Qual ferramenta de análise de causa raiz é melhor para os operadores?
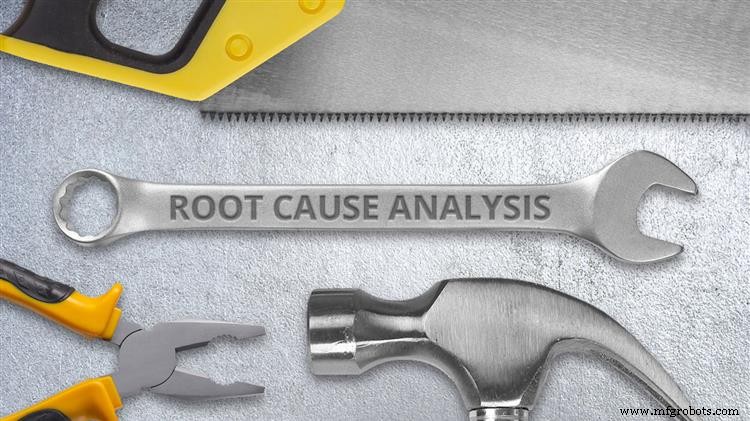
Sempre que for solicitado que você especifique a melhor ferramenta para um aplicativo, você deve primeiro considerar algumas coisas antes de se decidir por uma resposta. Você deve considerar quem vai usá-lo, para que essa ferramenta seria usada (sua aplicação) e o que o resultado se destina a alcançar. Nós sabemos a resposta à primeira consideração de sermos operadores. Com isso em mente, examinemos as demais áreas de preocupação para chegar a uma resposta.
1. Para que será usada a ferramenta?
Os operadores no ambiente da indústria de manufatura e processo desempenham papéis importantes na confiabilidade geral do equipamento. Em primeiro lugar, eles devem estar mais familiarizados com o funcionamento do equipamento em condições normais. A diferença entre o que aquele equipamento deveria estar fazendo e o que ele realmente é capaz de fazer em um determinado momento é a definição de um problema.
PROBLEMA =DEVE - REAL
Os primeiros indícios do início de um problema podem ser freqüentemente percebidos pelos operadores durante o curso normal de suas funções, se eles forem treinados para serem suficientemente atentos. Embora o uso de tecnologias preditivas, como análise de vibração, ultrassom e termografia infravermelha forneça uma indicação muito mais precoce, os operadores às vezes são chamados para ser a última linha de defesa antes que a falha ocorra. Portanto, um dos requisitos da ferramenta pode ser que ela seja capaz de encorajar e facilitar o uso de habilidades de observação aguçada.
2. Qual é o resultado final desejado?
A resposta rápida a essa pergunta é que a ferramenta escolhida deve ser capaz de orientar o operador através do processo de análise de causa raiz (RCA) até a (s) causa (s) raiz do problema que está sendo examinado. Existem pelo menos dois outros resultados-chave que também seriam benéficos para esta ferramenta.
Depois que a ferramenta é usada e a (s) causa (s) raiz (es) determinada (s), deve haver um sistema implementado que permita a resolução do problema. A ferramenta também deve ser de fácil aplicação, uma vez que a expectativa é que os operadores possam usá-la com bastante regularidade como parte de sua rotina diária.
A ferramenta para o trabalho
Com tudo isso em mente, eu recomendaria fortemente uma variação da metodologia de solução de problemas dos 5 Porquês. A técnica original dos 5 porquês foi desenvolvida por Sakichi Toyoda e ganhou destaque em seu uso no Sistema Toyota de Produção.
O arquiteto do Sistema Toyota de Produção, Taiichi Ohno, descreveu o método dos 5 porquês como “a base da abordagem científica da Toyota; ... repetindo 'por que' cinco vezes, a natureza do problema, bem como sua solução torna-se clara. ” Posteriormente, essa técnica também foi adotada na metodologia Seis Sigma.
A variação que proponho é chamada de 5 porquês reais (S-A-5 porquês). Nessa variação, antes de rastrear um defeito ou problema até sua causa raiz, o foco inicial é gasto para determinar quando, de fato, um problema está ocorrendo ou prestes a ocorrer.
Como preencher os 5 porquês reais obrigatórios
- A partir de observação atenta, determine se um problema está ocorrendo comparando o que o ativo ou processo deveria estar fazendo em circunstâncias normais com o seu desempenho atual.
- Anote o problema específico, conforme indicado pela diferença entre “deveria” e “real”.
- Pergunte “por que” o defeito ou problema está ocorrendo e escreva a resposta abaixo do problema.
- Continue perguntando “por que” até que a equipe tenha certeza de que a causa raiz foi isolada.
Os operadores em uma cultura focada na confiabilidade devem ter uma atitude questionadora e ser muito observadores. A inclusão da ferramenta S-A-5Whys em seu conjunto de habilidades beneficiará a organização pela identificação e resolução antecipada de problemas, levando ao aumento da confiabilidade dos ativos.
Sobre o autor:
Carl March possui vasta experiência nas áreas de manutenção, engenharia de confiabilidade, modelagem e projeto de sistemas. Carl é graduado em engenharia mecânica e pós-graduado em engenharia de sistemas automotivos. Como especialista no assunto de confiabilidade na Life Cycle Engineering, sua paixão e foco estão na transferência de conhecimento em RCM, TPM, análise de causa raiz e Excelência em confiabilidade para clientes em todo o mundo que buscam obter distinção na fabricação. Carl alcançou um nível significativo de reconhecimento profissional como um Certified Reliability Engineer (CRE) pela American Society for Quality e como um Certified Maintenance and Reliability Professional (CMRP) pela Society of Maintenance and Reliability Professionals. Você pode entrar em contato com Carl em [email protected].
Manutenção e reparo de equipamentos
- Qual é a melhor ferramenta para cortar chapas metálicas?
- Os perigos e armadilhas da análise de causa raiz
- Vodcast:ferramenta de solução de problemas de análise de causa raiz de 5 porquês
- Vodcast:Análise da causa raiz e prevenção de problemas
- Ex-engenheiro da Intel compartilha aprendizados sobre análise de causa raiz
- Em quais ferramentas de melhoria de confiabilidade devo investir?
- O que você deve procurar em uma célula de trabalho robótica pré-projetada
- O que procurar ao contratar operadores de equipamentos pesados
- Contratação:4 dicas para contratar os melhores operadores de carregadeira de rodas
- Como deve ser a ferramenta ideal para controle de produção?