Epóxi de 2 partes para aumento da produção de aeroestruturas compostas via RTM
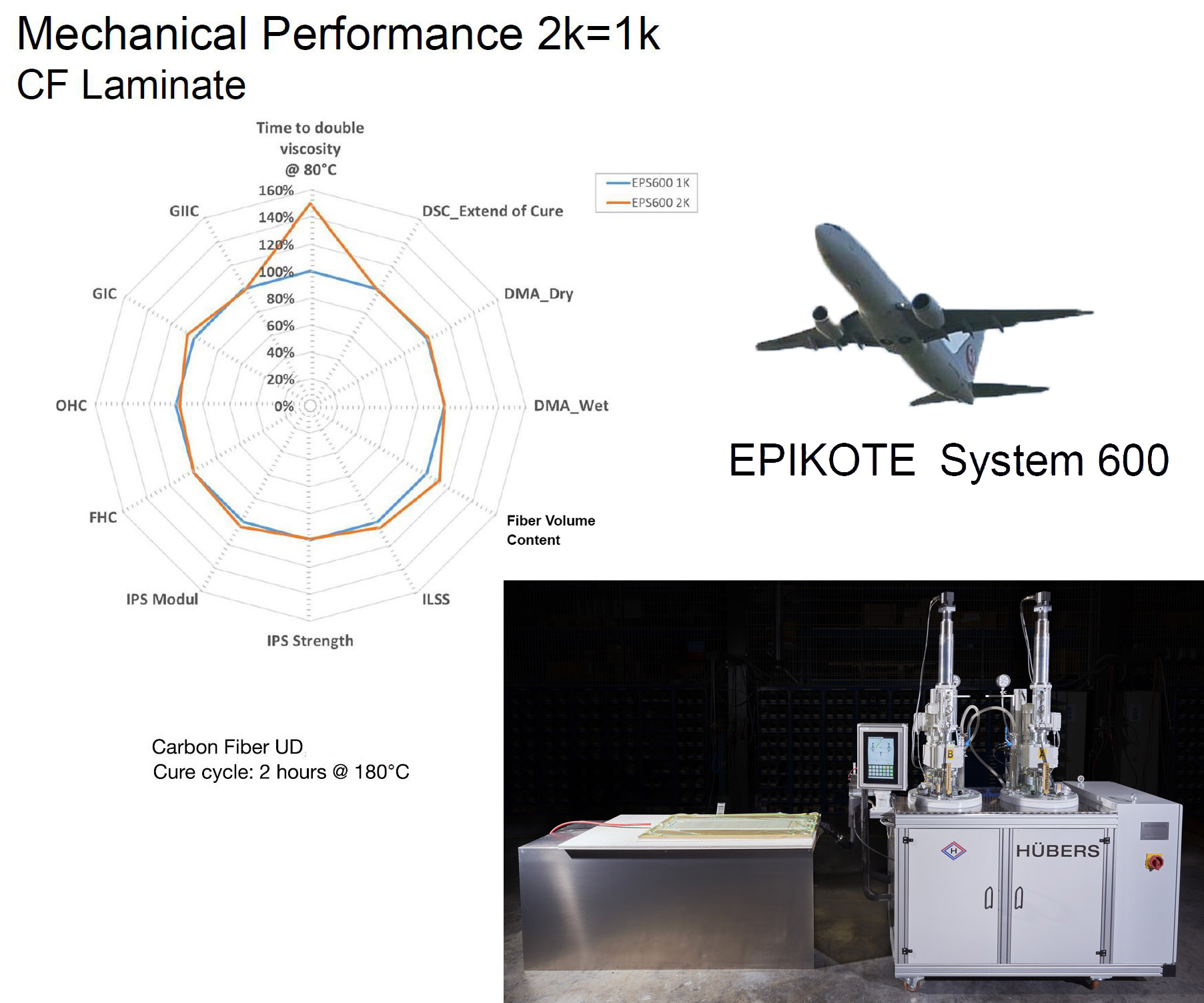
Este é o terceiro de minha série de blogs sobre tecnologias que você deve conferir no CAMX 2019 (23 a 26 de setembro, Anaheim, CA, EUA). A Hexion (Columbus, Ohio, EUA) desenvolveu um sistema de dois componentes (2K) para RTM de aeroestruturas com base em sua resina epóxi Epikote System 600. A introdução abaixo irá explicar porque este desenvolvimento é importante. Depois disso, darei mais detalhes sobre este novo sistema 2K e como a Hexion está atendendo às demandas dos OEMs aeroespaciais para garantia de qualidade in situ da resina misturada. No fundo, também discuto a infusão 2K / RTM de epóxi da Hexion para aplicações resistentes ao fogo (FR).
Por que resinas 2K para RTM?
No início deste ano, escrevi sobre programas na especialista em ferramentas Alpex Technologies (Mils, Áustria) e na subsidiária da Airbus, Composites Technology Center (CTC, Stade, Alemanha) para produzir peças de aeronaves compostas usando moldagem por transferência de resina (RTM) . Usar RTM na indústria aeroespacial não é novo. Há e tem havido uma variedade de peças de aeronaves feitas usando RTM, incluindo:
- Leme para o jato executivo Gulfstream G250 (Israel Aerospace Industries e North Coast Composites)
- Lâminas e caixa do ventilador para o motor de aeronave turbofan LEAP (Albany Engineered Composites)
- Moldura da porta A350 (Airbus Helicopters Donauworth)
- Demonstração da porta do passageiro A350 (Elbit Cyclone)
- Flap multispar de demonstração A320 (Airbus Bremen)
- A Matrix Composites produziu mais de 6.000 componentes para o F-22 usando RTM.
