O que é Planejamento de Processos | Etapas de Planejamento de Processos, Tipos, Vantagens
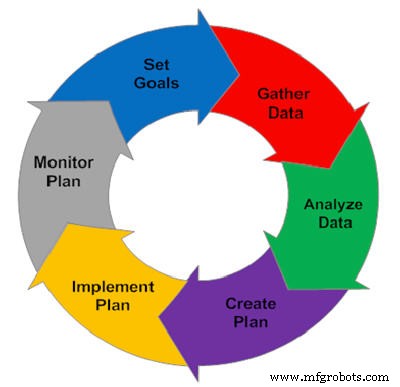
Neste artigo, você aprenderá sobre O que é planejamento de processos ? Quais são os requisitos para este processo, quais são as etapas de planejamento do processo , tipos , vantagens , desvantagens e a sequência de atividades incluídas. Vamos começar com a Definição .
O que é Planejamento de Processo?
Planejamento de processos é o procedimento usado para desenvolver uma lista detalhada das operações de fabricação necessárias para a produção de uma peça ou produto. É a ligação entre o design do produto e a fabricação do produto.
O planejamento do processo estabelece uma sequência eficiente de operações, seleciona equipamentos e ferramentas adequados e especifica suas operações de forma que o produto atenda a todos os requisitos estipulados na especificação. Ao mesmo tempo, o processo será realizado com custo mínimo e produtividade máxima.
Basicamente, existem duas maneiras pelas quais os planos de processo podem ser gerados. Eles são :
1. Planejamento de processo manual e 2. Planejamento de Processos Auxiliados por Computador
REQUISITOS PARA PLANEJAMENTO DE PROCESSO
Um plano de processo razoavelmente bom deve satisfazer os seguintes requisitos:
1. Uma breve descrição do trabalho a ser fabricado que define de forma clara e abrangente sua função de serviço.
2. Especificações e normas que estipulam a função de serviço.
3. Desenhos de trabalho do trabalho com especificação completa.
4. Desenho do branco.
5. Dados sobre a quantidade de peças a serem fabricadas em um período. peças de reposição necessárias para cada unidade.
6. Quantidade total de peças a serem fabricadas em um período.
7. Dados de equipamentos que incluem especificações e dados de capacidade de máquinas-ferramentas e outros equipamentos disponíveis, os dados relativos à disposição e carregamento de equipamentos na oficina.
8. Condições sob as quais a engenharia de produção e a fabricação devem ser organizadas e realizadas, ou seja, se uma planta nova ou existente, equipamentos disponíveis na planta, possibilidade de obter novos equipamentos, etc.
9. Localização da planta.
10. Disponibilidade de mão de obra para o pessoal da fábrica.
11. Data de início do trabalho e data de entrega.
Depois de entender os requisitos básicos, o próximo passo são as diferentes etapas no planejamento do processo .
Processo Etapas de planejamento
O objetivo do planejamento de processo é determinar e descrever o melhor processo necessário para produzir uma peça. Para atingir esses objetivos, as seguintes etapas de planejamento de processos podem ser seguidas:
1. Conhecer a função de serviço da peça.
2. Estudar e analisar criticamente as especificações de fabricação e vários padrões, por exemplo, precisão, saída, eficiência, etc., que definem a função de serviço.
3. Para se familiarizar com a produção anual do produto.
4. Estudar e analisar criticamente os desenhos de trabalho para ver se é viável em todos os aspectos produzir a peça e revelar e corrigir eventuais erros nos desenhos.
5. Determinar quais peças devem ser fabricadas e quais peças devem ser adquiridas com sua identificação completa e quantidade necessária.
6. Preparar uma lista de matérias-primas de qualidade e quantidade adequadas a serem adquiridas de fora, dando sua forma, tamanho e propriedades especiais.
7. Selecionar o processo mais econômico de obtenção dos blanks e determinar as quantidades a serem produzidas para fins de custeio.
8. Determinar o processo mais econômico de fabricação das peças tendo em vista os atuais compromissos de produção, prazo de entrega, quantidade a ser produzida e padrão de qualidade.
9. Determinar a melhor sequência de operação a ser executada em cada peça em um determinado processo.
10. Para selecionar as máquinas-ferramentas que realizarão as operações com as precisões necessárias.
11. Para selecionar quaisquer outros acessórios e equipamentos, como gabaritos, acessórios, matrizes, medidores, etc., que possam ser necessários para fornecer uma taxa de produção mais alta.
