RTM de velocidade com sensores de fluxo de calor
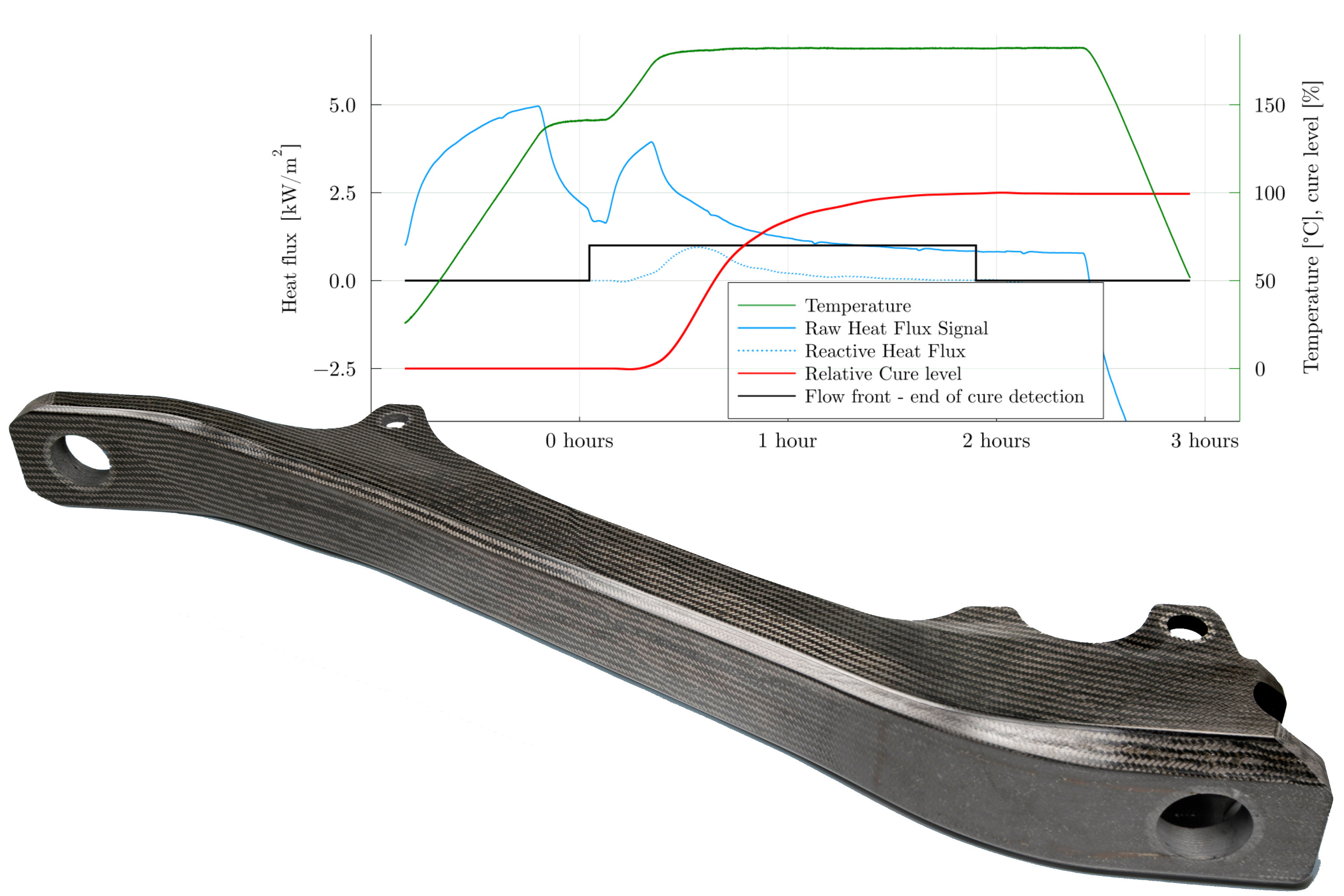
Representando de 3 a 5% do peso de uma aeronave, o trem de pouso há muito tem sido direcionado para redução de peso para melhorar a eficiência da aeronave. Isso se tornou ainda mais crítico com a mudança iminente para sistemas de propulsão elétrica que reduzem a energia e as emissões.
Por exemplo, a Safran Landing Systems (Vélizy, França) permitirá o desligamento dos motores, taxiamento elétrico por meio de motores elétricos integrados às rodas do trem de pouso da aeronave, reduzindo NOx, CO 2 , Emissões de CO e de hidrocarbonetos não queimados em 51%, 61%, 73% e 62%, respectivamente. Esta é uma grande vitória para uma aviação mais sustentável, mas os motores elétricos requerem energia e as baterias necessárias para fornecer essa energia são pesadas.
