7 projetos complexos obtidos com impressão 3D
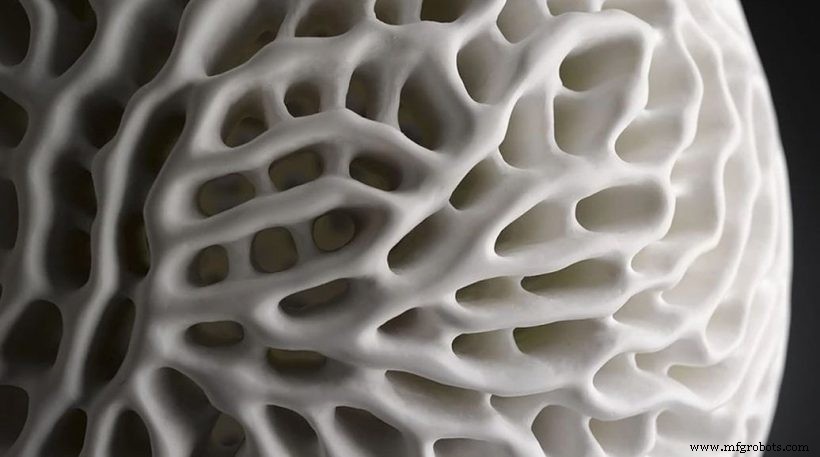
Aproveitando a flexibilidade de design proporcionada pela impressão 3D, os engenheiros podem dar vida às ideias mais desafiadoras. A impressão 3D é uma tecnologia que pode produzir formas e características inatingíveis com os métodos de fabricação convencionais. Para mostrar o poder da tecnologia, exploramos 7 exemplos de designs impressionantes que foram obtidos apenas com a impressão 3D.
1. Pinça de freio de titânio impressa em 3D da Bugatti
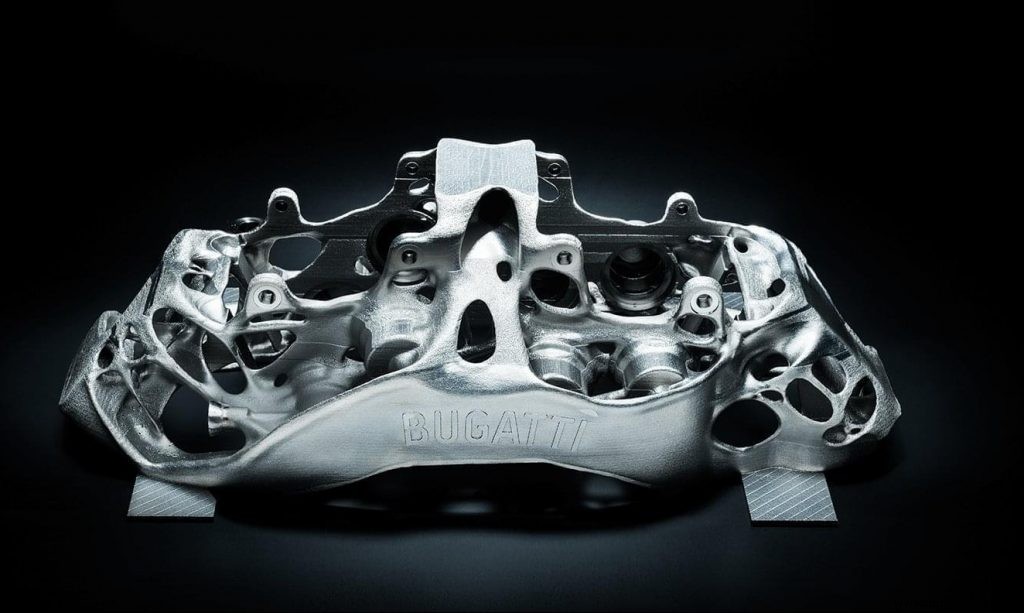
Aplicativo:Automotivo
Benefícios:Leveza, maior resistência
A montadora francesa Bugatti aproveitou a liberdade de design da impressão 3D para seu mais recente supercarro Chiron, produzindo o que se diz ser a pinça de freio mais poderosa do mundo - impressa em 3D em titânio.
Embora a pinça de freio funcione como uma pinça normal, a combinação de impressão 3D e titânio significa que ela é muito mais resistente e cerca de 40% mais leve do que a peça de alumínio atualmente em uso.
