A evolução do SLS:novas tecnologias, materiais e aplicações
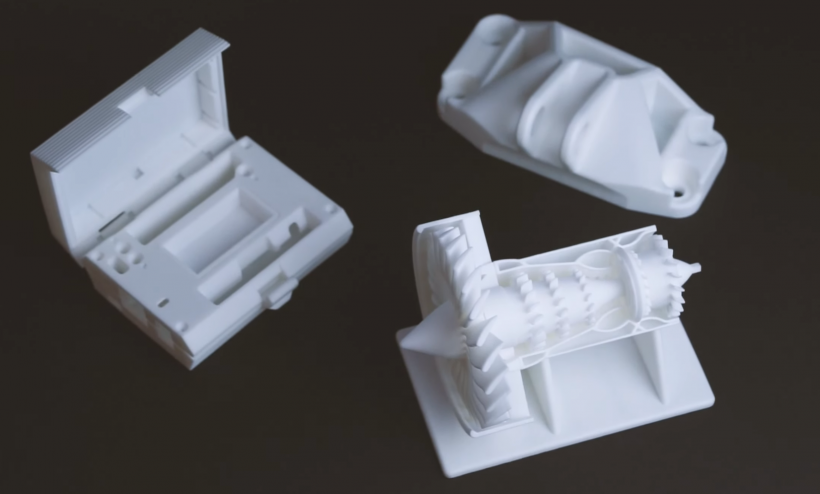
[Crédito da imagem:3D Hubs]
A Sinterização Seletiva a Laser (SLS) é uma das tecnologias de impressão 3D de polímero mais populares para aplicações industriais. Desde o seu surgimento, há mais de 30 anos, o SLS tem amadurecido gradualmente em uma tecnologia capaz de prototipagem funcional e, mais recentemente, também de produção.
Impulsionando esta evolução está a inovação contínua no campo de hardware e materiais, bem como a vontade dos adotantes de tecnologia para desenvolver novas aplicações SLS.
No artigo de hoje, daremos uma olhada nos desenvolvimentos recentes em SLS, para aprender mais sobre as capacidades atuais e oportunidades futuras da tecnologia.
Dê uma olhada em outros artigos que exploram a evolução das tecnologias de impressão 3D:
Impressão 3D de metal:onde estamos hoje?
Estereolitografia e processamento digital de luz:onde estamos hoje?
Como o Desktop está transformando a impressão 3D industrial
Impressão FDM 3D:Onde estamos hoje?
Tudo o que você precisa saber sobre jato de ligantes de metal (2019)
Uma breve história do SLS
A sinterização a laser usa um laser de alta potência para fundir materiais em pó, uma camada de cada vez. Um dos principais benefícios do uso da impressão SLS é que seus designs não precisam de nenhuma estrutura de suporte. À medida que a impressão está sendo construída, todos os espaços vazios são preenchidos automaticamente com o pó não utilizado, tornando as impressões SLS autossustentáveis.
Embora o conceito de impressão SLS tenha sido originalmente concebido no início dos anos 1980, foi somente em 1992 que a primeira impressora industrial SLS foi comercializada - a Sinterstation 2000 da DTM (posteriormente fundida com a 3D Systems). Seguiu-se a EOSINT P350 da EOS em 1994.
Desde então, uma vasta (e crescente) gama de máquinas entrou no mercado, marcando o início da era da impressão mais rápida e em maior escala num ambiente industrial contexto.
Desenvolvimentos notáveis em hardware SLS
A evolução da tecnologia SLS da EOS
A empresa alemã de impressão 3D de polímeros e metais, EOS, é talvez a maior especialista em SLS do mercado. Em 2016, a empresa afirmou ter cerca de 3.000 unidades instaladas em todo o mundo, 51 por cento das quais são sistemas SLS.
Ao longo de sua história de 30 anos, a EOS foi capaz de evoluir SLS para o nível de uma tecnologia madura, adequada para diversas aplicações, tanto em prototipagem quanto em produção.
Um dos marcos dessa jornada foi o lançamento da FORMIGA P 100 em 2006. O sistema estabeleceu padrões de qualidade da impressão 3D industrial no setor de plásticos, muitos anos após sua introdução.