12. Para dispor os equipamentos e locais de trabalho, calcule as cargas da máquina e faça as correções necessárias no processo.
13. Revisar o processo para corrigir todos os erros e deficiências que foram descobertos quando o processo foi realizado na produção real.
14. Para determinar os estágios de inspeção, procedimento de inspeção e medidores de limite necessários para diferentes estágios de fabricação para inspecionar com precisão e em um ritmo mais rápido.
15. Determinar o tempo de set-up e o tempo padrão para cada operação e fixar a taxa de pagamentos.
16. Determinar o tipo de mão de obra para a execução bem-sucedida do trabalho.
17. Para determinar o custo estimado do produto para ver se isso vai ou não completar no mercado de vendas.
Vale ressaltar que o planejamento do processo é uma dinâmica para simplificar o processamento levando em conta as mudanças tecnológicas do processo, e os planejadores são obrigados a analisar o processo de produção na manufatura.
Algumas das etapas acima mencionadas no planejamento do processo que requerem explicação adicional são indicadas abaixo com mais detalhes.
Especificações de fabricação: O principal documento no qual as especificações de fabricação são listadas é o desenho de detalhes. O desenho especifica:
1. Dimensões e precisão de usinagem com desvio permitido da forma geométrica adequada.
2. Precisão na coordenação de várias superfícies com desvio permitido.
3. Locais sujeitos a tratamento térmico e tipo de tratamento térmico necessário. 4. Qualidade da superfície.
5. Método de usinagem necessário para obter o acabamento superficial especificado, se necessário.
6. Locais de revestimento protetor com o tipo e espessura deste revestimento. 7. Local de localização para medição de dimensões na peça acabada. 8. Procedimento especial de inspeção, como radiografias, testes hidráulicos, quando necessário.
Por último, as especificações devem ser coordenadas com o processo de usinagem e inspeção ao máximo possível. Se necessário, pequenas alterações ou alterações podem ser feitas para tornar o planejamento bem-sucedido.
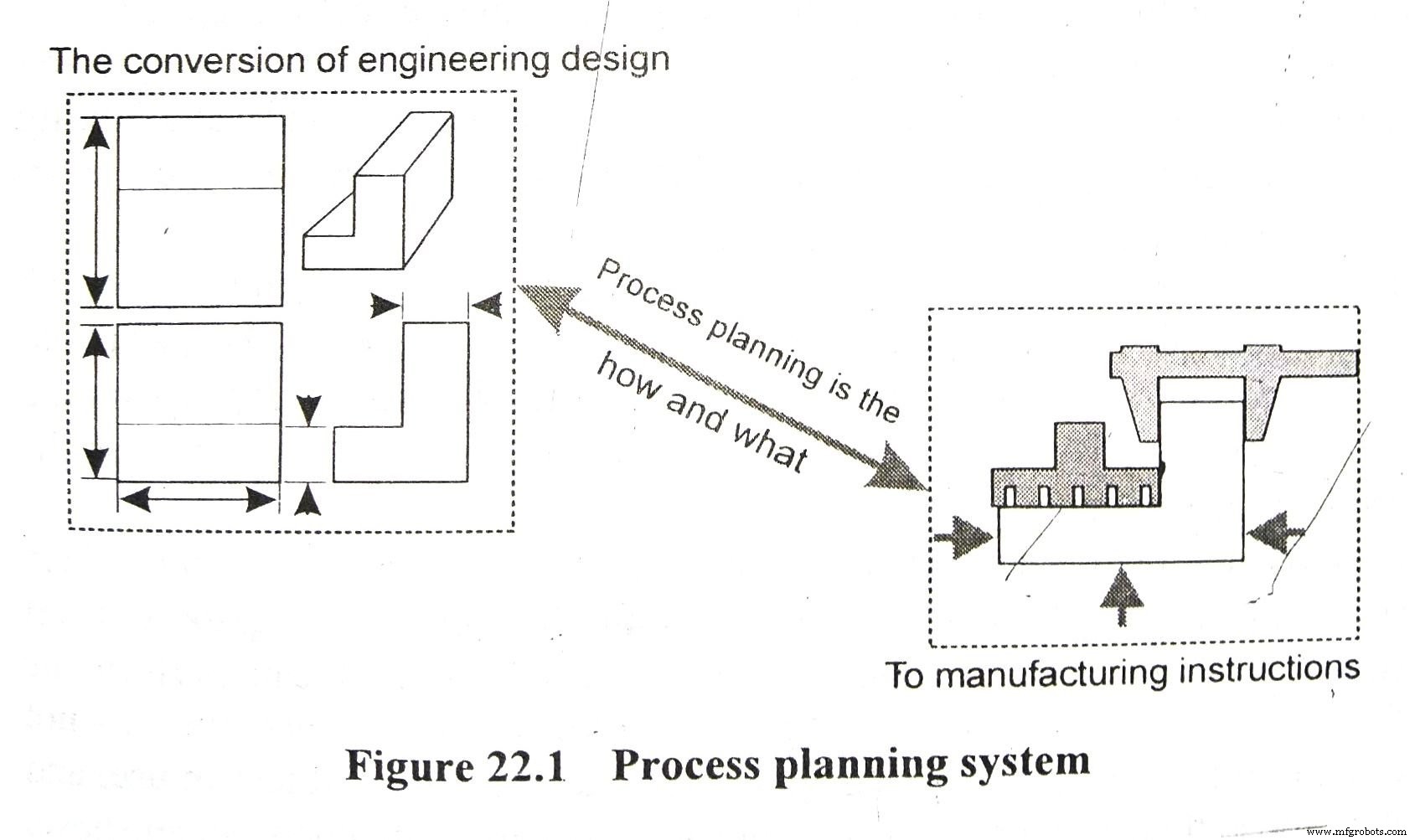
Determinação do espaço em branco: Na verdade, o planejamento do processo começa com a seleção dos espaços em branco. O tamanho do blank e as especificações da peça acabada estão inter-relacionados e determinam o esquema geral das operações de usinagem e acabamento.
A precisão do blank, que depende de seu método de fabricação, e as especificações da peça acabada da máquina determinam o esquema geral do processo de usinagem e suas subdivisões em operações de desbaste, semi-acabamento e acabamento.
