MMF # 3:Dobradiças vivas reforçadas com fibra, fortes o suficiente para ficar em pé
MarkForged Mechanical Features [MMF] é uma série de postagens de blog que detalham as práticas recomendadas para projetar peças de engenharia tradicionais comuns e recursos mecânicos para impressão 3D reforçada composta com impressoras MarkForged.
A fraca resistência da peça vertical é comum entre as impressoras 3D FFF (Fused Filament Fabrication), especialmente quando carregadas sob tensão. Nessas tecnologias de impressão 3D, a ligação ao longo do eixo vertical é mais fraca do que a resistência do material constituinte porque em cada parte há centenas de camadas aderidas umas às outras ao longo do eixo vertical, de modo que a conexão entre cada camada se comporta como uma costura ou um rachar quando carregado. A resistência no plano de uma camada é maior do que a adesão entre camadas porque o plástico em cada camada é depositado como um extrudado contínuo e exibe as propriedades de resistência do próprio material da peça. No Mark Two, essa diferença direcional em forças (ou anisotropia) também ocorre com nosso processo de Fabricação Contínua de Filamento (CFF) - todas as fibras compostas com as quais trabalhamos têm resistência à tração impressionante, mas porque são colocadas ao longo de planos paralelos ao placa de construção, essa força não é traduzida diretamente no eixo vertical. O projeto adequado para peças impressas em 3D envolve adaptar a geometria de um componente de forma que ele seja carregado principalmente no plano horizontal, e as peças criadas por uma impressora Markforged não são exceção. No entanto, com alguns truques de design na manga, você pode contornar esse problema e criar peças impressas em 3D de força industrial no Mark Two com muito mais propriedades isotrópicas.
Se você já manipulou nossos materiais antes, deve ter notado que nosso náilon pode ser bastante flexível por si só. Isso permite o projeto de dobradiças vivas ou seções flexíveis de componentes que podem formar uma junta ou dobradiça sem a necessidade de montagem. Saiba mais sobre como projetar dobradiças vivas e elementos flexurais aqui.
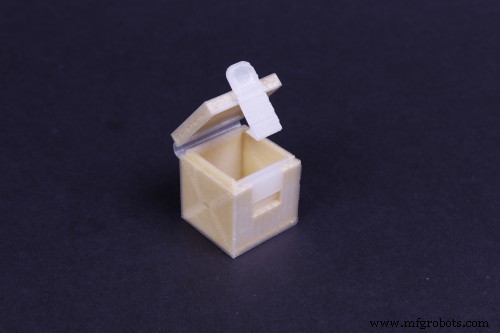
Embora o reforço de fibra na impressora Markforged possa enrijecer um pouco o náilon, você pode usar Kevlar® para criar dobradiças vivas reforçadas com fibra. Nessas estruturas dobráveis impressas em 3D, o náilon fornece a flexibilidade e a fibra fornece a resistência da junta. Com um pouco de origami reforçado com fibra, você pode projetar peças esqueletizadas com o mínimo de material de suporte que são fortes em todas as direções. Aqui está um exemplo:
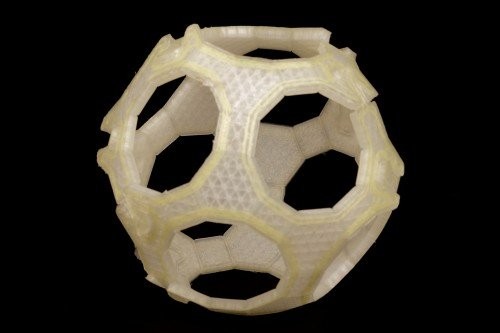
Uma parte como essa teria levado uma quantidade absurda de tempo e material de suporte para ser impressa conforme mostrado, e teria sido muito fraca ao longo do eixo vertical, então eu projetei para imprimi-la assim:
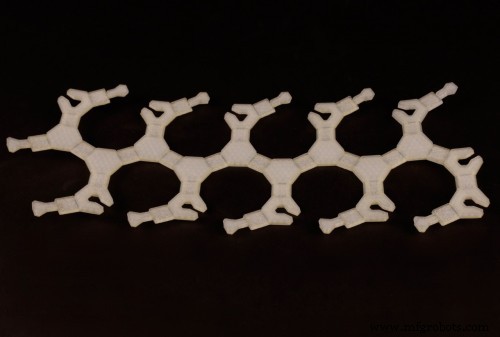
Dando uma olhada no layout de fibra em Eiger, você verá apenas uma camada de Kevlar com padrão concêntrico nesta impressão. Escolhi usar Kevlar porque, embora a fibra de carbono e a fibra de vidro sejam mais fortes, o Kevlar é o mais flexível dos materiais que oferecemos e retém muito de sua resistência à tração, mesmo quando dobrado em ângulos agudos. A fibra de carbono e a fibra de vidro são muito mais rígidas e se quebram em raios de curvatura que o Kevlar pode controlar sem problemas. A única camada de Kevlar fornece força suficiente para esta bola pesar algumas dezenas de libras, mas flexibilidade suficiente para que as articulações se dobrem perfeitamente.
