Aeroestruturas termoplásticas primárias dão mais um passo em frente
As características vantajosas dos compósitos termoplásticos, como tenacidade, resistência fora do plano comparativamente alta e sustentabilidade / reciclabilidade, têm atraído design de aeronaves engenheiros com a noção de estruturas primárias compostas termoplásticas por décadas. Mas aeronaves fabricação os engenheiros não têm certeza de como encontrar uma maneira econômica de avançá-los da simulação de CAD para o chão de fábrica. Eles não são, no entanto, dissuadidos:os esforços para desenvolver as tecnologias de fabricação necessárias continuaram em todo o mundo - talvez em nenhum lugar tão tenazmente quanto na Holanda.
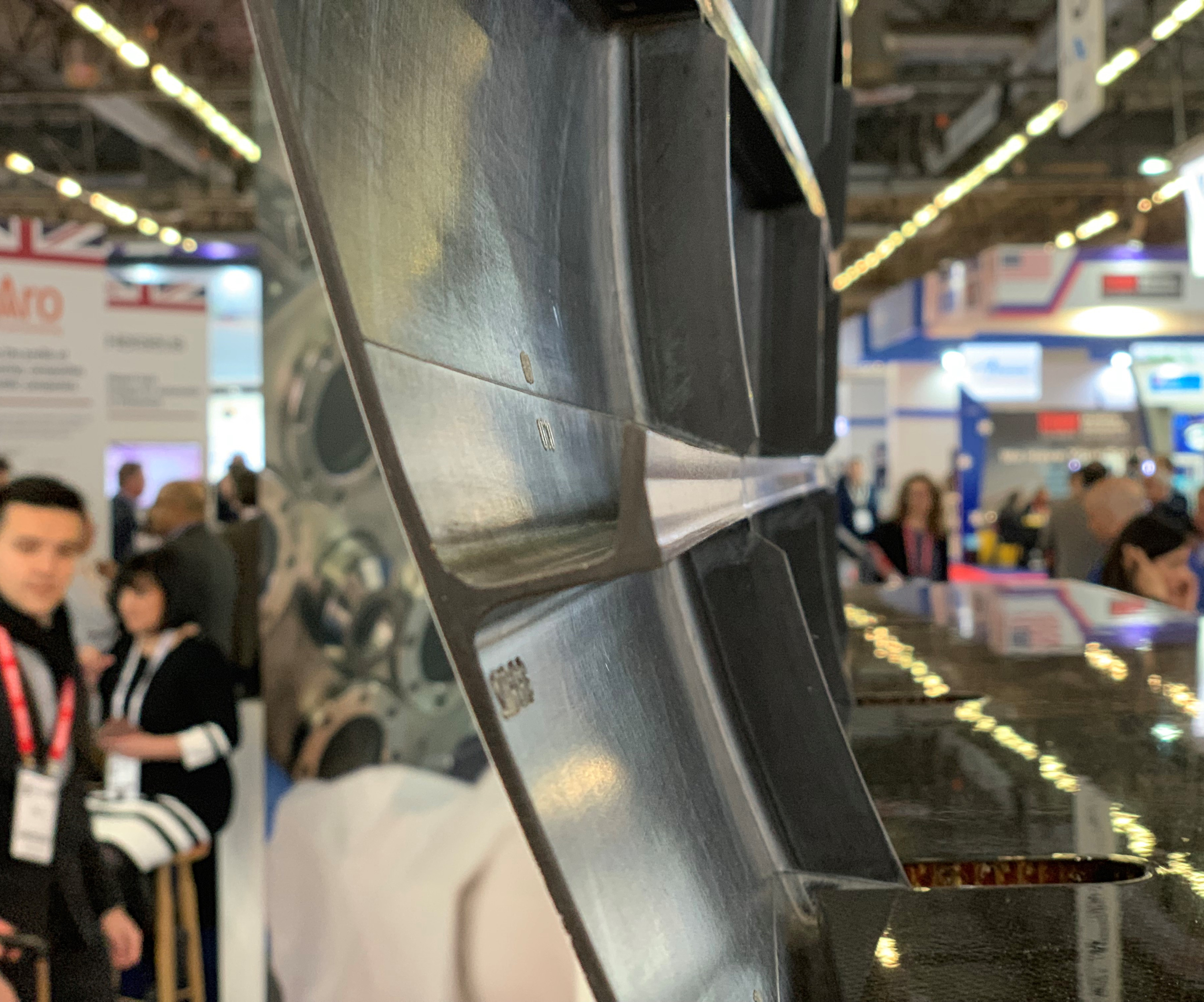
L-longarinas integrais. A fuselagem de fibra de carbono / PEKK do GKN Fokker, projetada e construída para a Gulfstream, incorpora longarinas longitudinais curvas com um ângulo levemente obtuso para permitir a liberação da ferramenta. CW foto | Jeff Sloan
Em 2009, nove empresas industriais e institutos de pesquisa holandeses, juntamente com a Airbus (Toulouse, França), formaram o Consórcio Thermoplastic Affordable Primary Aircraft Structure (TAPAS). A iniciativa expandiu-se para 12 parceiros em 2014 e continuou como TAPAS2. Visando aplicações desenvolvidas pela Airbus sob TAPAS2, GKN Fokker (Hoogeveen, Holanda) desenvolveu recentemente um demonstrador de fuselagem usando o que chama de “tecnologia de ortogrelha com junta de topo” que permite a produção econômica de um projeto de fuselagem composto termoplástico.
