Análise de causa raiz:um guia completo para fabricantes
Encontrando a origem dos problemas no chão de fábrica
A fabricação pode ser um empreendimento caótico, acelerado e complexo, forçando os fabricantes a não apenas identificar, mas também resolver desafios únicos. Esses problemas podem retardar a produção, criando gargalos ou paralisações quando menos se espera. Quando esses problemas surgem, muitos recorrem à análise de causa raiz (RCA) para ajudar a implementar uma solução.
Aqui está o que abordaremos neste guia detalhado sobre como identificar as causas-raiz. Sinta-se à vontade para pular para uma seção específica:
- O que é uma análise de causa raiz?
- Os benefícios da RCA
- Como realizar a análise de causa raiz
- Métodos e ferramentas disponíveis
- Explorando exemplos de análise de causa raiz
O que é uma análise de causa raiz?
A análise de causa raiz, ou RCA, é um processo específico que reconhece que interrupções e problemas podem ser atribuídos a uma causa específica e que uma solução para corrigir essa causa ecoará pela cadeia e resultará em um estado aprimorado. A RCA tenta identificar a causa de defeitos e problemas em vez de simplesmente tratar os sintomas ou "apagar incêndios".
Benefícios da análise de causa raiz
A análise de causa raiz é reconhecida como um componente crítico tanto na metodologia de manufatura enxuta quanto no Seis Sigma. Ele otimiza o tempo necessário para detalhar a causa de um problema e fornece uma estrutura para solução de problemas na fabricação.
Os benefícios da análise de causa raiz incluem:
- Economia de custos
- Como a análise de causa raiz trata a "doença" e não os sintomas, ela pode reduzir custos diminuindo o tempo de inatividade, reduzindo defeitos e melhorando os processos.
- Processos realistas
- Muitas empresas de manufatura operam com processos parcialmente quebrados. A análise de causa raiz ajuda a otimizar processos para fornecer soluções práticas e estabelecer POPs que podem ser seguidos sem cortar custos ou desviar o processo.
- Automação
- Hoje, as fábricas têm acesso e insights aos dados mais do que nunca. Esses dados podem ser analisados, analisados e contextualizados para tornar a análise de causa raiz consumível para outros departamentos e fábricas da mesma empresa. Isso funciona como um multiplicador de força para melhoria.
- Proatividade
- Como a automação por meio da análise de dados é ideal para os resultados da análise de causa raiz, as preocupações com segurança, manutenção e qualidade podem ser previstas com mais precisão e executadas rapidamente para reduzir o tempo de inatividade.
Como realizar uma análise de causa raiz
A abordagem de análise de causa raiz difere de empresa para empresa, bem como de problema para problema. Ele pode se concentrar em problemas específicos da máquina em um tipo de máquina de um OEM específico. Também pode ser usado para análise de gargalos entre departamentos. Ou pode ser usado para tratar defeitos em toda a fábrica dentro de uma empresa.
Geralmente, há seis etapas envolvidas na análise de causa raiz:
1. Definindo o problema
O primeiro passo é o mais crítico. Todos os membros da equipe devem entender o problema. Deve ser declarado objetivamente. E requer esclarecimento de questões para determinar que é realmente um problema urgente ou gargalo. Este é o estágio mais amplo e é uma declaração geral de problemas, como taxa de defeitos, gargalo ou remessa perdida.
2. Coletando os Dados
A coleta de dados é crucial na análise de causa raiz. Aqui, os membros da equipe tentam listar o maior número possível de elementos causais. Tudo está na mesa, e a lista pode ser ampla e detalhada. Hoje, é mais fácil localizar e aproveitar os dados na análise de causa raiz porque muitos fabricantes de equipamentos OEM incorporam a coleta de dados em suas máquinas. Também pode ser o caso de uma fábrica ter implantado dispositivos de coleta de dados para as máquinas que não os contêm nativamente.
