O que é Formando? Tipos de processo de formação [Notas e PDF]
A conformação é uma das técnicas de fabricação importantes na engenharia moderna. Quase muitos objetos que estão sendo usados em nossa vida diária são fabricados a partir de métodos ou processos de conformação.
Alguns exemplos são a bola usada em uma caneta esferográfica, válvulas hidráulicas e pneumáticas, recipientes de pasta de dente, recipientes para cozinhar, correntes, pás de ventilador , etc
A conformação de metal é amplamente utilizada em todo o mundo devido às suas vantagens positivas, como custo-benefício, propriedades mecânicas aprimoradas, alta resistência, maior produtividade e economia de material aprimorada.
A conformação encontrou suas aplicações em muitos campos, como as indústrias aeroespacial, automotiva e de defesa.
Um veículo automobilístico típico usa peças como as jantes, a carroceria, o chassi, as válvulas feitas pelo método de conformação.
Neste artigo, estudaremos o que é Conformação e quais são os diferentes tipos de processos de Conformação ? em detalhe. Em seguida, veremos também as vantagens, desvantagens e aplicações .
Formação do histórico do processo
A descoberta de um pingente de cobre no norte do Iraque por volta de 8.700 aC foi estabelecida como a primeira operação de mineração e trabalho industrial de metal conhecida. A mineração de cobre foi documentada nas Américas já em 4000-5000 aC no Lago Michigan.
Os metais tornaram-se cada vez mais significativos para suas civilizações individuais ao longo do tempo, tornando-se essenciais para as operações de construção, e a metalurgia tornou-se um componente importante da sociedade.
A arte de trabalhar com metal agora abrange uma ampla gama de profissões e indústrias.
A conformação e modelagem de metais é uma especialidade para muitas pessoas. Desde os tempos antigos, as técnicas evoluíram significativamente, e as máquinas agora realizam a maior parte da modelagem de metais.
Por exemplo, a laminação é realizada usando equipamentos de laminação de alta qualidade. A laminação é um método de dobrar uma tira contínua de metal em uma determinada forma.
Uma máquina formadora de rolos é composta por uma série de rolos que dobram o metal em um movimento contínuo. Apenas uma pequena porção do metal é dobrada por cada par de rolos, também conhecidos como cordões. O metal é laminado até cumprir os requisitos.
A evolução da metalurgia pode ser vista na arte da fabricação de rolos. O uso de uma máquina formadora de rolos e outros equipamentos formadores de rolos são exemplos de como a indústria metalúrgica progrediu ao longo do tempo.
O que é processo de formação?
A conformação de metal é um processo de fabricação de componentes de formas desejadas pela deformação plástica do material, pela aplicação de força compressiva, força de flexão ou cisalhamento, força de tração ou combinações de todas essas forças juntas, sem adicionar ou remover material.
Tipos de processo de formação
O Processo de Formação foi classificado em dois grupos; Formação a granel e moldagem de chapas metálicas .
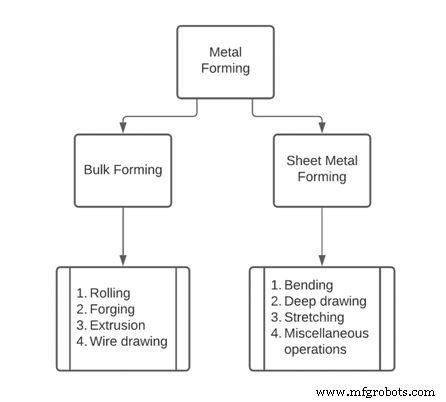
Além disso, a classificação detalhada do processo de conformação como você pode ver no layout acima.
Agora vamos conhecer todos os tipos em detalhes.
#1. Formação em massa
A moldagem em massa é um método de produção de grandes volumes de materiais de produtos cuja área de superfície é menor que a proporção de volume .
Aqui, para realizar a usinagem, são processadas forças de tração, forças de compressão, forças de cisalhamento ou uma combinação de quaisquer duas.
