Fibra de carbono / epóxi para redução de massa automotiva, produção em massa
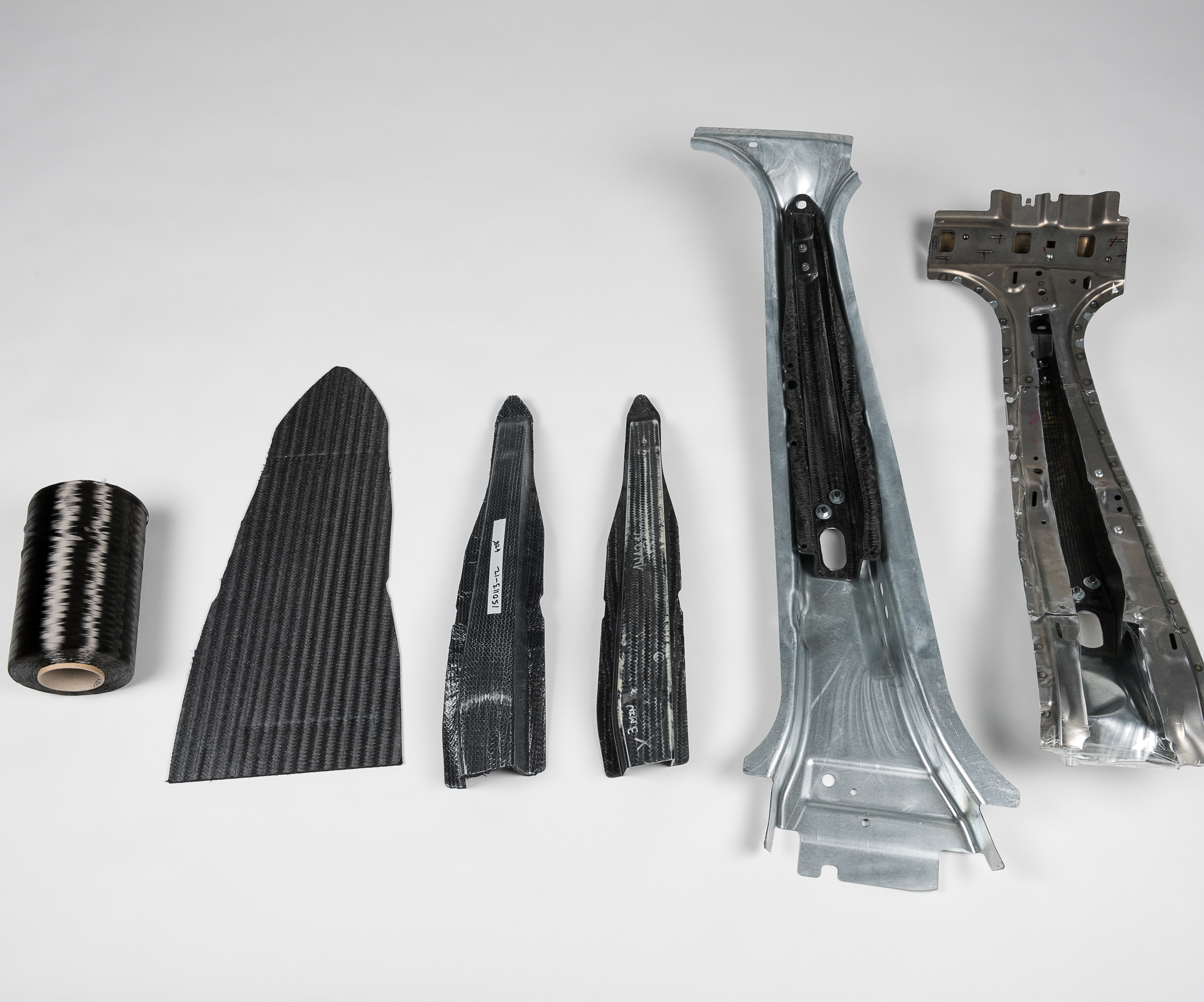
Projeto IACMI 3.2 avaliou compósitos reforçados com fibra de carbono infundidos com um novo sistema de resina à base de epóxi para desenvolver peças compostas estruturais com geometria complexa para substituir metais em aplicações críticas de segurança altamente carregadas em estruturas primárias de grandes volumes de passageiros veículos. Uma das primeiras aplicações avaliadas foi o uso de um pré-impregnado de fibra de carbono / epóxi no pilar B de um veículo de teste. O material pré-impregnado de alto desempenho reduziu diretamente a massa em 3 quilogramas e possibilitou a redução das chapas metálicas circundantes, que poderiam então ser especificadas em ligas menos caras, oferecendo peso adicional e economia de custos. Fonte | Ford Motor Co.
