Fibra de carbono habilitará eVTOLs de táxi aéreo
Este blog é uma resposta a um artigo de janeiro de 2019 em WIRED A revista, que afirma que a produção de composto de fibra de carbono está impedindo o desenvolvimento de aeronaves de veículos elétricos (EV) / decolagem e pouso vertical (VTOL) para o mercado de mobilidade urbana e táxi aéreo. Vou debater isso, mas também oferecer algumas novas tecnologias potencialmente disruptivas, então leia até o fim.
Embora eu aplauda o autor por cobrir essa indústria emergente rapidamente e por apontar a necessidade de projetar tendo a capacidade de fabricação em mente, ele às vezes é enganoso, provavelmente porque não tem muito conhecimento sobre a indústria de compósitos. Por exemplo:
Embora isso seja tecnicamente verdade, a Airbus está aumentando para 60 aeronaves A320 / mês em meados de 2019 e a Boeing está a caminho de 57 aeronaves / mês para o B737, também em 2019. Para o A320, isso significa produzir três 6,3 m de altura conjuntos de cauda plana vertical de plástico reforçado com fibra de carbono (CFRP) por dia e também três 12,45 m Conjuntos de cauda plana horizontal CFRP por dia .
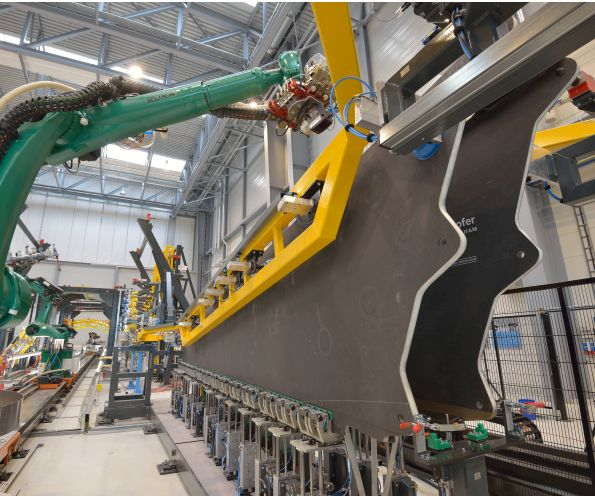
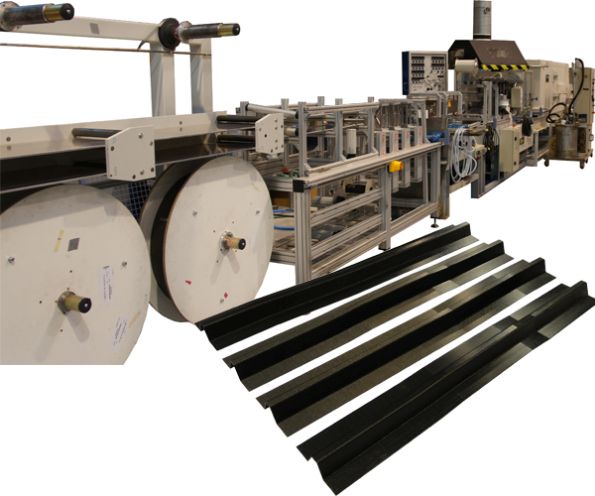
Além disso, a Airbus tem qualificado uma tecnologia após a outra - muitas usando compostos e todas destinadas a 60-70 aeronaves por mês - para a próxima iteração do A320, conhecido como A320 Neo Plus. Essas tecnologias de compósitos abrangem um portfólio que inclui moldagem por transferência de resina (RTM), moldagem por compressão de compostos de moldagem de folhas (SMC) e compostos termoplásticos (TPCs) que têm tempos de ciclo facilmente capazes de mais de 700 aeronaves por ano. Algumas das tecnologias mais recentes em desenvolvimento estão reduzindo os tempos de ciclo da peça CFRP de 4 horas para 15 minutos ou menos. A maioria das novas tecnologias qualificadas pela Airbus são altamente automatizadas, assim como os novos métodos de montagem.