Seleção de máquinas-ferramentas : A próxima etapa do planejamento do processo é a seleção de máquinas-ferramenta que é amplamente determinada pela escolha do método ou processo de usinagem de uma peça. Em outras palavras, os princípios que regem os processos de usinagem devem ser a base da seleção das máquinas-ferramenta. Embora seja difícil formular uma regra definitiva para selecionar a máquina-ferramenta para qualquer tipo de usinagem, os seguintes fatores devem ser considerados na seleção de uma máquina-ferramenta para uma determinada operação:
1. Tamanho, forma e material da peça de trabalho.
2. Precisão e acabamento superficial necessários.
3. Saída necessária e capacidade de produção da máquina-ferramenta.
4. Poder da máquina-ferramenta para saber se é suficiente para realizar a operação ou não.
5. Realização da operação para saber se é econômica ou não. 6. Facilidade e comodidade na operação da máquina-ferramenta.
Gráficos de disponibilidade : A tabela de disponibilidade é uma lista de máquinas-ferramenta organizadas de acordo com suas classes (ou seja, lista classificada), por exemplo, tornos de motor, tornos de torre, automáticos e similares, fornecendo sua identificação e número do modelo, localização, estado geral, ferramental disponível, velocidades de corte e avanços, etc. No entanto, no caso de máquinas-ferramentas novas, as velocidades de corte e avanços são obtidos no catálogo disponível com elas. Este gráfico de disponibilidade é necessário na seleção de máquinas-ferramenta para um novo produto em uma planta existente.
Gráficos de carga da máquina mostra qual máquina está ociosa e qual está carregada. Consequentemente, o planejador do processo selecionará a máquina-ferramenta específica que pode ser usada para realizar a operação de usinagem. O planejador de processo não está tão preocupado com o gráfico de carga da máquina quanto o planejador de produção.
Gráficos de capacidade : O gráfico de capacidade pode ser definido como um gráfico que mostra a capacidade de uma máquina-ferramenta de fazer o trabalho. O gráfico de capacidade mostra quanto de sua capacidade nominal uma máquina-ferramenta pode desempenhar sua função satisfatoriamente. Uma máquina-ferramenta, como qualquer outra máquina, não permanece nas mesmas condições em que foi adquirida devido ao desgaste do uso, e perde sua precisão a longo prazo. O gráfico de capacidade que mostra a condição atual da máquina é um guia para o planejador do processo fazer sua escolha das máquinas adequadas.