No entanto, RTM em aplicações aeroespaciais tem sido tradicionalmente um processo de baixa pressão com tempos de ciclo medidos em horas. Os programas do Alpex e CTC são focados em explorar a automação, injeção rápida e tempos de ciclo de 15 a 20 minutos oferecido por RTM de alta pressão (HP-RTM). Em meu artigo "HP-RTM para produção em série de aeroestruturas de CFRP econômicas", discuti a questão do uso de resinas epóxi de 2 componentes (2K) versus a norma atual de uso de sistemas pré-misturados de 1 componente (1K):
“Schiller [Jan Schiller, líder do projeto CTC para sistemas de produção e contato principal para tecnologias RTM] observa que todos os RTM anteriores estruturas de aeronaves usaram apenas sistemas 1K misturada pelo fornecedor, que então certifica a mistura e se responsabiliza por garantir que a resina atenda aos requisitos de qualificação. “Agora estamos considerando sistemas 2K, mas o desafio é garantir a qualidade da mistura ," ele explica. Os sistemas 1K pré-misturados requerem remessa fria e armazenamento para evitar a reação até o processamento da peça. Assim, as vantagens dos sistemas 2K incluem a eliminação dessa despesa, bem como maior reatividade para processamento mais rápido. ”
“Um problema, no entanto, é que a garantia de qualidade (QA) será transferida do fornecedor da resina para o fabricante das peças. “Este controle de qualidade requer detecção da proporção de mistura e a qualidade da resina mista . Ambos são necessários para a qualificação do Airbus de um novo material. Portanto, isso significa medições dos dois componentes imediatamente antes da mistura e da resina após a mistura . Hoje, temos apenas sensores antes do cabeçote de mistura, mostrando quanta resina e quanto endurecedor são dosados na mistura. Isso não é suficiente para a qualificação. ”
Hexion (Columus, Ohio, EUA), líder no desenvolvimento de epóxis de cura rápida para HP-RTM em compósitos automotivos (consulte "HP-RTM em ascensão"), anunciou em março de 2019 que desenvolveu um sistema 2K para RTM de aeroestruturas baseadas em sua resina epóxi Epikote System 600. Entrevistei o líder do segmento aeroespacial global de epóxi da Hexion, Jean Rivière, para saber mais sobre seu sistema 2K para a indústria aeroespacial e como eles estão atendendo a essa demanda de controle de qualidade in situ da resina misturada.
