Simulação de efeitos de manufatura leva a um projeto robusto
No projeto e na engenharia, as suposições costumam ser feitas como um mecanismo de simplificação e, às vezes, porque essa simplificação é suficiente. Mas muitas vezes é porque não se tem o tempo adequado nem ferramentas para contabilizar os efeitos não lineares.
Para muitos componentes, os processos de manufatura têm impacto significativo no desempenho do produto, mas costumam ser alguns dos efeitos mais comumente negligenciados. Quais efeitos de fabricação devem ser considerados e quais podem ser ignorados? As respostas a essas perguntas nem sempre são bem compreendidas. Freqüentemente, a prática padrão em engenharia é fazer com que os designers criem um projeto, passem isso para os analistas e, em seguida, os analistas criem e analisem o projeto. Freqüentemente, essa abordagem é bastante complicada e, como resultado, leva mais tempo do que o ideal. Por causa das conexões e do tempo não ideais para ir do CAD para o CAE, não é incomum gastar mais tempo na transferência de dados e na execução da análise inicial do que realmente construir, analisar e compreender o modelo.
Plataforma 3DEXPERIENCE - reunindo as ferramentas de design e mecânica de sólidos:
O 3D A plataforma EXPERIENCE da DASSAULT SYSTÈMES combina os recursos de design de classe mundial do CATIA com os conjuntos de ferramentas de mecânica sólida linear e não linear da SIMULIA. Essa capacidade poderosa permite uma conexão mais perfeita entre CAD e CAE do que é típico na indústria. Também permite processos guiados e modelos padronizados, que podem resultar em uma primeira resposta mais rápida. Portanto, em vez de cálculos e suposições simplificados iniciais feitos por engenheiros especialistas em análise estrutural, essas respostas iniciais podem ser incorporadas ao CAD e aos primeiros conjuntos de ferramentas de engenharia para chegar a um primeiro modelo e a uma primeira estimativa inicial quanto aos indicadores-chave de desempenho estruturais . Isso permite que as respostas estruturais lineares de primeira passagem sejam executadas e analisadas no CAD antes de serem repassadas aos analistas.
O engenheiro de análise estrutural pode então “afiar a lâmina” refinando ainda mais o modelo e adicionando efeitos apropriados ao modelo de “primeira passagem” entregue a eles. Algumas dessas considerações de fabricação podem ser simplesmente suposições lineares "expandidas", mas uma pode incluir contato, não linearidade do material e até mesmo efeitos de reforço de tensão, quando apropriado. Como veremos, esse refinamento pode ser crucial e pode revelar prontamente falhas que, de outra forma, poderiam passar despercebidas. Alguns exemplos “clássicos” de não linearidade são as não linearidades dos materiais - plasticidade no aço, comportamento não linear das borrachas, rachaduras e falhas em uma variedade de materiais e componentes. Embora muitas vezes sejam bem compreendidos, duas outras formas de não linearidade são mais frequentemente esquecidas - o efeito do contato e o impacto da "geometria não linear". Todas essas três formas de não linearidade podem ser resultado do processo de fabricação e todas são prontamente modeladas, analisadas e pós-processadas no 3D EXPERIENCE Platform.
Avaliamos dois exemplos que demonstram esses efeitos de manufatura e, em particular, enfocamos como cada um deles pode desempenhar um papel ao considerar o impacto dos efeitos de manufatura nos sistemas.
- Conexão por pressão em um braço de controle inferior:
O contato é geralmente bem compreendido pelos engenheiros - dois ou mais componentes “colidem” entre si e as forças são transferidas entre eles, o que dá origem a tensões e deformações. Um exemplo de contato que muitas vezes não é considerado, mas pode ser bastante crítico em suas implicações, é o de um “encaixe por pressão”. Em um ajuste de pressão, um componente de uma seção externa ligeiramente maior é “forçado” a outro de uma seção menor, daí o nome. O encaixe por pressão deve equilibrar os requisitos concorrentes:muito pouca interferência entre as peças pode resultar em um encaixe que pode sair facilmente e comprometer a integridade do sistema por meio da separação das peças. No entanto, muita interferência resultará em tensões e tensões elevadas, resultando em falha em uma ou ambas as partes.
