Uma introdução à fabricação de aditivos para arco elétrico [Atualização 2020]
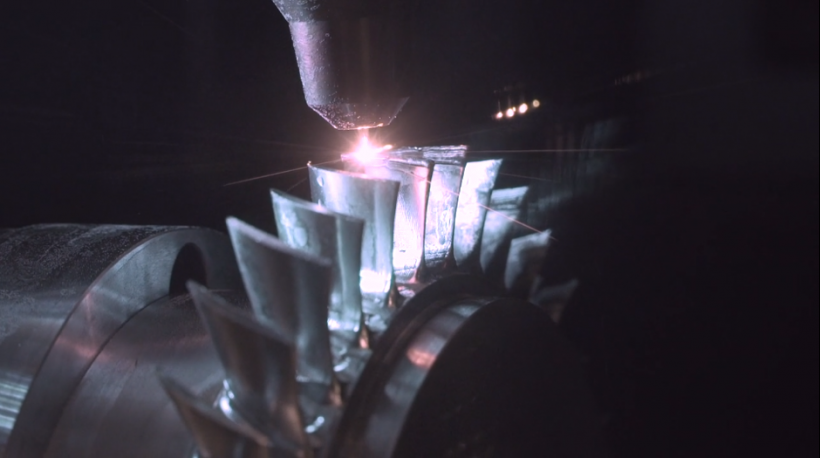
Fabricação de aditivos para arco elétrico (WAAM) é uma das tecnologias de impressão 3D de metal menos conhecidas, mas possui um grande potencial para aplicações de impressão 3D em grande escala em vários setores.
Este guia se concentrará em como WAAM funciona, seus benefícios e limitações, bem como as principais empresas WAAM e aplicativos de sucesso.
Como funciona a fabricação de aditivos para arco elétrico?
WAAM é uma variação de uma tecnologia de deposição de energia direta e usa um processo de soldagem a arco para imprimir peças de metal em 3D.
Ao contrário dos processos AM de pó de metal mais comuns, WAAM funciona derretendo fio de metal usando um arco elétrico como fonte de calor.
O processo é controlado por um braço robótico e o A forma é construída sobre um material de substrato (uma placa de base) do qual a peça pode ser cortada uma vez acabada.
O fio, quando derretido, é extrudado na forma de pérolas no substrato. À medida que as contas se unem, elas criam uma camada de material metálico. O processo é então repetido, camada por camada, até que a parte metálica esteja concluída.
Você pode ver o processo em ação aqui:
Materiais
WAAM pode trabalhar com uma ampla gama de metais, desde que sejam na forma de arame. Esta lista inclui aço inoxidável, ligas à base de níquel, ligas de titânio e ligas de alumínio. Qualquer metal que possa ser soldado também pode ser usado com WAAM.
Os benefícios da fabricação de aditivos para arco elétrico
A capacidade de imprimir grandes peças de metal em 3D
WAAM é particularmente adequado para a fabricação de peças de metal em grande escala. Isso está em contraste com as tecnologias de metal AM de pó de cama (PBF), que normalmente produzem componentes menores de alta definição.
Ao contrário das máquinas PBF AM, que têm um envelope de construção limitado, o braço robótico de uma máquina WAAM tem mais liberdade de movimento, o que significa que o tamanho de um componente não é limitado pelo espaço, mas apenas por a distância que o braço robótico pode alcançar. Isso permite a produção de peças maiores, o que não seria possível com processos PBF.
Processo e materiais mais baratos
Em termos de custos de material, o fio de solda usado no processo de impressão WAAM é significativamente mais barato do que o pó metálico usado no metal PBF.
Isso ocorre porque a tecnologia WAAM é baseada na soldagem, um método bem estabelecido tecnologia de fabricação por si só. O hardware WAAM geralmente inclui equipamento de soldagem pronto para uso, que é mais barato do que muitas impressoras 3D de metal disponíveis no mercado.
Além disso, o fio é normalmente mais fácil de manusear do que o pó, que requer equipamento de proteção especializado usar.
Peças de alta qualidade
As peças produzidas com WAAM são particularmente notáveis por sua alta densidade e propriedades mecânicas fortes, que são comparáveis às peças fabricadas com métodos de fabricação tradicionais.
Como a matéria-prima do arame é um material de entrada 100 por cento denso, há uma porosidade insignificante induzida no processo de fabricação, levando a uma peça final muito densa.
É adequado para operações de reparo
WAAM também é uma boa opção para operações de reparo e manutenção de componentes específicos como lâminas de turbinas, bem como moldes e matrizes.
Características desgastadas ou peças danificadas podem ser reparadas com WAAM depositando novo material em sua superfície. Isso pode resultar em economias de custo significativas, pois elimina a necessidade de produzir uma nova peça do zero.
