Uma introdução à fabricação de aditivos metálicos com DMLS
À medida que o desenvolvimento do produto acelera, as regras de design estão mudando. Em nenhum lugar isso é mais aparente do que na manufatura aditiva de metal. A sinterização direta a laser de metal é uma tecnologia de fabricação aditiva de metal com potencial significativo nas indústrias médica e aeroespacial. Mas requer uma nova maneira de pensar, mesmo nas fases iniciais do projeto. De muitas maneiras, representa a transição que os designers devem enfrentar ao procurar novas tecnologias para tornar o design e a fabricação de produtos mais rápidos e inovadores.
Existem vários benefícios do DMLS, principalmente porque os projetistas podem fabricar projetos em formas incomuns, economizando tempo e custos. Como outras tecnologias de impressão 3D, DMLS constrói peças uma camada de cada vez, sinterizando pó de metal atomizado com um laser de alta potência.
Por que usar manufatura aditiva para peças de metal?
Designers e engenheiros de produtos geralmente recorrem ao processo para experimentar formas orgânicas que não podem ser usinadas prontamente. Por exemplo, a capacidade de construir partes do corpo implantáveis que são adaptadas ao destinatário. Tradicionalmente, esses implantes normalmente precisam ser produzidos por meio de um processo de fabricação subtrativo, como uma máquina CNC de 5 eixos. Agora, existe a tecnologia para digitalizar a estrutura óssea real de uma pessoa e imprimir uma substituição direta de DMLS personalizada para seu corpo.
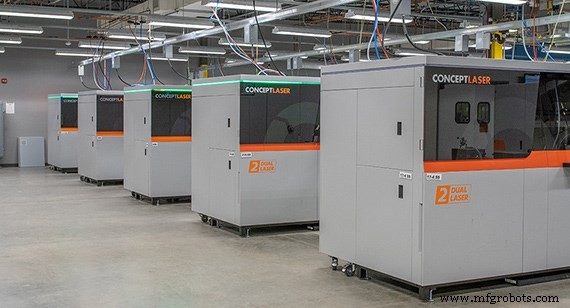
Outra oportunidade são ferramentas cirúrgicas com características ultrafinas e componentes médicos com formas orgânicas. Esses dispositivos podem ser projetados para moldagem por injeção de metal ou fundição, ambas com custos relativamente altos de ferramentas e prazos de entrega que podem durar semanas. Mas com o DMLS, você pode imprimir um protótipo de ferramenta manual cirúrgica com o peso e a força exatos do produto final e colocá-lo nas mãos de um cirurgião em poucos dias. A moldagem por injeção de metal tradicional ainda é valiosa e terá um preço de peça mais baixo em quantidades maiores, mas ainda leva de 6 a 12 semanas em vez de alguns dias.
Aeroespacial é outra indústria que adotou rapidamente a impressão 3D de metal. Materiais frequentemente encontrados no setor aeroespacial, como Inconel e titânio, estão prontamente disponíveis por meio do processo DMLS. A capacidade de fabricar peças metálicas complexas com recursos ocos abre uma gama de possibilidades para designers que tentam componentes leves. Outra vantagem da impressão 3D de peças metálicas é a integração de canais de resfriamento internos dentro de uma peça.
Os atributos de tempo, economia de custos e liberdade de design são essenciais para poder experimentar, projetar rapidamente e ver o que funciona. Mas o DMLS requer uma mudança no pensamento de design. Um dos maiores ajustes é como se adaptar à introdução de tensões internas durante o processo de construção. Começar com um pó de metal à temperatura ambiente, aplicar calor para um derretimento instantâneo, seguido de resfriamento rápido causa estresse em cada camada durante o processo de construção. As tensões internas criadas durante uma construção DMLS fazem com que a peça tente se enrolar para cima enquanto está sendo construída.
Como projetar peças de metal impressas em 3D
Agora que discutimos aplicações e benefícios comuns da tecnologia de impressão 3D em metal, vamos dar uma olhada em algumas diretrizes básicas sobre como projetar recursos em peças de metal impressas em 3D.
Ângulos autoportantes
Um ângulo autoportante descreve o ângulo do recurso em relação à placa de construção. Quanto menor o ângulo, menor a probabilidade de se sustentar. Cada material terá um desempenho ligeiramente diferente, mas a regra geral é evitar projetar um recurso autoportante com menos de 45 graus. Esta dica irá atendê-lo bem em todos os materiais disponíveis. Como você pode ver na figura acima, à medida que o ângulo diminui, o acabamento da superfície da peça se torna mais áspero e, eventualmente, a peça falhará se o ângulo for reduzido demais.
Saliências
As saliências diferem dos ângulos autoportantes porque são mudanças abruptas na geometria de uma peça e não uma inclinação suave. O DMLS é bastante limitado em seu suporte a saliências quando comparado a outras tecnologias de impressão 3D, como estereolitografia e sinterização seletiva a laser. Qualquer saliência maior que 0,020 pol. (0,5 mm) deve ter suporte adicional para evitar danos à peça. Ao projetar saliências, é aconselhável não ultrapassar os limites, pois grandes saliências podem levar à redução de detalhes de peças e, pior ainda, levar à falha de toda a construção.
