Projeto da lâmina da turbina hidrelétrica impulsionada por compósitos
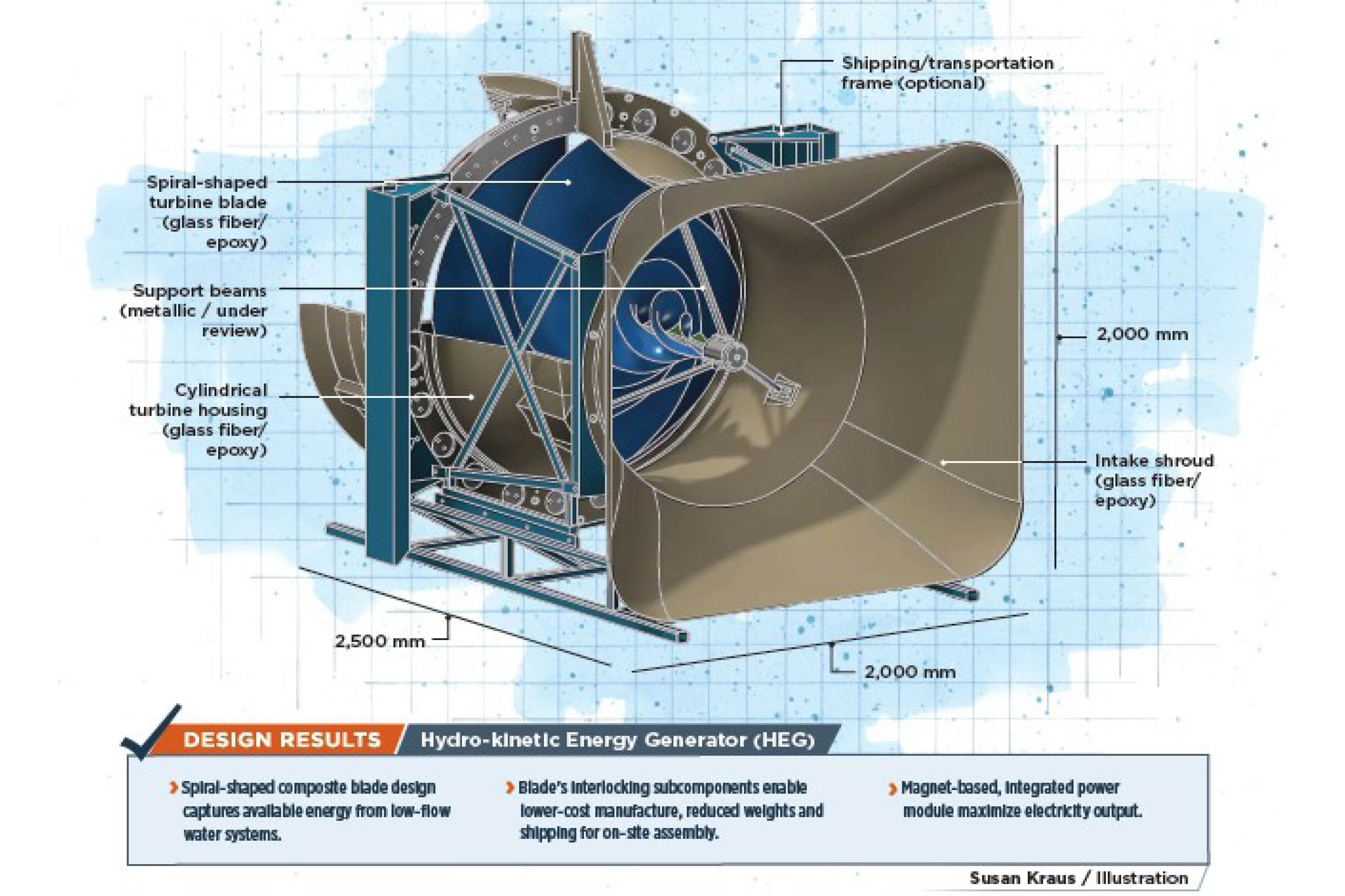
O termo “energia hidrelétrica” muitas vezes traz à mente imensas operações conduzidas por infraestrutura construída de propósito, como sistemas de barragens e grandes turbinas com lâminas de turbina tradicionalmente metálicas, baseadas em hélice. No entanto, muitas áreas estão ficando sem capacidade para grandes usinas hidrelétricas de alta potência. Ao mesmo tempo, a demanda por mais geração de energia renovável de baixo custo continua a crescer.
O Departamento de Energia dos Estados Unidos (DOE), em seu relatório “Visão Hidrelétrica” de 2018 descrevendo o estado atual da energia hidrelétrica nos Estados Unidos e suas metas para o futuro, previu que o crescimento do mercado hidrelétrico dos EUA - de 101 gigawatts (GW) de capacidade de energia em 2018 para uma capacidade potencial de quase 150 GW em 2050 - exigiria novas tecnologias avançadas que podem fornecer mais energia a custos mais baixos.