Usando um processo de impressão 3D de metal chamado Selective Laser Melting, a equipe da Bugatti foi capaz de experimentar uma variedade de geometrias e espessuras de parede inatingíveis com as técnicas de manufatura tradicionais.
O resultado:uma pinça de freio de formato complexo com espessuras de parede entre 1 mm e 4 mm.
O final de 2018 viu a Bugatti testar com sucesso a pinça em altas cargas, e a empresa agora se prepara para colocar o componente em produção.
No entanto, a Bugatti não é a única empresa a revolucionar o design das pinças de travão. A empresa britânica de tecnologia automotiva Carbon Performance também está usando a impressão 3D para "gerar designs sustentáveis" para peças automotivas impressas em 3D, incluindo pinças.
Para conseguir isso, Carbon Performance está usando sua nova plataforma de software alimentada por IA. A plataforma ajuda a projetar componentes que podem, por exemplo, melhorar a eficiência de combustível de um carro.
Usando seu software de design e impressão 3D, a Carbon Performance é capaz de produzir pinças de freio mais robustas e ecologicamente corretas, graças, em parte, ao seu menor peso. Ser capaz de criar peças de metal leves com impressão 3D significa que menos material é necessário e o processo de produção incorre em menos desperdício de material do que com a manufatura subtrativa. Criar designs leves é um dos principais benefícios da impressão 3D. À medida que a tendência para veículos elétricos e mais eficientes continua a crescer, veremos mais montadoras explorando a impressão 3D em seus esforços para criar componentes de automóveis leves e de melhor desempenho.
2. Suporte de assento de design geral da General Motor
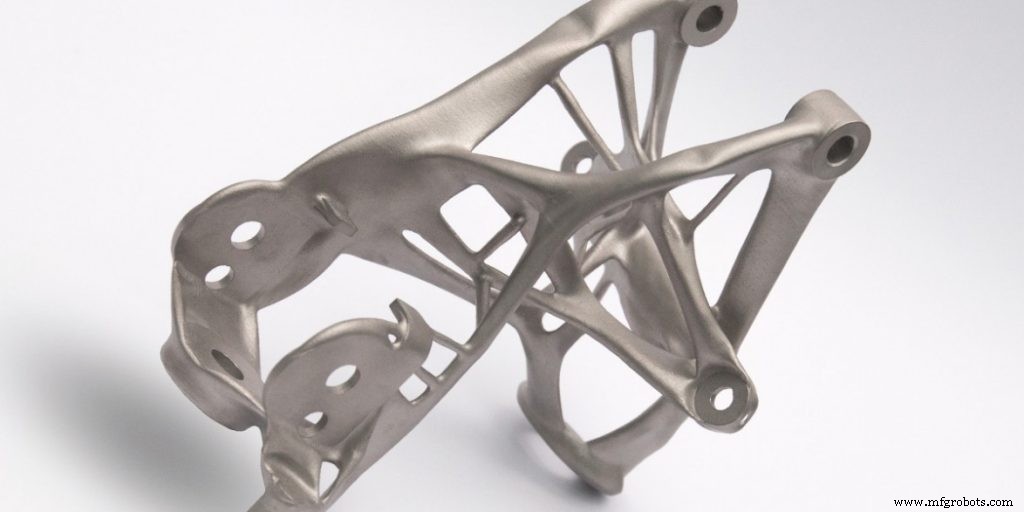
Aplicativo:Automotivo
Benefício:economia de peso significativa
A General Motors (GM) criou recentemente uma versão impressa em 3D de um suporte de assento existente usando ferramentas de design generativas.
O software de design generativo usa algoritmos avançados para gerar design múltiplo automaticamente variantes com base em parâmetros específicos, como peso, material, tamanho, resistência e métodos de fabricação. Os designs subsequentes apresentam formas orgânicas complexas que muitas vezes só podem ganhar vida com a ajuda da impressão 3D.
Este foi exatamente o caso com o suporte de assento da GM. Usando o software de projeto generativo Fusion 360 da Autodesk, 150 iterações de projeto foram produzidas. A GM então selecionou o projeto que oferecia a melhor relação entre peso, desempenho e capacidade de fabricação.
