Forjamento de aços carbono e ligas
Forjamento de aços carbono e ligas
O forjamento de aços carbono (C) e ligas constitui um processo de trabalho do metal, que tem a capacidade de formar o material na forma desejada do componente, enquanto refina a estrutura fundida do material de forjamento, cura os vazios de contração e melhora as propriedades mecânicas do material forjado. material. A quantidade de usinagem subsequente também é reduzida, embora isso dependa da geometria da peça acabada e dos processos de forjamento usados.
Os lingotes fundidos têm sido o ponto de partida tradicional para forjamentos, seja forjado diretamente do lingote, ou a partir de uma flor ou tarugo que foi trabalhado a quente a partir de um lingote. Com o amplo uso do aço de fundição contínua, o produto de fundição contínua agora é normalmente usado como estoque inicial. Além de lingotes fundidos, blocos e tarugos laminados e fundidos, outros materiais de partida para forjados são chapas, barras e vergalhões e fundidos de aço.
O forjamento de ferro e aço começou com o início da Idade do Ferro. Naquela época, o trabalho a quente por martelamento fazia parte do processo de produção de ferro forjado e de produtos em ferro forjado e aço. Os fornos de fundição de petróleo bruto usando minério de ferro de alta qualidade, carvão e fundentes produziam pequenas quantidades de ferro que precisavam ser soldadas manualmente para produzir estoque útil. Inicialmente, esse era o principal objetivo do forjamento na época. É geralmente reconhecido que o início da revolução industrial começou a sério no forjamento dos aços. Apesar (ou talvez por causa) dessa longa história, o forjamento de aços é um processo intuitivo e empírico.
Os forjados são normalmente classificados de várias maneiras, começando com as classificações gerais de forjamento em matriz aberta e forjamento em matriz fechada. Eles também são classificados em termos de fator próximo ao acabamento, ou a quantidade de estoque (cobertura) que deve ser removido do forjamento por usinagem para satisfazer os requisitos dimensionais e de detalhes da peça acabada. Finalmente, os forjados são ainda classificados em termos do equipamento de forjamento necessário para sua fabricação, como forjados por martelo, forjados laminados em anel e forjados de prensa múltipla. Das várias classificações, aquelas baseadas no fator próximo ao acabamento estão mais relacionadas às propriedades inerentes ao forjamento, como resistência e resistência à corrosão sob tensão. Em geral, o tipo de forjamento que requer menos usinagem para satisfazer os requisitos da peça acabada tem as melhores propriedades.
De acordo com a especificação ASTM A 788, o forjamento de aço é o produto de uma operação plástica substancialmente compressiva que consolida o material e produz a forma desejada. O trabalho plástico pode ser realizado por um martelo, máquina de forjamento por prensa ou máquina de laminação de anéis e deve deformar o material para produzir uma estrutura essencialmente forjada. As operações de laminação a quente podem ser usadas para produzir blocos ou tarugos para reforjamento. Os forjados podem ser subdivididos nas três classes seguintes com base em suas temperaturas de forjamento.
- Forjados trabalhados a quente – Forjados produzidos trabalhando em temperaturas acima da temperatura de recristalização do material.
- Forjados trabalhados a quente a frio – Os forjados trabalharam em temperaturas elevadas ligeiramente abaixo da temperatura de recristalização para aumentar a resistência mecânica. Os forjados trabalhados a frio podem ser feitos de material previamente trabalhado a quente por forjamento ou laminação. Um forjamento trabalhado a quente a frio pode ser feito em uma operação contínua em que o material é primeiro trabalhado a quente e depois trabalhado a frio por controle da temperatura de acabamento. Devido às diferenças na fabricação de barras laminadas a quente ou de barras acabadas a quente e a frio (semi-acabadas ou acabadas), os tarugos ou blocos não são considerados forjados.
- Forjados trabalhados a frio – Forjados produzidos por plástico trabalhando bem abaixo da faixa de temperatura na qual ocorre a recristalização do material. Os forjados trabalhados a frio devem ser feitos de material previamente trabalhado a quente por forjamento ou laminação.
As formas de produtos forjados para aço incluem chapas, perfis, barras, chapas, tiras, tubos, canos, extrusões e forjados. Geralmente, as extrusões estão incluídas nos forjados, mas a definição de um forjamento exclui chapas laminadas e barras. Isso ocorre porque os forjados, além de se conformarem aproximadamente com a forma acabada do componente requerido, não devem exibir as características de inclusões laminares por meio de fraqueza de espessura, às vezes associada à chapa laminada a quente, ou à instabilidade central, às vezes associada à barra laminada a quente.
Os aços carbono e ligas são normalmente os materiais mais forjados e são prontamente forjados em uma ampla variedade de formas usando processos de forjamento a quente, forjamento a quente ou forjamento a frio e equipamentos padrão. A seleção das temperaturas de forjamento para aços carbono e ligas é baseada no teor de carbono, composição da liga, faixa de temperatura para plasticidade ideal e quantidade de redução necessária para forjar a peça de trabalho. Destes fatores, o teor de carbono tem a maior influência nas temperaturas de forjamento de limite superior.
Apesar do grande número de composições disponíveis, todos os materiais desta categoria apresentam características de forjamento essencialmente semelhantes. Exceções a isso são os aços que contêm aditivos de usinagem livre, como sulfetos, uma vez que esses materiais são mais difíceis de forjar do que as classes de usinagem não livre. Normalmente, a forjabilidade a quente de aços carbono e ligas melhora à medida que a taxa de deformação aumenta. A melhoria na trabalhabilidade deve-se principalmente ao aumento do calor de deformação gerado em altas taxas de deformação.
