HP-RTM para produção em série de aeroestruturas CFRP econômicas
Quando a moldagem por transferência de resina (RTM) começou a fazer a transição para RTM de alta pressão (HP-RTM) há cerca de uma década, ela foi elogiada principalmente para aplicações automotivas, reduzindo os tempos de ciclo de peças compostas de horas para menos de 2 minutos. Menos tem sido dito sobre a aplicação dessa tecnologia em peças aeroespaciais. A indústria aeronáutica tem uma longa história com RTM convencional, incluindo seu uso para produzir milhares de pás de ventilador de plástico reforçado com fibra de carbono (CFRP) e caixas de contenção para motores de aeronaves comerciais. A Airbus até mesmo fez o protótipo de um flap multispar composto de uma peça de 7 metros de comprimento para o Airbus A320 usando RTM. Mas é possível fazer a transição dessa experiência com processos de horas de duração para moldagem totalmente automatizada de peças compostas de aeronaves em minutos? Vários jogadores importantes dizem que é possível.
RTM tradicional, referido aqui como LP-RTM para maior clareza, normalmente usa pressões de injeção de 10-20 bar. O HP-RTM, por outro lado, usa pressões de injeção de 30-120 bar.
“Começamos a trabalhar com processamento RTM aeroespacial há 10 anos por meio de um projeto financiado pela UE para fabricar estruturas de fuselagem”, disse Bernhard Rittenschober, chefe de pesquisa e desenvolvimento da Alpex Technologies (Mils, Áustria), um fornecedor de sistemas de ferramentas inovadores para compósitos em série produção de peças. “Naquela época, as previsões eram de que muitas peças do [Airbus] A350 seriam feitas com RTM, mas isso não se concretizou.” A Alpex, no entanto, continuou trabalhando na tecnologia e, como fornecedora das indústrias automotiva e aeroespacial, começou a estudar como os processos usados nessas duas indústrias poderiam ser fundidos. “A ideia era usar a resina epóxi [Hexcel] RTM6 qualificada na indústria aeroespacial, mas com as melhores práticas de ferramentas automotivas e um sistema de injeção automatizado para menor tempo de ciclo”, explica Rittenschober.
O resultado foi um programa de pesquisa de 2013-2015 chamado TAKE OFF, financiado pelo governo austríaco, do qual a Alpex participou com os parceiros Airbus Helicopters (Donauworth, instalação na Alemanha), fornecedor de equipamentos KraussMaffei (Munique, Alemanha), especialista em testes Aeroespacial e Compostos Avançados (AAC, Wiener Neustadt, Áustria) e fornecedor de resina Hexcel (Stamford, Conn., EUA). O programa demonstrou que o HP-RTM resultou em uma redução de 30 por cento no custo de uma moldura de porta A350 e desenvolvimento de tecnologia significativo, incluindo o uso de um sistema de resina de dois componentes (2K), injeção inteligente e monitoramento de cura por meio de sensores in-mold e o capacidade de reduzir ainda mais o tempo do ciclo parcial. Alpex continuou o desenvolvimento e vê potencial para esta tecnologia HP-RTM para ajudar a superar os problemas atuais de produção de CFRP.
Apoiando essa visão, o Composites Technology Center (CTC), uma subsidiária da Airbus Operations GmbH, também vem desenvolvendo RTM automatizado há uma década, primeiro com LP-RTM e depois fazendo a transição para HP-RTM cerca de cinco anos atrás. ( CompositesWorld observou a máquina KraussMaffei HP-RTM da CTC e o trabalho de desenvolvimento durante um tour de 2016 em suas instalações.) “HP-RTM resolve o gargalo de injeção e cura devido à sua mistura de alta velocidade, que permite o uso de resinas altamente reativas”, explica Jan Schiller, Líder de projeto CTC para sistemas de produção e contato líder para tecnologias RTM. “Desenvolvemos um processo que produz peças de geometria um tanto complexa com tamanho de 1-2 metros, atendendo aos requisitos aeroespaciais (por exemplo, 60 por cento do volume de fibra e menos de 2 por cento de vazios) em um tempo de ciclo de 20 minutos.” Ele acrescenta que, após visitas e discussões com fornecedores da Airbus no ano passado, uma série de peças foram identificadas para a transição para HP-RTM, permitindo uma produção com taxas mais altas para as aeronaves A320. “Agora estamos desenvolvendo processamento específico para eles e estamos trabalhando este ano para colocá-los em produção em série.”
