Compostos como reforços da carroceria
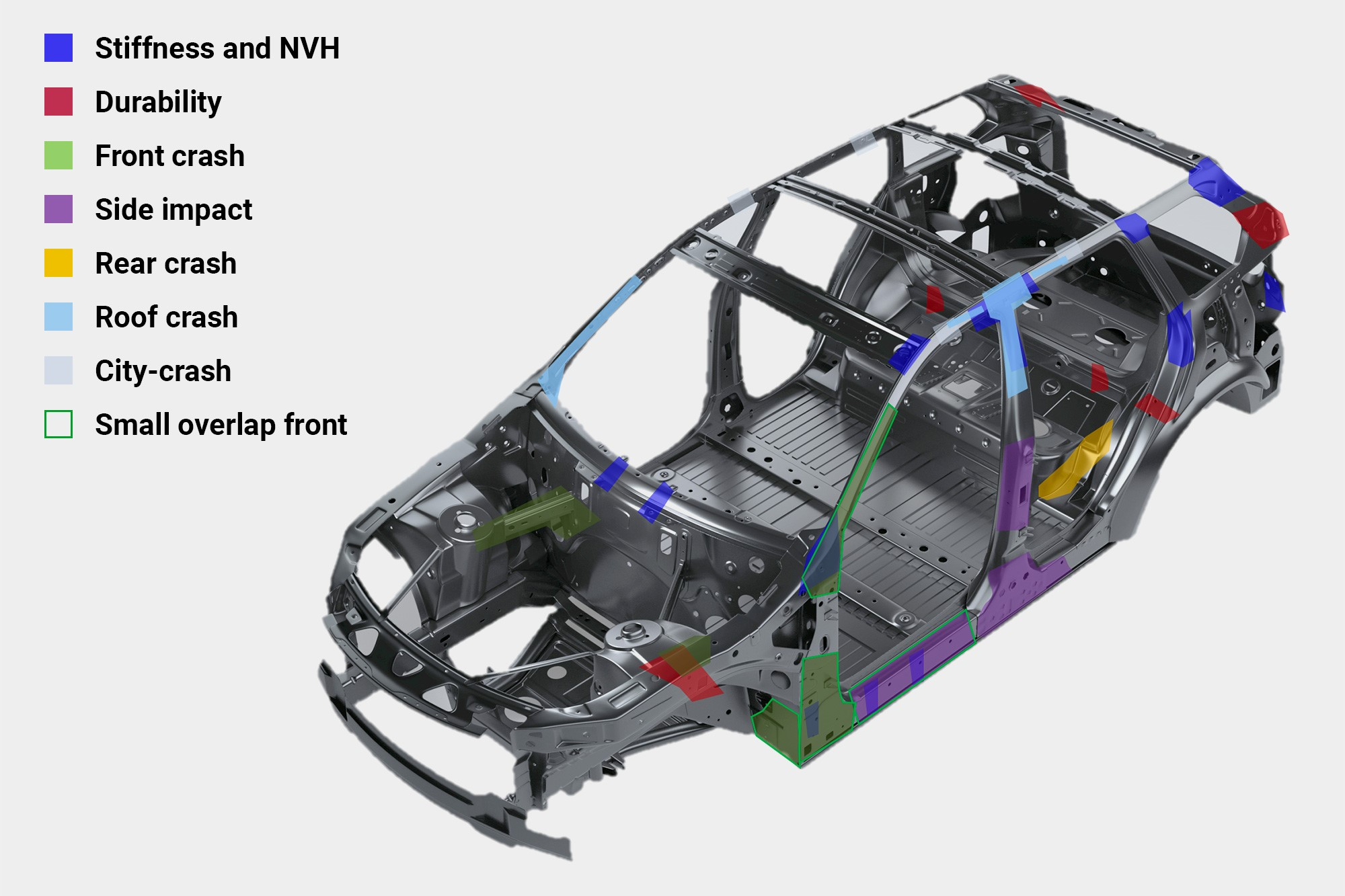
Embora os compostos tenham feito algumas incursões em estruturas automotivas body-in-white (BIW), os materiais usados nesta área do veículo têm sido dominados por aço e, mais recentemente, alumínio. Por causa disso, as montadoras dependem fortemente de soldas e fixadores mecânicos como parafusos e porcas para unir estruturas metálicas. Embora geralmente robustos, as juntas soldadas e os fixadores podem falhar. Eles também fazem pouco para melhorar a rigidez (sem aumentar indevidamente a massa) ou para mitigar ruído / vibração / aspereza (NVH) ou energia de impacto que passa por um veículo. Uma maneira de enfrentar esses desafios é reforçar as juntas e cavidades BIW com compósitos acoplados a adesivos estruturais.
