Fabricação de chips nanofluídicos de polidimetilsiloxano sob o processo de nanomilling baseado em ponta de AFM
Resumo
No campo da pesquisa atual, os dispositivos nanofluídicos baseados em polidimetilsiloxano (PDMS) são amplamente usados em aplicações médicas, químicas e biológicas. No presente trabalho, uma nova técnica de nanomilling (consistindo em um sistema AFM e um atuador piezoelétrico) foi proposta para fabricar nanocanais (com tamanhos controláveis) em chips PDMS, e o tamanho do nanocanal foi controlado pela tensão de condução e frequência introduzida no atuador piezoelétrico . Além disso, moldes de microcanais e nanocanais foram respectivamente fabricados por litografia UV e nanomilling à base de ponta de AFM e, finalmente, placas de PDMS com micro / nanocanais foram obtidas por processo de transferência. As influências da razão de peso de PDMS no tamanho do nanocanal também foram investigadas. O processo de colagem de placas de microcanais e nanocanais foi conduzido em um sistema de alinhamento caseiro composto por um microscópio óptico monocular e estágios de precisão. Além disso, os efeitos do tamanho do nanocanal nas características elétricas da solução de KCl (concentração de 1 mM) foram analisados. Portanto, pode-se concluir que dispositivos nanofluídicos de PDMS com múltiplos nanocanais de profundidade sub-100 nm podem ser fabricados de forma eficiente e econômica pelo método proposto.
Histórico
Devido aos seus consideráveis potenciais nos campos químico, médico e biológico, os sistemas micro / nanofluídicos são amplamente utilizados na análise de DNA [1,2,3,4], separação de células [5], pesquisa de proteínas [6,7,8], segurança alimentar [9] e monitoramento ambiental [10]. Com o rápido desenvolvimento da tecnologia de nanofabricação, a demanda por dispositivos nanofluídicos com tamanho unidimensional menor que 100 nm está aumentando continuamente [11]. Os chips nanofluídicos também podem ser usados com eficácia para detecção de vírus [12], manipulação de nanopartículas [13] e estudo de difusão de íons [14]. No entanto, a eficiência de detecção e a sensibilidade dos chips nanofluídicos dependem das dimensões de recursos e da distribuição dos nanocanais. É indispensável controlar com precisão as dimensões dos recursos dos nanocanais para a detecção livre de marcadores baseada em nanofluidos. Como fabricar nanocanais com dimensões e distribuição de recursos controláveis ainda é um desafio para a aplicação no campo nanofluídico.
Até agora, existem vários métodos que podem ser utilizados para a fabricação de chips nanofluídicos. A corrosão iônica reativa [15], fotolitografia convencional [16], processamento de feixe de alta energia [17], litografia de interferência [18], nanoimpressão [19] e tecnologias de gravação a quente [20, 21] são mais comumente usadas para a fabricação de dispositivos nanofluídicos; no entanto, todos esses métodos manifestam suas próprias limitações. A corrosão iônica reativa e a fotolitografia convencional são os métodos principais para a fabricação de canais micro / nanofluídicos. No entanto, as dimensões laterais dos canais fabricados dependem do comprimento de onda da luz incidente, portanto, as larguras dos canais produzidos são frequentemente encontradas na escala micrométrica, não em nanoescala [22]. Além disso, é inconveniente trocar as fotomáscaras quando se fabricam micro / nanoestruturas com características diferentes. A litografia por feixe de íons focados (FIB) e a litografia por feixe de elétrons (EBL) são métodos de processamento de feixe de alta energia, que podem facilmente fabricar chips nanofluídicos de alta precisão com nanocanais sub-100 nm. No entanto, o investimento para a instalação de fabricação é extremamente alto e os rígidos requisitos ambientais são necessários [23]. A litografia de interferência (IL) é adequada para a fabricação de estruturas periódicas simples sobre uma grande área; no entanto, não é adequado para usinar um único nanocanal [24, 25]. A resolução de processamento da nanoimpressão depende das propriedades do template, a questão crucial para esta abordagem é como fabricar o template com nanoestruturas de alta precisão [26]. Além disso, a moldagem sacrificial e o método baseado em ranger também são adotados para fabricar dispositivos em micro / nanoescala [27, 28]; no entanto, o controle preciso do tamanho do nanocanal é muito difícil nessas abordagens. Assim, uma abordagem de fabricação mais viável com as propriedades de alta precisão de usinagem, facilidade de uso, ampla faixa de processamento e baixa exigência de ambiente é exigida para a fabricação de dispositivos nanofluídicos.
Nos últimos anos, devido às suas altas precisões de usinagem, métodos de usinagem de ultraprecisão, como nanomilling, retificação de precisão e torneamento de ultraprecisão, são amplamente utilizados na fabricação de micro / nanoestruturas [29,30,31,32]. Além disso, desde a invenção do microscópio de força atômica (AFM) em 1986, a nanofabricação baseada em ponta de AFM é um método poderoso para preparar nanoestruturas [33]. O nanoscratching baseado em ponta tradicional possui algumas limitações, como largura de usinagem limitada e baixa eficiência de fabricação. A largura do nanocanal fabricado por esta abordagem depende da geometria da ponta do AFM, o que significa que os nanocanais com largura controlável são inacessíveis. Além disso, a eficiência de fabricação do processo tradicional de nano-arranhões com base na ponta é relativamente baixa, especialmente para o caso de empregar uma alimentação no processo de usinagem para aumentar a profundidade e a largura da nanoestrutura obtida. Devido às suas vantagens significativas, como tamanho de usinagem controlável e alta eficiência de fabricação, a nanomilling com ponta é amplamente adotada para fabricar nanocanais. Gozen et al. [34, 35] fabricou nanoestruturas em polimetil metacrilato (PMMA) através de um processo de nanomilling. Zhang et al. [36,37,38] prepararam nanoestruturas tridimensionais usando AFM e estudaram os efeitos de diferentes parâmetros de usinagem. Park et al. [39] investigaram o mecanismo do processo de nanomáquina e descobriram que as intensidades da força de corte foram significativamente reduzidas; entretanto, no sistema proposto, as instalações de usinagem foram consideradas relativamente complicadas e o processo de remoção de material não foi investigado em detalhes. A relação entre os parâmetros de usinagem, incluindo a frequência de condução e voltagem e as dimensões de recursos do nanocanal obtido, não foi estudada. Além disso, seu trabalho não se concentrou na aplicação dos nanocanais fabricados. Portanto, mais trabalho é necessário para explorar o escopo de aplicação desta abordagem de nanomilling baseada em ponta de AFM. O policarbonato (PC), por sua excelente usinabilidade, é comumente utilizado para nanofabricação [40]; no entanto, raramente é selecionado para fabricar chips nanofluídicos. Em contraste, o polidimetilsiloxano (PDMS) é amplamente utilizado para processar chips microfluídicos e nanofluídicos. Mata et al. [41] estudaram as influências da razão de peso do PDMS na tensão de tração. Park et al. [42] desenvolveram um novo método para melhorar a rigidez do PDMS. As aplicações de chips nanofluídicos em campo de teste sem etiqueta dependem principalmente da condutividade elétrica dos nanocanais [43], portanto, os resultados da medição são frequentemente afetados pelos tamanhos dimensionais dos nanocanais [44].