É realizado em máquinas que possuem um conjunto de ferramentas e matrizes. A utilização de uma ferramenta e da própria matriz nos faz entender que a matriz tem a mesma forma da saída a ser produzida e a ferramenta é pressionada contra a matriz para gerar a forma no material.
A conformação em massa envolve processos denominados Laminação, Forjamento, Extrusão e Desenho como seus processos de trabalho.
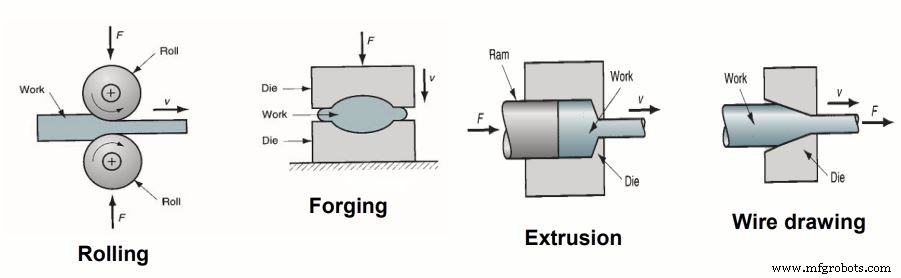
1.1 Em andamento
A laminação é um processo de conformação típico usado para fabricar produtos semi-acabados, como hastes, chapas e chapas, e produtos acabados, como cantoneiras, perfis em U e perfis. O rolamento pode ser feito tanto a quente quanto a frio.
Nesse processo, o tarugo em forma de placa é comprimido entre dois rolos que giram no sentido oposto, reduzindo assim a espessura do tarugo e confeccionando-o em um novo formato. Os rolos giratórios puxam a placa para o espaço e a comprimem. O produto final é o tamanho reduzido do tarugo.
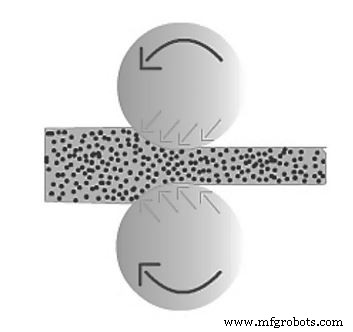
Uma variedade de laminadores evoluiu ao longo do tempo para a produção de artigos de diferentes formatos. Cada um é descrito abaixo.
1.2 Laminador de dois altos
O Laminador de Dois Altos é construído a partir de um suporte separado de três com dois rolos horizontais empilhados um em cima do outro.

Um ou ambos os rolos são ajustáveis neste tipo de moinho. O metal é passado entre dois rolos que giram na mesma velocidade, mas em direções diferentes durante a operação.
1.3 Laminação de três alturas
No caso da Laminação de Três Altos, são três rolos, um em cima do outro. Dois rolos serão usados por vez para uma única passagem. Neste caso, a direção de rolagem não será alterada.
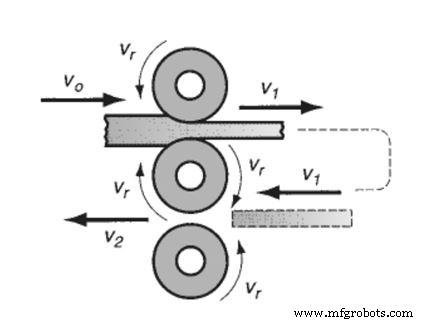
A folha será realocada para os dois rolos inferiores para uma redução adicional, uma vez que os dois rolos superiores tenham sido usados para a primeira redução. Este ciclo é repetido até que a diminuição desejada seja alcançada.
1.4 Laminação de quatro alturas
O Laminador de Quatro Altas consiste em dois rolos pequenos usados para reduzir a espessura e dois rolos de apoio grandes usados para suportar os rolos pequenos.
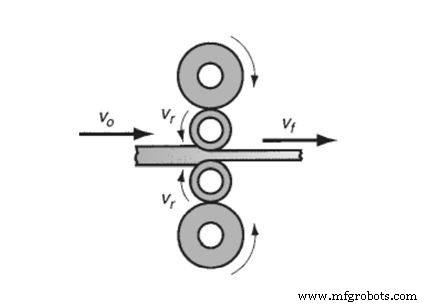
Como a área de contato rolo-folha é reduzida com rolos curtos, a força de rolo necessária é reduzida.