Um exemplo de tal solução é uma classe de materiais / tecnologias chamadas soluções de corpo composto (CBS). Isso inclui inserções estruturais 3D para reforçar estruturas de veículos primários que combinam elementos do BIW ou outras subestruturas de veículos, portadores termoplásticos (com reforço de fibra contínua ou descontínua) e adesivos estruturais espumantes ativados por calor. Os elementos CBS são instalados na parte da carroceria no início da construção do veículo, antes da aplicação do revestimento eletroforético de prevenção de ferrugem (E-coat).
Os componentes CBS são normalmente produzidos em um processo de sobremoldagem de 2K / injeção onde o transportador - incorporando abas de soldagem ou encaixes para unir temporariamente o CBS aos componentes BIW metálicos - é seletivamente sobremoldado com adesivo expansível e possivelmente um selante adicional (em um processo 3K) para funcionalidade adicional. O adesivo não curado seco ao toque (com base na química de epóxi personalizada) pode ser moldado em formas complexas, mas permite a cobertura E-coat de elementos metálicos, mantendo uma lacuna entre as superfícies de metal e compósito antes da expansão induzida por calor durante a pós -Cura em forno de revestimento. À medida que a espuma se expande, as lacunas são vedadas entre o transportador e os componentes circundantes, travando-os juntos em uma "macroestrutura" semelhante a uma caixa que melhora as propriedades mecânicas, especialmente sob cargas elevadas e dinâmicas.
Quando incorporados no início do projeto do veículo, os módulos CBS são opções eficientes em termos de massa e custo para aumentar a rigidez BIW local e global e melhorar a segurança e o conforto dos passageiros com massa menor. Eles também permitem soluções neutras ou de baixo custo versus soluções mais pesadas e totalmente metálicas. Inicialmente usado apenas no setor automotivo, um portfólio crescente de materiais de transporte e adesivos ampliou os usos de CBS, dos quais se destacam a seguir.
Projetado para desafios de desempenho
A tecnologia CBS foi desenvolvida e comercializada pela L&L Products Inc. (Romeo, Mich., EUA). Com uma longa história como fornecedor automotivo de selantes, contramedidas acústicas e reforços para melhorar o desempenho do BIW, a L&L desenvolveu a tecnologia para ajudar os clientes a aumentar a segurança dos passageiros e atender aos requisitos de colisão automotiva mais rigorosos com menor custo e peso, melhorando o processamento e a montagem durante a construção do veículo .
Entre 1995 e 2004, CORE Products, uma joint venture entre L&L e Gurit Essex (Wattwil, Suíça), foi responsável pelo desenvolvimento inicial de aplicativos e fabricação de CBS. A L&L acabou adquirindo todos os ativos da CORE, que agora opera como L&L Products Europe.
A L&L trabalhou em estreita colaboração com seus fornecedores de materiais durante o desenvolvimento inicial e a expansão subsequente da tecnologia CBS. Uma dessas empresas, a Lanxess AG (Colônia, Alemanha), há muito fornece materiais de transporte compostos e caracterização de materiais e suporte de simulação para L&L na Europa.
CBS no aplicativo
Além dos benefícios já mencionados, a tecnologia CBS oferece melhor transição de caminho de carga, gerenciamento de carga multiaxial e absorção de energia; maior estabilidade da seção (resistência ao colapso ou intrusão); NVH inferior; e dinâmica de direção aprimorada e desempenho em colisões com cargas mais altas. Além disso, oferece um tempo de implementação mais rápido durante o projeto / reprojeto do veículo e não requer alterações na sequência de montagem na oficina. Como a tecnologia CBS torna mais fácil controlar a transferência de energia através das estruturas corporais, ao mesmo tempo que minimiza a deformação e / ou intrusão, é ideal para aplicações projetadas para resistir a colisões frontais, laterais ou traseiras ou esmagamento do teto para melhor proteger os ocupantes, compartimentos de passageiros e baterias. Também é útil para estruturas que devem passar por protocolos desafiadores, como os testes de colisão de pequena sobreposição do Instituto de Seguros para Segurança de Rodovias (IIHS, Arlington, Va., EUA).