A justificativa para a seleção de forjamento em detrimento de outros métodos, às vezes mais econômicos, de produção de formas úteis é baseada em várias considerações. As propriedades mecânicas em materiais forjados são maximizadas na direção do fluxo principal do metal durante o trabalho. Para formas complexas, apenas o forjamento oferece a oportunidade de direcionar o fluxo de metal paralelo às principais cargas de serviço aplicadas e controlar, dentro de limites, o refinamento das estruturas originais dos materiais de forjamento. O refinamento da microestrutura é uma função da temperatura, direção e magnitude da redução do material forjado para a forma forjada. A maximização da integridade estrutural do material permite o refinamento da configuração do projeto, que por sua vez permite a redução de peso. O controle adequado do fluxo de metal para otimizar as propriedades em configurações de forjamento complexas geralmente precisa de uma ou mais operações de recalque antes do forjamento da matriz e pode exigir forjamento oco ou extrusão traseira para evitar a formação de rebarbas nas linhas de partição da matriz.
Devido às funções que os forjados de aço devem cumprir, os projetos de forjamento geralmente incluem grandes tamanhos de seções tratadas termicamente e podem ter formato irregular, de modo que tensões significativas podem ser aplicadas em serviço em todos os três eixos principais, a saber (i) longitudinal , (ii) transversal e (iii) transversal curto. Pela seleção cuidadosa do tamanho do material inicial e das etapas de forjamento, é possível que um forjamento mostre propriedades favoráveis em todas as três direções. Em outros casos, por exemplo, em um forjamento de disco retorcido, propriedades mecânicas favoráveis podem ser alcançadas em uma direção radial em torno de toda a circunferência, algo que é possível em um disco que foi simplesmente cortado de uma placa laminada.
Comportamento de forjamento a quente
O forjamento a quente de aços carbono e ligas em formas complexas raramente é limitado por aspectos de forjabilidade, com exceção das classes de usinagem livre. A espessura da seção, a complexidade da forma e o tamanho do forjamento são limitados principalmente pelo resfriamento que ocorre quando a peça de trabalho aquecida entra em contato com as matrizes frias. Por esta razão, equipamentos com tempos de contato de matriz relativamente curtos, como martelos, são frequentemente preferidos para forjar formas complexas em aço.
Forgeability – Forjabilidade é a capacidade relativa do aço de fluir sob carga compressiva sem fraturar. Exceto para grades ressulfurizadas e refosforizadas, a maioria dos aços carbono e baixa liga são geralmente considerados como tendo boa forjabilidade. As diferenças no comportamento de forjamento entre os vários tipos de aço são pequenas o suficiente para raramente afetar a seleção do aço pelo comportamento de forjamento. No entanto, a escolha do aço ressulfurizado ou refosforizado para um forjamento geralmente se justifica apenas se o forjamento for extensivamente usinado, uma vez que uma das principais razões para considerar a produção por forjamento é evitar operações de usinagem subsequentes, esta situação é incomum.
Um meio comum de medir a forjabilidade dos aços é o teste de torção a quente. Como o nome indica, este teste envolve a torção de amostras de barras aquecidas para fraturar em várias temperaturas diferentes selecionadas para cobrir a possível faixa de temperatura de trabalho a quente do material de teste. Os números de torções até a fratura, bem como o torque necessário para manter a torção a uma taxa constante, são relatados. A temperatura, na qual o número de torções é maior, se tal máximo existir, é considerada a temperatura ideal de trabalho a quente do material de teste. A forjabilidade de vários aços carbono, conforme determinado pelo teste de torção a quente, é mostrada na Figura 1. Vários outros testes, conforme dados abaixo, são usados para avaliar a forjabilidade dos aços.
- O teste de forjamento em cunha - Neste teste, um corpo de prova em forma de cunha é forjado entre matrizes planas e a deformação vertical que causa trincas é estabelecida.
- O teste de prensagem lateral – Este teste consiste em comprimir uma amostra de barra cilíndrica entre matrizes planas e paralelas com o eixo do cilindro paralelo às matrizes. As extremidades do cilindro não são restritas e a forjabilidade é medida pela quantidade de deformação obtida antes da rachadura.
- O teste de virada - Neste teste, um cilindro é comprimido entre matrizes planas e as deformações superficiais na fratura no equador do cilindro são medidas.
- O teste de recalque da barra entalhada – Este teste é semelhante ao teste de recalque, exceto que os entalhes axiais são usinados na amostra de teste para introduzir altos níveis de tensão local. Essas tensões mais altas podem ser mais indicativas das tensões experimentadas durante as operações reais de forjamento do que aquelas produzidas no teste de recalque padrão.
- O teste de tração a quente – Este teste frequentemente usa um aparelho de teste especial para variar as taxas de deformação e as temperaturas em uma ampla faixa.
Efeito da taxa de deformação na forjabilidade – A forjabilidade dos aços geralmente aumenta com o aumento da taxa de deformação. Este efeito foi demonstrado para o aço de baixo carbono em testes de torção a quente (Fig1), onde o número de torções até a falha aumenta com o aumento da taxa de torção. Acredita-se que esta melhoria na forjabilidade em taxas de deformação mais altas se deve ao aumento do calor de deformação produzido em taxas de deformação mais altas. Aumentos excessivos de temperatura devido ao calor de deformação, no entanto, podem levar à fusão incipiente, o que pode diminuir a forjabilidade e as propriedades mecânicas.
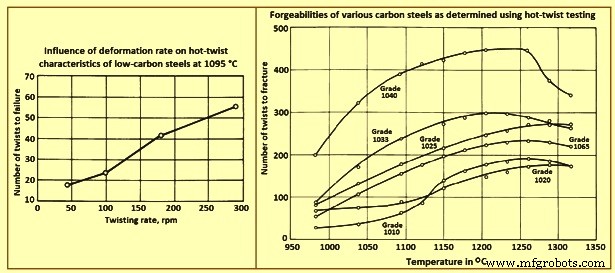
Fig 1 Influência da taxa de deformação e forjabilidades de vários aços carbono
Esforço de fluxo e pressão de forjamento – As tensões de fluxo e as pressões de forjamento podem ser obtidas a partir de curvas de torque geradas em testes de torção a quente ou de compressão a quente ou testes de tensão. Os dados dessas curvas mostram que os requisitos relativos de pressão de forjamento para este grupo de ligas não variam muito em temperaturas normais de forjamento a quente. Pressões consideravelmente maiores são necessárias para o material mais ligado, e este material de liga também mostra um aumento mais significativo na pressão de forjamento com redução crescente.