As limitações do WAAM
Tensões e distorções residuais
Um desafio associado ao WAAM é o gerenciamento de calor.
O processo de impressão envolve altas temperaturas, causando o acúmulo de tensão residual - um problema comumente enfrentado na impressão 3D de metal. Como a tensão residual pode frequentemente levar a deformações em um componente, o resfriamento deve ser fatorado no processo.
Alguns materiais requerem blindagem
Ao usar certos materiais, como o titânio, a blindagem é necessária para criar uma atmosfera inerte e garantir as condições de construção adequadas.
Isso significa que o processo deve ocorrer em uma câmara de gás inerte. Porém, a câmara de gás inerte limita o tamanho das peças que podem ser produzidas com esta tecnologia e a instalação de tal câmara aumentará o custo do equipamento.
Baixa resolução
WAAM normalmente produz peças de formato quase final com um acabamento superficial ruim. A superfície de uma peça, portanto, precisa ser acabada por meio de usinagem.
Principais players WAAM e aplicativos de tecnologia
WAAM3D
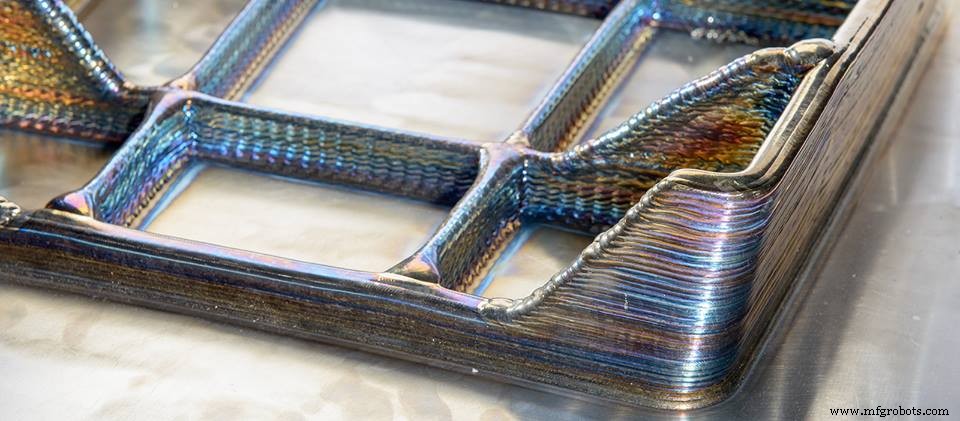
Em 2020, o mercado WAAM permanece pequeno, com um punhado de empresas desenvolvendo ativamente esta tecnologia de impressão 3D de metal.
WAAM3D é talvez um dos nomes menos conhecidos no campo, mas a empresa realizou uma extensa pesquisa antes de trazer sua tecnologia para o mercado.
WAAM3D foi fundada em 2018 para comercializar a propriedade intelectual da Cranfield University no campo WAAM.
De acordo com a empresa, a falta de cadeia de abastecimento - nomeadamente ferramentas de software, hardware projetado WAAM, matérias-primas, treinamento e serviços - tem impedido a merecida adoção industrial de processos WAAM, apesar de seus benefícios comerciais comprovados .
A empresa tem como objetivo criar essa cadeia de abastecimento e promover o uso de WAAM nas indústrias aeroespacial e de defesa, petróleo e gás, energia e nuclear.
Até agora, WAAM3D publicou várias aplicações de sucesso de sua tecnologia.
Um é o chassi traseiro do caça Eurofighter Typhoon da BAE Systems. A peça de titânio, que mede 2,5 mx 1,5 m em área plana, suporta os motores Eurojet EJ200 duplos capazes de produzir 60 kN (13.500 lbf) de empuxo seco.
Outra peça de titânio, uma pressão de 1 m de comprimento navio, foi fabricado para Thales Alenia Space. Ao usar WAAM para fabricar este componente, a equipe economizou mais de 200 kg de material por item e foi capaz de consolidar duas partes do navio em uma.
Além disso, a produção da peça supostamente demorou vários dias - uma redução significativa no prazo de entrega, uma vez que a peça geralmente leva vários meses para ser produzida.
No início deste ano, WAAM3D concluiu sua primeira rodada de financiamento da Série A, que deverá levar a empresa ainda mais comercializando a tecnologia WAAM.
AML3D
A Cranfield University inspirou a fundação de outra empresa:AML3D. O Diretor Executivo da AML3D, Andrew Sales, estudou em Cranfield e, fascinado pelo potencial da tecnologia, fundou um bureau de serviços WAAM na Austrália em 2014.