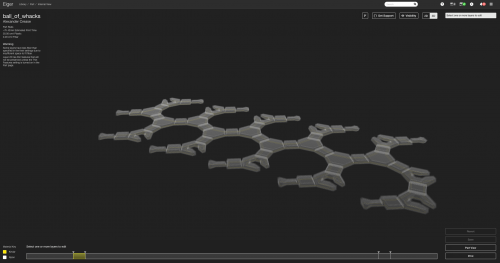
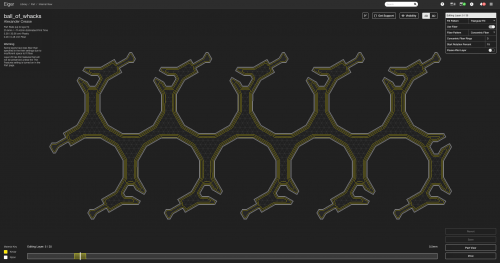
Depois de projetar o poliedro, aumentei as apostas para ver se conseguia imprimir em 3D algo dobrável que fosse forte o suficiente para suportar o peso do meu corpo. Decidi mantê-lo simples e projetei um cubo Kevlar dobrável no Autodesk Fusion 360. Eu precisava de um método para prender as faces do cubo juntas e uma junta para conectar faces que não eram diretamente adjacentes. Comecei modelando quatro faces do cubo, cada uma como um componente separado, para que pudesse manipular no ambiente CAD para simular o comportamento de dobra que desejava para minha junta. Para garantir uma conexão entre cada face, projetei uma junta de encaixe para que, ao dobrar cada face na orientação correta, a face encaixasse no lugar e os encaixes evitassem que o cubo se desdobrasse ou se deformasse.
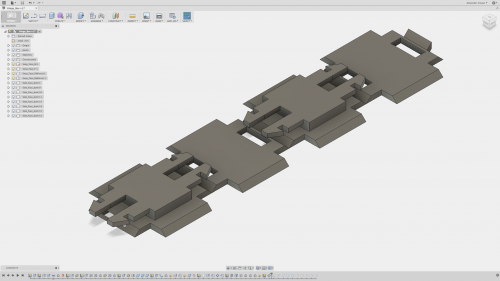
Eu também adicionei uma pequena junta de encaixe e espiga nas bordas que acabaria se conectando assim que a face mais à esquerda se encontrasse com a mais à direita.
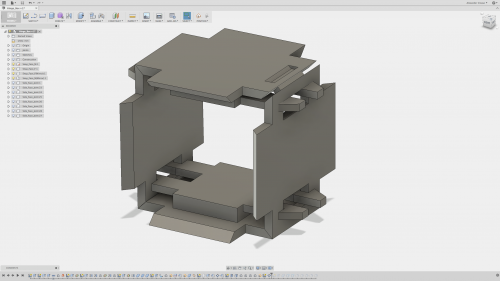
Decidi então tentar algo interessante com os dois lados restantes da caixa - em cada borda restante aberta, projetei uma seção de cada lado. Cada seção tem uma aba de ajuste de torção e um recorte para a aba correspondente na seção adjacente. Depois que a caixa for dobrada, todos eles podem ser encaixados para formar os dois lados restantes. Na imagem abaixo, fiz uma das peças transparente para mostrar os chanfros que adicionei para criar uma junta tipo cauda de andorinha que depende da flexibilidade do material a ser torcido no lugar.
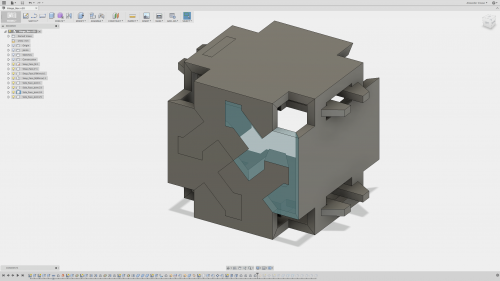
Uma vez que as geometrias de cada face foram gravadas em pedra, eu “desdobrei” o cubo em CAD para que todos os corpos fossem colocados planos na orientação em que eu queria que a peça fosse impressa. Você notará na imagem abaixo que cada um dos componentes se encontram ao longo de suas bordas - eles ainda não estão conectados. Neste ponto, eu ainda precisava combinar isso em uma única parte unificada, adicionando as camadas necessárias para criar a dobradiça viva.
