Fibra de carbono
Antecedentes
Uma fibra de carbono é um filamento longo e fino de material com cerca de 0,0002-0,0004 in (0,005-0,010 mm) de diâmetro e composto principalmente de átomos de carbono. Os átomos de carbono estão ligados entre si em cristais microscópicos que estão mais ou menos alinhados paralelamente ao longo eixo da fibra. O alinhamento do cristal torna a fibra incrivelmente forte para seu tamanho. Vários milhares de fibras de carbono são torcidas juntas para formar um fio, que pode ser usado sozinho ou tecido em um tecido. O fio ou tecido é combinado com epóxi e enrolado ou moldado para formar vários materiais compostos. Materiais compostos reforçados com fibra de carbono são usados para fazer peças de aeronaves e espaçonaves, carrocerias de carros de corrida, eixos de tacos de golfe, quadros de bicicletas, varas de pesca, molas de automóveis, mastros de veleiros e muitos outros componentes onde peso leve e alta resistência são necessários.
As fibras de carbono foram desenvolvidas na década de 1950 como reforço para componentes plásticos moldados em alta temperatura em mísseis. As primeiras fibras foram fabricadas aquecendo fios de rayon até que se carbonizassem. Este processo provou ser ineficiente, pois as fibras resultantes continham apenas cerca de 20% de carbono e tinham propriedades de baixa resistência e rigidez. No início dos anos 1960, um processo foi desenvolvido usando poliacrilonitrila como matéria-prima. Isso produziu uma fibra de carbono que continha cerca de 55% de carbono e tinha propriedades muito melhores. O processo de conversão de poliacrilonitrila rapidamente se tornou o principal método para a produção de fibras de carbono.
Durante a década de 1970, o trabalho experimental para encontrar matérias-primas alternativas levou à introdução de fibras de carbono feitas de um breu de petróleo derivado do processamento de petróleo. Essas fibras continham cerca de 85% de carbono e tinham excelente resistência à flexão. Infelizmente, eles tinham apenas uma resistência à compressão limitada e não eram amplamente aceitos.
Hoje, as fibras de carbono são uma parte importante de muitos produtos e novas aplicações são desenvolvidas a cada ano. Os Estados Unidos, Japão e Europa Ocidental são os principais produtores de fibras de carbono.
Classificação de fibras de carbono
As fibras de carbono são classificadas pelo módulo de tração da fibra. O módulo de tração é uma medida de quanta força de tração uma fibra de determinado diâmetro pode exercer sem quebrar. A unidade de medida em inglês é libras de força por polegada quadrada de área transversal, ou psi. As fibras de carbono classificadas como "módulo baixo" têm um módulo de tração abaixo de 34,8 milhões de psi (240 milhões de kPa). Outras classificações, em ordem crescente de módulo de tração, incluem "módulo padrão", "módulo intermediário", "módulo alto" e "módulo ultra-alto". As fibras de carbono de módulo ultra-alto têm um módulo de tração de 72,5-145,0 milhões de psi (500 milhões-1,0 bilhão de kPa). Como comparação, o aço tem um módulo de tração de cerca de 29 milhões de psi (200 milhões de kPa). Portanto, a fibra de carbono mais forte é cerca de cinco vezes mais resistente do que o aço.
O termo fibra de grafite refere-se a certas fibras de módulo ultra-alto feitas de piche de petróleo. Essas fibras têm uma estrutura interna que se aproxima muito do alinhamento tridimensional do cristal, característico de uma forma pura de carbono conhecida como grafite.
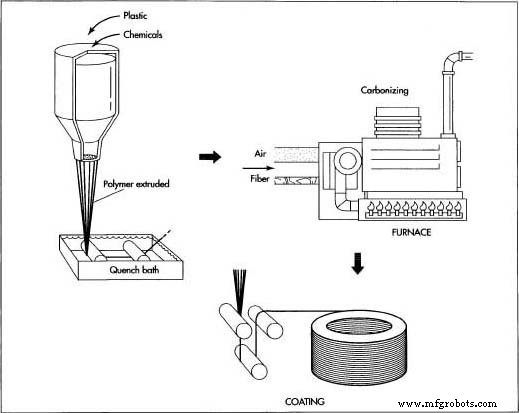
Matérias-primas
A matéria-prima usada para fazer a fibra de carbono é chamada de precursor. Cerca de 90% das fibras de carbono produzidas são feitas de poliacrilonitrila. Os 10% restantes são feitos de rayon ou piche de petróleo. Todos esses materiais são polímeros orgânicos, caracterizados por longas cadeias de moléculas unidas por átomos de carbono. A composição exata de cada precursor varia de uma empresa para outra e geralmente é considerada um segredo comercial.