Superando limitações de sistemas 1K
“Assim como com o pré-impregnado, os sistemas 1K para RTM e infusão na indústria aeroespacial devem ser mantidos frios e ter uma vida útil limitada”, diz Rivière. “Ao usar um sistema epóxi de 2 componentes (2K), você remove essas restrições. Vimos resinas epóxi 2K e altamente reativas usadas na fabricação de pás eólicas e estruturas automotivas. Então, por que não na indústria aeroespacial? ”
Rivière explica que, depois de conversar com muitos clientes sobre isso, a Hexion entendeu a principal preocupação - você precisa de uma validação de que a proporção de mistura está correta a qualquer momento antes da injeção no molde. Sem isso, você representa um risco inaceitável para o fabricante da peça ”, observa. Ele acrescenta que, anteriormente, não havia uma demanda para o tipo de volumes de produção vistos em pás eólicas e automotivas. Agora, no entanto, a Airbus e a Boeing querem exceder as taxas de produção atuais e, ao mesmo tempo, buscar mais peças compostas por aeronave. “Portanto, agora é necessário abandonar o layup pré-impregnado e adotar um epóxi 2K para RTM aeroespacial ou infusão”, diz Rivière.
Nos diagramas da cadeia de suprimentos abaixo, a tecnologia 2K não apenas remove as etapas de armazenamento a frio e reaquecimento, mas também elimina as restrições no tamanho do contêiner de resina para envio. “Você deve manter a massa de resina pré-misturada abaixo de 20 litros e manter esses tambores em temperatura muito baixa”, diz Rivière, “ou então a resina pode começar a reagir. Para um sistema 2K, tambores padrão de 200 litros podem ser enviados sem restrições de baixa temperatura. Portanto, há menos risco, nenhum resfriamento forte e menos precauções necessárias. ”
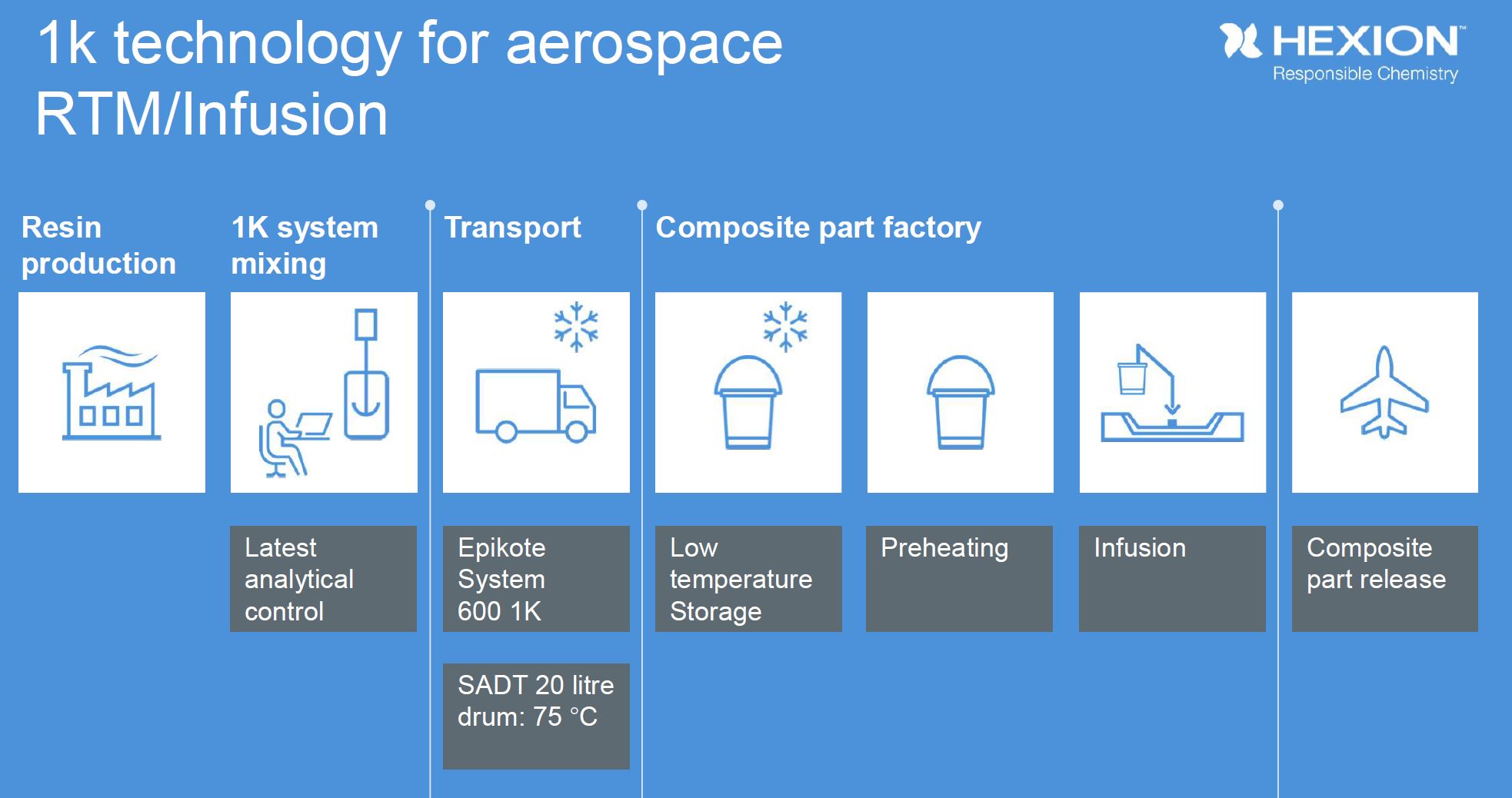
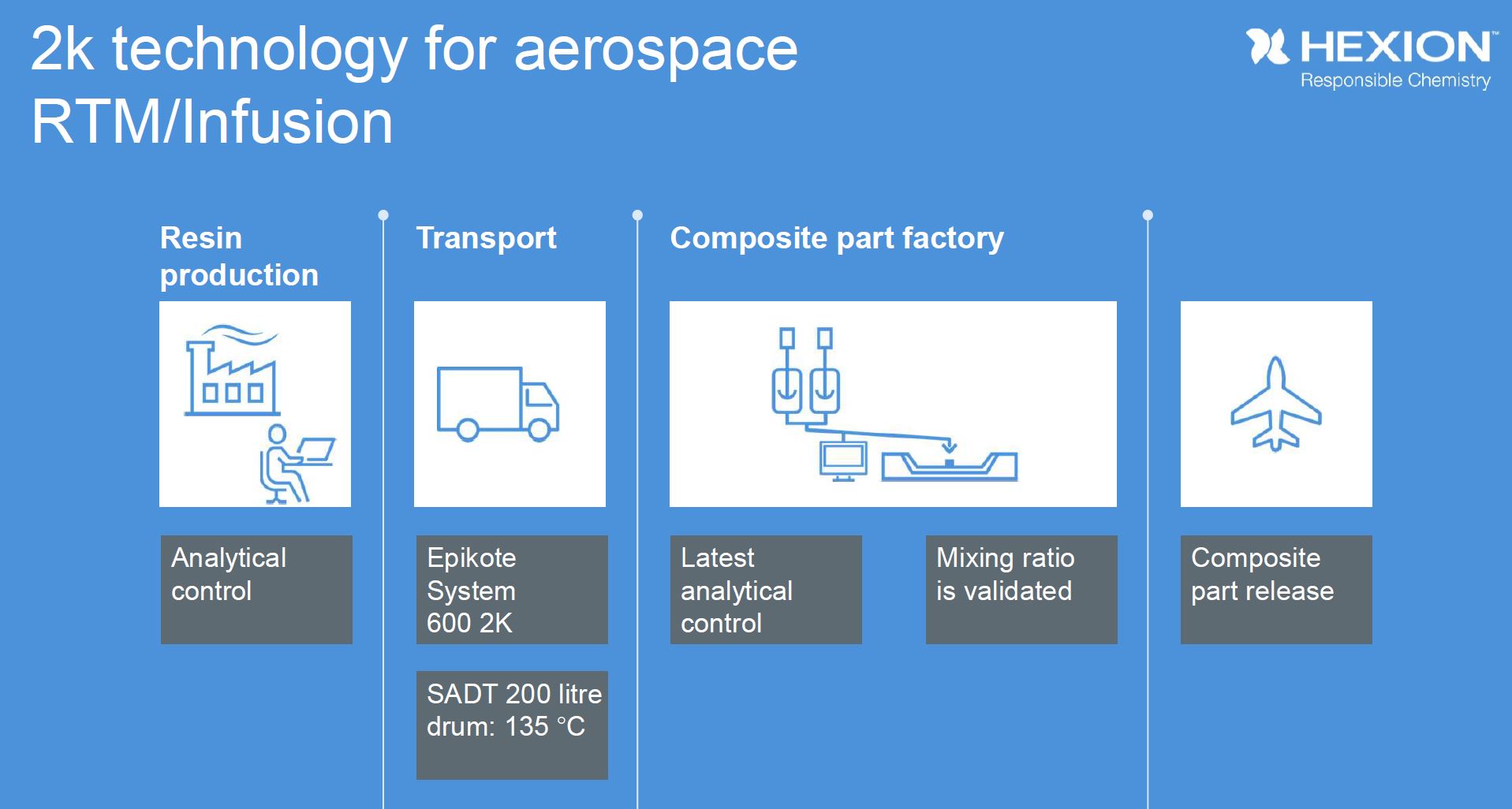
As cadeias de suprimentos acima mostram como o controle analítico muda. Embora apenas um controle inicial seja realizado no local de fabricação para sistemas de resina 1K, o controle é implementado em vários pontos de controle para o sistema 2K. Além do controle dos componentes A e B durante a produção da fábrica, a proporção de mistura A:B também é controlada digitalmente no equipamento de mistura, medição e dispensação (MMD) e novamente antes da injeção de resina no molde. FONTE | Hexion.