O que tornou o CBS digno de nota foi que ele estava entre as primeiras abordagens modulares de materiais mistos, era fácil de instalar, oferecia estabilidade térmica e química para o E-coating e não alterava o sequenciamento de montagem do veículo, mas melhorava o desempenho em massa inferior e neutro / custo mais baixo - o santo graal da indústria automobilística.
“A versatilidade de design da tecnologia CBS ajuda a simplificar a montagem em áreas com condições complexas ou de difícil acesso”, explica Núria Ignés, gerente de engenharia de produtos estruturais da L&L Products Reinforce da L&L Products EMEA (Altorf, França). “Por exemplo, o uso da tecnologia CBS em portas e outros fechos não apenas reduz o peso e aumenta a rigidez, mas pode simplificar a fabricação de portas se integrado no início do processo de design. Graças às ferramentas CAE e décadas de experiência, além da combinação de transportador e espuma, que fornece um anexo robusto para o BIW uma vez curado, podemos usar a quantidade certa do material certo no lugar certo para equilibrar rigidez com massa e custo ou absorção de energia com acústica e custo. ”
“Um aspecto realmente interessante da tecnologia CBS é sua natureza‘ bio-mimética ’”, acrescenta Peter Cate, gerente de marketing estratégico global da L&L. “Assim como as escoras de reforço celular no centro dos ossos são o método de massa mais eficiente da natureza para adicionar rigidez e gerenciar cargas em estruturas ocas, uma vez que o adesivo se expande, as unidades de CBS reforçam as cavidades da carroceria do veículo da mesma maneira, ajudando os engenheiros a otimizar a estrutura rigidez na massa mais baixa. ”
“Ao aumentar a rigidez local e geral e distribuir cargas de maneira mais eficaz em uma estrutura, os reforços CBS são soluções feitas sob medida para resolver problemas de rigidez localizada e fadiga de metal sem adicionar massa”, continua Pal Swaminathan, gerente de desenvolvimento de negócios, Tepex Automotive, Lanxess Corp . (Pittsburgh, Pensilvânia, EUA). “As melhorias de NVH também são comuns quando a tecnologia CBS é integrada às estruturas corporais. Mais uma vez, a análise cuidadosa de engenharia permite o desenvolvimento e soluções de otimização de localização para equilibrar as características de condução e manuseio. ”