Canais e Furos
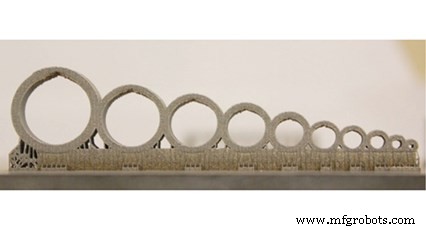
Recomenda-se que os canais não excedam um diâmetro de 0,30 pol. (8 mm). Semelhante a estruturas sem suporte, conforme você excede 0,30 pol., as estruturas voltadas para baixo ficarão distorcidas. Uma dica para contornar essa restrição é evitar projetar canais circulares. Em vez disso, crie canais com formato de gota ou diamante. Os canais que seguem essas formas criarão um acabamento de superfície mais uniforme dentro do canal e permitirão que você maximize o diâmetro do canal.
Pontes
Uma ponte é qualquer superfície plana voltada para baixo que é suportada por 2 ou mais recursos. A distância sem suporte mínima permitida que recomendamos é de 0,080 pol. Em relação a outras tecnologias de impressão 3D, essa distância é relativamente curta devido às tensões do rápido aquecimento e resfriamento. Na figura abaixo, você verá como a ponte puxa as estruturas de suporte à medida que a distância sem suporte aumenta. As peças que excedem esse limite recomendado terão baixa qualidade nas superfícies voltadas para baixo e não serão estruturalmente sólidas.
Pós-processamento de peças de metal impressas em 3D
Depois que uma peça é construída dentro da máquina, várias etapas podem ser tomadas para melhorar suas propriedades mecânicas, a qualidade do acabamento superficial e garantir que os recursos da peça estejam dentro da tolerância.
Tratamento Térmico
Passar as peças por um tratamento térmico é necessário depois que uma peça é construída, pois ajudará a aliviar as tensões internas que se desenvolvem durante o processo de sinterização. As tensões em uma construção irradiam para fora em direção à borda da peça e aumentam com cada camada adicional. Por exemplo, peças com seções transversais grossas terão mais tensão. Há uma variedade de processos de tratamento térmico que podem ser usados para resolver isso:
- Forno a vácuo: As peças são colocadas dentro de um forno selado a vácuo e, em seguida, expostas a um ambiente de alta temperatura, reduzindo assim as tensões internas.
- Prensagem isostática a quente (HIP): Comumente conhecido como HIP, esse processo aplica pressão e calor à peça para reduzir a porosidade e aumentar a densidade.
Usinagem CNC pós-construção
Algumas aplicações podem exigir usinagem adicional após o componente de metal ser impresso em 3D. Isso é útil quando tolerâncias apertadas ou qualidade de acabamento de superfície aprimorada são necessárias em recursos específicos, mas a geometria geral requer manufatura aditiva para ser produzida. Por exemplo, um componente de motor de foguete com canais de resfriamento complexos tem um recurso de acoplamento que requer uma tolerância de +/- 0,001". Em alguns casos, a usinagem CNC pós-construção pode até ser usada para reduzir custos devido a menos lascas no chão e uso mais eficiente de materiais.
Inspeções de qualidade
Muitas vezes, as peças de metal construídas com manufatura aditiva requerem validação dimensional ou uma avaliação da microestrutura do material. Para isso, máquinas de medição por coordenadas (CMM) podem ser usadas para verificar se os recursos da peça estão dentro da tolerância. A tomografia computadorizada ou a varredura de raios-X também podem ser usadas para examinar recursos internos e fornecer uma solução não destrutiva para garantir a integridade estrutural.
Saiba mais sobre a impressão 3D em metal
Se você quiser saber mais sobre DMLS e impressão 3D de metal em geral, temos vários outros recursos disponíveis. Primeiro, comece lendo nosso white paper sobre fabricação de peças de metal. Isso abrange tanto a usinagem quanto a impressão 3D e ajudará você a decidir qual processo será melhor para sua aplicação. E para obter mais detalhes sobre design de peças metálicas para manufatura aditiva, assista ao nosso webinar sob demanda "Projetando para impressão 3D em metal".
Tecnologia industrial
- Fabricação de aditivos líquidos:Construindo objetos 3D com líquido
- Manufatura Aditiva vs Manufatura Subtrativa
- Vantagens da fabricação de aditivos
- Aprimoramento da fabricação de aditivos com engenharia reversa
- O que você pode fazer com a impressão Metal 3D?
- Fabricação de aditivos de metal:O que você precisa saber
- Cinco fatos surpreendentes sobre a fabricação de aditivos de metal
- O que é manufatura aditiva? Comece com a impressão 3D
- Aproveitando a fabricação híbrida com tecnologias de adição e subtração de metal
- Manufatura Aditiva na Aeroespacial