Em 2012, a EOS lançou uma sucessora da FORMIGA 100, a FORMIGA P 110, que foi eleita a melhor máquina de sinterização a laser no levantamento Printer Guide 2018 da 3D Hubs.
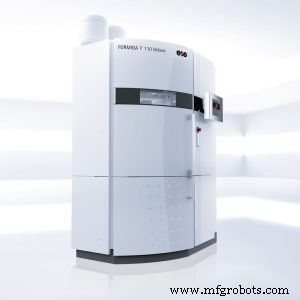
Apresentando um tamanho total de construção de 200 × 250 × 330 mm, a P 110 permitiu uma impressão de baixo volume mais econômica e foi usada para construções de protótipos de tamanho médio e peças com geometrias altamente complexas.
Avançando para 2018, o P 110 foi aprimorado para o FORMIGA 110 Velocis. Ele apresenta um sistema de aquecimento e processo de repintura melhorado e acelerado e usa o controle de software para pré-aquecer os materiais poliméricos com um feixe de laser de 30 watts em uma taxa de velocidade mais alta.
Agora, com melhorias técnicas adicionais e Com algum refino, o Velocis atinge um aumento de até 20 por cento na produtividade e melhor distribuição de temperatura para a área de construção, o que resulta em uma qualidade de peça mais homogênea.
SLS de alta temperatura Embora o material mais comumente usado em SLS continue sendo o náilon, a EOS também queria permitir o processamento de materiais mais avançados, como o PEEK, que normalmente requerem altas temperaturas para serem impressos.
Isso resultou na primeira plataforma SLS de alta temperatura, a EOSINT P 800, lançada em 2008. É capaz de processar polímeros até uma temperatura de cerca de 385 ° C, o que expandiu a tecnologia SLS para um nova gama de termoplásticos, nomeadamente PEEK.
10 anos depois, a EOS adicionou a EOS P 810 à sua gama de impressoras 3D de alta temperatura. O novo sistema é considerado o primeiro sistema de sinterização a laser de alta temperatura do mundo otimizado para um material PEKK reforçado com fibra de carbono.
Inovação contínua:Tecnologias FDR e LaserProFusion
As melhorias e inovações da EOS no campo da tecnologia SLS estão em andamento. Por exemplo, no Formnext deste ano, a EOS apresentou sua tecnologia de impressão 3D baseada em polímero de resolução de detalhes finos (FDR). O novo processo usa um laser CO para imprimir em 3D delicados, mas robustos, componentes de polímero com superfícies de resolução de detalhes finos e uma espessura de parede mínima de 0,22 mm. A EOS afirma ser o primeiro fabricante a desenvolver uma solução de laser CO para impressão 3D industrial em pó. A maioria das máquinas SLS atuais usa um ou alguns lasers de CO₂. O tipo de laser CO cria um feixe de laser ultrafino com um diâmetro de foco supostamente com metade do tamanho das tecnologias SLS atuais. Uma consequência importante dessa precisão adicional são os novos parâmetros de exposição que podem resultar em peças com superfícies extremamente finas.
A nova tecnologia poderia ser usada para unidades de filtro de impressão 3D e canais de fluido, plugues e outros componentes eletrônicos, bem como bens de consumo, como óculos.
Enquanto a tecnologia FDR está focada em componentes delicados, outra - ainda a ser comercializada - solução da EOS, a tecnologia LaserProFusion, é projetada para produtividade máxima.
A EOS vai equipar o sistema LaserProFusion com até 1 milhão de lasers de diodo, capazes de produzir mais de 5 quilowatts de potência laser acumulada. Esta tecnologia visa principalmente atender aos requisitos de produção em série, e a EOS afirma que pode ser usada como alternativa à moldagem por injeção em muitas aplicações.

Desde o lançamento da primeira impressora 3D SLS há 26 anos, a EOS tem sido uma das principais forças motrizes por trás do notável progresso na tecnologia SLS. Ela busca continuamente a visão de SLS como uma solução de produção em série, que está eventualmente se tornando uma realidade.
Tecnologia de voo da Farsoon
Outra empresa que busca revolucionar a tecnologia SLS é a Farsoon. Para tornar o SLS ainda mais rápido e preciso, Farsoon aproveita o poder de um laser de fibra em sua nova tecnologia de voo.
