Costelas da Asa do Amanhã:One-shot, termoplástico, consolidação OOA
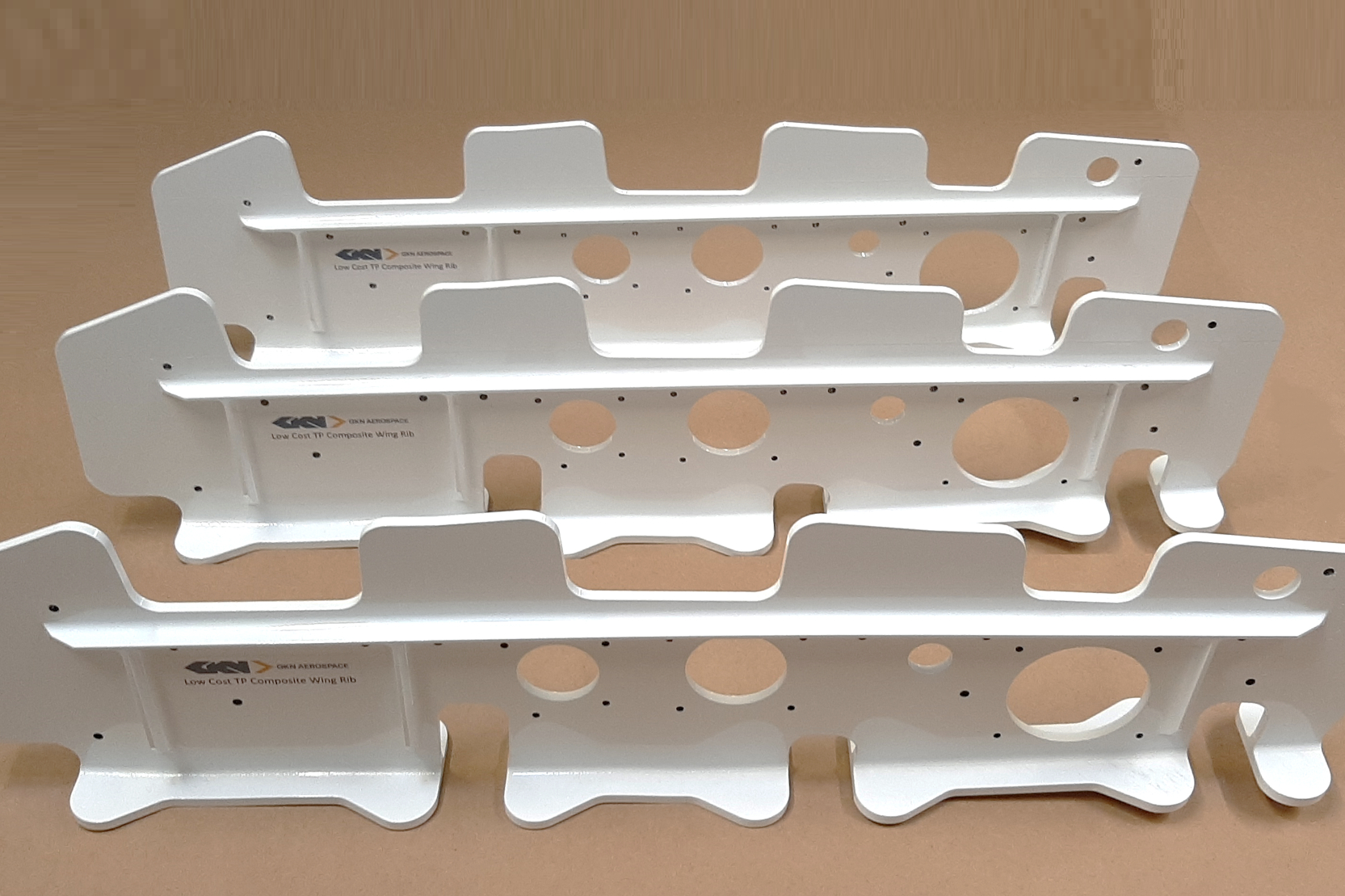
O programa Asa do Amanhã (WOT) da Airbus, lançado em 2015, passou os últimos seis anos explorando tecnologias de fabricação e montagem mais competitivas em termos de custos e de maior rendimento, para asas de aeronaves comerciais de corredor único (consulte CW Cobertura anterior do programa WOT).