Controle analítico
Para desenvolver essa tecnologia 2K, a Hexion trabalhou com a Hübers (Bocholt, Alemanha), fabricante de equipamentos de mistura, medição e dispensação (MMD), e a Composyst (Hurlach, Alemanha), que possui uma licença exclusiva para o Processo Assistido a Vácuo patenteado pela Airbus ( VAP) para infusão. Hübers tem uma forte reputação de sistemas MMD de alto desempenho usados na fabricação de componentes elétricos e eletrônicos (por exemplo, resina fundida e componentes impregnados para transformadores, etc.), enquanto Composyst é um especialista em injeção de resina e infusão para aplicações Airbus e, portanto, , entende o que o OEM de aeronaves está procurando em relação ao processamento e garantia de qualidade (QA) de resinas mistas.
“O controle analítico entra em ação depois que os componentes A e B do epóxi foram misturados com precisão pelo equipamento da Hübers e estão se preparando para serem introduzidos no molde”, explica Rivière. Os tubos pretos entre o sistema Hübers MMD e a configuração de infusão de VAP com saco a vácuo na imagem abaixo são um componente chave deste sistema de controle analítico. “É aqui que temos um dispositivo analítico que controla a proporção da mistura em tempo real”, diz Rivière. “Demonstramos a medição da taxa de mistura a cada 12 segundos, mas medições mais frequentes também são possíveis. Na verdade, a tecnologia permite um controle contínuo da taxa de mistura, que é relatada e registrada. ”
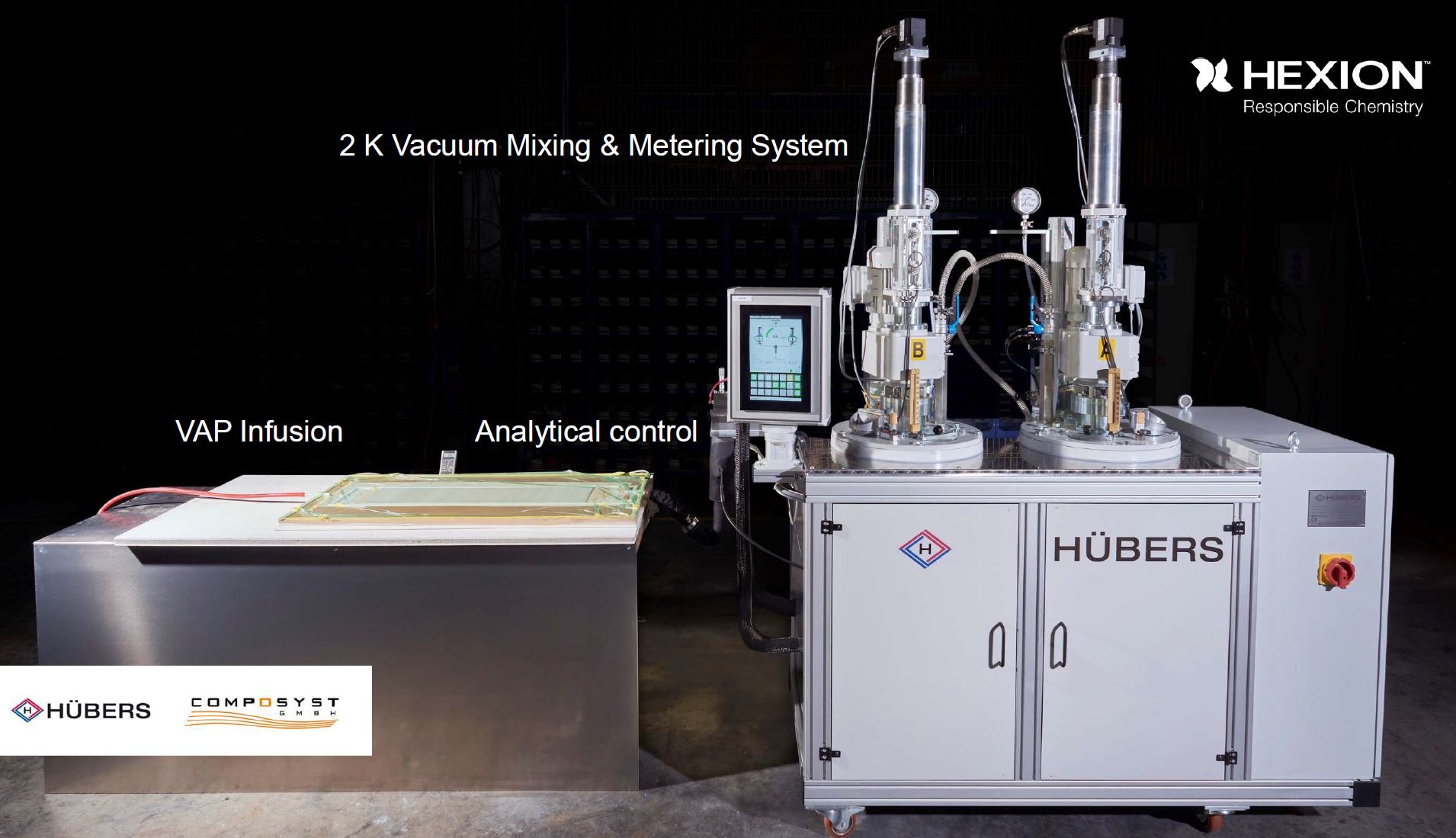