As montadoras na maioria das geografias enfrentam exigências desafiadoras para 2025 sobre emissões reduzidas no tubo de escape e / ou economia de combustível aprimorada para veículos de passageiros. No entanto, desenvolver tecnologia automotiva fundamentalmente nova para atender a esses requisitos é caro, portanto, consórcios para permitir que os membros da cadeia de suprimentos compartilhem os custos de pesquisa pré-competitiva estão sendo usados em muitos países.
Nos EUA, uma dessas organizações é o Institute for Advanced Composites Manufacturing Innovation (IACMI - The Composites Institute, Knoxville, Tenn., EUA). Entre as iniciativas da organização, membros do IACMI da indústria, academia e governo trabalham em projetos multifacetados - envolvendo desenvolvimento de materiais / processos integrados, modelagem / simulação, junção de vários materiais e reciclagem - para resolver problemas de engenharia, melhorar a massa do veículo, reduzir energia consumo e emissões, e criar novos empregos nos EUA.
Projeto 3.2 e o sistema de resina impossível
O Projeto 3.2 foi um dos primeiros projetos que o IACMI assumiu quando foi formado em junho de 2015, embora a tecnologia usada no projeto tenha realmente começado a ser desenvolvida alguns anos antes da criação do IACMI, com uma colaboração entre a Ford Motor Co. (Dearborn, Mich. , EUA) e a então Dow Automotive (agora The Dow Chemical Co., Midland, Michigan, EUA). Quando o IACMI foi formado e o Projeto 3.2 começou, a Ford e a Dow trouxeram seus trabalhos anteriores em um novo sistema de resina epóxi para o programa. Uma vez associado ao IACMI, o programa foi ampliado para incluir várias fases que representam novos usos para esta resina inovadora:um pilar B prepreg, uma tampa do deck com composto de moldagem em folha (SMC) e uma porta traseira SMC / alumínio.
Chamada VORAFUSE, a família de resinas desenvolvida pela Dow para Ford é projetada para uso em prepreg e SMC, e para processar em equipamentos de moldagem por compressão, amplamente disponíveis na indústria automotiva norte-americana. De acordo com os requisitos da Ford, a temperatura de transição vítrea da resina (T g ) é 150-160 ° C, ele molda a 145-155 ° C e cura em menos de 2 minutos a 150 ° C (embora a cura de menos de 1 minuto esteja disponível), tornando-o rápido o suficiente para alto volume ( 100.000-plus / year) produção de veículos. Alcança curas pós-molde de mais de 95%. O sistema está livre de solventes e compostos orgânicos voláteis (VOCs).
“Os CTQs [requisitos essenciais para a qualidade] definidos pela Ford são únicos e nunca foram alcançados em um único produto comercial antes”, explica Dave Bank, bolsista da Dow Polyurethanes R&D. “Por esse motivo, novos produtos químicos e uma série de produtos altamente não tradicionais foram necessários para atender a essas especificações exigentes.”