De acordo com Arnt Offringa, diretor do GKN Aerospace Global Technology Center Netherlands (Hoogeveen), A GKN Aerospace (Bristol, Reino Unido) tem sido muito ativa no programa WOT, incluindo o desenvolvimento de um demonstrador de longarina feito por moldagem por transferência de resina (RTM) e quatro nervuras de asa de alumínio. Outro demonstrador de tecnologia recentemente entregue pela GKN Aerospace envolveu o desenvolvimento de uma costela composta termoplástica de custo competitivo e um sistema de prensa modular inovador para a fabricação fora de autoclave (OOA) de um tiro para produzi-la.
Dando o salto para os termoplásticos
Em 2018, a GKN Aerospace iniciou discussões internas sobre materiais e tecnologias de fabricação que poderiam ser usados para produzir cinco demonstradores
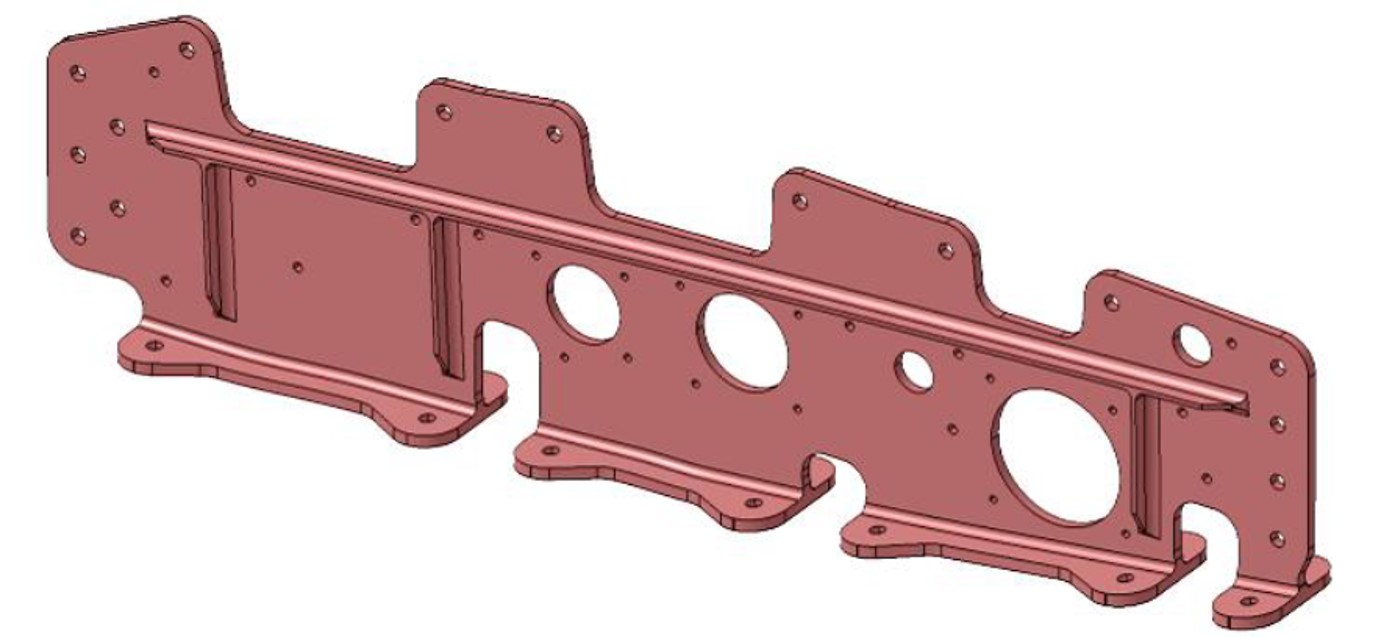
Desenhar a costela. Para permitir uma peça fina e leve, o design de nervura (superior) incorpora a tecnologia de junta de topo da GKN (inferior), com enchimentos de reforço moldados por injeção (meio, mostrado em verde).
