Combinação de plásticos e compostos para peças Classe A sem ferramentas
Produzir peças compostas com acabamento classe A não é o Santo Graal - muitas empresas fazem isso rotineiramente. No entanto, fazer isso usando infusão de resina sem ferramentas caras ou gelcoats e a uma taxa de uma parte por hora? Bem, isso é algo único.
De plásticos a compostos
A Plastics Unlimited foi fundada há 25 anos por Terry e Nancy Kieffer, explica seu filho Dakota Kieffer, diretor de vendas e marketing da empresa. “Eles eram fazendeiros em Iowa e começaram a procurar uma indústria nova e crescente”, explica ele, “Eles pensavam que plásticos seriam melhores do que soldagem ou marcenaria e não queriam competir com seus vizinhos. Eles examinaram a moldagem por injeção, a rotomoldagem e a reciclagem de plásticos, mas então se depararam com a termoformação e realmente entenderam isso. ” (A termoformação usa calor e vácuo / pressão para moldar as folhas termoplásticas em partes moldadas.)
Em seguida, os pais de Kieffer entraram em contato com uma empresa que fabrica peças de plástico reforçado com fibra de vidro (FRP). “Eles viram como o FRP era forte, mas também que exigia um processo longo e de várias etapas, cerca de quatro horas por peça - portanto, apenas duas peças eram produzidas por dia”, continua ele. “Em comparação com a nossa produção de plásticos, eles acharam que era muito lento. Estávamos virando peças a cada 2-6 minutos - talvez até produzindo 5-6 peças de uma vez - então, milhares de peças por dia. ” Para preencher a lacuna, o pai de Kieffer teve a ideia de usar uma concha de plástico termoformada como ferramenta .
O resultado é um processo de fabricação de peças compostas sem ferramentas, que a Plastics Unlimited chama de Composto Projetado Sem Ferramentas (TEC). “Ele remove o gelcoat e etapas de liberação da ferramenta ”, diz Kieffer. “Além disso, quando você termoforma, pode inspecionar a superfície Classe A e certificar-se de que está perfeita.” Em outras palavras, a superfície Classe A não está escondida sob um laminado composto. “Tudo o que era necessário era uma única ferramenta de termoformação, e o processo ainda fazia sentido para nossos clientes de peças de plástico.”
Processo composto patenteado
Kieffer observa que um composto combina dois materiais para fazer um material melhor do que qualquer um dos constituintes isoladamente. “Estamos combinando dois tipos diferentes de materiais e dois processos diferentes para fazer um produto melhor.” Notavelmente, um produto que compreende plástico, resina e fibra de vidro para oferecer uma combinação única de benefícios. “Os plásticos têm um desempenho muito melhor em impacto do que os gelcoats”, explica ele. “Também é possível imprimir qualquer textura ou desenho no plástico, por exemplo, um padrão de camuflagem. Os plásticos também oferecem muita profundidade de imagem sem polimento posterior, o que remove as operações de acabamento secundárias. ”