A indústria automotiva também pavimentou o caminho para uma produção em massa maior do que a exigida pelos eVTOLs ( WIRED citou a demanda projetada de 23.000 veículos até 2035). BMW está aumentando a produção de seu i3 e i8 modelos - ambos apresentam células de passageiros totalmente CFRP - de 130 a 200 unidades / dia e a Voith Composites, fornecedora da Audi, está produzindo a parede traseira CFRP para o A8 a uma taxa de 150-300 unidades / dia . Observe que o BMW i3 e i8 os módulos são muito semelhantes à fuselagem mostrada abaixo para os Airbus Helicopters EC 135 - ambos os fabricantes então fixam os componentes externos e internos a esta estrutura.
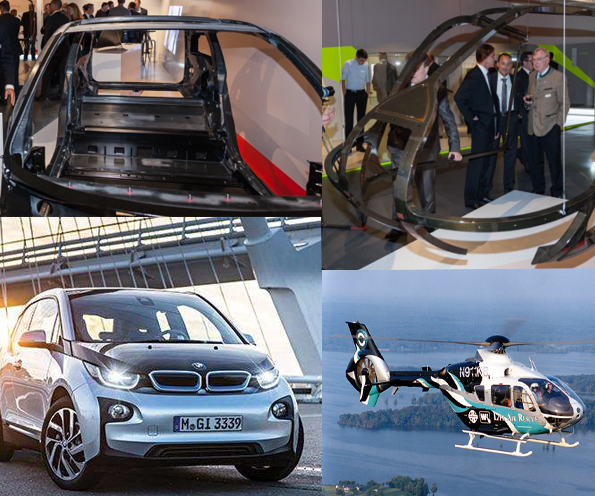
Os chassis BMW i3 e i8 são muito semelhante ao dos Airbus Helicopters EC135.
FONTE: Milestones of the Leading-Edge Cluster - Review and Future Prospects, MAI Carbon, pp 36-7 (superior), BMW and Airbus Helicopter (inferior).
Enquanto isso, o Audi A8 a parede traseira é feita com um tempo de ciclo de 5 minutos usando RTM e colocação automatizada de fita de fibra de carbono seca, adaptada em comprimento e orientação da fibra para atender a cargas específicas, e variando de uma base de 6 camadas (1,5 mm de espessura) até 19 camadas (3,7 mm de espessura) onde o reforço local é adicionado para atender ao carregamento de ponto alto. Esta peça única fornece 33% da rigidez torcional da célula de transmissão a 50% do peso em comparação com um conjunto de três a cinco peças de alumínio soldadas.
O Audi 2019 O A8 apresenta uma parede traseira CFRP feita em 5 minutos com fita de fibra de carbono. FONTE:Audi e Voith Composites.
Termoplásticos
Mas esses exemplos nem estão explorando a tecnologia termoplástica, favorecida como a escolha para a nova aeronave de médio porte (NMA) da Boeing, que deve ser anunciada antes do 2T 2019. As peças termoplásticas estão voando em aeronaves desde a década de 1990, enquanto o desenvolvimento continua , com a Airbus e fornecedores europeus Tier 1 prototipando seções cada vez maiores da asa e da fuselagem (com reforços integrados), escalando para demonstradores de fuselagem em tamanho real este ano. Observe que os compósitos termoplásticos também permitem a soldagem, dando mais oportunidades para eliminar os fixadores e a montagem.