“A separação termodinâmica de estabilidade de prateleira e polimerização na mistura de resina / curativa produz uma pasta seca que pode ser infundida na fibra de carbono sem o avanço da cura e produzindo um composto de moldagem seco e não pegajoso”, acrescenta Bank. “Ainda assim, quando as condições de moldagem atingem 150 ° C, a química é‘ quente ’e a cura avança rapidamente.” A Dow apresentou 21 pedidos de patentes e até agora obteve quatro para a tecnologia.
Recursos adicionais do sistema VORAFUSE:
- É estável em armazenamento em temperatura ambiente por mais de 50 dias, mas oferece cura instantânea a 150 ° C ou acima. Não requer armazenamento em freezer antes do corte e moldagem do kit, desde que a temperatura de armazenamento não exceda 40 ° C.
- Sua química livre de aderência é ideal para manuseio automatizado. Por não ter a aderência do prepreg tradicional, não causará acúmulo e problemas relacionados com robôs e outros equipamentos de manuseio automatizado.
- Ele contém um novo agente de liberação de molde interno (IMR) para que os processadores possam moldar 1.000 peças antes de ter que aplicar o desmoldante externo nas superfícies da ferramenta. O epóxi normalmente é antitético ao IMR porque é um adesivo muito eficaz para metais.
- O produto não curado pode ser reciclado em peças de alto valor cortando e devolvendo o material aos sistemas de moldagem como um composto reforçado com fibra descontínua que é ideal para moldar geometrias complexas como nervuras / saliências. Ao contrário do epóxi prepreg convencional e SMC, toda a sucata não curada pode ser reutilizada, tornando o material mais sustentável e economizando perdas de sucata que aumentam os custos das peças.
Fase 1:Pilar B do Pré-impregnado
Depois que o VORAFUSE foi incluído no Projeto 3.2, o IACMI começou a trabalhar em um aplicativo automotivo que se tornaria a Fase 1 do projeto geral. Os membros da equipe incluíam Ford, Dow, DowAksa US LLC (Tucson, Az., Braço da DowAksa BV com sede nos EUA, uma joint venture 50/50 entre Dow Chemical e Aksa Akrilik Kimya Sanayii A.Ş., Çiftlikköy-Yalova, Turquia); Michigan State University (East Lansing, Mich., U.S.); Purdue University (West Lafayette, Ind., U.S.); University of Tennessee-Knoxville (Knoxville, Tenn., U.S.); Continental Structural Plastics (CSP, Auburn Hills, Mich., U.S.); e Oak Ridge National Laboratory (Oak Ridge, Tenn., U.S.).
Na primeira fase, os pesquisadores desenvolveram um pré-impregnado contínuo (tecido trançado e não crimpado) reforçado com fibra de carbono impregnado com o epóxi. A resina VORAFUSE P6300 foi formulada para compatibilidade com a fibra de carbono de módulo padrão DowAksa A42 D012 24K. O objetivo da equipe era usar fibra de carbono / epóxi prepreg para desenvolver peças compostas estruturais com geometria complexa para substituir metal estampado em aplicações críticas de segurança altamente carregadas em estruturas primárias de carroceria de veículos de alto volume.
Para o demonstrador de tecnologia, o pilar B de um lado de um Ford Fusion veículo de teste foi usado. A viabilidade foi avaliada primeiro por simulação e, em seguida, as peças físicas foram moldadas e submetidas a todos os testes necessários - incluindo colisões de veículos em grande escala. As peças foram aprovadas com louvor, reduzindo a massa em 3 quilos por lado em comparação com os metais existentes. A sucata não curada foi reciclada para formar as estruturas de costelas complexas do pilar. O composto de alto desempenho permitiu a redução das chapas metálicas circundantes, que poderiam então ser especificadas em ligas menos caras, oferecendo peso adicional e economia de custos.
Tendo passado em todos os requisitos da Ford, o primeiro uso comercial do material foi para um cabeçalho de teto frontal e um painel de fechamento do piso frontal no Ford GT com uso intensivo de composto de carbono Super-carro.