O desenho final quase não se assemelha ao suporte original. Impresso em 3D em metal, o novo suporte do assento é 40% mais leve e 20% mais resistente que o original. Também foi fabricado como um componente, ao contrário da peça original, que deve ser montada a partir de 8 peças separadas. A capacidade da impressão 3D de criar peças complexas mais rapidamente e com mais flexibilidade torna a tecnologia uma escolha natural para a produção do componente redesenhado. O benefício mostrado neste exemplo é a consolidação de peças - a capacidade de imprimir várias peças como um único componente e, assim, reduzir o tempo e os custos de montagem.
Embora o suporte do assento da GM permaneça uma prova de conceito, a empresa vê um enorme potencial na combinação de impressão 3D e software de design generativo. Ambas as tecnologias certamente terão um papel fundamental no futuro da fabricação de veículos, facilitando um design e desenvolvimento de produtos mais rápidos, bem como a produção de peças automotivas complexas.
3. Implante de quadril topologicamente otimizado de Altair
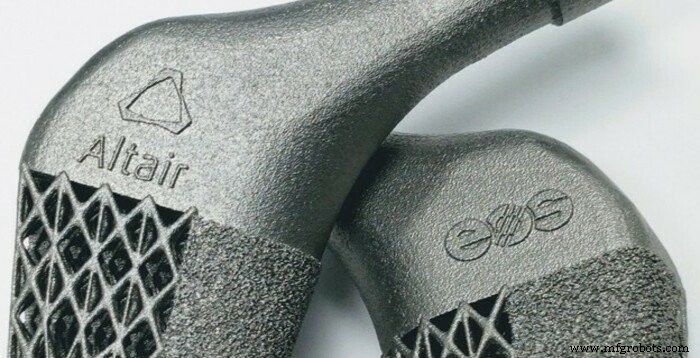
Aplicativo:Médico
Benefício:Otimização de materiais A otimização da topologia é uma técnica de projeto generativa que permite aos projetistas aplicar algoritmos avançados para otimizar a geometria de uma peça. Usando a tecnologia, a distribuição de material de uma peça pode ser otimizada para remover qualquer material desnecessário do design.
Uma empresa que está aproveitando a otimização da topologia é a Altair, que combinou a impressão 3D com a otimização da topologia para criar um implante de haste de quadril aprimorado. A impressão 3D oferece uma série de benefícios para implantes de quadril, incluindo a capacidade de personalizar um implante para as cargas específicas que ele deve suportar. O software de otimização de topologia facilita isso, permitindo que os engenheiros levem em consideração os vários casos de carga que um implante de quadril pode ver durante seu ciclo de vida.
Ao inserir parâmetros como casos de carga e restrições de projeto, o software otimiza a distribuição de material dentro de um volume de material definido. Esse processo resulta em um design que mostra onde o material pode ser removido para criar o implante de quadril de melhor desempenho.
A equipe do Altair usou esta abordagem para determinar as áreas sólidas e semidensas do implante antes de preencher as regiões semidensas com estruturas reticuladas para tornar o implante mais leve.
Comparado a um fêmur intacto ou com um implante pronto para uso, a equipe descobriu que o novo design ajuda a aumentar o limite de resistência para cerca de 10 milhões de ciclos. Isso significa que o implante de quadril pode suportar uma corrida de Los Angeles a Nova York e vice-versa - duas vezes.
O novo design também ajuda a reduzir a proteção contra tensões em 57%. A proteção contra tensões se refere à redução da densidade óssea causada pela colocação de um implante de titânio dentro de um paciente e pode levar a fraturas e luxações. Por esse motivo, projetar um implante o mais próximo possível do tecido ósseo original é a chave para reduzir a proteção contra tensões e eliminar esses efeitos indesejados.
Usar a impressão 3D como tecnologia de fabricação é a única maneira de dar vida a esses designs. Não só torna possíveis formas complexas como treliças, mas também pode produzi-las de forma mais econômica do que os métodos convencionais.
A partir de hoje, os implantes impressos em 3D topologicamente otimizados estão apenas começando a entrar nos casos de uso da vida real. Levará algum tempo para que os reguladores da área de saúde desenvolvam novos métodos de padronização para esses novos designs de implantes. No entanto, olhando para o futuro, é claro que a impressão 3D se tornará uma tecnologia chave para a criação de implantes de quadril de melhor ajuste, mais duradouro e de alto desempenho para um paciente específico.