A recompensa total de uma estrutura de aeronave primária de composto termoplástico - embora ainda esteja a anos de distância - pode agora estar à vista, já que a Gulfstream Aerospace (Savannah, Geórgia, EUA) fez parceria com a GKN Fokker para avançar sua tecnologia de fuselagem TAPAS2, apontando o caminho para a possível aplicação os materiais e o processo para uma fuselagem completa. A história por trás do painel da fuselagem recentemente desenvolvido (que foi exibido na JEC World no início deste ano) é um dos avanços nos métodos de design e fabricação e, além disso, em uma abordagem de engenharia de design-fabricação mais completamente integrada.
“Tradicionalmente”, explica o engenheiro-chefe da GKN Fokker, Andries Buitenhuis, “quer usem tecidos ou fitas unidirecionais, os designers se apegam principalmente às camadas convencionais de orientações de 0, 90 e 45 graus. Eles trabalhariam em suas tabelas de layup de dobras, independentemente de outras disciplinas. ” A nova abordagem é uma plataforma de software de design-manufatura integrada e digitalizada (desenvolvida por meio da TAPAS) na qual engenheiros de várias disciplinas estão todos olhando para o mesmo modelo digital e têm a capacidade de conceituar designs de peças mais complexos. “Isso abre um novo mundo de possibilidades de otimização sem precedentes”, continua Buitenhuis. “Em formas complexas, as direções das fibras podem estar em todos os lugares. Podemos construir laminados não convencionais e dar uma nova olhada nos projetos permitidos, lacunas e sobreposições de fabricação, raios…. E você pode otimizar a resistência da estrutura localmente. ” Essas opções de projeto expandidas empregam mais plenamente a capacidade de direcionamento de fibra de máquinas de colocação automatizada de fibra (AFP) e avanços em outras capacidades de fabricação discutidas abaixo.
A liberdade de design proporcionada por este sistema digital integrado provou ser indispensável para o design e fabricação de painéis de jatos executivos. Nos projetos de fuselagem TAPAS2, o painel de fibra de carbono / polietercetonecetona (PEKK) (feito com APC PEKK-FC da Solvay) apresenta uma junta moldura a pele soldada e sem fixadores, que é um contribuidor essencial para a relação custo-benefício do projeto. “Prevemos alcançar a paridade de custos com os invólucros da fuselagem de alumínio”, explica Arnt Offringa, chefe de tecnologia de compósitos termoplásticos da GKN Fokker, “e isso ocorre porque os invólucros de alumínio são rebitados”. Espera-se que a eliminação de fixadores mecânicos gere uma redução de custo de 20% e uma redução de peso de 10% nas estruturas primárias da aeronave em comparação com as soluções compostas convencionais. Obviamente, grande parte da economia de custo e peso vem da eliminação dos próprios fixadores, bem como dos custos de mão de obra para instalá-los. Também é de grande importância a eliminação de orifícios nos componentes compostos para acomodar os fixadores - orifícios que requerem reforço adicional e, portanto, aumento de peso.
