Produção automatizada de aerocompósitos:Moldagem líquida ou termoplástico soldado?
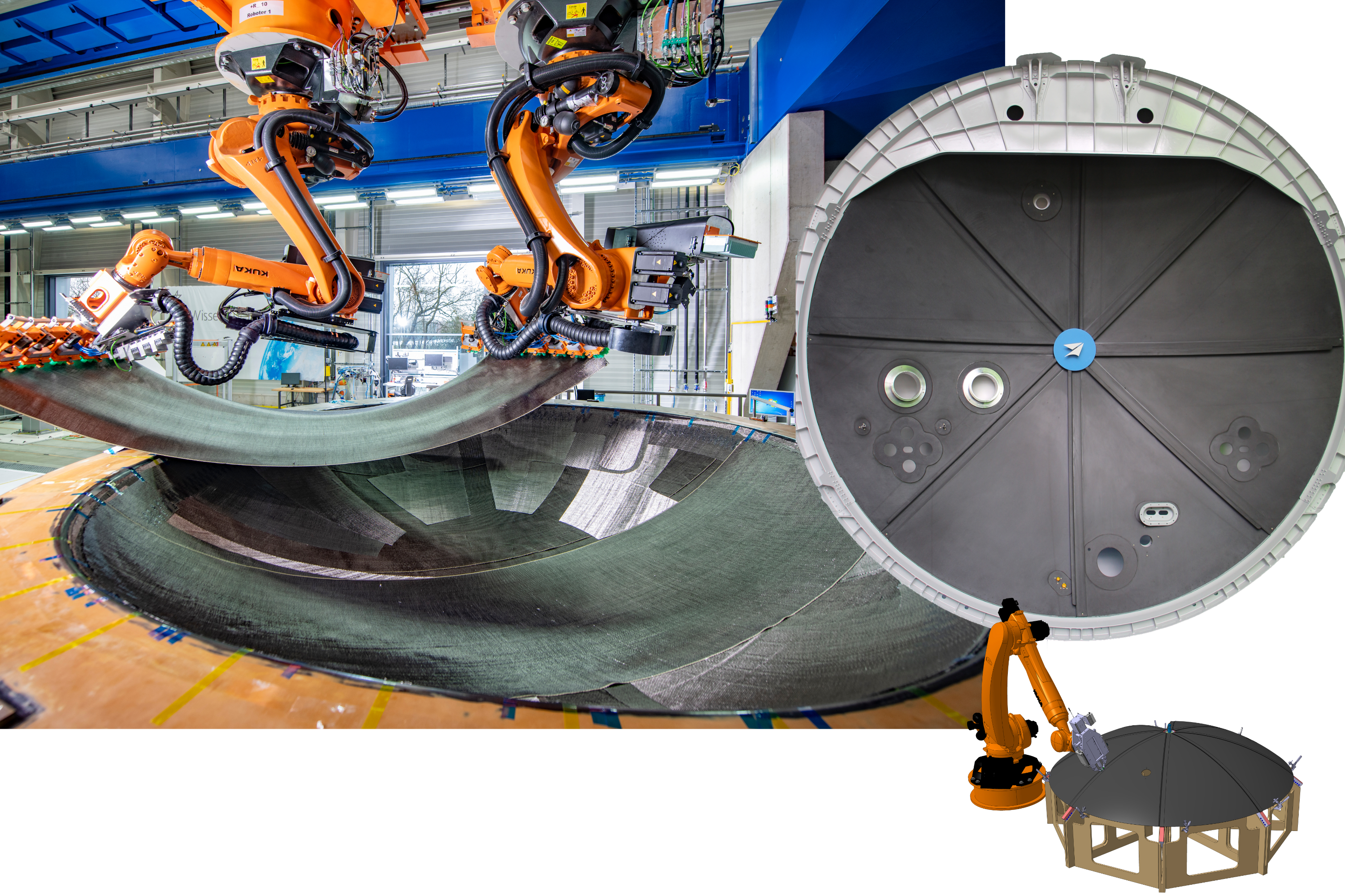
Conforme os OEMs e fornecedores exploram os materiais e processos que permitirão a próxima geração de aeronaves, duas abordagens diferentes estão sendo demonstradas. A primeira é a moldagem líquida de pré-formas de fibra seca vista, por exemplo, na linha de moldagem por transferência de resina de alta taxa (RTM) da Spirit AeroSystem (Prestwick, Escócia) para spoilers Airbus A320 e também no programa Wing of Tomorrow (WOT) conduzido pela Airbus que usa a colocação automatizada de tecidos não frisados (NCF) e infusão de resina líquida, seguida por cura fora da autoclave (OOA) em um forno (consulte "A linha RTM aeroespacial automatizada de alta taxa oferece spoilers de última geração" e "Atualização:asa inferior skin, Wing of Tomorrow ”respectivamente.)
O segundo são os compósitos termoplásticos (TPC) apresentados, por exemplo, no Demonstrador de Fuselagem Multifuncional Clean Sky 2 (MFFD), onde películas endurecidas são criadas usando a colocação automática de fibra - consolidada in-situ para a metade superior e autoclave consolidada para a inferior meio - seguido de montagem por soldagem. Esses programas usam automação para aumentar a taxa de produção e a qualidade, reduzindo custos. Mas como eles se comparam?
O Instituto de Estruturas e Design do Centro Aeroespacial Alemão (DLR) opera o Centro de Tecnologia de Produção Leve (ZLP) em Augsburg. Entre seus muitos projetos de fabricação de compósitos, PROTEC NSR e Fast Lane RPB apresentam uma oportunidade única de comparar, respectivamente, uma antepara de pressão traseira termofixa moldada por líquido (RPB) para o Airbus A350 de corredor duplo com um RPB termoplástico para o Airbus de corredor único A320. Ambos os projetos trabalharam com o fornecedor Tier 1 dessas estruturas, Premium Aerotec Group (PAG, Augsburg, Alemanha), e demonstraram automação ao avaliar o tempo de ciclo e custo.
Anteparo TS moldado por líquido
“Começamos há muitos anos com a PAG no projeto AZIMUT para analisar processos manuais para a fabricação de compósitos”, disse o Dr. Lars Larsen, chefe de tecnologias de montagem e união da ZLP Augsburg. “Nossa primeira solução de automação foi para layup, e então trabalhamos para automatizar mais operações.” O principal objetivo do PROTEC NSR era pegar essas soluções especializadas para a produção de RPB e colocá-las em um único processo automatizado, explica o Dr. Marcin Malecha, gerente de projeto do PROTEC NSR na DLR.