Uma solução potencial poderia ser geradores hidrelétricos menores capturando energia inexplorada de sistemas de água de baixo fluxo, como canais de irrigação e riachos, de acordo com Darren Wren, gerente geral da Kinetic NRG (Gold Coast, Austrália). Fundada em 2016 pelo falecido fundador, Paul Camilleri, a Kinetic NRG é uma empresa de energia renovável com financiamento privado focada no desenvolvimento de uma nova tecnologia de geração hidrelétrica para fornecer eletricidade confiável de baixo custo.
A primeira tecnologia da empresa é chamada de sistema Gerador de Energia Hidrocinética (HEG), que mede 1,5 metros de diâmetro com uma produção de até 30 quilowatts (kW) de fluxos de água de 2,0 metros por segundo. Essa saída o torna um “micro” sistema hidrelétrico de acordo com órgãos de classificação como o U.S. DOE, que define microssistemas como aqueles com até 100 kW de capacidade. Destinado ao uso direto em rios, canais de irrigação ou canais de cauda canalizando a água de barragens existentes, o HEG é projetado para energia hidrelétrica de baixa queda - o que significa que a "queda", ou distância entre a linha de água e a turbina, é inferior a 20 metros.
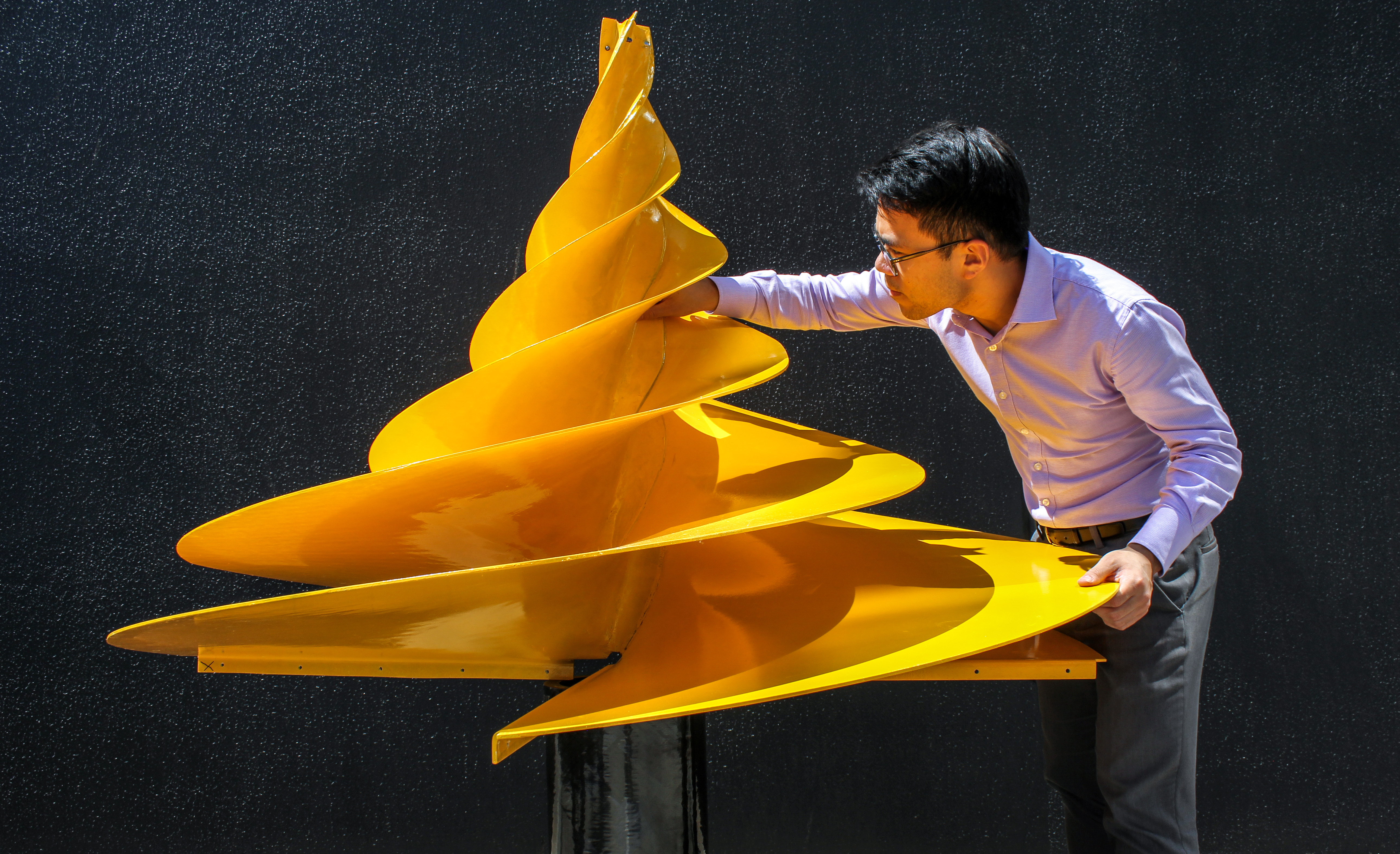
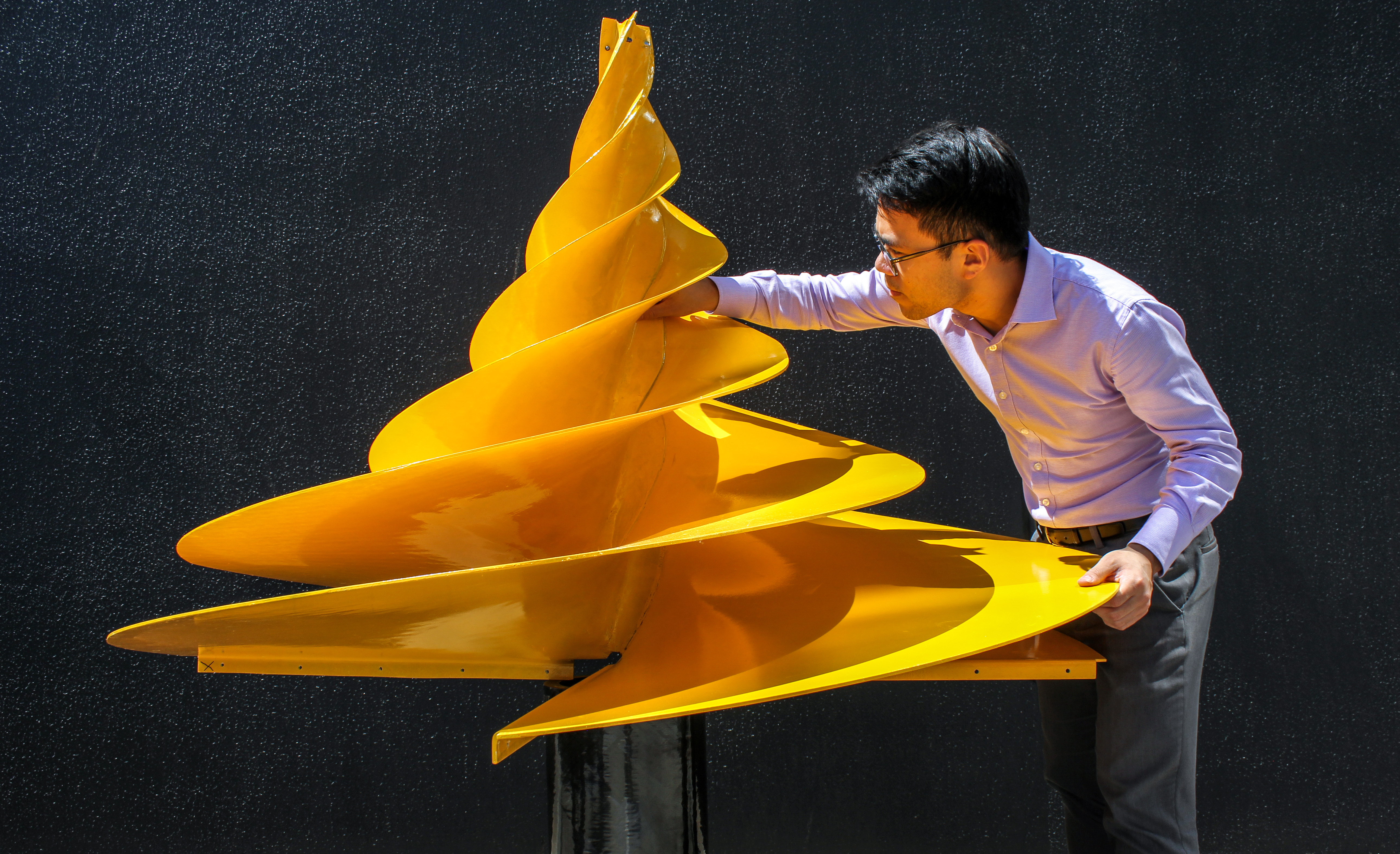
O desenvolvimento do HEG e de sua lâmina de turbina espiral está em andamento há cerca de cinco anos, diz Wren. “Tem sido uma jornada e tanto. O design que temos agora surgiu literalmente por meio de tentativa e erro. ”
Projetando uma lâmina modular fabricável
Os primeiros modelos de lâmina espiral em pequena escala do Kinetic NRG foram formados de metal, mas quando chegou a hora de fabricar o protótipo em escala real de 1,5 metro de diâmetro, “descobrimos que não poderíamos fazer isso”, diz Wren. O conceito era começar com uma peça plana de metal e então formar ou forjar um conjunto de espirais irradiando do centro. “Simplesmente não conseguíamos encontrar uma maneira de acessar certos pontos da peça para criar a força de que precisávamos”, explica ele.