moldura da porta HP-RTM A350
O desenvolvimento do Alpex foi concluído por meio do programa TAKE OFF austríaco por meio de um projeto chamado SPARTA. “A Airbus Helicopters escolheu o papel”, lembra Rittenschober. “A moldura da porta é o que você vê quando entra em um A350 com a porta aberta. Tem cerca de 2 metros de altura, 200-250 milímetros de largura e 8-10 milímetros de espessura, com uma forma e características de design complexas para atender aos vários requisitos da porta montada, que é a estrutura primária. ” A porta do A350 é composta por 14 peças fabricadas pela Airbus Helicopters em Donauworth, Alemanha, usando LP-RTM. A moldura escolhida para SPARTA é uma das peças mais desafiadoras da porta. “É uma boa parte de demonstração porque podemos comparar o HP-RTM diretamente com o LP-RTM aeroespacial padrão”, acrescenta Rittenschober.
A Alpex projetou e construiu as ferramentas LP-RTM usadas atualmente para a produção de molduras de portas A350 na Airbus Helicopters. Para o design e construção das ferramentas HP-RTM, aplicaria uma mentalidade mais automotiva. “Nosso objetivo era permitir a automação do tipo automotivo na produção de peças compostas aeroespaciais”, diz Rittenschober. “Isso é necessário se a Airbus pretende construir um futuro A320 com mais peças compostas e a uma taxa de 60 a 100 aeronaves por mês.”
Ele continua:“Estávamos vindo da produção de moldes para a BMW, que tentava ativamente simplificar suas peças e processos para reduzir o tempo de ciclo, enquanto o Airbus vinha da complexidade aeroespacial anterior. Por exemplo, quando começamos, a Airbus Helicopters perguntou quantas peças esse molde teria. ” Observe que a produção atual de portas LP-RTM incluía ferramentas complexas de várias peças. “Explicamos que a ferramenta HP-RTM terá apenas um molde superior e um inferior”, diz Rittenschober.
Assim, a Alpex começou com um projeto de molde simples e, em seguida, adicionou recursos para tornar o processamento mais robusto e flexível - por exemplo, sistemas de vedação usados para produção automotiva de alto volume. “Além disso, temos todos os sensores integrados no molde”, observa ele.
Pré-formas e processo
As pré-formas usadas atualmente para a moldura da porta A350 usam material tecido e requerem várias etapas de redução de volume, resultando em um ciclo de produção de três dias. “Decidimos usar tecido não crimpado (NCF) em vez disso”, diz Rittenschober. “Isso diminui o preço e o tempo de ciclo significativamente. Também acabamos demonstrando algumas peças com as pré-formas tecidas qualificadas para Hexcel, mas vemos uma mudança na indústria de compósitos fora do aeroespacial, com o desenvolvimento da SGL e outros longe dos tecidos e em fitas e formas de baixo custo como NCFs. ”
Quando questionado sobre os pontos de injeção e quaisquer problemas com a lavagem da fibra, Rittenschober explica que a ferramenta HP-RTM tem apenas um ponto de injeção, mas não há lavagem da fibra porque a pré-forma é presa de forma que seja fixada no molde e muito estável.
Outro ponto importante é que a Alpex escolheu usar um sistema de resina de dois componentes (2K) em vez do RTM6 de um componente usado atualmente pela Airbus Helicopters. Rittenschober afirma que o sistema 2K pode ser mais reativo, o que é mais adequado ao HP-RTM, e pode economizar custos porque não é pré-misturado e não requer envio de materiais perigosos. No entanto, requer uma temperatura mais alta de 180 ° C. “Esta foi a parte mais desafiadora para nós”, diz Rittenschober, “porque estávamos mais acostumados a processar a 120 ° C”.
A KraussMaffei instalou, em seu centro de tecnologia leve em Munique, Alemanha, as ferramentas acabadas em seu sistema RimStar Compact HP-RTM com mistura, medidor e injeção automatizados de alta pressão (até 80 bar / 1.100 psi). Em seguida, fez 20 peças de demonstração. Rittenschober descreve o processo de linha de base:injetar a 80 ° C, aumentar a 120 ° C, manter por uma hora, aumentar a 180 ° e manter para uma cura de 90 minutos, desacelerar (2 ° C / min) e desmoldar. “A injeção leva apenas 20 segundos”, diz ele, “mas o ciclo total de moldagem é de cerca de quatro horas”.