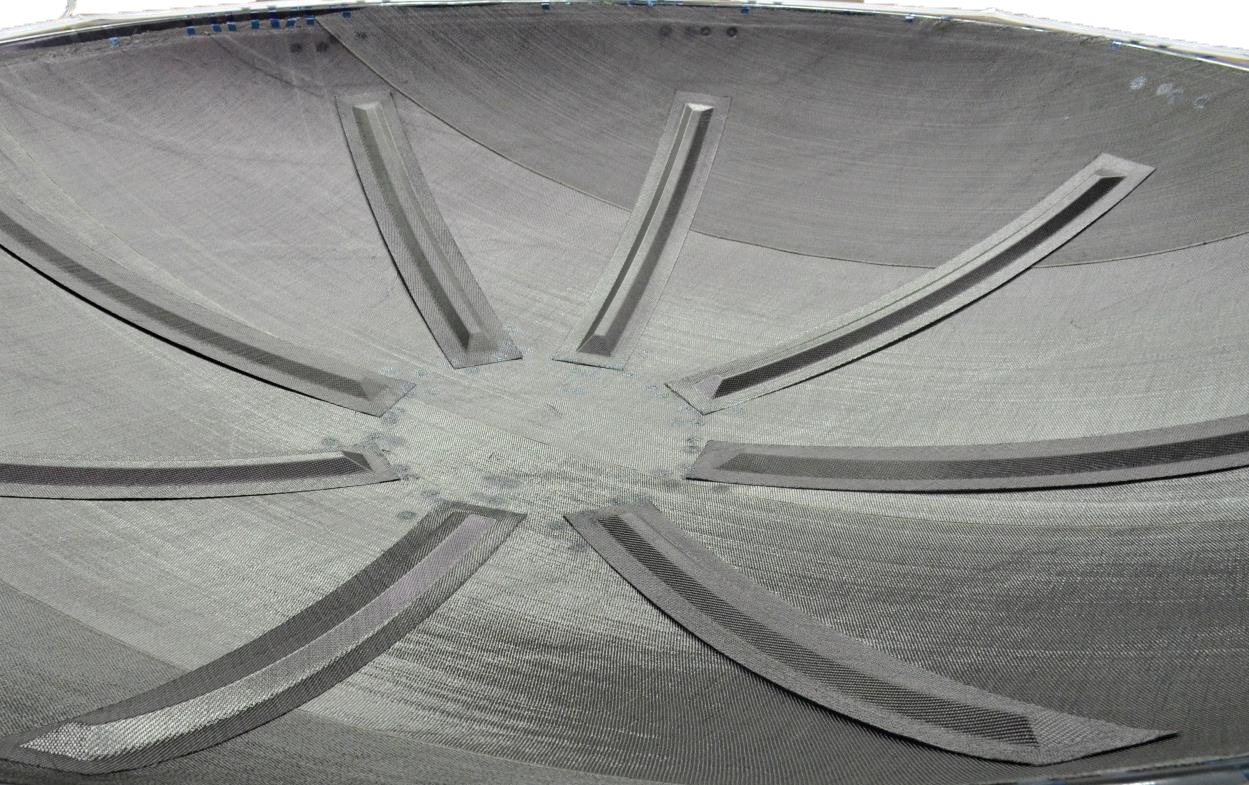
Pré-forma e garras. As etapas do processo para criar a pré-forma seca ensacada a vácuo são mostradas na Fig. 1 abaixo. Este foi infundido com resina epóxi RTM6 usando o processo assistido por vácuo patenteado da Airbus (VAP), que emprega uma membrana semipermeável para reduzir a porosidade. O layup da pré-forma compreendeu dois conjuntos de 16 camadas de até 5 metros de comprimento usando a largura total de 1,27 metros do tecido de fibra de carbono acetinado com 5 arnês. Embutidos entre esses dois conjuntos estavam 25 peças de reforço em forma complexa, com tamanhos de até 1,5 por 2,5 metros. Oito longarinas foram colocadas no topo.
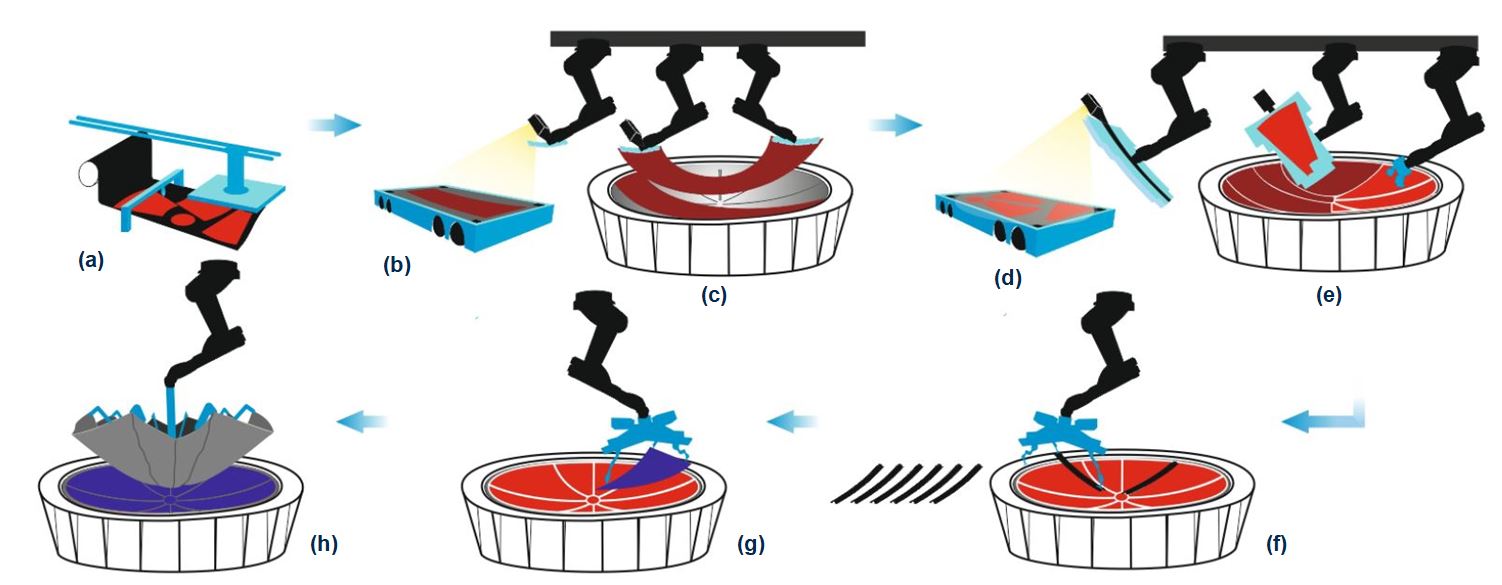
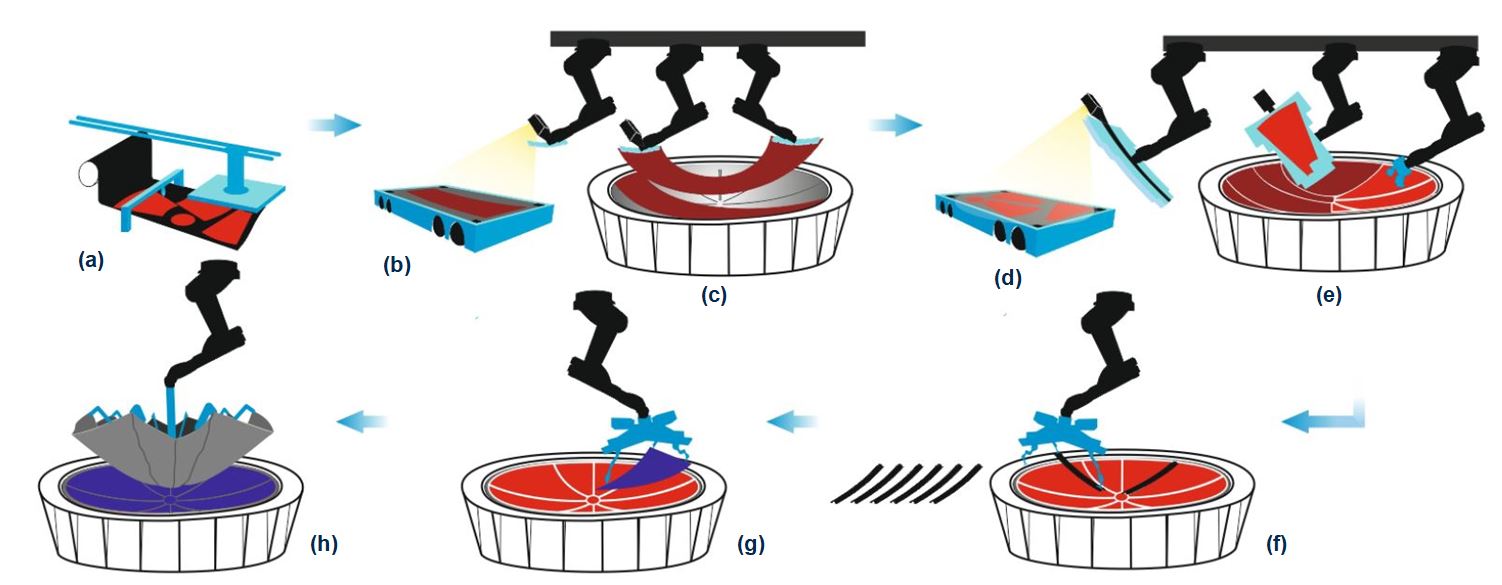
“Desenvolver ferramentas e garras que pudessem atingir a precisão necessária no drapeamento e manuseio foi um dos maiores desafios”, observa Larsen. Isso se deveu em parte à complexa mistura de camadas que exigiam três mecanismos de drapeamento diferentes:
- Aplicação de material de largura total diretamente do rolo que deve se adaptar ao formato do molde.
