Briquete de carvão
Antecedentes
O carvão vegetal é um combustível desejável porque produz um fogo quente, duradouro e virtualmente sem fumaça. Combinado com outros materiais e formado em pedaços uniformes chamados briquetes, é popularmente usado para cozinhar ao ar livre nos Estados Unidos. De acordo com a associação da indústria de churrasco, os americanos compraram 883.748 toneladas de briquetes de carvão em 1997.
O carvão vegetal básico é produzido pela queima de um material rico em carbono, como a madeira, em uma atmosfera com baixo teor de oxigênio. Esse processo elimina a umidade e os gases voláteis que estavam presentes no combustível original. O material carbonizado resultante não apenas queima por mais tempo e de forma mais constante do que a madeira inteira, mas é muito mais leve (um quinto a um terço de seu peso original).
História
O carvão vegetal é fabricado desde os tempos pré-históricos. Há cerca de 5.300 anos, um infeliz viajante morreu nos Alpes tiroleses. Recentemente, quando seu corpo foi recuperado de uma geleira, os cientistas descobriram que ele carregava uma pequena caixa contendo pedaços de madeira carbonizada embrulhados em folhas de bordo. O homem não tinha ferramentas para iniciar o fogo, como pederneira, então parece que ele pode ter carregado carvão em brasa.
Há cerca de 6.000 anos, o carvão era o combustível preferido para fundir cobre. Após a invenção do alto-forno por volta de 1400 A.D. , o carvão foi amplamente usado em toda a Europa para fundição de ferro. No século XVIII, o esgotamento da floresta levou à preferência pelo coque (uma forma de carvão vegetal à base de carvão) como combustível alternativo.
As florestas abundantes no leste dos Estados Unidos tornaram o carvão um combustível popular, especialmente para a ferraria. Também foi usado no oeste dos Estados Unidos até o final dos anos 1800 para extrair prata do minério, para abastecer ferrovias e para aquecimento residencial e comercial.
A transição do carvão vegetal de um combustível para aquecimento e industrial para um material de cozinha recreativo ocorreu por volta de 1920, quando Henry Ford inventou o briquete de carvão. Ford não só teve sucesso em fazer uso lucrativo da serragem e restos de madeira gerados em sua fábrica de automóveis, mas seu negócio secundário também incentivou o uso recreativo de carros para passeios de piquenique. As churrasqueiras e o Ford Charcoal foram vendidos nas concessionárias de automóveis da empresa, algumas das quais dedicaram metade de seu espaço ao negócio de suprimentos de cozinha.
Historicamente, o carvão era produzido empilhando madeira em um monte em forma de cone e cobrindo-o com sujeira, grama ou cinzas, deixando orifícios de entrada de ar ao redor da parte inferior da pilha e uma chaminé no topo. A madeira foi incendiada e queimada lentamente; em seguida, os orifícios de ar foram cobertos para que a pilha esfriasse lentamente. Em tempos mais modernos, a cava de carvão de uso único foi substituída por um forno de pedra, tijolo ou concreto que suportaria 25-75 cordões de madeira (1 cordão =4 pés x 4 pés x 8 pés). Um lote grande pode queimar de três a quatro semanas e levar de sete a dez dias para esfriar.
Este método de produção de carvão gera uma quantidade significativa de fumaça. Na verdade, as mudanças na cor das transições do sinal de fumaça para diferentes estágios do processo. Inicialmente, sua tonalidade esbranquiçada indica a presença de vapor, pois os vapores de água são expelidos da madeira. Como outros componentes de madeira, como
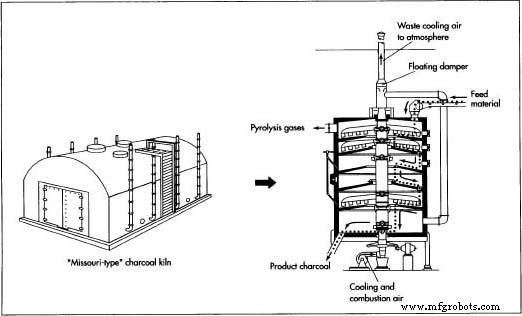
Um método alternativo de produção de carvão foi desenvolvido no início dos anos 1900 por Orin Stafford, que então ajudou Henry Ford a estabelecer seu negócio de briquetes. Chamado de método de retorta, envolve a passagem da lenha por uma série de lareiras ou fornos. É um processo contínuo em que a madeira entra constantemente em uma extremidade da fornalha e o material carbonizado sai da outra; em contraste, o processo de forno tradicional queima madeira em lotes discretos. Praticamente nenhuma fumaça visível é emitida de uma retorta, porque o nível constante de saída pode ser tratado com eficácia com dispositivos de controle de emissão, como pós-combustores.
