Passeio pela fábrica:STELIA Aerospace, Méaulte, França
Com 7.000 funcionários em todo o mundo e receitas de € 2,2 bilhões em 2018, a STELIA Aerospace (Toulouse, França) declara claramente seus principais produtos e posição na indústria:Nº 1 na Europa / Nº. 3 no mundo para aeroestruturas, No. 1 mundial para assentos de piloto e da tripulação e No. 3 mundial para assentos de passageiros da primeira classe e da classe executiva.
O uso de compostos da STELIA Aerospace se estende às seções da fuselagem dianteira do Airbus A350, asas para aeronaves turboélice ATR, várias estruturas de helicópteros e em alguns produtos de assento, incluindo seu mais novo assento OPAL. As instalações de produção de compósitos incluem unidades francesas Méaulte (grandes seções da fuselagem) e Salaunes (peças compostas menores), peças detalhadas e montagem em Marrocos e na Tunísia e uma ampla gama de peças compostas para aeronaves, defesa e espaço na unidade anterior da Composites Atlantic em Lunenburg, Nova Scotia, Canadá.
A STELIA Aerospace foi formada por meio da fusão em 2015 de duas subsidiárias anteriores da Airbus - Aerolia e Sogerma. Sua unidade de Méaulte - uma unidade de 1,5 horas ao norte de Paris - cobre 49 hectares com 150.000 metros quadrados de espaço de produção, 1.500 funcionários e 500 subcontratados, e é uma parte importante da cadeia de abastecimento da Airbus. Sua localização em uma pequena cidade esconde uma potência de produção, “entregando 860 seções de fuselagem do nariz para A320, A330, A350, A380 e A400M em 2018”, disse o gerente de comunicações da STELIA Méaulte, François Fournier. Ele é o meu guia na produção da fuselagem de nariz do A350 da “Fábrica do Futuro” e nas instalações da STELIALAB R&T, acompanhado por Olivier Canal, STELIA Aerospace Méaulte chefe de fabricação, montagem e automação de R&T, fábrica digital e compósitos e Simon Maire-Vigeur , chefe da fabricação de compósitos de R&T, STELIALAB.
“Fábrica do Futuro”
Durante uma apresentação introdutória no prédio da sede do site, Fournier explica que a STELIA Aerospace investiu em tecnologias futuras, como fabricação e automação digital, incluindo realidade aumentada / realidade virtual usada para aumentar a eficiência na produção e robôs / cobôs para uma montagem mais eficiente.
“O futuro é composto e estruturas metálicas ”, observa Canal. “Estamos tentando definir soluções futuras não para substituir nossos trabalhadores, mas para torná-los mais eficientes.”
Essa busca por eficiência talvez seja melhor exemplificada pela iniciativa “Fábrica do Futuro”, iniciada cinco anos atrás, para atender às rampas na produção de A320 e A350. “Abraçamos uma nova estratégia industrial para este local”, lembra Canal, que foi gerente de projeto da iniciativa. “Queríamos a capacidade de atender a taxas de produção variáveis e desenvolver ferramentas flexíveis que pudéssemos reaproveitar de um programa para outro.”
Outro resultado desse repensar foi a dedicação de prédios a programas específicos. “Cada um teria uma linha e uma equipe”, diz Canal, “e seria projetado com uma abordagem de manufatura enxuta, que se concentra na eliminação de desperdícios em mão de obra, movimentação, materiais e processos”. A STELIA Aerospace também redesenhou a linha A320 e obteve um aumento de 10 a 20 por cento na produtividade, “o que na verdade é uma melhoria significativa”, diz Canal. “Conseguimos isso em 2,5 anos, mudando mais de 50 por cento da pegada de fabricação deste site, mantendo a produção e Entrega 100 por cento no prazo sem perda de qualidade. ” Esse sucesso é creditado ao apoio da administração de alto nível, “mas também trabalhamos duro para que os trabalhadores tivessem propriedade”, observa ele.
Canal explica que o projeto do prédio de produção do A350 de 30.000 metros quadrados foi ditado pelo fluxo, exemplificado em seu formato em U, com matérias-primas entrando por uma extremidade e seções acabadas da fuselagem saindo pela outra. “Tudo para a produção de nossas estruturas A350 está neste prédio, desde a configuração inicial até a montagem final. Isso é importante, por exemplo, para permitir que quaisquer problemas de qualidade sejam identificados e resolvidos de forma rápida e fácil ”, diz ele.