Enquanto isso, em comparação com a pulverização de fibra picada em um processo de moldagem aberta, esta tecnologia patenteada permite um maior conteúdo de fibra, maior qualidade e nenhum / baixo composto orgânico volátil (VOCs). Ele ressalta que pulverizar fibra picada em plásticos para banheiras e spas não é patenteado. “Sempre usamos infusão a vácuo para fazer o FRP parte do produto”, diz Kieffer, acrescentando que “nossas peças têm um acabamento liso, então somos mais um RTM leve com placas de calafetagem. Estamos sempre levando isso para o próximo nível. Os clientes nos procuram com um problema e tentamos encontrar uma solução que atenda às suas necessidades. Somos muito inovadores e patenteamos nossos novos desenvolvimentos. ”
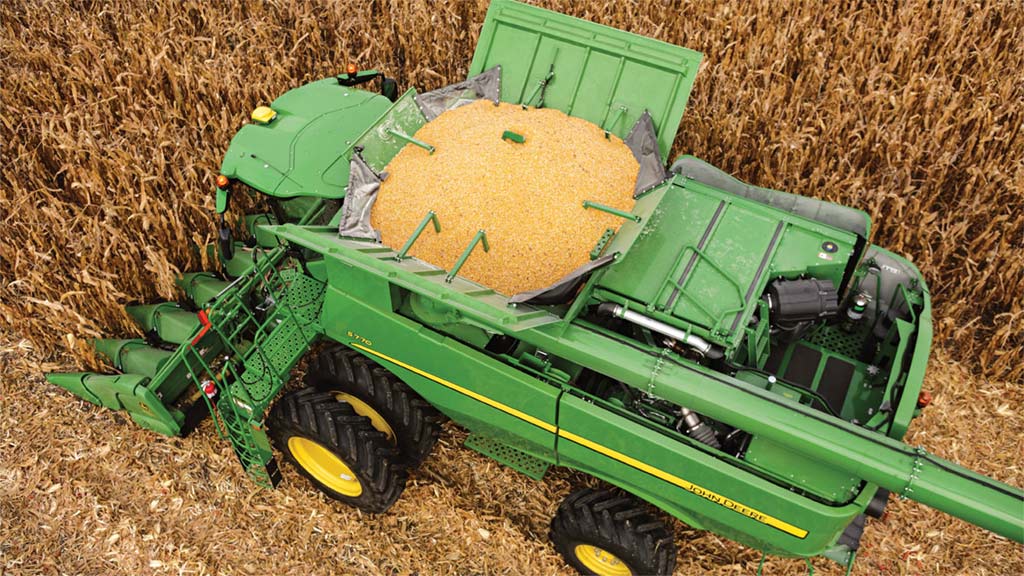
Partes de exemplo
Uma das peças que a Plastics Unlimited produz usando esse processo é uma extensão de tanque graneleiro para colheitadeiras John Deere feitas pela Deere &Company (Moline, Illinois, EUA). “Esta é a parte superior da colheitadeira, que é aberta, onde fica o grão”, explica Kieffer. “Comparado com o tanque de aço original, o nosso é mais durável. Nós o fazemos com um acabamento liso por dentro e verde John Deere por fora com inserções pretas nos cantos. É a maior extensão de tanque graneleiro disponível e pode dobrar. É um produto com mais engenharia em comparação com nossos concorrentes, com espuma e nervuras adicionadas para aumentar a rigidez. ” Também é necessário algum reforço de aço, que na verdade é moldado, diz Kieffer, "não colado secundariamente".
Esta combinação de materiais e processo confere muita tenacidade à peça acabada. “Temos vídeos de queda de blocos de concreto nessas partes”, diz Kieffer. Ao moldar acessórios de aço, ele diz que a resistência à tração pode 4-5 vezes a obtida com a colagem secundária usando adesivos de metacrilato de metila padrão da indústria.
A Plastics Unlimited pode fazer até 2.500 dessas peças por mês, com alguns dos painéis medindo 5 pés por 7 pés. “Isso exigiria ferramentas caras, se não fosse feito com nosso método”, diz Kieffer, observando que o TEC pode ser usado para peças muito grandes - até 2,5 metros por 3,5 metros. “Nossas peças podem ter mais formato e geometria do que aço. Isso é importante para nossos clientes porque permite que eles se diferenciem por meio do estilo. Nossa resistência aos raios ultravioleta também é melhor do que a maioria dos gelcoats. ”
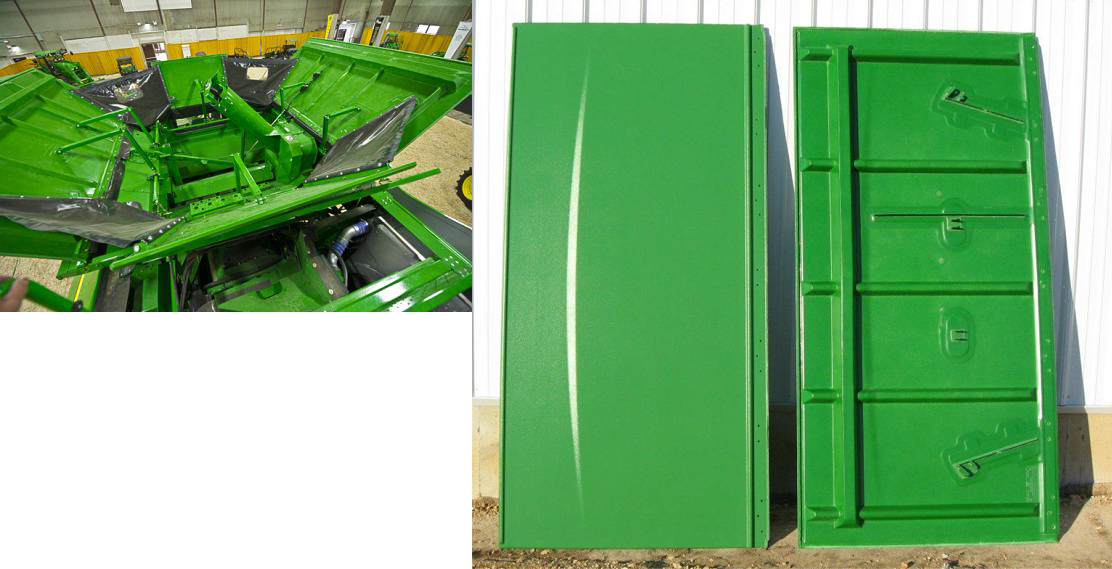
A Plastics Unlimited fornece peças para uma variedade de empresas, incluindo elevadores telescópicos Harley-Davidson e Gehl. “Também fazemos peças de toque suave que parecem e têm a sensação de couro”, diz Kieffer. A empresa também fabrica componentes de caminhões para Navistar e peças de veículos recreativos (RV) para Winnebago. “Preferimos a produção em volume, de 100.000 peças por ano até algumas centenas.”
