Escolha da técnica certa para análise de falhas
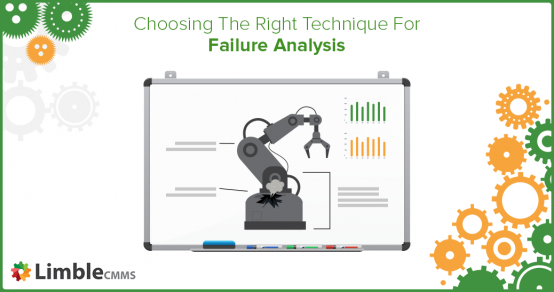
Aprender com as falhas do passado é a melhor maneira de compreender e prevenir quebras futuras do equipamento. Na prática, esse processo de aprendizagem cai sob a égide da análise de falha.
Hoje em dia, existem muitas técnicas de análise de falha para escolher. Todos eles vêm com um conjunto específico de vantagens, desafios e casos de uso. Vamos ver o que está disponível, quais etapas você precisa realizar e quais são as técnicas certas para sua situação.
O que é análise de falha?
A análise de falha é o processo de coleta e análise de dados de falha, geralmente para identificar a causa raiz do mau funcionamento / avaria de um ativo. Essas informações podem ser usadas para melhorar o projeto da máquina / componente, ajustar os cronogramas de manutenção e melhorar os processos de manutenção. Em última análise, seu objetivo é melhorar a confiabilidade dos ativos.
O processo de análise de falha geralmente é feito depois que uma falha já ocorreu. É parte integrante do processo de RCA (Root Cause Analysis). No entanto, ele também pode ser usado para determinar vários fatores que podem causar uma falha potencial - para que possamos selecionar e aplicar os métodos de prevenção corretos.
Dependendo de sua finalidade, a análise de falhas pode ser realizada por engenheiros de fábrica e de manutenção, engenheiros de confiabilidade ou engenheiros de análise de falhas.
Os engenheiros de manutenção conduzem análises de falhas primárias com base em seu conhecimento das operações da planta. Caso a equipe interna não possua os conhecimentos necessários, é aconselhável contratar consultores que prestem serviços de análise de falhas.
Por último, mas não menos importante, os engenheiros de confiabilidade empregam diferentes técnicas de análise de falhas para melhorar a tolerância a falhas e garantir a robustez de seu sistema.
Casos de uso comum para análise de falha
Os motivos mais comuns para conduzir análises de falhas são discutidos abaixo.
Identificando as causas raiz da falha
Em muitos casos, as falhas de máquina são manifestações de nível superficial de problemas mais profundos que não foram resolvidos a tempo. Às vezes, uma combinação de diferentes fatores leva a um colapso inesperado.
Visto que as quebras são muito caras e causam interrupções, as equipes de manutenção precisam se esforçar muito para evitá-las. Além da manutenção de rotina, identificar as causas raiz das falhas - e eliminá-las - é a melhor maneira de evitar as quebras.
Prevenção de falhas potenciais
Uma máquina ou sistema possui muitos componentes interconectados e interdependentes. Esses componentes não têm a mesma probabilidade de causar uma falha em todo o sistema. As informações e os dados do sistema podem ser usados para analisar as probabilidades de falhas potenciais.
Testes e simulações podem ser executados para encontrar os elos mais fracos e melhorá-los - seja por meio de ajustes no projeto ou alterando as recomendações de operação e manutenção.
Melhorando o design do produto
Como acabamos de aludir no parágrafo anterior, a análise de falhas pode ser feita para melhorar o projeto do equipamento ou do componente. Os engenheiros podem empregar diferentes técnicas de análise de falha para identificar possíveis problemas em seus projetos.
Em um lado mais prático, eles também podem conduzir testes destrutivos para avaliar as características dos componentes e materiais que planejam usar em seu produto final.
Os insights obtidos com esses testes e análises são usados para criar ou melhorar a qualidade do produto.