Os rolos de apoio grandes são necessários para diminuir a deflexão elástica dos rolos pequenos quando a folha é passada entre eles.
1,5 fábrica de cluster
Um Cluster Mill é composto por dois rolos operacionais e quatro ou mais rolos de apoio.
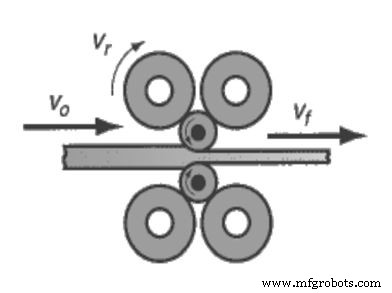
O número de apoios ou rolos de suporte necessários é determinado pela quantidade de suporte necessária para os rolos de trabalho (diâmetro pequeno). Os moinhos de cluster são normalmente empregados em operações de laminação a frio.
1.6 Ring Rolling
A Laminação de Anel é um método de formação que envolve a laminação de um componente de anel de parede espessa de diâmetro menor em um anel de parede fina de diâmetro maior.

À medida que o anel de parede espessa é comprimido, o material deformado se alonga, fazendo com que o diâmetro do anel aumente.
1.7 Forjamento
O forjamento é um método de formação a granel no qual forças de compressão e tração são aplicadas a uma peça de trabalho ou tarugo para fabricá-la em um produto final usando um par de ferramentas chamadas matriz e punção.
Matrizes abertas ou fechadas podem ser usadas para forjamento. Na maioria dos casos, o forjamento em matriz aberta é usado para moldar as matérias-primas em uma forma adequada para posterior conformação ou usinagem.
Neste processo, o tarugo é comprimido entre duas matrizes. As matrizes contêm um contorno moldado que deve ser gerado no produto final. Na compressão do tarugo entre um par de matrizes, a forma é conferida ao tarugo, obtendo-se assim o produto final.
1.7.1 Forjamento em matriz aberta
Para operações como estiramento, desbaste e assim por diante, os Forjados de Matriz Aberta são feitos com um par de matrizes de face plana.
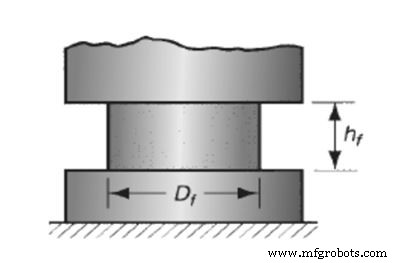
O forjamento em matriz aberta é uma tecnologia vital em uma variedade de indústrias.
Permite a forma bruta e de acabamento de metais, principalmente aço e ligas de aço. É necessária uma matriz com lados abertos que permite que a peça de trabalho se mova livremente de maneira lateral quando atingida. Este design também permite o forjamento de peças muito grandes.
1.7.2 Forjamento em matriz fechada
O forjamento em matriz fechada é realizado comprimindo um tarugo de matéria-prima em uma cavidade produzida entre duas matrizes moldadas.
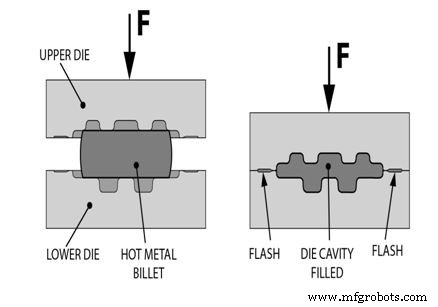
A forma da cavidade da matriz é obtida pela formação de produtos. A moldagem fechada é usada para fazer peças de válvulas, peças de bombas, pequenas engrenagens, bielas, chaves e outros itens.
1.7.3 Cunhando
O processo de cunhagem é a aplicação de tensão compressiva na superfície da matéria-prima para conferir formas únicas do punção de estampagem.