Para o A350, a STELIA Aerospace produz a seção 11 da fuselagem do nariz, que é toda em metal para melhor resistir aos danos causados por pássaros, bem como o complexo conjunto híbrido de metal / composto para a seção 12 e a unidade inferior da seção 11/12, que inclui o nariz compartimento do trem de pouso. Fournier mostra o vídeo "Factory of the Future" da STELIA Aerospace, apontando a linha pulsada, como aquela usada para montagem automotiva. “Montamos uma linha de demonstração para permitir que os trabalhadores treinem e desmistifiquem essa linha móvel, que funciona em um tempo takt específico para atender a plena produção”, diz Canal.
Outro aspecto foi a tecnologia digital. “As soluções digitais nos permitiram colocar todos os esquemas técnicos e etapas em um tablet e garantir o acesso à última maquete 3D para cada seção”, diz Canal. Os trabalhadores são, portanto, mantidos informados sobre os detalhes e mudanças cruciais, enquanto os gerentes são facilmente notificados sobre os problemas potenciais. “Também desenvolvemos realidade aumentada para auxiliar na montagem, por exemplo, projeção nas conchas da fuselagem mostrando quais peças e onde as fixações devem ser feitas”, observa Canal. Ele acrescenta que a inspeção cobots são usados para completar digitalizações 3D de seções acabadas que são então comparadas com a maquete digital, identificando quaisquer objetos estranhos ou peças ausentes, problemas de qualidade, etc.
Nosso tour começou na sala limpa do prédio de produção do A350, onde máquinas de colocação automática de fibra (AFP) Coriolis (Quéven, França) colocam grandes conchas de fuselagem de polímero reforçado com fibra de carbono (CFRP) para a unidade inferior da seção 11/12 e a coroa e duas conchas laterais para a seção 12. Essas conchas são então combinadas com longarinas pré-fabricadas, ensacadas a vácuo e curadas em autoclave. Após a cura, eles são aparados e carregados em ferramentas de manuseio que permitem fácil transporte em todas as etapas de montagem, que inclui perfuração robótica e instalação de fixadores. Cada painel é inspecionado usando teste não destrutivo automatizado (NDT). As montagens concluídas são entregues na linha de montagem da fuselagem da Airbus em Saint Nazaire, França.
STELIALAB
A próxima parada é o centro STELIALAB R&T de 2.000 metros quadrados, que ocupa a metade esquerda do IndustriLAB, um centro regional de tecnologia e treinamento localizado logo ao sul do complexo fechado STELIA. As atividades da STELIALAB são dedicadas a compósitos, montagens e tecnologias digitais.
O passeio aqui começa novamente na salle blanche (sala limpa), uma sala razoavelmente grande e aberta com suprimentos de ensacamento e ferramentas de armazenamento. Simon Maire-Vigueur explica que a missão do grupo é identificar o futuro da produção de baixo custo e alto volume para peças grandes e complexas. A industrialização de compostos termofixos inclui processos de AFP de alta velocidade e infusão de resina líquida (LRI), incluindo moldagem por transferência de resina (RTM), para grandes estruturas de caixa fechada, como componentes de asa, planos de cauda horizontais e planos de cauda verticais.
Saindo da sala limpa, entramos na sala AFP ocupada por uma máquina Coriolis que pode colocar peças de até 4 metros de comprimento. Dedicado à R&T, Maire-Vigueur observa que é ocupado por mais de 200 dias por ano. STELIALAB desenvolveu um processo para integrar endurecedores secos criados por AFP e películas que são curadas em autoclave (OOA) usando um forno ou ferramentas autoaquecidas. “Preferimos LRI com pressão de injeção mais baixa porque podemos usar ferramentas mais baratas”, diz Maire-Vigueur.