Garantindo a conformidade
Regulamentações e padrões impostos por governos ou órgãos da indústria geralmente requerem análise de falha. Métodos de análise de falhas são usados para garantir que o produto esteja de acordo com os padrões exigidos.
Avaliação de responsabilidade
Os processos judiciais relacionados com as falhas requerem que a causa da falha seja analisada. O mesmo é feito como parte das liquidações de sinistros de seguros específicos para garantir que as condições do contrato sejam atendidas. Nesses casos, a análise de falha pode ser um requisito legal.
Naturalmente, o resultado da análise de falhas também pode ser usado como proteção contra litígios.
Etapas para conduzir a análise de falha
As técnicas de análise de falhas variam amplamente com base nos casos de uso específicos. Dito isso, as etapas para conduzir a análise de falhas seguem o mesmo padrão.
Etapa 1:Defina o problema
Uma declaração de problema bem definida é essencial para qualquer análise profunda. A análise de falhas requer que os engenheiros definam o problema da forma mais clara e concisa possível. A declaração do problema deve conter detalhes sobre:
- a falha que ocorreu
- os dados que precisam ser coletados
- a técnica de análise de falha a ser usada
- as expectativas para a análise de falha (metas)
Etapa 2:Coletar dados de falha
Todos os dados relevantes devem ser coletados. Isso inclui dados quantitativos e dados qualitativos.
Os dados quantitativos referem-se aos dados de operações, dados de manutenção, idade da máquina, etc. Podem ser obtidos:
- de registros de manutenção
- do banco de dados CMMS ou qualquer outra ferramenta usada para monitorar a integridade e o desempenho dos ativos
- por meio da solução de problemas
- realizando uma inspeção visual (como parte da investigação da falha)
Os dados qualitativos não podem ser facilmente quantificados. Esses dados são obtidos entrevistando operadores de máquina, técnicos de manutenção, gerentes de operações, etc. Todos os dados relevantes relativos à falha devem ser coletados.
Etapa 3:Criar um cronograma de falha
As causas básicas resultam em uma reação em cadeia que forma as falhas no nível da superfície que observamos. Os dados de falha coletados podem esclarecer as sequências de eventos que aconteceram. Com informações suficientes, a equipe que realiza a análise pode criar uma linha do tempo de falha. Isso serve como um auxílio visual e mental para o processo de análise.
Esperançosamente, a linha do tempo fornecerá clareza sobre a relação de causa e efeito entre os eventos.
Etapa 4:selecione os dados úteis e descarte o resto
A linha do tempo criada na etapa anterior também é usada para identificar dados úteis. Os dados quantitativos e qualitativos coletados na etapa 2 são mapeados para os eventos na linha do tempo. Os dados que encontram um lugar na linha do tempo são úteis para a análise final.
O restante dos dados pode ser descartado, pois não é relevante para os eventos que causaram a falha. Dessa forma, as equipes de análise de falhas não perderão tempo e esforço analisando informações irrelevantes.
Etapa 5:Administrar a técnica de análise de falha escolhida
A próxima etapa é conduzir a técnica de análise de falha escolhida (iremos discuti-la na próxima seção). O método selecionado depende do caso de uso específico, da indústria e da experiência dos engenheiros de análise de falhas que conduzem a análise.
Etapa 6:analise os resultados, teste e aplique uma solução
O resultado da análise de falha é estudado em detalhes. Na maioria dos casos, o objetivo da análise de falhas é implementar soluções que podem prevenir falhas futuras. Diferentes soluções propostas são testadas e a melhor solução é utilizada para melhorar o sistema / máquina.
Técnicas comuns de análise de falhas
A análise de falhas não é uma ciência exata. É uma exploração curiosa da verdadeira causa por trás das falhas e pode ser considerada um ofício.
Ainda assim, a análise de falhas não pode ser feita sem qualquer estrutura. Ao longo dos anos, os engenheiros desenvolveram algumas técnicas que podem ser usadas como estrutura para analisar todos os tipos de falhas.
