportes são componentes bastante simples de fabricar usando métodos tradicionais. No entanto, com o advento da impressão 3D, os engenheiros podem agora explorar novas maneiras de otimizar projetos de suporte.
Isso é amplamente possível, graças à capacidade da impressão 3D de criar formas geométricas complexas que seriam impossíveis ou proibitivas em termos de custo e tempo com os meios de fabricação tradicionais.
Os principais benefícios dos suportes impressos em 3D são:
Produção mais rápida
A produção de suportes de metal complexos normalmente requer várias configurações da máquina e pode levar muitas horas para ser concluída. A impressão 3D, por outro lado, pode oferecer uma solução mais rápida. Um dos motivos é que é possível aninhar várias peças dentro de uma impressora 3D, permitindo a produção de vários suportes simultaneamente na mesma máquina. Para um suporte que foi previamente moldado por injeção, a economia de tempo é ainda maior porque a impressão 3D elimina o tempo de espera de produção de uma ferramenta de molde.
Montagem eliminada
Alguns suportes são feitos de várias peças, o que pode aumentar o tempo necessário para a montagem do suporte. A impressão 3D torna possível projetar e produzir um suporte como uma parte consolidada, exigindo menos trabalho e tempo para montar o suporte. A impressão 3D de um suporte como uma peça única também provavelmente aumentará a resistência geral de uma peça.
Em um exemplo, a Philips usou a impressão 3D para produzir um suporte redesenhado que mantém as lâmpadas no lugar na linha de produção. A peça quebrava com frequência, com uma ou duas falhas por semana, em grande parte devido à exposição repetida a altas temperaturas, combinada com uma estrutura com linhas de solda de um suporte de quatro peças.
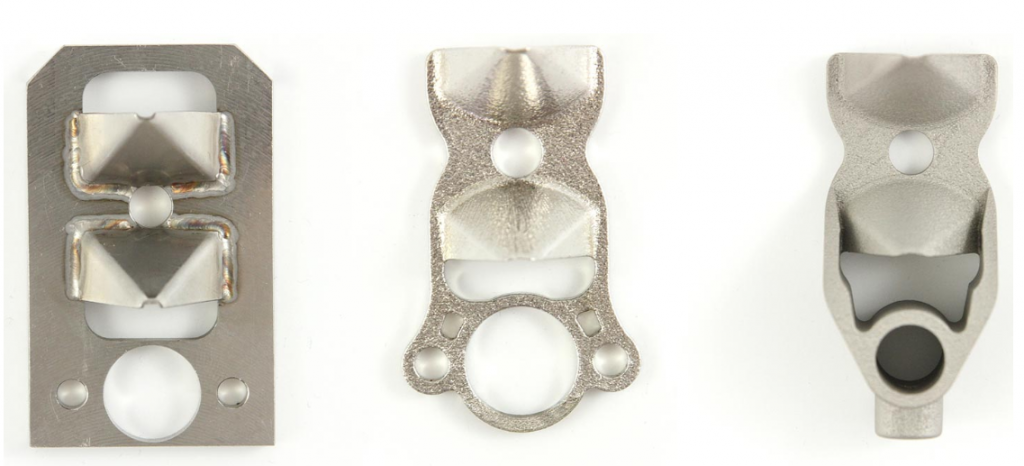
A Philips foi capaz de reprojetar uma peça de metal como um suporte de estrutura única, reduzindo a demorada montagem da peça e removendo completamente os pontos de pressão da linha de solda. Durante os primeiros três meses de uso, o suporte reinventado não se quebrou nenhuma vez.
Redução do desperdício de material
O processo de impressão 3D de um suporte como um componente geralmente usa menos material, criando assim um suporte mais leve.
Essa economia de peso se traduz em menor uso de material e, em alguns casos, pode melhorar o desempenho de um sistema onde um suporte é usado.
Pegue os motores GEnx da GE como exemplo. Os motores usavam suportes feitos com métodos tradicionais, como fresagem. Isso significa que as peças foram fresadas de um grande bloco de metal, com mais da metade acabando como resíduo.
A equipe que trabalhava nos suportes percebeu que, com a impressão 3D da peça, seria capaz de reduzir em até 90 por cento do desperdício.