Efeito da taxa de deformação na pressão de forjamento – As pressões de forjamento necessárias para um determinado aço aumentam com o aumento da taxa de deformação. Estudos com aços de baixo carbono indicam que a influência da taxa de deformação é mais pronunciada em temperaturas de forjamento mais altas. Este efeito é mostrado na Figura 2, que fornece curvas de tensão-deformação para aços de baixo carbono forjados em várias temperaturas e taxas de deformação. Efeitos semelhantes foram observados em ligas de aço.
Fig 2 Pressão de forjamento para aço de baixo carbono recalcado em várias temperaturas e duas taxas de deformação
Seleção de aços para forjamento
Lingotes, blocos, tarugos e placas de aço carbono e liga para forjamento são laminados a quente ou fundidos para dimensões aproximadas da seção transversal e, portanto, as tolerâncias de retilineidade, curvatura, torção e planicidade não se aplicam. Produtos de aço semi-acabados para forjamento são produzidos para pesos de peças especificados ou comprimentos especificados.
Condicionamento de superfície – Produtos de aço semiacabados para forjamento podem ser condicionados por escarificação, lascamento ou retificação para remover ou minimizar as imperfeições da superfície. No entanto, deve-se ter em mente que, independentemente do condicionamento da superfície, o produto ainda pode conter algumas imperfeições na superfície.
Tolerâncias de peso – As tolerâncias para tarugos, blocos e placas são frequentemente +/- 5% para peças individuais ou para lotes com peso inferior a 18 toneladas. Os lotes com peso superior a isso estão frequentemente sujeitos a tolerâncias de peso de +/- 2,5 %.
Corte – Produtos de aço semi-acabados para forjamento são geralmente cortados no comprimento por cisalhamento a quente. Dependendo da composição do aço, também podem ser usados serragem a quente ou corte por chama.
Qualidade – A qualidade, como o termo é aplicado a produtos de aço semi-acabados para forjamento, depende de muitos fatores diferentes, incluindo o grau de solidez interna, relativa uniformidade da composição química e relativa liberdade de imperfeições da superfície.
O aço semiacabado de qualidade para forjamento é usado em aplicações de forjamento a quente que podem envolver tratamento térmico subsequente ou operações de usinagem. Tais aplicações requerem um controle relativamente próximo da composição química e da produção do aço.
A seleção do aço para um componente forjado é parte integrante do processo de projeto e o desempenho aceitável depende dessa escolha. Uma compreensão cuidadosa do uso final da peça acabada serve para definir as propriedades mecânicas necessárias, requisitos de acabamento superficial, tolerância a inclusões não metálicas e os métodos e critérios de inspeção correspondentes.
Aços de qualidade para forjamento são produzidos para uma ampla gama de composições químicas. Com cada uma das práticas de fusão e laminação, é feito um nível de teste e avaliação de qualidade. Se houver necessidade, uma ou mais restrições especiais de qualidade podem ser especificadas para o aço, como o nível de ocorrência de inclusões não metálicas. Ocasionalmente, para aplicações de maior confiabilidade, é necessário que o aço seja submetido ao processo de refusão a arco a vácuo ou refusão por eletroescória.
O uso de aços microligados evoluiu nos últimos anos em aplicações como virabrequins automotivos. Esses aços normalmente têm pequenas adições (0,05% a 0,1%) de vanádio ou nióbio e podem atingir propriedades aceitáveis na condição sem tratamento térmico (como forjado). Consequentemente, essas ligas retêm as vantagens do processo de forjamento ao mesmo tempo em que são economicamente competitivas com os fundidos devido à eliminação do ciclo de tratamento térmico.
Requisitos de projeto – A seleção de aço para uma peça forjada normalmente precisa de algum compromisso entre fatores opostos, por exemplo, resistência versus tenacidade, resistência à corrosão por tensão versus peso, custo de fabricação versus capacidade útil de carga, custo de produção versus custo de manutenção e custo de a matéria-prima de aço versus o custo total de fabricação do forjamento. A seleção do material também envolve a consideração das práticas de fusão, métodos de conformação, operações de usinagem, procedimentos de tratamento térmico e deterioração das propriedades com o tempo em serviço, bem como as propriedades mecânicas e químicas convencionais do aço a ser forjado.
Um projeto de forjamento eficiente alcança o máximo desempenho a partir da quantidade mínima de material consistente com as cargas a serem aplicadas, produtividade e expectativa de vida desejada. Para combinar o aço com seu componente de projeto, o aço é primeiro avaliado quanto à resistência e tenacidade e, em seguida, qualificado quanto à estabilidade à temperatura e ao ambiente. Os aços ótimos são então analisados quanto à produtividade e, finalmente, quanto à economia.
A análise de falhas é uma fonte de dados útil para combinar as propriedades dos aços com os requisitos. A falha de um componente pode ocorrer durante a operação dentro da faixa de tensão do projeto. Uma causa de falha prematura é a falta de orientação adequada de uma tensão crítica de projeto com o fluxo de grão preferido de um forjamento. Falhas imprevistas também podem ocorrer devido à deterioração das propriedades com o tempo e serviço. Por exemplo, trincas por corrosão sob tensão, que resultam de tensões de tração sustentadas, podem ocorrer mesmo em uma atmosfera ambiente típica. Sob essas condições, a falha é mais provável de ocorrer em locais no forjamento que coincidem com o grão final exposto. As análises de falhas podem descobrir outras causas de falhas prematuras, como crescimento excessivo de grãos, inclusões de impurezas não metálicas, dobras de fluxo de grãos devido à prática de forjamento imprópria, falta de uma estrutura metalúrgica forjada e a produção inadvertida de geradores de tensão por usinagem em um filete afiado ou por mau encaixe na montagem.
Efeitos do forjamento nas propriedades
A modelagem de uma configuração complexa a partir de uma barra ou tarugo de aço carbono ou liga precisa primeiro que o aço seja “arranjado” em uma forma inicial adequada (pré-formada) e, em seguida, que ele flua para a configuração final da peça. Esse rearranjo do metal tem pouco efeito na dureza e resistência do aço, mas certas propriedades mecânicas (como ductilidade, resistência ao impacto e resistência à fadiga) são aprimoradas. Essa melhoria nas propriedades (Fig 2) ocorre porque o forjamento (i) quebra a segregação, cura a porosidade e ajuda na homogeneização, (ii) produz uma estrutura de grão fibroso que aumenta as propriedades mecânicas paralelamente ao fluxo de grão e (iii) reduz à medida que - tamanho do grão fundido.