Não surpreendentemente, o pré-impregnado de fibra de carbono / epóxi tem um custo adicional, então é melhor para veículos com requisitos de redução de massa significativos que podem pagar um prêmio por oportunidades significativas de redução de peso.
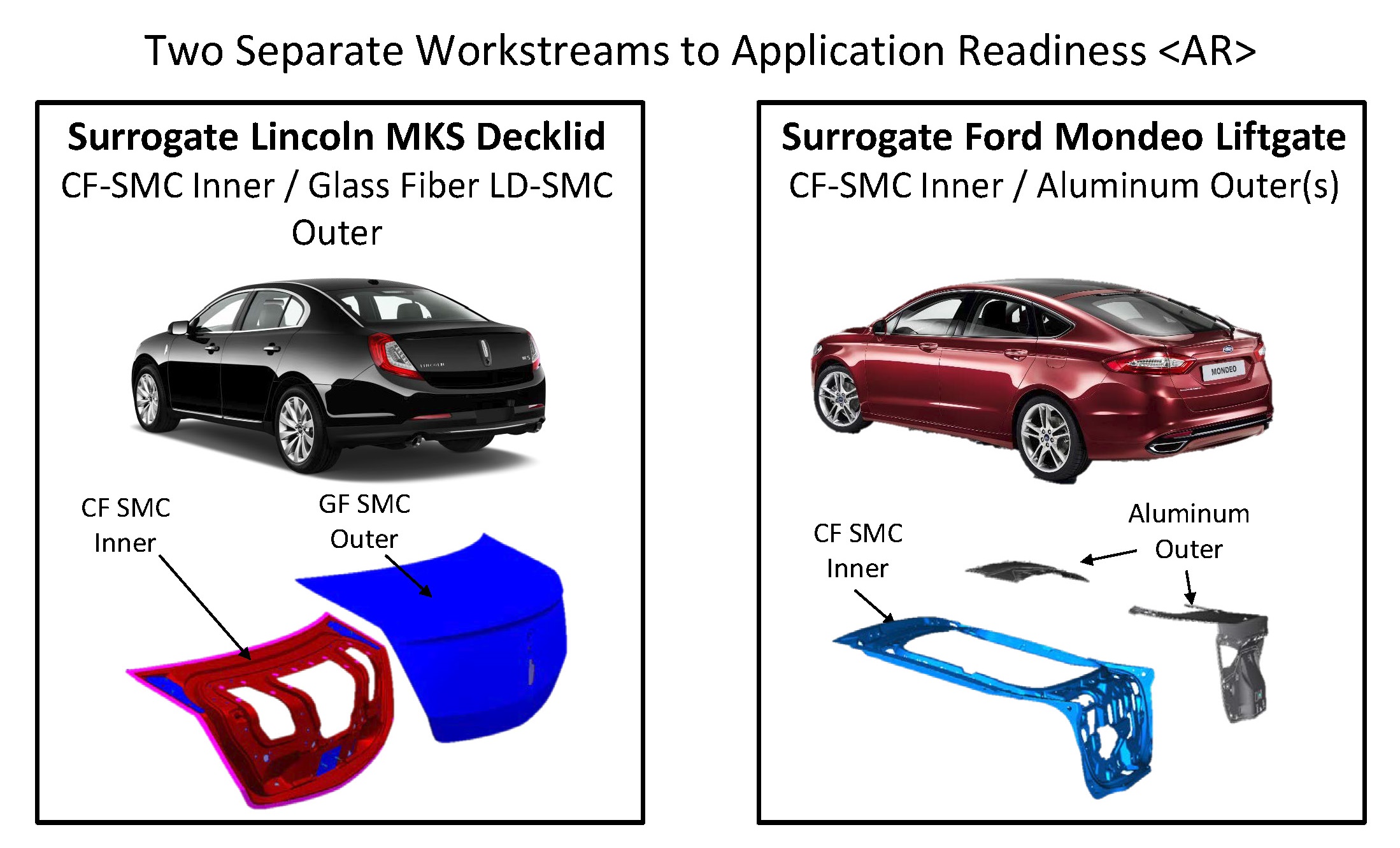
Fase 2 / Fluxo de Trabalho 1:Decklid All-SMC
Com base nos sucessos do pré-impregnado, os pesquisadores do projeto exploraram em seguida o SMC descontínuo reforçado com fibra de carbono com a nova resina epóxi em estruturas 3D complexas com funções críticas de segurança. Em um demonstrador, o SMC de fibra de carbono / epóxi foi usado como o painel interno / estrutural de uma tampa do deck colada (tampa do porta-malas), e em outro demonstrador foi usado para o painel interno / estrutural de uma porta elevatória colada muito maior e mais complexa ( porta traseira / porta contendo vidros, motores do limpador, luzes, etc.). Em ambos os fluxos de trabalho, as restrições do projeto original, hardware, técnicas de união e adesivos estruturais permaneceram inalterados. Alvos mecânicos desafiadores de mais de 300 MPa de resistência à tração e mais de 40 GPa de rigidez à tração - comparável ao magnésio e alumínio fundidos existentes - foram usados. O SMC também precisava de um fluxo maior do que o pré-impregnado, então um grau ligeiramente diferente, VORAFUSE M6400, foi desenvolvido.
Para o demonstrador do decklid, que representou um avanço incremental sobre a tecnologia atual de vidro / SMC, o SMC de fibra de carbono / epóxi substituiu o SMC de poliéster insaturado reforçado com fibra de vidro estrutural convencional por um decklid interno em um Lincoln MKS veículo protótipo. O painel interno de SMC de fibra de carbono / epóxi foi ligado a um painel externo de SMC de fibra de vidro / poliéster de baixa densidade (LD, 1,25 SG), que substituiu um componente de SMC de fibra de vidro / poliéster de densidade padrão (1,9 SG). Tanto os materiais antigos quanto os novos do painel externo eram compatíveis com a Classe A. A ferramenta original foi reutilizada