Portanto, a fim de superar as desvantagens do processo de raspagem baseado em ponta tradicional, a abordagem de nanomilling é empregada para conduzir o processo de fabricação de nanocanal neste estudo. Além disso, a folha de PC foi selecionada como a amostra experimental para mitigar o desgaste da ponta, bem como para reduzir o custo de fabricação. Além disso, o tamanho do nanocanal na folha de PC foi controlado pela voltagem de condução e frequência introduzida no atuador piezoelétrico. As influências da razão de peso de PDMS no tamanho do nanocanal também foram investigadas. Além disso, com o objetivo de verificar os efeitos de diferentes tamanhos dimensionais na condutividade elétrica de nanocanais, o teste de medição de corrente foi realizado em solução de KCl.
Métodos
Configuração do sistema de nanomilling
O sistema de nanomilling baseado em ponta de AFM proposto consistia em um AFM comercial (Dimension Icon, Bruker Company, Germany) e um atuador piezoelétrico (P-122.01, PI Company, Germany) (Fig. 1a). As faixas de deslocamento do atuador piezoelétrico nas direções xey foram limitadas a 1 μm. Além disso, o atuador piezoelétrico foi acionado por sinais sinusoidais com tensões apropriadas (gerados a partir de um dispositivo gerador de sinal comercial (AFG1022; Tektronix, Inc., EUA)) sob a amplificação de um amplificador de sinal (PZD350A; TREK, Inc., EUA). Uma folha de PC foi fixada no suporte artesanal (feito de resina epóxi) por um parafuso de fixação. A operação de nanomáquina foi realizada usando uma ponta revestida de diamante piramidal retangular de espessura de 100 nm (DT-NCLR, Nanosensors, Suíça). O cantilever da ponta (constante de mola normal de 68 N / m) foi feito de silício (Fig. 1b), e uma ponta de silicone (raio de 10 nm) (TESPA, Bruker Company, Alemanha) foi empregada para medir as ranhuras após usinagem.
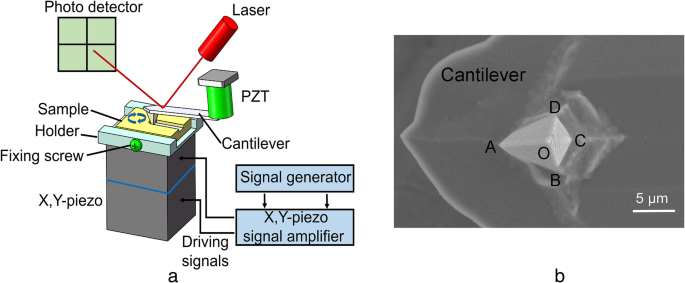
a Diagrama esquemático do sistema de nanomilling. b Micrografia SEM da ponta AFM revestida com diamante
Fabricação de moldes de nanocanais e microcanais
A rota de fabricação de nanocanais em um chip PDMS é exibida na Fig. 2. O sistema AFM e o atuador piezoelétrico foram empregados para fabricar moldes de nanocanais (com tamanhos controláveis) em folha de PC. A folha de PC (peso molecular de 35.000) com tamanho de 15 mm x 12 mm x 1 mm foi adquirida na Goodfellow. A média e o desvio padrão da rugosidade da superfície (Ra) da folha de PC foram medidos como 0,6 nm e 0,2 nm, respectivamente (esses valores foram obtidos por varredura de uma área de 50 μm x 50 μm da amostra no modo de toque AFM). Para gerar um movimento circular, o atuador piezoelétrico foi acionado por sinais senoidais com 90 ° de diferença de fase nas direções x e y. As larguras dos nanocanais usinados dependiam da amplitude do movimento circular gerado. A faixa de tensão de acionamento fornecida ao atuador piezoelétrico foi definida de 30 V a 150 V com um espaçamento de 30 V e, além disso, duas frequências de mergulho de 100 Hz e 1500 Hz foram selecionadas. Durante a usinagem ao longo da direção da borda para a frente, os materiais são expelidos em formação de empilhamento e muitas vezes são encontrados uniformemente distribuídos em ambos os lados de um nanocanal [45] e ajuda a evitar qualquer vazamento de chips nanofluídicos durante o processo de ligação; portanto, a direção de usinagem edge-forward foi selecionada no presente estudo. Nanocanais de 80 μm de comprimento foram fabricados usando o módulo Nanoman do sistema AFM. Qualquer processo de usinagem é afetado pelo valor do avanço; portanto, a fim de eliminar essa influência, a taxa de alimentação deve ser variada com a freqüência de condução. No presente estudo, o valor de alimentação foi definido como 10 nm, e as taxas de alimentação para as frequências de 100 Hz e 1500 Hz foram calculadas como 1 μm / se 15 μm / s, respectivamente. A carga normal da ponta dependia da tensão de saída gerada pelo fotodetector sensível à posição (PSD); assim, diferentes cargas normais usadas em nosso estudo foram alcançadas pelo ajuste de uma tensão relativa (ponto de ajuste). De acordo com nosso trabalho anterior [46], a carga normal de usinagem foi calculada pela Eq. (1) e a sensibilidade foi medida a partir da inclinação da curva força-distância obtida [47].