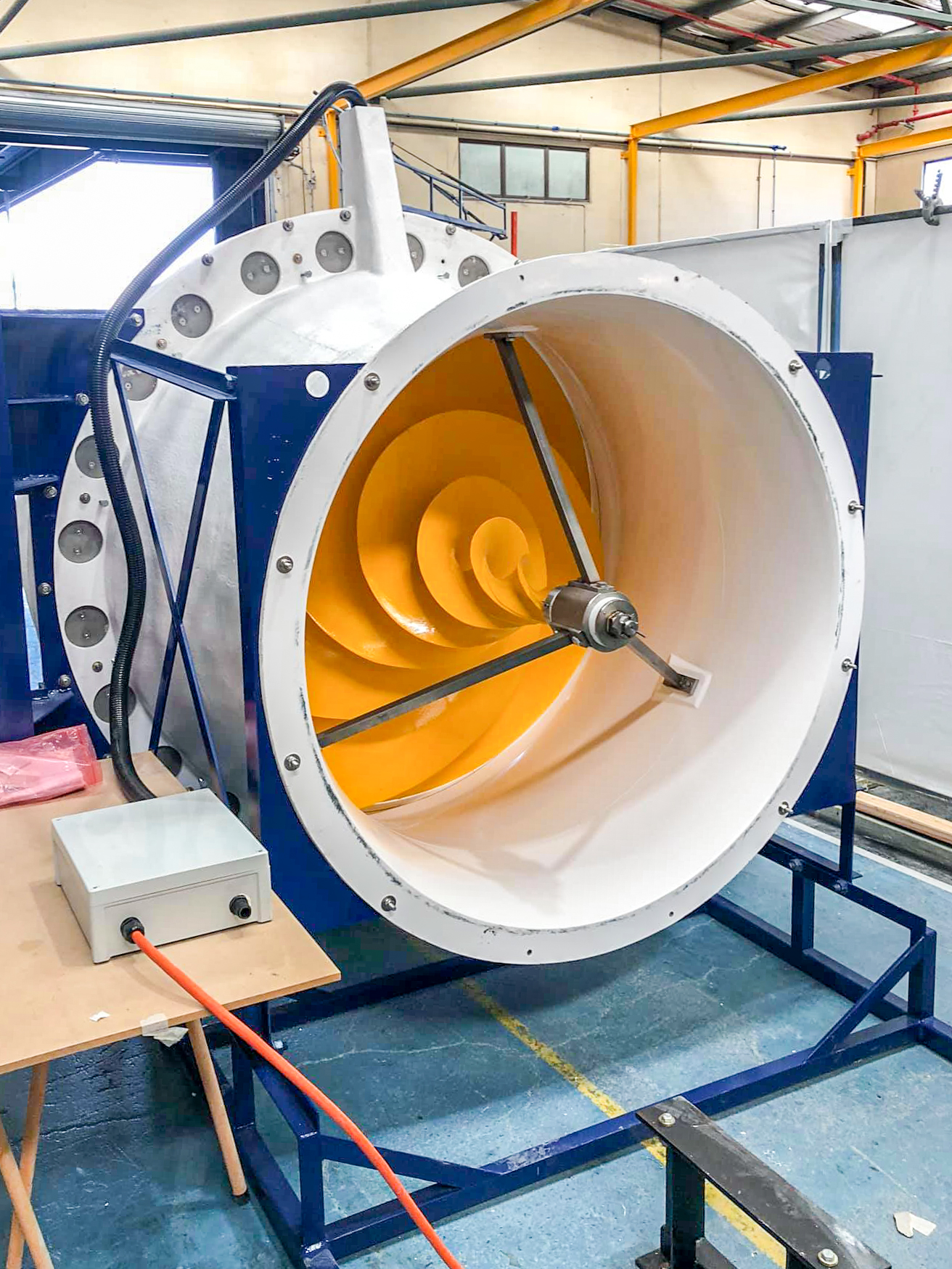
A empresa acabou abandonando seus esforços metálicos, mas não o design em si. Wren diz que a Kinetic NRG fez parceria com uma universidade local para explorar técnicas e materiais de fabricação alternativos, como náilon ou cerâmica, e começou a conversar com empresas de impressão 3D para ver se a manufatura aditiva poderia ser uma opção viável. Ainda assim, nenhuma solução se apresentou que fornecesse a combinação certa de capacidade de fabricação e propriedades mecânicas. Finalmente, após uma jornada de três anos, o Kinetic NRG foi introduzido por meio de uma conexão de rede de abastecimento com a equipe da empresa de engenharia Advanced Composite Structures Australia (ACS-A, Melbourne), especializada em projeto e fabricação de produtos de baixo volume e alto valor - componentes compostos adicionados para uma variedade de mercados finais.