O módulo de simulação dentro do 3D A plataforma de EXPERIÊNCIA permite prontamente a capacidade não apenas de capturar tal ajuste de pressão (em vez da abordagem simplificada), mas também pode levar em conta a variação na interferência, a fim de estudar as tensões resultantes devido ao próprio ajuste de pressão e quando essas tensões de ajuste de pressão estão incluídos no carregamento “padrão”. Deixar de levar em conta os efeitos do ajuste de pressão pode ter consequências catastróficas.
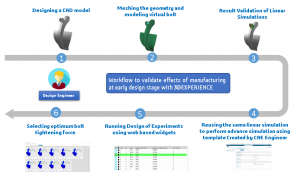
Conforme mostrado no exemplo acima, um braço de controle inferior (que é um exemplo comum de ajuste à pressão) pode falhar inesperadamente se os efeitos do ajuste à pressão não forem considerados durante a simulação. Os resultados à esquerda são equivocados e podem causar problemas de garantia para os fabricantes. Esses tipos de falhas inesperadas e recalls também podem afetar a reputação dos OEMs.
Freqüentemente, na indústria, os efeitos do ajuste por pressão são considerados durante a análise detalhada do componente. O ajuste de pressão excessivo detectado e corrigido no estágio inicial do projeto economizaria tempo e custo geral do projeto.
Abaixo, resumimos o 3D EXPERIENCIE o fluxo de trabalho para conseguir isso:
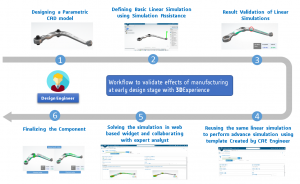
- Modelagem CAD paramétrica:
Design baseado em parâmetros em 3D A plataforma EXPERIENCE potencializa a possibilidade de testar um projeto para suas diferentes configurações. A interferência entre o braço de controle inferior e a bucha pode ser definida e variada por meio de um parâmetro de projeto, conforme mostrado na imagem abaixo.
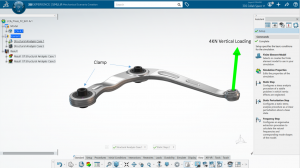
- Modelagem e simulação integradas:
A plataforma unificada para modelagem e simulação CAD torna mais fácil para o projetista analisar o componente projetado antes de passá-lo para o engenheiro de simulação. Assistência de simulação em 3D A plataforma EXPERIENCE pode guiar até mesmo um analista não especialista para realizar simulações lineares e não lineares básicas antes de passar o modelo para um analista especialista. Neste caso, dois casos de simulação separados para carga vertical de 4KN e carga lateral (X direcional) de 2,5KN são definidos. Para ignorar os efeitos não lineares no nível do engenheiro de projeto, as buchas são amarradas ao braço de controle inferior e o cilindro interno da bucha é preso.
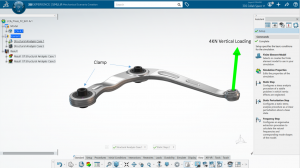
- Reutilização da simulação linear para realizar simulação não linear avançada:
Para um estudo detalhado e preciso, o engenheiro de projeto pode alterar os parâmetros de conexão entre a bucha e o braço de controle inferior para incluir efeitos de encaixe por pressão na simulação. A associatividade entre CAD e FEM torna mais fácil definir um novo recurso de simulação ou modificar um recurso existente dentro da simulação linear. O gerenciador de recursos fornece uma visão consolidada dos recursos de simulação definidos e torna muito fácil modificar com um número mínimo de cliques do mouse.
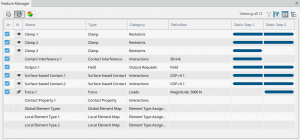
- Automação e colaboração:
Um analista especialista pode definir modelos de simulação para determinados fluxos de trabalho bem definidos e disponibilizá-los prontamente para que os engenheiros de projeto realizem análises detalhadas enquanto consideram os efeitos da manufatura. Os widgets baseados na Web para realizar essas simulações predefinidas geram uma colaboração eficaz entre o designer e o engenheiro de simulação, que pode revisar e finalizar o design.