GKN Fokker atingiu o nível de preparação tecnológica (TRL) 3 (prova de conceito) com Airbus para uma fuselagem pressurizada, demonstrando paridade de custos com painéis de fuselagem de alumínio, sob TAPAS2 em dezembro de 2017. Ao longo do caminho, a equipe do GKN Fokker expandiu sua visão para este termoplástico tecnologia de fuselagem de aviões comerciais a aplicações de jatos executivos.
interesse da Gulfstream
A história de trabalho bem-sucedido da GKN Fokker para a Gulfstream em componentes de compósitos termoplásticos tornou a parceria com o fabricante de jatos executivos um próximo passo lógico. “É amplamente conhecido que a Gulfstream voa há anos com peças compostas termoplásticas”, disse Mark Chapman, gerente da Iniciativa de Estruturas e Materiais Avançados da Gulfstream (ASMI). Ele acrescenta que o projeto do painel da fuselagem "é uma progressão natural do que temos feito, começando com peças mais simples e avançando em direção às peças estruturais primárias". A GKN Fokker fez parceria com a Gulfstream no desenvolvimento de vários componentes secundários de compostos termoplásticos, incluindo elevadores de cauda e lemes, bem como painéis de piso no G650.
Em 2015, Offringa e Buitenhuis apresentaram os desenvolvimentos do projeto TAPAS2 à Gulfstream, e Chapman e sua equipe reconheceram o potencial de colher os benefícios dos resultados do TAPAS2. “Vimos os benefícios potenciais da redução de peso, melhor resistência ao impacto e dureza e desempenho aprimorado”, lembra Chapman. O design sem prendedores também é atraente. “A tecnologia de soldagem nos permitiria montar a fuselagem com mais eficiência” do que uma montagem fixada mecanicamente, diz Chapman.
A parceria com a GKN Fokker apóia a pesquisa e o desenvolvimento da Gulfstream de formatos de fuselagem mais complexos que podem não ser economicamente viáveis de produzir com estruturas de metal. “Você só pode esticar o metal até agora”, observa Chapman. “As emendas e a estrutura de suporte necessárias para formas complexas não são muito eficientes.” Offringa concorda:“Essas geometrias complexas são difíceis de fabricar com tecnologias convencionais”.
Unindo design e fabricação
Para alcançar um design produtivo e livre de fixadores, a abordagem de GKN Fokker se concentra em resistir às duas forças principais às quais as juntas da fuselagem estão sujeitas:pressão da cabine e impactos, como quedas de ferramentas. A pressão da cabine exerce força radial sobre a fuselagem, criando altas cargas na junta entre a estrutura e a pele. Em projetos convencionais, as armações da fuselagem incluem “orifícios de rato” através dos quais passam as longarinas. Sob a força da pressão da cabine, esses buracos de rato servem como descontinuidades que estão sujeitas a altas forças de desprendimento - uma grande preocupação para um design sem fixadores, dada a baixa resistência fora do plano dos compósitos em comparação com os metais. Os impactos também geram cargas elevadas na junta entre a estrutura e a pele porque a estrutura não flexiona sob o impacto.