para moldar painéis internos de fibra de carbono / epóxi SMC e painéis externos de fibra de vidro / poliéster. O encolhimento - embora ligeiramente diferente entre os dois sistemas de resina - era próximo o suficiente para não causar problemas de ajuste e acabamento (em outras palavras, nenhuma mudança dimensional significativa foi observada).
A prototipagem virtual submeteu a montagem ligada a uma série de casos de carga desafiadores, incluindo rigidez de torção, rigidez de canto frontal, deflexão em cascata e cargas de trava. Dezenas de painéis internos e externos foram moldados, colados e testados - incluindo impactos traseiros desafiadores de 89 quilômetros por hora. As montagens passaram nos testes virtuais e físicos sem problemas.
A massa do decklid foi reduzida em 30% (de 10,5 para 7,33 kg) em relação ao benchmark. No entanto, se os orçamentos permitissem que o painel interno fosse refeito - o que poderia ter sido projetado mais fino devido ao seu desempenho mecânico superior em comparação com o existente - então os pesquisadores calcularam que a massa poderia ter sido reduzida em pelo menos 35% com paredes de 2 milímetros, e ainda mais com paredes de 1,5 mm.
O SMC de fibra de carbono / epóxi passou em todos os requisitos da Ford e agora pode ser usado em plataformas comerciais, embora o custo seja mais alto do que o SMC de fibra de vidro / poliéster convencional.
Fase 2 / Fluxo de trabalho 2:SMC / porta traseira de alumínio
Para o último projeto, os pesquisadores se voltaram para um cenário verdadeiramente desafiador:substituir metal leve por fibra de carbono / epóxi SMC para produzir um conjunto ligado híbrido (metal / composto) para portas elevatórias maiores e mais complexas no Ford Mondeo veículos de teste de cinco portas / hatchback. Para minimizar as alterações nas sequências de construção do veículo, os pesquisadores projetaram o conjunto para ser adicionado ao corpo em branco (BIW) antes do tratamento eletroforético de revestimento de ferrugem (e-revestimento) e dos ciclos de pintura e cozimento associados.