Assim, a demanda por estruturas de trem de pouso leves parece um ajuste perfeito para a aplicação de compósitos, exceto por um problema. “Como o trem de pouso é uma estrutura de caminho de carga única, a falha de um componente estrutural pode resultar em uma condição séria de pouso de emergência”, diz Peet Vergouwen, tecnólogo do GKN Fokker Landing Gear (Helmond, Holanda). O trem de pouso GKN Fokker trabalhou por mais de uma década para demonstrar a viabilidade técnica de estruturas compostas de trem de pouso, incluindo o desenvolvimento de suportes de arrasto de polímero reforçado com fibra de carbono (CFRP) para o F-35 Lightning II . “Devido à sua criticidade, as estruturas do trem de pouso estão entre as mais conservadoras em aeronaves comerciais.” Conseqüentemente, eles foram fabricados principalmente com metais de alta resistência.
Essa maré está começando a mudar, no entanto. Clean Sky 2 está buscando uma redução de peso de 30%, mas via componentes CFRP no projeto HECOLAG (High Efficiency Composites LAnding Gear), para duas aplicações. Na primeira aplicação, uma alternativa de CFRP foi desenvolvida para o escora superior de arrasto de alumínio existente para o trem de pouso do nariz do A350-1000, originalmente desenvolvido e fabricado pela Liebherr-Aerospace (Lindenberg, Alemanha). Os parceiros da HECOLAG Royal Netherlands Aerospace Centre (NLR, Marknesse) e GKN Fokker Landing Gear projetaram este suporte de arrasto CFRP de acordo com os requisitos da Liebherr. Usando tecnologia de pré-formação automatizada desenvolvida internamente, a NLR construiu protótipos funcionais do suporte de arrasto CFRP, que foram testados pelo GKN Fokker Landing Gear.
Na segunda aplicação que está sendo avaliada pela HECOLAG, NLR e GKN Fokker Landing Gear também desenvolveram um CFRP suporte lateral inferior em conjunto com a Safran Landing Systems para o trem de pouso principal eletrificado. CW irá relatar especificamente sobre os resultados gerais do projeto HECOLAG mais tarde em 2021, mas aqui, o foco está no subprojeto INNOTOOL 4.0, guiado pelo gerente de tópico GKN Fokker Landing Gear para avançar a produção altamente automatizada de estruturas de trem de pouso CFRP usando moldagem por transferência de resina (RTM) . Especificamente, o INNOTOOL 4.0 busca demonstrar ferramentas integradas a sensores que abrirão caminho para ferramentas menores com menos massa para ciclos de produção mais rápidos, manuseio mais fácil e menor consumo de energia, bem como maior automação para menor custo e controle de processo inteligente de compósitos 4.0. O projeto INNOTOOL 4.0 é financiado pela Empresa Comum Clean Sky 2 no âmbito do programa de pesquisa e inovação Horizon da UE sob o GAP nº 821261.
objetivos do INNOTOOL 4.0
O demonstrador para esta segunda parte do HECOLAG (veja a imagem de abertura) é mais uma parte genérica, explica Vergouwen. “É para demonstrar o projeto de peças, simulação e metodologias de fabricação que fornecerão o desempenho, a taxa de produção e o custo necessários para aeronaves de corredor único.” No final de 2017, o consórcio HECOLAG definiu a peça do demonstrador CFRP inicial e a ferramenta de produção, analisou o comportamento térmico da ferramenta e realizou testes de desempenho. Este produto grande e complexo foi aprovado na revisão de projeto preliminar e atingiu um nível de preparação de tecnologia (TRL) de 4 no final daquele ano. “Com base nos problemas e nas lições aprendidas com o primeiro demonstrador, estávamos procurando parceiros para desenvolver a tecnologia de ferramentas RTM para otimizar e encurtar o ciclo de cura”, disse Vergouwen. Em 2018 foi lançada a Chamada Clean Sky 2 para Parceiros, adjudicada ao consórcio INNOTOOL 4.0, composto pelo fornecedor de equipamentos e automação Techni-Modul Engineering (TME, Coudes, França) e pelo especialista em injeção de resina Isojet Equipements (Corbas, França). Eles começaram a trabalhar em abril de 2019 e completaram os marcos iniciais em março de 2021.
“A peça composta deve ter um custo competitivo com aço e alumínio forjados”, observa Vergouwen no GKN Fokker Landing Gear. “Isso só é possível com automação, permitindo um número muito baixo de horas de trabalho e materiais mais acessíveis do que o atual CFRP curado em autoclave de grau aeroespacial.”
Assim, a INNOTOOL 4.0 buscou integrar sensores nas ferramentas RTM que irão monitorar e gerenciar os processos de injeção e cura, incluindo detecção de frente de fluxo de resina. “O objetivo é ser totalmente automatizado - carregue a pré-forma, aperte um botão e o equipamento de moldagem irá gerenciar a temperatura, pressão, vácuo e cura”, diz Stéphane Besson, diretor comercial da TME. No entanto, esta é a primeira vez que GKN Fokker Landing Gear e TME trabalham com monitoramento de cura. “Já trabalhamos com sensores de temperatura e pressão antes”, diz Besson, “mas não com sensores de fluxo de resina e polimerização”.