Enquanto as máquinas SLS atuais usam lasers de CO₂, o fabricante chinês de impressoras 3D substituiu o laser de CO₂ padrão com um laser de fibra.
Um sistema de laser de fibra é capaz de fornecer mais potência ao leito de pó e melhorar a distribuição de energia ao material. Isso ocorre porque um feixe de laser de fibra permite um tamanho de ponto de laser menor. Isso se traduz em maior densidade de potência, permitindo que o pó seja sinterizado em menos tempo.
Além de um laser de fibra, a Farsoon também desenvolveu um novo sistema de digitalização, que resulta em uma velocidade de digitalização de mais de 20 m / s. Isso é cerca de 4 vezes maior do que tecnologias comparáveis. Além disso, a potência adicional de um laser torna os detalhes de recursos tão pequenos quanto 0,3 mm possível.
Projetada para ajudar a impulsionar a adoção da impressão 3D SLS para produção de alto volume, a Flight Technology é certamente um passo à frente em nesta direção.
Impressão SLS 3D com dois pós
Enquanto a EOS e outras empresas SLS estabelecidas estão principalmente focadas na inovação linear, a start-up belga, Aerosint, adotou uma abordagem radical para desenvolver um sistema SLS que será capaz de imprimir com dois pós diferentes. Isso permitirá que a máquina use um dos pós como material de suporte barato. Normalmente, o pó de suporte não fundido em uma máquina SLS é o mesmo material usado para imprimir uma peça e tende a ser caro. Claro, isso não seria um problema se o pó pudesse ser 100 por cento reutilizado, o que atualmente é impossível.
Uma das razões é que, no processo SLS, os polímeros são expostos a altas temperaturas durante longos períodos de tempo, sofrendo alterações químicas que tornam suas características de sinterização muito menos previsíveis. Atualmente, a única maneira de superar esse problema é misturando pó 'usado, mas não fundido' com cerca de 50 por cento de pó virgem, a fim de ser reutilizado.
Conforme estimado por um provedor de serviços, fora de 500 kg de pó que compra por mês, '25% se torna uma parte, 25% é desperdício e 50% é reutilizado para atualizar a próxima compilação '.
Apresentando uma máquina que pode usar material de suporte barato e um segundo material para impressão de peças, poderia economizar uma quantia significativa de dinheiro para aqueles que usam processos SLS.
A tecnologia da Aerosint, deposição seletiva de pó, consegue isso depositando seletivamente o material em pó de um tambor rotativo que passa sobre uma área de construção. Um tambor deposita um material, portanto, pelo menos dois tambores são usados para obter a deposição de pó múltiplo.
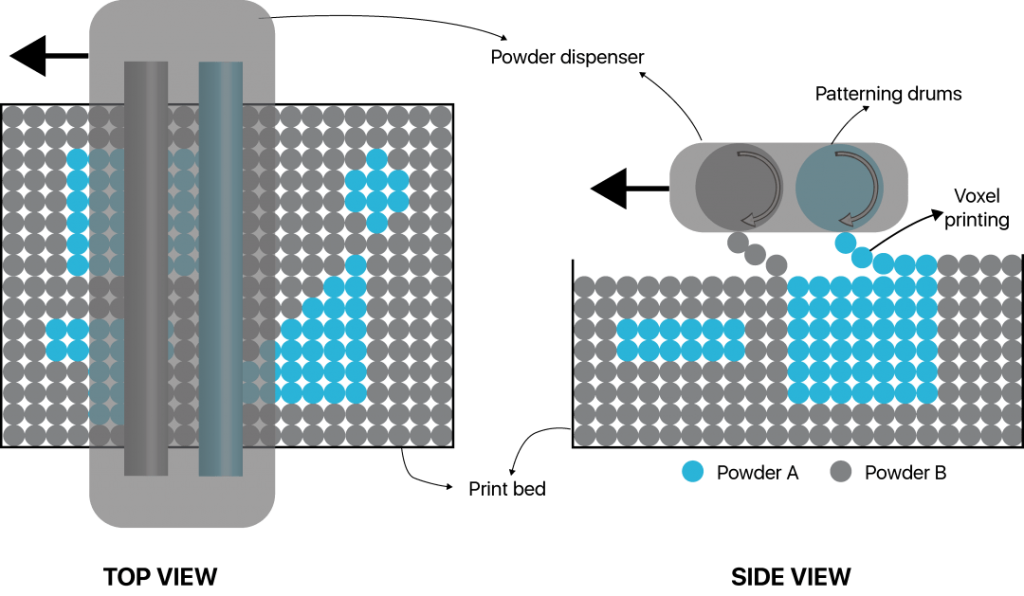
A técnica do Aerosint é inerentemente linha por linha e pode atingir taxas de impressão de até 200 mm / s. Esta velocidade é comparável às velocidades de deslocamento do recobridor SLS de hoje.