Wren chama o que aconteceu a seguir de "um encontro de mentes", explicando que Kinetic NRG trabalhou com Paul Falzon, gerente geral da ACS-A, e sua equipe em vários métodos para fabricar e projetar a peça usando materiais compostos - materiais que a ACS-A conhecia com a experiência seria capaz de fornecer os requisitos de forma, peso e rigidez que o Kinetic NRG precisava.
O formato inovador da lâmina foi o principal desafio de design do projeto, com requisitos mecânicos para a lâmina baseados, de acordo com Wren, nos padrões definidos pelo U.S. DOE e pela International Electrotechnical Commission. O resto dos componentes do sistema - transmissão, gerenciamento de energia, comunicação, etc. - são produtos padrão de prateleira que são conhecidos por atender a todos os regulamentos necessários.
De acordo com Falzon, o ACS-A primeiro avaliou as tentativas metálicas no design da lâmina e, em seguida, determinou como atingir o formato, as tolerâncias dimensionais e o peso da lâmina exigidos. A lâmina também precisava ser capaz de resistir a ambientes aquáticos e ser rígida o suficiente para suportar o eixo de aço da turbina ao qual está fixada. A equipe ACS-A começou com o design de metal original e fez a “engenharia reversa” de uma lâmina composta de fibra de vidro para corresponder à rigidez original, diz Falzon. No entanto, algumas alterações de projeto precisaram ser feitas ao mudar de uma estrutura formada de metal soldada para um laminado composto. Como Falzon explica, “Demos um passo para trás e perguntamos:‘ Ok, se vamos aproveitar ao máximo os materiais compostos, como é essa coisa? ’”
Depois de várias iterações e discussões, o projeto atual que tomou forma compreende quatro lâminas compostas idênticas que se interligam para formar a forma espiral final. “A lâmina composta é na verdade mais espessa do que o design de aço, mas mais leve por causa da densidade mais baixa dos materiais com os quais estamos trabalhando”, diz Falzon. “Ser mais espesso também significa que temos muito mais rigidez à flexão em comparação com o design de aço, então você obtém um produto muito mais rígido em geral.”
