Avançando no Demonstrador de Fuselagem Multifuncional (MFFD)
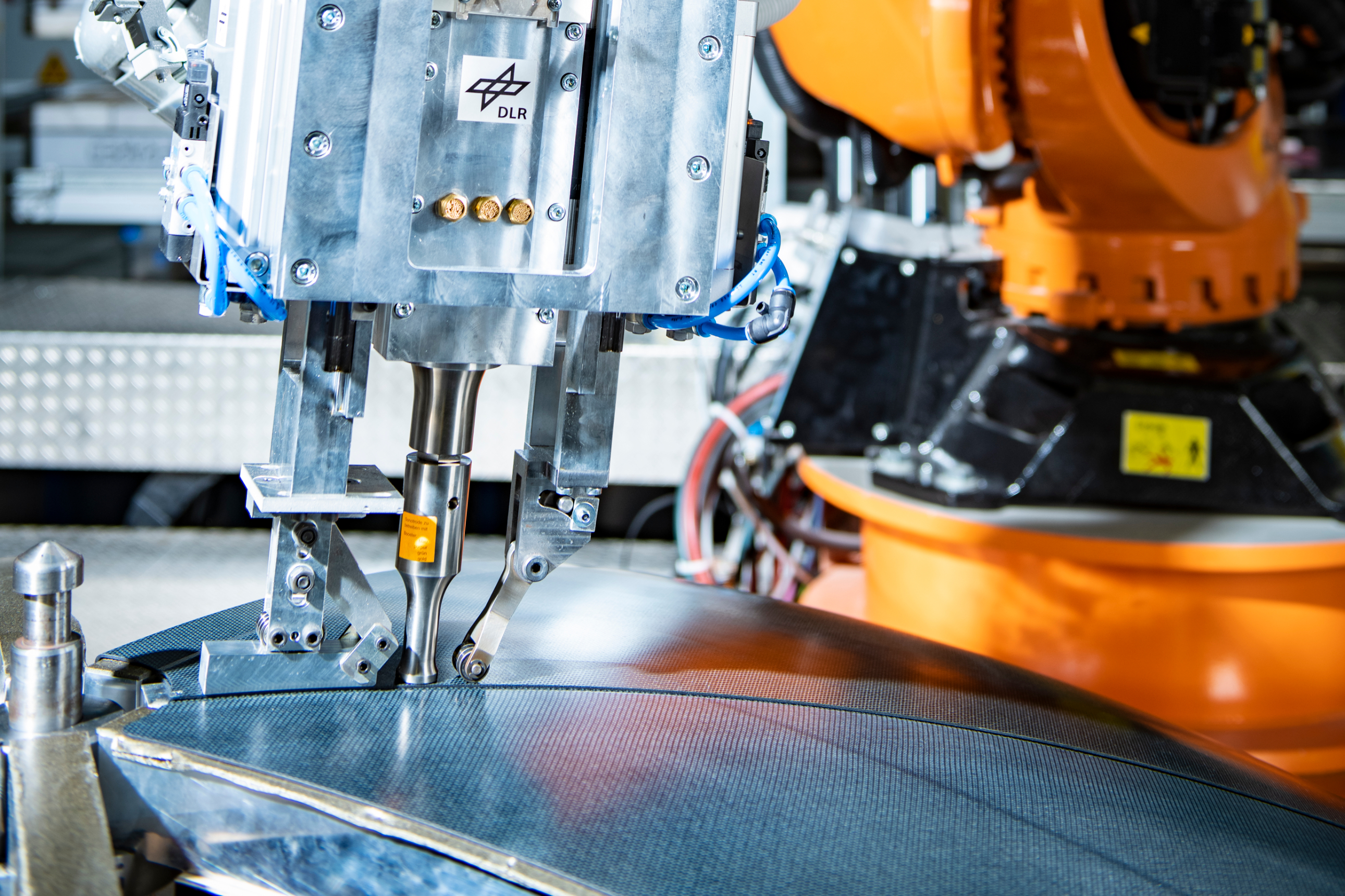
A redução das emissões de combustível e consumo de energia, e a capacidade de produzir aeronaves comerciais de corredor único a taxas de pelo menos 60 por mês, estão impulsionando o desenvolvimento de tecnologia da parceria europeia Clean Sky 2 para a próxima geração de aeronaves que voarão pelos céus em 2035 e além . Compostos leves e processos de fabricação mais rápidos e ecologicamente corretos estão tornando essas metas uma realidade, especialmente para o projeto Multifunctional Fuselage Demonstrator (MFFD).