O amadurecimento desta tecnologia abrirá um mar de oportunidades para os fabricantes, incluindo os benefícios de redução do desperdício de pó, economia de custos de material e redução do tempo de pós-processamento.
Levando impressoras SLS 3D para um formato compacto
Em 2014, o mercado de SLS viu uma nova safra de empresas aproveitando a expiração da patente SLS original e procurando tornar a tecnologia mais acessível.
Essa mudança deu origem ao SLS de bancada Impressoras 3D, não pequenas o suficiente para serem chamadas de 'desktop', mas compactas o suficiente para caber em uma bancada de trabalho. O surgimento de impressoras 3D de bancada abriu a tecnologia para prossumidores e pequenas empresas que podem não ter dinheiro ou espaço para um sistema SLS industrial.
As start-ups, como Sinterit, Sharebot, Sintratec e, mais recentemente, Formlabs, entrou na corrida pela impressão 3D SLS de formato compacto.
A Sharebot foi a primeira empresa a colocar uma máquina SLS de bancada no mercado com SnowWhite, que começou a ser enviada aos clientes em 2016. Ao contrário dos sistemas Sintratec e Sinterit, que são equipados com lasers de diodo, o SnowWhite apresenta um laser de CO2 mais poderoso, que é comumente instalado em máquinas profissionais de ponta.
O laser e um pequeno volume de construção de 100 x 100 x 100 mm, que permite a impressão com tão pouco pó quanto 300 g , torna o sistema SnowWhite particularmente adequado para aplicações de desenvolvimento de materiais.
Outro grande player neste campo é a empresa polonesa Sinterit, com seu sistema Sinterit Lisa, que continua na vanguarda neste segmento de mercado em crescimento. A partir de € 6.990, Sinterit Lisa apresenta um volume de construção de 150 x 200 x 150 mm e uma resolução de camada mínima de 0,075 mícrons, tornando-o adequado para pequenas empresas que desejam uma introdução à tecnologia SLS sem ter que investir muito capital em equipamentos volumosos.
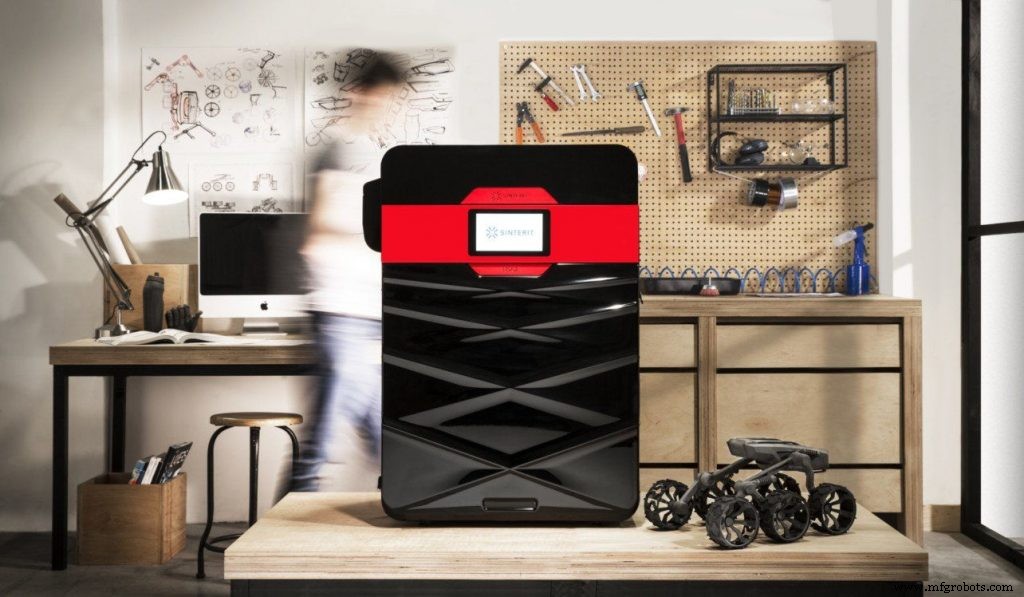
No ano passado, a empresa também apresentou a Sinterit Lisa Pro, a mais recente impressora SLS 3D de bancada.