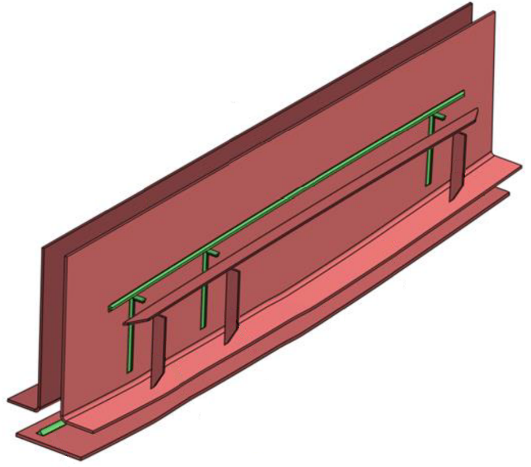
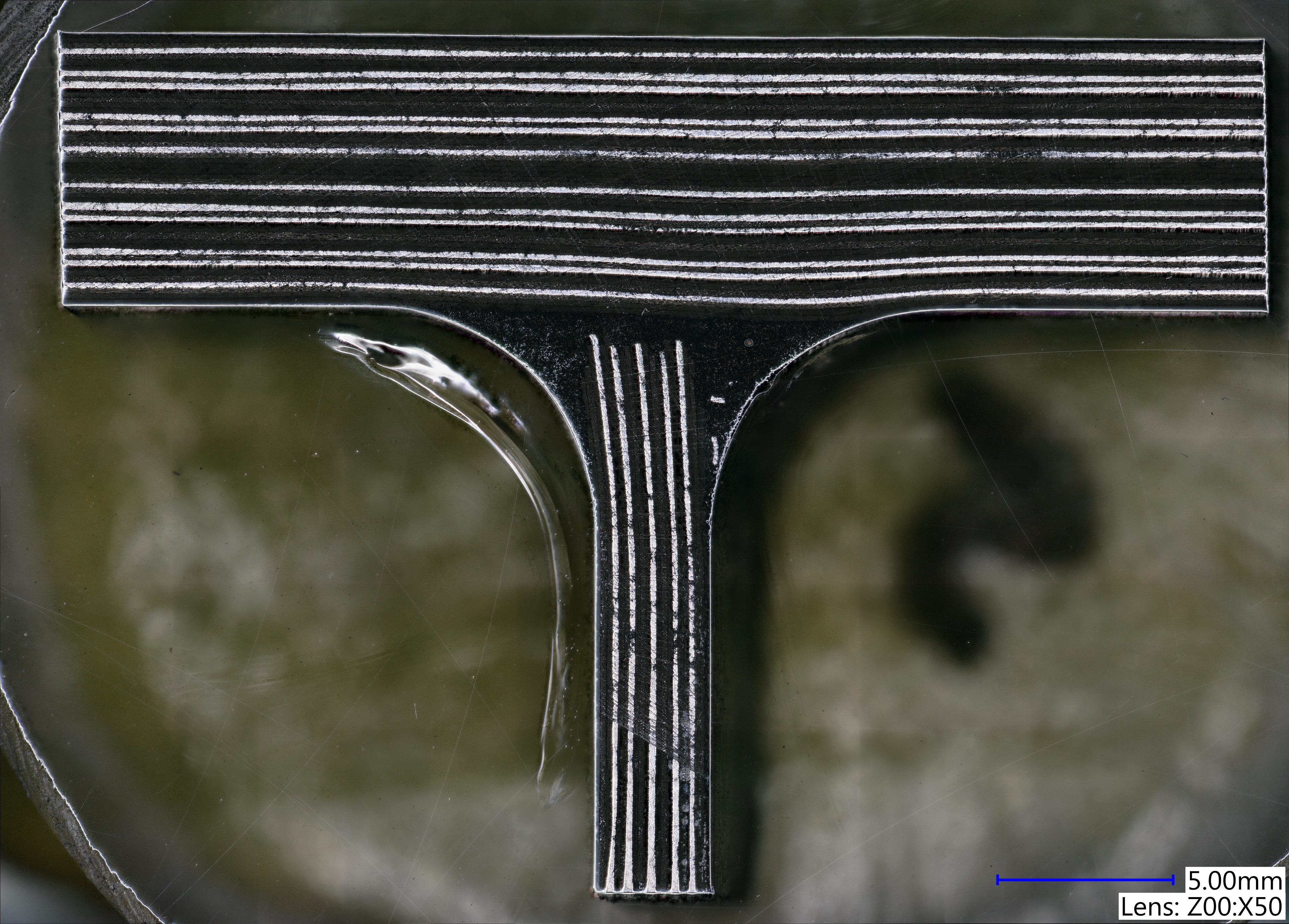
costelas para o programa WOT. A GKN Aerospace comparou várias opções de materiais, incluindo termofixos e compostos termoplásticos. O alumínio, o material tradicional para reforços de aeronaves comerciais, foi escolhido para produzir quatro reforços internos maiores, mas para os reforços externos menores, a empresa decidiu explorar uma opção composta. Offringa observa que, como o demonstrador WOT será uma asa composta, desenvolver uma nervura composta que possa competir com o alumínio é um passo lógico.
“Uma nervura composta em uma asa composta é benéfica por vários motivos”, diz ele. “Em primeiro lugar, o uso de compostos com compostos significa que não há diferença na expansão térmica entre os materiais, como você faria com uma nervura de metal em uma asa composta ou vice-versa. Em segundo lugar, você não terá problemas ou preocupações com relação à corrosão. Compósitos também significam peso reduzido. Por último, mas não menos importante, o uso de compostos torna a inspeção mais fácil. ”
Offringa explica que costelas de metal típicas requerem inspeção humana visual assim que a asa final é montada. No entanto, devido à localização das costelas no interior da asa, isso significa que grandes escotilhas elípticas precisam ser cortadas na pele da asa inferior para que os humanos possam entrar na asa para inspecioná-las. “Se você for para uma costela composta, terá menos fadiga nas costelas e menos rachaduras de fadiga em potencial para inspecionar. A inspeção se torna muito mais simples e menos intensiva, e você não precisa mais construir escotilhas na pele da asa. Será uma pele de asas contínua ”, afirma.
