A evolução da crimpagem de mangueiras hidráulicas
Desde seu início humilde operado manualmente até máquinas habilitadas para IoT, os crimpadores de mangueira hidráulica são uma peça crítica do equipamento que qualquer usuário de energia fluida deve entender.
Seria difícil encontrar alguém nesta indústria hidráulica que nunca tenha feito um conjunto de mangueira hidráulica. Técnicos hidráulicos ganham a vida fabricando encanamentos de várias configurações. Ainda assim, até designers e engenheiros provavelmente sujaram as mãos na escola como parte de uma aula introdutória sobre o assunto. Na maioria das vezes, os profissionais de energia fluida começam a trabalhar na loja de mangueiras local antes de passar pelas fileiras de um distribuidor ou fabricante. No entanto, muitos de vocês que estão lendo agora estão familiarizados com as técnicas usadas para crimpar uma mangueira hidráulica.
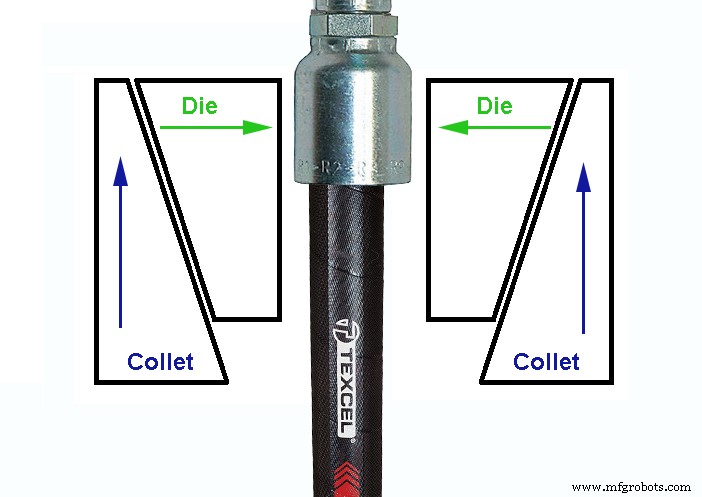
Como seria de esperar, o equipamento de crimpagem de mangueiras teve origens humildes. Qualquer máquina capaz de exercer força radial sobre o diâmetro externo de uma virola de ponta de mangueira resolveria o problema. No início de seus projetos, os engenheiros aproveitaram o arranjo de cone e assento para as matrizes de crimpagem, um sistema ainda mais popular hoje. A pinça atua como um assento e, quando pressiona contra o formato cônico das matrizes, as matrizes são forçadas para dentro (consulte a figura 1).
Os jogadores de mão vieram primeiro
Desde que você possa empurrar as matrizes ou pinças para obter o vetor de força interno desejado, o formato cônico oferece uma vantagem mecânica para auxiliar na compressão da ponteira da extremidade da mangueira. A primeira tecnologia de crimpagem de mangueira usava a boa e velha força humana para alcançar o resultado desejado. As primeiras prensas de estampagem operavam girando uma grande alça em T, girando um parafuso de máquina através de uma cabeça fixa, forçando a extremidade contra o conjunto de matrizes de duas peças.
No caso desses moldes manuais portáteis, as matrizes se movem para baixo contra a pinça fixa e, à medida que as matrizes se movem para baixo, elas também se comprimem para dentro. O técnico deve segurar a ponta da mangueira com cuidado com uma mão enquanto gira a alça com a mão oposta. Depois que as matrizes agarram o encaixe com firmeza suficiente, o técnico usa as duas mãos para apertar o crimpador até que ele chegue ao fundo. É essencial usar apenas as matrizes e pontas de mangueira correspondentes específicas para a aplicação.
Essas unidades manuais portáteis não oferecem a mesma tecnologia de diâmetro de crimpagem automática que os novos sistemas que empregam micrômetros. Você simplesmente prende a unidade até que as duas peças cheguem ao fundo e espere que você atinja sua especificação de crimpagem. Medir a crimpagem ainda oferece ao técnico a confirmação de que a crimpagem está dentro da especificação, mas eles precisam contar com sua experiência com o dispositivo para produzir resultados consistentemente precisos. Devo mencionar também que muitos técnicos ainda usam máquinas portáteis de estampagem manual hoje.
A hidráulica adiciona velocidade e potência
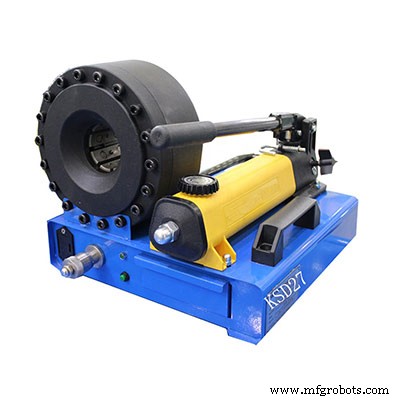
Algo é satisfatório em uma máquina de crimpagem de mangueiras acionada hidraulicamente. Uma máquina totalmente elétrica simplesmente não parece certa, como um hambúrguer sem carne ou um Mazda Miata com transmissão automática. A adição de densidade de potência hidráulica à máquina de crimpagem ofereceu ao técnico um método mais rápido e poderoso de crimpagem de pontas de mangueira. A pinça no frisador hidráulico é essencialmente um cilindro hidráulico anular. Em alguns casos, dois cilindros empurram esse anel anular. A força criada a partir dos cilindros empurra as pinças ou as matrizes, forçando-as a se fecharem na extremidade da mangueira com grande força.