4. Ponte de pedestres impressa em 3D do MX3D
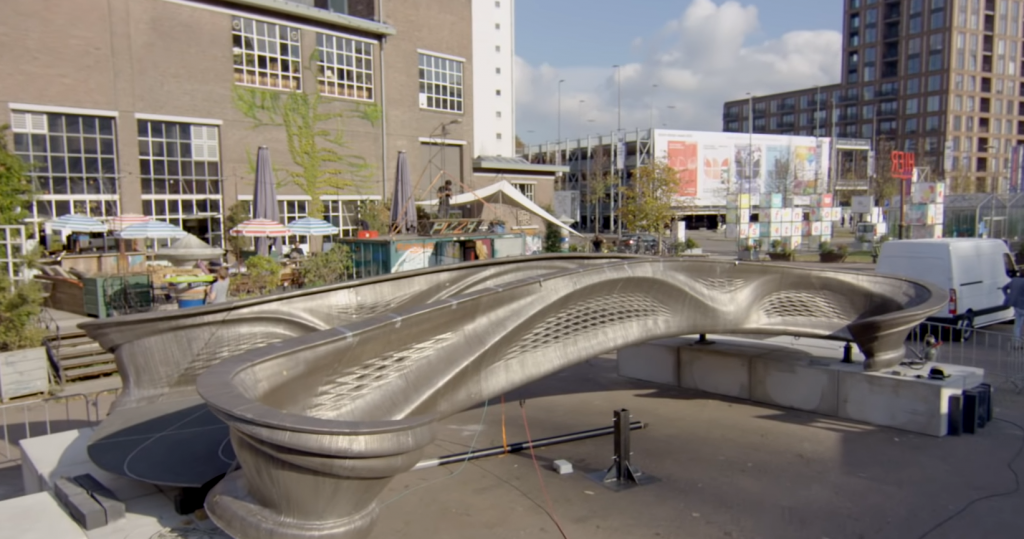
Aplicativo:Construção
Benefício:Design inovador
Revelada na Dutch Design Week em 2018, a ponte pedonal impressa em 3D de aço inoxidável da MX3D é um dos projetos de design mais empolgantes no espaço de impressão 3D.
Ao encaixar máquinas de soldagem em braços robóticos, a equipe do MX3D foi capaz de imprimir em 3D uma ponte de 12 metros de comprimento, obtendo uma aparência e formato únicos. Por exemplo, o desenho da ponte é orgânico e semelhante a um tecido, com muitas curvas e detalhes intrincados. A superfície da ponte foi deixada sem alisamento, deixando visíveis as camadas de aço depositadas que dão à ponte um acabamento áspero e incomum.
Curiosamente, a impressão 3D não foi a única tecnologia de ponta usada para este projeto. Para garantir a segurança e o desempenho otimizado da ponte, a estrutura de aço impressa em 3D é equipada com uma rede de sensores para monitorar o estado da ponte, registrando o número de pessoas que passam por ela e medindo coisas como dispersão de peso e qualidade do ar.
Todo o projeto levou quase quatro anos para ser executado e agora a ponte concluída está programada para ser instalada em Amsterdã ainda este ano.
5. GE Research desenvolve um trocador de calor bioinspirado
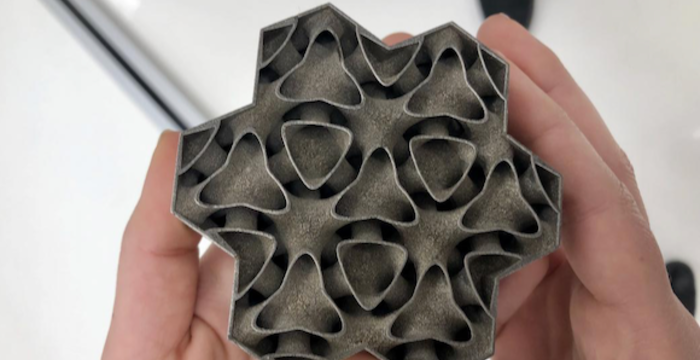
Aplicação:Energia
Benefício:desempenho aprimorado A GE Research está desenvolvendo um trocador de calor ultraeficiente e de baixa emissão para equipamentos de geração de energia, como turbinas a gás. Surpreendentemente, para conseguir isso, a equipe criou um design inovador inspirado nos pulmões humanos.