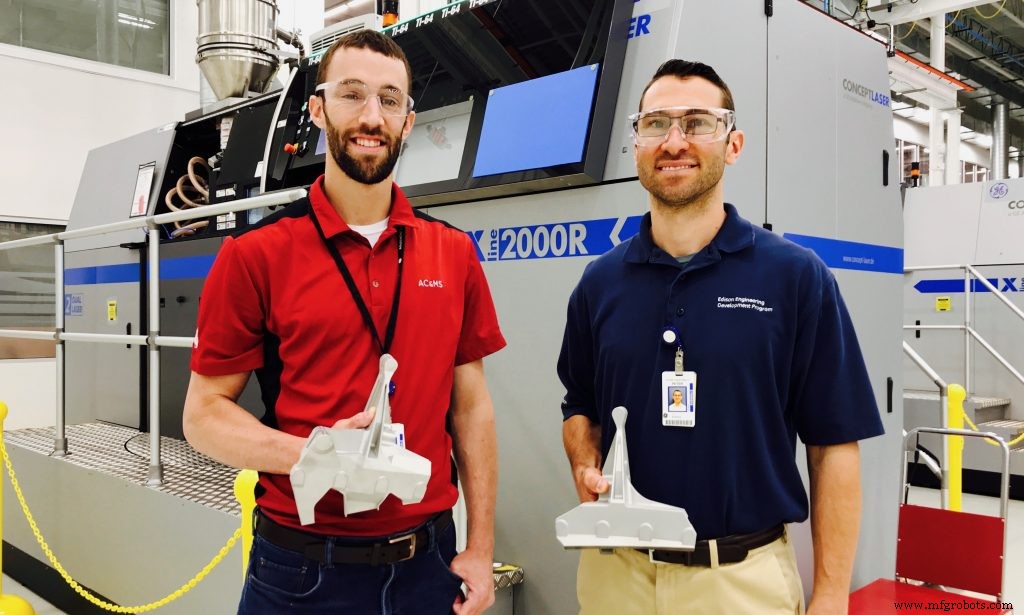
A equipe também implementou pequenas melhorias de design que reduziram o peso do suporte em 10 por cento. De acordo com a equipe, ‘quando se trata de voar, cada grama conta’. Isso significa que a redução do peso do componente pode ter um impacto na taxa de consumo de combustível do avião, reduzindo-a e, portanto, levando a uma aeronave mais eficiente.
Em outro exemplo, os engenheiros da Ford recentemente imprimiram em 3D um suporte de freio de mão elétrico de plástico para o Ford Mustang Shelby GT500 que é 60 por cento mais leve do que uma versão de aço previamente estampada.
A possibilidade de substituir metal por plástico ou compósito
Para algumas aplicações, a impressão 3D pode ser usada para produzir suportes em plástico em vez de metal. Os suportes de plástico podem ser mais adequados para aplicações como produtos de consumo com uma vida útil limitada ou produtos com componentes eletrônicos sensíveis onde os suportes de metal não funcionam.
Um exemplo vem de um fabricante de dispositivos de comunicação, Boyce Tecnologias. A empresa usou impressão 3D para construir peças de plástico para os totens do NYC Transit. Cada um desses sistemas apresenta uma tampa de acrílico verde em sua parte superior que abriga uma faixa de LED para iluminação, bem como um instrumento de antena sensível.
Para evitar a interrupção do sinal da antena, não deve haver nenhum material metálico à sua frente. Isso significa que a empresa teve que fabricar os suportes para a faixa de LED e a carcaça para a antena em plástico. A equipe de Boyce teve apenas um curto período de tempo para design, engenharia e produção, tornando a impressão 3D uma solução adequada.
Usando o sistema BigRep Studio, Boyce foi capaz de prototipar suportes de montagem curvos para as luzes LED para iluminar a tampa e, em seguida, passar direto para a fabricação dessas peças nesta mesma plataforma.
A impressão 3D desses suportes permitiu que fossem feitos de forma rápida e econômica do que a moldagem por injeção ou usinagem, ao mesmo tempo em que atendiam ao requisito de não metal acima da antena.
Mais exemplos de colchetes impressos em 3D
Aeroespacial
Suportes de titânio impressos em 3D para Boeing 787 Os suportes aeroespaciais impressos em 3D, feitos de ligas de titânio, estão se tornando mais comuns no projeto de aeronaves. Um exemplo é um suporte para uma trava de porta de acesso para o Boeing 787, instalado pela Spirit AeroSystems.