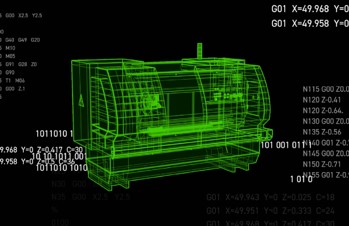
3. Separando Causas de Sintomas
É comum confundir sintomas como causas. Algumas ferramentas e métodos podem ajudar no detalhamento para separar os sintomas das causas. A suposição é que, se as causas puderem ser determinadas e corrigidas, os sintomas deixarão de existir. Aqui, a coleta de dados também pode ser crítica, pois muitos sistemas de coleta de dados possuem análises capazes de determinar categorias de problemas.
4. Determinando a ação corretiva
Uma vez que a causa raiz é determinada, uma solução eficaz pode ser elaborada. Isso pode incluir treinamento, modificação mecânica, layout do piso ou coleta de dados mais robusta e recursos analíticos. Muitas vezes, os dados podem ajudar na elaboração da ação corretiva. Ao ter dados e insights em tempo real em mãos quando a causa raiz é determinada, os gerentes podem criar uma solução relevante e real com base em dados reais.
5. Implementando a solução
Uma vez estabelecida a causa raiz e identificada a ação corretiva, a equipe deve implementar a solução. Isso significa revisar ou substituir SOPs antigos, criar novos fluxos de trabalho e auditar os resultados. Quanto mais profunda a capacidade de coleta de dados, maior o impacto da análise na solução escolhida. Pode até ser possível programar ações autônomas ou semi-autônomas das máquinas para ajudar a implementar ou monitorar o progresso da solução ou afetar seu crescimento.
6. Validando e Estendendo os Resultados
Nenhuma solução dura muito tempo sem um processo de auditoria. Esta peça de auditoria deve validar a eficácia da solução. Isso se torna mais acessível quando a coleta de dados é robusta e submetida à análise em tempo real. Ao fazer isso, a validade da solução pode ser monitorada ou ajustada para melhorar a eficácia. E se a resposta for um sucesso, a causa raiz pode ser transferida para outros processos e departamentos da empresa.
A análise de causa raiz pode ser realizada manualmente por uma equipe. Mas quando combinado com coleta e análise de dados avançados, acelera e aumenta o impacto. As soluções podem ser implementadas em outras fábricas e outros departamentos com problemas semelhantes e podem melhorar a eficiência da produção e reduzir os defeitos na produção.
Métodos e ferramentas de análise de causa raiz
Para empresas que realizam análises de causa raiz, existem muitas ferramentas e metodologias disponíveis para uso. Fornecemos uma breve visão geral de muitas dessas estratégias abaixo:
Os cinco porquês
Uma das ferramentas de análise de causa raiz mais diretas também é uma das mais eficazes. Simplesmente perguntar "por que" cinco vezes pode ajudar a detalhar a causa. Isso força um pensamento mais profundo e crítico até que todas as desculpas tenham se esgotado. Realisticamente, pode demorar um pouco mais ou menos de cinco, mas a metodologia é que a resposta final pode ser revelada perguntando por que até que todas as soluções sejam adotadas.
Diagramas de espinha de peixe
Diagramas de espinha de peixe, também conhecidos como diagramas de Ishikawa, são gráficos visuais de causa e efeito que ajudam a construir as causas de todos os fatores contribuintes. O problema é considerado a “cabeça” do peixe. As causas são categorizadas como ossos menores em uma lista de categorias de causas. O aspecto visual ajuda as equipes a avaliar opções que podem não ter ocorrido apenas no pensamento abstrato.
Fonte da imagem
Modo de falha e análise de efeitos
Para produtos de alta complexidade cujo desempenho contínuo é crítico, a análise de modo e efeitos de falha (FMEA) é uma opção para determinar a causa raiz. Este método analisa as áreas onde podem ocorrer falhas de projeto. De muitas maneiras, está procurando a causa raiz dos defeitos e falhas antes que eles aconteçam. Ele pode ajudar na determinação de falhas de processo para montagem ou fabricação.