Melhorias típicas na ductilidade e resistência ao impacto de aços tratados termicamente em função da redução do forjamento são mostradas na Fig. 3. Esses dados ilustram que a melhora máxima em cada caso ocorre na direção do alongamento máximo. A tenacidade e a ductilidade atingem máximos após uma certa quantidade de redução, após a qual uma redução adicional é de pouco valor.
Fig 3 Efeito das relações de forjamento nas propriedades mecânicas
A aba 1 fornece as propriedades mecânicas longitudinais típicas de forjados de aço de baixo e médio carbono nas condições recozidas, normalizadas e temperadas e revenidas. Como pode ser esperado, a resistência aumenta com o aumento do teor de carbono, enquanto a ductilidade diminui. Deve-se reconhecer que os forjados de matriz fechada, em sua maioria, são feitos de tarugos forjados que receberam um trabalho prévio considerável. Os forjados de matriz aberta, no entanto, podem ser feitos de tarugos forjados ou de produtos fundidos.
Tab 1 Propriedades longitudinais de forjados de aço carbono em quatro teores de carbono | |||||||
Sl. No. | Conteúdo de carbono | Resistência máxima à tração | Força de rendimento, deslocamento de 0,2% | Alongamento | Redução na área | Resistência à fadiga * | Dureza |
% | MPa | MPa | % | % | MPa | HB | |
Recozido | |||||||
1 | 0,24 | 438 | 201 | 39 | 59 | 185 | 122 |
2 | 0,30 | 483 | 245 | 31,5 | 58 | 193 | 134 |
3 | 0,35 | 555 | 279 | 24,5 | 39 | 224 | 157 |
4 | 0,40 | 634 | 348 | 24 | 42 | 248 | 180 |
Normalizado | |||||||
1 | 0,24 | 483 | 247 | 34 | 56,5 | 193 | 134 |
2 | 0,30 | 521 | 276 | 28 | 44 | 209 | 148 |
3 | 0,35 | 579 | 303 | 23 | 36 | 232 | 164 |
4 | 0,40 | 690 | 355 | 22 | 36 | 255 | 196 |
Azeite temperado e revenido a 595 graus C | |||||||
1 | 0,24 | 500 | 305 | 35,5 | 62 | 193 | 144 |
2 | 0,30 | 552 | 301 | 27 | 52 | 224 | 157 |
3 | 0,35 | 669 | 414 | 26,5 | 49 | 247 | 190 |
4 | 0,40 | 724 | 386 | 19 | 31 | 277 | 206 |
* Teste de feixe rotativo no limite de resistência de 10.000.000 |
O metal flui em várias direções durante o forjamento em matriz fechada. Como exemplo, no forjamento de uma forma de nervura e teia, como um componente de estrutura de ar, quase todo o fluxo de metal é na direção transversal. Tal fluxo transversal melhora a ductilidade nessa direção com pouca ou nenhuma redução na ductilidade longitudinal. A ductilidade transversal pode concebivelmente igualar ou superar a ductilidade longitudinal se as reduções de forjamento forem grandes o suficiente e se o fluxo de metal for principalmente na direção transversal. Efeitos semelhantes são observados no recalcamento de tarugos forjados. Neste caso, no entanto, o eixo longitudinal original do material é encurtado por recalcamento e o deslocamento lateral do metal é na direção radial. Quando as reduções de recalque excedem cerca de 50%, a ductilidade na direção radial geralmente excede aquela na direção axial (Fig. 4).
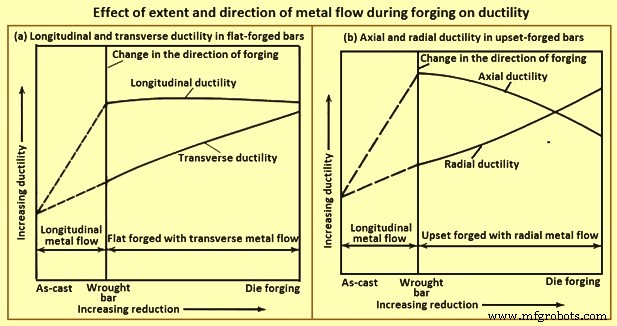
Fig 4 Influência típica da redução de recalque na ductilidade axial e radial de aços forjados
Estrutura forjada e ductilidade – Outro aspecto do controle do material garante que o forjamento final tenha sofrido deformação plástica suficiente para atingir a estrutura forjada necessária para o desenvolvimento das propriedades mecânicas nas quais o projeto foi baseado. Embora alguma deformação plástica seja alcançada durante a quebra de um produto fundido em um tarugo de forjamento, muito mais é transmitido durante o processo de forjamento em matriz fechada. O controle de material para forjados de alta resistência pode exigir a determinação das propriedades mecânicas do tarugo forjado, bem como aquelas do forjamento.
Uma medida de ductilidade ou tenacidade é determinada medindo a redução na área obtida em amostras de teste de tensão transversal. Quando os ensaios correspondentes são feitos de amostras transversais e longitudinais retiradas de forjados tratados termicamente com o mesmo nível de resistência, é possível comparar as propriedades mecânicas de tarugos e forjados e estimar a proporção da estrutura metalúrgica final forjada contribuída por cada um.
Ductilidade e a quantidade de redução de forjamento – O principal objetivo do controle de material é garantir que as propriedades mecânicas ideais sejam alcançadas no forjamento acabado. A quantidade de redução alcançada no forjamento tem um efeito marcante na ductilidade, como mostrado na Figura 4, que compara a ductilidade no lingote fundido, na barra ou tarugo forjado (laminado) e no forjamento. As curvas na Figura 4(a) indicam que quando uma barra forjada ou tarugo é forjado plano em uma matriz, um aumento na redução do forjamento não afeta a ductilidade longitudinal, mas resulta em um aumento gradual na ductilidade transversal. Quando uma barra ou tarugo semelhante é forjado em uma matriz, um aumento na redução do forjamento resulta em uma diminuição gradual na ductilidade axial e um aumento gradual na ductilidade radial.