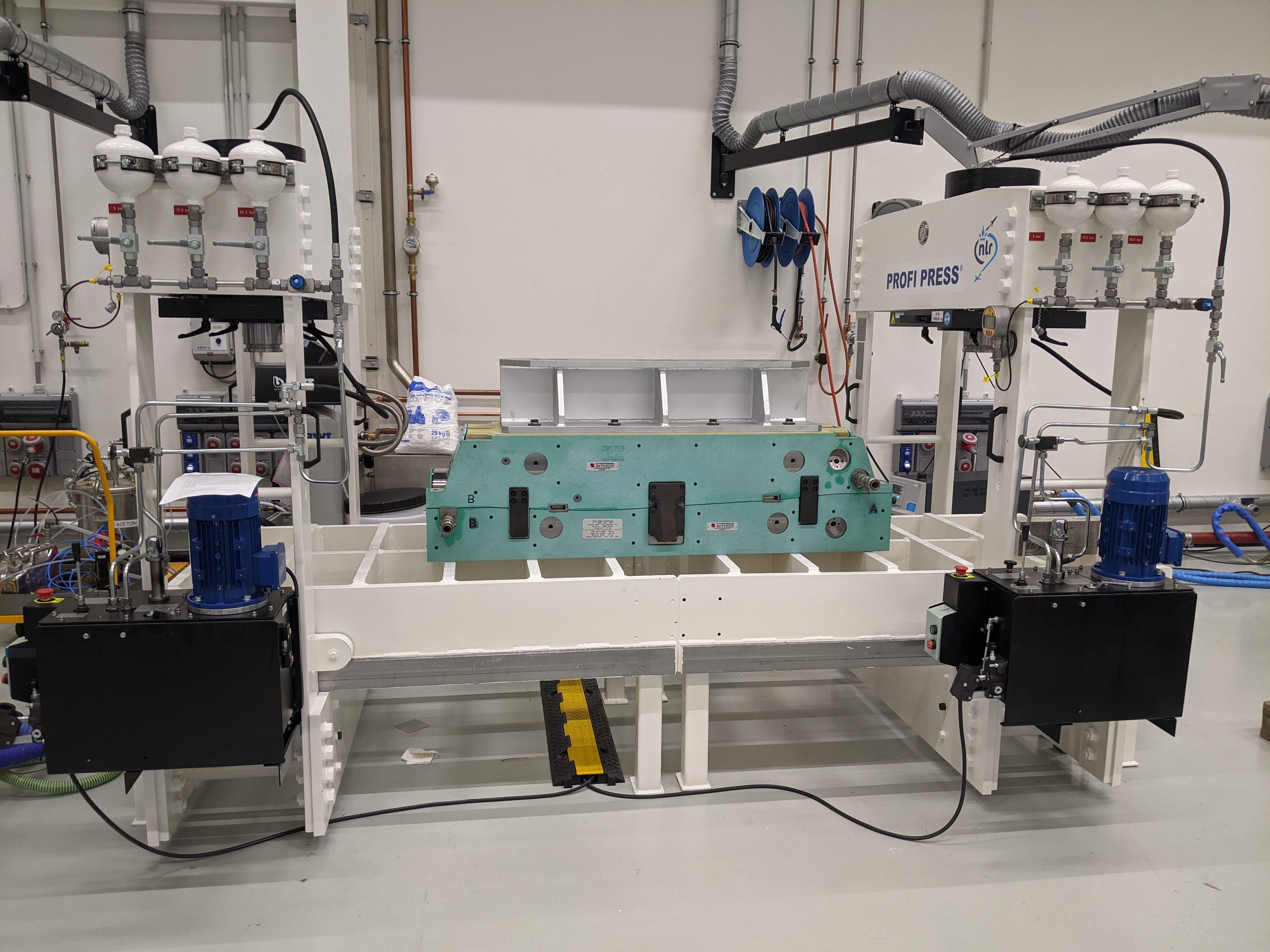
Os marcos iniciais do projeto INNOTOOL 4.0 exigiam que a TME e a Isojet entregassem uma ferramenta de moldagem equipada com sensor e um sistema de injeção para a NLR que seria usada para produzir peças de demonstração em março e abril de 2021. Em paralelo, a TME usaria uma ferramenta existente para a produção de Placas CFRP - tamanho 600 x 600 milímetros com espessura de 1-8 milímetros - modificadas com os mesmos sensores para testes de controle de processo em suas instalações. “Isso é algo que você prefere fazer em pequena escala pela primeira vez, em vez de diretamente em uma ferramenta grande com uma peça de alto custo”, diz Vergouwen. Assim, a TME utilizou uma ferramenta diferente, mas os mesmos sensores para mostrar suas capacidades e profundidade. Com esse teste concluído, a NLR reutilizaria a ferramenta HECOLAG principal para produzir uma nova rodada de demonstradores CFRP para otimizar ainda mais o controle do processo nas peças reais.