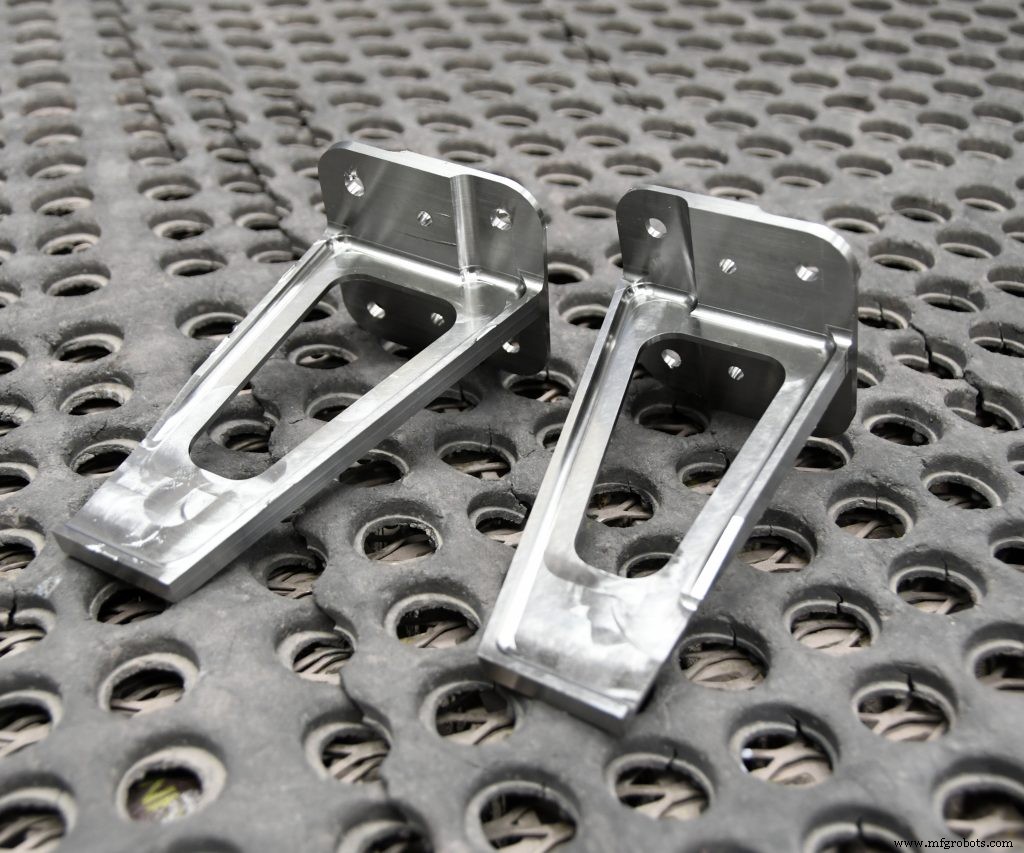
O encaixe da fechadura da porta, que antes era usinado, agora é impresso em 3D pela Norsk Titanium, usando sua tecnologia proprietária de Deposição de Plasma Rápido (RPD). O nome descreve o processo:um arco de plasma permite a deposição controlada de titânio em taxas de construção rápidas. A tecnologia é supostamente 50-100 vezes mais rápida do que os sistemas baseados em pó e usa 25-50 por cento menos titânio do que os processos de forjamento.
A principal razão para mudar para a impressão 3D de titânio é a oportunidade de diminuir a fabricação custo. O titânio é caro e, ao usinar uma peça de um bloco de titânio, muito desse material caro é desperdiçado. O segundo problema é uma grande quantidade de tempo de máquina e despesas com ferramentas de corte que vão para a usinagem do metal, elevando o custo de produção.
Ao imprimir um suporte em 3D, a Spirit pode reduzir esses custos substancialmente, ao mesmo tempo que agiliza o tempo de colocação no mercado de novas peças em pelo menos 60 por cento.
Liebherr-Aerospace 3D imprime suportes para Airbus
Em outro exemplo na indústria aeroespacial, a Liebherr-Aerospace começou a imprimir 3D os suportes do trem de pouso do nariz do Airbus A350 XWB.
Esses suportes serão os primeiros qualificados Peças de titânio impressas em 3D introduzidas no sistema Airbus.