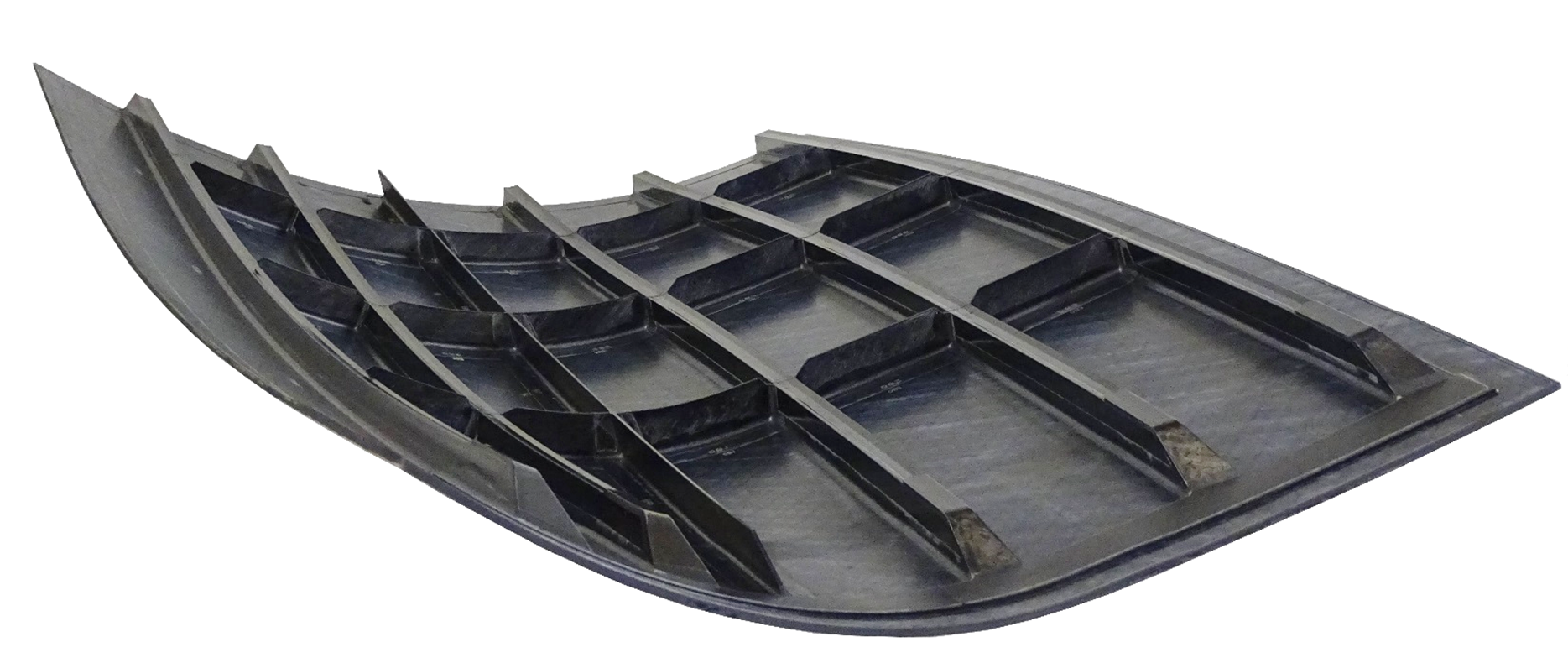
Curvatura dupla. O painel da fuselagem composto termoplástico acomoda a geometria complexa de um jato executivo Gulfstream na popa da fuselagem com layup AFP orientado por fibra da pele e co-consolidação da ortogrelha. Observe as longarinas da lâmina circunferencial, que mais tarde são soldadas ao quadro. Fonte | GKN Fokker
A equipe GKN Fokker / Gulfstream sabia que era inviável enfrentar os desafios criados por uma curvatura complexa com metal ou com abordagens convencionais de projeto-manufatura de compostos. Em particular, Buitenhuis aponta, “Um projeto de fuselagem complexo não seria possível sem direção de fibra.” Esta capacidade das máquinas AFP é o que liberou os projetistas para otimizar a orientação da fibra localmente com base na forma complexa da casca e divergir das opções de orientação de fibra 0/45/90 padrão. “A direção de fibra para otimização de formas e peso é um dos avanços mais significativos deste projeto”, acredita Chapman.
GKN Fokker fez a pele do painel da fuselagem em uma máquina AFP ultrassônica que a empresa desenvolveu para uma colocação rápida de fita termoplástica. A fita é unidirecional, o que também melhora o desempenho do laminado em comparação com as fitas de tecido.
Lidando com sucesso as altas cargas criadas pelas forças de pressão e impacto da cabine, bem como outras demandas de desempenho, o novo conceito desenvolvido sob TAPAS e TAPAS2, e que agora é empregado no painel da Gulfstream, é o que é descrito como uma “junta de topo endurecida ortogonalmente pele com armações soldadas. ” Desempacotar esta descrição destaca três características principais de design e os desenvolvimentos de fabricação necessários para implementá-los:(1) a ortogrelha, (2) a junta de topo e (3) tecnologia de soldagem.
Orthogrid
Os requisitos de resistência do painel são atendidos em parte por meio do reforço da grade ortogonal totalmente interconectada. Essa ortogrelha elimina os picos de carga associados aos orifícios do mouse, livrando o projeto de pontos nos quais as forças de deslocamento são aumentadas. A ortogrelha consiste em longarinas longitudinais contínuas e armações compreendendo dois componentes distintos:longarinas de lâmina circunferencial descontínuas, mas conectadas, e armações soldadas no topo destas.