Os pulmões humanos são um dos trocadores de calor mais eficientes e compactos. O órgão desempenha sua função de troca de calor com uma rede de capilares, que dividem o fluxo de sangue em pequenos fluxos. Esta rede aquece o ar mais frio que inalamos, ao mesmo tempo que regula a temperatura do corpo.
O trocador de calor da GE funciona de maneira semelhante, mas em temperaturas e pressões muito mais altas. O componente possui uma rede trifurcada de canais, que leva o ar quente que sai de uma turbina a gás. Esta rede está entrelaçada com outra rede de canais cheios de fluido de trabalho mais frio correndo na direção oposta. O ar quente e o fluido frio não se misturam, mas sua proximidade permite que o ar quente seja resfriado, melhorando a eficiência térmica de uma turbina a gás.
Crucialmente, a impressão 3D era a única tecnologia capaz de produzir um design tão complexo.
Assim que o processo de desenvolvimento estiver concluído, a GE será capaz de imprimir em 3D um trocador de calor que pode operar de forma econômica a 250 ° C (450 ° F) graus mais alta do que os trocadores de calor atuais. Com uma temperatura operacional significativamente aumentada, o componente impresso em 3D representa uma nova geração de trocadores de calor de alto desempenho.
6. Suporte de teto leve da BMW
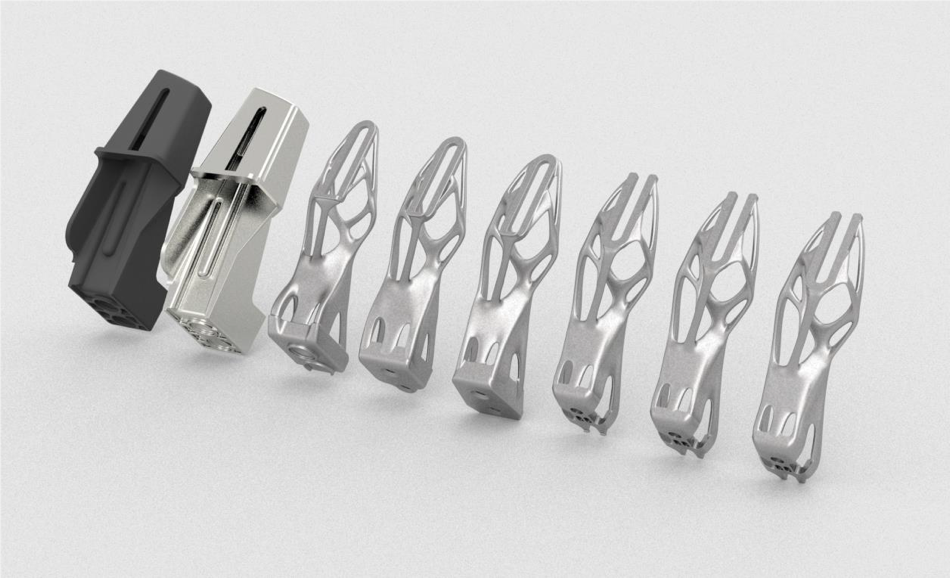
Aplicativo:Automotivo
Benefício:redução de peso
Em 2018, a BMW lançou seu icônico carro i8 Roadster, com um premiado suporte de metal impresso em 3D.
O suporte de teto, um pequeno componente que ajuda a dobrar e desdobrar a parte superior do carro, exigia um novo design para maximizar o desempenho do mecanismo de dobramento do teto. Para atingir esse objetivo, os engenheiros da BMW recorreram a um software de otimização de topologia.
Usando este software, os engenheiros foram capazes de inserir parâmetros como o peso, o tamanho do componente e a carga que ele irá suportar. O software então gerou um projeto que otimizou a distribuição do material da peça.
O projeto realizado pela equipe de engenharia era impossível de lançar. A equipe descobriu que a única maneira de tornar esse design possível era por meio da impressão 3D de metal.
Graças à tecnologia Selective Laser Melting (SLM), os engenheiros criaram um suporte de telhado de metal que é 10 vezes mais rígido e 44% mais leve do que a alternativa convencional.