PLANEJAMENTO DA SEQUÊNCIA DE OPERAÇÕES
Determinar a melhor sequência de operações é uma das etapas importantes no processo de planejamento e na realização de um produto projetado para produção. Tanto o custo do produto quanto a qualidade do produto estão intimamente relacionados à sequência de operação. Uma sequência diferente de operações realizadas resultará em tempos operacionais diferentes, tempos de transporte diferentes para o centro de trabalho, ferramentas diferentes em vista de diferentes superfícies de localização e fixação.
Se uma nova planta for montada para um produto, o planejador do processo tem muito mais liberdade para determinar a seqüência de operação que pode ser mais adequada para o propósito. No caso de uma planta existente, a sequência de operação para um novo produto deve ser determinada com base no equipamento disponível e na condição de carregamento do equipamento. Neste último caso, o planejador do processo deve receber as seguintes informações:
- Lista de máquinas disponíveis.
- Lista de ferramentas de uso geral disponíveis.
- Capacidade do equipamento.
- Gráficos de carga da máquina.
- Dados padrão.
No entanto, em qualquer caso, existem certos princípios fundamentais que devem ser seguidos no planejamento da sequência de operação ideal . Estes são :
1. Primeiro as superfícies de referência devem ser selecionadas com a devida atenção. A seleção de dados influencia todas as operações de usinagem e inspeções subsequentes. Uma superfície que deve permanecer sem usinagem deve ser selecionada como a primeira superfície de referência de configuração somente no caso da primeira operação de usinagem. Nas operações subsequentes, apenas superfícies usinadas podem servir como ponto de referência de configuração.
2. As superfícies cuja usinagem não reduz a rigidez do trabalho de forma apreciável, devem ser usinadas mais cedo na sequência.
3. As operações internas são realizadas antes das operações externas. Essa não é uma regra que precisa ser sempre observada. O principal motivo para realizar operações internas cedo é que as superfícies internas são menos propensas a serem danificadas no manuseio de materiais e processos subsequentes, de modo que suas superfícies frequentemente fornecem um meio melhor de segurar o trabalho e, assim, ajudam a garantir a concentricidade entre os diâmetros interno e externo.
4. A operação na sequência deve começar removendo a maior camada de metal . A remoção de camadas grossas por cortes pesados revelará defeitos internos nas matérias-primas (geralmente peças fundidas ou forjadas) muito mais facilmente do que cortes leves. A peça de trabalho também é aliviada de tensões internas que eliminam o perigo de empenamento em operações subsequentes.
As grandes forças de corte e fixação que podem estar associadas ao corte pesado afetam a precisão das superfícies acabadas de outra parte da mesma peça de trabalho e exigem máquinas destinadas a operações de desbaste. Além disso, cortes pesados envolvendo acabamentos grosseiros ou ásperos são geralmente mais rápidos com trabalhadores menos caros do que acabamentos finos.
5. As operações nas quais se espera um aumento do número de rejeições devido à revelação de defeitos conforme indicado acima, devem ser realizadas o mais próximo possível do início da sequência da máquina. É sempre vantajoso descobrir que o trabalho está sendo executado no material defeituoso o mais rápido possível com o menor investimento em processos secundários.
6. As operações de acabamento devem ser realizadas no final da sequência de operações para reduzir o perigo de danificar as superfícies acabadas, de alterar suas dimensões e coordenação em relação a outras superfícies da peça.
7. Operações de desbaste e acabamento deve ser feito em máquinas separadas para que a precisão das máquinas destinadas ao acabamento não seja perturbada por cargas pesadas em trabalhos de desbaste.
8. Estágios de inspeção deve ser introduzido (a) após o desbaste, (b) antes das operações que serão realizadas em outras lojas e departamentos, (c) antes de uma operação trabalhosa e importante (por exemplo, antes de preparar superfícies de referência) e depois delas, e (d) após a última operação de usinagem.