Matérias-primas
Os briquetes de carvão são feitos de dois ingredientes principais (compreendendo cerca de 90% do produto final) e vários ingredientes menores. Um dos principais ingredientes, conhecido como carvão, é basicamente o carvão vegetal tradicional, conforme descrito acima. É responsável pela capacidade do briquete de acender facilmente e de produzir o desejado sabor de fumaça de lenha. A matéria-prima mais desejável para esse componente são as madeiras nobres como a faia, a bétula, o bordo duro, a nogueira e o carvalho. Alguns fabricantes também usam madeiras macias, como o pinho, ou outros materiais orgânicos, como caroços de frutas e cascas de nozes.
O outro ingrediente principal, usado para produzir um fogo de alta temperatura e longa duração, é o carvão. Vários tipos de carvão podem ser usados, variando de linhita sub-betuminosa a antracita.
Ingredientes menores incluem um agente de ligação (normalmente amido feito de milho, milo ou trigo), um acelerador (como nitrato) e um agente de branqueamento de cinzas (como cal) para que o churrasco de quintal saiba quando os briquetes estão prontos para cozinhe.
O processo de fabricação
A primeira etapa do processo de fabricação é carbonizar a madeira. Alguns fabricantes usam o método do forno (lote), enquanto outros usam o método da retorta (contínua).
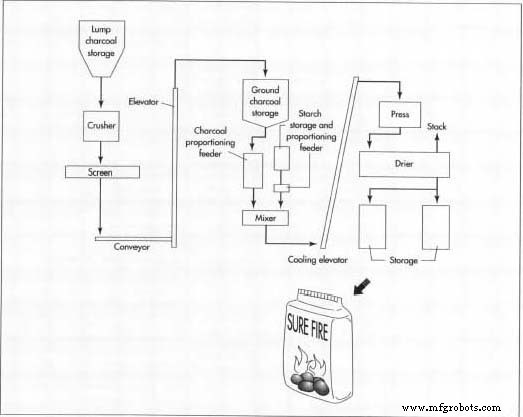
Queimando a madeira
- 1 (Processo em lote) Leva um ou dois dias para carregar um forno de concreto de tamanho típico com cerca de 50 cabos de madeira. Quando o fogo é iniciado, as portas de entrada de ar e saídas de ar são totalmente abertas para atrair oxigênio suficiente para produzir um fogo quente. Durante o período de queima de uma semana, as portas e aberturas são ajustadas para manter a temperatura entre cerca de 840-950 ° F (450-510 ° C). No final do período de queima desejado, as portas de entrada de ar são fechadas; as aberturas de exaustão são seladas uma ou duas horas depois, após o término da fumaça, para evitar o aumento de pressão dentro do forno. Após um período de resfriamento de duas semanas, o forno é esvaziado e a madeira carbonizada (carvão) é pulverizada.
- 2 (Processo contínuo) A madeira é dimensionada (quebrada em pedaços de dimensões adequadas) em um moinho de martelos. Um tamanho de partícula de cerca de 0,1 pol. (3 mm) é comum, embora o tamanho exato dependa do tipo de madeira sendo usado (por exemplo, casca, serragem seca, madeira úmida). A madeira então passa por um grande secador de tambor que reduz seu conteúdo de umidade pela metade (para aproximadamente 25%). Em seguida, ele é alimentado no topo do forno de soleira múltipla (retorta).
Externamente, a retorta parece um silo de aço, com 40-50 pés (12,2-15,2 m) de altura e 20-30 pés (6,1-9,14 m) de diâmetro. No interior, contém uma pilha de lareiras (três a seis, dependendo da capacidade de produção desejada). A câmara superior é a lareira de temperatura mais baixa, da ordem de 525 ° F (275 ° C), enquanto a câmara inferior queima a cerca de 1.200 ° F (650 ° C). O calor externo, de queimadores a óleo ou gás, é necessário apenas nos estágios inicial e final da fornalha; nos níveis intermediários, os gases de madeira em evolução queimam e fornecem calor suficiente para manter os níveis de temperatura desejados.