As técnicas de análise de falha mais populares são discutidas abaixo.
5 porquês
5 porquês representa uma metodologia simples usada para identificar relações de causa e efeito entre eventos. Baseia-se em perguntar “por que” o problema inicial aconteceu. A primeira resposta então forma a base para a próxima pergunta “por que”. Continuamos perguntando isso até chegarmos a algo fundamental ou completamente fora de nosso controle.
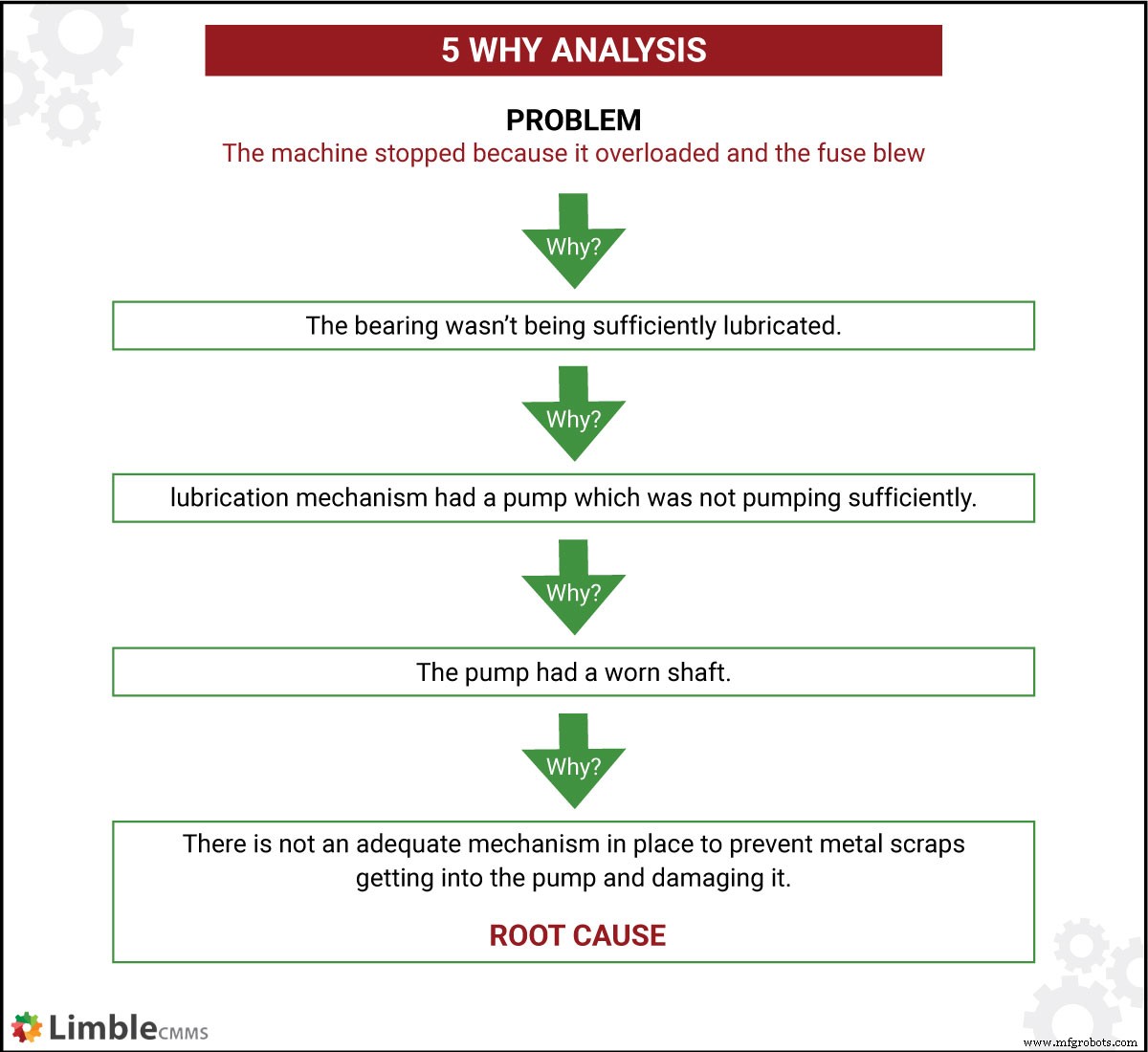
Leitura recomendada: 5 Porquês:A Ferramenta de Análise de Causa Raiz final.