Observe o tubo preto entre o equipamento Hübers MMD e a configuração de infusão VAP, onde a Hexion desenvolveu a medição em linha da proporção da mistura de resina antes da injeção. Hexion
“Com este sistema”, ele continua, “há um controle duplo:o controle normal na unidade MMD e nosso controle analítico de pré-injeção no topo. Em primeiro lugar, Rivière destaca que as máquinas Hübers MMD são conhecidas por sua precisão e exatidão. “Eles têm um sistema de bombeamento duplo para os dois componentes e devem manter a precisão de volume e temperatura, bem como a proporção de mistura para as aplicações que fornecem. Nosso sistema então adiciona uma segunda medição após a mistura e um pouco antes da injeção, onde você pode definir alvos para alarmes. ” Caso a proporção de mistura medida não atenda às metas e acione o alarme, o sistema evacuará a resina misturada em um recipiente separado, desviando do molde para que não introduzido na parte infundida. “Dessa forma, é possível recuperar o processo e continuar a injeção”, observa Rivière.
Ele diz que o sistema de controle analítico pós-injeção e pós-mistura da Hexion fornece um registro independente para rastreabilidade e também pode ser integrado à unidade MMD, dependendo das necessidades do cliente. Rivière observa que a unidade Hübers MMD também realiza a desgaseificação completa da resina, que é exigida pela indústria eletrônica, onde não pode haver vazios ou porosidades nos componentes da aplicação. “Esse sistema também