$$ {F} _ {\ mathrm {N}} ={V} _ {\ mathrm {setpoint}} \ times sensibilidade \ times {K} _ {\ mathrm {N}} $$ (1)
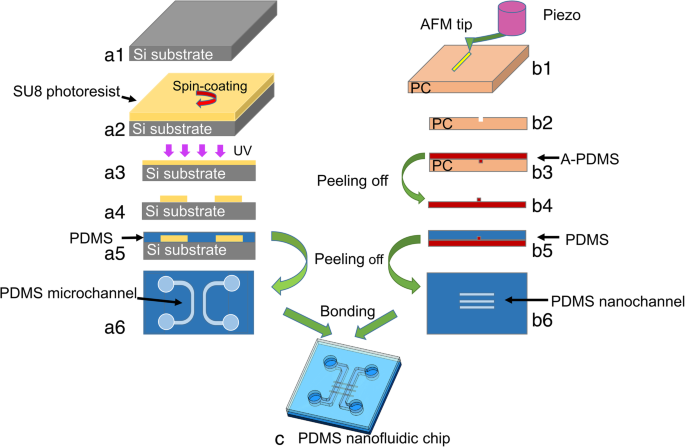
Fluxograma de fabricação de chips nanofluídicos:(a1) - (a6) Etapas de trabalho de fabricação de microcanais em um chip PDMS; (a1) Folha de silicone usada para substrato de litografia; (a2) Spin-coating de SU8 fotoresiste em substrato de Si; (a3) Exposição da camada SU8 à luz ultravioleta; (a4) Microestruturas convexas obtidas; (a5) revestimento de PDMS em molde de microcanal; (a6) Chip PDMS final com microcanais; (b1) - (b2) Etapas de trabalho de fabricação de nanocanais em um chip PDMS; (b1) arranhões na ponta do AFM na folha do PC; (b2) Molde nanocanal obtido após raspagem; (b3) revestimento A-PDMS em molde de nanocanal; (b4) chip A-PDMS com nanoestruturas convexas; (b5) Revestimento PDMS regular no molde A-PDMS; (b6) Chip PDMS final com nanocanais; (c) Chip nanofluídico PDMS após ligação
Portanto, as cargas normais para o processo de nanomilling foram definidas como 17 μN e 25 μN. Além disso, para comparação, os moldes de nanocanais em folha de PC também foram fabricados sem vibração; esse método é chamado de arranhão único. As cargas normais para o processo de arranhão único foram definidas como 25 μN, 33 μN, 42 μN, 50 μN e 58 μN. O diagrama esquemático da seção transversal do molde de nanocanal é exibido na Fig. 2 (b2).
Os moldes de microcanais foram preparados pelo processo de litografia UV. O fluxograma na Fig. 2 (a1-a4) descreve os detalhes da operação do processo de litografia. O fotorresiste (SU-82015; MicroChem, EUA) foi revestido por spin em substrato de Si a 500 rps por 30 s e a 4000 rps por 120 s. Um par de microcanais em forma de "U" formou o chip microcanal (Fig. 2 (a6)), que foi interligado por nanocanais para formar o chip nanofluídico final. A largura do microcanal era de 30 μm e o diâmetro do reservatório de 1 mm. Além disso, a distância entre dois microcanais em forma de “U” foi de 50 μm (Arquivo adicional 1:Figuras S1 e S2).
Impressão de transferência de microcanais e nanocanais
O molde de microcanais convexos (Fig. 2 (a4)) e o molde de nanocanais côncavos (Fig. 2 (b2)) foram transferidos por PDMS (Sylgard 184, Dow Corining, EUA) para preparar o chip nanofluídico final. A Figura 2 (b3) - (b6) apresenta o processo tecnológico de transferência do molde em nanocanais, que consistiu em duas etapas:primeira transferência e segunda transferência. Para investigar os efeitos da razão em peso do monômero para o agente de cura no tamanho do nanocanal, três diferentes razões de peso de PDMS (A-PDMS) foram empregadas durante o primeiro e o segundo processos de transferência. As relações de peso PDMS para o primeiro processo de impressão de transferência foram definidas como 9:1, 7:1 e 5:1, enquanto os valores para a segunda transferência foram definidos como 10:1, 9:1 e 8:1. A Figura 2 (a5) e (a6) exibe o processo de transferência do molde de microcanais usando a abordagem de transferência em uma etapa. A proporção de peso de PDMS de 10:1 foi usada para a transferência de microcanal convexo. Durante todos os processos de impressão de transferência, o elastômero PDMS de dois componentes foi primeiro uniformemente agitado e, em seguida, colocado em uma caixa para preparar o molde. A caixa foi então mantida em um dessecador a vácuo por 30 min e desgaseificada por 2–3 vezes para remover todas as bolhas de ar presas. O molde preparado foi mantido em um forno aquecido a 80 ° C por 4 h e, por fim, a réplica do PDMS foi cuidadosamente retirada do molde.
Chip Bonding
Os chips nanofluídicos preparados foram ligados por tratamento com plasma de oxigênio (Zepto, Diener electronic, Germany) por uma duração de 32 s sob uma pressão da câmara de 1,5 mbar e uma potência da câmara de 81 W (Fig. 2 (c)). As superfícies dos microcanais e nanocanais foram limpas por fitas adesivas, e os quatro reservatórios em chips de microcanais PDMS foram perfurados antes da ligação. Água deionizada foi usada para manter os chips limpos após o tratamento de plasma, e os chips foram mantidos alinhados juntos usando um sistema de alinhamento caseiro que consistia em um suporte, um microscópio monocular e um estágio de precisão unidimensional (TSDT-401S; SIGMAKOKI, Japão ) (Fig. 3a). Os detalhes do sistema de alinhamento caseiro podem ser encontrados no ESI. Os chips foram então ligados a uma temperatura de 95 ° C por 20 min, a fim de se obter um chip de micro / nanocanal (Fig. 3b).
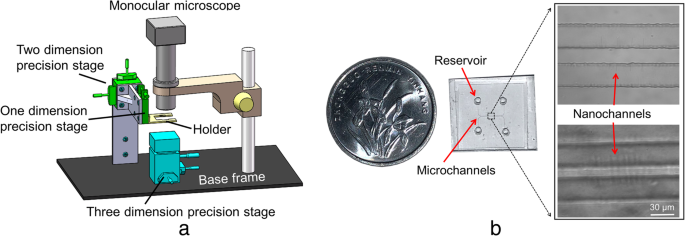
a Diagrama esquemático do sistema de alinhamento caseiro e b chip nanofluídico
Resultados e discussão
Trajetória rotativa do atuador piezoelétrico
O atuador piezoelétrico bidimensional é um componente crítico para conduzir o movimento rotativo em um sistema de nanomilling baseado em ponta de AFM. Portanto, para caracterizar seus movimentos sob uma gama de tensões e frequências de acionamento, foram realizados testes de arranhões preliminares. Sob o modelo de contato com uma faixa de varredura de 0 nm, a ponta AFM primeiro se aproximou da superfície da folha de PC sob uma determinada carga normal e foi mantida estática. A rotação do atuador piezoelétrico bidimensional foi controlada por uma frequência e tensão pré-definidas. Após a conclusão do processo de raspagem, a ponta do AFM foi levantada da superfície da folha de PC. Assim, a amplitude de movimento do atuador piezoelétrico foi obtida em função da tensão e frequência de acionamento. As tensões de condução foram definidas na faixa de 30–150 V com um espaçamento de 30 V, enquanto as frequências de condução foram definidas como 100 Hz e 1.500 Hz. A relação entre as amplitudes medidas e as tensões de acionamento em duas frequências de acionamento é exibida no Arquivo adicional 1:Figura S3. É evidente que os valores da amplitude de usinagem aumentaram com o aumento das tensões de acionamento, e o valor da amplitude de usinagem em 1500 Hz foi maior do que 100 Hz. Verificou-se que as larguras do nanocanal fabricado pelo nosso método proposto variaram de 350 nm a 690 nm.