Tempo e custo do ciclo
O ciclo de cura ainda longo para a moldura da porta SPARTA é conduzido pela formulação e processamento de resina Hexcel RTM6 que é qualificado para Airbus. “Conseguimos atingir ciclos de cura de 30 minutos a 180 ° C com uma pós-cura adicional sob vácuo para remover o estresse térmico e garantir propriedades mecânicas”, observa Rittenschober, acrescentando que as propriedades eram muito boas e comparáveis ao LP Parte -RTM.
“Mostramos que você pode usar o processo e automatizar a produção para volumes maiores de peças”, diz Rittenschober. “Você pode injetar e curar no molde e depois pós-curar fora da prensa.” Ele admite que isso requer conjuntos extras de ferramentas, mas apenas uma única unidade de prensa e injeção. “Com este sistema, você pode reduzir o custo da peça em € 700, o que permite pagar pelo equipamento facilmente com uma taxa de produção de 500 a 1.000 peças / ano, que não é nem um volume muito alto.”
Desenvolvimento de processo CTC e demonstradores
Ferramentas e processos à parte, o projeto da porta HP-RTM também incluiu o uso inovador do formato de fibra. “Começamos com tecidos já qualificados pela Airbus e tivemos muito sucesso”, lembra Schiller. “Em seguida, continuamos com NCF e têxteis mais inovadores.” Este último incluiu a colocação de fibra seca e intercalação com camadas de estopa espalhadas para maior tenacidade, mas o último apresentou problemas com empacotamento apertado de fibras e camadas, causando baixa permeabilidade e impedindo a infiltração de resina. “Também há desenvolvimentos para resolver isso, como NCF com fibras especiais para melhorar a permeabilidade”, acrescenta.
Em relação às pressões para HP-RTM, Schiller enfatiza que a decisão de usar o processo foi motivada mais pela tecnologia de mistura da indústria de poliuretano do que por altas pressões do processo. “Estamos usando o HP-RTM apenas para obter uma boa mistura de resinas altamente reativas”, explica ele. “Pode haver um pouco de pressão mais alta no molde, mas este é um efeito secundário da injeção rápida. Para peças automotivas com tempos de ciclo de 2 minutos, eles devem infiltrar a pré-forma seca com resina muito mais rápido do que nós. Nosso tempo de cura de 15 minutos permite mais tempo para a infiltração de resina, o que também reduz a pressão no molde. ”
A tonelagem de impressão, entretanto, depende do tamanho da peça. “Fazer peças de até 2 metros de tamanho funciona bem (cerca de 1.500 toneladas), mas peças de 4 a 6 metros exigem o cálculo do business case porque o investimento na prensa se torna muito alto”, diz Schiller. O CTC exibiu uma nervura CFRP de 1,5 por 0,5 metros representando qualquer estrutura primária aeroespacial possível no JEC World em 2018. Ele também receberá uma prensa de tonelagem mais alta no final de 2019.
resinas 2K e controle de qualidade baseado em sensor
Schiller observa que todas as estruturas de aeronaves RTM anteriores usavam apenas sistemas 1K misturados pelo fornecedor, que então certifica a mistura e é responsável por garantir que a resina atenda aos requisitos de qualificação. “Agora estamos considerando sistemas 2K, mas o desafio é garantir a qualidade da mistura”, explica. Os sistemas 1K pré-misturados requerem remessa fria e armazenamento para evitar a reação até o processamento da peça. Assim, as vantagens dos sistemas 2K incluem a eliminação dessa despesa, bem como maior reatividade para processamento mais rápido. Um problema, entretanto, é que a garantia de qualidade (QA) será transferida do fornecedor da resina para o fabricante das peças. “Este controle de qualidade requer a detecção da proporção de mistura e a qualidade da resina misturada. Ambos são necessários para a qualificação do Airbus de um novo material. Portanto, isso significa medições dos dois componentes imediatamente antes da mistura e da resina após a mistura. Hoje, temos apenas sensores antes do cabeçote de mistura, mostrando quanta resina e quanto endurecedor são dosados na mistura. Isso não é suficiente para a qualificação. ”