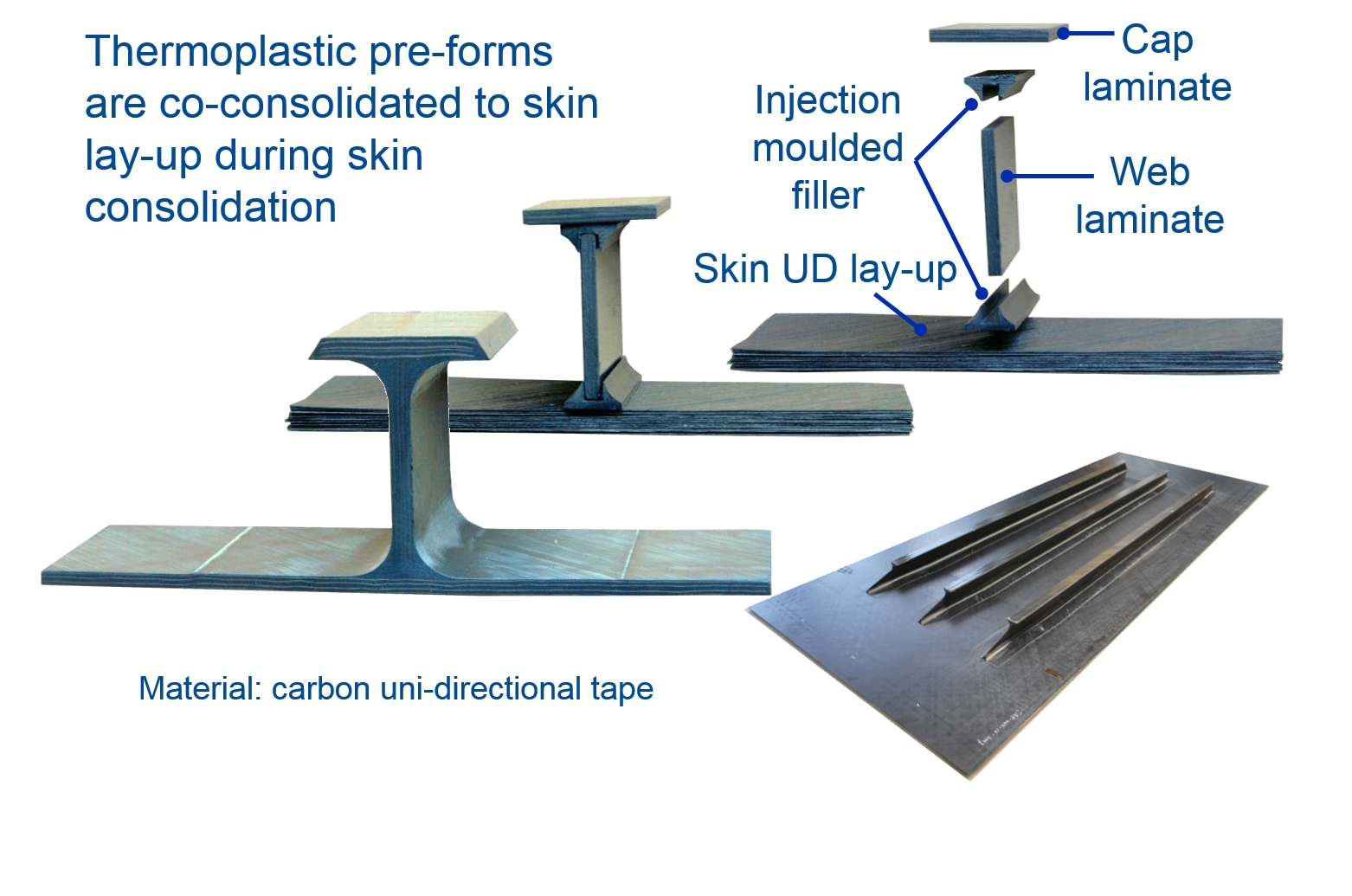
Junta de topo econômica. A GKN Fokker inovou e patenteou uma junta de topo que permite a união de ortogrelha e ortogrelha com pele usando elementos moldados por injeção de fibra curta de baixo custo e laminados planos de fibra contínua para a longarina e tampa (aqui uma longarina em T; o painel Gulfstream incorpora Longarinas L com a mesma técnica). Fonte | GKN Fokker
Portanto, isso representa uma nova geração em design de reforço de fuselagem que evoluiu durante anos de desenvolvimento de ortogrelha. Inicialmente, GKN Fokker usou longarinas em T nas quais as tampas dos membros longitudinais e circunferenciais eram contínuas e sobrepostas nos cantos. A união com a estrutura, entretanto, exigia a remoção da tampa circunferencial. Assim, as longarinas T tornaram-se longarinas L e as armações tornaram-se longarinas de lâmina circunferencial com armações então soldadas a elas.