Kieffer reconhece que a injeção de fibra longa (LFI) e a moldagem por injeção de resina (RIM) são processos competitivos, “mas as peças não são tão estruturais quanto o que fazemos. Por exemplo, um tanque graneleiro da colheitadeira contém 400 alqueires, o que exerce 10 toneladas de força. As peças RIM, que não são fortemente reforçadas, simplesmente não podem atender a este tipo de requisito de carga e as ferramentas RIM são muito caras. ”
Desenvolvimento contínuo
“Fazemos muito trabalho de P&D com nossos clientes”, afirma Kieffer. “Exploramos diferentes resinas, espumas, laminados, camadas de reforço e acabamentos, e depois mostramos protótipos para que possam fazer testes com muita rapidez. Tentaremos tornar a peça mais manufaturável, procurando como reduzir custos e melhorar o desempenho, além de atender aos vários requisitos em serviço, como temperaturas extremas de calor e frio e impacto. ”
A Plastics Unlimited possui 100.000 pés quadrados de espaço de produção e 75 funcionários, incluindo uma equipe de três engenheiros. Sua máquina CNC Thermwood de 5 eixos permite a produção interna de ferramentas e também a prototipagem rápida, esta última importante para os clientes que buscam encurtar os prazos de desenvolvimento.
“Também estamos trabalhando com empresas de transporte público e aeroespacial”, ele continua. “Muitos interiores de metrô são atualmente FRP com gelcoat mais estrutura de alumínio por trás dele. Eles precisam de um acabamento superficial leve, mas também cosmético. Estamos analisando uma ampla gama de aplicações, incluindo médicas, elétricas e de construção. ”
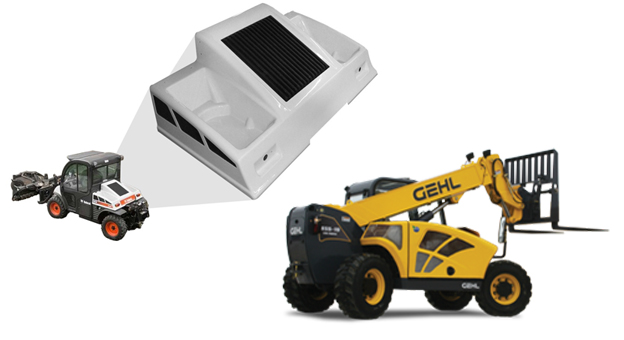
A empresa também está estudando a termoformação de plásticos reforçados com fibra de carbono (CFRP). “Formamos os materiais Tepex e Polystrand e estamos trabalhando em vários desenvolvimentos com um cliente médico”, diz Kieffer. “Podemos usar materiais plásticos de alta qualidade, como Kydex, e reforçá-los com CF / epóxi para a indústria aeroespacial, ou materiais como poliuretano, policarbonato e ABS, que fornecem um bom acabamento externo e são econômicos. Por trás desses últimos plásticos, podemos usar poliéster reforçado com fibra de vidro, viniléster ou laminados de epóxi. ”
A Plastics Unlimited opera na interseção de plásticos, metais e compostos, diz Kieffer. “Nossas peças são normalmente 30 a 40 por cento mais leves que o aço. Mas descobrimos que o mercado ainda precisa de um pouco de educação sobre o que são os compósitos e o que eles podem fazer ”. Ao mesmo tempo, a empresa vê um grande potencial de crescimento futuro. “Nem todos os materiais funcionam juntos e, especialmente, nem todas as resinas funcionam com todos os plásticos”, observa ele. “Fizemos tantos testes e desenvolvemos ao longo dos anos que entendemos muito bem o cenário e as possibilidades. Temos uma experiência única e oferecemos uma gama única de soluções possíveis. ”
Resina
- Kubernetes no Azure:ferramentas e dicas para o sucesso
- Padrões e ferramentas de programação para computação em nuvem
- TPEs ‘Smooth-Touch’ para embalagens emergentes e requisitos de design de peças
- Peças do braço do robô para automação de seleção e posicionamento
- Personalização de sensores ultrassônicos para otimização e controle de processos compostos
- Resinas epóxi reprocessáveis, reparáveis e recicláveis para compósitos
- Victrex e parceiro Bond para impressão 3D de peças PAEK
- 20 ferramentas e equipamentos básicos de soldagem para iniciantes
- Processos de acabamento para peças e componentes
- MANUTENÇÃO DIÁRIA E PERIÓDICA PARA TRANSPORTADORES E PEÇAS