Redução de peso, resistência à corrosão e benefícios de inspeção menos invasivos podem ser obtidos a partir de compostos termofixos ou termoplásticos. “Fizemos um estudo interno e olhamos peso, custo e industrialização, e depois de comparar as diferentes tecnologias, optou-se pelo termoplástico, porque tinha o maior potencial e o melhor business case em relação ao custo”, diz Offringa .
Dada a sua proximidade com o centro de tecnologia da asa de Filton, Reino Unido, da Airbus, onde o demonstrador WOT será testado, a filial de Bristol, Reino Unido da GKN Aerospace é o principal centro de trabalho WOT da empresa. No entanto, dada a experiência da GKN Aerospace Netherlands em termoplásticos de seus dias como Fokker Technologies, as duas equipes da GKN Aerospace juntaram forças para o demonstrador de costelas. “O design foi feito no Reino Unido, mas o desenvolvimento da manufatura foi feito na Holanda, então foi uma ótima cooperação entre as diferentes equipes da GKN Aerospace”, disse Offringa.
Sue Partridge, chefe do WOT da Airbus, observa:“A colaboração com parceiros é um aspecto importante do Programa Asa do Amanhã. Combinando nossos recursos, podemos desenvolver soluções que aproveitem as capacidades de ambas as organizações para um melhor resultado ”.
Para as costelas WOT entregues à Airbus, a GKN Aerospace usou fitas de fibra de carbono / polietercetonecetona (PEKK-FC) da Solvay (Bruxelas, Bélgica), que se baseia na formulação de cristalização rápida Novaspire PEKK-FC (FC) da empresa. Offringa observa que o material de fibra de carbono / poliariletercetona (PAEK) de baixo ponto de fusão da Toray Advanced Composites (Morgan Hill, Califórnia, EUA) também está sendo avaliado como uma opção para futuras estruturas de costelas.