O principal resultado deste projeto, que é liderado pela Airbus (Hamburgo, Alemanha) com parceiros da academia e da indústria da aviação, é um demonstrador de barril de fuselagem de aeronave comercial composto de termoplástico de 8 metros de comprimento, a ser produzido por 2022. O MFFD é uma das três seções de fuselagem em escala real que estão sendo produzidas na Plataforma de Demonstração de Aeronaves Inovadoras (IADP) da Clean Sky 2 para Large Passenger Aircraft (LPA).
Iniciado em 2014, os objetivos do projeto MFFD incluem:
- Ative taxas de produção de 60-100 aeronaves por mês
- Reduza o peso da fuselagem em 1.000 quilogramas
- Reduza os custos recorrentes em 20%.
Para atingir esses objetivos, dezenas de projetos individuais e pacotes de trabalho estão sendo concluídos, com duas estruturas principais sendo produzidas:uma concha superior da fuselagem e uma concha inferior da fuselagem, que serão soldadas para formar o demonstrador final. Na verdade, a união sem poeira (sem prendedores ou orifícios) por meio de soldagem é um componente importante do programa. Ambas as metades estão sendo fabricadas em pré-impregnado de fibra de carbono termoplástico de poliariletercetona de baixo ponto de fusão Toray Cetex TC1225 (PAEK) da Toray Advanced Composites (Morgan Hill, Califórnia, EUA). De acordo com o Dr.-Ing. Lars Larsen, chefe de tecnologias de junção e montagem do Centro Aeroespacial Alemão (DLR; Augsburg, Alemanha), ambas as metades testarão o uso de diferentes técnicas de fabricação.
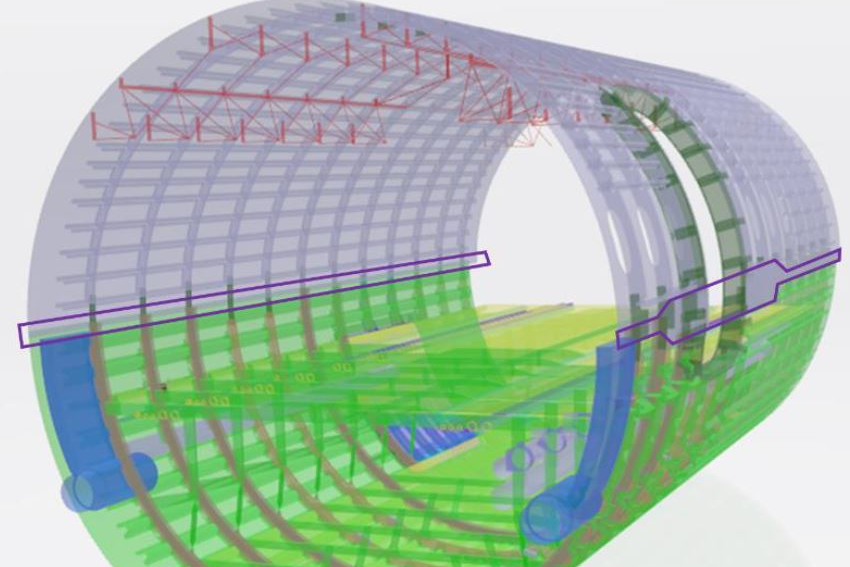
A seção inferior da fuselagem do MFFD está sendo produzida por meio do projeto STUNNING (fuselaGe termoplástica multifuncional SmarT e multifunções INtegradas), que por sua vez possui diversos projetos embaixo dela (como o MECATESTERS, voltado para soldagem por indução). A seção inferior compreenderá o casco inferior da fuselagem com longarinas e armações soldadas, a cabine e a estrutura do piso de carga e os elementos internos e do sistema relevantes.
STUNNING é liderado por GKN Fokker (Papendrecht, Holanda) com os principais parceiros Diehl Aviation (Laupheim, Alemanha), Netherlands Aerospace Centre (NLR; Amsterdam, Holanda) e Delft University of Technology (TU Delft; Delft, Holanda). O projeto visa amadurecer ainda mais os processos de montagem automatizada, fabricação de termoplásticos e tecnologias de soldagem, design integrado e desenvolvimento de fabricação e arquiteturas de sistemas elétricos avançados.