A fibra de carbono / epóxi SMC substituiu o magnésio nos painéis estruturais / internos que eram colados aos painéis externos de alumínio existentes. Como novas ferramentas tiveram que ser criadas para produzir o painel composto, a peça foi reprojetada. A espessura do painel foi variada de acordo com os requisitos de rigidez / resistência e para adicionar nervuras. Além disso, reforços metálicos foram usados em áreas de fixação de alta carga para amortecedores a gás, travas, dobradiças e travas, o que tornou o painel composto um pouco mais espesso - algo que o espaço da embalagem permitia.
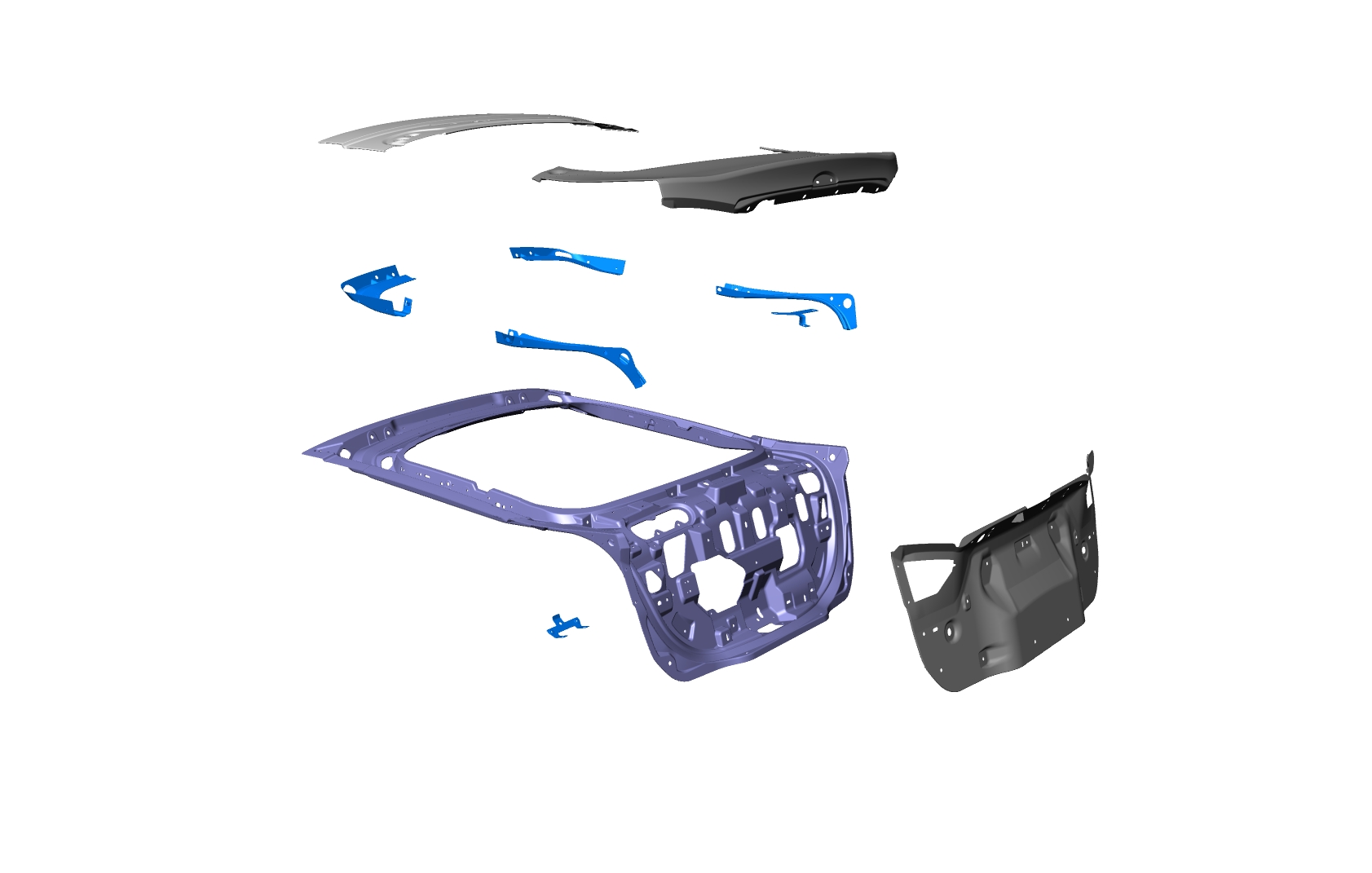
Uma vista explodida da porta traseira SMC / alumínio (com ferragens metálicas) para a versão de cinco portas / hatchback do Ford Mondeo. Fonte | Ford Motor Co.