Projetando uma nervura de asa de próxima geração
Existem mais de 20 reforços em uma asa típica de aeronave de corredor único. A nervura do demonstrador de composto termoplástico é a 14ª na asa do demonstrador; os outros irão demonstrar materiais e processos alternativos.
As nervuras compostas termoplásticas são freqüentemente fabricadas por meio da formação de estampas para aeronaves de pequeno porte, diz Offringa. No entanto, a GKN Aerospace descartou a formação de carimbo tradicional como uma opção para a nervura WOT porque as asas de aeronaves comerciais, mesmo para corpos estreitos como o demonstrador WOT, são colocadas sob cargas de compressão e tensão muito altas.
“Se você fosse estampar formando uma nervura termoplástica no sentido tradicional, então você teria que fazer uma nervura muito grossa, com uma teia grossa para torná-la mais forte, de modo que possa suportar as forças que agem sobre ela”, diz Offringa, e isso não é preferível, dados os requisitos de redução de peso. Além disso, a formação de carimbo não seria capaz de criar um componente de flange inferior de dupla face na nervura onde a parte se conecta à pele da asa inferior; um componente extra precisaria ser fabricado e aparafusado ao resto da nervura. A GKN Aerospace precisava de um processo de fabricação que permitisse mais flexibilidade para o projeto que a equipe tinha em mente.
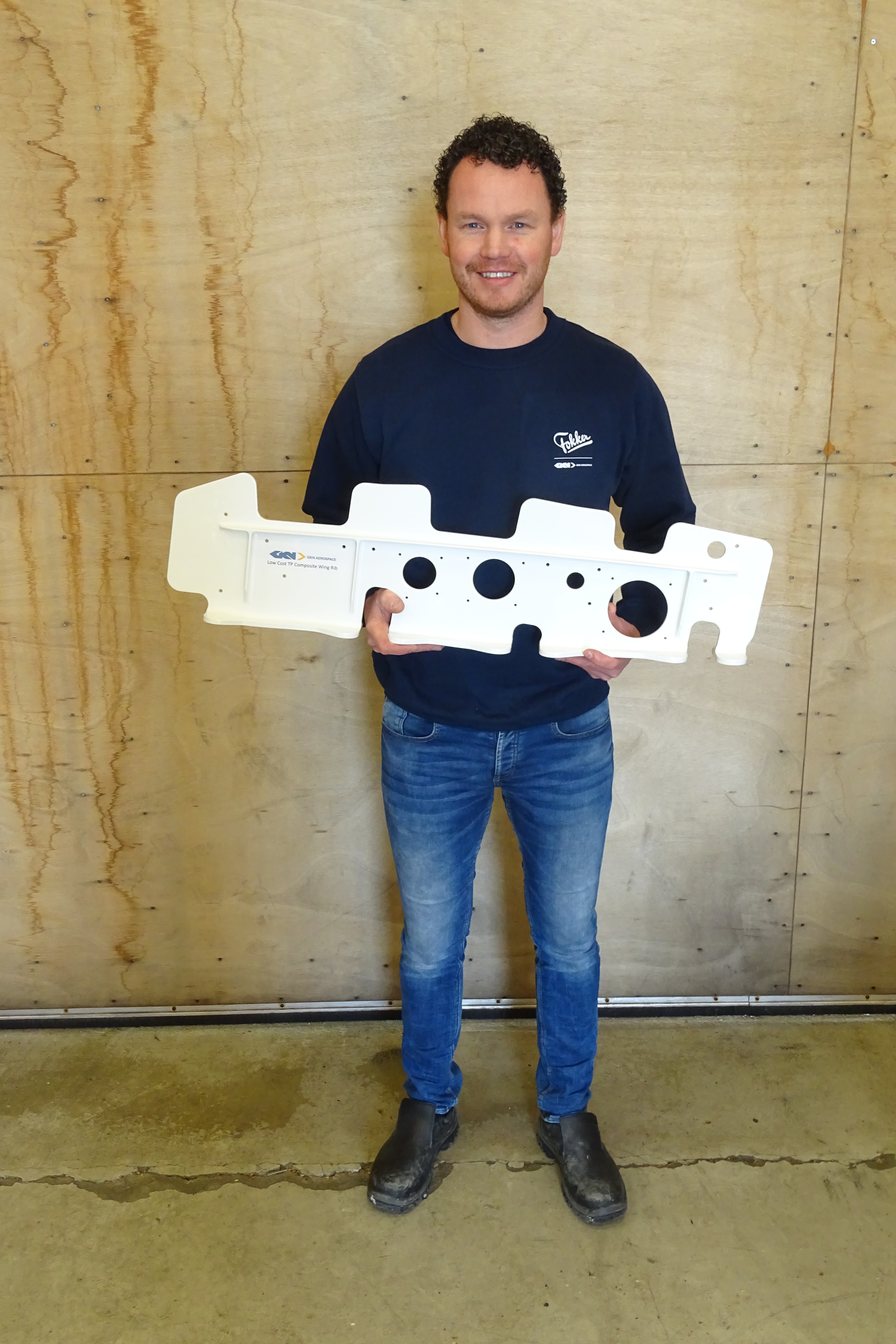
A nervura termoplástica de 90 centímetros de comprimento e 24 centímetros de altura da GKN Aerospace apresenta uma teia vertical e um flange bidirecional de 8 mm de espessura estendido da parte inferior da nervura. Para atender aos requisitos de peso, a teia tem apenas 7 milímetros de espessura. Para evitar flambagem e aumentar a rigidez, a teia é reforçada por elementos de reforço de 3 mm de espessura usando a tecnologia de junta de topo da GKN Aerospace, que usa pré-formas planas de reforço e materiais de "enchimento" moldados por injeção para criar uma junta forte e contínua (consulte "Termoplástico aeroestruturas primárias dão mais um passo à frente ”para aprender sobre o uso dessa tecnologia em um painel da fuselagem da Gulfstream fabricado com fitas de fibra de carbono / PEKK-FC da Solvay).
“Sabíamos que se pudéssemos fazer esse formato em compósitos e torná-lo robusto, teríamos um design muito leve com a redução de peso que estávamos procurando. Mas o problema era:como fazer uma forma tão complicada de maneira econômica e com taxas altas? É aí que colocamos nosso esforço para criar este novo produto ”, diz Offringa.
Fabricação OOA em uma etapa
O processo se baseia na tecnologia que a GKN Aerospace usou anteriormente para o projeto TAPAS (Estrutura de Aeronave Primária Termoplástica Acessível) e para o desenvolvimento de um painel de fuselagem para a Gulfstream que usa a tecnologia de junta traseira da empresa. Para a costela WOT, a GKN Aerospace desenvolveu um processo de consolidação OOA em uma etapa. “Levamos nosso trabalho anterior para o próximo nível, saindo da autoclave pela primeira vez”, observa Offringa.
Primeiro, fitas termoplásticas unidirecionais (UD) são cortadas nas larguras corretas e um laminador é usado para pré-formar os elementos planos em duas pré-formas de teia em forma de L. As pré-formas de teia, uma pré-forma plana para o flange e pré-formas menores e elementos de preenchimento moldados por injeção que compõem as longarinas são todas carregadas em uma ferramenta, que é colocada dentro de uma prensa de co-consolidação modular que é semelhante a uma moldagem de transferência de resina (RTM) pressione. A prensa fecha e um sistema de bexiga é usado para criar pressão nas direções horizontal e vertical, simulando a pressão em uma autoclave. Um sistema de aquecimento por resistência integrado leva o composto à temperatura de fusão brevemente antes de resfriar para consolidação.