Em 2019, a empresa obteve a certificação do organismo de acreditação da indústria de transporte marítimo global, Lloyd's Register. Com a certificação em vigor, o AML3D entregou sua primeira peça a um cliente marítimo:um conjunto de anéis de desgaste de aço inoxidável martensítico.
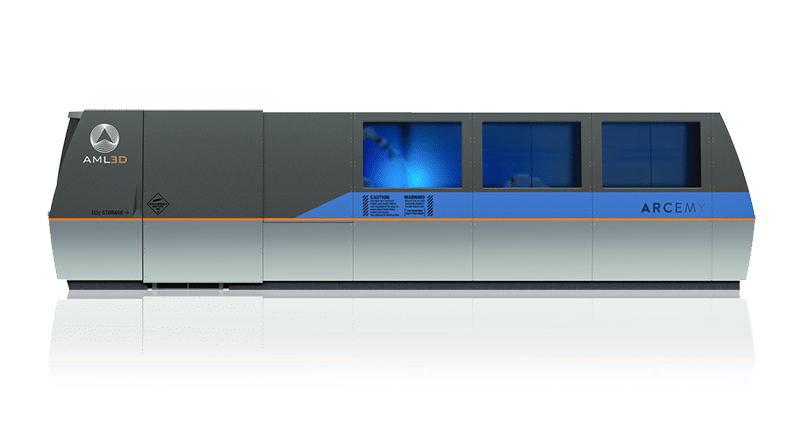
As peças são tradicionalmente forjadas e requerem uma etapa de pós-processamento de tratamento térmico adicional. Esse processo aumenta o lead time total para seis a oito semanas. Esses itens de longo prazo devem ser mantidos em um inventário físico ou substituídos prematuramente.
Usando WAAM, AML3D foi capaz de fabricar os anéis pelo mesmo custo, reduzindo o prazo de entrega para apenas alguns dias. Esta é uma melhoria crítica para os navios que permanecem no cais por um tempo limitado.
Para aumentar ainda mais sua capacidade, a empresa agora planeja lançar uma unidade de produção em Cingapura no curto prazo. Isso é impulsionado pela demanda do hub marítimo de Cingapura, já que o local é um hub estratégico para rotas de transporte comercial.
Ramlab
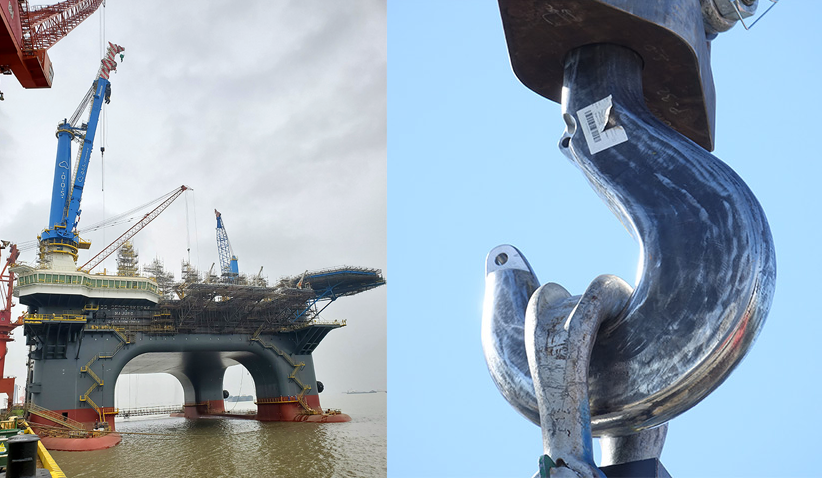
Na mesma linha, o Additive Manufacturing Fieldlab do Porto de Rotterdam (RAMLAB) está usando WAAM para acelerar a produção de peças marítimas. A empresa fez sucesso em 2017 ao imprimir em 3D um protótipo em escala real da hélice de navio aprovada de primeira classe do mundo.
O “WAAMpeller” usa 298 camadas de liga de níquel alumínio e bronze e pesa 400 kg. A parte foi concluída em sete meses - demonstrando o potencial do WAAM para otimizar a produção de futuros componentes de embarcações.
Em 2018, a Ramlab, em colaboração com a Huisman Equipment, iniciou outro projeto para imprimir em 3D um grande offshore gancho da grua, pesando cerca de 1000 kg. A Huisman Equipment levou este projeto ainda mais longe e imprimiu em 3D, certificou e instalou um gancho WAAM de 36.000 kg, projetado especificamente para uso em operações de içamento offshore.
MX3D
Uma das primeiras aplicações que abriu a tecnologia WAAM para o mundo foi uma ponte de aço impressa em 3D, desenvolvida pela start-up holandesa MX3D.
O projeto da ponte, que começou em 2018, levou mais de um ano para ser concluído, mas serviu como uma vitrine do potencial da impressão 3D de metal em grande escala.