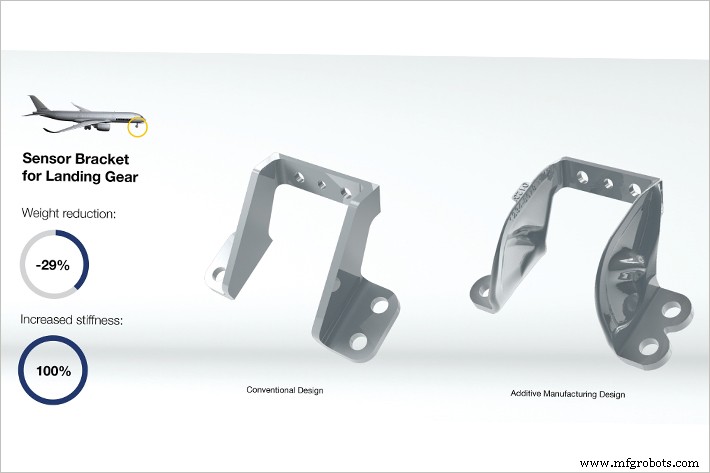
Ao contrário do Spirit AeroSystems, a Liebherr conseguiu redesenhar uma peça para obter uma redução de peso de 29 por cento. O uso de impressão 3D também ajudou a aumentar a rigidez do componente em 100 por cento.
Em 2019, a Liebherr-Aerospace atingiu um marco importante:o Escritório Federal de Aviação da Alemanha deu à empresa luz verde para produzir componentes usando AM. Desde então, a Liebherr imprime peças seriais de titânio em 3D, incluindo suportes.
Automotivo
Um suporte de teto, otimizado e impresso em 3D pela BMW
Em 2018, a BMW lançou seu icônico carro i8 Roadster, com um premiado suporte de metal impresso em 3D.
O suporte de teto, um pequeno componente que ajuda a dobrar e desdobrar a parte superior do carro, exigia um novo design para maximizar o desempenho do mecanismo de dobramento do teto. Para atingir esse objetivo, os engenheiros da BMW combinaram a impressão 3D com um software de otimização de topologia.
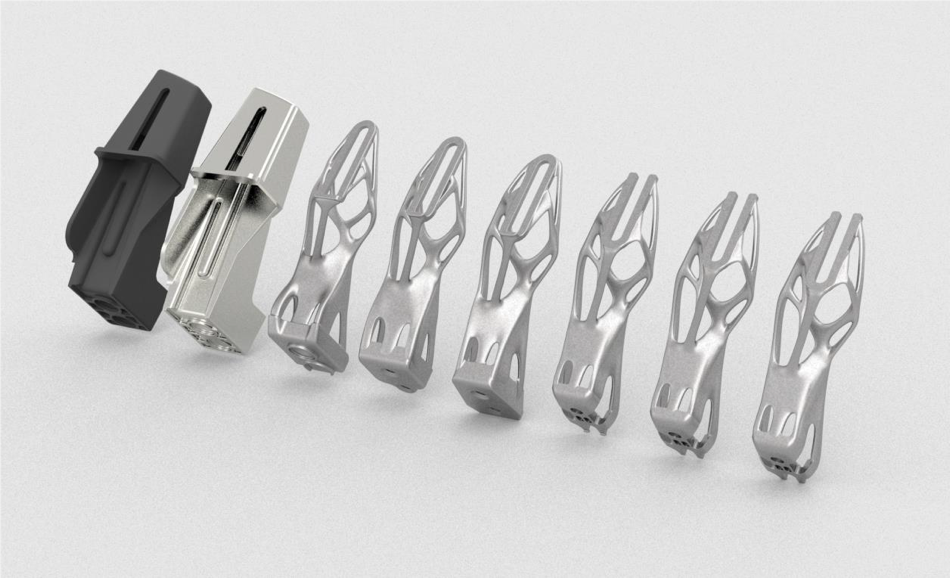
Usando o software, os engenheiros puderam inserir parâmetros como o peso, o tamanho do componente e a carga que ele irá suportar. O software então gerou um projeto que otimizou a distribuição do material da peça.
O projeto realizado pela equipe de engenharia era impossível de lançar. A equipe descobriu que a única maneira de tornar esse design possível era por meio da impressão 3D de metal.
Graças à tecnologia Selective Laser Melting (SLM), os engenheiros criaram um suporte de telhado de metal que é 10 vezes mais rígido e 44 por cento mais leve do que a alternativa convencional.