Análise da árvore de falhas
Para análise de causa raiz em sistemas de segurança críticos, onde defeitos de engenharia podem causar efeitos desastrosos, a análise de árvore de falhas (FTA) é uma ferramenta eficaz de análise de causa raiz. Ajuda a entender como as falhas do sistema podem acontecer e quais falhas são possíveis. Esse "estado indesejado" é então atribuído a eventos de falha de nível inferior em uma árvore que ajuda a identificar possíveis falhas e permite que os engenheiros projetem para compensar ou eliminar o risco de falha.
Gráficos de Pareto
Um gráfico de Pareto é outro método de visualização testado e comprovado que ajuda as equipes a entender a frequência dos problemas na análise de causa raiz. Ele "classifica" os problemas visualmente para ajudar as equipes a saber o que precisam resolver primeiro. Os gráficos de Pareto também são valiosos quando existem muitas causas diferentes.
Ao listá-los em ordem de importância, as soluções podem ser criadas primeiro para eliminar os defeitos mais significativos. A análise de causa raiz, geralmente parte das metodologias lean ou seis sigma, pode ser repetida para abordar os poucos níveis a seguir no gráfico para continuar as melhorias após a fase inicial.
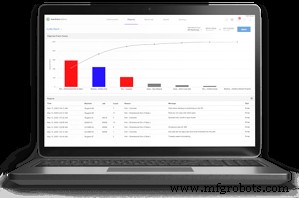
Os gráficos de Pareto facilitam a identificação de 20% dos problemas que estão causando 80% do problema.
É/Não é análise
Já foi dito que metade da vida é saber o que não fazer. Assim como os cinco porquês, a Análise É/Não É é simples, mas poderosa. Ao dividir visualmente o problema em uma categoria "é" e "não é", as equipes de análise de causa raiz podem criar uma lista para se concentrar, ajudando-os a entender quais condições afetam a situação e quais não. Ele mantém as equipes no caminho certo e as impede de listar ou buscar causas falsas.
Explorando exemplos de análise de causa raiz com MachineMetrics
Encontrar a causa raiz de qualquer problema requer uma equipe dedicada e muito trabalho. E quanto mais manual for o esforço, mais tempo levará para a modificação do processo. Mas as equipes de otimização de processos hoje têm um aliado na luta para determinar as causas-raiz.
A coleta de dados está se tornando rapidamente o padrão nos ambientes de fabricação atuais. Dispositivos sofisticados de coleta de dados, software e programas analíticos substituem as planilhas, gráficos criados manualmente e sistemas de entrada baseados em humanos usados para análise de causa raiz.
Com plataformas como MachineMetrics, as empresas agora podem utilizar a coleta de dados automatizada em tempo real, bem como análises avançadas para renderizar dados utilizáveis, padronizados e contextualizados para aqueles que procuram as causas-raiz dos problemas. Esses dados coletados diretamente do controle das máquinas significam que a precisão e as causas raiz imparciais podem ser determinadas de forma mais rápida e eficaz do que os processos manuais.
Vamos explorar alguns exemplos de como o MachineMetrics pode ser usado para identificar a causa dos problemas no chão de fábrica:
RCA em tempo real:o painel de turno atual
O painel de turnos atual é uma ótima solução para monitorar o progresso da produção em tempo real. Ele fornece visibilidade do desempenho em relação à meta para que os operadores possam comparar o desempenho esperado e o real. Dessa forma, você pode capacitar operadores e gerentes para identificar problemas rapidamente.
Essa é uma ótima estratégia de curto prazo e em tempo real para resolver problemas no dia a dia, antes que uma análise mais aprofundada possa ser concluída.
Existem várias visualizações que podem ser usadas para o painel de turno atual, incluindo meta de peças, OEE, utilização e tempo de inatividade.
