Sistema de corte pré-impregnado reduz o desperdício, acelera a montagem do jato executivo suíço
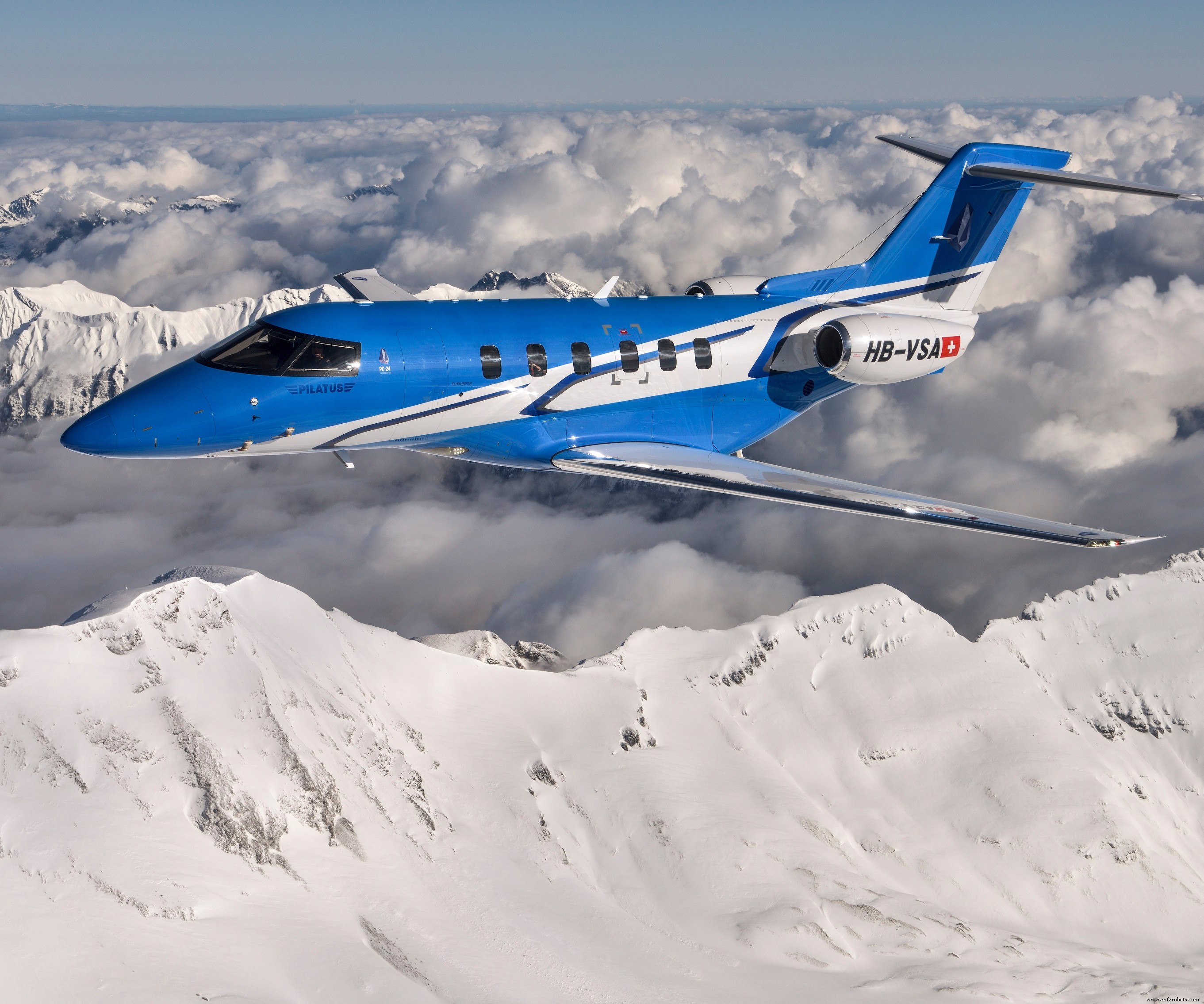
Fonte | Zünd
Graças aos componentes de carbono e fibra de vidro, o PC-24 o jato executivo, fabricado pela Pilatus Aircraft AG (Stans, Suíça), possui um peso base de apenas 5,3 toneladas (menos de 12.000 libras), o que o ajuda a decolar e pousar em pistas curtas, não pavimentadas ou de cascalho normalmente reservadas para aviões turboélice. Na verdade, o PC-24 é capaz de decolar em uma pista de até 890 metros (2.920 pés) e requer apenas 720 metros (2.362,2 pés) para o pouso.