9. A sequência de operações de usinagem deve ser coordenada com operações de tratamento térmico que são de vital importância na fabricação de peças de máquinas. A deformação do local de trabalho após o tratamento térmico exigirá um aumento nas tolerâncias de usinagem para operações subsequentes para correção necessária na forma geométrica da peça por usinagem.
10. A movimentação de materiais é uma necessidade de qualquer atividade produtiva, pois se aplica à movimentação de matérias-primas, peças em processo, produtos acabados, materiais de embalagem e descarte de sucatas. Assim, sequência de operações e manuseio de materiais estão intimamente ligados. Esta é uma área lucrativa para possível redução de custos e leva uma grande fatia do custo de fabricação. Portanto, a tendência moderna é mecanizar o sistema de manuseio sempre que possível.
11. A espera de materiais nas lojas, bem como em processo, deve ser evitada na medida do possível, pois envolve diferentes parâmetros de custo associados a eles. Na medida do possível, eles estão localizados adjacentes ao ponto de uso por custo mínimo envolvido .
A sequência de operação não é rígida. Varia de produto para produto e até mesmo no mesmo produto. Há sempre algum espaço para melhoria e deve ser continuamente revisto para desenvolver melhores métodos, aumentar a produtividade e reduzir custos.
Processo Planilha de planejamento
A folha de planejamento do processo é um registro detalhado onde todas as informações relacionadas às diferentes operações necessárias para fabricar uma peça são listadas em forma de tabela. Isso também é conhecido como folha de análise , folha de instruções , folha de operação ou folha de design de processo . Um exemplo de uma folha de processo é dado na Tabela 22.1.
A descrição das operações e seus elementos indicados na ficha de processo deve fornecer informações extremamente concisas, mas abrangentes, sobre o que deve ser feito e por quê. Os dados devem indicar claramente como e com o que o trabalho deve ser feito e, se possível, o dispêndio de tempo que isso exigirá.