Fabricação de moldes de nanocanais em folha de PC
As relações entre o tamanho do nanocanal e os parâmetros de usinagem sob single scratching e nanomilling são apresentadas na Fig. 4a eb, respectivamente. As larguras e profundidades dos nanocanais usinados são representados por W 0 e D 0 , respectivamente (Fig. 5a).
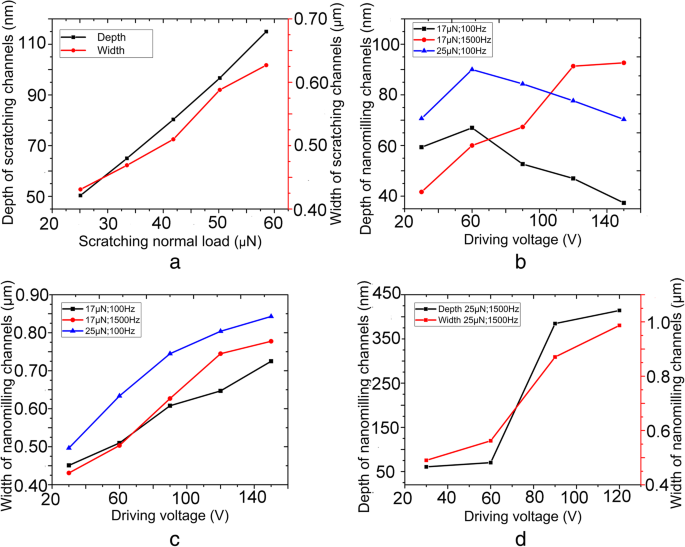
Relação entre o tamanho do nanocanal usinado e os parâmetros de usinagem: a arranhão único com cargas normais variam de 25 μN a 58 μN, b profundidade e c largura dos canais usinados quando fabricados com cargas normais de 17 μN, 25 μN e frequências de condução de 100 Hz, 150 Hz, d a profundidade e largura dos canais usinados quando fabricados com carga normal de 25 μN e frequência de condução de 1500 Hz
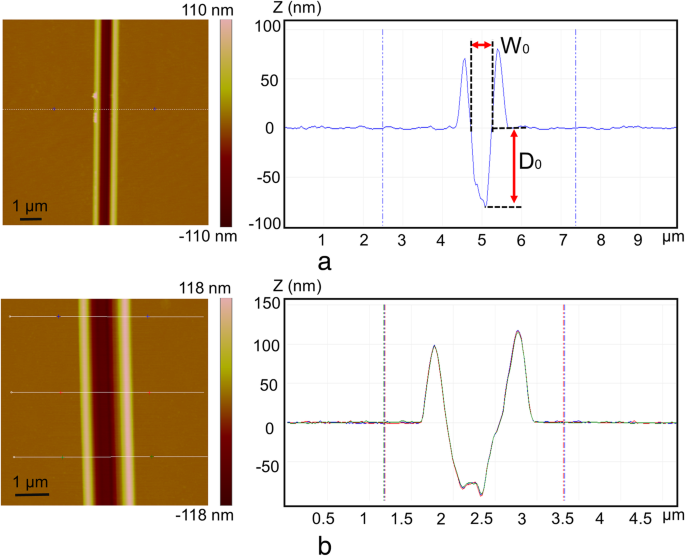
Imagens AFM típicas do nanocanal usinado com diferentes parâmetros de usinagem: a Coçar sob uma carga normal de 42 μN. b Nanomilling sob uma carga normal de 25 μN, uma frequência de 100 Hz e uma tensão motriz de 60 V
É observável a partir da Fig. 4a que as larguras e profundidades dos nanocanais fabricados aumentaram com o aumento das cargas normais. A imagem AFM típica de coçar sob uma carga normal de 42 μN é exibida na Fig. 5a. É perceptível que os materiais foram expelidos do nanocanal para formar acumulações, que foram uniformemente distribuídas em ambos os lados do nanocanal. Porque o formato da ponta do AFM é simétrico à superfície que foi formada pela aresta “OA” durante o processo de usinagem (Fig. 1b). Assim, os materiais foram expelidos uniformemente pela borda frontal da ponta durante o arranhão da borda frontal. As Figuras 4b, c e d ilustram a relação entre o tamanho do nanocanal usinado e a voltagem motriz. É evidente a partir da Fig. 4b que a profundidade do nanocanal aumentou no início e, em seguida, começou a diminuir sob uma frequência de 100 Hz com cargas normais de 17 μN e 25 μN. A folha de PC usada em nosso estudo foi um polímero amorfo, que apresenta um comportamento elástico-viscoplástico em combinação de um endurecimento por deformação exponencial em níveis de alta deformação [48, 49]. A carga normal durante a usinagem foi calculada pela Eq. (2), onde \ (\ overrightarrow {n} \) e \ (\ overrightarrow {t} \) são a unidade normal e a unidade tangente ao vetor da linha de fluxo, respectivamente, p e τ significa pressão normal local e tensão de cisalhamento, respectivamente, e \ (\ overrightarrow {z} \) é a unidade vertical [50].
$$ {F} _ {\ mathrm {N}} =p \ cdot \ int \ overrightarrow {n} \ cdot \ overrightarrow {z} ds- \ tau \ cdot \ int \ overrightarrow {t} \ cdot \ overrightarrow {zds } $$ (2)
No presente estudo, os tamanhos dimensionais dos nanocanais fabricados foram encontrados em nanoescala, portanto, os valores de pressão normal local e tensão de cisalhamento foram assumidos como constantes. Além disso, a Eq. (2) foi convertido na forma simplificada da Eq. (3), onde S n e S h respectivamente, são as projeções horizontais e verticais da interface entre a ponta do AFM e a amostra.