Outra modificação é necessária porque as longarinas curvas usadas tanto longitudinalmente quanto circunferencialmente tornam a liberação da ferramenta muito mais desafiadora. Assim, as longarinas em L são projetadas com um ângulo da capa até a alma de mais de 90 graus, para que as peças da ferramenta sempre possam deslizar para fora da grade da longarina.
Articulações de topo
A GKN Fokker desenvolveu não apenas o design da ortogrelha, mas também uma nova abordagem de fabricação para a grade, bem como o mecanismo de junção da grade com a pele. “A grade pode ser proibitivamente cara de fabricar”, observa Offringa, “mas nossa grade é construída de laminados planos e 'enchimentos' moldados por injeção simples”.
Mais especificamente, a GKN Fokker aplicou sua tecnologia patenteada de junta de topo ao painel da Gulfstream (também aos painéis TAPAS anteriores). A teia e a tampa dos componentes da longarina em T ou L, bem como os componentes da longarina da lâmina, são fabricados a partir de pré-formas cortadas por jato de água de uma fibra de carbono plana / laminado PEKK. Os elementos de união (pele para web e web para tampa) são moldados por injeção, enchimento em forma de pi feito de um material de fibra curta de carbono / PEKK. Tanto a resina quanto o tipo de fibra de carbono correspondem aos dos membros da grade.
A pele e a ortogrelha são co-consolidadas em uma ferramenta de linha de molde interna Invar (IML). A ferramenta apresenta ranhuras nas quais os componentes da ortogrelha e blocos de ferramentas são carregados. A pele formada por AFP é então colocada no IML e todo o conjunto é ensacado e consolidado em autoclave.