Roteiro TPC
Esta máquina AFP também foi usada para colocar a pele para o demonstrador de fuselagem / cauda de helicóptero composto totalmente termoplástico (TPC) como parte do programa de desenvolvimento ARCHES TP. Exibido no Paris Air Show 2017 e também no JEC World em 2018 e 2019, ele foi feito usando 8 cabos de fita de fibra de carbono / polietercetonecetona (PEKK) de 0,25 polegadas de largura com aquecimento a laser. “Integramos a proteção contra raios com o AFP durante o layup”, observa Maire-Vigueur. “A pele foi curada com OOA usando filme de ensacamento Kapton, o que na verdade não é muito conveniente”. As longarinas em forma de ômega eram feitas de painéis planos de fita unidirecional adquiridos e formados por estampagem pela Aviacomp (Toulouse, França). O mesmo processo foi utilizado para as molduras, mas utilizando chapas feitas de tecido fornecido pela Porcher (Badinières, França) e estampadas na Cetim (Nantes, França). Embora as armações fossem fixadas mecanicamente de maneira padrão, as longarinas eram fixadas por meio de soldagem por indução dinâmica e automatizada. “Isso permite custos mais baixos e novas possibilidades de design”, observa Maire-Vigueur. “Também demonstramos sobremoldagem para pontos de fixação, como chicotes elétricos.”
Quando questionado sobre os desafios do programa, Maire-Vigueur cita os layups, soldagem e cronograma de 15 meses. “Mesmo conseguir a estampagem sem muita distorção no tecido não foi fácil”, acrescenta. Embora o projeto do tailboom tenha sido concluído pelo escritório de design da STELIA Aerospace em Toulouse, toda a produção foi supervisionada pela STELIALAB. No entanto, o ARCHES TP foi apenas uma etapa no roteiro de compósitos termoplásticos da STELIA Aerospace. A empresa continua a desenvolver tecnologias TPC para demonstrar a viabilidade de uma fuselagem TPC em escala real nos anos seguintes.
Repensando futuras aeroestruturas
Saindo da sala AFP, o passeio prossegue por um corredor muito grande e aberto que é seccionado em "células de desenvolvimento" seguras por paredes temporárias para proteger a propriedade intelectual. Atravessando o corredor e virando à esquerda, chegamos a uma área com uma pequena autoclave Scholz (Coesfeld, Alemanha) com capacidade para 450 ° C e uma máquina de injeção para infusão de resina. “Como nosso roteiro é curar OOA, na verdade usamos a autoclave como um forno, curando compósitos termoplásticos sem pressão”, explica Maire-Vigueur. Há uma sala de acabamento com cortinas e uma área próxima a ela com equipamento NDT, incluindo um pequeno sistema C-scan.