Primeiros aplicativos
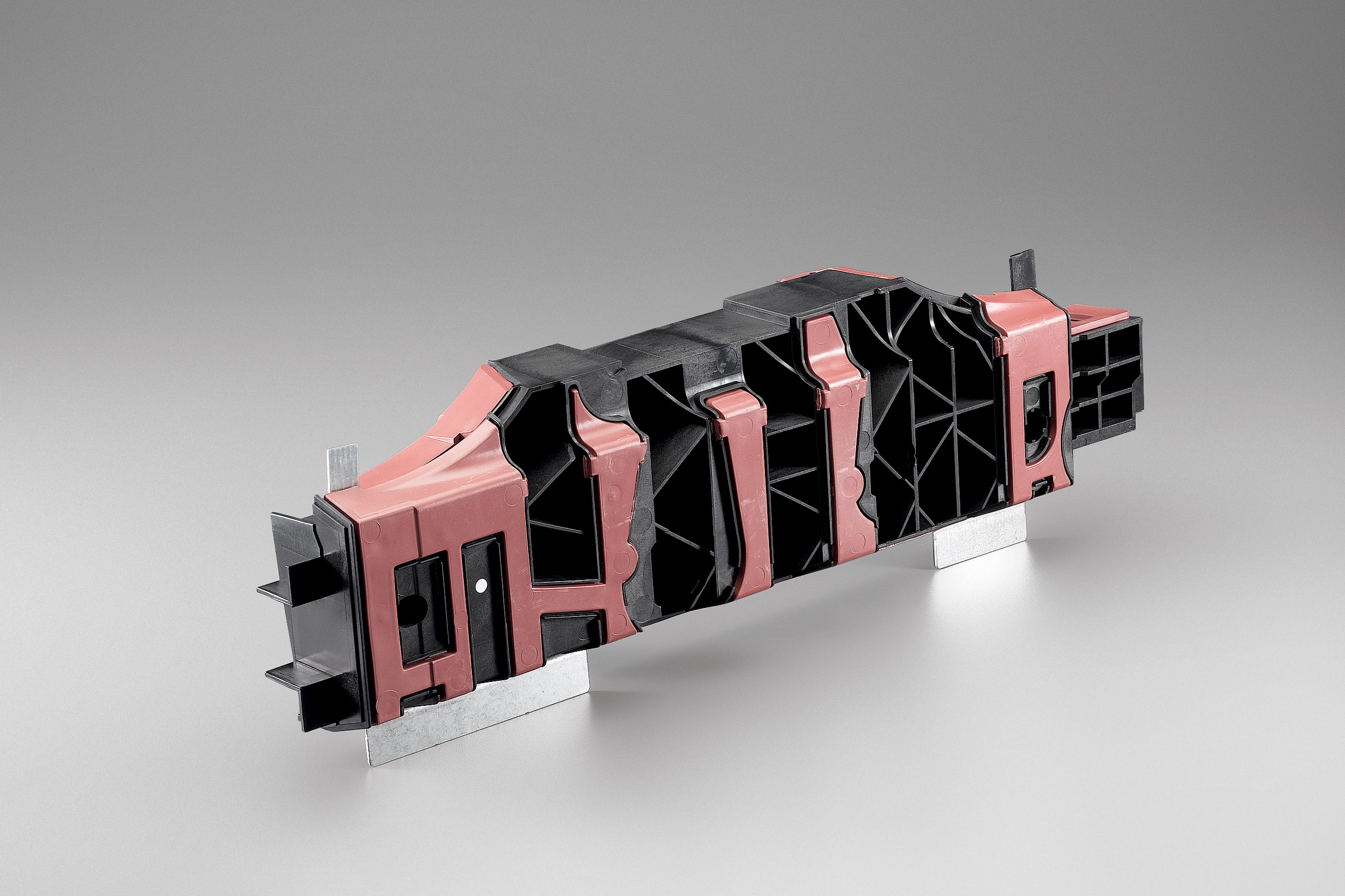
A primeira aplicação automotiva comercial da L&L do CBS foi em 1998; em 2002, a tecnologia estava ganhando aceitação no mercado. Um bom exemplo inicial foi implementado em 2006 Citroën C4 Picasso sedans do Grupo PSA (Paris, França - agora Stellantis N.V., Amsterdã, Holanda). Nove componentes CBS - nas seções inferiores dos pilares A, seções inferior e superior dos pilares B e na travessa acima do eixo traseiro - reduziram a massa do veículo em 12 quilogramas em comparação às opções metálicas. Algumas inserções CBS aumentaram seletivamente a capacidade de carga e minimizaram a intrusão no compartimento do passageiro durante o impacto, melhorando a segurança do ocupante. Outros melhoraram o desempenho NVH do BIW. Todos os transportadores foram moldados por injeção de 35% em peso de vidro curto / poliamida 6 (PA6). Unidades CBS semelhantes foram usadas no Ford Transit 2012 vans da Ford Motor Co. (Dearborn, Mich., EUA).
Novo transportador, opções de espuma
Ao longo dos anos, a L&L e seus fornecedores expandiram a tecnologia CBS com novas formulações de espuma, uma gama mais ampla de resinas transportadoras e reforços e aplicando o conceito a diferentes estruturas.
Por exemplo, a maioria dos portadores de CBS para aplicações em colisões é projetada usando PA6 reforçado com vidro de 30% em peso e estabilizado por calor, porque é necessário um equilíbrio entre rigidez e ductilidade em uma forma 3D complexa. Duas dessas transportadoras foram usadas em membros longitudinais dianteiros para uma plataforma de veículo elétrico principal (EV), onde, segundo as informações, eles não apenas simplificaram a montagem (reduzindo a contagem de peças), mas também reduziram a intrusão no firewall em 20%.