Suportes leves da Bugatti
Os veículos da Bugatti também apresentam uma série de suportes impressos em 3D. Um é um suporte de spoiler de titânio fabricado em colaboração com Fraunhofer IAPT. Diz-se que este spoiler melhora o design aerodinâmico dos veículos Bugatti.
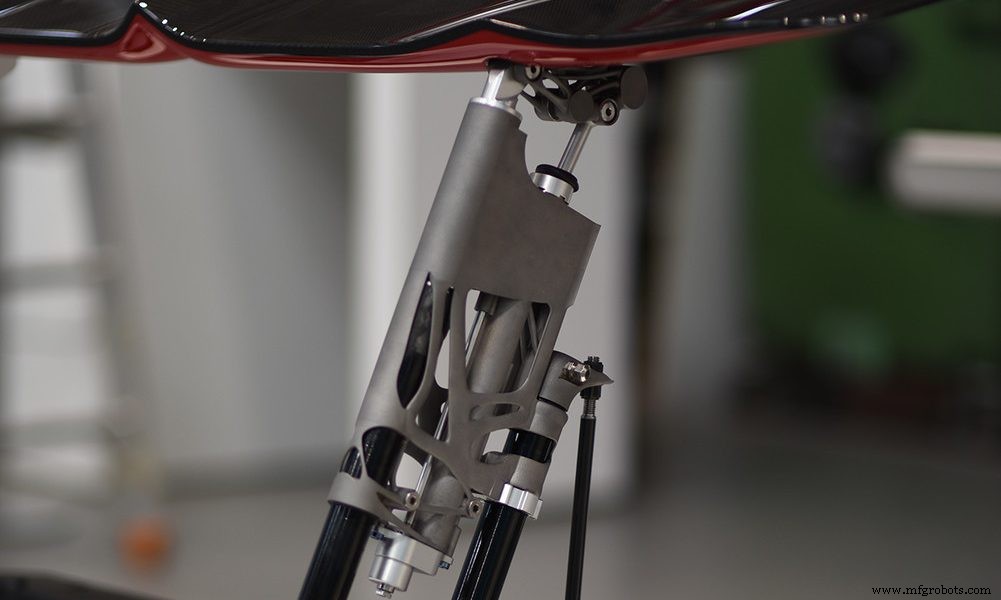
Outro parceiro no projeto da braçadeira de spoiler foi a Siemens, que ajudou a otimizar a braçadeira para produção. No final, a parte final apresentou uma resistência à tração de 1.250 MPa, uma densidade de material de mais de 99,7 por cento e uma redução de peso de 53 por cento.
A impressão 3D também foi usada para reinventar um pequeno suporte do motor com refrigeração a água integrada para o supercarro Bugatti Chiron. A peça serve como um escudo térmico ativo, reduzindo significativamente o calor transferido do motor. O componente inovador, impresso em AlSi10Mg em uma impressora SLM280 Twin 3D pela SLM Solutions, foi instalado em todos os veículos da série desde o lançamento do primeiro Bugatti Chiron.
colchetes impressos em 3D:pequenos componentes com uma grande oportunidade
Os suportes são peças pequenas e bastante comuns, que eram difíceis de otimizar no passado, quando os engenheiros eram limitados por métodos tradicionais de fabricação. Hoje, os engenheiros podem projetar suportes otimizados e dar vida a esses projetos com a ajuda da impressão 3D.
Graças à tecnologia, os suportes podem ser mais leves, porém mais rígidos e duráveis. Os exemplos acima também demonstram que, ao alavancar a impressão 3D, a vida útil do componente e o desempenho geral podem ser melhorados.
Claramente, ainda estamos longe dos colchetes impressos em 3D em massa. Dito isso, aplicações especializadas, como suportes de aeronaves e suportes produzidos em pequenos volumes, continuarão sendo um bom nicho para a tecnologia no futuro.
impressao 3D
- Soldagem e colagem de peças de plástico impressas em 3D
- Explorando a impressão 3D Polyjet
- O que é bioimpressão?
- Destaque do aplicativo:Impressão 3D para implantes médicos
- Destaque do aplicativo:Impressão 3D para Odontologia Digital e Fabricação de Alinhador Transparente
- Destaque do aplicativo:Impressão 3D para fabricação de bicicletas
- Destaque do aplicativo:Impressão 3D para rolamentos
- Destaque do aplicativo:Impressão 3D para trocadores de calor
- COVID-19 tem impulso de impressão 3-D para o centro das atenções
- Aplicação da impressão 3D na indústria automotiva