$$ {F} _ {\ mathrm {N}} =p \ cdot {S} _n- \ tau \ cdot {S} _h $$ (3)
A relação entre S n e S h é expresso na Eq. (4), onde α e β respectivamente são os ângulos incluídos entre a superfície da ponta e os planos vertical e horizontal.
$$ {S} _ {\ mathrm {n}} =\ frac {S _ {\ mathrm {h}}} {\ cos \ alpha} \ cdot \ cos \ beta $$ (4)
A carga normal foi calculada pela Eq. (5).
$$ {F} _ {\ mathrm {N}} =\ left (p \ cdot \ frac {\ cos \ beta} {\ cos \ alpha} - \ tau \ right) \ cdot {S} _h $$ (5 )
É evidente a partir da Eq. (1) que os valores de carga normal foram constantes durante todo o processo de usinagem. De acordo com Briscoe et al. [51], o valor da taxa de deformação média foi calculado pela Eq. (6), onde V e w significam a velocidade da ponta e a espessura do cavaco sem cortes, respectivamente. O valor máximo da espessura do cavaco não cortado foi encontrado em ~ 10 nm.
$$ {} _ {\ varepsilon} ^ {\ bullet} =\ frac {\ mathrm {d} \ varepsilon} {\ mathrm {d} t} \ approx \ frac {V} {w} $$ (6)
Além disso, os valores da velocidade de ponta foram obtidos da Eq. (7), onde f é a frequência do sinal de entrada.
$$ V =\ pi \ cdot {W} _o \ cdot f $$ (7)
Os valores da taxa de deformação média em 100 Hz foram encontrados na faixa de 1,42 × 10 4 s -1 ~ 2,27 × 10 4 s -1 . Os valores da pressão normal local ( p ) começou a subir com o aumento das taxas de deformação, quando as taxas de deformação variaram de 1,42 × 10 4 s -1 para 2,27 × 10 4 s -1 [52]. O valor de τ era muito menor do que p , significa que a carga normal depende principalmente de p . Portanto, a fim de manter os valores de carga normal (F N ) constante durante todo o processo de usinagem, os valores da profundidade de usinagem devem ser menores em tensões de acionamento mais altas. No entanto, o tamanho dimensional final do nanocanal fabricado foi afetado pela recuperação do material da amostra. A recuperação da amostra diminuiu com o aumento das velocidades de usinagem na faixa de 142 ~ 227 μm / s [53]:assim, indica que uma recuperação elástica maior ocorreu em 30 V. Consequentemente, a profundidade do nanocanal fabricado em 30 V (~ 142 μm / s) foi mais raso do que 60 V (~ 161 μm / s). Arquivo adicional 1:Figura S4 (a) e Fig. 5b são as imagens AFM típicas do nanocanal usinado a 100 Hz sob cargas normais de 17 μN e 25 μN, respectivamente. É óbvio que o acúmulo no lado direito do nanocanal é maior do que o esquerdo. O movimento rotativo da amostra durante o processo de nano-fresagem é no sentido anti-horário e o ângulo de corte da aresta de corte principal muda com a rotação. A espessura do chip não cortado é muito pequena para formar chips no início e no final de um ciclo de processo de nanomilling. A espessura do chip não cortado no meio de um ciclo de processo de nanomilling é relativamente grande; entretanto, o pequeno ângulo de ataque contribui para a formação dos engavetamentos. Assim, mais materiais são empurrados para o lado direito do canal, e os empilhamento são assimétricos . Os detalhes para a formação de engavetamentos assimétricos podem ser encontrados em nosso estudo anterior [54].
É observável a partir da Fig. 4b ed que a profundidade do nanocanal começou a aumentar com o aumento das tensões de acionamento em 1500 Hz sob cargas normais de 17 μN e 25 μN. A Figura 4d mostra que a profundidade do nanocanal aumentou drasticamente de 60 V (~ 2,64 mm / s) para 90 V (~ 4,10 mm / s) sob uma carga normal de 25 μN. De acordo com Geng et al. [55], o estado de remoção de material é significativamente afetado pela velocidade de corte. Os materiais foram expulsos do nanocanal em forma de empilhamento durante a usinagem a uma velocidade de 2,64 mm / s, enquanto o estado de remoção de material foi alterado de empilhamento para cavaco a 4,10 mm / s (Arquivo adicional 1:Figura S4 (b)) . Portanto, o aumento na profundidade de usinagem em 90 V (~ 4,10 mm / s) pode ser atribuído à mudança no estado de remoção de material. A largura do nanocanal fabricado começou a aumentar com o aumento das tensões de acionamento. A Figura 6 exibe o diagrama esquemático da trajetória da ponta de AFM durante a nano-fresagem, as elipses tracejadas, as elipses sólidas pretas e as setas azuis representam o processo de usinagem acabado, o processo de usinagem em andamento e a direção do movimento da ponta de AFM, respectivamente. A largura ( W 2 ) do canal usinado na Fig. 6 (b) era maior do que ( W 1 ) na Fig. 6 (a). AS 1 e AS 2 (linhas sólidas vermelhas) representam o comprimento de contato entre a seção transversal da ponta de AFM e o material de amostra. O valor de AS 1 foi considerado maior do que AS 2 quando a largura de usinagem “ L 1 ”Era igual a“ L 2. ”
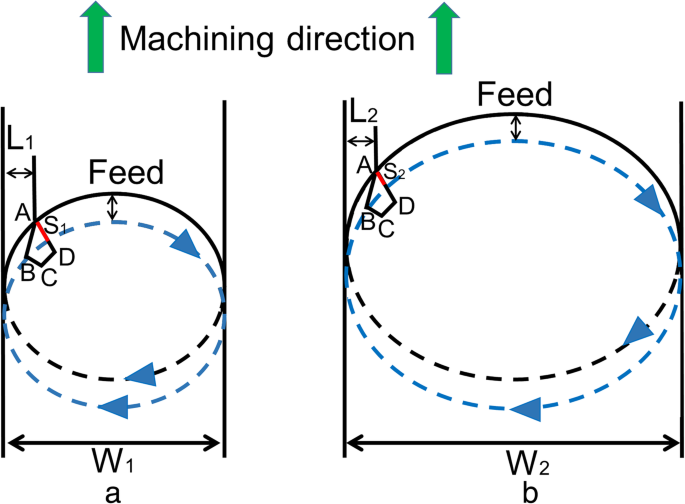
Representação esquemática da trajetória da ponta de AFM durante o processo de nanomilling:a largura usinada do nanocanal ( a ) é menor do que nanocanal ( b ), e as elipses tracejadas, as elipses sólidas pretas e as setas azuis representam o processo de usinagem concluído, o processo de usinagem em andamento e a direção do movimento da ponta do AFM, respectivamente
O valor de S h na Eq. (5) foi obtido pela Eq. (8), onde D e AS, respectivamente, são a profundidade do canal usinado e o comprimento de contato entre a seção transversal da ponta de AFM e o material de amostra.
