Filtro de cerâmica
Antecedentes
Durante muitos processos industriais, uma etapa de filtragem pode ser necessária para remover impurezas e melhorar a qualidade do produto final. Dependendo do processo, o filtro pode estar sujeito a altas temperaturas e ambiente corrosivo. Portanto, é necessário um material de filtro com boa temperatura e resistência química.
Os filtros de cerâmica atendem a esses requisitos e são usados em uma ampla gama de aplicações. Uma das principais aplicações é a filtração de metal fundido durante a fundição de vários componentes. Outro são os filtros de exaustão do motor diesel. O mercado mundial de filtros de metal fundido ultrapassa US $ 200 milhões por ano.
A indústria de fundição de metal é a sexta maior da América do Norte, contribuindo com mais de US $ 20 bilhões para a economia dos EUA. Cerca de 13 milhões de toneladas de peças fundidas de metal são embarcadas a cada ano, sendo 85% feitas de metais ferrosos (ferro). As peças fundidas são utilizadas em mais de 80% de todos os bens duráveis.
No processo de fundição, um metal sólido é derretido, aquecido à temperatura adequada (e às vezes tratado para modificar sua composição química) e, em seguida, é derramado em uma cavidade ou molde, que o contém na forma adequada durante a solidificação. Assim, em uma única etapa, formas simples ou complexas podem ser feitas de qualquer metal que possa ser fundido. As peças fundidas variam em tamanho de uma fração de polegada e uma fração de onça (como os dentes individuais em um zíper), a mais de 30 pés (9,14 m) e muitas toneladas (como as enormes hélices e estruturas de haste do oceano forros).
Embora haja uma série de processos de fundição diferentes, a fundição sob pressão é usada para mais de um terço de todas as fundições de metal e contribui com mais de US $ 7,3 bilhões para a economia dos EUA todos os anos. Este processo envolve a injeção de metal fundido em uma matriz de aço sob alta pressão. O metal - alumínio, zinco, magnésio e às vezes cobre - é mantido sob pressão até solidificar na forma desejada. As peças variam de peças de motor e transmissão de automóveis; a componentes complexos para computadores e dispositivos médicos; ou para grampeadores de mesa simples.
Os vários processos de fundição diferem principalmente no material do molde (seja areia, metal ou outro material) e no método de vazamento (gravidade, vácuo, baixa pressão ou alta pressão). Todos os processos compartilham a necessidade de que os materiais se solidifiquem de uma maneira que maximize as propriedades, ao mesmo tempo que evita defeitos potenciais, como espaços vazios de contração, porosidade do gás e inclusões aprisionadas.
Essas inclusões podem ser removidas colocando-se filtros de cerâmica no sistema de passagem que leva ao molde. Esses filtros devem resistir ao ataque em alta temperatura por uma variedade de metais fundidos. Esses metais podem conter elementos reativos como alumínio, titânio, háfnio e carbono. O uso desses filtros pode reduzir as taxas de refugo em 40% e aumentar os rendimentos em 10% para a fabricação de uma ampla variedade de peças feitas de ligas de ferro, aço inoxidável, superligas, alumínio ou outras ligas não ferrosas.
Filtros de metal fundido geralmente vêm em duas formas:uma estrutura tipo espuma porosa com poros interconectados que variam em direção ou seção transversal, ou uma estrutura celular porosa extrudada ou em colmeia com células de várias formas (quadradas ou triangulares) e seção transversal constante. Embora globalmente o tipo de filtro mais popular seja a espuma, os filtros celulares são usados em 75% das aplicações na América do Norte.
Os filtros podem ter células abertas ou células fechadas. Filtros de célula aberta (reticulados) consistem em uma rede de vazios interconectados cercados por uma teia de cerâmica e são amplamente usados para filtração de metal fundido. Os filtros de células fechadas (espumas) consistem em uma rede semelhante, mas os feixes são interligados por faces finas que isolam a célula individual. A porosidade aberta em uma estrutura de célula aberta é crítica em aplicações de filtro. As propriedades de um filtro dependem da geometria celular (densidade, tamanho da célula) e das propriedades do material. As vantagens incluem estabilidade em alta temperatura e baixo peso.
O tamanho dos poros desses filtros são definidos como células ou poros por polegada linear (ppi). Para filtros de favo de mel, isso varia de 64-121 ppi ou 240 ppi. Para filtros de espuma, o tamanho dos poros é muito mais difícil de medir, mas geralmente varia de 10-30 ppi.