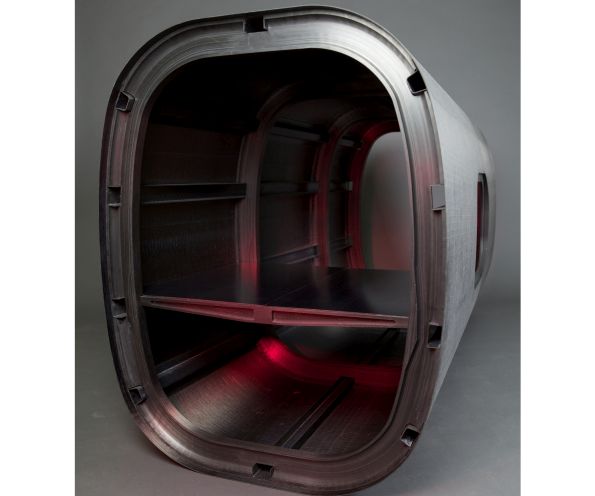
Automated Dynamics, agora parte do Trelleborg Group , produziu esta lança traseira de helicóptero CF / PEEK integralmente reforçada em 2012 usando consolidação in-situ durante a colocação automática de fibra, eliminando longos ciclos de autoclave, bem como fixadores e adesivos.
FONTE:Automated Dynamics, Trelleborg
A cadeia de suprimentos de materiais e processamento TPC se fundiu rapidamente nos últimos três anos, com todos os principais fornecedores de fibra de carbono agora produzindo fitas termoplásticas e peças sobremoldadas de baixo tempo de ciclo, demonstradas por várias empresas para aplicações aeroespaciais e automotivas. A soldagem termoplástica também foi demonstrada por várias empresas.
Trecho de “Overmolding as enabler for composites, aeroespacial to automotivo”, entrevistando Scott King no fabricante de compósitos CCP Gransden:
CCP Gransden refinou sua termoformação de uma etapa e tecnologia de sobremoldagem de composto termoplástico para produzir componentes leves e complexos com tempos de ciclo tipicamente <2 min, usando uma ampla gama de polímeros e fibras. FONTE:CCP Gransden
Tecnologia mais recente
Mas a tecnologia avançou desde 2014 e agora inclui vários desenvolvimentos interessantes:
Termofixos termoplásticos sobremoldados
O projeto OPTO-Light em AZL Aachen demonstrou reforços e clipes de composto termoplástico sobremoldado (TPC) em uma fibra de carbono / epóxi parte composta.
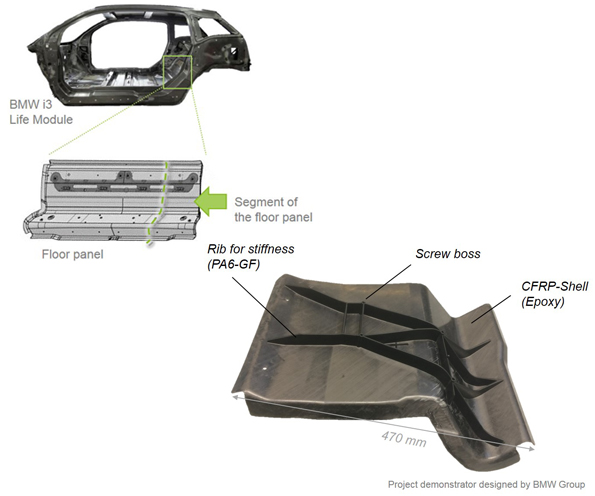
Overmolding + Pultrusões de Carga UD
O projeto MAI Skelett demonstrou pultrusões TPC sobremoldadas em um processo de duas etapas e 75 segundos para produzir um membro estrutural do teto / quadro do pára-brisa que excede todos os BMW i3 requisitos de peças ao integrar acessórios e clipes, bem como alterar o comportamento de colisão do modo de falha frágil para dúctil para aumentar a resistência residual da BIW.
O parceiro do projeto SGL Carbon agora fornece fibra de carbono com dimensionamento adequado para soluções de matriz única usando a família PP ou PA6, incluindo pultrusões, organosheet e composto de sobremoldagem, bem como experiência em design e processo para desenvolvimento de peças, este último por meio de seu Centro de Aplicações Leves (LAC, Meitingen, Alemanha).