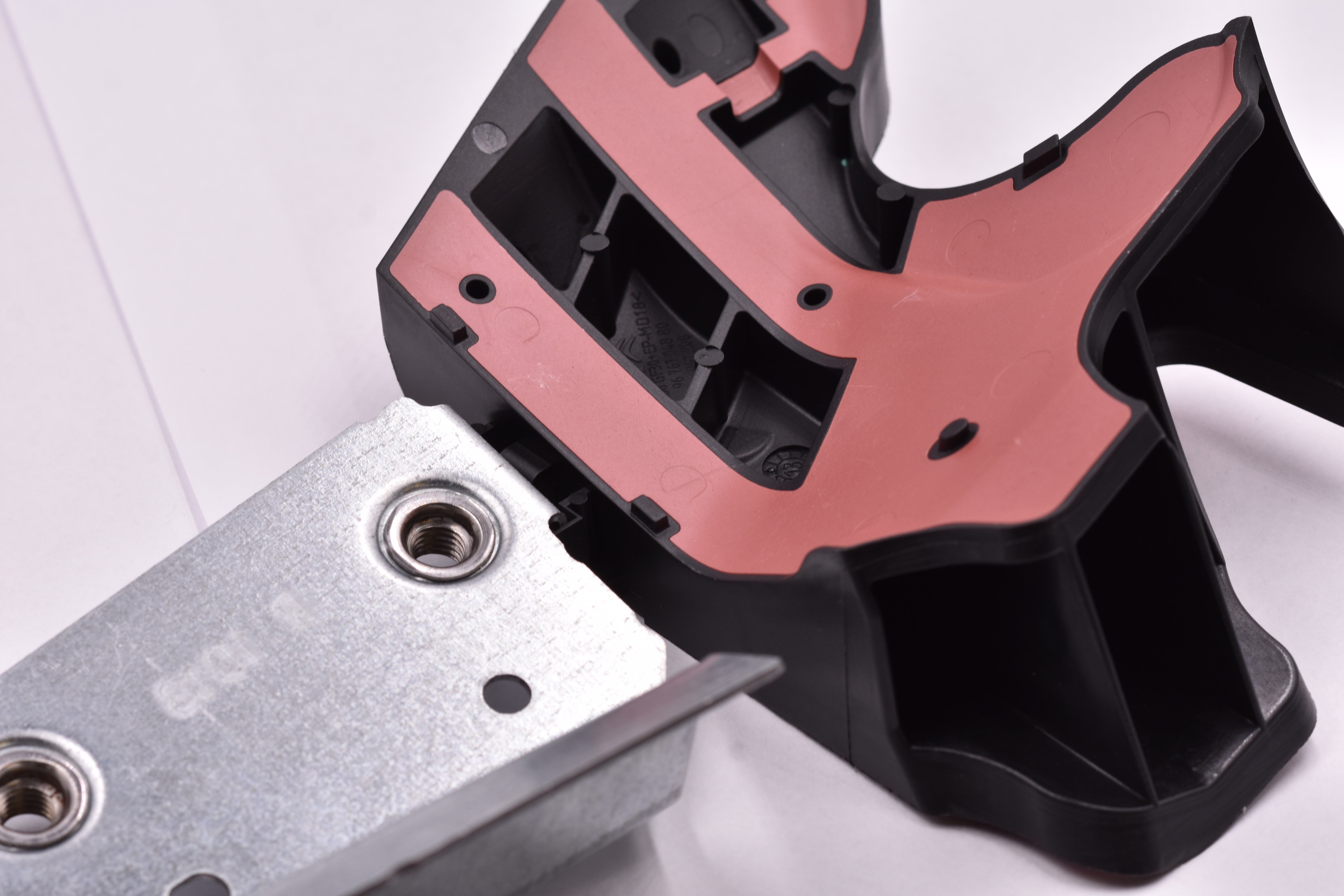
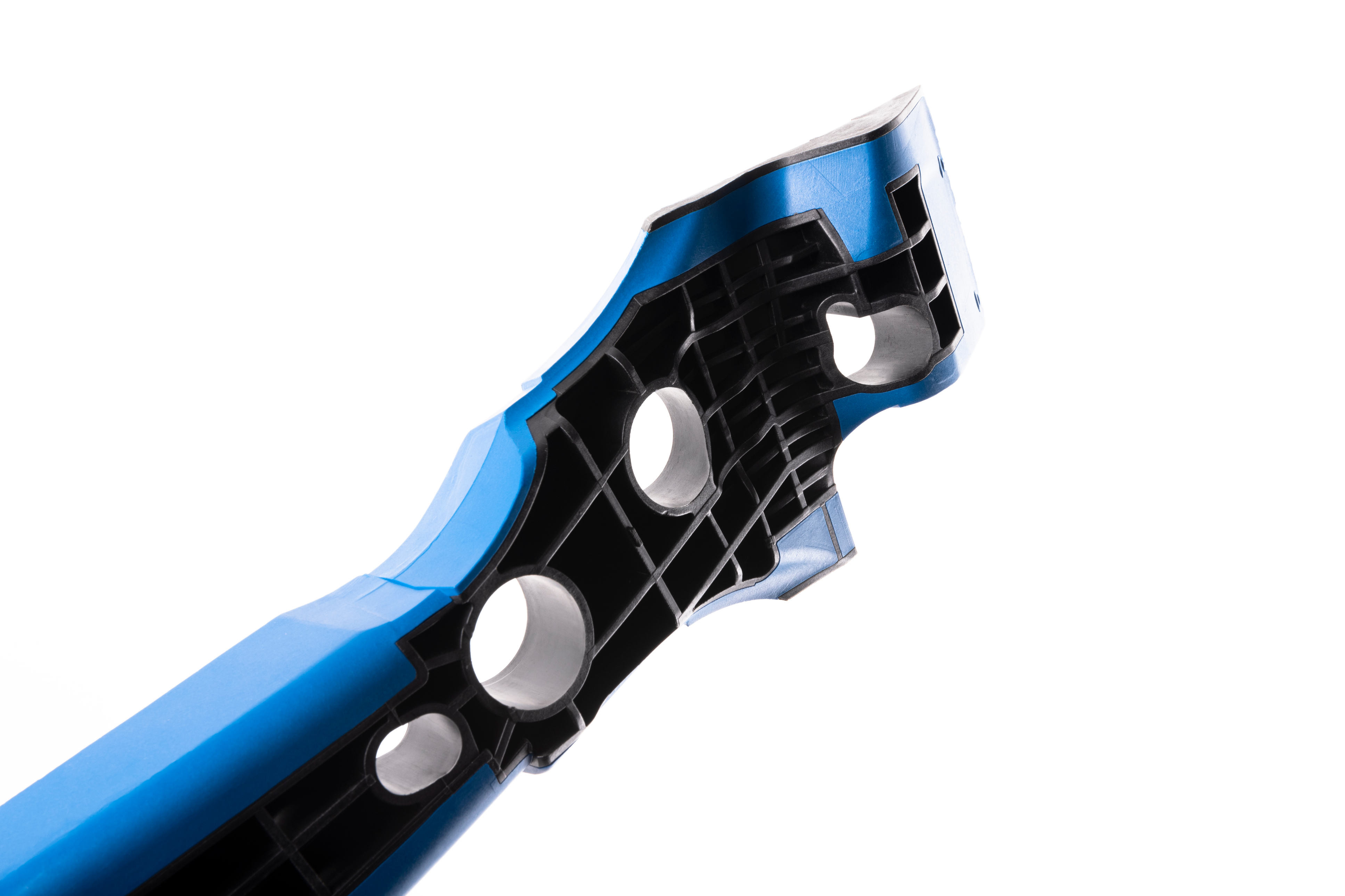
Para requisitos de maior impacto, transportadores híbridos estão agora disponíveis, como os pilares A de reforço no Porsche 2019 com carroçaria em grande parte de alumínio 911 Carrera Cabriolet carro esporte da Porsche AG (Stuttgart, Alemanha). Por ser um conversível, enrijecer a estrutura sem teto era fundamental para proteger os passageiros em caso de capotamento. Para manter os veículos leves e ágeis, a Porsche substituiu as barras de proteção de aço tubular por inserções CBS nos pilares A. Os cascos dos pilares foram produzidos em aço de alta resistência, que foram estabilizados e reforçados por inserções de CBS dentro de cada pilar. O corpo principal do transportador foi moldado por compressão em folha orgânica (47% em peso de tecido de vidro sarja / PA6), que foi pré-aquecido, pré-formado e, em seguida, moldado por injeção com nervuras (30% em peso de vidro curto / PA6 / 6). O lado da folha orgânica contém o adesivo expansível L&L L-5235. Esta tecnologia híbrida não apenas atendeu a todas as metas de desempenho e peso (o que a opção de aço tubular alegadamente não atendeu), mas também reduziu a massa do veículo em 5,4 quilogramas, facilitando a montagem e reduzindo o centro de gravidade do veículo, o que melhorou a dinâmica de direção.
