Aeroespacial e Defesa em Foco:Componentes do Trem de Pouso
Como parte 3 de nossa série sobre fabricação aeroespacial, analisamos detalhadamente a fabricação de componentes de trem de pouso com foco na experiência dos fabricantes de ferramentas ao trabalhar com alguns dos maiores fabricantes e subcontratados aeroespaciais do setor.
Até agora, neste ano, nos aprofundamos na fabricação de asas de aeronaves e componentes de motores na indústria aeroespacial e de defesa. Agora vamos aprofundar os componentes do trem de pouso.
Como uma das seções mais críticas da aeronave, os sistemas de trem de pouso suportam uma carga pesada. Literalmente, todo o peso de um avião, caça ou helicóptero é suportado pelo trem de pouso durante o táxi, pouso e decolagem. E dependendo de onde a aeronave está pousando, como em um porta-aviões no meio do Oceano Pacífico, os materiais que compõem o trem de pouso podem diferir.
“O trem de pouso retrátil que agora é comum em aeronaves comerciais e militares foi desenvolvido pela primeira vez para o avião Triad de Glenn Curtiss em 1911”, escreve o National Air and Space Museum em um post no blog.
O trem de pouso de um avião controla como ele se comporta no solo, mas também como um avião se comporta no céu, pois afeta outras áreas, incluindo peso, desempenho e confiabilidade.
Conversamos com três dos principais fabricantes de ferramentas do setor para obter uma perspectiva sobre os desafios de materiais e nuances de corte de metal - e discutimos exemplos do mundo real em que ferramentas e usinagem fizeram a diferença para fabricantes aeroespaciais.
Materiais usados nos componentes atuais do trem de pouso
Predominantemente, os fornecedores de ferramentas dizem que veem dois tipos principais de material nos grandes componentes do trem de pouso atual, que incluem o 300M, um aço de baixa liga que é muito duro, ou o Ti-5553, uma liga de titânio, conhecida por sua resistência e temperabilidade.
Em aeronaves comerciais, Boeing e Airbus usam ambos os materiais, mas isso depende dos requisitos de carga do modelo do avião, diz Scott Causey, engenheiro de aplicação da Seco Tools.
A maioria desses tipos de materiais é usada em qualquer variedade desses componentes do trem de pouso, incluindo - a viga do caminhão, os suportes, os links de torque e o suporte, que às vezes também é chamado de "cilindro principal".
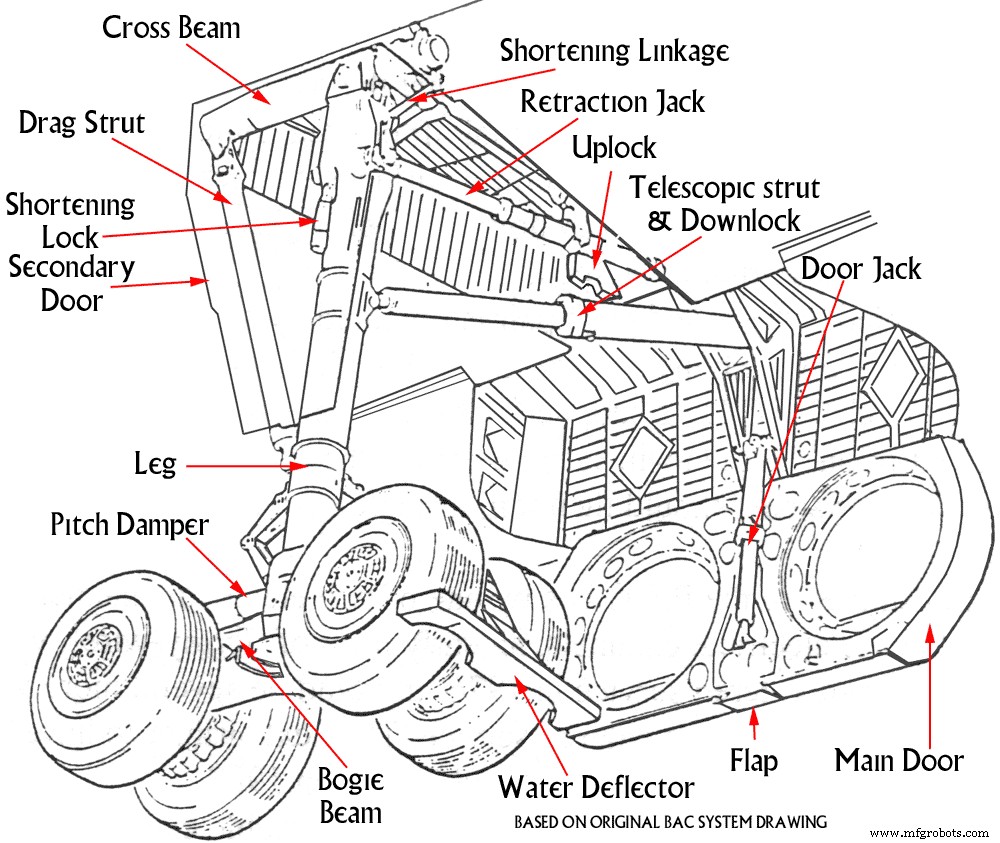
Fonte:Concordesst.com
Mas existem outros materiais usados em outros componentes do trem de pouso, incluindo alumínio, liga de aço 4340 e um pouco de titânio, que é frequentemente encontrado em suportes, braçadeiras e elos do trem de pouso, explica Causey.