- Drapeamento de camadas estruturais de corte largo onde dois robôs colaboram, um por borda do tecido, para pegar e criar a geometria alvo do molde para garantir a conformidade sem rugas antes da colocação.
- Acomodação para camadas pequenas e moldadas de até 1,5 por 2,5 metros .
“Para os robôs cooperantes, desenvolvemos efetores finais que contêm seis módulos conectados por juntas esféricas”, explica Larsen. “Isso permite que o efetuador se deforme, de maneira semelhante a uma cobra, de acordo com a geometria alvo do molde. Dispositivos de aquecimento integrados ativam o aglutinante no tecido conforme ele é transportado e moldado, mantendo sua forma e posição 3D depois de colocado. ”
Drapeamento e colocação automatizados
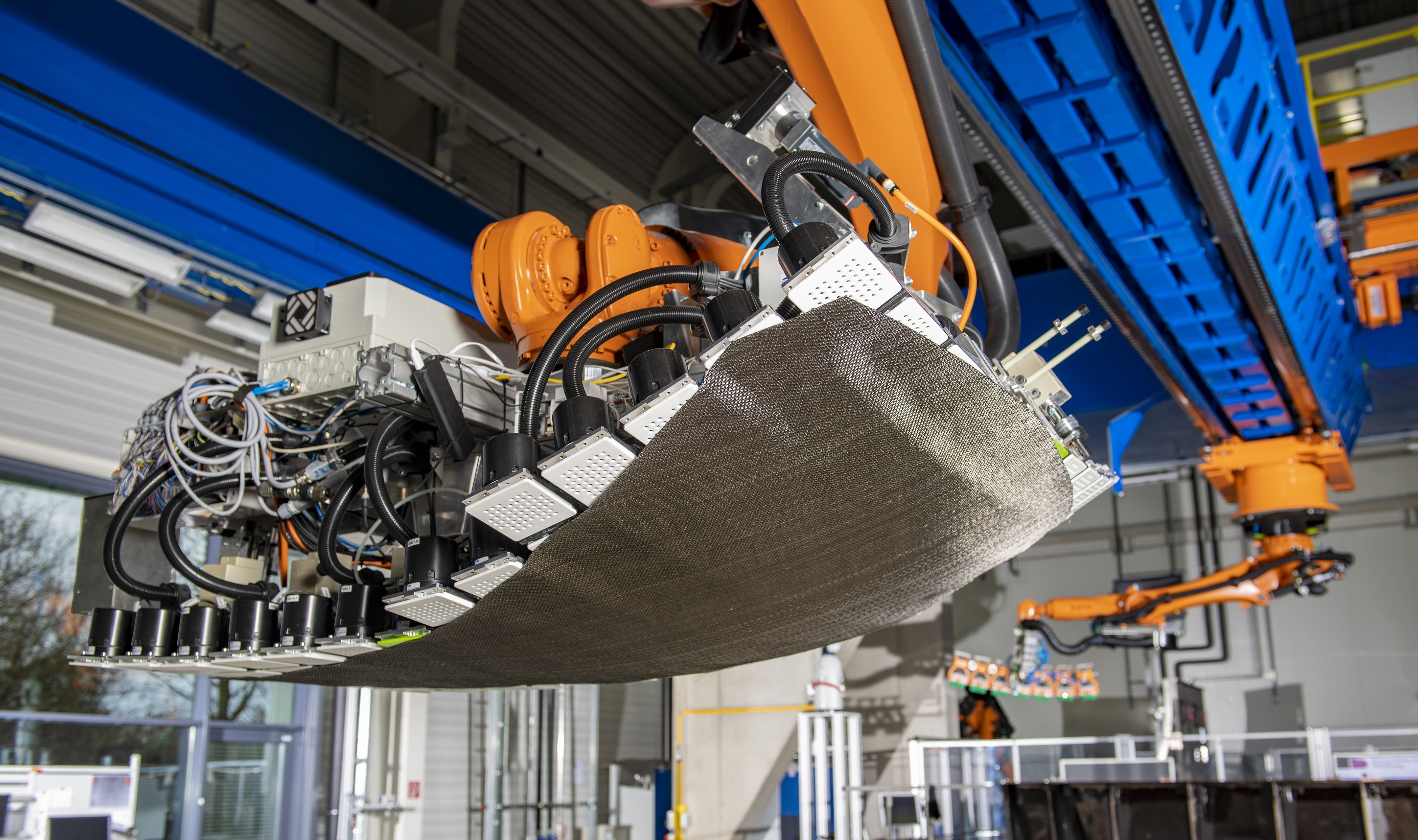
O efetor final apresenta uma pinça que utiliza 127 módulos equipados com sucção a vácuo para pegar as camadas de tecido cortadas, transformá-las em uma forma 3D e, em seguida, aquecê-las antes de colocá-las no molde. Crédito da foto:Instituto de Estruturas e Design do Centro Aeroespacial Alemão (DLR)
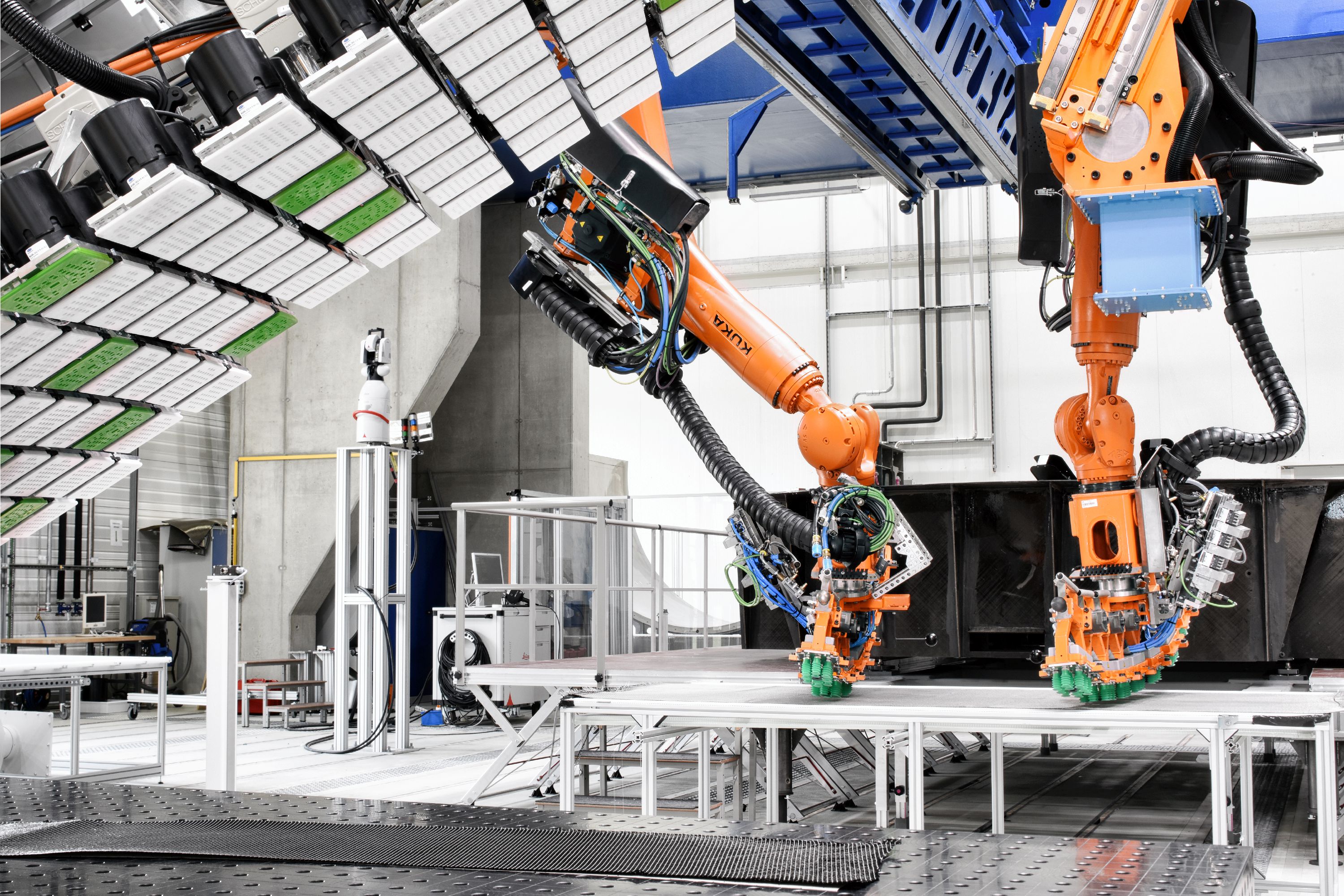