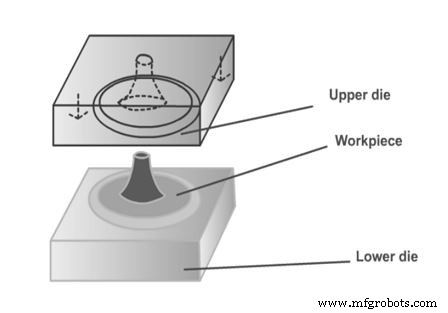
Exemplos são moedas e medalhões de metal impressos.
1.7.4 Forjamento de molde de impressão
No forjamento de molde de impressão, as superfícies do molde têm uma forma que é transmitida à peça de trabalho durante a compressão, restringindo muito o fluxo de metal. O material distorcido adicional fora da impressão do molde é chamado de rebarba. Isso será removido mais tarde.
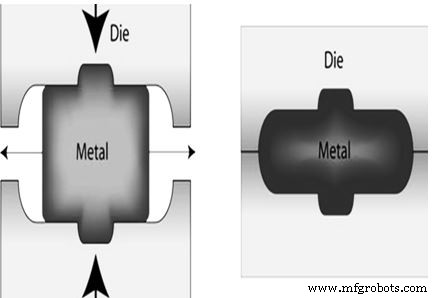
O forjamento de moldes de impressão é incapaz de produzir produtos com tolerâncias apertadas.
Para atingir as precisões exigidas, geralmente é necessária a usinagem.
O processo de forjamento produz a forma fundamental do item, com usinagem adicional nas partes da peça que requerem acabamento de precisão, como furos e roscas.
1.7.5 Forjamento sem flash
Na técnica Flash Less Forging, a peça de trabalho é totalmente limitada dentro da matriz no forjamento sem rebarba, e nenhuma rebarba é produzida. A quantidade de peça de trabalho inicial utilizada deve ser gerenciada com precisão para que corresponda ao volume da cavidade da matriz.
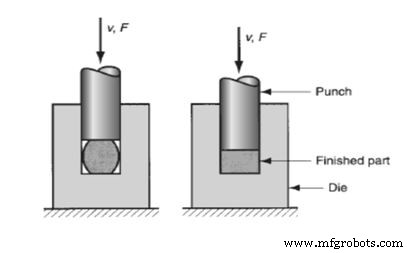
Esta técnica de forjamento sem rebarbas é apropriada para fazer geometrias de peças básicas e simétricas, bem como materiais de trabalho como Al, Mg e suas ligas, devido às demandas.
1.7.6 Forjamento de rolo
Roll Forging é um método de modelagem que é usado para diminuir a seção transversal de uma haste cilíndrica ou retangular, passando-a por um conjunto de rolos opostos com ranhuras correspondentes em relação à forma desejada do item acabado. Embora também combine laminação e forjamento, é categorizado como uma operação de forjamento.
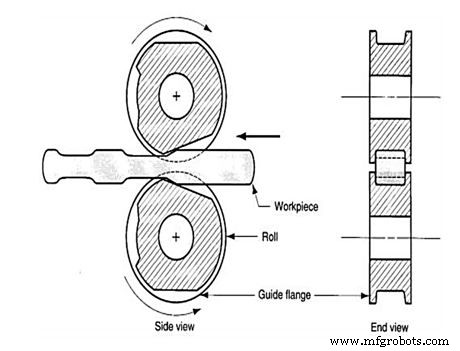
Neste processo, os rolos giram em parte dependendo do grau de deformação. Os produtos forjados a rolo geralmente são mais fortes e possuem a estrutura de grãos necessária em comparação com a usinagem do mesmo item.
1.7.7 Forjamento orbital
No Forjamento Orbital, a forma é transmitida ao material neste método por uma matriz superior em forma de cone que é enrolada de forma síncrona e empurrada para dentro do trabalho. Um molde inferior é usado para suportar o trabalho.
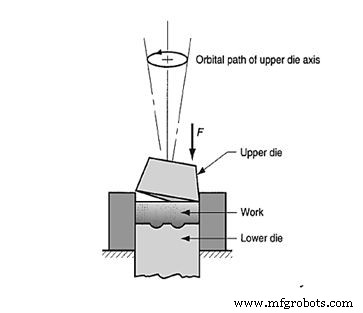
Por causa do eixo inclinado do cone, apenas uma pequena porção da superfície da peça é comprimida em qualquer ponto do processo de conformação.