$$ {S} _h =\ frac {1} {2} \ cdot \ left | D \ left | \ cdot \ right | \; AS \ right | $$ (8)
Portanto, a Eq. (5) foi reescrito na forma da Eq. (9).
$$ {F} _ {\ mathrm {N}} =\ frac {1} {2} \ cdot \ left (p \ cdot \ frac {\ cos \ beta} {\ cos \ alpha} - \ tau \ right) \ cdot \ left | D \ left | \ cdot \ right | AS \ right | $$ (9)
Os valores de α e β foram mantidos constantes durante todo o processo de usinagem. Os valores da taxa de deformação em 1500 Hz foram encontrados na faixa de 2,03 × 10 5 ~ 3,66 × 10 5 s -1 ; portanto, pode-se presumir que a pressão normal local ( p ) atingiu seu valor limite em 1500 Hz. Além disso, a velocidade de usinagem não manifestou nenhum efeito na recuperação da amostra durante a usinagem a 30– 150 V (~ 2,03–3,66 mm / s) [53]; assim, os tamanhos dimensionais finais do nanocanal foram determinados apenas pelas dimensões de usinagem. Os valores de AS 2 (Fig. 6 (b)) foram considerados menores do que os de AS 1 (Fig. 6 (a)) para larguras usinadas maiores, e de acordo com a Eq. (9), o valor de D foi maior para um valor menor de AS. Portanto, os valores da profundidade de usinagem aumentaram com o aumento das tensões de acionamento. Uma imagem AFM típica do nanocanal fabricado sob uma carga normal de 25 μN, uma tensão de acionamento de 120 V e uma frequência de 1500 Hz é apresentada no arquivo adicional 1:Figura S4 (b). É perceptível que os materiais foram removidos na formação do chip e da pilha, e os materiais expelidos se acumularam apenas em um lado do nanocanal. Além disso, os materiais expelidos se acumularam na formação de cavacos na parte inferior do nanocanal durante a usinagem a 150 V sob uma carga normal de 25 μN. Portanto, os dados de tamanho do nanocanal fabricado durante a usinagem a uma voltagem de 150 V e uma frequência de 1500 Hz (sob uma carga normal de 25 μN) estavam vazios na Fig. 4d.
É evidente a partir da Fig. 4c que a largura dos nanocanais começou a aumentar com o aumento das tensões de acionamento. Além disso, quando os valores de carga normal e tensão de condução foram mantidos constantes, a largura do nanocanal fabricado a uma frequência de 1500 Hz foi maior do que a de 100 Hz. Além disso, a profundidade de usinagem do nanocanal fabricado a 1500 Hz era mais profunda do que a de 100 Hz, e o tamanho da seção transversal da ponta foi considerado maior durante a usinagem de um nanocanal mais profundo. Portanto, os nanocanais foram fabricados mais largos durante a usinagem mais profunda.
Primeira transferência de moldes de nanocanais
Nanocanais usinados pelo método de raspagem única sob cargas normais de 25 μN, 33 μN, 41 μN, 50 μN e 58 μN foram aplicados ao primeiro processo de transferência. Além disso, moldes de nanocanais fabricados por nanomilling a uma frequência de 100 Hz na faixa de voltagem de condução de 30-150 V (com um espaçamento de 30 V) também foram usados no processo de transferência. Os nanocanais (profundidade de 80 nm e largura de 510 nm) usinados pelo método de arranhão único foram denominados como "nanocanal I", enquanto os nanocanais (profundidade de 50 nm e largura de 610 nm, profundidade de 90 nm e largura de 630 nm) fabricados por nanomilling foram chamados de "nanocanal II ”e“ nanocanal III ”, respectivamente. Três diferentes proporções de peso de PDMS (5:1, 7:1 e 9:1) foram usadas no primeiro processo de transferência.
As Figuras 7a eb revelam os efeitos de diferentes proporções de peso de PDMS no tamanho da parede sob uma carga normal de 25 μN e uma frequência de 100 Hz, e a linha tracejada preta representa o tamanho do nanocanal original antes da transferência. A imagem AFM típica e a seção transversal correspondente da parede obtida do nanocanal III a uma proporção de peso de 5:1 durante a primeira transferência são exibidas na Fig. 7c e d, e esta parede foi denominada como "parede III". Os efeitos de diferentes proporções de peso PDMS no tamanho da parede sob o processo de arranhão único com uma carga normal de 17 μN e uma frequência de 100 Hz foram mostrados no ESI (consulte o arquivo adicional 1:Figuras. S5, S6, S7 e S8 do ESI para detalhes). As paredes obtidas do “nanocanal I” e “nanocanal II” foram denominadas como “parede I” e “parede II”, respectivamente. É evidente que as alturas de todas as paredes em diferentes proporções de peso de PDMS eram aproximadamente as mesmas. The widths of the walls were larger than the original nanochannel width, and the width at the weight ratio of 5:1 was found to be the largest. Due to the thermal expansion of PC sheet, a small deviation was noticed between final wall size and original nanochannel size. It was also observed that the elasticity of PDMS increased as the PDMS weight ratio decreased from 5:1 to 7:1 [41, 42]. Hence, the wall obtained at the weight ratio of 5:1 was stiffer and its elastic recovery was smaller; thus, the width of the wall obtained at the weight ratio of 5:1 was the largest.