Filtros de espuma, que foram introduzidos pela primeira vez há mais de 20 anos para fundição de não ferrosos, também são usados em unidades de vazamento direto para fundição de aço. Inclusões que variam de 0,125-2 pol (0,3175-5,1 cm). ou mais em comprimento e até 0,25 pol. (0,635 cm) de profundidade podem ser removidos. Essas inclusões vêm de materiais de moldagem, refratários de panela e reoxidação durante o processo de vazamento.
A filtração ocorre por interferência mecânica, com grandes inclusões separadas na face do filtro e inclusões menores presas dentro do filtro. Os filtros de espuma são capazes de reter inclusões significativamente menores do que suas áreas de poros abertos e também podem remover inclusões líquidas.
O comportamento do choque térmico (a resistência a mudanças repentinas de temperatura) para filtros de espuma depende do tamanho de suas células, aumentando com células maiores. A força é inicialmente retida após o choque térmico e então diminui gradualmente com o aumento da temperatura de têmpera. Uma densidade mais alta também pode melhorar a resistência ao choque térmico.
Matérias-primas
O material do filtro é geralmente um pó de óxido de metal de várias composições. Estes incluem óxido de alumínio, óxido de zircônio, espinela (uma combinação de óxidos de magnésio e alumínio), mulita (uma combinação de óxidos de alumínio e silício), carboneto de silício e suas combinações. Fibras cerâmicas de várias composições também podem ser adicionadas para melhorar certas propriedades. Outros aditivos incluem ligantes (hidrato de alumina, silicato de sódio), agentes antiespumantes (silicone ou álcool) e outros produtos químicos para melhorar as propriedades da pasta. A água geralmente é usada para fazer a pasta cerâmica.
Design
Para obter o desempenho ideal do filtro, um filtro deve ser projetado com a composição, tamanho de poro e propriedades adequadas que correspondem à aplicação específica. O tamanho e a forma devem ser ajustados para se ajustar ao sistema de molde da peça a ser fundida. Deve ser permitida uma área de porta suficiente para que o filtro não obstrua o sistema de portas durante a filtração. A área do filtro deve ser de três a cinco vezes a área total de obstrução que o filtro está alimentando.
Os principais critérios de desempenho ao projetar um filtro são taxa de fluxo, eficiência de filtragem, resistência a quente / frio, resistência à escória, resistência ao choque térmico, nível de qualidade e custo. Cada projeto é melhor em alguns do que em outros, com compensações de projeto significativas necessárias em muitos casos.
O processo de fabricação
Existem vários métodos usados para fazer filtros de cerâmica. O método da esponja polimérica, que será descrito com mais detalhes aqui, produz estruturas de células abertas impregnando uma esponja polimérica com uma pasta de cerâmica, que é então queimada para deixar uma cerâmica porosa. O método de formação de espuma direta pode produzir estruturas de células abertas e fechadas, sendo a estrutura de espuma mais comum. Neste método, uma mistura química contendo o componente cerâmico desejado e materiais orgânicos é tratada para desenvolver um gás. As bolhas são então produzidas no material, fazendo-o espumar. O material cerâmico poroso resultante é então seco e queimado. Para o favo de mel ou estrutura celular, um método de formação de plástico chamado extrusão é usado, onde uma mistura de pó cerâmico mais aditivos é forçada através de uma matriz moldada (como massa de brinquedo). A estrutura celular
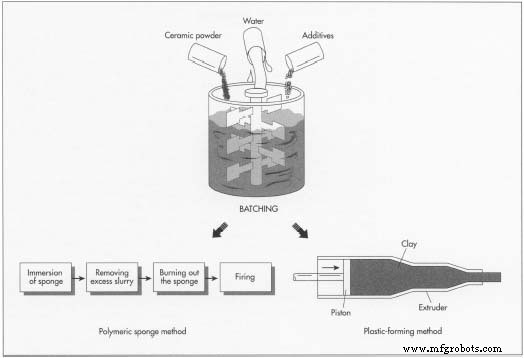
Selecionando a esponja
- 1 Primeiro, uma esponja polimérica deve ser selecionada com propriedades adequadas. O tamanho dos poros da esponja determina o tamanho dos poros da cerâmica final após a queima. Também deve ser capaz de recuperar sua forma original e se converter em um gás a uma temperatura inferior à necessária para queimar a cerâmica. Os polímeros que podem satisfazer esses requisitos incluem poliuretano, celulose, cloreto de polivinila, poliestireno e látex. As esponjas poliméricas típicas variam em tamanho de 3,94-39,4 pol. (10-100 cm) de largura e 0,394-3,94 pol. (1-10 cm) de espessura.
Preparando a pasta
- 2 Após a seleção da esponja, a pasta é feita misturando o pó cerâmico e os aditivos em água. O pó cerâmico geralmente consiste em partículas com menos de 45 mícrons de tamanho. A quantidade de água pode variar de 10-40% do peso total da pasta.