Soldagem
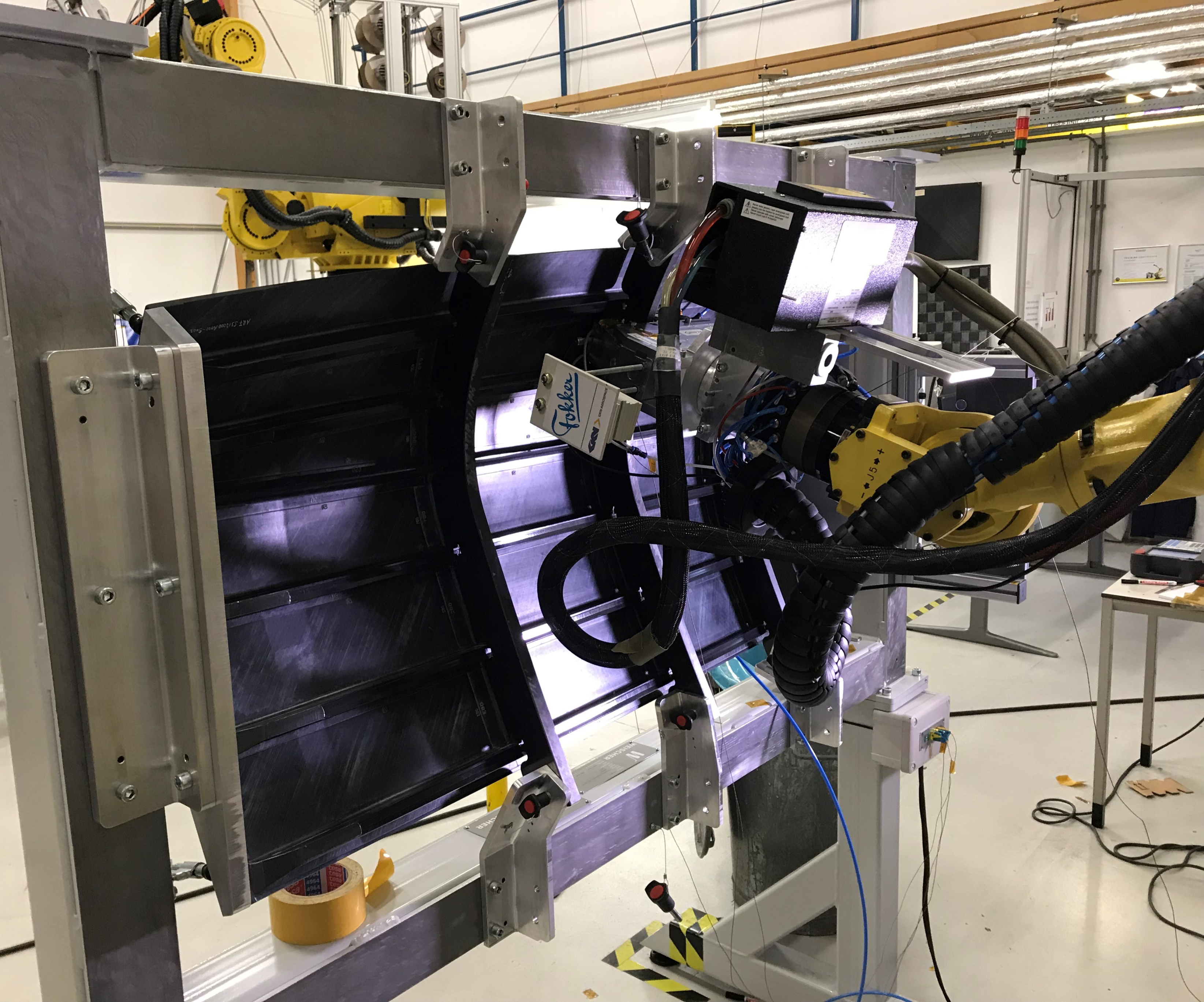
Soldagem automatizada. Contribuindo para a viabilidade econômica do painel de fuselagem de compósito termoplástico, a GKN Fokker desenvolveu e empregou uma técnica de soldagem robótica. Fonte | GKN Fokker
A combinação do projeto da ortogrelha e da junta de topo permite a união sem fixadores da ortogrelha e da estrutura por meio de soldagem. Várias tecnologias de soldagem foram desenvolvidas pelos membros da equipe TAPAS durante a fase TAPAS2, incluindo tecnologias de indução, condução e soldagem ultrassônica. O painel da Gulfstream empregou soldagem por condução para unir a teia da estrutura à longarina da lâmina circunferencial. Essa tarefa é realizada com o cabeçote de solda montado em um robô - outro desenvolvimento que contribui para a manufatura econômica.
Uma etapa de várias
GKN Fokker iniciou sua colaboração com a Gulfstream em 2017, criando conceitos de design para o painel da fuselagem. O projeto e a fabricação de vários painéis curvos seguiram-se em 2018 e 2019, com o primeiro demonstrador de painel marcante exibido na JEC World deste ano.
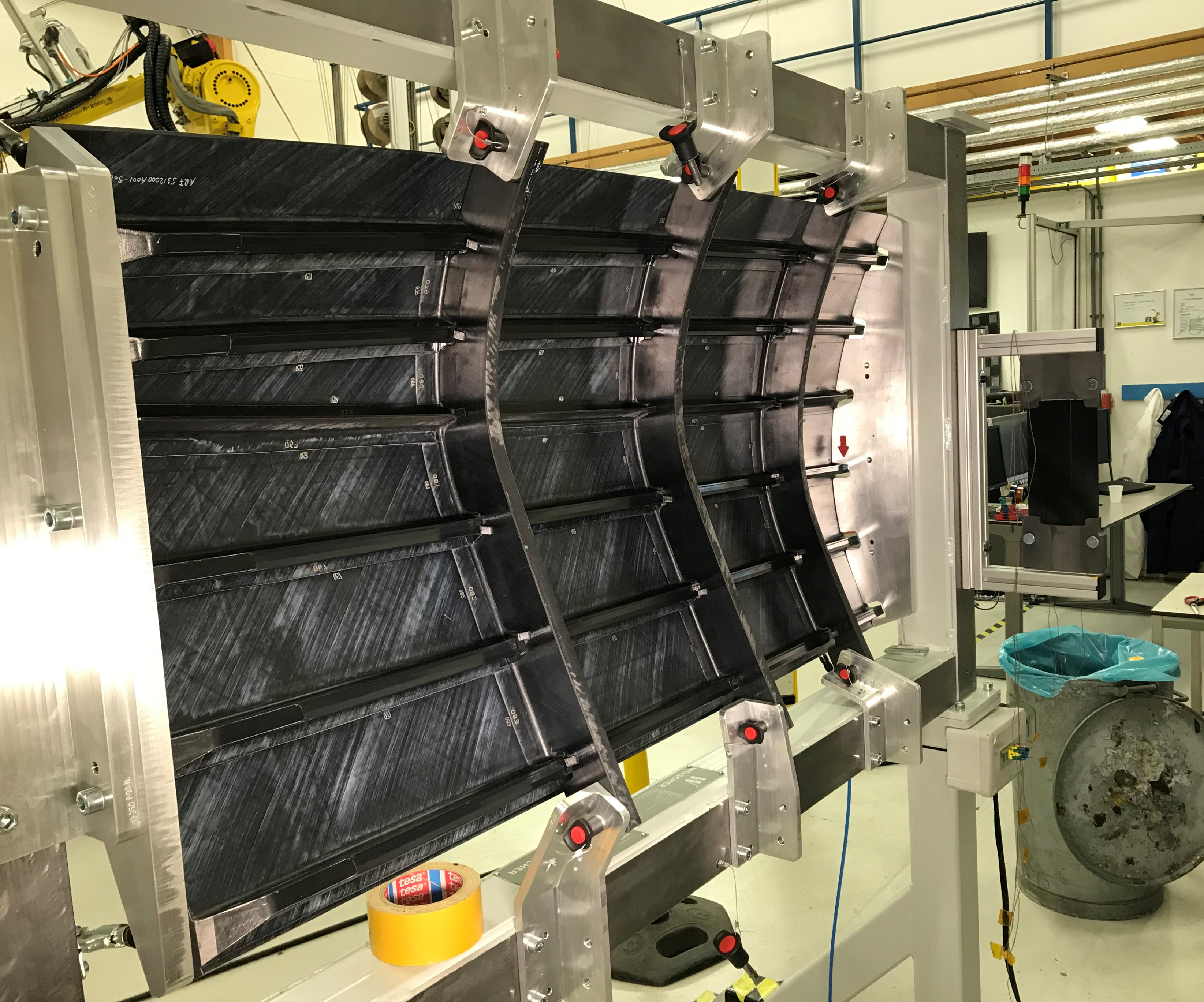
Componente concluído. Com os elementos da estrutura soldados às longarinas da lâmina circunferencial, o painel da fuselagem da Gulfstream está pronto para teste, avaliação e desenvolvimento contínuo enquanto as empresas trabalham para a produção de fuselagens de compósito termoplástico. Fonte | GKN Fokker