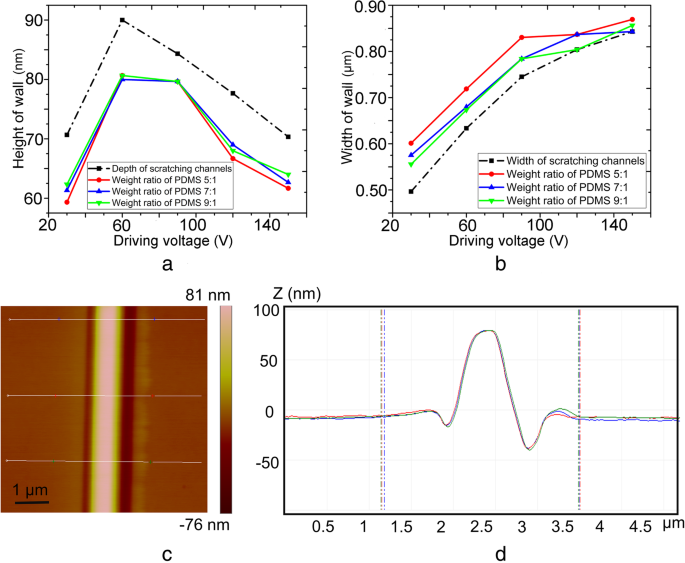
Relationship between a wall height, b wall width, and transfer parameters (various weight ratio of PDMS) during first transfer process, where the channel molds were fabricated with a normal load of 25 μN and a frequency of 100 Hz, and c typical AFM image and d corresponding cross-section of the wall obtained from nanochannel III at a weight ratio of 5:1
Second transfer of nanochannel molds
The final PDMS slabs with nanochannels were obtained during second transfer process based on the wall obtained at a weight ratio of 5:1 in the first transfer process. Three different PDMS weight ratios (10:1, 9:1, and 8:1) were used during second transfer process. Figure 8a and b present the relationship between nanochannel size obtained under a normal load of 25 μN and a frequency of 100 Hz and transfer parameters during second transfer. It is clear from Fig. 8a that the depths of the nanochannels were larger than the original machining size, moreover, the depth at 10:1 was found to be larger than other two ratios. Further, the widths of the wall were also larger than the original size, and the width at 10:1 was found to be the largest (Fig. 8b). Figure 8c and d present a typical AFM image and corresponding cross-section of the nanochannel (120 nm depth and 690 nm width) obtained from wall III at a weight ratio of 10:1 during second transfer, and it was termed as “nanochannel C.” The relationship between the nanochannel sizes obtained under single scratching process with a normal load of 25 μN and a frequency of 100 Hz and the transfer parameters during the second transfer process were shown in ESI (see Additional file 1:Figures. S9, S10, S11 and S12 of ESI for details), the nanochannels obtained from “wall I” and “wall II” were termed as “nanochannel A” and “nanochannel B”, respectively.
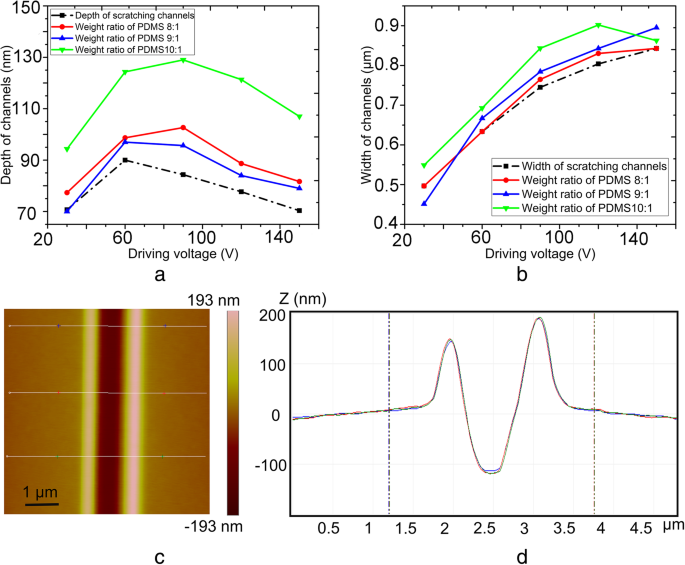
Relationship between a nanochannel height, b nanochannel width, and transfer parameters (various weight ratio of PDMS) during second transfer, where the channel molds were fabricated with a normal load of 25 μN and a frequency of 100 Hz, and c typical AFM image and d corresponding cross-section of the nanochannel obtained from wall III at a weight ratio of 10:1 during second transfer
The depths of nanochannels obtained from walls II and III were larger than the original machining size, whereas the depth obtained from wall I was smaller than the initial machining size. Furthermore, the changes in width were identical to the changes in depth. The aspect ratio of wall I was larger than those of walls II and III, thus each wall manifested different thermal expansion values. Hence, the changing trends of width and depth during second transfer were different though at the same PDMS weight ratio. The values of the depth and width of walls II and III at 9:1 and 8:1 were found to be closer to the original machining size compared with 10:1. Because the elastic recoveries of PDMS at 9:1and 8:1 are closer to 5:1 than 10:1, which indicates an almost similar recovery trend for PDMS at 9:1, 8:1, and 5:1.
Application of nanochannel devices in electric current measurement
Nanochannel devices are often used in the fields of single nanoparticle manipulation, electrokinetic transport phenomena, DNA analysis, and enzymatic reaction detection. The main working principle of nanofluidic chips depends on the variation in electric current; therefore, it is important to measure the electrical conductivities of nanochannel devices. The electrical conductance in a nanochannel can be estimated by Eq. (10) [56].
$$ G={10}^3N\;{}_Ae\frac{wh}{l}\sum {\mu}_i{c}_i+2{\mu}_e\frac{w}{l}{\delta}_n $$ (10)
onde μ i is the mobility of ion i , c i is the concentration of ion i , δ n is the effective surface charge inside the nanochannel, and NA and e signify Avogadro constant and electron charge, besides, w , h e l are the nanochannel width, height and length, respectively. It is obvious that the electrical conductance of a nanochannel is affected by the nanochannel feature dimensions and the solution concentration. The electric double layer (EDL) plays an important role in the nanochannel when the ratio of DEL thickness to the nanochannel height increases. The diffuse layer thickness of EDL is 3~5 times of the Debye length (λ D ), which can be expressed by Eq. (11) [57].