A ductilidade dos lingotes fundidos varia com a composição química, a prática de fusão e o tamanho do lingote. A ductilidade dos lingotes de aço da mesma composição de liga também varia, dependendo se eles são vazados a partir de aço fundido ao ar ou refundido a vácuo. Ao iniciar com um lingote grande de uma liga específica, às vezes é prático rolar porções do lingote em vários tamanhos de tarugos ou barras com quantidades variadas de redução de forjamento. A quantidade mínima de redução não é padrão, mas raramente é inferior a 2:1 (relação da área da seção do lingote para a área da seção do tarugo). A redução do lingote de aço ao tarugo é normalmente muito maior que 2:1. Em contraste, alguns forjados de ligas resistentes ao calor são forjados diretamente de um lingote fundido.
Freqüentemente, não é viável preparar tarugos para forjados que são tão grandes que precisam de todo o peso de um lingote. A quantidade de redução de forjamento representada por estruturas metalúrgicas forjadas é melhor controlada pela observação e teste de amostras de teste de macrogravação e tensão retiradas de forjados concluídos. Essas amostras permitem a exploração de áreas críticas e, geralmente, de todo o forjamento. Eles são selecionados nas direções longitudinal, transversal longa e transversal curta, conforme necessário. Os testes de gravação permitem a observação visual do fluxo de grãos. Testes mecânicos correlacionam resistência e tenacidade com o fluxo de grãos.
Fluxo de grãos – A macrogravação permite a observação direta da direção e contorno do grão e também serve para detectar dobras, dobras e fluxo reentrante. Por macrogravação de amostras adequadas, o fluxo de grãos pode ser examinado nas direções longitudinal, transversal longa e transversal curta. A macrogravação também permite a avaliação de seções completas, de ponta a ponta e de lado a lado, e uma revisão da uniformidade do tamanho dos macrogrãos. A Fig. 2 mostra o fluxo de grãos em uma peça forjada representativa.
Tamanho do grão e microconstituintes – O exame metalográfico, usando um microscópio, é mais adequado para examinar áreas questionáveis reveladas por macrogravação, para medir o tamanho do grão e para determinar a natureza e a quantidade de microconstituintes.
Força de fadiga – Os testes de fadiga são usados no controle de materiais sob condições e para fins como (i) testes de laboratório de pequenas amostras para o desenvolvimento ou qualificação de material, (ii) testes de laboratório de componentes completos ou subconjuntos para desenvolvimento de projeto, e (iii) vigilância de componentes ou conjuntos em campo para garantir sua confiabilidade contínua em serviço.
O ensaio de fadiga laboratorial de pequenas amostras para qualificação ou desenvolvimento de material é feito por métodos padronizados. Amostras de teste são retiradas de produtos de usinagem ou de forjados de matriz fechada, conforme necessário. Amostras padrão são pequenas o suficiente para permitir a seleção de muitos locais dentro de um forjamento e correlacionar com várias direções de fluxo de grãos. O teste geralmente é feito à temperatura ambiente ao ar, embora seja viável o teste em temperaturas mais altas ou mais baixas e em atmosferas especiais.
A aplicação de testes de fadiga de laboratório em pequena escala para a análise de componentes ou montagens introduz variáveis adicionais. Um é o efeito da condição da superfície. As curvas da Figura 5(a) mostram que a resistência à fadiga das amostras de aço varia acentuadamente, dependendo se a superfície é polida, usinada, laminada a quente ou forjada. O aço testado é um aço forjado de baixa liga tratado termicamente de 269 HB a 285 HB, equivalente a uma resistência à tração de 876 MPa e limite de escoamento de 696 MPa. A preparação da amostra exigia que as amostras fossem usinadas e polidas após o tratamento térmico e que a laminação ou o forjamento precedessem o tratamento térmico. Para uma vida de fadiga de 106 ciclos, o limite de fadiga é de 395 MPa para as amostras moídas, 315 MPa para as amostras usinadas, 205 MPa para as amostras laminadas e apenas 150 MPa para as amostras forjadas.
As curvas da Fig. 5(b) aplicam-se a aços com resistência à tração variando de 345 MPa a 2.070 MPa e são aproximações de vários testes. A preparação de amostras para amostras forjadas ou descarbonetadas no nível de resistência à tração de 965 MPa inclui aços usinados em bruto a partir de barras, aquecidos a cerca de 900 ° C em um forno de mufla a gás por 20 minutos a 30 minutos, muito levemente estampados de um original 7,47 mm de diâmetro a um diâmetro final de 7,16 mm e refrigerado a ar. O tratamento térmico consistiu em austenitização em banho de sal a cerca de 830°C por 45 minutos, têmpera em óleo, têmpera ao ar por 1 hora em torno de 620°C e têmpera em água. O forjamento e o tratamento térmico produziram uma superfície descarbonetada a uma profundidade de cerca de 0,064 mm. Essas amostras apresentaram resistência à fadiga, a 106 ciclos, em torno de 310 MPa, em comparação com 470 MPa para amostras não forjadas, mas usinadas ou polidas e livres de descarbonetação. A descarbonetação reduz os níveis de resistência obtidos pelo tratamento térmico. O controle laboratorial da condição da superfície é difícil de duplicar na produção em quantidade dos componentes forjados. Portanto, a resistência à fadiga de componentes de tamanho normal varia em uma faixa mais ampla do que a de amostras pequenas, devido a variações nas condições da superfície.
Fig 5 Efeito da condição da superfície no limite de fadiga
Resistência à fratura – A fratura frágil de peças forjadas e outros componentes como resultado da propagação de trincas em níveis de tensão consideravelmente abaixo do limite de escoamento do aço levou a um amplo estudo das características da fratura e métodos de avaliação da tenacidade à fratura. Os resultados desses estudos são de grande importância para o controle de materiais, principalmente no que diz respeito ao desenvolvimento de testes para avaliação da tenacidade à fratura, nos quais podem ser baseados padrões para controle de materiais.