Aqui, tanto a garra de 127 módulos (esquerda) quanto os robôs colaboradores (plano de fundo) podem ser vistos. Crédito da foto:Instituto de Estruturas e Design do Centro Aeroespacial Alemão (DLR)
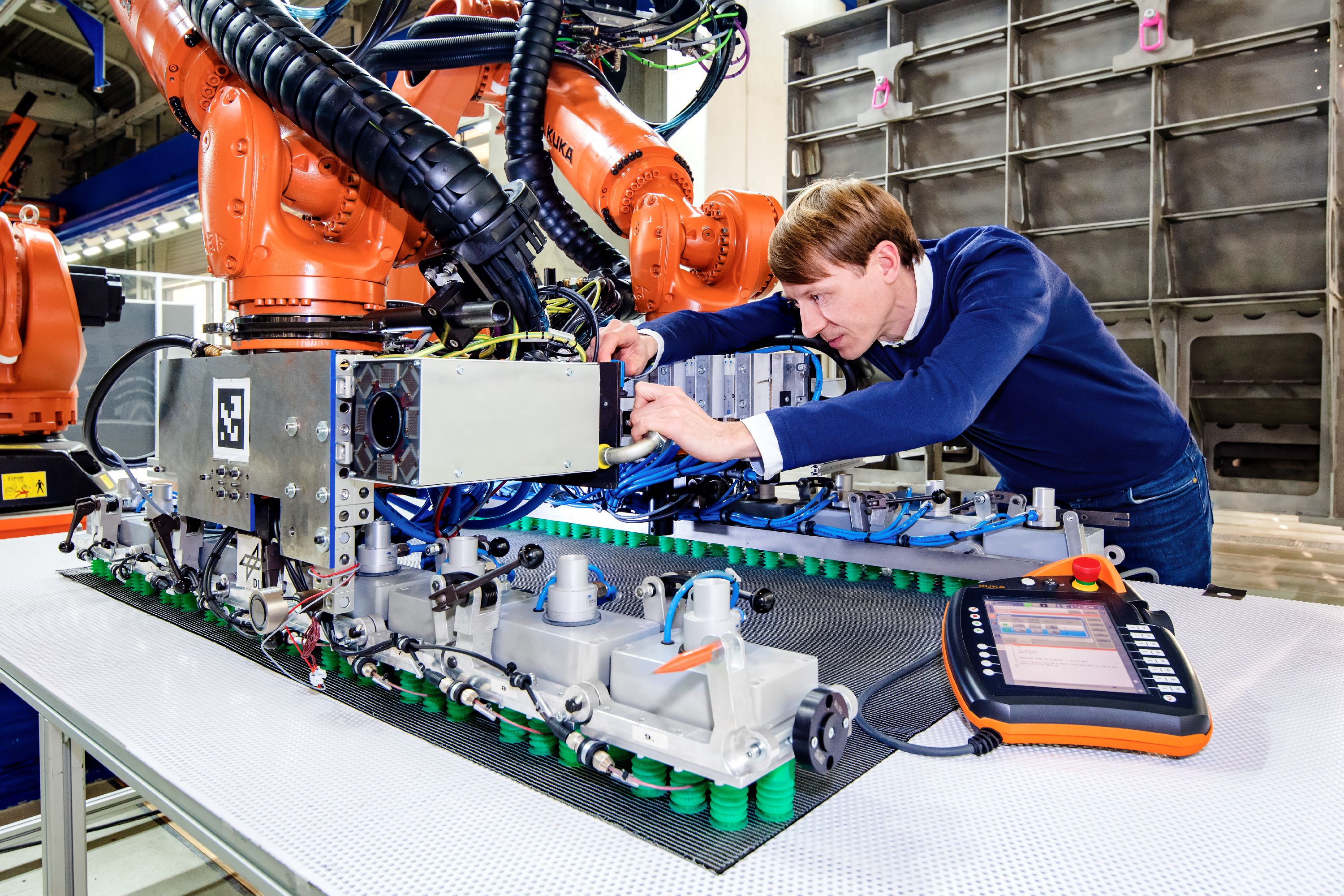
Para os robôs colaboradores, foram desenvolvidos efetores finais que contêm seis módulos conectados por juntas esféricas. Crédito da foto:Instituto de Estruturas e Design do Centro Aeroespacial Alemão (DLR)

Cada robô pega uma borda da grande camada de tecido. Eles então trabalham juntos enquanto transportam a camada para criar a geometria alvo necessária antes de colocar o tecido no molde. Crédito da foto:Instituto de Estruturas e Design do Centro Aeroespacial Alemão (DLR)
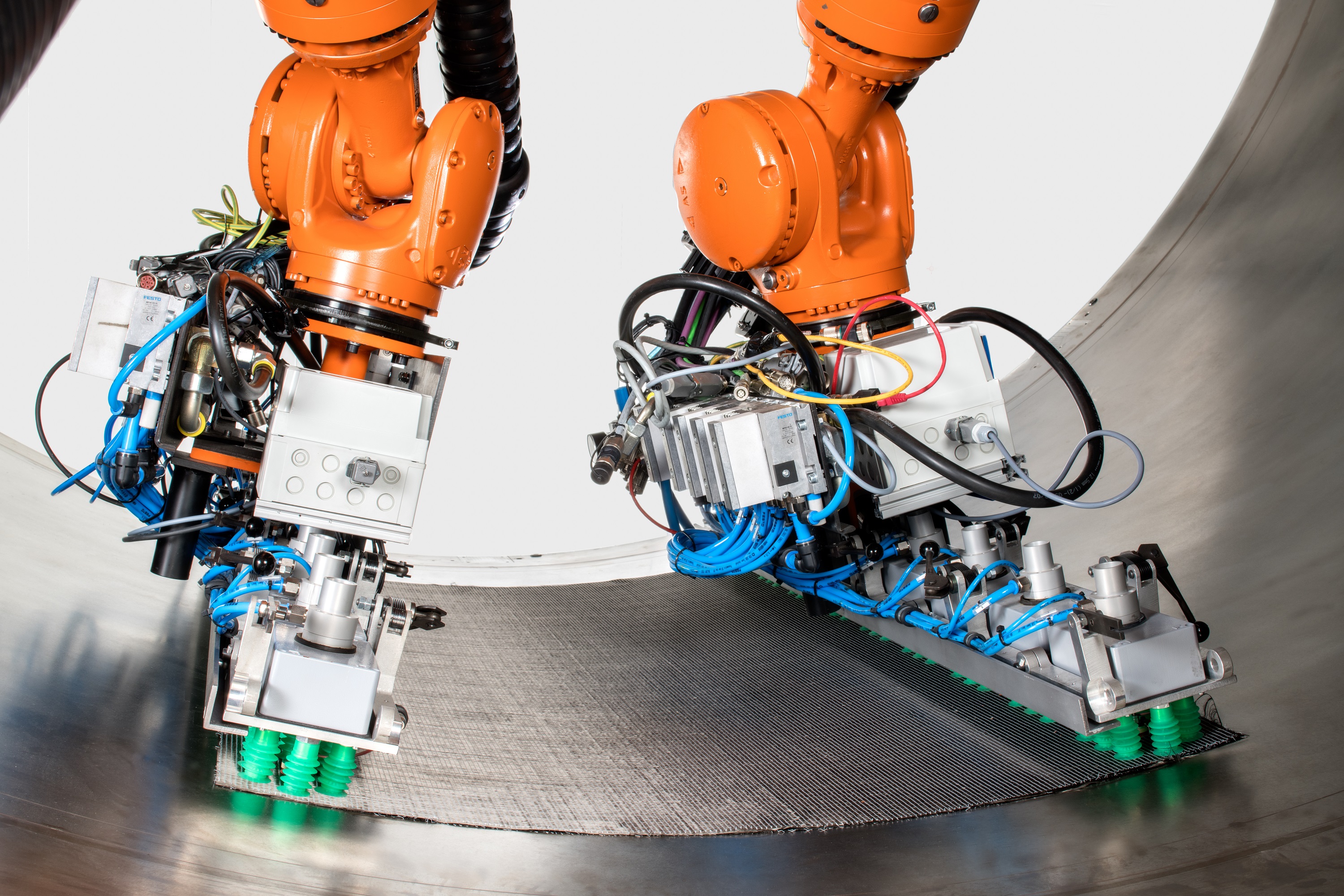
Crédito da foto:Instituto de Estruturas e Design do Centro Aeroespacial Alemão (DLR)
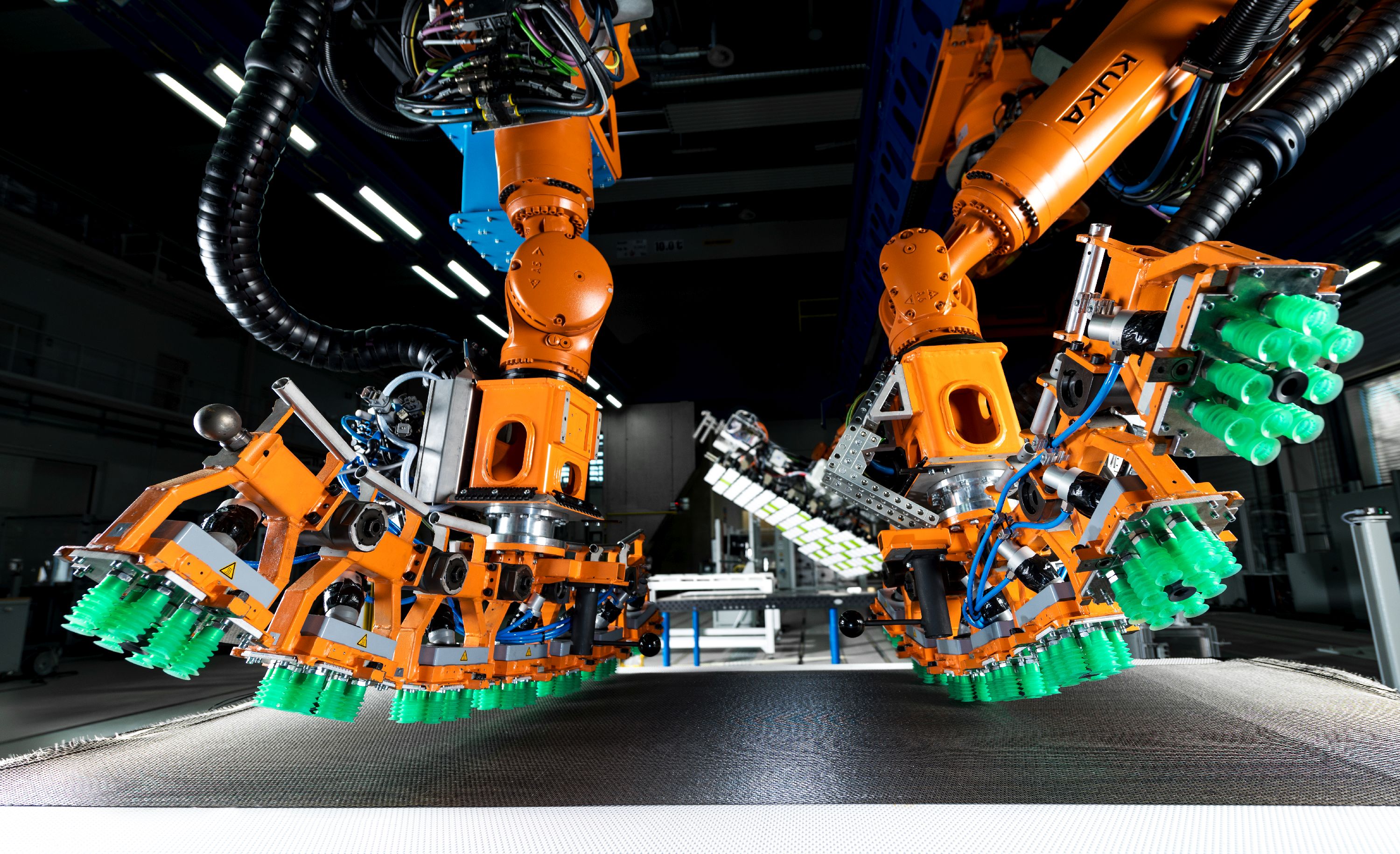
Close-up dos efetores finais do robô colaborativo. Crédito da foto:Instituto de Estruturas e Design do Centro Aeroespacial Alemão (DLR)
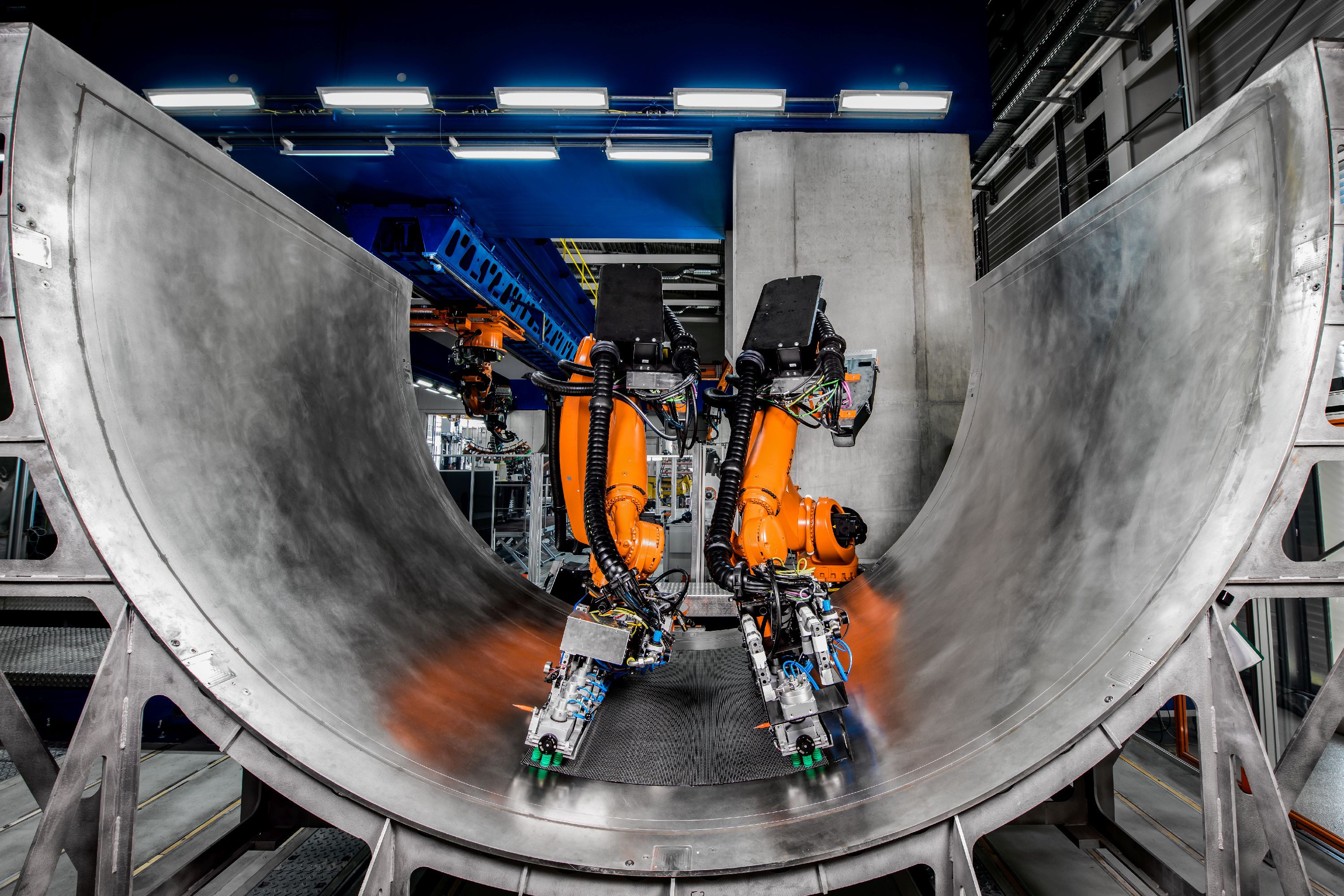
Este sistema que a DLR desenvolveu inicialmente para uma antepara de pressão traseira A320 agora também foi demonstrado para um painel da fuselagem e foi projetado para ser flexível para uma variedade de grandes estruturas aerodinâmicas, com base em seus arquivos de design digital, sem ensinar novamente os robôs. Crédito da foto:Instituto de Estruturas e Design do Centro Aeroespacial Alemão (DLR)