$$ {\lambda}_D=\sqrt{\frac{\varepsilon_0{\varepsilon}_r{k}_bT}{2{n}_{i\infty }{(ze)}^2}} $$ (11)
onde n i ∞ denotes ion density in the solution, ε o is the permittivity of vacuum, ε r is the dielectric constant of electrolyte solution, z is the valency of buffer solution (z = z + − z - = 1 for KCl), and kb e T are the Boltzmann constant and temperature, respectively. In the present study, three different nanofluidic chips were obtained after the completion of transfer process. Nanofluidic chips consisted of nanochannels A, B, and C were termed as nanofluidic chips A, B, and C, respectively. Each nanofluidic chip contained four nanochannels. The widths and the depths of nanofluidic chips A, B, and C were measured as 60 nm and 500 nm, 80 nm and 680 nm, and 120 nm and 690 nm, respectively. The effective length of nanochannels in all chips was calculated as 50 μm. As shown in Fig. 8, pile-ups distribute on the sides of the nanochannels A, B, and C. The pile-ups may fill into the nanochannels and lead to a failure of the preparation for the nanofluidic chips. Thus, in order to verify the reliability of the fabricated nanochannel devices, electrical conductivity measurement test was conducted. KCl with 1 mM concentration was as the electrolyte solution in our study, and the values of electrical current were measured by an electrometer (Model 6430, Keithley, USA). The schematic sketches of the measurements for electric current in microchannel and nanochannel are presented as the inset figures in Fig. 9a and b, respectively. The experiments were carried out under DC power (applied by an Ag electrode) with an increment of 2 V for 3-s duration. Figure 9a presents the measured I - V curves of microchannels in three different nanofluidic chips, and a linear relationship between current and voltage was observed. Moreover, as the effect of EDL in microchannels was negligible and the dimensional sizes of microchannels in different nanofluidic devices were identical, the values of current in different chips were nearly the same. It is evident from Fig. 9b that the values of current in different nanofluidic devices were distinct due to different nanochannel sizes. For KCl solution of 1 mM concentration, the value of λ D was about 10 nm, thus the diffuse layer thickness of EDL was found as 30~50 nm [57]. Consequently, EDL got overlapped along the depth (60 nm) of nanofluidic chip A; however, no overlapping was observed in nanofluidic chip C (depth of 120 nm). However, it was difficult to determine whether EDL got overlapped or not in nanofluidic chip B (depth of 80 nm). It assumes that the effective surface charges (δ n ) in all nanochannels are identical as the charge density of a surface is material property [58, 59]. The concentration of the ions in a nanochannel depends on the EDL field, the stronger the EDL field, the higher the ion concentration in the nanochanel [44]. In the present study, the EDL field in nanofluidic chip A is the strongest as the highest ratio of the DEL thickness to the nanochannel height, which signifies that the ion concentration in the nanochannel of nanofluidic chip A is the highest. De acordo com a Eq. (10), the nanochannel of nanofluidic chip A is more conductive due to the higher ion concentration. Hence, the value of electrical current in nanofluidic chip A was the largest, whereas nanofluidic chip C yielded the smallest value. In addition, at larger width sizes, EDLs did not overlap along the width directions of nanochannels. In nanofluidic chip B, when the value of applied electric field was lower than 25 V, a linear relationship was noticed between current and applied voltage; however, a limiting region appeared as the value of applied voltage increased and finally, became liner again as the electrical field increased further, this phenomenon belongs to ohmic-limiting-overlimiting current characteristic [60, 61]. The results of electrical current measurement revealed that the nanofluidic devices fabricated by the proposed method were effective, the pile-ups of the nanochannels A, B, and C had almost no influence on the performance of the nanofluidic devices.
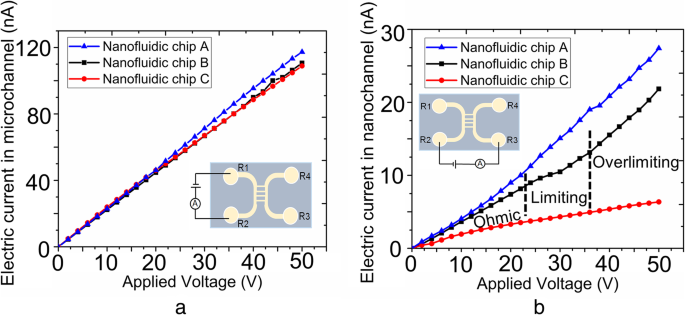
Electric current measurement results based on the fabricated nanochannel devices, the cross-section size (depth × width) of nanochannels for nanofluidic chip A, B, and C are 60 × 500 nm, 80 × 680 nm and 120 × 690 nm, respectively. a Current in microchannels. b Current in nanochannels. The insets display the schematic sketches of the measurements
Conclusões
In the present research, nanochannels with controllable sizes (sub-100-nm depth) were fabricated by AFM tip-based nanomilling, and for the first time, the machined nanochannels were applied to prepare nanofluidic devices. The multichannel nanofluidic devices were prepared in four steps:(1) fabrication of nanochannels by AFM tip and piezoelectric actuator, (2) fabrication of microchannels by lithography, (3) transfer of micro- and nanochannels, and (iv) bonding. Further, nanochannel sizes were controlled by changing the driving voltages and frequencies inputted to the actuator. The heights of the wall obtained during first transfer were smaller than the original machining size, whereas the widths were larger than the original machining size. The experiment results revealed that during second transfer process, nanochannel sizes affected PDMS weight ratios. Finally, micro-nanofluidic chips with three different nanochannel sizes were obtained by bonding a PDMS nanochannel chip on a PDMS microchannel chip. Moreover, the electrical current measurement experiment was conducted on the fabricated nanofluidic chips, and it was found that the values of current were affected by nanochannel sizes. Therefore, PDMS nanofluidic devices with multiple nanochannels of sub-100-nm depth can be efficiently and economically fabricated by the proposed method.
Compared with other fabrication approach, the proposed method for fabrication of the nanofluidic devices in the study is easy to use and low cost; besides, the nanochannels with controllable dimension size can be obtained easily. However, the commercial AFM system cannot equip with a large-scale high-precision stage due to the spatial limitation; thus, the maximum fabrication length of the nanochannel is confined as 80 μm. In addition, the tip wear cannot be neglected after long-term fabrication due to the high machining speed, which should be investigated in future work.
Abreviações
- AFM:
-
Microscópio de força atômica
- DC:
-
Direct current
- EDL:
-
Electric double layer
- KCL:
-
Potassium chloride
- PC:
-
Polycarbonate
- PDMS:
-
Polidimetilsiloxano
- PSD:
-
Position-sensitive photodetector
Nanomateriais
- Corte e vinco:Um curso intensivo sobre este processo de fabricação
- Blog:Compreendendo o processo de fabricação do PDMS
- Os métodos de fabricação de compósitos mais populares
- As diferentes maneiras como o processo de acabamento adiciona valor funcional aos projetos de fabricação de metal
- Usando uma impressora 3D para melhorar seu processo de fabricação - Vídeo
- Seu guia para cisalhamento do processo de fabricação de metal
- O processo de fabricação de tubos requer planejamento de rota imaginativo
- O processo de fabricação de tubulações requer o cumprimento de especificações exatas
- Quanto tempo seu processo de fabricação requer?
- Os benefícios do jateamento para seu projeto de fabricação de metal personalizado