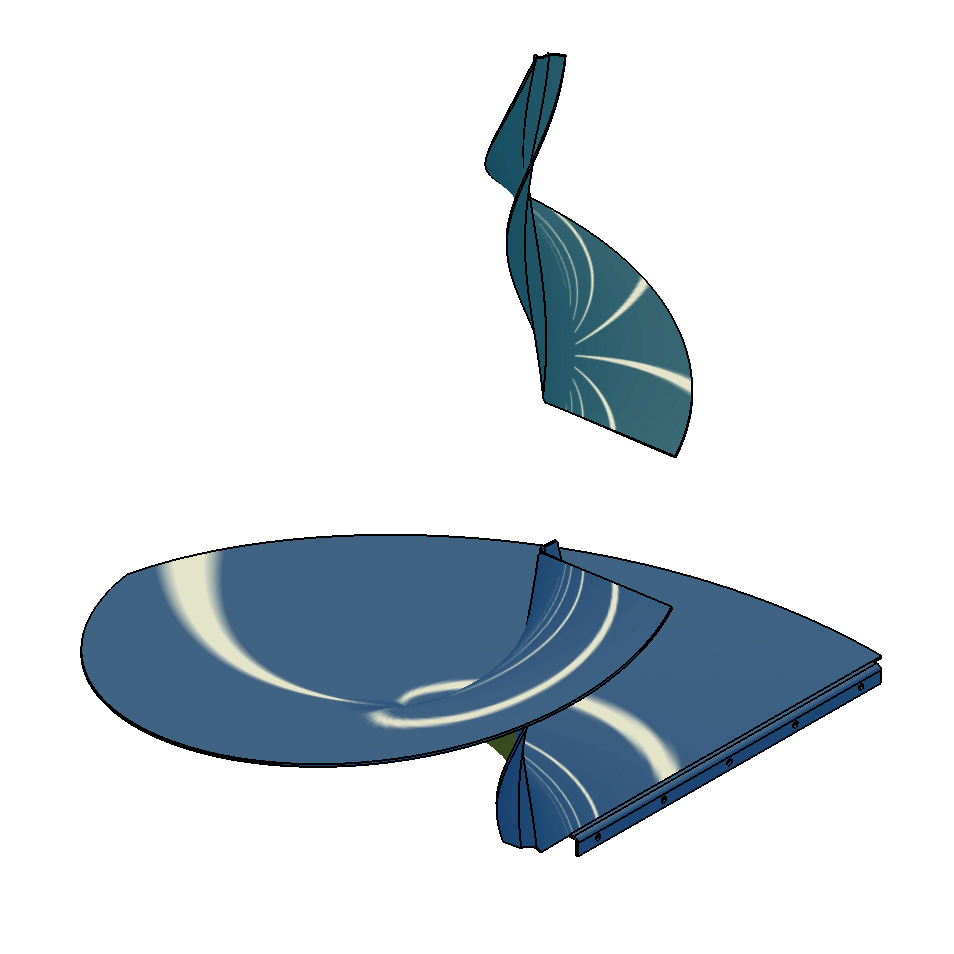
Ferramentas invertidas
Desenvolver a forma da ferramenta, diz Falzon, foi a parte mais desafiadora do processo. A equipe ACS-A avaliou a forma original do conjunto da lâmina usando o software CATIA da Dassault Systèmes (Waltham, Massachusetts, EUA). Isso levou ao desenvolvimento das superfícies da lâmina e conceitos de design de ferramentas. “Quando você olha para as peças como elas são hoje, elas são realmente feitas em uma orientação de cabeça para baixo. O modelo da lâmina teve que ser invertido para criar o ferramental, e é bizarro até que você veja o ferramental real quando ele chega. É bastante complexo ”, diz Falzon. Ele explica que o ferramental teve que ser invertido “para garantir que poderíamos obter o acabamento superficial necessário no lado da lâmina exposta ao fluxo de água” e para garantir que cada um dos componentes da lâmina fabricados pudesse ser desmoldado em uma peça. As ferramentas também tinham que ser precisas:os componentes da lâmina de intertravamento tinham que ser capazes de se alinhar exatamente quando montados, uns com os outros e com o eixo central da turbina. Para o protótipo, o ferramental, fornecido pela Sykes Australia (Sydney), foi fabricado a partir de pasta de ferramental de baixo custo depositada em um suporte de espuma e depois usinado em CNC até a forma final.
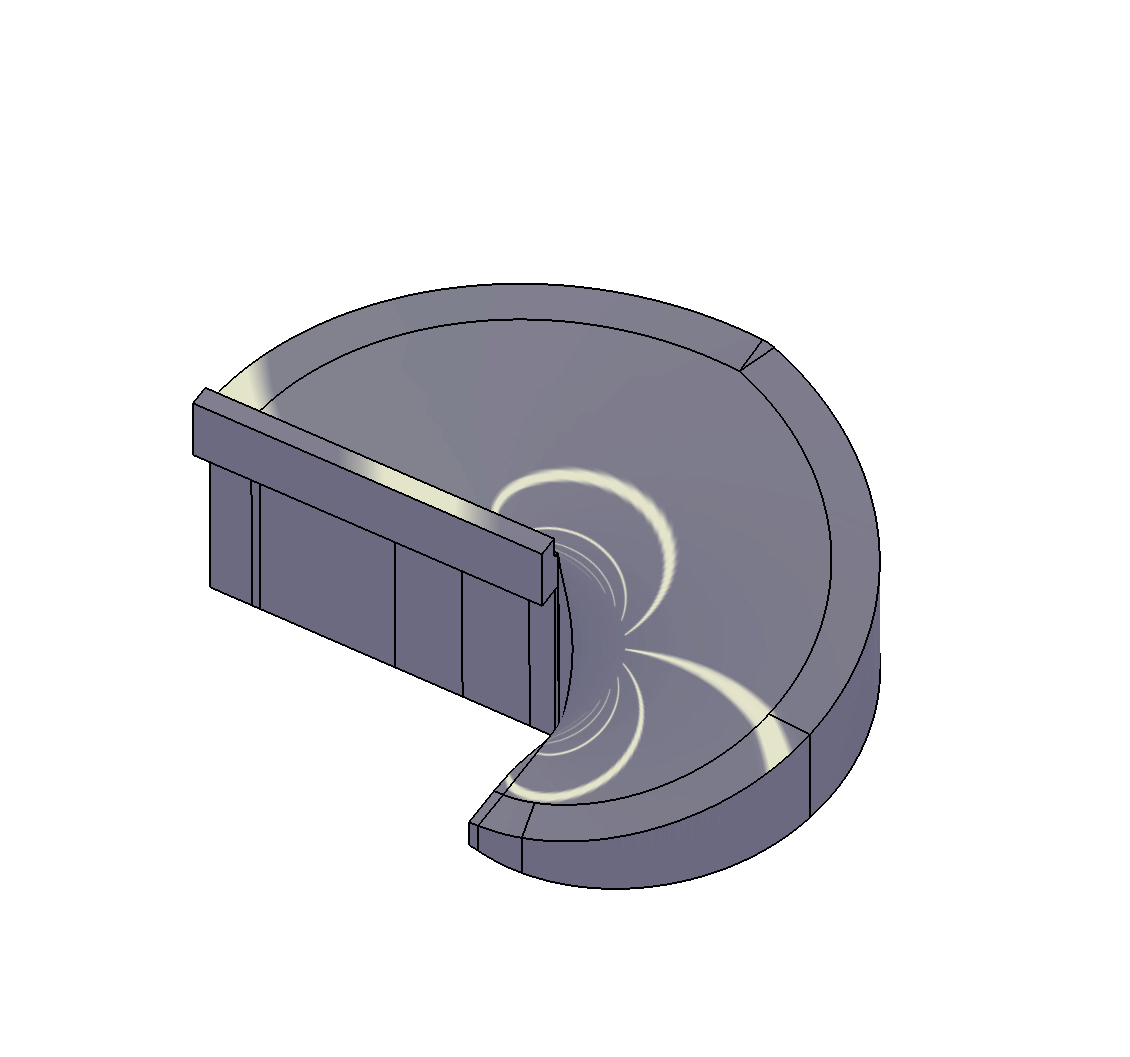
Uma vez que o ferramental foi desenvolvido, o protótipo de lâmina atual em escala real foi construído a partir de tecido não frisado de fibra de vidro (NCF) e resina epóxi, fabricado via layup manual e curado em temperatura ambiente, seguido por pós-cura em um forno em temperatura elevada e aplicação de uma tinta de grau marinho. Os materiais foram selecionados, observa Falzon, para atender aos requisitos estruturais e de