Anterior Próximo
Para as camadas pequenas e moldadas até 1,5 por 2,5 metros, foi desenvolvido um segundo tipo de garra que utiliza 127 módulos equipados com sucção a vácuo para coleta. “Esta garra pega o material em um estado 2D e, em seguida, dobra-o na geometria alvo”, explica Malecha. “Ele deve decidir qual dos 127 módulos vai segurar firme e qual vai deixar deslizar para transformar a folha 2D em uma forma 3D. Portanto, é muito semelhante a como as mãos trabalham para armar. Fizemos muitos experimentos e ganhamos experiência sobre onde segurar e onde liberar. A força pode ser ajustada pela intensidade da aderência dos módulos no material ”.
Inspeção em linha. Sensores ópticos nas garras modulares monitoraram o processo de drapeamento. Depois de colocar uma camada, um efetor final combinando um Leica T-Scan (Hexagon Manufacturing, Cobham, Reino Unido) e um sistema de medição de ângulo de fibra baseado em câmera da Profactor (Steyr, Áustria) inspeciona a qualidade. “Primeiro medimos os ângulos das fibras e comparamos com o arquivo CAD”, diz Malecha, “e então medimos as bordas de cada peça e verificamos sua posição em relação ao arquivo CAD”.
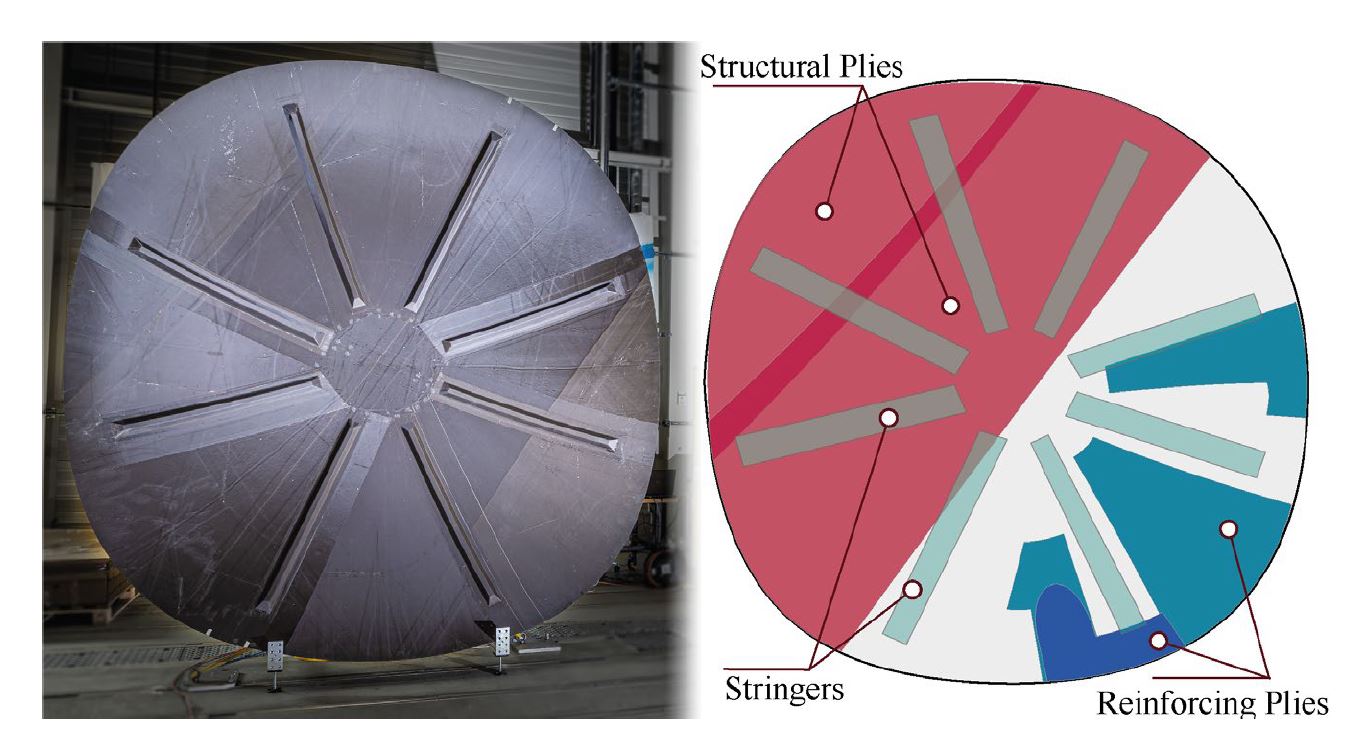
Fibras e ensacamento a vácuo. Depois de completar a pré-forma, oito reforçadores (longarinas) foram fixados na parte superior. Para esta tarefa, a Multi Kinematic Gripper foi desenvolvida e também foi utilizada para aplicar os materiais auxiliares da bolsa a vácuo. Esta garra é composta por três robôs pequenos e independentes de 6 graus de liberdade (DOF) e um braço rígido, todos montados no flange central de um robô industrial de 6 graus de liberdade. Os materiais auxiliares do ensacamento a vácuo - peel ply, filme de liberação perfurado e meio de fluxo de resina (materiais auxiliares do lado da ferramenta) - foram pré-cortados e pré-unidos, projetados para onde foram colocados. “Eles não precisavam ser drapeados, apenas colocados”, observa Malecha. A membrana pré-fabricada semipermeável foi aplicada de forma semiautomática por meio de um efetor final com um mecanismo "semelhante a um guarda-chuva", enquanto a colocação da fita adesiva e do saco de vácuo externo permanecia manual, mas também podia ser automatizado.