GKN Fokker continua a construir painéis e espera alcançar o TRL4 (validação de componentes) ainda este ano. “No momento, estamos discutindo o caminho para a maturidade plena”, relata Offringa. Ressaltando que o design do painel não visa uma plataforma específica, Chapman relata que os testes do painel ajudarão a aprofundar o entendimento da Gulfstream sobre as propriedades e desempenho do material. Em relação ao caso de negócios mais amplo para estruturas primárias de compósito termoplástico, incluindo o desempenho do jato, custo de fabricação, custo de uso e durabilidade, Chapman comenta:"Obteremos um melhor entendimento deles conforme avançarmos na estrada de pesquisa e desenvolvimento. Por enquanto, nosso foco é tornar essas formas complexas de maneira econômica. ”
Resina
- Covestro Aumenta o Investimento em Compósitos Termoplásticos
- Lances mestre termoplásticos reforçados com grafeno lançados
- Solvay Expande a Capacidade do Composto Termoplástico
- As negociações tarifárias tomam outra direção
- Compostos termoplásticos na Oribi Composites:CW Trending, episódio 4
- Instituto de Estruturas e Projeto DLR aumenta a maturidade de estruturas de fuselagem de compósito termoplástico
- Suprem expande as capacidades termoplásticas
- Compósitos termoplásticos de soldagem
- Os designers precisam aproveitar as tendências do setor de fundição sob pressão
- Dicas de design para moldagem por injeção