A Pilatus começou a usar peças de fibra de carbono no início de sua história de fabricação de aviões, começando com seus primeiros componentes de plástico reforçado com fibra de carbono (CFRP) e plástico reforçado com fibra de vidro (GFRP) para o PC-6 Aeronave universal de metal Porter. Os poucos componentes compostos no PC-6 , que decolou pela primeira vez em 1959 e passou por uma tiragem de produção de cerca de 500 aviões antes de ser substituído por seu sucessor, o PC-12 , foram colocados à mão. PC-6 a montagem, portanto, exigia uma força de trabalho experiente e altas tolerâncias para as peças.
Em contraste, o tipo de aeronave mais recente da empresa, o PC-24 , consiste em muitas peças, muitas delas fresadas com tolerâncias na faixa de Mμ. O PC-24 usa compósitos principalmente para revestimento interno e externo. As carcaças do motor e pontas das asas também são feitas de fibra de carbono, assim como as portas do trem de pouso, dutos de ar, vários tubos, tampas e bordas de fuga nas asas.
Não só o PC-24 incluem mais componentes compostos do que o PC-6 fez em 1959, mas a montagem é muito mais rápida agora, possibilitada, diz Pilatus, por causa dos avanços nas tecnologias de produção. Para isso, são fundamentais a redução permanente de custos, a otimização da produtividade e a capacidade de implementar tecnologias de produção modernas.
Os sistemas de corte digital pré-impregnado fazem parte dessa tendência. A Pilatus confia nos sistemas de corte Zünd (Altstätten, Suíça) há anos e, em 2019, adicionou um sistema de corte pré-impregnado Zünd G3 L-2500. O sistema G3 corta uma única camada de materiais para os respectivos componentes em um processo amplamente automatizado e, a seguir, rotula as peças cortadas com um módulo de jato de tinta integrado.
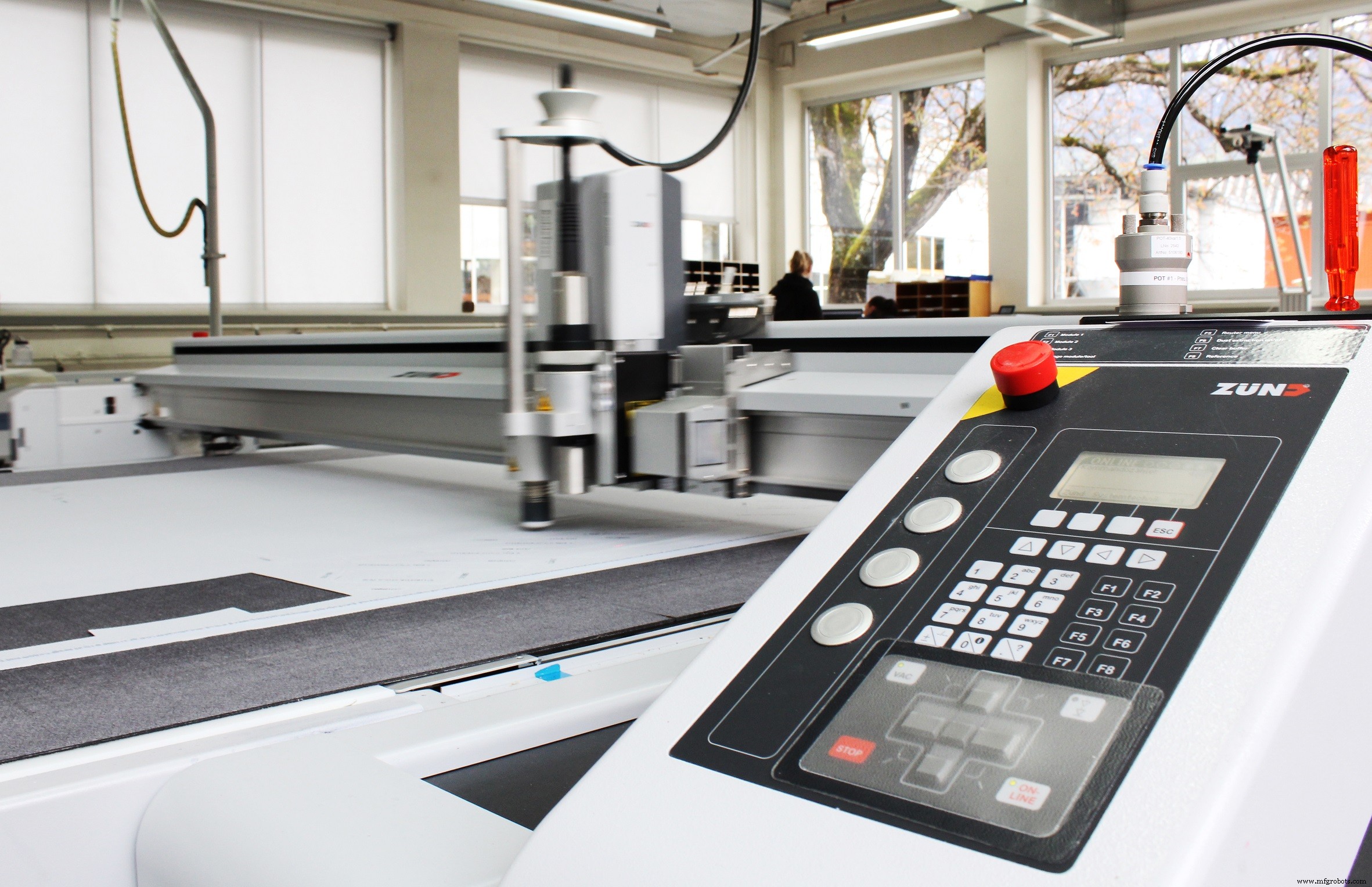
Fonte | Zünd