Enquanto isso, a Alpex está trabalhando para desenvolver um sistema de qualidade em linha para fornecer a verificação de 100% de resina devidamente misturada que a Airbus exige. “Trabalhamos com sensores in-mold da Netzsch desde o início deste desenvolvimento”, observa Rittenschober. “Agora que a Netzsch fez parceria com a Kistler (Winterthur, Suíça), uma nova tecnologia está disponível. Podemos monitorar a temperatura, a pressão e a cura da resina a partir de um único sensor, que incluímos no molde. ”
“O Alpex diz para usar sensores in-mold, e os fornecedores de equipamentos de mistura / injeção dizem que os sensores devem estar em seus sistemas ”, diz Schiller. "Ambos estão certos." Mas ele observa que também há necessidade de melhorias neste último. “No HP-RTM automotivo, a proporção da mistura de resina é medida ao longo de todo o processo, portanto, é uma média”, explica Schiller. “No entanto, preciso dessa medição em cada ponto discreto durante o processo, para saber que a proporção da mistura está sempre correta, mesmo pelo último meio segundo durante a injeção. Precisamos de melhor resolução de tempo nos sistemas de medição. ” Schiller sugere que sensores provavelmente serão necessários antes do cabeçote de mixagem, dentro do cabeçote de mixagem e no molde. “Estamos trabalhando neste desenvolvimento de controle de qualidade em paralelo à avaliação de resinas 2K em aplicações aeroespaciais e, juntamente com os fornecedores de máquinas, identificamos sistemas de sensores que prometem resolução suficiente. Eles serão validados neste ano. ”
A Alpex também está testando um novo sensor piezoelétrico multifuncional híbrido desenvolvido pela Aerospace &Advanced Composites (AAC, Wiener Neustadt, Áustria). Colocado em o molde RTM, atua como um sensor de pressão para monitorar o fluxo de resina frontal no molde. Uma vez que a pré-forma é impregnada pela resina e a cura começa, a mudança no espectro de impedância é usada pelo sensor para determinar o grau de cura. Uma vez que a cura está completa, os sensores piezoelétricos são curados na superfície da peça a ser usada para o monitoramento da saúde estrutural no modo passivo como sensores de emissão acústica ou no modo ativo usando ondas ultrassônicas guiadas. Eles foram demonstrados para monitoramento de impacto e danos em peças acabadas.
Observe que esses dados de processo podem ser analisados por sistemas de produção inteligentes da Indústria 4.0 para identificar rotas para melhorias adicionais em qualidade e eficiência. Esses dados de processo também podem ser registrados para o gêmeo digital de cada parte.
Potencial futuro
Rittenschober diz que o único obstáculo real para a tecnologia HP-RTM é a certificação:“Estamos demonstrando com a Airbus Helicopters que esse processo pode funcionar, mas alguém precisa certificá-lo”. Schiller concorda que é sempre um obstáculo descobrir quem será o primeiro, mas ele também calculou casos de negócios para muitas peças no ano passado. “Para 200 peças por ano, não faz sentido. Porém, para peças no A320, por exemplo, torna-se atraente. Todos os meses, vemos uma meta de taxa mais alta para o programa A320. Muitas dessas peças foram projetadas na década de 1980 e são produzidas manualmente, para que pudessem facilmente ser muito mais eficientes com o HP-RTM. ”
Com tempos de ciclo parcial de 20 minutos demonstrados pelo CTC, o HP-RTM também pode ser atraente para o mercado de aeronaves de decolagem e aterrissagem vertical elétrica (eVTOL), onde volumes de produção de 5.000 aeronaves por ano foram sugeridos como um limite superior pelo fabricante de táxi aéreo UBER.