Durante o processo de fabricação, uma variedade de gases e líquidos são usados. Alguns desses materiais são projetados para reagir com a fibra para obter um efeito específico. Outros materiais são projetados para não reagir ou impedir certas reações com a fibra. Tal como acontece com os precursores, as composições exatas de muitos desses materiais de processo são consideradas segredos comerciais.
O processo de fabricação
O processo de fabricação de fibras de carbono é parte químico e parte mecânico. O precursor é puxado em longos fios ou fibras e então aquecido a uma temperatura muito alta sem permitir que ele entre em contato com o oxigênio. Sem oxigênio, a fibra não pode queimar. Em vez disso, a alta temperatura faz com que os átomos da fibra vibrem violentamente até que a maioria dos átomos que não são de carbono seja expelida. Este processo é chamado de carbonização e deixa uma fibra composta de fibras longas e firmes
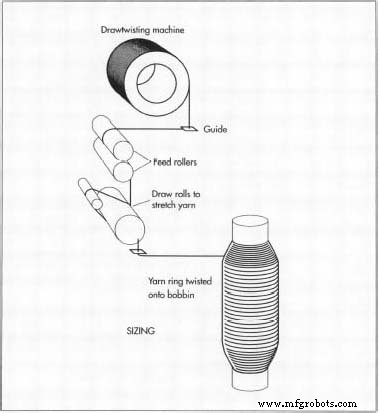
Aqui está uma sequência típica de operações usadas para formar fibras de carbono de poliacrilonitrila.
Spinning
- 1 O pó de plástico de acrilonitrila é misturado com outro plástico, como acrilato de metila ou metacrilato de metila, e é reagido com um catalisador em uma suspensão convencional ou processo de polimerização em solução para formar um plástico de poliacrilonitrila.
- 2 O plástico é então fiado em fibras usando um dos vários métodos diferentes. Em alguns métodos, o plástico é misturado com certos produtos químicos e bombeado por meio de minúsculos jatos para um banho químico ou câmara de resfriamento, onde o plástico coagula e se solidifica em fibras. Isso é semelhante ao processo usado para formar fibras têxteis poliacrílicas. Em outros métodos, a mistura de plástico é aquecida e bombeada por meio de pequenos jatos em uma câmara onde os solventes evaporam, deixando uma fibra sólida. A etapa de fiação é importante porque a estrutura atômica interna da fibra é formada durante este processo.
- 3 As fibras são então lavadas e esticadas até o diâmetro de fibra desejado. O alongamento ajuda a alinhar as moléculas dentro da fibra e fornece a base para a formação dos cristais de carbono fortemente unidos após a carbonização.
Estabilizando
- 4 Antes de as fibras serem carbonizadas, elas precisam ser alteradas quimicamente para converter sua ligação atômica linear em uma ligação em escada termicamente mais estável. Isto é conseguido aquecendo as fibras ao ar a cerca de 390-590 ° F (200-300 ° C) durante 30-120 minutos. Isso faz com que as fibras captem moléculas de oxigênio do ar e reorganizem seu padrão de ligação atômica. As reações químicas de estabilização são complexas e envolvem várias etapas, algumas das quais ocorrem simultaneamente. Eles também geram seu próprio calor, que deve ser controlado para evitar o superaquecimento das fibras. Comercialmente, o processo de estabilização usa uma variedade de equipamentos e técnicas. Em alguns processos, as fibras são puxadas por uma série de câmaras aquecidas. Em outros, as fibras passam por rolos quentes e por camadas de materiais soltos mantidos em suspensão por um fluxo de ar quente. Alguns processos usam ar aquecido misturado com certos gases que aceleram quimicamente a estabilização.
Carbonização
- 5 Uma vez que as fibras estão estabilizadas, elas são aquecidas a uma temperatura de cerca de 1.830-5.500 ° F (1.000-3.000 ° C) por vários minutos em um forno cheio com uma mistura de gás que não contém oxigênio. A falta de oxigênio impede que as fibras queimem em altas temperaturas. A pressão do gás dentro do forno é mantida mais alta do que a pressão do ar externo e os pontos onde as fibras entram e saem do forno são vedados para impedir a entrada de oxigênio. À medida que as fibras são aquecidas, elas começam a perder seus átomos não-carbono, além de alguns átomos de carbono, na forma de vários gases, incluindo vapor d'água, amônia, monóxido de carbono, dióxido de carbono, hidrogênio, nitrogênio e outros. À medida que os átomos que não são de carbono são expelidos, os átomos de carbono restantes formam cristais de carbono fortemente ligados que são alinhados mais ou menos paralelos ao longo eixo da fibra. Em alguns processos, dois fornos operando em duas temperaturas diferentes são usados para controlar melhor a taxa de aquecimento durante a carbonização.