Para aplicações onde um processo de forno não está disponível para ativar o adesivo expansível, ou onde suporte adicional é necessário na oficina de pintura, a L&L diz que está trabalhando em outras soluções de cura ambiental.
Diversas tecnologias relacionadas com base em CBS também foram desenvolvidas. Em breve, para ter sua primeira aplicação comercial, o sistema de compósito contínuo (CCS) da L&L combina portadores pultrudados reforçados com fibra de vidro ou carbono - por exemplo, poliuretano (PUR) com ou sem tecidos, bem como mechas - com selantes formulados sob medida ou adesivos estruturais. Os elementos CCS, que também podem incorporar peças CBS e componentes metálicos, melhoram a rigidez e a resistência de estruturas de seção transversal constante em massa inferior (normalmente 75% menos do que aço e 30% menos do que alumínio). Eles são resistentes à corrosão, não condutores / eletricamente isolantes, oferecem baixo coeficiente de expansão térmica linear (CLTE) e fornecem gerenciamento de energia altamente previsível, tornando-os ideais para reforçar membros estruturais em veículos monobloco ou seções de estrutura para veículos de carroceria, além de quadros de bateria para EVs.
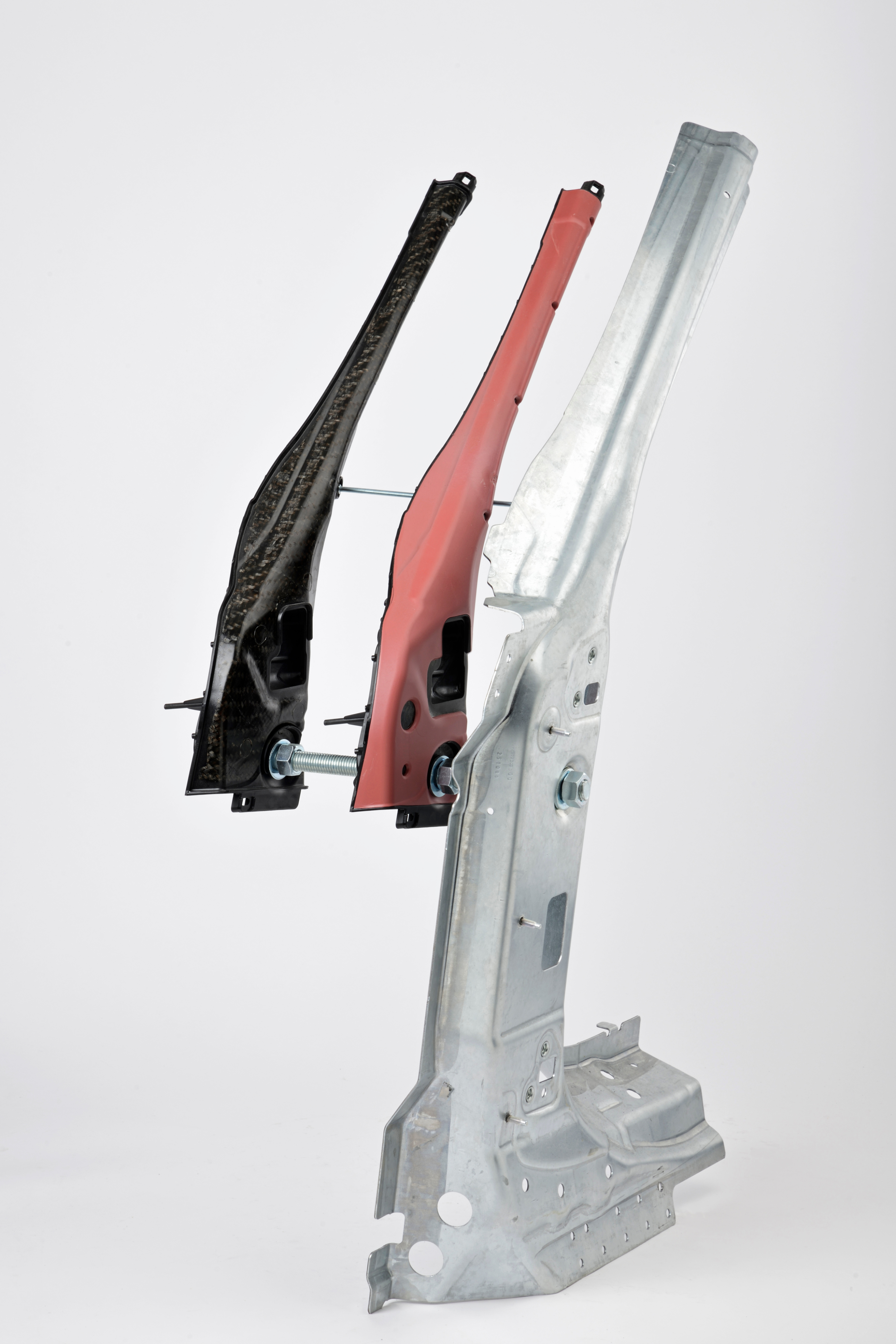
Os reforços de painel composto compreendem adesivos estruturais expansíveis e auto-aderentes coextrudados com reforço de fibra de vidro que são aplicados às superfícies de painel de metal formado na oficina. O sistema não apenas melhora a rigidez (reduzindo a ondulação e a flambagem) de painéis grandes / relativamente sem suporte, mas também melhora o NVH devido ao aumento do momento de inércia. Além disso, oferece oportunidades para reduzir os painéis para reduzir a massa e o custo. As aplicações comerciais incluem portas automotivas, painéis de teto e piso, capôs, pára-lamas, portas elevatórias e portas traseiras; aplicações potenciais incluem invólucros de bateria.