Uma inovação potencial significativa neste segmento poderia ser a Fuse 1, uma impressora 3D SLS que foi anunciada pelo líder em estereolitografia de mesa, Formlabs, em 2017. Apresentando um volume de impressão de 165 x 165 x 320 mm e um laser de fibra, o sistema custa cerca de US $ 10.000 e está programado para lançamento comercial em meados de 2020.
A enxurrada de impressoras 3D FDM e SLA / DLP para desktops mais baratas no início da década de 2010, causou interrupções na indústria, ao mesmo tempo que contribuiu significativamente para o crescimento da indústria de AM. O SLS acessível está apenas começando essa jornada e pode seguir um caminho semelhante. Isso, em última análise, estenderá o alcance do SLS a uma gama mais ampla de indústrias e usuários.
A evolução dos materiais SLS
As primeiras impressoras SLS 3D usaram mais náilon, um termoplástico de engenharia popular, elogiado por suas propriedades leves, resistência e durabilidade. O náilon, também conhecido como poliamida (PA), é estável contra impactos, produtos químicos, calor, luz ultravioleta, água e sujeira, tornando-o ideal para prototipagem rápida e produção.
Hoje, o náilon ainda permanece o material SLS mais popular. No entanto, o progresso da tecnologia e dos materiais de impressão 3D possibilitou o surgimento de compósitos à base de náilon - materiais misturados com fibra de carbono, fibra de vidro e alumínio para melhorar ainda mais as propriedades mecânicas e térmicas da poliamida. Além do náilon, as impressoras 3D SLS atuais também podem processar PEEK, PEKK, TPUs flexíveis, polímeros retardadores de chama e polímeros antiestáticos. A possibilidade de processar materiais de alto desempenho está intimamente ligada à inovação tecnológica. Como no exemplo EOS, a empresa primeiro precisou criar uma impressora 3D de alta temperatura antes de poder imprimir materiais como PEEK.
Novos materiais SLS
O ritmo de desenvolvimento de novos materiais para SLS também é encorajador.
A empresa italiana de impressão 3D, CRP Technology, é talvez um dos principais desenvolvedores independentes de materiais SLS, famosa por sua marca Windform . A empresa oferece uma linha de compostos à base de náilon e pós de plástico semelhantes a borracha.
As mais recentes adições à linha Windform foram Windform FR1 e Windform FR2 - compostos retardadores de chama, adequados para aplicações em aeronaves (por exemplo, peças internas, componentes de cockpit, dutos de ar e válvulas de saída de ar); peças de transporte (interiores de veículos, conjuntos de carcaças e gabinetes) e bens de consumo e eletrônicos (iluminação e eletrodomésticos).
A empresa química DSM, recentemente, também avançou no desenvolvimento de materiais para SLS. Isso resultou em um pó de polibutileno tereftalato (PBT) lançado no ano passado. Curiosamente, o DSM especifica que o material é na verdade o primeiro pó PBT a ser disponibilizado comercialmente para impressão 3D SLS. PBT é um polímero termoplástico de engenharia com aplicações na indústria eletrônica, graças às suas propriedades isolantes.
Além disso, Forward AM, uma subsidiária de um gigante químico, BASF, oferece uma gama de materiais SLS sob o Ultrasint marca. O material Ultrasint Poliamida PA6 Preto FR resistente a chamas é o mais recente nessa linha e possui alta rigidez e boa estabilidade térmica. De acordo com a Forward AM, ela já está sendo usada para produzir novos componentes para veículos que atendem aos requisitos de proteção contra incêndio em veículos.