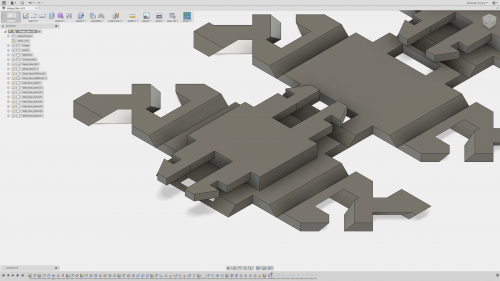
Para fazer isso, capturei os perfis das faces inferiores de cada componente, expulsei-os em 0,875 mm e combinei todos os corpos separados em um. Isso dá espessura à dobradiça viva:a espessura de 0,875 mm adiciona material suficiente para uma única camada de Kevlar caber dentro e criar uma dobradiça viva reforçada com fibra. Observe abaixo que agora cada aresta onde os componentes separados se encontram agora tem espessura.
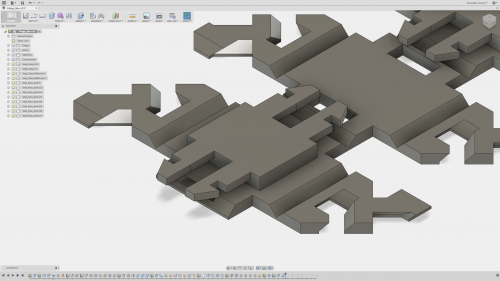
E aqui está a visão completa da peça disposta e pronta para impressão:
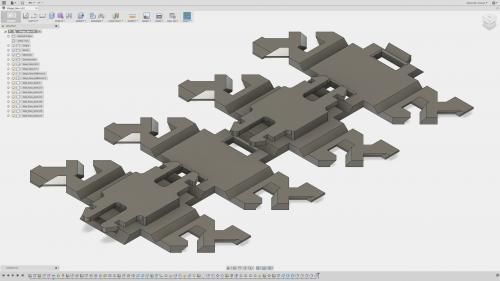
Em Eiger, coloquei anéis concêntricos de fibra na primeira camada de Kevlar para criar e reforçar a junta. Para fortalecer o resto da peça, criei painéis sanduíche começando em cada face acima da primeira camada de Kevlar. Como explicamos em um post anterior, os painéis sanduíche são fundamentais para materiais compostos, pois fornecem alta resistência com baixo peso. Os painéis sanduíche reforçam cada face do cubo para torná-los componentes impressos em 3D fortes e rígidos - tenha em mente que cada face tem apenas cerca de 3 mm de espessura. Eu também fui capaz de encaixar Kevlar nas juntas de encaixe para reforçar suas pequenas características, que discutimos em um post anterior. O GIF abaixo mostra as primeiras camadas, incluindo a camada de dobradiça viva reforçada com Kevlar (camada 5) e as camadas inferiores do painel sanduíche (camadas 6-8).