A forma de tais folhas pode variar para diferentes condições de produção. O caráter de uma folha de processo dependerá principalmente da escala de produção e do grau de importância do produto que está sendo fabricado. Além disso, diferentes tipos de chapas são usados em conceitos de fabricação que já estão em operação e em organizações que projetam novas plantas.
Na maioria dos casos, no entanto, as seguintes informações são listadas nas folhas de processo:
1. Informações sobre a peça de trabalho que incluem nome, desenho e função de serviço, se possível.
2. Informações sobre a peça em branco que inclui material, tamanho do estoque quando usado como peça em branco, caractere etc.
3. Descrições e números das operações e dos seus elementos.
4. Informações relativas aos equipamentos de fabricação, como acessórios de máquinas, ferramentas, equipamentos auxiliares, etc.
5. Dados sobre gabaritos, acessórios e ferramentas, como descrição, tamanhos ou números de código.
6. Elementos de tempo padrão como tempo de ajuste, tempo de manuseio e tempo de usinagem, etc.
7. Classificação do trabalho do trabalhador para cada operação.
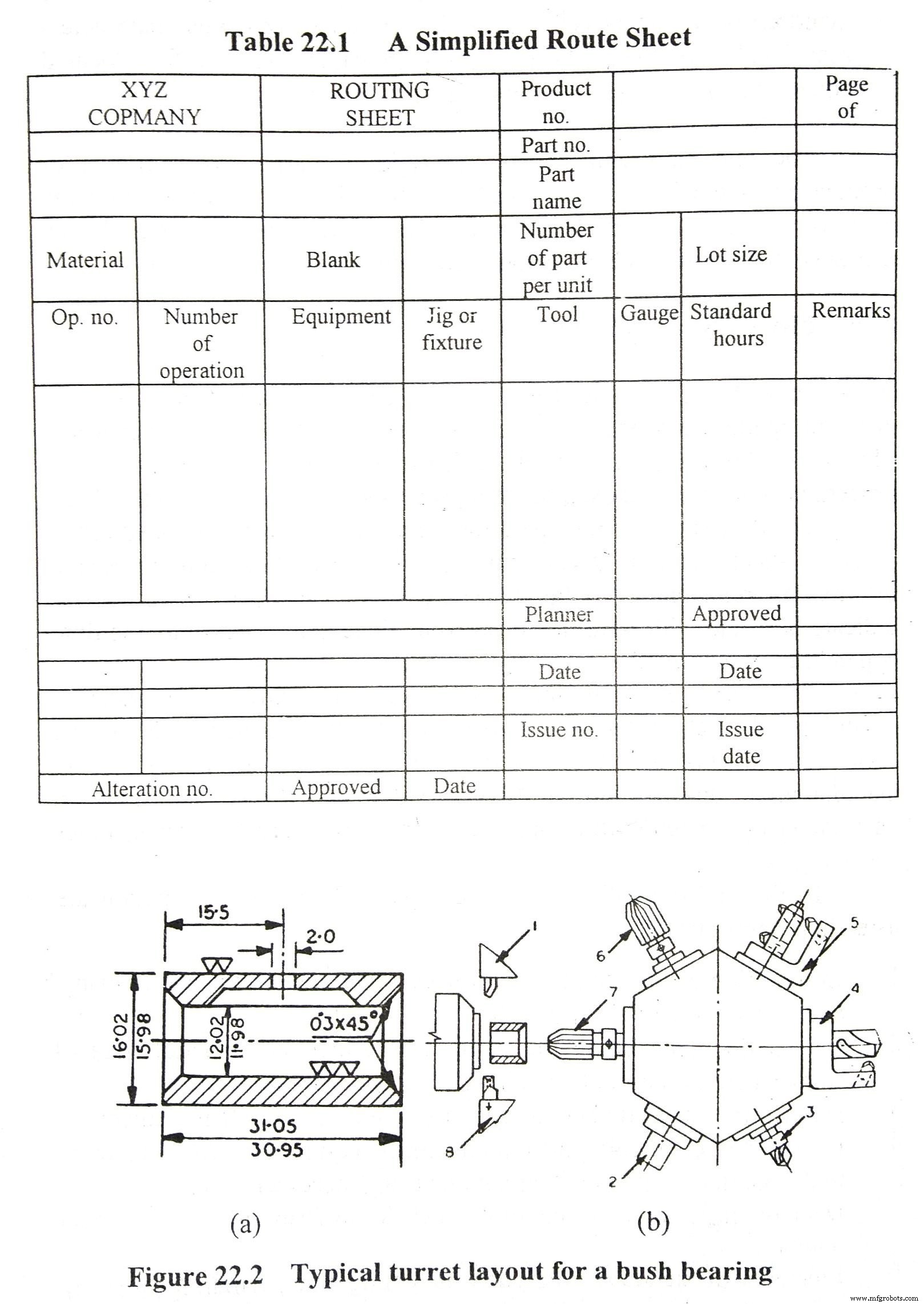
No planejamento de processos de fabricação para operações de usinagem, frequentemente são desenhados esboços de operação para várias operações, conforme mostrado na fig. 22.2. As superfícies que serão usinadas dando a tolerância desejada.
Um Exemplo de Sequência de Operação
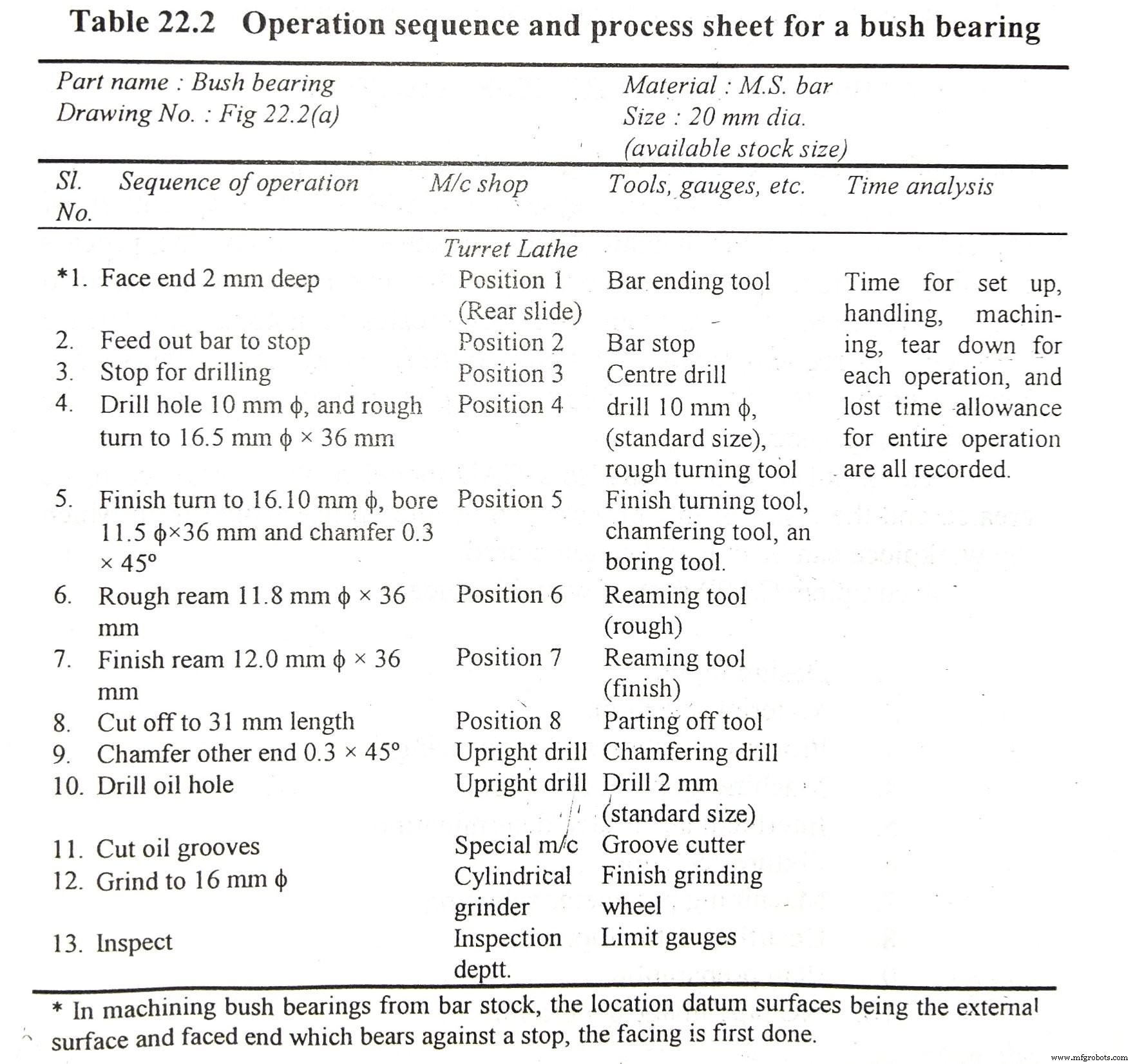
Desvantagens do Planejamento de Processo Manual
O planejamento manual de processos (MPP) tem muitas desvantagens. Eles são :
- MPPs são amplamente subjetivos.
- A qualidade do plano de processo está diretamente relacionada à habilidade e experiência do planejador.
- A incorporação de mudanças de processo é extremamente difícil.