Projeto de ferramenta de produção RTM
A TME começou a produção do projeto da ferramenta RTM usando o software CATIA V5 da Dassault Systèmes (Vélizy-Villacoublay, França) para projetos mecânicos e elétricos e ANSYS (Canonsburg, Pa., EUA) para simulação térmica e mecânica. Esta ferramenta seria combinada com o sistema 1K-2K baseado em pistão da Isojet (para resinas de uma e duas partes) para injetar Hexcel (Stamford, Connecticut, EUA) HexFlow 2K RTM 6 e Solvay (Alpharetta, Geórgia, EUA) 1K PRISM EP 2400, resinas epóxi de grau aeroespacial de um componente a uma pressão de injeção de até 20 bar.
“A forma desta ferramenta de moldagem é muito complexa”, observa Besson, “combinando espessuras variadas na pré-forma seca 3D com uma forma tubular fechada. Isso cria transições de espessura complexas, com problemas em torno da montagem da pré-forma, precisão da camada final, gradientes de temperatura interna e encolhimento da resina, bem como como otimizar o método de aquecimento e a capacidade de aquecimento do mandril interno para permitir um tempo de ciclo curto. Para permitir tempos de ciclo curtos, todos os elementos da ferramenta devem ser simples de usar, robustos e permitir rápido aquecimento e resfriamento. ” Embora o projeto INNOTOOL 4.0 solicitasse brevemente soluções de molde não metálicas, um conjunto típico combinado de moldes de aço superior e inferior foi criado devido às pressões necessárias para minimizar as rugas e garantir o alinhamento da fibra durante a conformação.
Os moldes superiores e inferiores combinados e o mandril são aquecidos e resfriados. “Os moldes combinados usam um circuito de água integrado enquanto o mandril é aquecido eletricamente”, explica Besson. “A circulação de água fornece rápido aquecimento e resfriamento para reduzir o tempo de ciclo da peça e o aquecimento elétrico atinge o mesmo no mandril onde o espaço é limitado.”
“Outro desafio era o número de peças no mandril”, diz Besson. “Devido ao formato complexo e à necessidade de remoção do mandril após a moldagem, ele era composto por seis componentes de autoaquecimento e dois elementos de suporte por onde passam os sensores para controlar a temperatura interna das peças do mandril. Em uso, esses elementos são montados manualmente com o auxílio de um suporte de base que orienta o operador. ” O trabalho com um mandril inflável como solução será concluído dentro do projeto HECOLAG maior, mas isso não foi incluído no subprojeto INNOTOOL 4.0.
Sensores de fluxo de calor
A TME planejou inicialmente usar sensores dielétricos para monitorar o fluxo e a cura da resina (consulte “Combinando medições dielétricas AC e DC para monitoramento de cura de compósitos”), mas mudou para sensores de fluxo de calor da TFX (Boncourt, Suíça). “À medida que avançávamos no desenvolvimento, queríamos sensores que permitissem o controle da medição sem contato direto com o polímero e os materiais compósitos”, explica Jorge Lopez Torres, gerente de projeto da TME. “Os sensores TFX permitiram isso porque medem o fluxo de calor, que se propaga através dos materiais.” Ele ressalta que esta é basicamente a mesma medida usada na calorimetria exploratória diferencial (DSC), uma técnica de laboratório que analisa o estado de cura de um polímero ou compósito. Notavelmente, os sensores TFX e os testes DSC medem o calor liberado durante a polimerização / cura e resultam em uma curva de fluxo de calor em função da temperatura e do tempo.
Para sensores TFX, os dados de temperatura vêm de um sensor de temperatura interno dentro dos sensores de fluxo de calor. Embora os sensores dielétricos sejam similarmente equipados com um sensor de temperatura interno, os dois sensores são muito diferentes. “Os sensores dielétricos medem diretamente as propriedades do polímero durante a cura”, explica o gerente da TFX, Dr. Fabien Cara. “Os sensores de fluxo de calor não fornecem o estado do material em um determinado instante. No entanto, medir o calor gerado durante o fluxo de resina e a polimerização fornece uma boa visão de como o processo está se comportando e como o ciclo de cura pode ser repetido para cada peça produzida. E como o DSC, precisamos ver toda a curva do processo de cura, mas nossa capacidade de monitorar a cura é muito confiável. ”
Décadas de experiência
Fundada como Thermoflux em 2000, os sensores TFX têm sido usados em testes em centros de P&D e em aplicações industriais por mais de 100 clientes em todo o mundo. “Começamos a trabalhar com a RTM há mais de 15 anos”, diz Cara, “primeiro com a BMW para peças automotivas e também para o centro técnico agora conhecido como Institute de Soudure [(Saint-Avold, França)]. Em 2006 e 2012, iniciamos dois grandes projetos para monitorar a cura das pás do ventilador de motores de aeronaves feitas com RTM e pré-formas tecidas em 3D. A Safran tem um sistema de aquisição de dados que desenvolvemos para eles em seu laboratório de compósitos perto de Paris. Eles podem gravar até 100 sinais simultaneamente [(fluxo de calor, temperatura e pressão]) e analisá-los para cura e monitoramento dos ciclos do processo. ” A TFX também trabalhou com a Hexcel em seu laboratório em Les Avenières, França, para monitorar a qualidade e os ciclos de processamento com resinas termofixas injetadas em pré-formas secas. Os sensores TFX também foram usados em um projeto com IRT-M2P (Porcelette, França) para demonstrar RTM de compressão (Saiba mais). “Nossos sensores são muito eficientes para processos rápidos, como moldagem por compressão, inclusive com compostos de moldagem SMC e BMC”, observa Cara. “Também ganhamos um prêmio JEC Innovation em 2016 com a Huntsman Advanced Materials [(Basel, Suíça)] por um desenvolvimento intitulado‘ Peças estruturais de epóxi com qualidade de autoclave em menos de 1 minuto ’”.