Tempo e custo do ciclo. Para a Malecha, o maior desafio era construir o sistema modular de execução de manufatura (MES) baseado em inteligência artificial (IA) para monitorar e controlar a cadeia de processo. “Tivemos que construir sistemas de gerenciamento de dados que pudessem reunir processos bastante diferentes e, em seguida, comandá-los por meio do MES por meio de uma porta de troca de dados”, explica ele. “Podemos usá-los à medida que são necessários em tempo real, permitindo mais flexibilidade e uso mais amplo em comparação com o cumprimento de um pedido de fabricação estrito.”
A tecnologia PROTEC NSR foi validada pela fabricação de um demonstrador em tamanho real em janeiro de 2019 e alcançando um nível de maturidade de TRL 5-6 em meados de 2019. Em comparação com o estado da arte atual da PAG, esta cadeia de processo automatizada reduz o tempo de ciclo da aplicação de tecido laminado em 58% e a coleta e colocação das camadas cortadas em 50%. Os custos de fabricação dessas operações foram reduzidos em 11,5% e 31%, respectivamente.
RPB termoplástico
“Este projeto começou em 2018 com PAG e Institut für Verbundwerkstoffe (IVW, Kaiserslautern, Alemanha) para mostrar o que é possível com compósitos termoplásticos em grandes peças e estruturas primárias,” explica o Dr. Stefan Jarka, gerente de projeto da Fast Lane RPB e especialista em tecnologias de soldagem na ZLP Augsburg. “Um RPB não é realmente primário, porque os requisitos mecânicos não são tão altos quanto uma asa ou fuselagem, mas mostra o que é possível para estruturas grandes, planas e ligeiramente curvas. Em apenas quatro meses, desenvolvemos um demonstrador A320 RPB como um exemplo de como converter uma estrutura de alumínio existente em compósitos termoplásticos. ”
Este demonstrador usou tecido de fibra de carbono Cetex (CF) / sulfeto de polifenileno (PPS) organosheet (Toray Advanced Composites, Nijverdal, Holanda) e soldagem por resistência. Um elemento resistivo entre as duas superfícies a serem soldadas gera calor e permanece na estrutura soldada. GKN Fokker (Hoogeveen, Holanda) tem usado essa técnica por décadas para produzir portas de trens de pouso para aeronaves e bordas de ataque fixas. Para este A320 RPB, a equipe ZLP usou um elemento resistivo CF em vez da malha de aço inoxidável convencional.
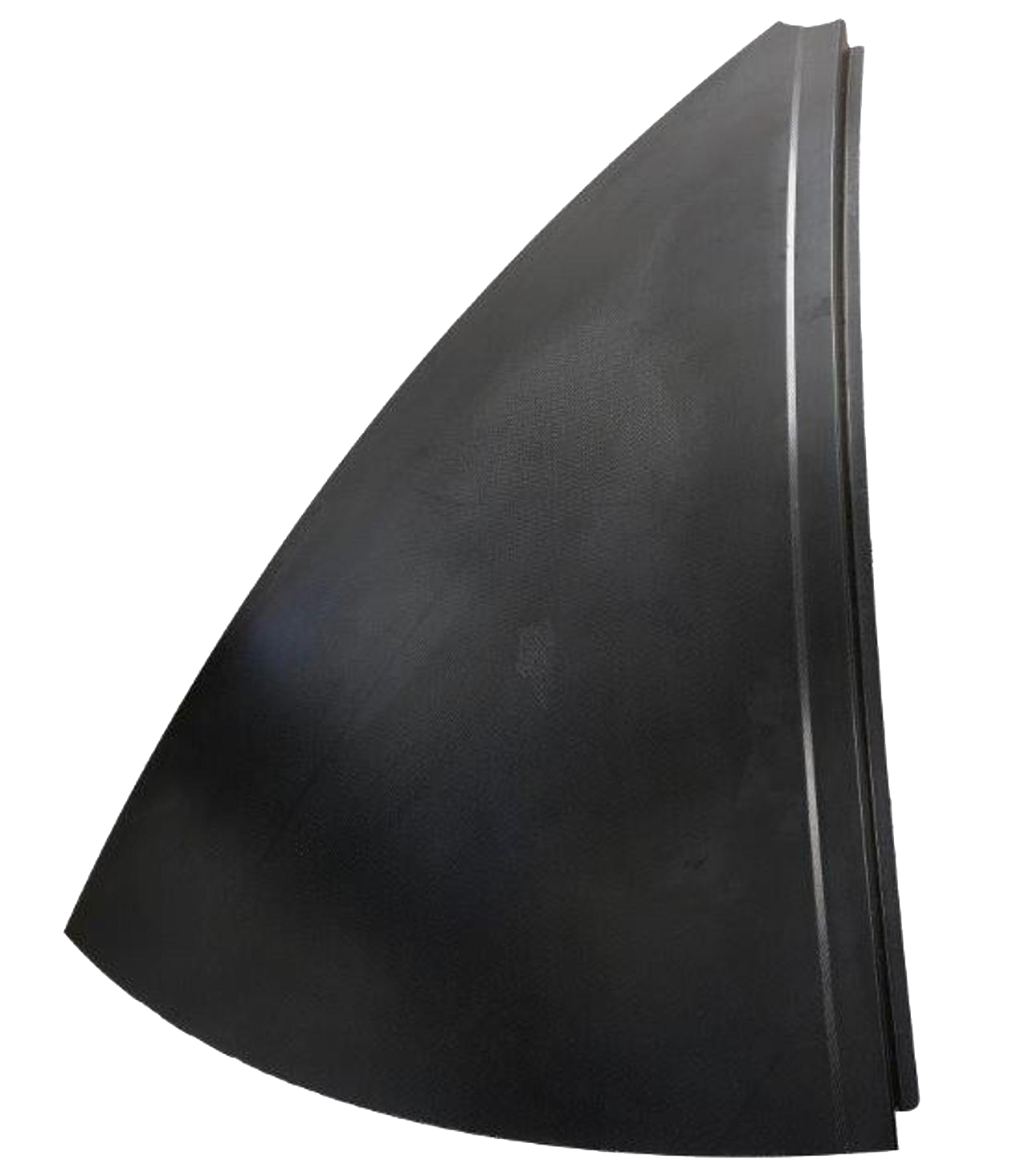
“O compósito termoplástico RPB deveria ter o mesmo preço ou mais barato, mas o material é muito mais caro”, observa Larsen. Assim, o menor custo de produção devido à automação foi fundamental, assim como o uso de oito seções de pétalas idênticas. “Essas seções foram necessárias para formar a forma de curva dupla da peça”, explica Jarka. “A termoformação como uma única peça exigiria uma prensa muito grande que seria muito cara. Assim, oito seções menores foram moldadas por prensagem pelo IVW usando ferramentas de metal combinadas e nós as montamos usando soldagem automatizada. O nível de automação para conformação por pressão termoplástica é maior do que para compósitos termofixos. Você está usando principalmente ferramentas de metal combinadas, com a temperatura alta, mas constante, sendo o principal problema, mas isso também torna o ciclo de prensa automatizado muito rápido ”.