custo da peça. Os subcomponentes de intertravamento são colados - escolhidos em vez da fixação mecânica para melhor controle e precisão dimensional na montagem. “O verdadeiro truque”, diz ele, “é garantir que as lâminas possam se encaixar, mas uma vez que laminamos e unimos tudo, forma uma montagem muito rígida que atinge o desempenho de formato hidrodinâmico e estrutural necessário.”
A análise digital da rigidez da estrutura e outras propriedades mecânicas foi realizada usando ferramentas da MSC Software (Newport Beach, Califórnia, EUA). “Este sistema é muito mais eficiente, mais leve e capaz de fazer mais trabalho do que o projeto original”, acrescenta Falzon.
Rumo à produção comercial
De acordo com Wren, a meta de produção inicial da Kinetic NRG será de 950 unidades ao longo de um período de três anos, e então aumentando a partir daí para vários milhares por ano. Os clientes potenciais, diz Wren, podem incluir pessoas físicas e jurídicas, empresas de energia e municípios - uma ampla gama, destacando a versatilidade do conceito de HEG. Os sistemas podem ser instalados como “mini usinas hidrelétricas” dentro de canais de irrigação, ou colocados a jusante de geradores hidrelétricos existentes para gerar energia a partir do fluxo subutilizado, ou como energia suplementar para comunidades ou empresas remotas, diz ele.
Atualmente, o protótipo em escala real do HEG está passando por testes mecânicos na água; enquanto isso, processos de fabricação em grande escala estão sendo avaliados para produção comercial.
A ACS-A espera continuar ajustando o design da lâmina, conforme necessário, dependendo dos resultados dos testes mecânicos e dos requisitos para a fabricação o mais econômica possível. Especificamente, Falzon diz que a ACS-A está explorando processos de pré-formação automatizados “para que possamos obter a forma certa com o mínimo de trabalho manual”, seguido por moldagem por transferência de resina leve (L-RTM) ou outro processo de alta velocidade.