A TFX possui sensores para todo tipo de processo de moldagem de compósitos, baseados no método de transferência de calor ao sensor:condução (RTM, moldagem por compressão e injeção), convecção (autoclave, forno) e radiação (enrolamento de filamento, AFP). Os sensores usados no projeto INNOTOOL 4.0 eram condutores, projetados para serem embutidos em moldes RTM de metal. “Eles fornecem um sinal excepcionalmente repetível a uma distância de até 1 milímetro da superfície da ferramenta e do material composto”, observa Cara.
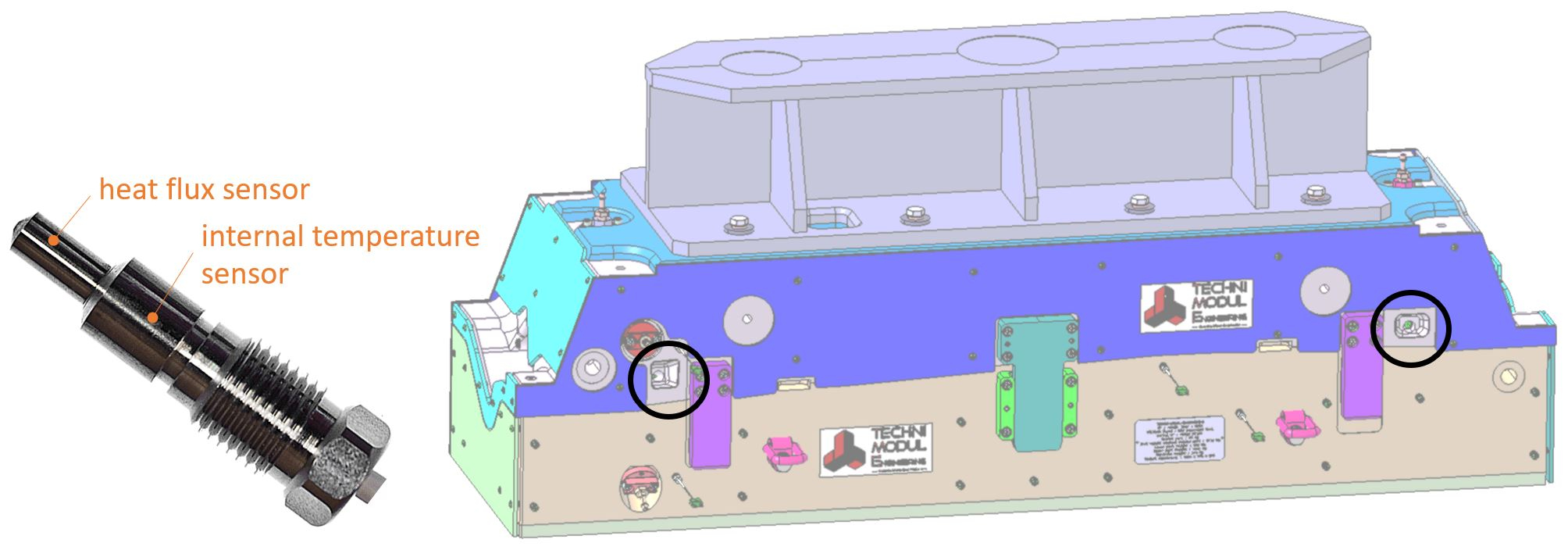
A TME instalou dois sensores TFX-191 - um na entrada da resina e um na saída da resina - no molde superior do conjunto de ferramentas de produção combinado que foi enviado para a NLR (Fig. 1, 2). A NLR usou esta ferramenta de produção para fazer peças de demonstração HECOLAG em março e abril de 2021. Os sensores TFX-191 são para ferramentas metálicas espessas.
Em paralelo, a TME pegou uma ferramenta interna menor usada para fazer placas de amostra de CFRP e a modificou com dois sensores TFX-224, que são mais curtos, para ferramentas mais finas (Fig. 3). Este conjunto de ferramentas de placa RTM foi então usado para conduzir testes de demonstração de sensor de acordo com os objetivos INNOTOOL 4.0 descritos acima. “Esses sensores são semelhantes aos que usamos para Safran”, diz Cara, “mas agora foram aprimorados para serem muito mais compactos e sensíveis.” Os sensores foram colocados próximos ao centro da peça e à saída da resina. Além dos sensores de fluxo de calor, a TFX desenvolveu e forneceu dois sistemas de aquisição de dados - um entregue ao Isojet e outro usado pela TME para os testes de placa CFRP.