Esses conjuntos multimateriais foram submetidos a requisitos exigentes, incluindo cargas de torção e flexão, estabilidade lateral, resistência à corrosão, durabilidade de longo prazo e testes de colisão traseira. Eles também tiveram que atender aos rígidos requisitos de estabilidade dimensional com relação a margens e fluidez.
Embora o sistema híbrido tenha facilmente atendido à maioria dos requisitos, havia problemas de encaixe e acabamento devido ao coeficiente de expansão térmica linear (CLTE) incompatíveis entre os painéis internos compostos e os painéis externos de alumínio, o que levou ao acúmulo de tensão residual nas juntas coladas e à distorção do painel após o resfriamento baixa. O trabalho subsequente com a equipe de simulação da Purdue University se concentrou em melhorar as previsões de módulo, resistência e cinética de cura para o adesivo epóxi 1K (escolhido por sua capacidade de sobreviver a temperaturas de e-coating) na esperança de fazer engenharia reversa de um adesivo que funcionasse melhor. A distorção foi reduzida em uma ordem de magnitude, mas errou ligeiramente o alvo. Várias soluções são possíveis:um adesivo de cura 2K / temperatura ambiente ou cura por indução pode ser experimentado ou um novo adesivo de alta temperatura pode ser desenvolvido. A longo prazo, substituir o alumínio por composto de fibra de carbono no painel externo eliminaria o problema, assim como produziria a porta traseira fora de linha e acrescentá-la-ia mais tarde na sequência de construção do veículo. No entanto, ambas as opções adicionam custo.
O Projeto 3.2 está sendo finalizado, mas produziu uma tecnologia interessante, algumas das quais - o pré-impregnado de pilar B e SMC decklid - estão prontas para uso comercial e algumas apontam para áreas onde é necessário mais trabalho.
“Trabalhar com o IACMI e nossos parceiros industriais e acadêmicos nos permitiu mergulhar muito mais profundamente na tecnologia desde o início, para desenvolver a ciência fundamental e aproveitar uma base de conhecimento muito mais ampla do que poderíamos ter feito sozinhos,” resume o líder do Projeto 3.2 Patrick Blanchard, Líder técnico - sistemas de polímeros avançados, pesquisa e inovação da Ford. “Estamos ansiosos para identificar novas oportunidades comerciais e atividades de P&D para continuar trabalhando com nossos parceiros IACMI.”
Resina
- Eletrodomésticos de fibra de carbono para sua casa
- Os 3 principais usos para impressão 3D de fibra de carbono na manufatura
- Usos inovadores para fibra de carbono
- Fibra de carbono em aplicações automotivas
- 5 usos divertidos para folhas de fibra de carbono
- Para que é usado o envoltório de fibra de carbono?
- Materiais:Vidro e PP reforçado com fibra de carbono para automotivo
- Hexion apresenta solução epóxi de dois componentes para produção de compósitos aeroespaciais
- Foiling Iate a motor impressiona em fibra de carbono / epóxi
- Série projetada para linha de produção automotiva