A região sob compressão circula à medida que a matriz mais alta gira. Há uma redução significativa na demanda de carga da prensa causada pelo contato de deformação parcial em qualquer etapa da conformação.
1.7.8 Forjamento isotérmico
O forjamento isotérmico é uma técnica de forjamento a quente na qual o trabalho é mantido em alta temperatura durante o processo de conformação. As matrizes de forjamento também são mantidas na mesma alta temperatura. Ao eliminar a frieza do trabalho em contato com as superfícies frias da matriz, o metal flui mais facilmente e o esforço necessário é reduzido.
A técnica é mais cara do que o forjamento tradicional e é normalmente usada para metais difíceis de forjar, como Ti, superligas e formas de componentes complicadas. Para evitar a oxidação rápida do material da matriz, a operação é realizada em ambiente de vácuo ou inerte.
1.8 Extrusão
A extrusão é um procedimento de formação a granel que envolve forçar ou comprimir o metal de trabalho através de um orifício de matriz para produzir uma forma de seção transversal desejada.
A extrusão é normalmente distribuída em duas formas de trabalho. Um como extrusão direta ou direta e o outro como extrusão indireta ou inversa.
1.8.1 Extrusão direta ou direta
Na extrusão direta, um tarugo de metal é primeiro carregado no recipiente. O recipiente tem um orifício de molde de contorno moldado. Um aríete é então usado para forçar o tarugo de metal através do orifício da matriz para produzir o artigo.
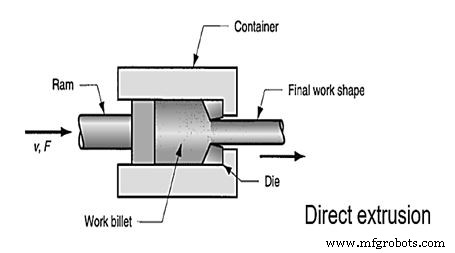
Os produtos extrudados incluem tubos, latas, copos, engrenagens de tamanho pequeno, eixos, etc.
Alguma porção do tarugo sempre permanece no final de cada extrusão e é chamada de topo.
1.8.2 Extrusão indireta ou inversa
Em vez de ser montada no recipiente, a matriz é montada no aríete. O metal flui através do orifício da matriz no lado do aríete na direção oposta ao movimento do aríete conforme é comprimido pelo aríete.
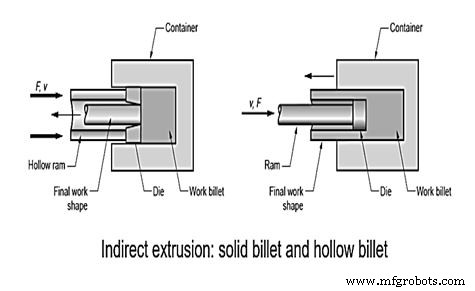
Não há atrito no contato, pois não há movimento relativo entre o tarugo e o recipiente, portanto, a força do aríete é menor do que na extrusão direta.
1.9 Desenho de fios:
O processo de trefilação é usado para fazer fios de pequeno diâmetro a partir de hastes, reduzindo seu diâmetro e alongando seu comprimento com força de tração.
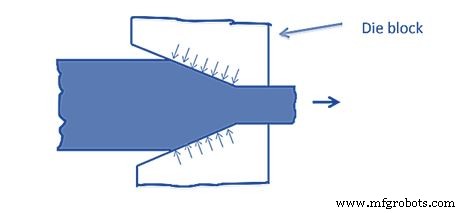
O desenho do fio é usado para fazer cordas musicais. O desenho do tubo pode ser usado para criar tubos sem costura.
Neste processo, uma haste ou barra é puxada através de um orifício de matriz para formar a espessura desejada de fio, reduzindo sua área de seção transversal.