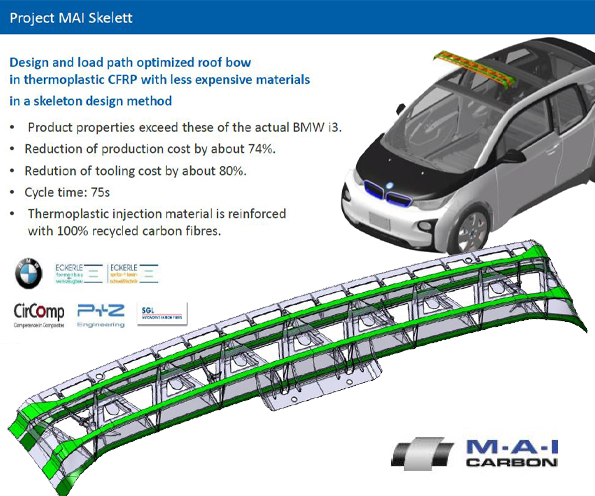
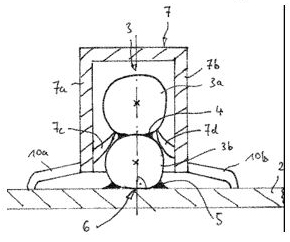
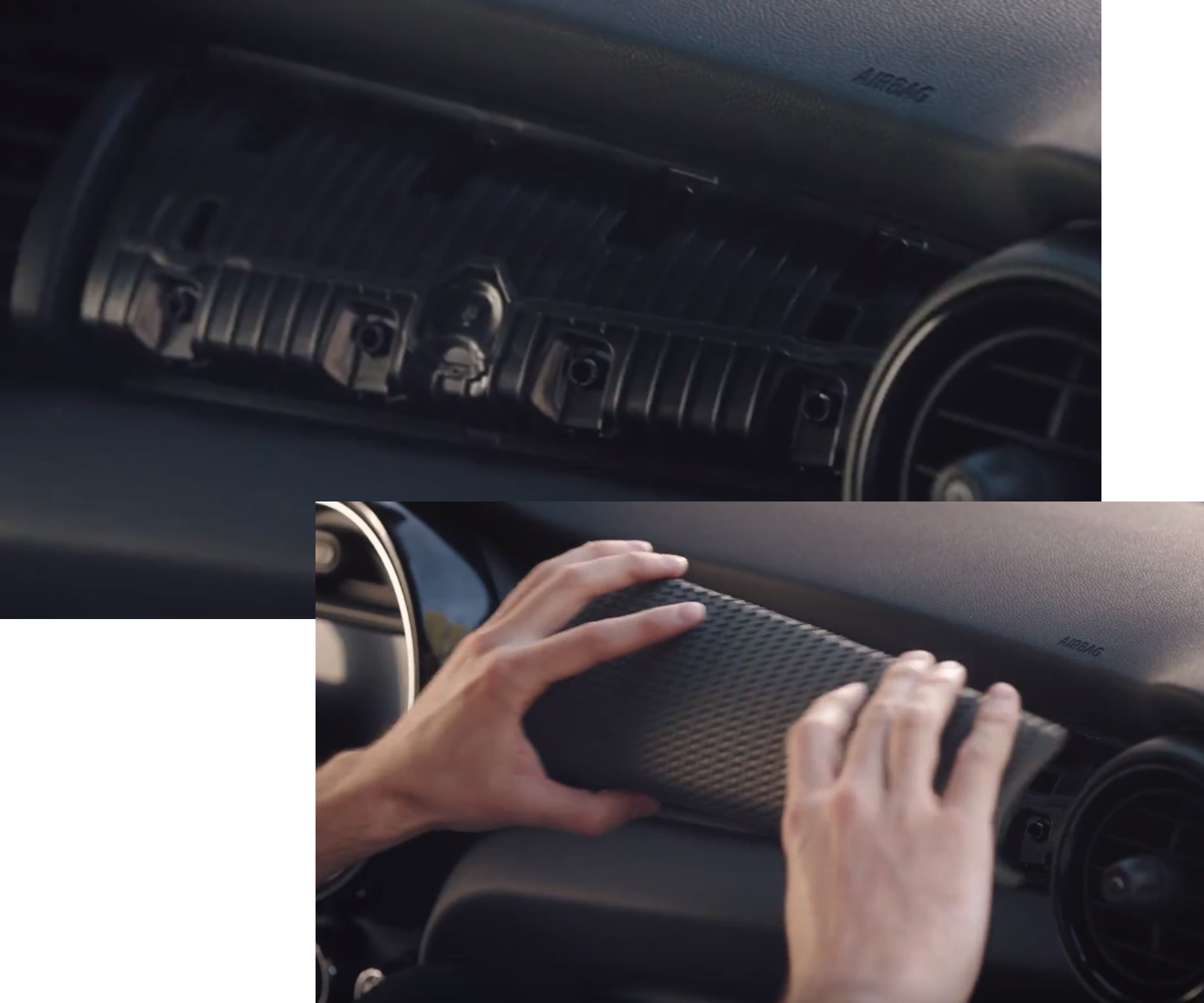
Novo patenteado da BMW , o sistema de fixação de alta precisão utiliza clipes moldados por injeção ou sobremoldados (parte inferior) e bolas impressas em 3D (parte superior) sem prendedores, orifícios perfurados ou adesivo. As imagens inferiores mostram como este sistema permite que o acabamento interior impresso em 3D personalizado seja “encaixado” como parte do programa MINI Yours Customized 2019.
FONTE:Patente DE 10 2013 214 269 B3 (topo)
https://www.youtube.com/watch?v=1pyxNKw-nf8 (inferior)
Voltar para o WIRED artigo e suas reivindicações não informadas:
É verdade que este método de produção de CFRP tem sido usado por muitos anos, mas também é verdade que os fabricantes de aeronaves e automotivos já mudaram para materiais e processos mais automatizados e com resíduos quase nulos, bem como termoplásticos com vantagens comprovadas em eliminando fixadores, permitindo reciclabilidade / conteúdo reciclado e capacidade de reparo.
No final, o WIRED O autor contradiz toda a sua tese porque o pioneiro da eVTOL ICON planeja não apenas avançar com sua fuselagem CFRP, mas também fabricar peças para aeronaves maiores. Obviamente, a fibra de carbono não vai aterrar o eVTOLS, mas, em vez disso, já desempenha um papel fundamental nas empresas que estão promovendo uma engenharia inteligente para uma ampla gama de veículos futuros, tanto no ar quanto na estrada. Usar o que há de mais moderno em tecnologia faz sentido porque todos esses novos veículos precisam ser certificados de qualquer maneira.