“Nosso impacto na indústria é duplo:o nível de automação que aplicamos à montagem do demonstrador e o desenvolvimento de maneiras sustentáveis de produzir peças”, disse o Dr. Bas Veldman, gerente de programa da GKN Fokker.
De acordo com um artigo publicado por Veldman em fevereiro de 2020, a montagem modular da fuselagem inferior é a chave para atingir o objetivo de tempos de produção rápidos. Para fabricar o revestimento principal da fuselagem, grandes pré-formas feitas de fibra de carbono / pré-impregnado termoplástico são colocadas por uma máquina de colocação automática de fita aquecida ultrassônica ou a laser (ATL), mas não consolidadas in-situ. Os detalhes são colocados por uma máquina de colocação automática de fibra (AFP). Os robôs então colocam as pré-formas em um molde de consolidação fêmea e, após o ensacamento, a pele é consolidada em uma autoclave. Segundo Veldman, os processos fora da autoclave também estão sendo investigados. As longarinas e armações serão soldadas à pele.
“Originalmente, o plano era ter todas as peças fabricadas este ano”, diz Veldman, mas devido aos atrasos relacionados ao coronavírus, “agora está em transição para o próximo ano também. Mas temos algumas peças que já foram concluídas ”, incluindo muitas das peças menores moldadas por prensagem, como clipes, suportes e suportes que serão usados para prender assentos de aeronaves e outros componentes. Enfatizando a fabricação sustentável, Veldman acrescenta que alguns dos clipes são fabricados a partir de sobras reaproveitadas de outras peças do demonstrador, por meio de um projeto Clean Sky 2 denominado ECO-CLIP.
Começando no início de 2020, o consórcio que produz a casca superior de 8 metros de comprimento inclui a Airbus, Premium Aerotec (Augsburg, Alemanha), que é o líder de design estrutural e industrial; DLR, responsável pelo desenvolvimento de tecnologia de soldagem e layup de pele; e Aernnova (Vitoria-Gasteiz, Espanha), que está produzindo as longarinas.
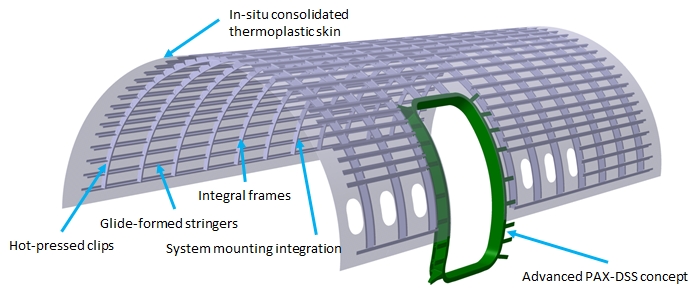
Para a indústria aeroespacial fazer a transição para materiais termoplásticos mais caros, Larsen diz:“Temos que mostrar que podemos economizar custos durante a produção”. O consórcio da metade superior está desenvolvendo uma nova tecnologia de colocação de fibra avançada (AFP) com, notadamente, consolidação in-situ para a camada de fibra de carbono / PAEK, bem como a industrialização de soldagem ultrassônica contínua e soldagem por resistência para integração das longarinas, quadros e outros componentes, melhorando a segurança e reduzindo custos. O DLR está construindo primeiro uma concha de teste pré-demonstrador de 1 metro de comprimento para validar as tecnologias antes que o demonstrador em escala real seja construído, e planeja ter a pele para a concha pré-demonstrador fabricada até o final de 2020. Integração de as longarinas estão programadas para o início de 2021.
As versões em escala real de ambas as metades devem ser concluídas até o final de 2021. Depois de concluídas, elas serão soldadas no demonstrador final no Instituto Fraunhofer de Tecnologia de Fabricação e Materiais Avançados IFAM (Stade, Alemanha).
Resina
- Indo além do básico:Aprendizado de máquina e AM
- As vantagens do projeto composto de aeronaves em aviões de todos os tamanhos
- Por que a automação é o único caminho para a manufatura
- 5 Aplicações Robóticas na Indústria Aeroespacial
- O cenário da manufatura:olhando para trás e olhando para o futuro
- Três benefícios de mover o gerenciamento de gastos para a nuvem
- A primeira seção composta da fuselagem para o primeiro jato comercial composto
- Atendendo ao mundo dos compósitos em Israel e nos EUA
- Qual é a tensão direta do diodo?
- Geração de nitrogênio na indústria aeroespacial