2. Extrusão de impacto
A extrusão por impacto é sempre realizada a frio. A extrusão de impacto para trás permite paredes muito finas. Fabricação de tubos de pasta de dente, por exemplo, ou caixas de bateria.
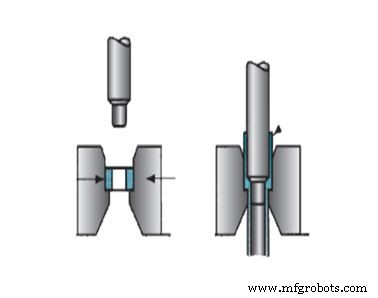
É feito em velocidades mais rápidas e com cursos mais curtos. A pressão de impacto, em vez de exercer pressão, é usada para extrudar o tarugo através da matriz. No entanto, o impacto pode ser realizado por extrusão para frente ou para trás ou uma combinação dos dois.
2.1 Extrusão hidrostática
Na técnica de extrusão hidrostática, o tarugo é cercado por fluido dentro do recipiente durante o processo, e o fluido é pressionado pelo movimento de avanço do aríete. Por causa do fluido, não há atrito dentro do recipiente e o atrito no orifício da matriz é mínimo. Fluidos e métodos especiais devem ser empregados ao trabalhar em altas temperaturas.
A ductilidade de um material aumenta quando há pressão hidrostática sobre ele e não há atrito. Como resultado, esta abordagem pode ser utilizada em metais que são muito frágeis para os procedimentos tradicionais de extrusão.
Este método é usado em metais dúcteis, com grandes taxas de redução concebíveis.
#2. Conformação de chapas metálicas
A conformação de chapas metálicas envolve a aplicação de forças de tração e cisalhamento para fabricar chapas, chapas e tiras em uma forma desejada possível usando um conjunto de ferramentas. O punção e a matriz são usados como ferramentas no processo de fabricação.
A conformação de chapas metálicas está associada às operações; Dobra, desenho, cisalhamento, blanking e puncionamento para produzir os materiais.
O método de formação de chapas usa técnicas de deformação de chapas plásticas como estampagem profunda, corte, dobra, bainha, flangeamento, ondulação, estiramento/estiramento, estampagem.
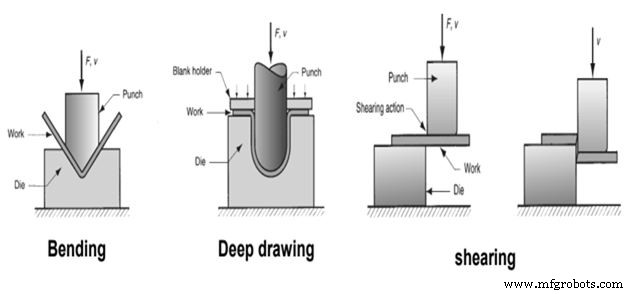
2.1 Desenho profundo:
A estampagem profunda é um processo de chapa metálica no qual a chapa metálica é forçada em um copo de forma oca usando forças de tração e compressão sem alterar sua espessura.
Neste processo, a folha é colocada sobre a abertura da matriz e empurrada para dentro dela com um punção. Um suporte em branco é usado para manter a folha plana na superfície da matriz.
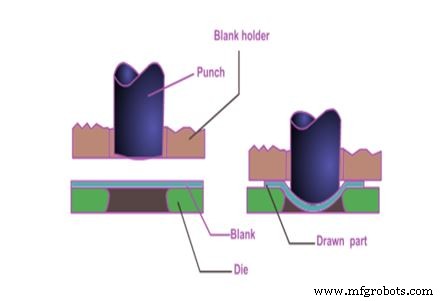
Em muitos casos, a alteração necessária para criar essa peça será substancial (a taxa de trefilação é muito alta). Nesses casos, a conformação completa da peça requer mais de uma etapa de estampagem profunda.
Quaisquer etapas de desenho adicionais necessárias para concluir a operação de desenho são chamadas de Redesenho.