E há outros componentes menores no trem de pouso, incluindo flanges, cavidades, furos escareados, furos perfurados e muitos pontos de conexão, diz Mark Francis, engenheiro da equipe aeroespacial e de defesa da Kennametal. Por exemplo, um buraco pode ter 8 a 10 polegadas de diâmetro e 36 polegadas de profundidade. Você precisa de ferramentas e processos específicos para realizar a tarefa.
"Outro material que vemos para casos de uso de porta-aviões muito específicos é o uso do AerMet 100 - um aço de alta resistência e difícil de usinar", diz Francis. "Ele pode suportar cargas de alto impacto - pense na resistência à fratura e na tenacidade necessárias para um porta-aviões pousando na pista curta de um porta-aviões - além de ser muito resistente à corrosão com sal e água no oceano."
O AerMet 100 é usado quase exclusivamente em caças com destino a porta-aviões.

As áreas mais desafiadoras dos componentes do trem de pouso para usinagem e fabricação
Como você pode imaginar, os maiores componentes do trem de pouso podem ser lentos para usinar – principalmente por causa de seu tamanho. Peças como o cilindro principal e a viga do caminhão, comumente chamadas de “viga do eixo”, podem se estender até cerca de 25 pés de altura.
Outras partes difíceis incluem o controle deslizante, ou “cilindro interno”, diz Causey.
“Os furos de identificação nessas peças podem ter até 70 polegadas de comprimento”, diz Atul Sharma, engenheiro de aplicação aeroespacial da Seco Tools. “Eles são muito grandes e longos. E a tolerância pode ser difícil de manter ao cortar. A fixação pode ser um desafio.”
Todos os fabricantes de ferramentas com quem conversamos deixaram bem claro que essas peças grandes geralmente demoram a usinar. Há uma suposição de que você pode usinar 300 milhões de materiais a uma alta superfície de pés por minuto. Mas a realidade é que essas peças grandes são simplesmente muito pesadas e grandes - e exigem acessórios especializados para evitar que as peças vibrem e tirar o máximo proveito da ferramenta de corte.
Mas em comparação com muitos materiais de níquel, Waspalloys e Rene, esses materiais de aço e titânio não são incrivelmente difíceis, explica Bill Durow, gerente global de escritório de projetos de engenharia aeroespacial, da Sandvik Coromant.
“Em muitos casos, é a escala dos componentes. Eles são enormes”, diz Durow. “E nada é uniforme. Eles geralmente têm formas estranhas, então você não pode simplesmente jogá-lo em um torno necessariamente. Muitas vezes, os fabricantes aeroespaciais estão usando um grande moinho de furos ou grandes máquinas de pórtico, que levam muito tempo.”
Veja os sistemas de trem de pouso desde o projeto até a fabricação e a peça acabada. Fonte:Sistemas de Pouso Safran
Os fabricantes de ferramentas estão vendo uma tendência de alguns fabricantes aeroespaciais se afastarem da máquina de pórtico e fresamento de furo em direção à usinagem do eixo B e usando aplicativos de fresamento de torneamento para menos configurações e menos fixações - e realizando perfis de 4 a 5 eixos em torno das peças.
Mas esse método mais novo requer mais programação – e um novo pensamento sobre geometrias de corte para ajudar a aumentar a eficiência na produção de trens de pouso. Não é incomum que o trem de pouso leve meses para ser concluído do início ao fim.