Na área de ensaios de laboratório e técnicas analíticas, a maior ênfase tem sido dada ao desenvolvimento de métodos confiáveis para avaliar a resistência de aços que contêm trincas ou defeitos semelhantes a trincas. Especificamente, o interesse centrou-se em métodos para determinar a tenacidade à fratura por deformação plana. Os componentes forjados são avaliados testando pequenas amostras removidas de locais selecionados no forjamento que são representativos das várias direções de grão.
Um procedimento de teste compreende o teste de flexão das amostras entalhadas e trincadas por fadiga em um ambiente neutro. The objective of this test is to get a lower limiting value of fracture toughness which can be used to estimate the relationship between stress and defect size in a metal under service conditions in which high constraint is expected. In the test procedure referred to, a test sample with a chevron notch is suitably pre-cracked in fatigue. It is then tested in a bend test fixture provided with support rolls which rotate and move apart slightly to permit rolling contact and virtually eliminate the friction effect. The sample is subjected to three-point bending, and the imposed load versus displacement change across the notch is recorded on an autographic recorder. Fracture toughness is rated by a calculated parameter, the critical stress intensity.
End-grain exposure – Lowered resistance to stress-corrosion cracking in the long-transverse and short-transverse directions is related to the end-grain exposure. A long, narrow test sample sectioned so that the grain is parallel to the longitudinal axis of the sample has no exposed end grain, except at the extreme ends, which are not subjected to the loading. In contrast, a corresponding sample cut in the transverse direction has end-grain exposure at all points along its length. End grain is especially pronounced in the short-transverse direction on die forgings designed with a flash line. Consequently, forged components designed to reduce or eliminate end grain have better resistance to stress-corrosion cracking.
Estresse residual – The sustained tensile stress at the surface of a forging which contributes to stress-corrosion cracking is the total of applied and residual stresses. When the residual stress constitutes a significant percentage of the total stress, it is to be reduced or eliminated. Common sources of residual tensile stresses include quenching, machining, and poor fit in assembly. Each can be suitably modified to reduce or eliminate tensile stresses, especially those present in an exposed surface. As an example, drastic quenching places the surface of a heat-treatable alloy in a state of compression and the core in a state of tension. Furthermore, the compressed surface can be entirely removed during rough machining, exposing the tension-stressed core material. This hazard can be avoided by quenching after, rather than before, rough machining. In some applications, a surface in tension is placed in compression by shot peening.
Hydrogen-stress cracking occurs without corrosion. Hence, its initiation is not confined to exterior surfaces in contact with a corrosive medium. It can start at any suitable nucleus, such as an inclusion or void, as well as at a surface notch or other irregularity. Hydrogen-stress cracking at the interior is described as hydrogen embrittlement or hydrogen flaking. Hydrogen-stress cracking has been observed, studied, and brought under control in most high-strength steels. The modern practice of vacuum melting can reduce residual hydrogen to negligible amounts. A hydrogen content of 3 ppm to 6 ppm in air-melted steel can be readily lowered to 0.6 ppm to 1 ppm by vacuum arc remelting. Provided that the initial hydrogen content of the steel is acceptably low, material control procedures are to ensure that hydrogen pickup is avoided in all subsequent processing, including forging, heat treating, hot salt bath descaling, pickling, and plating. During forging, steels develop a surface scale and a decarburized surface layer, both of which are subsequently removed by grit blasting and machining. Unless the steel is acid pickled, there is no possibility of hydrogen pickup.
Many of the critical parts made from steel forgings are protected by a coating of cadmium. Steel parts heat treated to strength levels higher than 1,655 MPa are especially sensitive to hydrogen pickup, in case they are coated with cadmium, the coating is deposited in vacuum. Parts heat treated to strength levels lower than 1,655 MPa can be cadmium plated electrolytically, provided that a titanium-containing plating bath is used and the parts are subsequently baked at around 190 deg C for 12 hours.
Mechanical properties – A major advantage of shaping metal parts by rolling, forging, or extrusion stems from the opportunities such processes offer the designer with respect to the control of grain flow. The strength of these and similar wrought products is almost always greatest in the longitudinal direction (or equivalent) of grain flow, and the maximum load-carrying ability in the finished part is achieved by providing a grain-flow pattern parallel to the direction of the major applied service loads when, in addition, sound, dense, good-quality metal of sufficiently fine grain size has been produced throughout.
Grain flow and anisotropy – Steel which is rolled, forged, or extruded develops and retains a fiber like grain structure aligned in the principal direction of working. This characteristic becomes visible on external and sectional surfaces of wrought products when the surfaces are suitably prepared and etched. The fibers are the result of elongation of the micro-structural constituents of the steel in the direction of working. Hence, the phrase ‘direction of grain flow’ is normally used to describe the dominant direction of these fibers within wrought metal products.
In wrought steel, the direction of grain flow is also evidenced by measurements of mechanical properties. Strength and ductility are almost always greater in the direction parallel to that of working. The characteristic of showing different strength and ductility values with respect to the direction of working is referred to as mechanical anisotropy and is exploited in the design of wrought products. Although the best properties in wrought steels are most frequently the longitudinal (or equivalent), properties in other directions can yet be superior to those in products not wrought, that is, in cast ingots or in forging stock taken from a lightly worked ingot.
Rectangular sections show anisotropy among all the three principal directions i.e. longitudinal, long transverse, and short transverse. A design which employs a rectangular section involves the properties in all these directions, not just the longitudinal. Hence, the longitudinal, long-transverse, and short-transverse service loads of rectangular sections are analyzed separately.
Anisotropy in high strength steel – Although all wrought steels are mechanically anisotropic, the effects of anisotropy on mechanical properties vary among different metals and alloys. For example, a vacuum-melted steel of a given composition is generally less mechanically anisotropic than a conventionally killed, air-melted steel of the same composition. Response to etching to reveal the grain flow characteristic of anisotropy also varies. Steels with poor corrosion resistance are readily etched, while those with good corrosion resistance need more corrosive etchants and extended etching times to reveal grain flow. In general, fatigue properties are markedly affected by the relation of flow-line direction to direction of stresses from applied loads. When flow lines are perpendicular to load stresses, a stress-raising effect is produced.