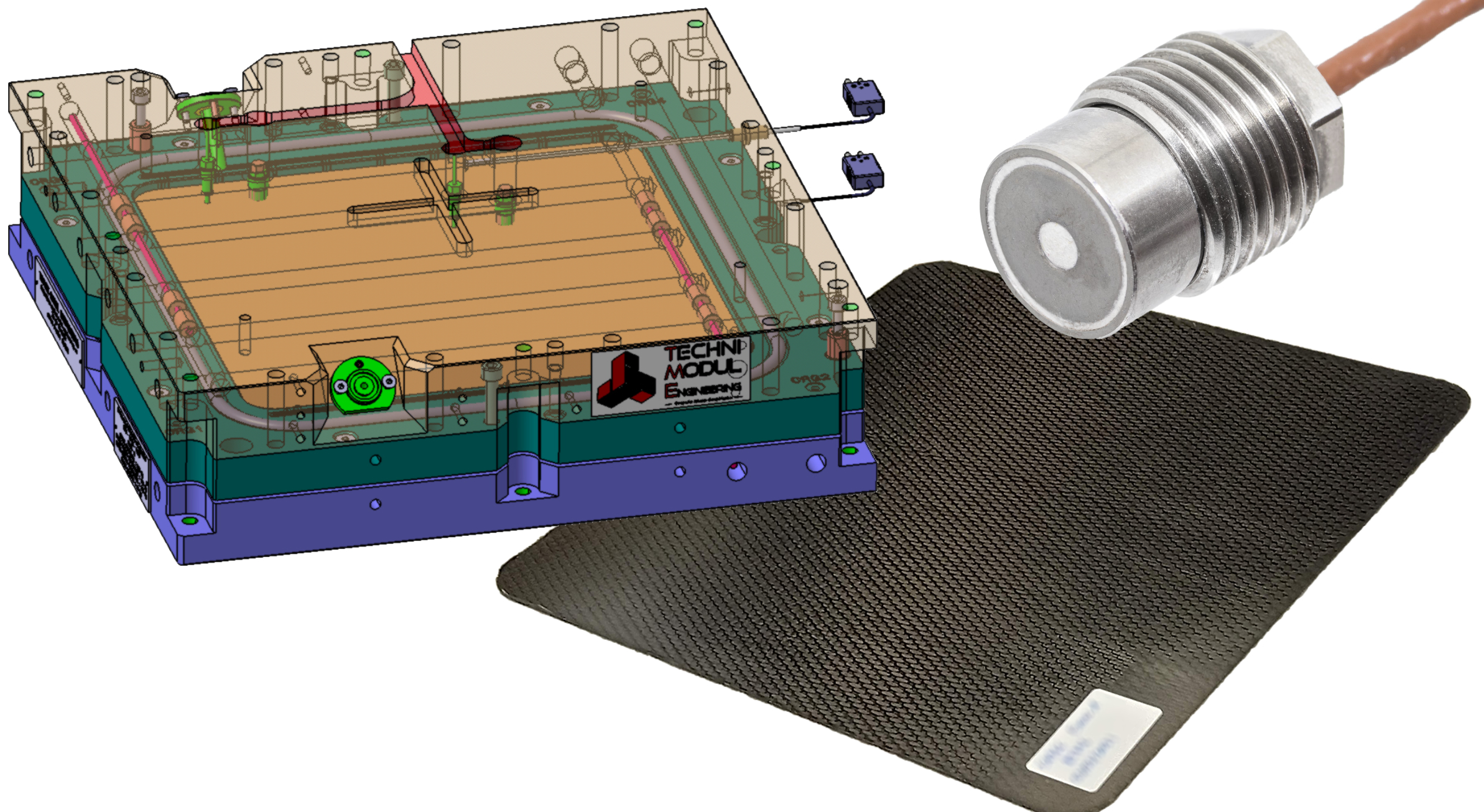
resultados do teste INNOTOOL 4.0
Os testes que a TME conduziu usando sua ferramenta de placa modificada com sensores TFX testaram duas resinas diferentes - HexFlow RTM 6 e PRISM EP 2400 - bem como a influência da espessura da peça e do tempo de cura geral. “Os sensores forneceram bons sinais para monitorar o ciclo de cura”, diz Cara. “A equipe então analisou as curvas de cura e mostrou que o tempo de cura para RTM 6 poderia ser reduzido em pelo menos 30 minutos a partir da cura de duas horas prescrita.”
Isso pode ser visto na curva abaixo, onde t =0 horas é o início da injeção. Observe que o tempo de cura começa quando a temperatura atinge 180 ° C e o fim da cura corresponde a 99% do nível de cura relativo (consulte o eixo vertical à direita). O fim da cura também coincide com a estabilização do fluxo de calor bruto.