Tratando a superfície
- 6 Após a carbonização, as fibras apresentam uma superfície que não se liga bem aos epóxis e outros materiais usados em materiais compostos. Para dar às fibras melhores propriedades de ligação, sua superfície é ligeiramente oxidada. A adição de átomos de oxigênio à superfície fornece melhores propriedades de ligação química e também desgasta e torna a superfície mais áspera para melhores propriedades de ligação mecânica. A oxidação pode ser obtida pela imersão das fibras em vários gases, como ar, dióxido de carbono ou ozônio; ou em vários líquidos, como hipoclorito de sódio ou ácido nítrico. As fibras também podem ser revestidas eletroliticamente, tornando-as o terminal positivo em um banho preenchido com vários materiais condutores de eletricidade. O processo de tratamento de superfície deve ser controlado cuidadosamente para evitar a formação de pequenos defeitos na superfície, como caroços, que podem causar falha da fibra.
Dimensionamento
- 7 Após o tratamento de superfície, as fibras são revestidas para protegê-las de danos durante o enrolamento ou tecelagem. Este processo é denominado dimensionamento. Os materiais de revestimento são escolhidos para serem compatíveis com o adesivo usado para formar materiais compostos. Os materiais de revestimento típicos incluem epóxi, poliéster, náilon, uretano e outros.
- 8 As fibras revestidas são enroladas em cilindros chamados bobinas. As bobinas são carregadas em uma máquina de fiar e as fibras são torcidas em fios de vários tamanhos.
Controle de qualidade
O tamanho muito pequeno das fibras de carbono não permite a inspeção visual como método de controle de qualidade. Em vez disso, produzir fibras precursoras consistentes e controlar de perto o processo de fabricação usado para transformá-las em fibras de carbono controla a qualidade. Variáveis de processo como tempo, temperatura, fluxo de gás e composição química são monitoradas de perto durante cada estágio da produção.
As fibras de carbono, assim como os materiais compostos acabados, também são submetidos a testes rigorosos. Os testes de fibra comuns incluem densidade, resistência, quantidade de cola e outros. Em 1990, a Associação de Fornecedores de Materiais Compostos Avançados estabeleceu padrões para métodos de teste de fibra de carbono, que agora são usados em toda a indústria.
Preocupações com saúde e segurança
Existem três áreas de preocupação na produção e manuseio de fibras de carbono:inalação de poeira, irritação na pele e o efeito das fibras em equipamentos elétricos.
Durante o processamento, pedaços de fibras de carbono podem se quebrar e circular no ar na forma de uma poeira fina. Estudos de saúde industrial mostraram que, ao contrário de algumas fibras de amianto, as fibras de carbono são muito grandes para serem um perigo para a saúde quando inaladas. Eles podem ser irritantes, no entanto, e as pessoas que trabalham na área devem usar máscaras de proteção.
As fibras de carbono também podem causar irritação na pele, especialmente nas costas das mãos e pulsos. Roupas de proteção ou o uso de cremes de barreira para a pele são recomendados para pessoas em uma área onde há presença de poeira de fibra de carbono. Os materiais de colagem usados para revestir as fibras geralmente contêm produtos químicos que podem causar reações graves na pele, que também requerem proteção.
Além de fortes, as fibras de carbono também são bons condutores de eletricidade. Como resultado, a poeira de fibra de carbono pode causar centelhas e curtos em equipamentos elétricos. Se o equipamento elétrico não puder ser realocado da área onde o pó de carbono está presente, o equipamento é lacrado em um gabinete ou outro gabinete.
O Futuro
O mais recente desenvolvimento em tecnologia de fibra de carbono são minúsculos tubos de carbono chamados nanotubos.
Esses tubos ocos, alguns tão pequenos quanto 0,00004 pol. (0,001 mm) de diâmetro, têm propriedades mecânicas e elétricas exclusivas que podem ser úteis na fabricação de novas fibras de alta resistência, tubos de ensaio submicroscópicos ou possivelmente novos materiais semicondutores para circuitos integrados.
Processo de manufatura
- Carbono M2
- Fibras de carbono:Passado, Presente e Futuro
- 5 produtos de fibra de carbono surpreendentes
- A fibra de carbono pode ser reciclada?
- Benefícios dos calçados de fibra de carbono
- Fibra de carbono em aplicações aeroespaciais
- Fibra de carbono em aplicações automotivas
- Como a fibra de carbono é produzida?
- Folha de fibra de carbono T300
- Folha de fibra de carbono T700