Forging lubricants
For many years, oil-graphite mixtures have normally being used as lubricants for forging carbon and alloy steels. Recent advances in lubricant technology, however, have resulted in new types of lubricants, including water/graphite mixtures and water-base synthetic lubricants. Each of the normally used lubricants has advantages as well as limitations (Tab 2) which is required to be balanced against process requirements.
Tab 2 Advantages and limitations of the main lubricants used for hot forging of steels | |||
Sl. No. | Type of lubricant | Advantages | Limitations |
1 | Water-base micro-graphite | Eliminates smoke and fire; provides die cooling; is easily extended with water | Must be applied by spraying for best results |
2 | Water-base synthetic | Eliminates smoke and fire; is cleaner than oils or water-base graphite; aids die cooling; is easily diluted, and needs no agitation after initial mixing; reduces clogging of spray equipment; does not transfer dark pigment to part | Must be sprayed; lacks the lubricity of graphite for severe forging operations |
3 | Oil-base graphite | Fluid film lends itself to either spray or swab application; has good performance over a wide temperature range (upto 540 deg C). | Generates smoke, fire, and noxious odours; explosive nature may shorten die life; has potentially serious health and safety implications for workers |
Selection criteria – Lubricant selection for forging is based on several factors, including forging temperature, die temperature, forging equipment, method of lubricant application, complexity of the part being forged and environmental and safety considerations. At normal hot-forging temperatures for carbon and alloy steels, water-base graphite lubricants are used almost exclusively, although some hammer shops still employ oil-base graphite.
The most common warm-forming temperature range for carbon and alloy steels is 540 deg C to 870 deg C. Because of the severity of forging conditions at these temperatures, billet coatings are often used in conjunction with die lubricants. The billet coatings used include graphite in a fluid carrier or water-base coatings used in conjunction with phosphate conversion coating of the work piece. For still lower forging temperatures (less than around 400 deg C, molybdenum disulphide has a greater load-carrying capacity than does graphite. Molybdenum disulphide can either be applied in solid form or dispersed in a fluid carrier.
Heat treatment of carbon and alloy steel forgings
Normally steel forgings are specified based upon one of four man conditions namely (i) as forged with no further thermal processing, (ii) heat treated for machinability, (iii) heat treated for final mechanical / physical properties, or (iv) special heat treatment to enhance dimensional stability, particularly in more complex part configurations.
As forged with no further thermal processing – Although the vast majority of steel forgings are heat treated before use, a large tonnage of low carbon steel (0.1 % to 0.25 % C) is used in the as-forged condition. In such forgings, machinability is good, and little is gained in terms of strength by heat treatment. In fact, a number of widely used specifications permit this economic option. It is also interesting to note that, compared to the properties produced by normalizing, strength and machinability are slightly better, which is most likely attributable to the fact that grain size is somewhat coarser than in the normalized condition.
Heat treated for machinability – When a finished machined component is to be produced from a roughly dimensioned forging, machinability becomes a vital consideration to optimize tool life, increase productivity, or both. The specification or forging drawing can specify the heat treatment. However, when specifications give only maximum hardness or micro-structural specifications, the most economical and effective thermal cycle is to be selected. Available heat treatments include full anneal, spheroidize anneal, sub-critical anneal, normalize, or normalize and temper. The heat treatment chosen depends on the steel composition and the machine operations to be performed. Some steel grades are inherently soft while others become quite hard in cooling from the finishing temperature after hot forging. Some type of annealing is usually required or specified to improve machinability.
Heat treated for final mechanical / physical properties – Normalizing or normalizing and tempering can produce the needed minimum hardness and minimum ultimate tensile strength. However, for most steels, a hardening (austenitize) and quenching (in oil, water, or some other medium, depending on section size and hardenability) cycle is employed, followed by tempering to produce the proper hardness, strength, ductility, and impact properties. For steel forgings to be heat treated above the 1,035 MPa strength level and having section size variations, it is general practice to normalize before austenitizing to produce a uniform grain size and minimize internal residual stresses. In some instances, it is normal practice to use the heat for forging as the austenitizing cycle and to quench at the forge unit. The forging is then tempered to complete the heat treat cycle. Although there are obvious limitations to this procedure, definite economies are possible when the procedure is applicable (usually for symmetrical shapes of carbon steels which need little final machining).
Special heat treatment to enhance dimensional stability – Special heat treatments, particularly in more complex part configurations, are sometimes used to control dimensional distortion, relieve residual stresses before or after machining operations, avoid quench cracking, or prevent thermal shock or surface (case) hardening. Although most of the heat-treating cycles can apply, very specific treatments can be needed. Such treatments normally apply to complex forging configurations with adjacent differences in section thickness, or to very high hardenability steels and alloys. When stability of critically dimensioned finished parts permits only light machining of the forging after heat treatment to final properties, special treatments are available, including mar-quenching (mar-tempering), stress relieving, and multiple tempering.
Many applications, such as crankshafts, camshafts, gears, forged rolls, rings, certain bearings, and other machinery components, need increased surface hardness for wear resistance. The important surfaces are normally hardened after machining by flame or induction hardening, carburizing, carbo-nitriding, or nitriding. These processes are listed in the approximate order of increasing cost and decreasing maximum temperature. The latter consideration is important in that dimensional distortion normally decreases with decreasing temperature. This is particularly true of nitriding, which is usually performed below the tempering temperature for the steel used in the forging.
Micro-alloyed forging steels
Micro-alloying (the use of small amounts of elements such as vanadium and niobium to strengthen steels) has been in practice since the 1960s to control the micro-structure and properties of low carbon steels. Most of the early developments have been related to plate and sheet products in which micro-alloy precipitation, controlled rolling, and modern steelmaking technology combined to increase strength significantly relative to that of low carbon steels.