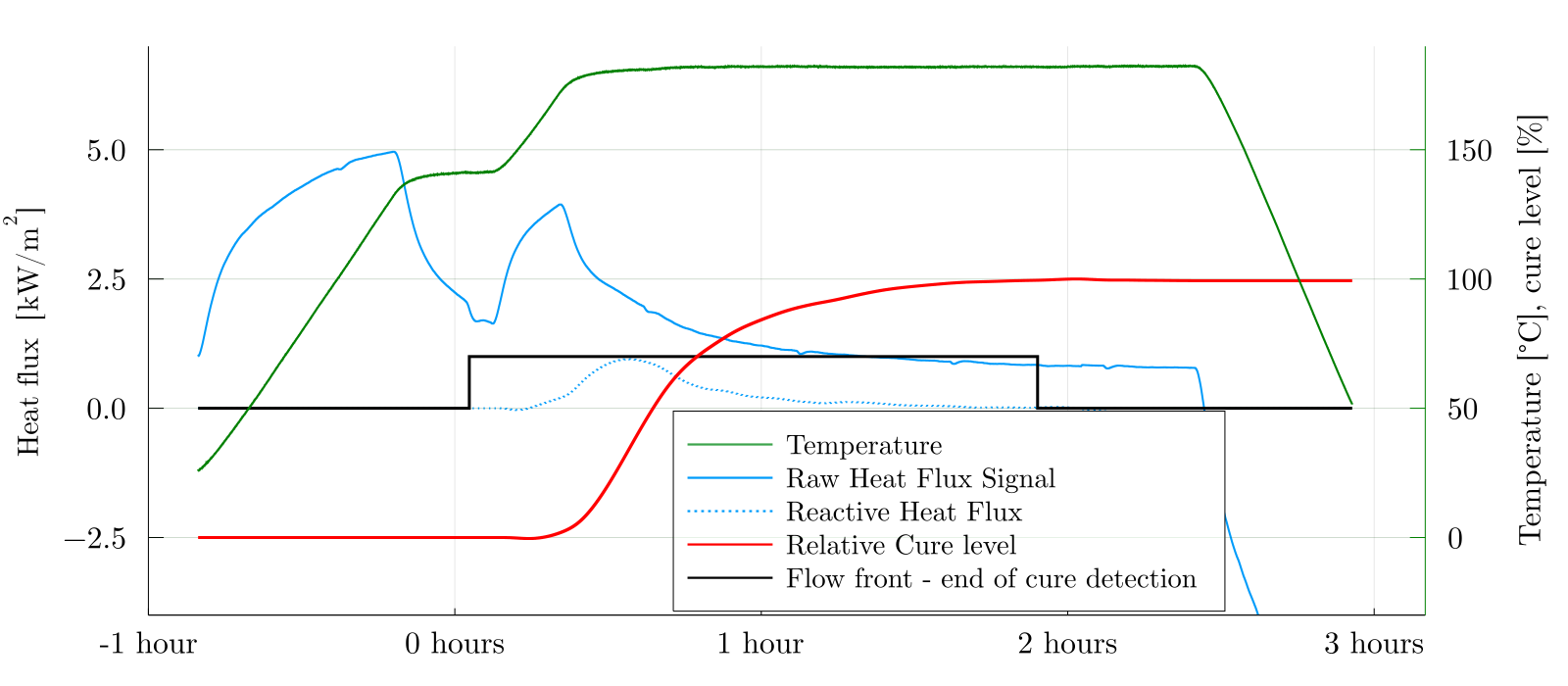
Isso foi verificado por medições do estado de cura de peças desmoldadas usando análise mecânica dinâmica (DMA), uma técnica de laboratório alternativa para DSC que mede a temperatura de transição vítrea (T g ) para compósitos. “Os resultados do DMA confirmaram que para a resina RTM 6, o T g permanece inalterado após 90 minutos de cura a 180 ° C ”, acrescenta.
O efeito da espessura também foi investigado. “As primeiras placas CFRP testadas pela TME em seus testes de demonstração de sensores tinham menos de 2 milímetros de espessura”, observa Cara. “Essas placas também tinham um alto volume de fibra (50-60%) e um ciclo de cura lento para evitar problemas exotérmicos e potenciais com estresse térmico e qualidade das peças. Tudo isso é muito normal para peças aeroespaciais, mas significa que há muito pouca resina e, portanto, a quantidade de fluxo de calor liberado pela reação da resina foi pequena. Então, estávamos, de fato, procurando a agulha do fluxo de calor devido à cura da resina dentro de um oceano de aquecimento da ferramenta e da peça ”.
Em outras palavras, como Cara explica, “A maioria dos ciclos de cura de RTM aeroespacial envolve a injeção de resina em uma temperatura e, em seguida, a aceleração para curar em uma segunda temperatura mais alta. Assim, ao terminar a injeção, você aquece a ferramenta até a temperatura de cura, o que gera um grande fluxo de calor em todo o sistema. ” No entanto, como acontece com o teste de DSC, a chave para monitorar a cura com sensores de fluxo de calor é medir o calor liberado durante a polimerização / cura e exibir essas medições em uma curva de fluxo de calor versus temperatura no sistema de moldagem e tempo. “Então, inventamos um método que nos ajuda a subtrair a linha de base de aquecimento do molde e a condução desse calor para a peça, de forma que seja possível identificar o fluxo de calor da reação da resina.”