A principal dificuldade com as primeiras máquinas de crimpagem era a falta de versatilidade. As matrizes usadas eram específicas para a ponta da mangueira, incentivando o técnico ou a oficina de mangueiras a usar apenas produtos do mesmo fabricante. Se uma loja desejasse usar várias mangueiras e extremidades, um método para variar o diâmetro de crimpagem tinha que oferecer variabilidade no OD de crimpagem e, ao mesmo tempo, oferecer precisão de até milésimos de polegada.
Rather than limit the technician to fixed diameter dies, instead offering dies capable of a range of internal diameters brought in that variability to allow multiple types and sizes of assemblies. Instead of an exact diameter of, say, 0.733 in., the dies now offer a range from 0.700-0.788 in. for example. What could previously only crimp a ½ in. hose end may now crimp 1- and 2-wire hose from 3/8 to ½ in.
Dies designed for variable diameter applications present the challenge of accuracy, of course. The dies can only bottom out on their smallest setting, which may not always be helpful for any hose or fitting the shop offers. Crimp machine designers had to engineer a method to stop the crimping procedure at the desired size accurately. No technician is skilled enough to stop the hydraulic pump by feel with 0.002 in. accuracy or better.
Accurate and repeatable
Installing an adjustable limit switch offered the most accurate and repeatable solution to the variable die set. An adjustable micrometer attached to the limit switch allows the technician to set the depth of the limit switch to within a thousandth of an inch or less. When the crimp actuator contacts the limit switch, the pump stops automatically. So long as the micrometer has been calibrated, the crimp diameter is both accurate and precise for every single operation.
Hydraulic crimpers using the micrometer were the standard for decades, offering precise control to make hose assembly quick and straightforward. Much of the advancement, until recently, has been improvements to the practicality of the machine. Dual-stage hydraulic pumps provided the technician with rapid die travel until the clamping pressure was met, where the stages switched to the smaller, high-pressure pump for maximum force.
Convenient die storage systems to offer rapid and precise tooling changes also sped up the pace for busy hose shops changing between sizes. A die-set loader offered the technician ease of pulling dies from their holder where they’re inserted into the crimper before being clamped in place. The tidy die storage and replacement systems so widespread today beat the old habit of sifting through drawers or bins where every die of every size mingled with no organization.
Electronic control
Just as the rest of the industry moved towards electronic control, so too did the hose crimping machine. Some technicians found the traditional dial-micrometer hard to read and adjust, and often found itself out of calibration. Linear position sensors replaced the limit switches, and then the adjustment option went digital. A small LCD screen shows the crimp setting, which increased accuracy and reduced the chance for error. The precision of the linear transducer all but guarantees perfect, repeatable crimps.
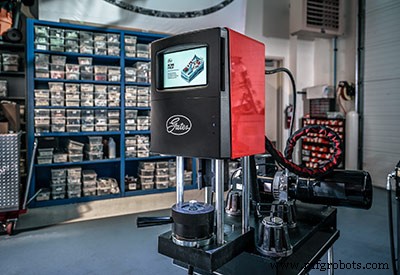
Some hydraulic hose assembly equipment manufacturers have produced semi-automated hose assembly stations. One such machine requires only that the operator load the parts into the machine. The operator loads the stems and ferrules separately, two at a time, and then inserts the hose ends into the machine. The operator starts the sequence that inserts the stems into the pre-cut hose ends along with the ferrules.
The operator unclamps the hose assembly, and if it’s long enough, simultaneously inserts each end into the automatic crimper. A moment later, the technician pulls out a complete hose assembly. If the hose length isn’t long enough to span the gap and into the two openings, the ends are done individually but in parallel. The insertion and crimping functions are completed while the technician works on the opposing operation. Capable of two hundred complete hose assemblies per hour, this machine quickly offers a return on its investment.
Crimpers get smart
The industrial world continues to find new and creative ways to utilize Industry 4.0 concepts, and hose crimping technology is no different. Busy hose shops require speed and versatility, leaving little time for thumbing through catalogues looking for crimp specs. Many top crimp manufacturers offer high-end machines with touch screen HMIs employing wireless links to the manufacturer database.
This system might not be impressive for the technician who has memorized the crimp specs for their standard 100R1 or 100R2 assemblies. But when they’re asked to crimp various assemblies of stainless wrapped thermoplastic hose, they’ll be elated to know the required die information pulls up on the touchscreen. A quick selection of hose, dash size and stem results in readily available crimp specs populated right into the crimper settings.
Just like the fluid power industry at large, crimping technology will continue to advance. Expect to see augmented reality identify the hose and fittings visually, such as with QR codes, then automatically populate crimp specifications. Expect hydraulic hose crimping technology to become more versatile, more productive and more easily maintained.
Equipamento industrial
- Atuador hidráulico para elétrico:discutindo o básico
- Como substituir uma mangueira hidráulica
- A evolução do serviço dinâmico de Houston
- A evolução da visão 3D
- Por que minha mangueira hidráulica está vazando?
- Como desconectar uma mangueira hidráulica de um trator
- Como identificar as conexões de mangueira hidráulica corretas
- O que determina a velocidade de um motor hidráulico
- onde fica a bomba hidráulica de um trator
- O que determina a velocidade de um motor hidráulico?