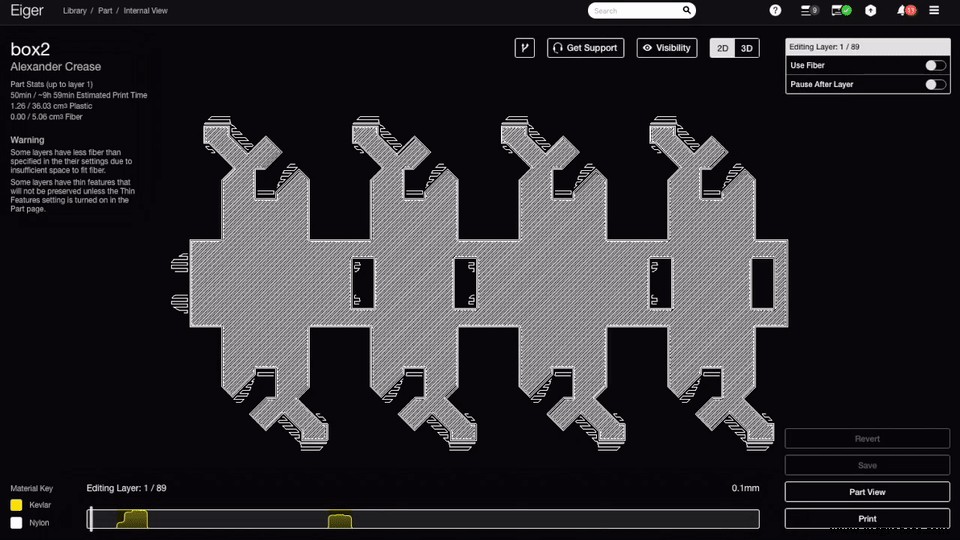
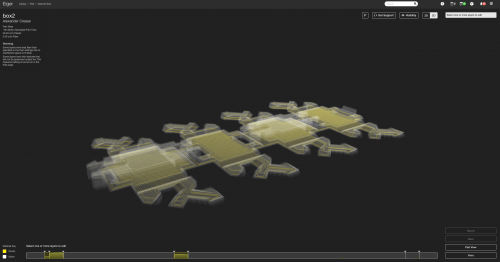
Depois de impresso, juntei tudo e torci nas juntas do painel lateral, e fiz um cubo dobrável impresso em 3D com algum reforço de Kevlar!
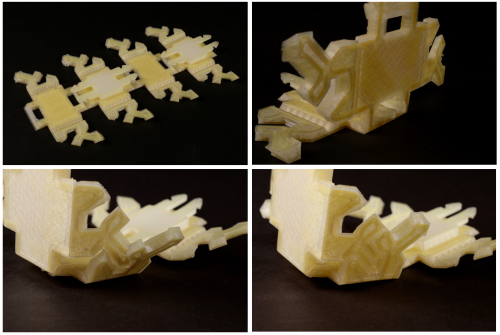
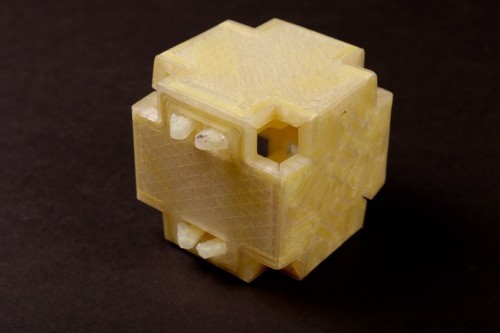
Cada lado do cubo fornece reforço substancial em tração e flexão, tornando o cubo em sua totalidade muito difícil de comprimir e isométrico ao longo dos três eixos principais. Consegui colocar todo o peso de meu corpo nele (cerca de 130 libras), sem nem mesmo uma sugestão de deformação. Eu sou uma pessoa bastante pequena, então fiz um teste muito mais rigoroso. Não obtive leituras muito boas, mas estimo que segurou cerca de 300-400 libras antes de falhar. Aqui está o que aconteceu:
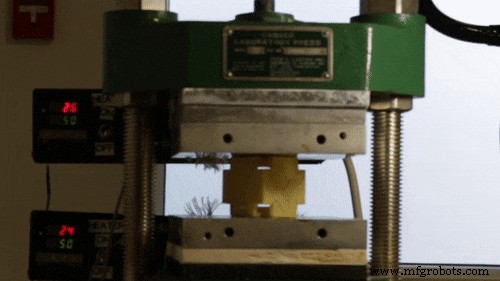
Então, depois de algumas centenas de libras, a coisa mais surpreendente foi que a peça não quebrou de verdade, todas as juntas apenas se separaram e o cubo inteiro se achatou, então, com um pouco de endireitamento, ele pode ser trazido de volta à sua forma original. Portanto, ao criar estruturas dobráveis com dobradiças vivas reforçadas com fibra, você pode fazer algumas peças impressas em 3D realmente fortes em todas as direções.
Quer imprimir você mesmo? Baixe o arquivo STL ou .mfp!
Quer testar a força por si mesmo? Peça uma peça de amostra grátis aqui!
impressao 3D
- O que são dobradiças duplas?
- 5 Benefícios de escolher dobradiças de alumínio
- Uma introdução às dobradiças contínuas
- Os benefícios de dobradiças vivas
- A tecnologia laser existente é forte o suficiente para atrair alienígenas a 20.000 anos-luz de distância
- Meu primeiro roteador mini CNC personalizado — deve ser forte o suficiente
- Ferro-Titanit® U
- DIFENDER 400
- Entendendo a resistência à compressão
- Como projetar dobradiças vivas impressas em 3D