- Mudanças tecnológicas ou mudanças nos tamanhos dos lotes requerem a mudança no plano de processo. Os MPPs demoram a responder.
- É difícil verificar se o plano de processo é consistente e otimizado. Quando não estiver otimizado, especificará a necessidade excessiva de ferramentas e materiais.
- É cansativo pesquisar manualmente os planos de processo de peças semelhantes entre a grande quantidade de documentação da empresa.
Planejamento de Processo Auxiliado por Computador
Planejamento de processo auxiliado por computador (CAPP) tornou-se o elo mais crítico para sistemas CAD/CAM integrados. CAPP é a aplicação de computadores para auxiliar o planejador de processo humano a executar a função de planejamento de processo. O CAPP também não reduz o tempo e o esforço necessários para preparar planos de processo consistentes, mas apenas cria uma interface automatizada entre o Projeto Auxiliado por Computador (CAD) e Manufatura Auxiliada por Computador (CAM) para alcançar a integração completa dentro do sistema de fabricação.
A entrada deste processo é um modelo CAD da peça de trabalho a ser criada e o resultado deste processo é um plano de processo detalhado a partir do qual a peça de trabalho pode ser criada/fabricada.
Um sistema CAPP completo incluiria:
1. Entrada de projeto.
2. Seleção de materiais.
3. Seleção e sequenciamento de processos.
4. Seleção de máquinas e ferramentas.
5. Determinação de superfície intermediária.
6. Seleção de acessórios,
7. Seleção de parâmetros de usinagem.
8. Estimativa de custo/tempo.
9. Preparação do plano.
10. Geração de imagem de fita NC.
Duas abordagens básicas para o planejamento automatizado de processos são:
1. Variante e 2. Gerativo
1 . Método de variante
Método de variante: O planejamento de processo variante explora as semelhanças entre os componentes (peças) e pesquisa em um banco de dados para recuperar o plano de processo padrão para a família de peças à qual o componente pertence. O plano é recuperado e modificado para criar um plano adequado para a nova peça.