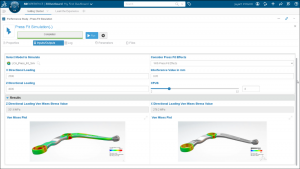
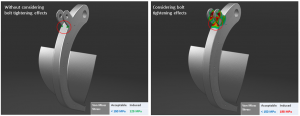
Portanto, ferramentas abrangentes em 3D A plataforma EXPERIENCE torna possível otimizar a interferência do ajuste por pressão no estágio inicial do projeto e evitar falhas e recalls indesejados.
- Modelagem de parafuso em uma junta da forquilha:
O segundo exemplo de efeitos de fabricação é o de uma junta de manilha. Uma junta de manilha é simplesmente um acoplamento que consiste em uma articulação em forma de U (às vezes chamada de “extremidade do garfo”) através da qual um pino ou parafuso passa. Este pino normalmente se conecta a uma articulação ou haste, permitindo que a articulação gire em torno do pino enquanto o “fixa” na extremidade do garfo em todas as outras direções.
As juntas fixas são usadas em uma miríade de produtos e são bastante comuns em suspensões automotivas e de equipamentos pesados, em aplicações de maquinário industrial, em ligações aeroespaciais e em uma variedade de outros casos de uso. Eles podem ser muito pequenos com um simples "pino" minúsculo como a junta para produtos domésticos baratos, mas para equipamentos industriais e grandes máquinas podem muitas vezes ser tão grandes a ponto de pesar mais que uma pessoa e requerem parafusos muito grandes como o "pino.a" Em aplicações de máquinas maiores, muitas vezes não é suficiente simplesmente “conectar” a extremidade do garfo à haste, já que o próprio parafuso deve ser apertado com força, o que pode adicionar tensões de fabricação à peça antes mesmo de quaisquer “cargas operacionais” serem consideradas. Essas cargas aparafusadas tendem a “dobrar” a extremidade do garfo e podem resultar em pré-tensões significativas. Se essas tensões de fabricação forem ignoradas, podem resultar em fatores incorretos de segurança para cargas operacionais, resultando em tensões de pico de carga não conservadoras e previsão excessiva de vidas em fadiga.
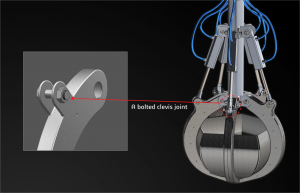
Nesta pinça de mandíbula, uma junta de manilha aparafusada é usada para conectar o link ao componente da mandíbula. Para uma montagem como essa, parafusos grandes (com altas pretensões de parafuso associadas) precisam ser usados para evitar a desconexão. As cargas dos parafusos irão “puxar” os garfos da junta da manilha e resultar em tensões de montagem. Equipamentos de serviço pesado, pois muitas vezes têm engenharia excessiva - é melhor ter um pouco de massa extra do que arriscar tempo de inatividade para equipamentos tão caros. Porém, mesmo com altos fatores de segurança, é importante considerar como esses efeitos de fabricação combinam com as cargas operacionais.
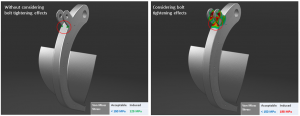
Para os resultados da simulação mostrados na figura 9, as cargas operacionais por si só resultam em tensões bastante modestas nos garfos e estão quase 20% abaixo das tensões alvo. No entanto, levando em consideração as tensões induzidas pela fabricação além das tensões operacionais, os resultados reais são 30% mais altos do que o objetivo. Tais tensões, embora bem abaixo do rendimento, podem, no entanto, resultar em eventual fadiga do componente, resultando em falhas de campo e tempo de inatividade operacional. Portanto, selecionar uma força de aperto ideal do parafuso é muito importante para evitar esses problemas. 3D A plataforma EXPERINCE fornece uma ferramenta de design amigável para realizar este tipo de simulações, conforme resumido no seguinte fluxo de trabalho:
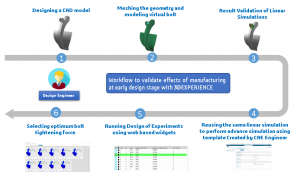
- Modelagem de um parafuso virtual:
Definir uma geometria CAD de parafuso para estudar o efeito do aperto pode incluir complexidade desnecessária (como não linearidade devido a contatos) para um engenheiro de projeto. Portanto, a ferramenta de definição de parafuso virtual em 3D O EXPERINCE fornece uma abordagem simplificada para definir uma representação de parafuso como uma entidade FE e permitir a pré-carga para estudar os efeitos de aperto. O projetista pode simplesmente selecionar as arestas de uma peça ou usar a detecção de parafuso para definir o parafuso virtual na localização da junta da manilha.