A Pilatus processa cerca de cinco rolos de pré-impregnado por dia (aproximadamente 90 metros quadrados), ou cerca de 90.000 metros quadrados por ano, com a taxa de consumo aumentando continuamente à medida que mais e mais componentes CFRP e GFRP são usados nos aviões da empresa. A Pilatus confiou no corte digital da Zünd por mais de 15 anos, começando com uma fresa da série PN. O aumento da demanda por componentes de fibra de carbono começou a exceder a capacidade, o que levou ao acréscimo de um Zünd G3 L-2500 em 2019. Depois de concluído o corte, as peças são equipadas e colocadas em armazenamento refrigerado até o processamento posterior. As estruturas compostas Pilatus podem consistir em até 350 camadas de pré-impregnado.
Outro fator para o sucesso da Pilatus foi o foco no aumento da produtividade. De acordo com Patrick Rohrer, gerente de projeto de aquisição de sistema da Pilatus, “Ao lidar com materiais de alto custo, como carbono ou fibra de vidro, a eficiência e a otimização do material são sempre uma preocupação. Trabalhamos constantemente para aumentar a utilização e, assim, reduzir o desperdício - principalmente porque ainda temos poucas opções de reciclagem ”.
A empresa diz que reduziu as taxas de desperdício de 30% para 20% e cita os recursos de aproveitamento eficientes do software Cut Center - ZCC da Zünd como um fator importante para esse sucesso. As diferentes camadas de uma peça são aninhadas estaticamente, o que significa que as camadas individuais de uma peça são aninhadas na quantidade solicitada de acordo com o pedido . O aninhamento dinâmico, que ocorre quando camadas individuais de peças de vários pedidos são aninhadas e combinadas em um único arquivo de corte, também pode ser usado sempre que fizer sentido. Isso, diz Zünd, aumenta ainda mais o grau de utilização da matéria-prima.
fibra
- Como funciona o corte por jato de água?
- 5 Benefícios do corte a jato de água
- Jato de água vs Corte a laser:Qual é a diferença?
- Como otimizar a máquina de corte a jato de água de forma eficiente?
- O que considerar antes de comprar uma máquina de corte por jato de água abrasiva?
- Solução reduz erupções do sistema para Solvay
- Confiabilidade reduz perda de tempo, talento e recursos
- Usinagem e corte com jato de água abrasivo
- Automatizar seu sistema de corte a laser é adequado para sua aplicação?
- ICS destaque no Hartford Business Journal