Tanto a BASF quanto a DSM adquiriram recentemente as impressoras 3D SLS do fabricante francês Prodways. Com o aumento da capacidade SLS, as duas empresas químicas poderão acelerar o desenvolvimento de materiais avançados para impressão 3D SLS.
Pós-processamento em SLS
Embora a tecnologia SLS elimine a necessidade de design e remoção da estrutura de suporte, tem seus desafios de pós-processamento. A maior delas é a necessidade de remover o excesso de pó que fica na superfície de uma peça e às vezes fica preso dentro de uma peça.
Atualmente, esses desafios são enfrentados por meio de lavagem e limpeza manuais e de técnicas tradicionais, como jateamento e turbilhonamento.
No entanto, esses métodos precisam de muita intervenção manual, aumentando o risco de danificar geometrias frágeis e produzir peças finais inconsistentes.
Quando se trata de acabamento de superfície, as peças SLS são freqüentemente alisadas por lixamento e usando equipamentos semiautomáticos que normalmente não são projetados para impressão 3D. Essas abordagens não são práticas para tirar o máximo proveito dos recursos de uma impressora SLS e escalar para volumes de produção maiores.
Felizmente, vários participantes da indústria estão desenvolvendo soluções automatizadas para pós-processamento de peças SLS.
PostProcess Technologies, por exemplo, oferece soluções pulverizadas por sua tecnologia Thermal Atomized Fusillade (TAF), em que dois jatos perpendiculares de eixo único, compostos de ar comprimido, detergente e sólidos suspensos, fornecem jateamento direcionado sequências, usando rotação de peças de 360 ° para exposição máxima da superfície.
A empresa do Reino Unido, AMT, vai lançar uma solução de depuração automatizada ainda este ano.
Por fim, a mudança da depuração manual para a automatizada ajudará a otimizar o fluxo de trabalho de impressão 3D SLS de uma maneira significativa, não apenas reduzindo o tempo de trabalho manual, mas também permitindo que as empresas escalonem sua produção SLS com mais eficiência.
Aplicativos SLS:um uso crescente na produção
Enquanto a tecnologia SLS continua a ser usada na prototipagem, cada vez mais também está se tornando popular para testes de peças funcionais, bem como aplicações de produção.
Aeroespacial
A indústria aeroespacial, por exemplo, está usando o SLS para criar peças internas das aeronaves. Um exemplo disso é a Emirates, a maior companhia aérea dos Emirados Árabes Unidos. A companhia aérea está usando impressão 3D para produzir componentes de cabine de aeronave, incluindo coberturas de monitoramento de vídeo e grades de ventilação. Estes últimos já foram certificados e instalados para testes a bordo em aeronaves da Emirates.
A Emirates está fazendo parceria com a 3D Systems para produzir as coberturas de monitoramento de vídeo, usando a tecnologia SLS e o material de nylon DuraForm ProX FR1200 da 3D Systems, que atende aos limites de retardamento de chama exigidos pela indústria aeroespacial para peças internas da cabine.
Bens de consumo
Na indústria de bens de consumo, a Chanel é pioneira no uso da impressão 3D SLS para pincéis de rímel. A marca agora está imprimindo em 3D milhões de pincéis de rímel, em colaboração com o provedor francês de serviços de impressão em 3D, Erpro Group.
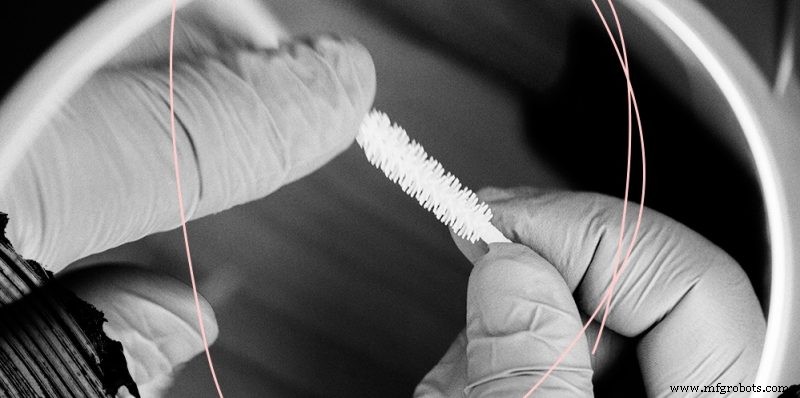
Usando a tecnologia SLS, o design do pincel foi otimizado - por exemplo, a textura áspera e granular, obtida com a tecnologia SLS, melhora a adesão da máscara aos cílios.