Dentro de cada câmara, a madeira é agitada por braços de turba que se estendem de um eixo central que corre verticalmente por toda a retorta. Este processo de agitação lenta (1-2 rpm) garante uma combustão uniforme e move o material através da retorta. Em níveis alternados, os braços da turba empurram a madeira em chamas em direção a um buraco ao redor do poço central ou em direção a aberturas ao redor da borda externa do piso, de forma que o material possa cair para o próximo nível inferior. Conforme o carvão em combustão sai da câmara final, ele é extinto com um spray de água fria. Ele pode então ser usado imediatamente ou pode ser armazenado em um silo até que seja necessário.
Uma retorta típica pode produzir aproximadamente 5.500 lb (2,5 toneladas métricas) de carvão por hora.
Carbonizando o carvão
- 3 Graus inferiores de carvão também podem ser carbonizados para uso em carvão vegetal. O carvão triturado é primeiro seco e depois aquecido a cerca de 590 ° C (1.100 ° F) para eliminar os componentes voláteis. Depois de ser resfriado a ar, ele é armazenado até que seja necessário.
Briquetagem
- 4 O carvão e os ingredientes menores, como o aglutinante de amido, são alimentados nas proporções adequadas em um misturador de pás, onde são bem misturados. Neste ponto, o material tem cerca de 35% de teor de umidade, dando-lhe uma consistência parecida com a do solo úmido.
- 5 O material misturado é colocado em uma prensa que consiste em dois rolos opostos contendo indentações do tamanho de um briquete. Por causa do teor de umidade, do agente de ligação, da temperatura (cerca de 105 ° F ou 40 ° C) e da pressão dos rolos, os briquetes mantêm sua forma conforme caem do fundo da prensa.
- 6 Os briquetes caem em um transportador, que os carrega por um secador de passagem única que os aquece a cerca de 275 ° F (135 ° C) por três a quatro horas, reduzindo seu teor de umidade para cerca de 5%. Os briquetes podem ser produzidos a uma taxa de 2.200-20.000 lb (1-9 toneladas métricas) por hora. Os briquetes são ensacados imediatamente ou armazenados em silos para aguardar a próxima execução de embalagem programada.
Saco
- 7 Se briquetes de "luz instantânea" estão sendo produzidos, um solvente de hidrocarboneto é atomizado e pulverizado sobre os briquetes antes do ensacamento.
- 8 Os briquetes de carvão são embalados em uma variedade de tamanhos de saco, variando de 4-24 lb. Alguns pacotes pequenos e convenientes são feitos para que o consumidor possa simplesmente acender o fogo em todo o saco sem primeiro remover os briquetes.
Subprodutos / resíduos
Durante o final do século XIX e início do século XX, a recuperação de ácido acético e metanol como subprodutos do processo de carbonização da madeira tornou-se tão importante que o próprio carvão se tornou essencialmente o subproduto. Após o desenvolvimento de técnicas mais eficientes e menos dispendiosas para sintetizar ácido acético e metanol, a produção de carvão diminuiu significativamente até ser revitalizada pelo desenvolvimento de briquetes para culinária recreativa.
O processo em lote para carbonizar madeira produz quantidades significativas de fumaça particulateladen. Ajustar as saídas de exaustão com pós-combustores pode reduzir as emissões em até 85%, mas devido ao custo relativamente alto do tratamento, ele não é comumente usado.
O nível de operação mais constante das retortas não apenas torna mais fácil controlar suas emissões com pós-combustores, mas também permite o uso produtivo de gases de escape combustíveis. Por exemplo, esses gases podem ser usados para abastecer secadores de madeira e secadores de briquete ou para produzir vapor e eletricidade.
A produção de briquetes de carvão vegetal é ecologicamente correta de outra forma:o maior fabricante de briquetes dos Estados Unidos usa apenas resíduos para seu abastecimento de madeira. Lascas de madeira, serragem e cascas de fabricantes de paletes, fabricantes de pisos e serrarias são convertidas de pilhas de resíduos em briquetes úteis.
O Futuro
Os métodos de produção de carvão e briquete mudaram pouco nas últimas décadas. A inovação mais significativa nos últimos anos foi o desenvolvimento de briquetes de "luz instantânea". Uma nova versão lançada em 1998 estará pronta para cozinhar em cerca de 10 minutos.
Processo de manufatura