Na abordagem variante, o plano de processo é gerado em duas etapas operacionais. Eles são :
1. Fase preparatória e 2. Fase de produção.
Preparatório Palco
Na estágio preparatório os componentes existentes são codificados, classificados e agrupados em famílias de peças. A classificação e a codificação oferecem uma maneira relativamente fácil de identificar a semelhança entre as peças. A partir daí, as famílias de peças podem ser formadas agrupando peças semelhantes.
Vários esquemas de codificação são estabelecidos. MICLASS, DCLASS, OPITZ, CODE são alguns dos esquemas de classificação. Depois que as famílias de peças são formadas, cada família recebe um plano padrão. Um plano padrão consiste em um conjunto de processos de usinagem, que representa o conjunto comum de processos para fazer as peças.
Produção Palco
Na fase de produção o componente de entrada é codificado com base em sua característica geométrica ou nos requisitos de processamento. O mesmo esquema de codificação usado na etapa preparatória também é utilizado aqui. O código resultante é usado como base na qual a peça é atribuída a uma família de peças.
Se o sistema de codificação for utilizado de forma eficiente, a peça deve ser semelhante às outras peças pertencentes à sua família. Um plano de processo para a nova peça pode ser obtido modificando o plano padrão (da família de peças à qual a nova peça pertence) recuperado da base de dados.
2 . Método Gerador
Método Gerador: O Generative Computer Aided Process Planning (GCAPP) sintetiza as informações de fabricação para criar um plano de processo para um novo componente (peça). Lógicas de decisão e métodos de otimização são codificados no próprio sistema, resultando em mínima ou nenhuma interação humana no planejamento do processo.
Um sistema generativo produz um plano de processo completo a partir do desenho de engenharia ou de um arquivo CAD.
As três áreas de um sistema GCAPP são:
1. Definição de componentes em termos de arquivo CAD. Ele contém recursos de peças e especificações de peças.
2. Identificação, captura e representação do conhecimento do planejador do processo. Isso leva em consideração o raciocínio das decisões tomadas pelo planejador de processos sobre seleção de processos, sequenciamento etc.
3. Compatibilidade da lógica do planejador
No GCAPP, as especificações do projeto são inseridas no sistema. A lógica de decisão reconhece o material de estoque e os recursos de usinagem da peça. Além disso, determina sequências ideais de operações juntamente com os tipos e locais de fixação ideais.
Desvantagens do planejamento generativo de processos auxiliado por computador
As seguintes desvantagens são observadas nos sistemas GCAPP.
1. Uso limitado até o momento. As informações necessárias (como tolerâncias) geralmente não estão disponíveis no modelo CAD.
2. Muito conhecimento deve ser adicionado ao sistema para torná-lo capaz de lidar com todos os diferentes tipos de peças que são alimentadas.
3. Devido ao grande grau de complexidade dos algoritmos e ao enorme esforço de cálculo, alguns sistemas se especializam no desenvolvimento de planos para tipos específicos de geometrias. Alguns sistemas chegam a verificar a fabricação de uma peça e sugerir alterações no projeto, se necessário.
Até agora você aprendeu sobre as etapas do planejamento de processos, definição, tipos, sequências de atividades, vantagens e desvantagens de diferentes tipos de planejamento de processos. Por favor, compartilhe este artigo com seus amigos e dê sua opinião nos comentários abaixo.
Tecnologia industrial
- O que são técnicas de teste:tipos, vantagens e desvantagens
- O que é uma máquina virtual - Tipos e vantagens
- O que é design de sistema incorporado:etapas no processo de design
- O que é Brochar? - Processo, Trabalho e Tipos
- O que é forjamento? - Definição, processo e tipos
- O que é cementação? - Definição, tipos e processo
- O que é fundição de metal? - Definição, tipos e processo
- Quais são as principais etapas do processo de usinagem?
- Quais são os 4 tipos de processo de fabricação?
- Quais são as etapas envolvidas no processo de montagem de PCB?