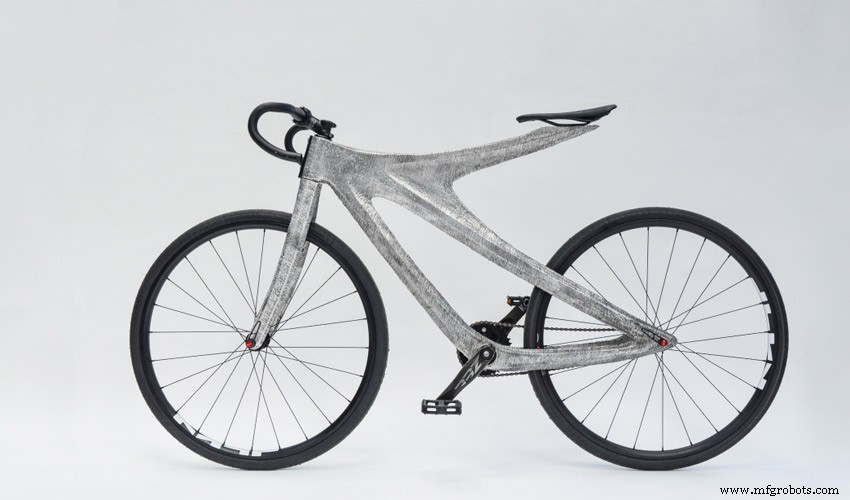
Mais recentemente, a equipe MX3D usou sua tecnologia para imprimir em 3D um quadro de bicicleta de alumínio. A moldura de aparência futurística foi projetada com a ajuda de um software de design generativo e impressa em 3D em duas partes em menos de 24 horas, mostrando a alta velocidade de impressão da tecnologia WAAM do MX3D. O MX3D também desenvolveu uma 'configuração de fixação inteligente', que permitiria que qualquer quadro WAAM personalizado fosse preparado facilmente para andar.
Gefertec
Outro jogador na arena WAAM é a empresa alemã Gefertec. Em 2017, apresentou sua tecnologia de fabricação 3DMP®, que faz parte da série de máquinas GTarc AM da Gefertec.
O maior sistema possui um sistema de 3 eixos para a produção de peças de até 3 m3 com um máximo massa de 3000 kg.
O que é interessante sobre as máquinas da Gefertec é que elas podem ser integradas a um sistema de fresagem. Isso significa que existe a possibilidade de se criar um sistema híbrido, onde a tecnologia 3DMP® é usada para criar uma peça, que é imediatamente finalizada com a usinagem.
Um exemplo do uso da tecnologia Gefertec envolve a impressão 3D de uma tampa de metal do rolamento do conjunto de rodas para uma locomotiva. Este modelo de locomotiva foi colocado em serviço nas décadas de 1960 e 1970, o que significa que pode ser difícil adquirir peças de reposição, que muitas vezes não estão mais disponíveis.
Como resultado, a entrega do componente tradicionalmente demorava até nove meses, e durante esse tempo a locomotiva ficaria fora de serviço, gerando altos custos.
Gefertec's A impressora 3D foi usada para produzir essa peça sobressalente, e o projeto, desde o design inicial até a engenharia reversa e a produção, foi concluído em dois meses. Embora esta seja a primeira produção de uma peça de trabalho, com um processo estabelecido em vigor, é possível reduzir o lead time ainda mais, potencialmente para apenas algumas semanas.
WAAM - a opção viável para manufatura aditiva de metal em grande escala
Com uma tecnologia relativamente nova como WAAM, leva tempo para que os aplicativos se desenvolvam e os benefícios sejam sentidos em toda a indústria. No entanto, vemos a demanda por grandes componentes metálicos impressos em 3D crescendo, sugerindo que a adoção do WAAM será acelerada.
Em última análise, está claro que WAAM está transformando a forma como as grandes peças de metal são produzidas, dando às empresas a opção de um método de produção mais rápido e econômico.
impressao 3D
- Manufatura Aditiva vs Manufatura Subtrativa
- Vantagens da fabricação de aditivos
- Uma pesquisa sobre fluxos de trabalho de manufatura aditiva
- Entrevista com especialista:MELD Manufacturing CEO Nanci Hardwick sobre Preenchimento do Potencial da Fabricação de Aditivos de Metal
- Fabricação de aditivos de metal:5 perguntas a fazer a um fornecedor potencial de pó de metal
- Podcast de fabricação de aditivos, episódio 3
- Podcast de fabricação de aditivos, episódio um
- Fabricação aditiva em aplicativos de consumo
- Manufatura Aditiva em Eletrônicos
- Manufatura Aditiva na Aeroespacial