Diagrama de espinha de peixe / Diagrama de Ishikawa
Diagrama espinha de peixe (também conhecido como diagrama de Ishikawa) é uma técnica de análise de falha que é visualizada na forma de uma espinha de peixe. A cabeça representa o problema que estamos analisando, enquanto os ossos representam as causas potenciais.
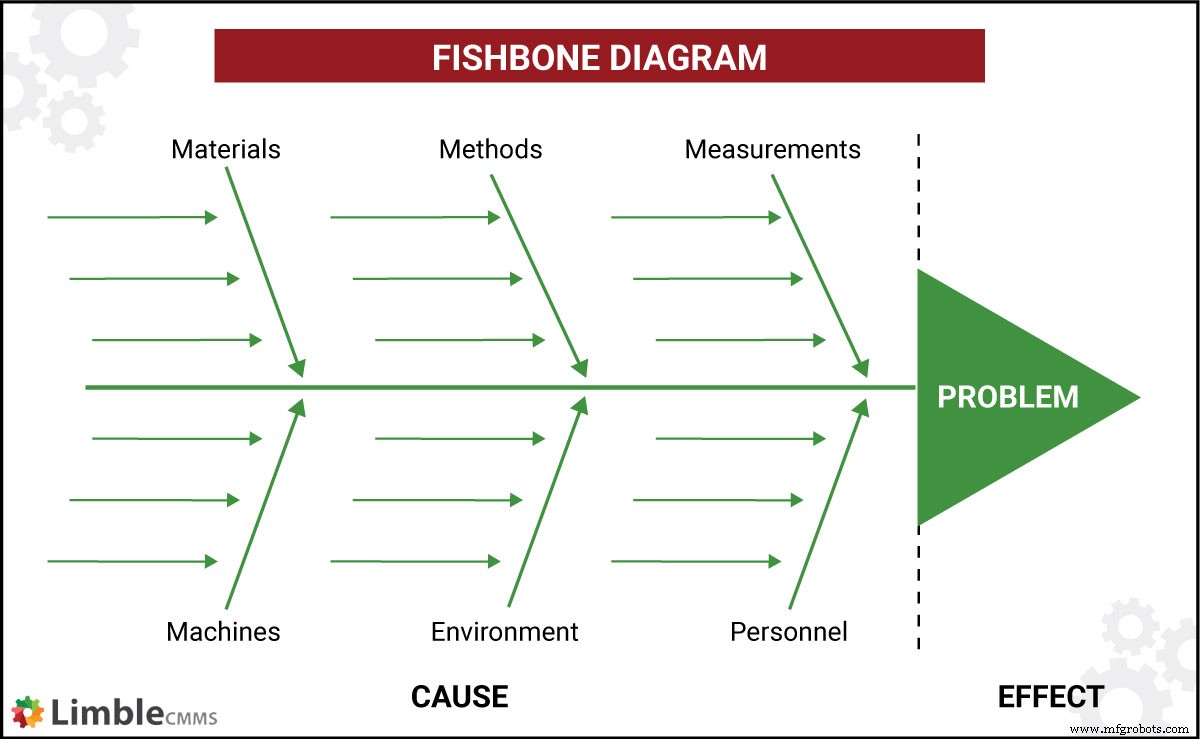
Todo o diagrama é baseado na ideia de que vários fatores podem levar à falha / evento / efeito que estamos investigando. É amplamente utilizado para melhoria de processos na área médica, indústria aeroespacial e TI.