permite o controle portátil da pressão no molde, gerenciando o fluxo da resina em níveis altos ou baixos”, destaca. “Você pode obter uma impregnação muito boa com esse tipo de controle e também pode encurtar o tempo do processo de infusão ao mesmo tempo em que atende aos requisitos de qualidade aeroespacial em termos de porosidade e volume de fibra.”
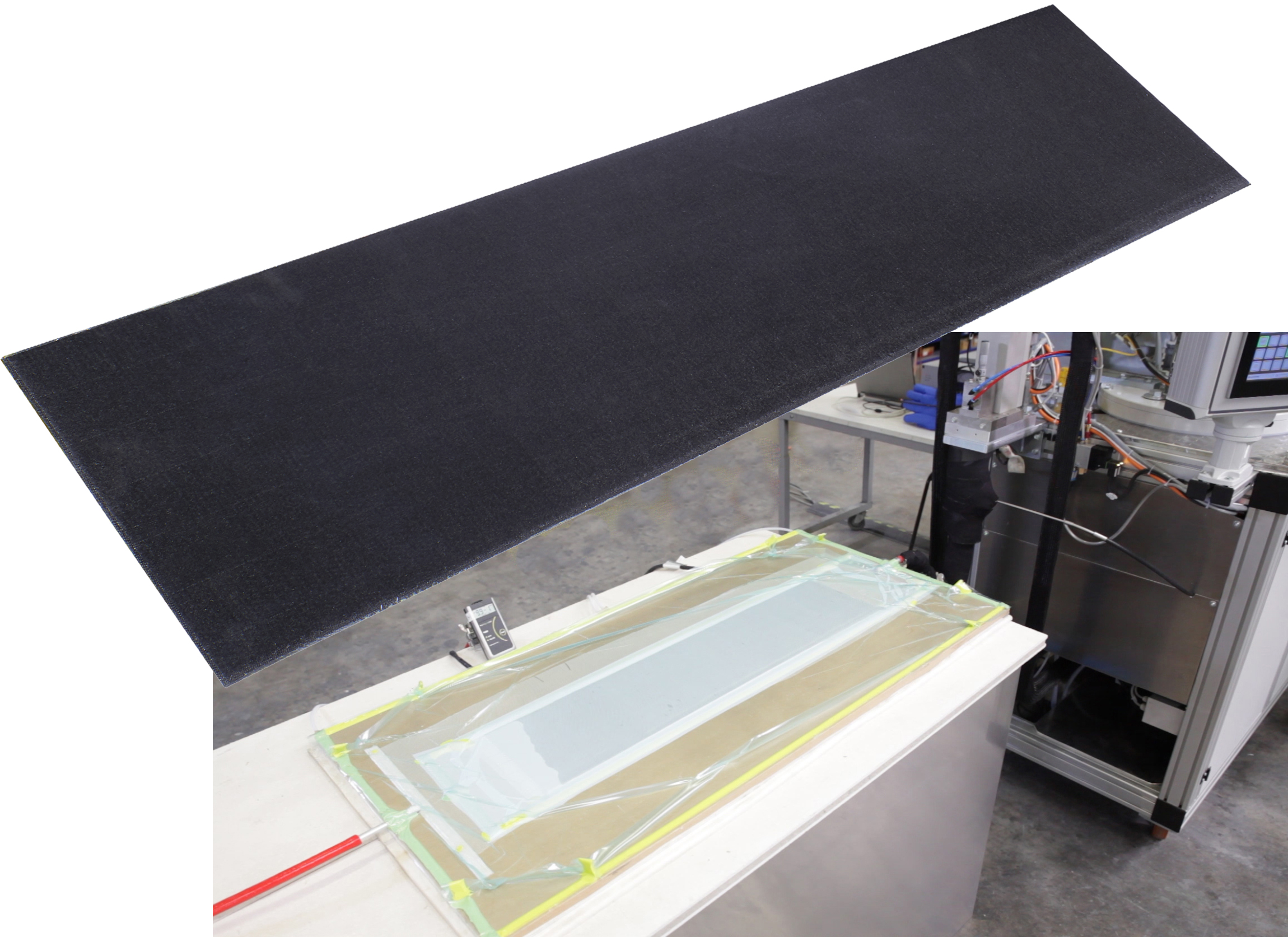
Fotos mostrando configuração de infusão usando equipamento Hübers MMD e controle analítico Hexion 2K e um laminado UD de fibra de carbono de 2 centímetros de espessura preparado usando esta configuração, atingindo mais de 60% do volume de fibra. FONTE | Hexion
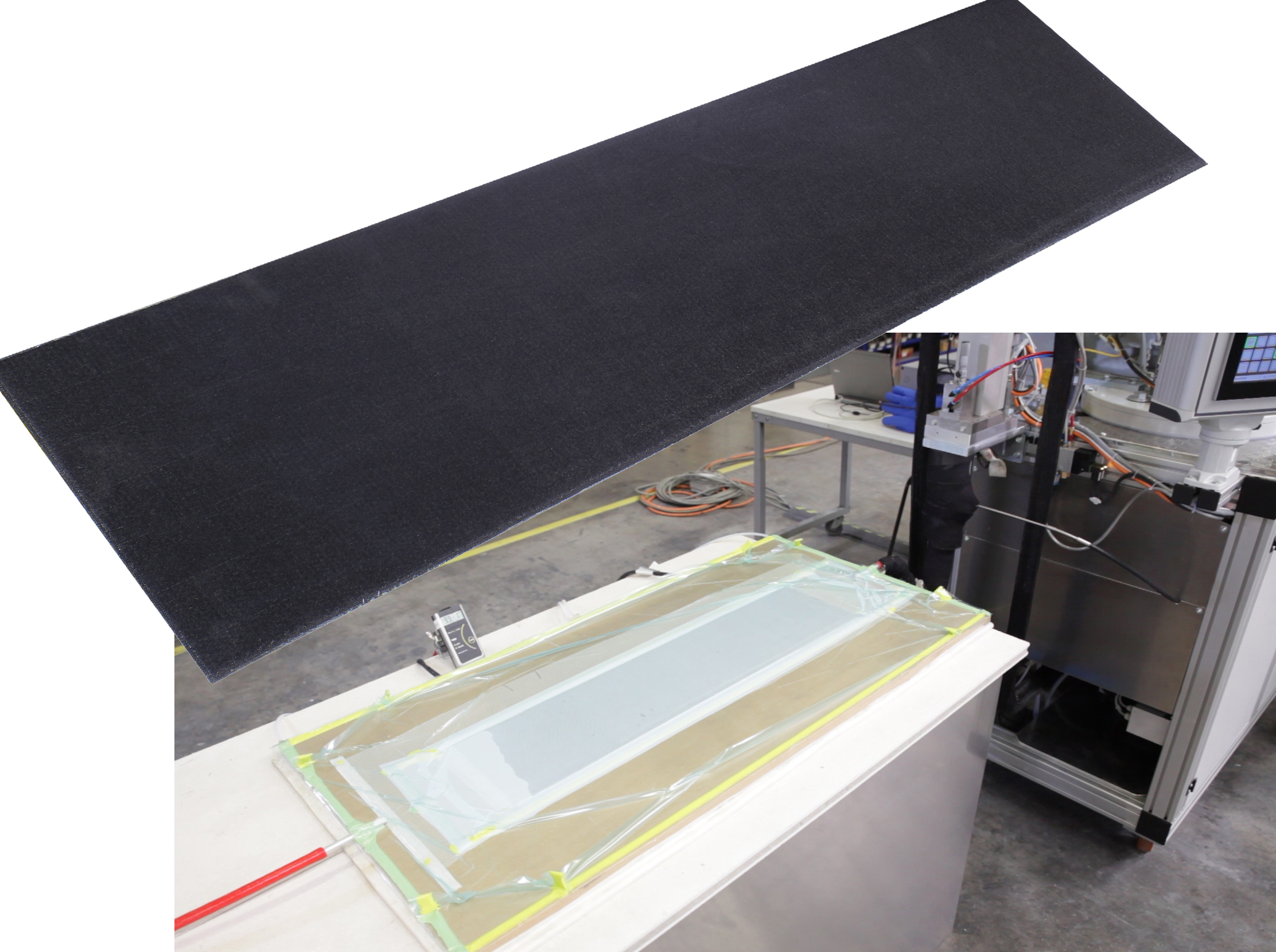
Janela de melhor processamento
“Como a mistura é feita com um misturador estático e em um curto espaço de tempo pouco antes da injeção, a mistura de resina oferece uma vida útil mais longa (até 40% em comparação com 1K)”, observa Rivière . Isso fornece uma janela de processamento melhor e produzimos laminados de fibra de carbono espessos com 60% do volume de fibra. O desempenho mecânico dos sistemas 2K versus 1K é o mesmo porque a química é a mesma. Acreditamos que este será um processo mais confiável e o valor completo é quando você conecta o controle de mistura à configuração de injeção de resina. ”
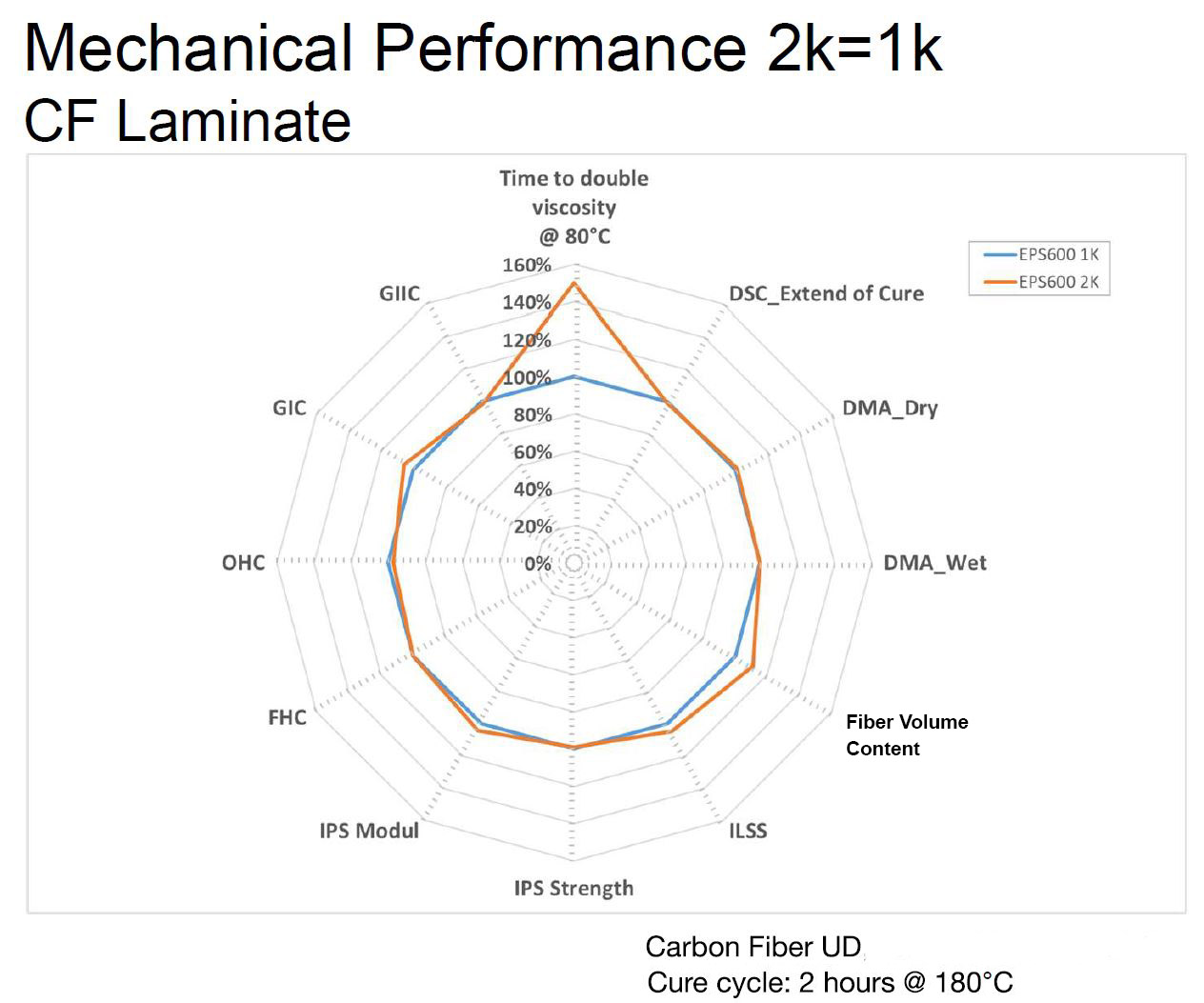
FONTE | Hexion
A Hexion apresentará informações detalhadas sobre seu sistema 2K Epikote 600 para RTM e seu EPON FlameX epóxi para atender aos requisitos de incêndio, fumaça e toxicidade (FST) de aeronaves (veja abaixo) no Teatro CAMX no piso de exposição:
- Nova tecnologia 2K para fabricação aeroespacial de epóxi
Terça-feira, 24 de setembro - 11h-11h25 - Sistemas Epóxi FlameX para aplicações de segurança contra incêndio
Terça-feira, 24 de setembro - 11h30 - 11h55
Você também pode obter mais detalhes no estande Y24 da Hexion.
EPON FlameX epóxi para infusão / RTM de compósitos resistentes ao fogo
A Hexion também desenvolveu um epóxi de 2 componentes para infusão / RTM de peças que devem atender aos requisitos de resistência ao fogo (FR) e chamas, fumaça e toxicidade (FST). Com o objetivo de substituir os pré-impregnados fenólicos por moldagem líquida de epóxi, os impulsionadores para este desenvolvimento incluem:
- Aumento das taxas de produção
- Regulamentos REACH para sistemas livres de halogênio e não fenólicos
- Resinas mais fortes e resistentes versus fenólicos quebradiços
- Custo competitivo com os fenólicos, mas muito mais baratos do que os termoplásticos.
O sistema EPON FlameX da Hexion não usa halogênio ou aditivos particulados para alcançar resistência ao fogo, mas em vez disso constrói esse desempenho na espinha dorsal molecular da resina. Não há filtragem de partículas durante a infusão. A resina infunde bem com uma viscosidade de 250 cps a 60-70 ° C (140-158 ° F) e cura em 1,5 horas a 150 ° C (302 ° F). A pós-cura autônoma ou com suporte de ferramenta a 180 ° C é recomendada para obter as propriedades estruturais máximas.