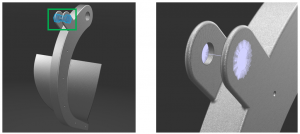
- Definindo uma simulação linear:
Semelhante ao exemplo de encaixe por pressão, a assistência de simulação pode orientar o engenheiro de projeto para configurar a simulação. Selecionando os recursos CAD como face, aresta ou vértice, o engenheiro de projeto pode definir facilmente as condições de carga e limite. Nesse caso, a mandíbula é presa na face inferior e 10KN de carga são aplicados na junta da manilha.
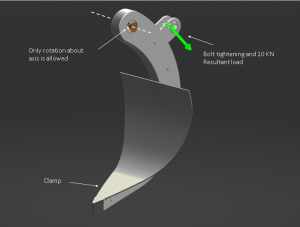
- Modelo personalizado para DOE e otimização:
O analista especialista pode definir um modelo de simulação baseado na web para que o engenheiro de projeto estude o efeito de diferentes valores da força de aperto do parafuso na junta da manilha. O projeto de experimentos pode ser formado no próprio estágio inicial do projeto, sem envolver o analista especialista no loop. Nesse caso, o efeito da pré-carga do parafuso variando de 1KN a 5KN com diferença de 500N é estudado usando o modelo DOE do compositor de processo.
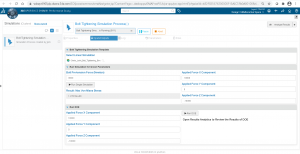
- Validação de resultados com base na web em Análise de resultados:
Assim que o processo for concluído, o engenheiro de design pode colaborar com o analista especialista para visualizar os resultados no widget baseado na web conhecido como Análise de resultados. Apenas modificando os parâmetros de entrada, como carga e força de aperto do parafuso, o designer pode reutilizar o modelo para diferentes modelos que têm uma aplicação semelhante. Conforme mostrado nas imagens abaixo, o engenheiro de projeto pode concluir que a força do parafuso acima de 2KN pode exceder a tensão além do limite aceitável (150 MPa).
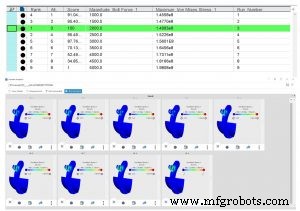
Assim, um engenheiro CAE especialista pode se concentrar em simulações mais avançadas e o engenheiro de projeto cuida dos efeitos da fabricação no estágio inicial do projeto e economiza tempo e custo geral do processo.
Conclusão:
Se os efeitos da fabricação forem considerados no início do estágio de projeto, pode-se entender com mais precisão os verdadeiros “fatores de segurança” no projeto. Ferramentas de design amigável no 3D A plataforma EXPERIENCE pode ajudar a prever o desempenho do produto de forma mais consistente e, como resultado, pode reduzir os custos de garantia, recalls e custos operacionais para os clientes.
Veja todas as nossas soluções de Transporte e Mobilidade visitando:
https://www.3ds.com/products-services/simulia/solutions/transportation-mobility/
Equipamento industrial
- O que é a imprensa entrando na manufatura?
- 4 Tendências de automação promissoras na fabricação de aditivos
- Design Generativo e Impressão 3D:A Fabricação do Amanhã
- O design de referência simplifica os sistemas de alerta precoce de terremotos
- Projeto do sistema de portas | Fundição | Ciência da Manufatura
- Projeto para fabricação de PCBs
- A manufatura lidera o pacote IoT
- Bosch projeta e entrega fábrica de baterias GMG
- Por que o design para fabricação é importante?
- A Drawing Press alcança ótimos efeitos de perfuração