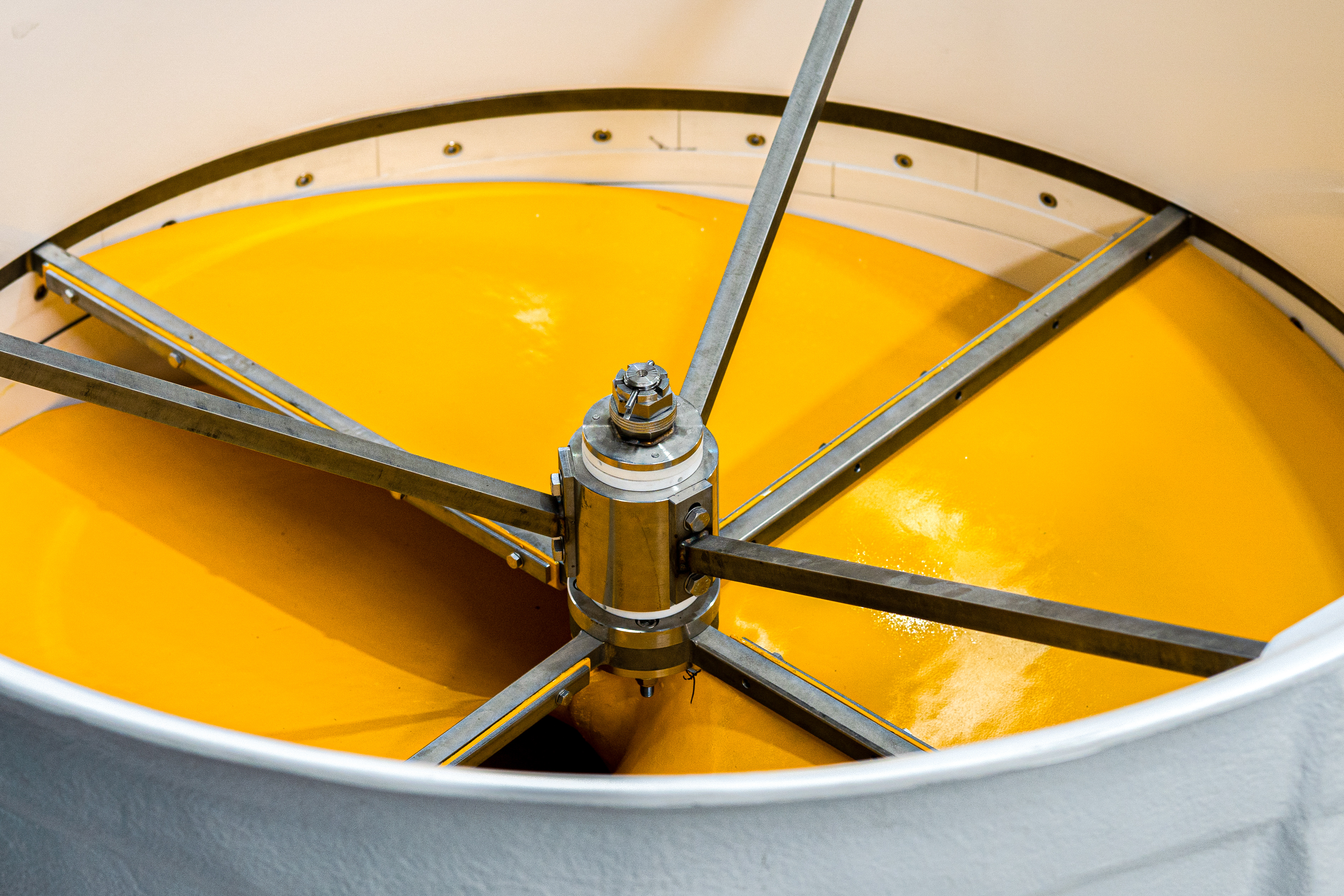
Métodos para a montagem da turbina também estão em avaliação, o objetivo é, diz Wren, que os subcomponentes das pás sejam produzidos modularmente e montados localmente, para evitar os custos e desafios no envio de unidades inteiras em escala real, criando oportunidades de emprego locais e reduzindo os custos de instalação . Para tornar isso possível, o ACS-A pode precisar modificar a maneira como as lâminas se interligam e também o número de subcomponentes em cada montagem. “Ainda teremos as lâminas completas em sua forma original, que ainda será uma parte fundamental disso”, diz Wren, “mas podemos mudar onde as transições ocorrem para fazer a mesma forma em menos componentes para mais fácil montagem no local. ”
As duas empresas também estão avaliando a conversão dos componentes metálicos da turbina em compósitos, para diminuir o peso da montagem geral. “Usaremos vidro onde for apropriado e fibra de carbono onde for apropriado, mas, em última análise, precisamos atingir um ponto de preço para a tecnologia a fim de tornar o custo de geração de energia para o sistema competitivo”, disse Falzon.
Conforme o processo de design e fabricação se aproxima da otimização, o próximo desafio será, de acordo com Wren, garantir o investimento certo e as parcerias de fabricação para atingir os volumes comerciais.
Resina
- Design de referência do emblema inteligente apresenta Bluetooth SoC
- Lidando com os desafios do projeto na medição de energia DC de precisão
- Megger doa para o programa de energia eólica de Iowa Lakes
- Considerações e restrições do projeto do sistema de transmissão de energia
- CompositesWorld SourceBook 2022
- Iniciativa CETEC estabelecida para comercializar tecnologia para reciclabilidade completa de pás de turbinas eólicas
- Compósitos contínuos, Siemens Energy aplica materiais de alto desempenho para geradores de energia
- Compostos como reforços da carroceria
- Compostos de alto desempenho em Israel
- Entendendo a energia hidrelétrica