Leitura recomendada: Como usar a ferramenta espinha de peixe para análise de causa raiz.
Modos de falha e análise de efeitos (FMEA)
FMEA é uma técnica de análise de falha preventiva. É usado para prever falhas potenciais com a ajuda de dados anteriores e projeções futuras. Ele analisa as formas potenciais em que uma máquina falha e as consequências de cada uma dessas falhas.
A análise de efeitos e modos de falha é uma técnica de análise de falha preventiva em que cada parte de um sistema é submetida ao escrutínio de uma equipe de especialistas. Ele serve como uma estrutura para instigar sessões de brainstorming rigorosas.
A técnica é amplamente utilizada em engenharia de confiabilidade, engenharia de segurança e controle de qualidade.
Leitura recomendada: FMEA e FMECA:Como realizar a análise de efeitos e modos de falha.
Análise da árvore de falhas (FTA)
Análise da árvore de falhas faz uso de relacionamentos de lógica booleana para identificar a causa raiz da falha. Ele tenta modelar como a falha se propaga através de um sistema. Isso ajuda os engenheiros de confiabilidade a criar sistemas bem definidos com redundâncias adequadas, onde as falhas de componentes nem sempre se transformam em falhas em todo o sistema.
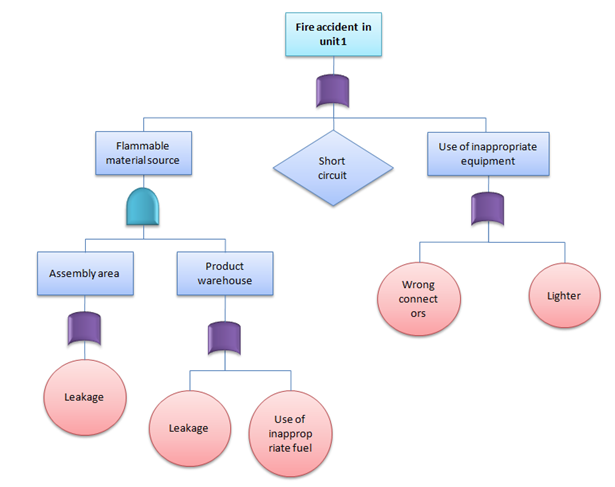
Fonte da imagem
O FTA é amplamente utilizado na indústria aeronáutica, geração de energia e defesa.
Leitura recomendada: O que é a análise da árvore de falhas e como executá-la.
Gráficos de Pareto
Como regra geral, em qualquer sistema, 80% dos resultados (ou falhas) são causados por 20% de todos os motivos potenciais.
O princípio é apelidado de princípio de Pareto (alguns o conhecem como a regra 80-20). Essa distorção entre causa e efeito é evidente em muitas distribuições diferentes, desde a distribuição de riqueza entre pessoas e países até as causas do fracasso em uma máquina.

Fonte da imagem
Os gráficos de Pareto são ferramentas quantitativas para identificar as causas raiz que causam o maior número de falhas. Eles são amplamente usados em cenários em que várias causas raízes precisam ser abordadas, mas os recursos são escassos.
Leitura recomendada: Como conduzir uma análise de causa raiz usando gráficos de Pareto.
Análise de barreira
Análise de barreira é uma metodologia de análise de causa raiz que determina as barreiras à segurança do alvo. Aqui, o destino é definido como o componente, máquina ou sistema que deve ser protegido contra falhas.
Os vários caminhos que podem causar falha da máquina são identificados. Elementos nessas vias que atuam como barreiras para uma operação segura são determinados. Eles são alterados para eliminar os problemas no sistema.