O que há de novo no setor aeroespacial? Inovação em manufatura aditiva. Leia “ A incrível evolução da impressão 3D no setor aeroespacial e de defesa .”
Usinagem do trem de pouso no mundo real
Aqui estão três exemplos de peças e componentes de trem de pouso do mundo real sendo feitos onde a ferramenta certa ou a nova abordagem causaram impacto.
Link de torção
Desafio: Um cliente da Seco Tool estava lutando com um link de torção - uma área do trem de pouso que acopla os cilindros interno e externo - enquanto cortava material de titânio 10-2-3. Os tempos de ciclo foram de 60 horas com seis configurações distintas. O cliente estava sempre muito atrasado na entrega das peças e estava prestes a perder o contrato com um OEM.
Solução: A Seco Tools trabalhou com o cliente e parceiros para atender a usinagem do cliente por meio de uma parceria com a DMG Mori. A Seco Tools ajudou a encontrar uma abordagem totalmente nova começando do zero com desenhos, modelos e ferramentas.
Resultado: O cliente reduziu as configurações de fabricação de peças e ferramentas de seis para duas – e diminuiu os tempos de ciclo de 60 horas para 23 horas, ou 62%. Isso impulsionou a produção e permitiu que a entrega das peças fosse pontual. Em última análise, a solução permitiu que o fabricante aeroespacial mantivesse seu contrato.
Ferramentas projetadas para o material
Desafio: Um componente de trem de pouso forjado de 400 libras feito de Ti-5553 estava queimando ferramentas para um cliente da Kennametal. O cliente estava programando uma nova troca de ferramenta a cada 30 minutos. Quando terminada, esta parte pesa cerca de 210 libras. Mas esse material de titânio tinha uma caixa alfa que era difícil de romper.
Solução: A Kennametal usou fresas com design helicoidal com pastilhas de 8 lados e brocas projetadas especificamente para esta classe de titânio específica e resistente.
Resultado: O tempo de desbaste passou de 25 horas para 15 horas. O tempo de ciclo foi reduzido em 40%. A vida útil da ferramenta foi aumentada em 300%:as ferramentas agora duravam 120 minutos antes que uma nova aresta de corte fosse necessária.
Uma nova abordagem usando uma ferramenta existente
Desafio: As peças para os componentes do trem de pouso estavam recebendo muito movimento de 5 eixos e da ferramenta, pois uma ferramenta instalada estava pegando a parte de trás da pastilha - e quebrando o parafuso, pois o cortador tinha uma trava de olho para mantê-lo apertado. O cliente aeroespacial teve que interromper sua produção com muita frequência, pois as peças exigiam muita intervenção manual e babá. As coisas estavam se movendo muito devagar.
Solução: A Sandvik Coromant aplicou uma ferramenta originalmente projetada para usinagem de lâminas na usinagem horizontal e a aplicou a esta aplicação vertical – e sugeriu a rampa ou “cura” da ferramenta para que ela fosse levantada um pouco, de dois a três graus, para evitar o corte para trás da ferramenta . Ele também usou técnicas de bossagem redonda e teve um desempenho muito bom.
Resultado: Segurança do processo. O movimento de inserção foi embora. Os parafusos de inserção não estavam mais quebrando. E o cliente foi capaz de parar de cuidar do processo e passar para um ambiente de produção mais “sem luz”. Os operadores podiam trabalhar em várias máquinas simultaneamente.
Como você está lidando com a redução do tempo de ciclo em sua fabricação aeroespacial? Converse com seus colegas no fórum metalúrgico . [registro obrigatório]
Tecnologia industrial
- Fabricação de aditivos com compostos na indústria aeroespacial e defesa
- Os Fatores de Risco Complexos do Aeroespacial e da Defesa
- A incrível evolução da impressão 3D no setor aeroespacial e de defesa
- Aeroespacial em foco:Perfuração e Fresamento Compósitos CFRP
- Desenvolvendo novos caminhos para o crescimento da receita com IIoT para OEMs aeroespaciais e de defesa
- Os 4 principais desafios enfrentados pela indústria OEM aeroespacial e de defesa
- Desafios de implementação da indústria 4.0 na fabricação aeroespacial e de defesa
- Componentes da placa de circuito e suas aplicações
- O mercado de componentes aeroespaciais e componentes de aeronaves de precisão
- Teste de PCB:um foco em testes funcionais e em circuito