Os reforços do painel em favo de mel apresentam epóxi leve - em forma de pasta para aplicação manual ou líquido de baixa viscosidade para bombeamento automatizado - que, uma vez curado, pode ser usinado ou lixado. Eles são projetados para estabilizar núcleos de favo de mel, predominantemente em locais estratégicos no interior de aeronaves, por exemplo, sem adicionar massa em excesso. Outros usos incluem reforço de borda (vedação / reforço de bordas de painel composto), colagem de insertos e reforço local onde dobradiças / inserções de metal são instaladas em painéis de compósitos.
O que o futuro reserva
Desde sua primeira patente em 1999, a L&L registrou inúmeras invenções para a tecnologia CBS. Dada a ampla gama de opções de transportadores e adesivos agora disponíveis nesta família de produtos, não é surpreendente que as aplicações tenham se expandido além do setor automotivo para caminhões e aeroespacial. Qual é o próximo?
“Com o passar dos anos, os produtos CBS evoluíram para atender a novos requisitos de aplicação que combinam funções”, acrescenta Ignés. “Por exemplo, o que começou como apenas um reforço estrutural evoluiu não apenas para enrijecer, mas também para melhorar as funções acústicas ou para aumentar a absorção de energia. Dado o conjunto de propriedades altamente desejáveis que a tecnologia CBS oferece, esperamos não apenas ver o uso automotivo crescer, mas também em outras indústrias. ”
Resina
- CompositesWorld SourceBook 2022
- Resolução de problemas de termoformação de compósitos termoplásticos
- A evolução dos compostos aditivos
- Compostos termoplásticos:Suporte de pára-choque estrutural
- People in Compposites - Janeiro de 2019
- CAMX 2018:Pré-visualizações da exposição
- Compósitos termoplásticos de soldagem
- Visualização do SPE ACCE 2018
- Compostos de alto desempenho em Israel
- Compósitos para impressão 3D com fibra contínua