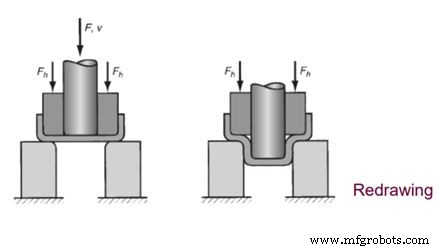
2.2 Dobragem de chapas:
A flexão de chapa é definida como a deformação do metal em torno de um eixo reto. O metal na borda interna do plano neutro é comprimido enquanto o metal nas bordas externas do plano neutro é esticado durante a operação de dobra. A espessura da chapa de metal não muda como resultado da flexão.
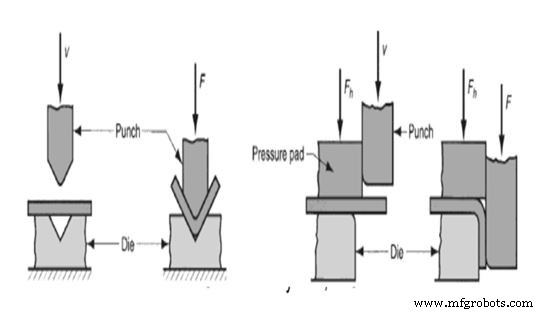
2.3 Alongamento ou formação de alongamento:
A conformação por estiramento é um processo de conformação de chapas metálicas no qual a chapa metálica é intencionalmente esticada e dobrada ao mesmo tempo para alterar sua forma.
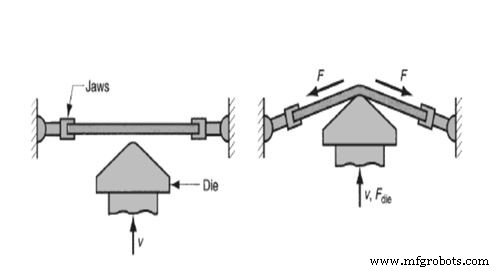
A folha é mantida em ambas as extremidades por garras ou grânulos de estiramento e depois esticada por punção, fazendo com que a folha seja tensionada acima de sua resistência ao escoamento e fabricando-a na forma desejada.
O metal foi plasticamente distorcido quando a tensão é liberada. O impacto combinado de alongamento e flexão faz com que a peça tenha uma mola inferior.
Aula em vídeo sobre o processo de conformação de metais:
Aplicações do processo de conformação de metal:
A técnica de conformação de metal é usada para produzir tubos sem costura, hastes e anéis de turbina. Também é usado para criar fornos de cimento.
Este processo de conformação pode ser usado para criar rolamentos, chapas, chapas de aço e vários componentes para um automóvel.
Este método também é usado para fabricar componentes de mísseis e aeronaves e também para fazer dobradiças, parafusos e pregos.
Vantagens do processo de conformação de metal:
As seguintes vantagens dos processos de conformação são do seguinte modo:
- Artigos com maior resistência.
- Muito menos desperdício de material.
- Um componente menor com alta resistência pode ser fabricado.
- Os artigos produzidos têm dimensões precisas.
- Taxa uniforme de formação.
- Ótimo acabamento de superfície.
- Menos tempo de usinagem em comparação com o método convencional de remoção de metal.
- Propriedades mecânicas melhoradas.
Desvantagens do processo de conformação de metal:
As seguintes desvantagens dos processos de conformação são do seguinte modo:
- O requisito de potência é alto.
- Existe um alto requisito de forças mecânicas.
- O encruamento do material de trabalho é um limite para a quantidade de conformação.
- O material frágil não pode ser fabricado neste processo.
- Há também o uso do processo de tratamento térmico na conformação de metais algumas vezes.
Tecnologia industrial
- O que é a formação de almofada de borracha na usinagem?
- O que é o processo de fabricação de chapas metálicas?
- O que é estampagem? - Tipos, operação e aplicação
- O que é Casting?- Definição| Tipos de Fundição
- O que é Brochar? - Processo, Trabalho e Tipos
- O que é forjamento? - Definição, processo e tipos
- O que é Chapeamento de Metal? - Definição, Tipos e Benefícios
- O que é fundição de metal? - Definição, tipos e processo
- Processo de conformação de chapas metálicas
- Quais são os 4 tipos de processo de fabricação?