Assim, embora as condições do processo nas placas finas iniciais fossem muito desafiadoras, diz Cara, “ainda podíamos ver o fluxo de calor da reação da resina. No entanto, ao fazer também peças mais espessas, fomos capazes de ver exatamente a diferença nos níveis de fluxo de calor de acordo com a espessura da peça e isso validou nosso monitoramento de cura nas peças finas. ” Observe que a curva acima (também mostrada na foto de abertura) foi obtida com a resina RTM 6 em uma placa de 3,2 mm de espessura.
Os resultados da detecção da frente de fluxo de resina, no entanto, foram mais problemáticos. “Para o sensor próximo à saída, pudemos ver muito bem o fluxo, mas não para o sensor próximo ao centro, onde a resina chegou muito tarde”, diz Cara. “A detecção de fluxo frontal com sensores de fluxo de calor exige que o fluxo de resina produza uma mudança no campo térmico local. Isso ocorre quando a resina não está na mesma temperatura da pré-forma. ” Ele observa que ΔT maior que 0,1 ° C é suficiente para detecção. “Porém, com os testes de placa de CFRP fina, a temperatura no molde era muito uniforme e a resina chegava muito lentamente. Portanto, o contraste térmico não foi suficiente para detectar a chegada da resina em relação ao ruído térmico no sistema como um todo. A chegada da resina na saída, no entanto, foi mais rápida devido aos corredores [lacunas entre a pré-forma e a borda do molde, consulte “Fabricação das peças de geometria complexa do RAPM”], o que ajuda a criar um contraste térmico maior, mais fácil de detectar e monitorar. ”
Cara sugere que o monitoramento da frente do fluxo de resina poderia ser melhorado com novos sensores ativos que a TFX desenvolveu, que usam uma capacidade de aquecimento integrada dentro do sensor. “Isso permite que os sensores ajudem a fornecer o contraste térmico necessário em peças e processos onde é inerentemente difícil”, explica ele.
Estendendo a capacidade de controle de processo composto
“Estamos felizes com o trabalho que concluímos até agora”, diz Torres, “mas este é apenas um primeiro passo. O objetivo é usar esses sensores de fluxo de calor para gerenciar o processamento de compósitos em ambientes de produção. ” Isso é possível, diz Cara, enviando automaticamente um sinal do sistema de sensores para o equipamento de injeção com base na chegada da resina e para a prensa com base em uma inclinação zero na curva de cura. Torres acrescenta que a TME possui sistemas de controle de processo da injetora e da impressora RTM que gerenciam a temperatura e a pressão. “A próxima etapa”, diz ele, “é integrar os sensores TFX a esses sistemas de controle e gerenciar o processo geral a partir de um laptop”. Cara observa que os sensores TFX e a aquisição de dados também funcionam com sensores de pressão (por exemplo, Kistler, Winterthur, Suíça) para auxiliar no controle geral do processo, e sua empresa está desenvolvendo um sensor que medirá o fluxo de calor, temperatura e pressão em um único dispositivo integrado.
Mas esse controle de processo é acessível? Cara diz que o investimento inicial de $ 10-30.000 para o sistema de monitoramento geralmente obtém um retorno na fase de desenvolvimento, reduzindo a tentativa e erro por meio de processos aprimorados e compreensão das peças. “O sistema passa a fornecer economia durante a produção, reduzindo o tempo de ciclo, garantindo a repetibilidade e fornecendo detecção precoce de desvios ou não conformidades.”
Na GKN Fokker, Vergouwen acredita que uma vez comprovada a capacidade de reduzir o tempo de ciclo e melhorar os custos, “então é possível imaginar compostos não apenas no tipo de componente de trem de pouso demonstrado nos projetos INNOTOOL 4.0 e HECOLAG, mas em todos os tipos de partes. Isso abriria nosso espaço de design e nos permitiria expandir ainda mais os limites do trem de pouso leve. ” Besson vê uma aplicação ainda mais ampla:“Este tipo de controle de processo pode ser desenvolvido para todos os tipos de moldes e peças compostas.”
Resina
- Tipos de sensores com seus diagramas de circuito
- ams para iluminar a Sensors Expo 2019 com demonstrações inovadoras
- Mapeamento do fluxo de temperatura doméstico com sensores baratos
- Meça temperaturas com um sensor DS18B20 de 1 fio e Raspberry Pi
- Controle de um efeito com sensores reais
- Leitura de sensores analógicos com um pino GPIO
- Sensores analógicos lendo com Raspberry Pi e Zabbix Supervisor
- Controlador de irrigação Win10 IOT com sensores de umidade
- Melhorar o monitoramento da poluição do ar com sensores IoT
- Simplificando a fabricação de sensores com compostos adesivos