Um ponto-chave era feito no artigo do CEO da BetaTechnologies, Kyle Clark:
O CEO da Blue Force Technologies, Scott Bledsoe, também enfatizou a importância de ter aerodinâmica, propulsão, estilo, estruturas e fabricação equipes, cada uma com um assento igual à mesa durante cada etapa de design e desenvolvimento.
Mas talvez o mais importante seja se manter atualizado sobre onde a fabricação de compósitos está se movendo e se conectar com os diversos fornecedores de materiais, equipamentos e tecnologia que desejam compartilhar sua experiência e ajudar a desenvolver aplicações futuras. Entre em contato conosco em CompositesWorld porque é isso que fazemos - fornecer conexões e informações técnicas e confiáveis.
Resina
- Fibra de carbono
- 3 razões pelas quais os fabricantes de fibra de carbono farão mais em breve
- O que é fibra de carbono?
- A ascensão dos plásticos reforçados com fibra de carbono
- Plástico Reforçado com Fibra de Carbono (CFRP)
- A fibra de carbono é condutiva?
- O último GT do Ford será um supercarro de fibra de carbono de edição limitada
- Cabine de aeronave reimaginada por Pagani e Airbus tem teto digital
- Tênis de fibra de carbono Air Jordan 1 é um item obrigatório do colecionador
- Reciclagem de compósitos - chega de desculpas