Alpex continuará a desenvolver uma série de avanços RTM, diz Rittenschober. “Acreditamos que o HP-RTM tem potencial real para ajudar a resolver alguns dos problemas com uma produção industrializada e mais econômica de aeroestruturas CFRP.” Schiller concorda, observando que, para muitas das aplicações específicas do A320, existem inúmeras peças CFRP por conjunto de navios. “Assim, o benefício de um processo mais eficiente começa a se acumular. Se conseguirmos obter o primeiro aplicativo em produção, haverá outros. ”
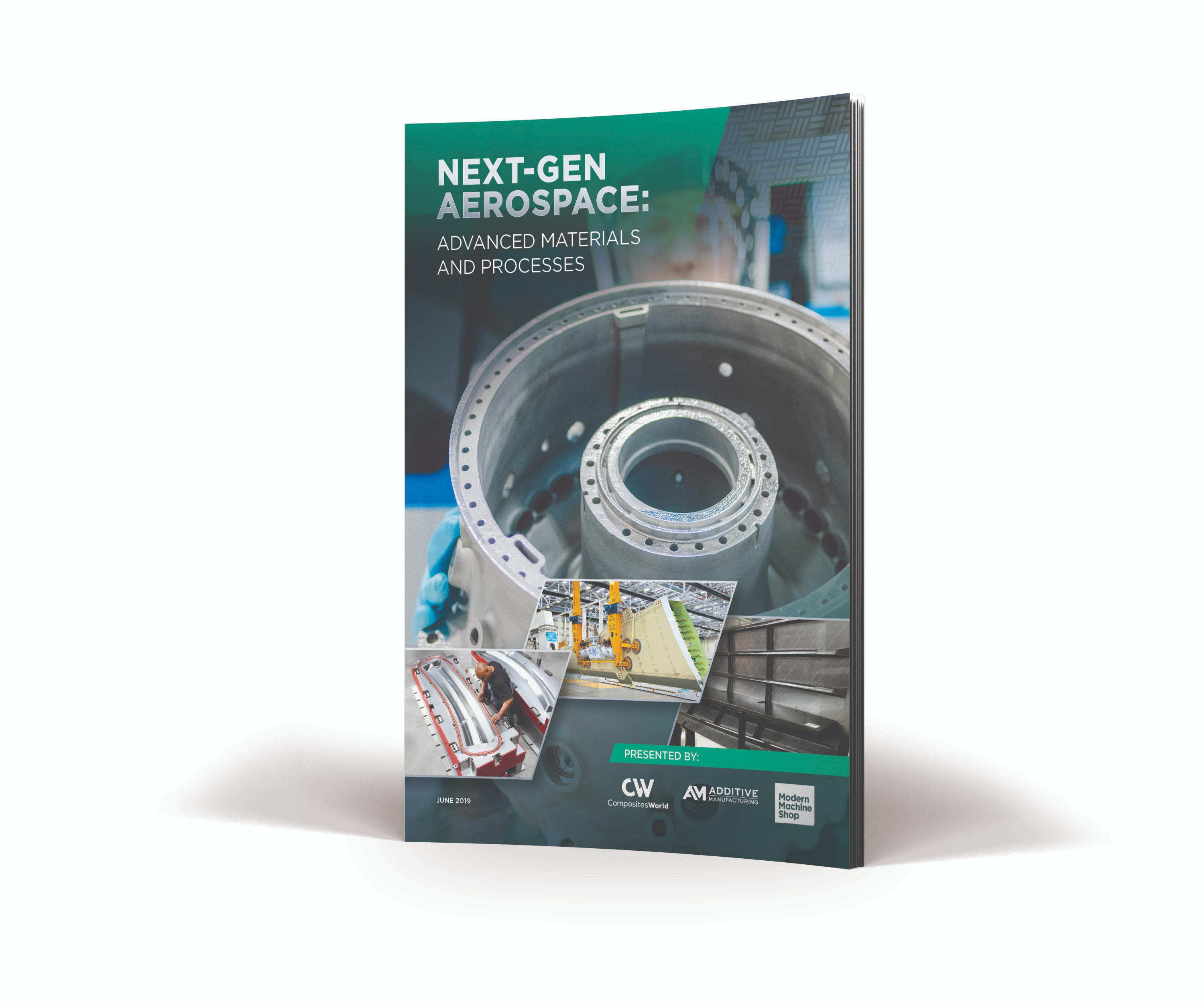
A próxima geração de
Fabricação aeroespacial
Com o setor de aviação comercial projetado para dobrar nos próximos 20 anos, atender à demanda por aeronaves de passageiros e carga exigirá novas tecnologias e taxas de fabricação sem precedentes.
Saiba mais sobre os materiais e processos que moldarão as aeronaves de última geração em uma coleção de histórias de CompositesWorld, Modern Machine Shop e Fabricação de aditivos , disponível para ler ou baixar gratuitamente . Baixe aqui.
Resina
- Aditivos:Corantes econômicos para aplicações de fios e cabos
- Compostos de purga para produção de embalagens de poliolefina de parede fina
- Fraunhofer encomenda células de produção Engel automatizadas para P&D de compósitos termoplásticos
- Projeto para fabricação automatizada de compósitos de aeroestruturas de baixo volume
- Fitas termoplásticas continuam a mostrar potencial para aeroestruturas compostas
- Karl Mayer lança linha de produção para fitas UD termoplásticas
- Jato de água de fusão, laser para eficiência em usinagem CFRP / CMC
- Broetje-Automation amplia portfólio AFP para produção composta em série
- INEOS Styrolution para construir local de produção para compósito termoplástico StyLight
- Práticas de rastreabilidade para produção de fundição