A peça, que agora é produzida em pequenas séries, apresenta um enorme potencial de leveza para projetos de veículos quando combinada com o poder das técnicas de otimização de topologia.
7. KW Micro Power e VELO3D colaboram para inovar um componente de microturbina
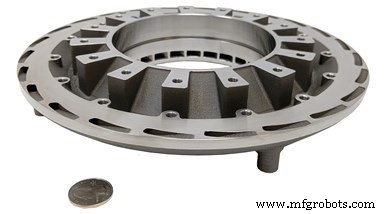
Aplicação:Energia
Benefício:Recursos internos complexos
Por alguns anos, a empresa de engenharia, KW Micro Power, tem trabalhado no projeto de um gerador de microturbina, mas enfrentou desafios ao levar esse projeto para produção. Um dos principais desafios residia na produção de um dos componentes do dispositivo.
O componente em questão é um disco de titânio com canais internos complexos que ajudam a gerenciar os gases de escape de forma mais eficiente. Quando impresso em 3D em metal, este componente requer estruturas de suporte para evitar inclinação ou empenamento durante o processo de impressão.
No entanto, a complexidade das características internas do componente impossibilitou a remoção dos suportes após a produção.
Para superar este desafio, a empresa colaborou com a VELO3D, um fabricante de impressoras 3D que desenvolveu sua tecnologia de impressão 3D em metal, Intelligent Fusion. Essa tecnologia permite que a impressora Sapphire 3D da VELO3D imprima peças com estruturas de suporte mínimas e tensões residuais reduzidas, que muitas vezes são a causa de empenamento.
Isso é conseguido devido a um recobridor patenteado sem contato, que é usado para fornecer uma nova camada de pó a ser derretida e fundida com um laser. Na impressão 3D de metal à base de pó, quando o pó é colocado no topo de outra camada, um revestidor pode desalojar a peça se não for fixada a uma placa de construção.
No sistema de safira do VELO3D, a lâmina de re-revestimento não está em contato com o leito de pó. Uma vez que o pó é depositado, uma lâmina raspadora e um processo de vácuo são aplicados na parte superior do pó para se certificar de que está absolutamente nivelado.
Com um recobridor não em contato com a camada anterior de pó, uma peça não precisa de nenhum suporte para ancorá-la em uma placa de construção de metal. Nesse ínterim, a simulação e um sistema de controle de circuito fechado que alimenta a impressora permitem que recursos internos complexos sejam impressos sem suporte.
Para aproveitar todo o poder da impressora Sapphire 3D, a equipe da VELO3D ajudou a KW Micro Power a melhorar ainda mais o design do componente gerador. A peça acabada é 37% mais leve do que o projeto original e tem um desempenho melhor graças às tensões reduzidas. Mas o mais importante é que o design, que antes era considerado não fabricável, foi possível graças a uma nova geração de tecnologias de impressão 3D em metal.
Trazendo as ideias mais complexas para a vida
A impressão 3D oferece uma tremenda flexibilidade de design, permitindo que designers e engenheiros experimentem novas formas e recursos, incluindo formas otimizadas topologicamente, estruturas reticuladas e designs leves.
Com tantas oportunidades desbloqueadas pela impressão 3D, a tecnologia permite que os fabricantes produzam produtos inovadores com designs otimizados e customizados, o que seria impossível com a manufatura tradicional.
No entanto, para desbloquear esse potencial, é crucial seguir os princípios de design exclusivos da manufatura aditiva. Somente quando armadas com a compreensão sobre as possibilidades e limitações da impressão 3D, as empresas podem usar a tecnologia para realizar suas idéias mais criativas.
impressao 3D
- Uma introdução à impressão 3D com plásticos
- Entrevista com um especialista:Dr. Alvaro Goyanes da FabRx
- Impressão 3D com silicone - está chegando a hora?
- Introdução à impressão 3D em cerâmica
- Um guia para impressão 3D com HP Multi Jet Fusion
- Um breve guia para impressão 3D com jato de pasta
- Impressão do fusível 1 com o fusível 1
- KUHMUTE redesenha mobilidade com impressão 3D SLS
- Impressão 3D de alta velocidade com AION500MK3
- Compósitos para impressão 3D com fibra contínua