Viramos novamente e entramos em um grande laboratório de testes. “Podemos estudar seções transversais polidas para controle de qualidade e investigações de materiais e processos”, diz Maire-Vigueur. O laboratório também possui um braço Romer (Hexagon Manufacturing Intelligence, Shropshire, Reino Unido) para medição coordenada e equipamento para relação de volume de fibra, dureza e testes químicos. “Todos os engenheiros de nossa equipe de R&T são capazes de fazer seus próprios materiais e controle de processo”, observa Maire-Vigueur. “Nós os treinamos para serem capazes de operar desde o projeto, passando pela fabricação, até a inspeção e teste das peças finais. Isso é importante para compreender todo o processo e permite uma avaliação rápida dos problemas suspeitos e suas causas. O design não é separado da fabricação e dos testes de qualidade. ”
A parada final é um grande laboratório de automação dentro de uma das áreas muradas. Uma breve olhada no interior mostra o trabalho que explora novas montagens usando robôs e cobots. “Estamos analisando o desenvolvimento de ferramentas menores e mais funcionais e tentando imaginar como você poderia juntar as peças com mais rapidez e menor custo”, diz Canal. “Nossa cultura é expandir limites e abrir novos caminhos. Temos sido líderes na implementação de robótica e agora somos líderes na promoção da tecnologia de compósitos. Demonstramos nossa capacidade de repensar e repensar o futuro e nunca iremos parar. ”
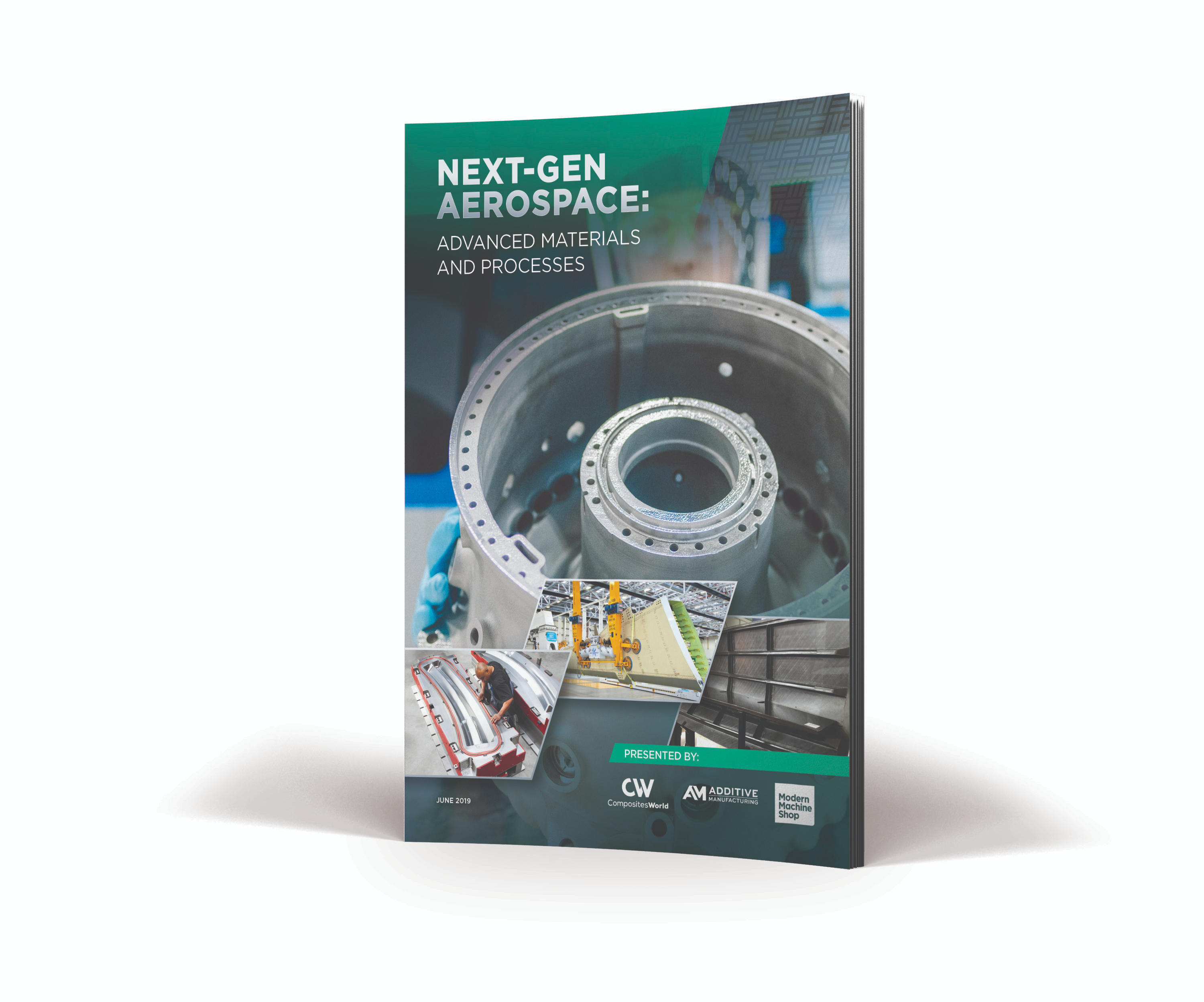
A próxima geração de fabricação aeroespacial
Com o setor de aviação comercial projetado para dobrar nos próximos 20 anos, atender à demanda por aeronaves de passageiros e carga exigirá novas tecnologias e taxas de fabricação sem precedentes.
Saiba mais sobre os materiais e processos que moldarão as aeronaves de última geração em uma coleção de histórias de CompositesWorld, Modern Machine Shop e Fabricação de aditivos , disponível para ler ou baixar gratuitamente . Venha aqui.
Resina
- Vespel®:O Material Aeroespacial
- Poliplásticos para expandir a produção Topas COC
- Radici está expandindo significativamente a capacidade de produção global
- Polykemi investe em sua própria planta de composição nos EUA
- Rethink Robotics ganha nova sede e planta de produção
- Toyota escolhe local da Carolina do Norte para a planta de produção de baterias EV
- Fabricantes visitam Southco para um tour pela fábrica, discussão de melhores práticas de melhoria contínua
- Arkema Inc. constrói planta de produção U.S. PEKK
- Hexion apresenta solução epóxi de dois componentes para produção de compósitos aeroespaciais
- Kaneka Aerospace alcança certificação aeroespacial AS9100D