As peças feitas com este sistema passam o seguinte sem revestimentos adicionais ou medidas FR:
- queima vertical 60s FAR25.853 (a)
- Toxicidade de fumaça BSS7239
- Densidade de fumaça BSS7238
Ele também passará pela liberação de calor OSU 65/65, em certas configurações com um revestimento ou revestimento de gel intumescente certificado. Isso é necessário apenas para partes que podem ser tocadas durante o táxi, decolagem e pouso da aeronave.
“Demonstramos caixas suspensas que atualmente requerem de 10 a 12 horas para fabricar usando processos prepreg fenólicos convencionais, mas podem ser produzidas em 90 a 120 minutos com infusão ou RTM usando o sistema FlameX”, diz Nathan Bruno, especialista em aplicações de epóxi e desenvolvimento de produtos da Hexion . “Além disso, como não há enchimentos, ele tem uma densidade mais baixa em comparação aos epóxis FR preenchidos.”
As aplicações incluem interiores de aeronaves, áreas de carga, lavatórios, cozinhas e componentes de assentos, bem como interiores marítimos, ferroviários e arquitetônicos.
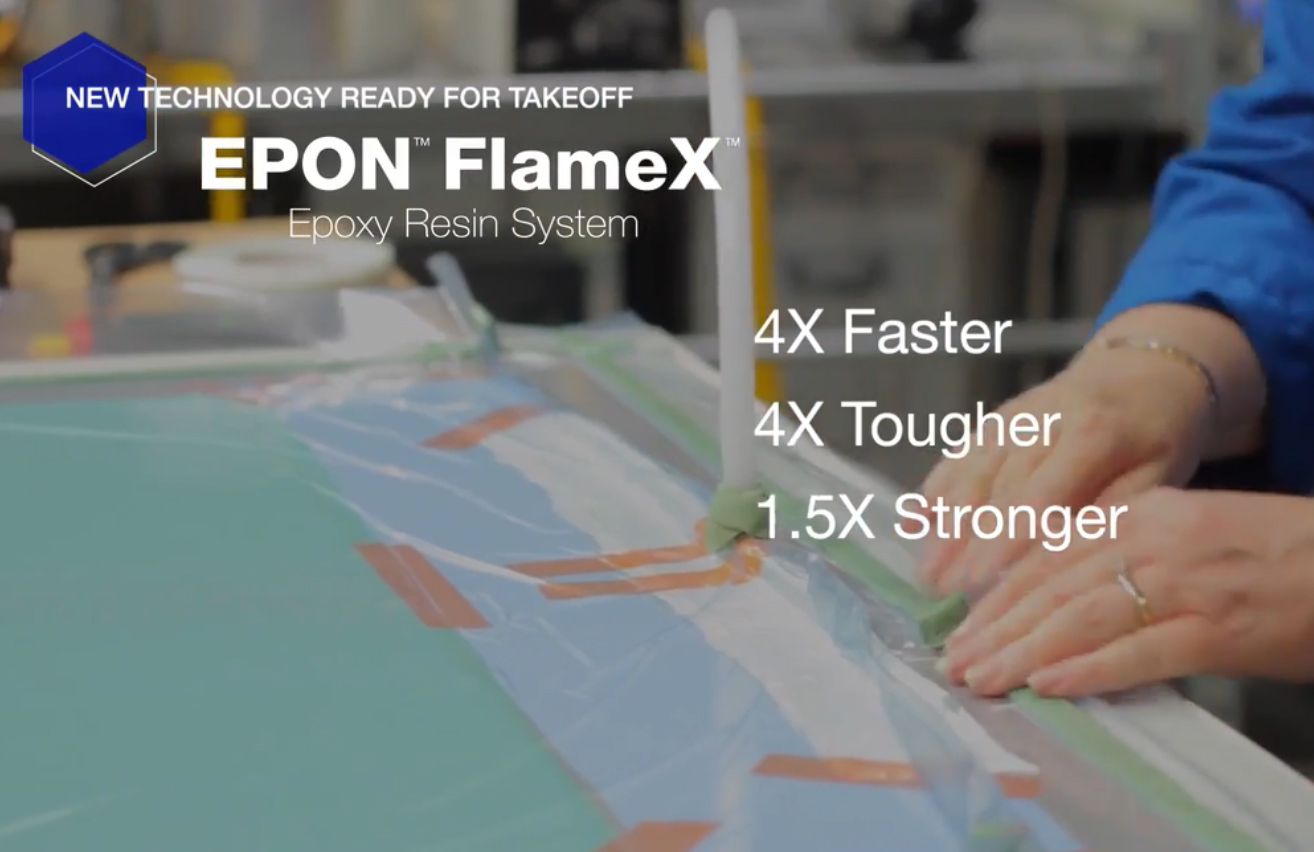
Resina
- Lanxess adiciona duas novas linhas de produção para material composto Tepex
- Compostos de purga para produção de embalagens de poliolefina de parede fina
- Os usos da resina epóxi para a arte estão ganhando popularidade
- Fraunhofer encomenda células de produção Engel automatizadas para P&D de compósitos termoplásticos
- Broetje-Automation amplia portfólio AFP para produção composta em série
- INEOS Styrolution para construir local de produção para compósito termoplástico StyLight
- Total Composite Solutions (TCS) lança solução pré-impregnada de epóxi para a indústria aeroespacial
- Hexion apresenta solução epóxi de dois componentes para produção de compósitos aeroespaciais
- Techsil lança adesivo epóxi transparente para substratos compostos
- Rhodes Interform fabrica prensa composta para AMRC