Mergulhando a esponja
- 3 Antes da imersão, a esponja geralmente é comprimida para remover o ar, às vezes usando um êmbolo mecânico várias vezes. Depois de imersa na pasta, a esponja pode se expandir e a pasta preenche as células abertas. A etapa de compressão / expansão pode ser repetida para atingir a densidade desejada.
Removendo o excesso de pasta
- 4 Após a infiltração, entre 25-75% da pasta deve ser removida da esponja. Isso é feito comprimindo a esponja entre placas de madeira, centrifugando ou passando por rolos predefinidos. O espaço entre os rolos determina a quantidade removida. Às vezes, a espuma impregnada passa por outra etapa de modelagem, pois ainda é flexível.
Secagem
- 5 A esponja infiltrada é então seca usando um dos vários métodos - secagem ao ar, secagem em forno ou aquecimento por micro-ondas. A secagem ao ar leva de oito a 24 horas. A secagem no forno ocorre entre 212-1.292 ° F (100-700 ° C) e é concluída em 15 minutos a seis horas.
Queimando a esponja
- 6 Outra etapa de aquecimento é necessária para retirar os orgânicos da pasta e queimar a esponja. Isso ocorre no ar ou em uma atmosfera inerte entre 662-1.472 ° F (350-800 ° C) por 15 minutos a seis horas a uma taxa de aquecimento lenta e controlada para evitar o sopro da estrutura cerâmica. A temperatura depende da temperatura na qual o material esponjoso se decompõe.
Queimando a cerâmica
- 7 A estrutura cerâmica deve ser aquecida a temperaturas entre 1.832-3.092 ° F (1.000-1.700 ° C) para densificar o material em uma taxa controlada para evitar danos. O ciclo de queima depende da composição específica da cerâmica e das propriedades finais desejadas. Por exemplo, um material de óxido de alumínio pode exigir queima a 2.462 ° F (1.350 ° C) por cinco horas.
Controle de qualidade
As matérias-primas geralmente devem atender aos requisitos de composição, pureza, tamanho de partícula e outras propriedades. As propriedades monitoradas e controladas durante a fabricação são geralmente dimensionais e, em seguida, específicas do projeto. Para filtros de espuma, o peso do filtro deve ser medido para determinar a eficiência do revestimento. Filtros extrudados são medidos quanto à densidade. Ambos os parâmetros estão relacionados às propriedades de resistência.
Subprodutos / resíduos
O processo de fabricação é cuidadosamente controlado para minimizar o desperdício. Em geral, o excesso de pasta não pode ser reciclado, pois pode alterar a pureza e as cargas sólidas da pasta original, afetando assim as propriedades finais.
O Futuro
O mercado de fundição de metal deverá cair 2,7% em 1999, principalmente devido ao enfraquecimento da economia global, com embarques totais estimados em 14,5 milhões de toneladas. As vendas aumentarão ligeiramente para US $ 28,8 bilhões. Embora os embarques de fundidos continuem diminuindo ligeiramente em 2000 e 2001, no longo prazo, os embarques devem chegar a quase 18 milhões de toneladas em 2008, com vendas de US $ 45 bilhões. Os embarques e as vendas terão taxas de crescimento em 10 anos de 1,7% e 4,75%, respectivamente.
O aumento do uso de componentes de metal mais leves, como peças fundidas de alumínio, impulsionou o crescimento no setor automotivo. Hoje, há uma média de 150 lb (68,1 kg) de peças fundidas de alumínio por veículo, uma quantidade projetada para crescer para 200 lb (90,8 kg) por ano até o ano 2000.
Os filtros cerâmicos continuarão a desempenhar um papel importante na produção de peças fundidas de qualidade e acompanharão o crescimento do mercado de fundição. O volume em dólares pode diminuir devido às contínuas reduções de preços. As exigências de qualidade e produtividade para fundições de metal estão aumentando a necessidade de filtros, uma vez que fornecem uma maneira rápida e confiável de obter boas fundições. Assim, os compradores de elenco estão especificando "filtrado" com cada vez mais frequência.
Processo de manufatura
- Filtros passa-baixo
- Schaffner apresenta uma nova série de filtros RFI
- O problema com filtros de combustível de pré-enchimento
- Usando Cerâmica em Sistemas de Exaustão para Purificar Emissões
- 16 técnicas de ferraria
- Cisalhamento de metal
- O que é uma Fundição?
- Considerações para selecionar um filtro de ar comprimido
- A importância da filtragem em sopradores industriais e de aeração
- A hora certa para trocar seus filtros hidráulicos