Nossos clientes normalmente montam monitores em todo o chão de fábrica para que todas as partes interessadas tenham visibilidade completa em todas as máquinas aplicáveis.
Identifique as principais causas de tempo de inatividade com relatórios Pareto
Um dos relatórios mais úteis para entender os motivos de inatividade é o Downtime Pareto, que agregará todos os motivos de inatividade registrados.
Com este relatório, você pode identificar facilmente os motivos de inatividade mais flagrantes. Além disso, você pode segmentar os dados entre diferentes turnos, células de máquinas ou até máquinas individuais para uma visão mais detalhada de onde podem estar os problemas. Além disso, você pode ver onde o tempo de inatividade não planejado está ocorrendo versus o tempo de inatividade planejado.
As categorias comuns de tempo de inatividade incluem troca excessiva de ferramentas, troca excessiva de trabalho, falta de operador e manutenção não planejada da máquina. Com o MachineMetrics, você não apenas terá uma visão precisa do tempo de inatividade, mas também poderá determinar onde está o problema.
O MachineMetrics Downtime Pareto visualiza os principais motivos do downtime no chão de fábrica.
Analisando o relatório de produção para identificar ineficiências de produção
Há muitas métricas disponíveis no Relatório de produção MachineMetrics. Gerentes de melhoria contínua, supervisores de chão de fábrica e engenheiros podem analisar o relatório de produção para entender melhor o desempenho de uma planta. Quando se trata de otimizar sua eficiência, existem várias métricas de eficiência de produção e tempo de execução do trabalho que você deseja garantir que estejam no relatório:
Eficiência de produção
As métricas disponíveis no Relatório de Produção relacionadas à eficiência de produção da máquina para um Trabalho concluído incluem:
- Eficiência de produção
- Total de meio período
- Meio período real
- PPH médio
- PPH ideal
- PPH esperado
- Esperado meio período
- Período Ideal
- Configuração total
- Configuração esperada
Tempos de execução do trabalho
As métricas disponíveis no Relatório de produção relacionadas aos tempos de execução da máquina para um trabalho concluído incluem:
- Primeiro horário de início
- Último horário de término
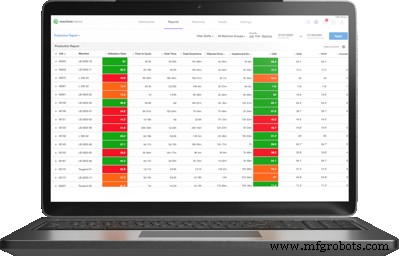
O Relatório de Produção é preenchido com informações sobre a eficiência com que as peças e os trabalhos estão sendo concluídos.
Comece a identificar ineficiências hoje
Com o MachineMetrics, os dados do chão de fábrica são coletados automaticamente em tempo real e padronizados para propagar relatórios e visualizações prontos para uso (e personalizados). Coloque o poder de volta nas mãos dos tomadores de decisão com dados precisos que explicam exatamente o que está acontecendo no chão de fábrica, fornecendo visibilidade para tomar melhores decisões.
Comece a identificar ineficiências e corrigir problemas hoje. Agende uma demonstração com nossa equipe hoje para discutir como o MachineMetrics pode reduzir o tempo de inatividade, aumentar a capacidade e gerar impacto nos resultados da sua organização.
Comece a identificar problemas de produção
Agende uma demonstraçãoTecnologia industrial
- Guia de planejamento de contingência de manutenção para fabricantes
- Software de otimização da cadeia de suprimentos - um guia abrangente para fabricantes
- Os perigos e armadilhas da análise de causa raiz
- Vodcast:ferramenta de solução de problemas de análise de causa raiz de 5 porquês
- Ex-engenheiro da Intel compartilha aprendizados sobre análise de causa raiz
- Um guia completo para soldagem de aço inoxidável
- Como Soldar Alumínio - Um Guia Completo
- Guia de Padrões IPC para PCBs
- 10 principais fluxos de trabalho para fabricantes
- A importância da análise da causa raiz