As etapas gerais do processo para o demonstrador RPB são mostradas na Fig. 2. “O processo de soldagem que usamos não era novo”, diz Jarka, “mas teve que ser mais desenvolvido para unir o comprimento de 1,5 metro [e 40 milímetros- larga] para a peça de 3 metros de diâmetro e integrar um sistema de inspeção de qualidade. Os componentes foram primeiro fixados na posição correta usando um gabarito de posicionamento e, em seguida, energia elétrica foi aplicada para gerar o fundido de plástico na zona de solda. ”
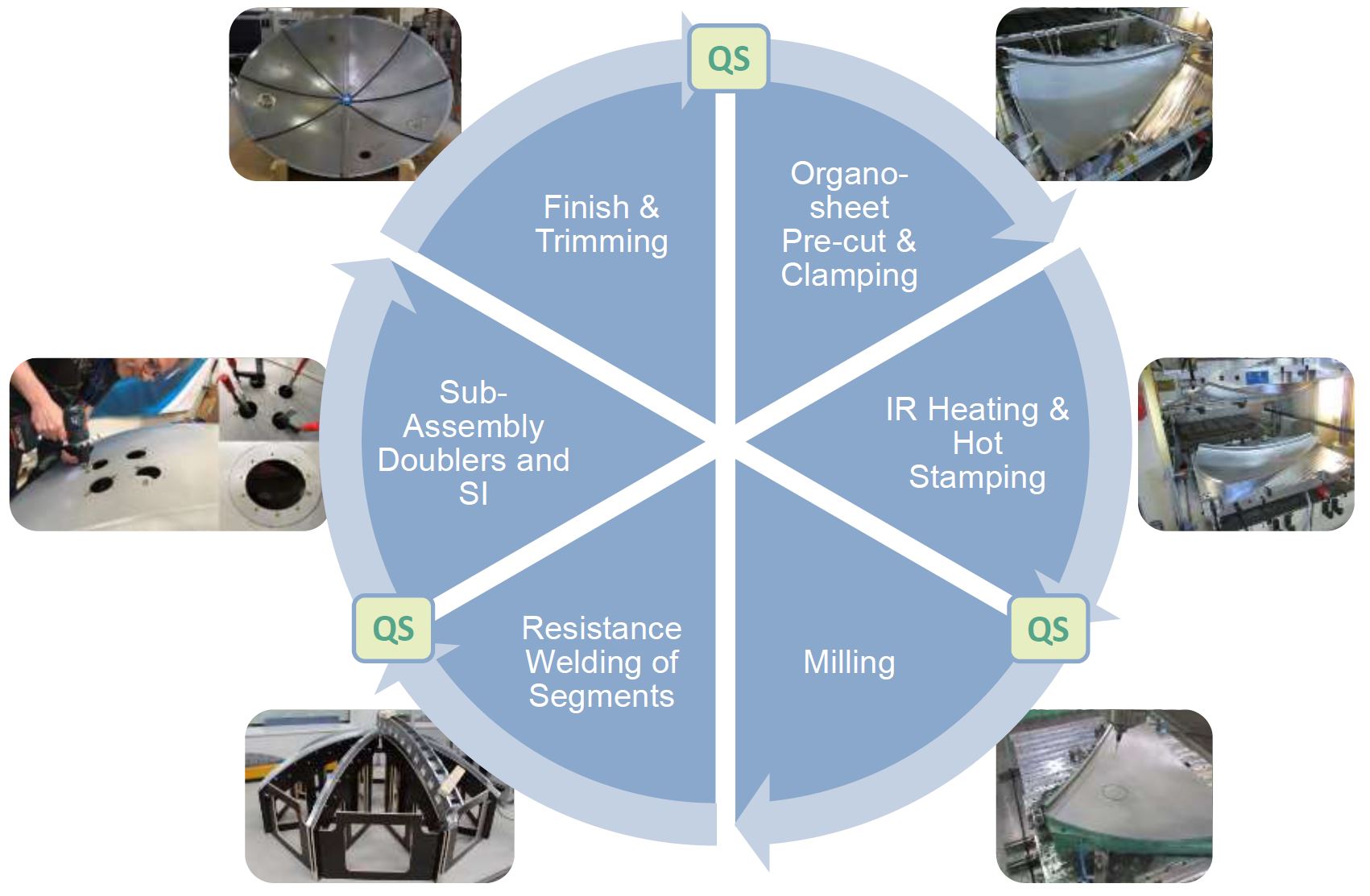
Fig. 2. Etapas do processo RPB termoplástico
Etapas do processo usadas para produzir oito seções (parte inferior) de folha orgânica CF / PPS formada por selo que foram então unidas por soldagem por resistência para formar uma antepara do demonstrador A320. Crédito da foto:Instituto de Estruturas e Design do Centro Aeroespacial Alemão (DLR)
Integrando QA. “Tentamos a termografia, tanto ativada por lâmpada de flash quanto por ultrassom, mas não é tão fácil medir a zona de soldagem com isso”, explica Jarka. “A termografia é muito rápida, mas não lhe diz facilmente se você tem uma boa consolidação.” Em vez disso, eles usaram um equipamento de teste padrão para fazer várias amostras soldadas, medindo a corrente, a tensão e a temperatura. “Nós então os inspecionamos com teste ultrassônico (UT) e fizemos correlações entre os parâmetros do processo e boa consolidação”, diz Larsen. “Se tivermos bons parâmetros, teremos uma boa parte. Também construímos uma simulação de processo para comparar os dados que obtemos durante a soldagem com a linha de base inicial que estabelecemos. ”
Automação e tempo de ciclo. “Todo o processo foi muito rápido, na escala de peças automotivas”, diz Jarka. “Alcançamos o TRL 3 em nossa revisão de 2019 e, desde então, amadurecemos para o TRL 4. Alcançaremos o TRL 6 no final de 2021.” Antes da pandemia, o PAG havia indicado que colocaria o termoplástico RPB em produção em 2021. Embora o futuro agora seja menos claro, o termoplástico RPB ainda é visto como permitindo a "fuselagem de amanhã", reduzindo o peso de 41 para 35 quilos, processo e o tempo de montagem em 75% e o custo geral da peça em mais de 10%.
Comparando compostos TS e TP
“Os processos termoplásticos são tão rápidos que você pode ser mais barato em relação ao alumínio e até atingir uma taxa de produção de 100 aeronaves por mês”, diz Jarka. “O RPB é uma boa aplicação para soldagem termoplástica, mas também para automação”, diz Malecha. “O RPB de fibra seca moldado em líquido é mais caro para automatizar.”
“Mas essa automação é interessante porque você pode obter ganhos reais automatizando apenas alguns dos subprocessos”, diz Larsen. “Por exemplo, com a automação dos auxiliares, poderíamos concluir o ensacamento a vácuo em cerca de uma hora, cerca de 10 vezes mais rápido do que o processo manual.” No entanto, ele admite que o custo é um grande obstáculo para implementar essa melhoria. “O custo das ferramentas digitais, robôs e desenvolvimento é alto demais para uma única peça, como o RPB. Mas se pudéssemos desenvolver uma abordagem modular onde você pudesse usar este sistema para muitas peças, então esse custo poderia ser espalhado mais amplamente, tornando-o acessível quando calculado com o tempo e mão de obra reduzidos. ” O ZLP realmente conseguiu isso, conforme explicado em CW Artigo de julho de 2020:“Compósitos 4.0:Transformação digital, produção adaptativa, novos paradigmas.”
“Ainda não existem muitas comparações entre estruturas termofixas e termoplásticas compostas”, diz Malecha. “Mas estamos começando a comparar processos termofixos e termoplásticos.” Ele observa que o próximo objetivo é mostrar que as linhas de solda termoplástica têm as propriedades necessárias para as asas e fuselagens de aeronaves. E esse desempenho também deve ser mostrado para grandes asas moldadas por líquido integradas, por exemplo. Isso é exatamente o que os programas MFFD e WOT se propuseram a realizar. E aguardamos seus resultados, bem como os de muitos outros projetos Clean Sky 2 e EC, para mostrar os próximos passos à frente.
Resina
- Blog:Moldagem por Injeção de Borracha de Silicone Líquido
- Tecnologia de produção de painel de favo de mel termoplástico EconCore
- Karl Mayer lança linha de produção para fitas UD termoplásticas
- INEOS Styrolution para construir local de produção para compósito termoplástico StyLight
- Tecnologia de produção Herone ganha Prêmio de Inovação JEC
- Termoplásticos sobremoldados, ciclo de 2 minutos, uma célula
- LANXESS expande capacidade de produção de compósitos termoplásticos reforçados com fibra contínua
- A Airtech lança materiais de ensacamento a vácuo de alta temperatura para moldagem termoplástica
- Processo Finex para Produção de Ferro Líquido
- Produção automatizada de acoplamentos de perfuração de petróleo