Em Além dos produtos de beleza, a SLS é cada vez mais utilizada na área médica e de calçados para a produção de palmilhas e sandálias customizadas.
Motorsports
No automobilismo, a tecnologia pode ajudar as equipes de corrida a inovar os designs dos carros e testá-los mais rápido do que seria permitido pelas tecnologias tradicionais.
A equipe Sauber de Fórmula 1 (F1) da Alfa Romeo é um bom exemplo de como uma empresa de esportes motorizados pode alavancar a impressão 3D SLS. O SLS é usado principalmente para o desenvolvimento aerodinâmico do carro Alfa Romeo F1 no túnel de vento, bem como em uma ampla variedade de moldes de laminação, núcleos e peças de série complexas.
Durante a produção, eles usam um material à base de pó, desenvolvido pela Sauber Engineering, que é usado quando são necessários componentes particularmente leves e rígidos, desde ventilação de freio F1 e componentes de carroceria para veículos de pré-produção e protótipos , a uma ampla gama de elementos de construção prontos para uso.
O céu é o limite para as aplicações SLS. Dados os desenvolvimentos recentes em materiais e tecnologia SLS, esta afirmação soa especialmente verdadeira.
SLS:uma das melhores opções para impressão 3D de polímero
O mercado de impressão SLS 3D está em constante evolução. A tecnologia é democratizada com a introdução de sistemas de bancada compactos e acessíveis. Nesse ínterim, os fabricantes de equipamentos SLS industriais colocam um foco maior em soluções que ajudam a estabelecer o SLS como uma ferramenta de produção.
Como resultado, o volume de projetos, alcançado com a tecnologia SLS, é cada vez maior.
Prova disso é o fato de que mais de 75 por cento dos projetos de impressão 3D usaram métodos SLS em 2019, de acordo com o relatório de Sculpteo. Uma lição aqui é que o SLS é considerado uma das melhores opções para impressão 3D de polímero. Acreditamos que isso continuará a ser verdadeiro no futuro próximo e distante.
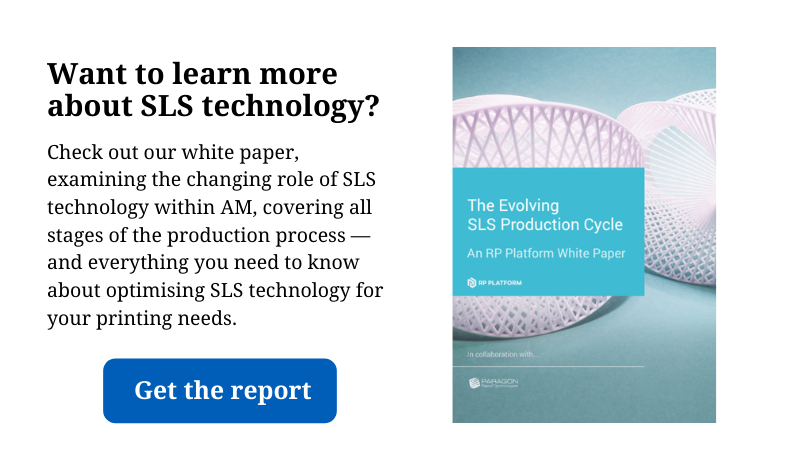
impressao 3D
- 4 Usos de háfnio | As aplicações das ligas de háfnio
- 13 Tipos de materiais refratários e suas aplicações
- A sinergia de IoT celular e Bluetooth LE
- Apresentação de slides do K 2019:Novas resinas, novas aplicações em materiais
- Projetando aplicativos IoT sem fio para as novas redes emergentes - LTE e NB-IoT
- 5G, IoT e os novos desafios da cadeia de suprimentos
- Noções básicas de extrusão de plástico:processo, materiais, aplicações
- A evolução dos materiais médicos
- Fuso de fresagem e as aplicações notáveis
- 9 Tipos de ferramentas de rosqueamento e os aplicativos