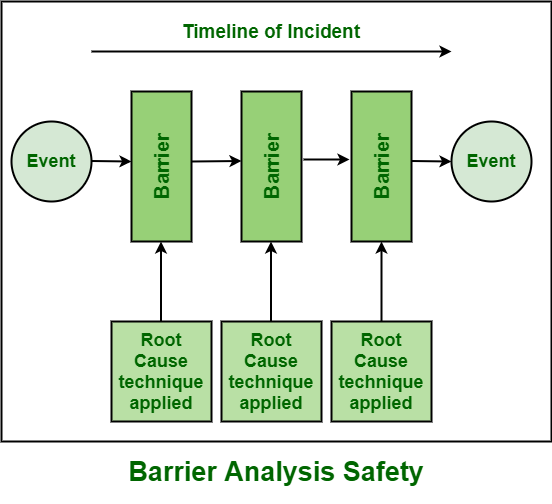
Fonte da imagem
A análise de barreiras identifica os impedimentos para operações bem-sucedidas. As barreiras são contornadas ou eliminadas como resultado. É uma técnica de análise de causa raiz amplamente utilizada na indústria de TI.
Leitura recomendada: Amostra de uma análise de barreira para investigações de causa raiz.
Uma comparação rápida de técnicas de análise de falha
Segue abaixo uma tabela rápida que compara as técnicas de FA com base no tempo necessário para treinar sua equipe interna para utilizá-las, quanto tempo leva para conduzi-las, bem como as principais vantagens e limitações dos respectivos métodos de análise de falhas.
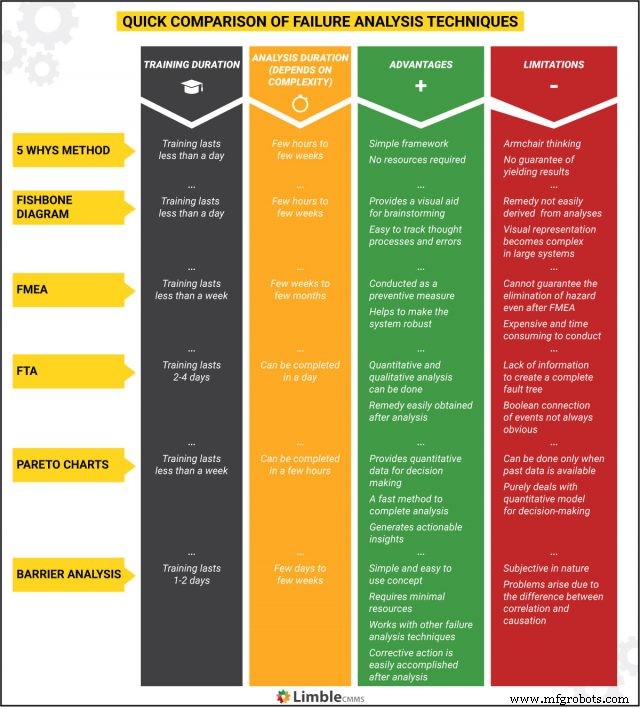
Principais conclusões
A análise de falhas é uma ferramenta versátil com muitos propósitos. Ele pode ser usado para investigar falhas passadas, compreender os mecanismos de falha e prever os modos de falhas futuras.
Não existe uma solução "tamanho único" para conduzir análises de falhas. A seleção da técnica dependerá do objetivo da análise, dos recursos disponíveis, do acesso aos dados relevantes e do que a equipe de análise de falhas conhece e prefere usar.
Manutenção e reparo de equipamentos
- ips para escolher o serviço de reparo CNC correto
- Escolhendo as ferramentas certas para trabalhar em ambientes de trabalho explosivos
- Escolhendo o laser certo
- Dicas para escolher a miniescavadeira do tamanho certo
- A importância da análise de óleo para caminhões comerciais
- Escolhendo o acessório certo para o aluguel de seu equipamento
- Escolhendo o equipamento certo para paisagismo
- Escolhendo o seguro certo para seu equipamento pesado
- Escolhendo o equipamento compacto certo para sua fazenda
- Escolhendo os materiais certos para usinagem CNC