The application of micro-alloying technology to forging steels has lagged behind that of flat-rolled products because of the different property requirements and thermo-mechanical processing of forging steels. Forging steels are normally used in applications in which high strength, fatigue resistance, and wear resistance are needed. These requirements are most often filled by medium carbon steels. Thus, the development of micro-alloyed forging steels has been based around the grades containing 0.3 % to 0.5 % C.
The driving force behind the development of micro-alloyed forging steels has been the need to reduce the production costs. This is accomplished in these materials by means of a simplified thermo-mechanical treatment (that is, a controlled cooling following hot forging) which achieves the desired properties without the separate quenching and tempering treatments required by conventional carbon and alloy steels. In Fig 6, the processing sequence for conventional (quenched and tempered) steels is compared with the micro-alloyed steel-forging process.
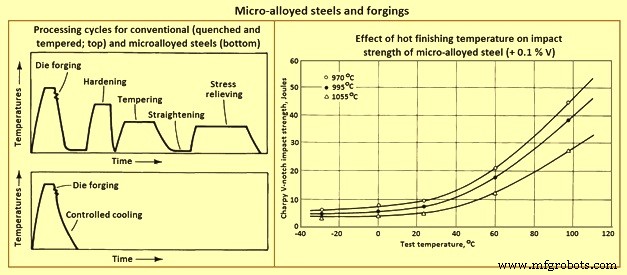
Fig 6 Micro-alloyed steels and forgings
Effects of micro-alloying elements
Carbon – Most of the micro-alloyed steels developed for forging have carbon contents ranging from 0.3 % to 0.5 %, which is high enough to form a large amount of pearlite. The pearlite is responsible for substantial strengthening. This level of carbon also decreases the solubility of the micro-alloying constituents in austenite.
Niobium, vanadium, and titanium – Formation of carbo-nitride precipitates is the other major strengthening mechanism of micro-alloyed forging steels. Vanadium, in amounts ranging from 0.05 % to 0.2 %, is the most common micro-alloying addition used in forging steels. Niobium and titanium enhance strength and toughness by providing control of austenite grain size. Frequently niobium is used in combination with vanadium to achieve the benefits of austenite grain size control (from niobium) and carbo-nitride precipitation (from vanadium).
Manganese – Manganese is used in relatively large amounts (1.4 % to 1.5 %) in many micro-alloyed forging steels. It tends to reduce the cementite plate thickness while maintaining the inter-lamellar spacing of pearlite developed. Hence, high manganese levels require lower carbon contents to retain the large amounts of pearlite required for high hardness. Manganese also provides substantial solid solution strengthening, enhances the solubility of vanadium carbonitrides, and lowers the solvus temperature for these phases.
Silicon – The silicon content of most commercial micro-alloyed forging steels is around 0.3 %. Some grades contain upto 0.7 %. Higher silicon contents are associated with significantly higher toughness, apparently because of an increased amount of ferrite relative to that formed in ferrite-pearlite steels with lower silicon contents.
Sulphur – Many micro-alloyed forging steels, particularly those needed for use in automotive forgings in which machinability is critical, have relatively high sulphur contents. The higher sulphur contents contribute to their machinability, which is comparable to that of quenched and tempered steels.
Aluminum and nitrogen – As in hardenable fine-grain steels, aluminum is important for austenite grain size control in micro-alloyed steels. The mechanism of aluminum grain size control is the formation of aluminum nitride particles. It has been shown that nitrogen is the major interstitial component of vanadium carbo-nitride. For this reason, moderate to high nitrogen contents are needed in vanadium containing micro-alloyed steels to promote effective precipitate strengthening.
Controlled Forging
The concept of grain size control has been used for many years in the production of flat rolled products. Particularly in plate rolling, the ability to increase austenite recrystallization temperature using small niobium additions is well known. The process used to produce these steels is usually referred to as controlled rolling. The benefits of austenite grain size control are not, of course, limited to flat rolled products. Although the higher finishing temperatures needed for rolling of bars limit the usefulness of this approach to micro-structural control, finishing temperatures for micro-alloyed bar steels is nonetheless to be controlled.
It has been shown that, although strength is not significantly affected by finishing temperature, toughness of vanadium-containing micro-alloyed steels decreases with increasing finishing temperature. This effect is shown in Fig 6, which compares Charpy V-notch impact strength for a micro-alloyed steel finished at three temperatures. This detrimental effect of a high finishing temperature on impact toughness also carries over to forging operations, that is, the lower the finish temperature in forging, the higher the resulting toughness, and vice versa. After extensive testing, it has been shown that the finishing temperature for forging if reduced to near 1000 deg C, results in impact properties equal to or better than those of hot rolled bar. It is also shown that rapid induction preheating is beneficial for micro-alloyed forging steels, and that cost savings of 10 % (for standard micro-alloyed forgings) to 20 % (for resulphurized grades) are possible.
Lower finishing temperatures, however, take their toll in terms of higher required forging pressures (and thus higher machine capacities needed) and increased die wear. The improved toughness resulting from lower finishing temperatures, as well as any cost savings which can be achieved as a result of the elimination of heat treatment, is to be weighed against the cost increases caused by these factors.
Micro-alloyed cold heading steels -Steels used in the production of high-strength fasteners by cold heading have been earlier produced from quenched and tempered alloy steels. To obtain sufficient strength with adequate ductility needed six processing steps. Recent developments have led to the use of micro-alloyed niobium-boron steels which need no heat treatment. These steels make use of niobium and boron additions to develop bainitic structures with high work-hardening rates. In most cases they use the deformation of cold heading to achieve the required strength levels without heat treatment.
Processo de manufatura
- Liga 10 (C17500) TF00 Forjamento e Extrusão
- Liga 3 (C17510) TB00 Forjamento e Extrusão
- Liga 3 (C17510) TF00 Forjamento e extrusão
- Forja de liga 25, extrusão TB00 (C17200)
- Forja de liga 25, extrusão TF00 (C17200)
- AMPCOLOY® 972 Forjados
- AMPCO® 18 Forjados
- Uma visão geral sobre o aço ferramenta e suas aplicações
- Uma visão geral do aço ferramenta e suas aplicações que o acompanham
- Diferentes tipos de ferramentas e equipamentos de forjamento