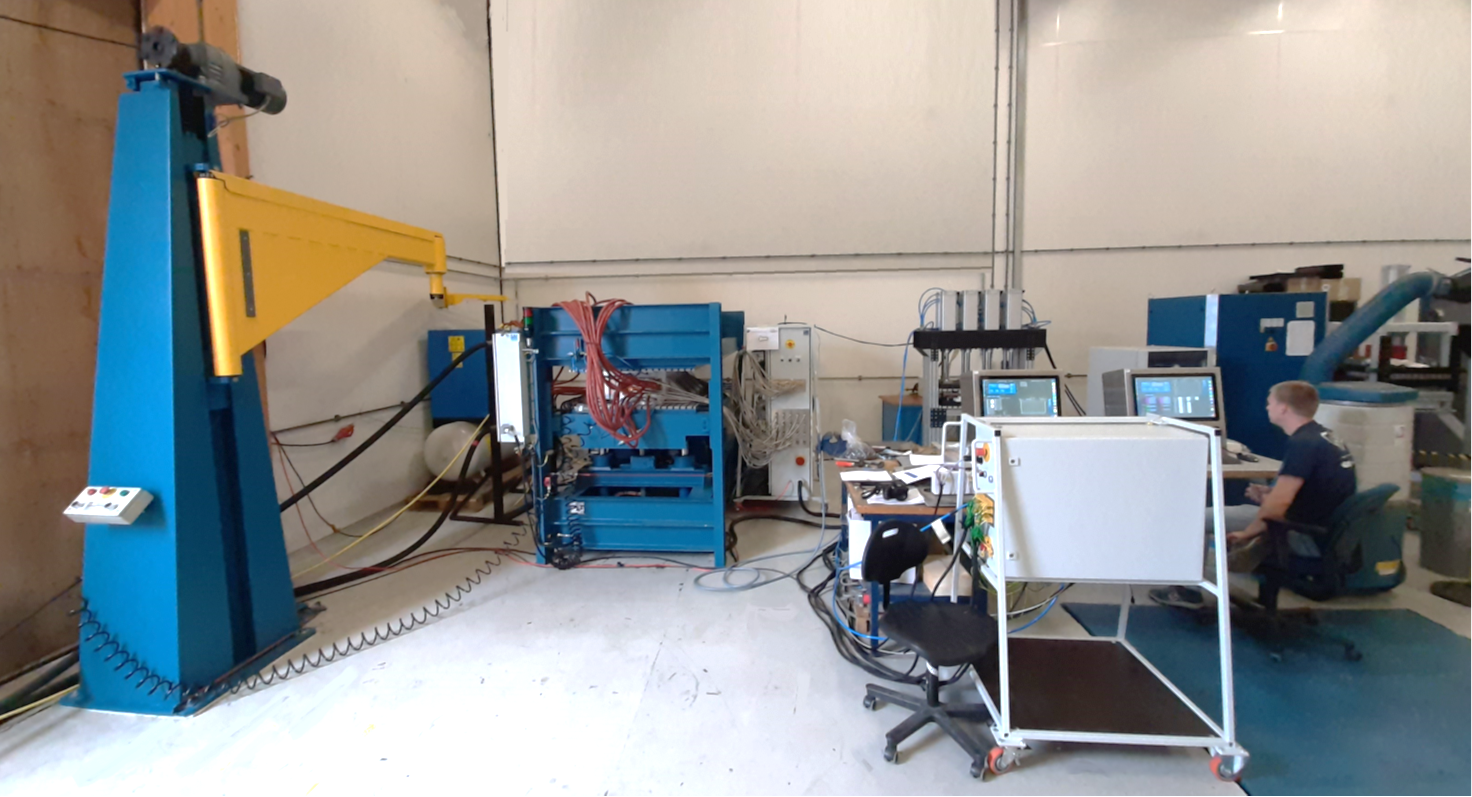
“Colocamos a maior parte do esforço de desenvolvimento no ajuste e otimização das ferramentas”, diz Offringa. O sistema é projetado para ser modular; as ferramentas podem ser trocadas para acomodar nervuras com diferentes dimensões ou outros tipos de peças, mantendo o mesmo sistema de aquecimento e resfriamento. Embora não seja necessária para essas nervuras, a prensa GKN Aerospace desenvolvida em seu Centro de Tecnologia pode acomodar peças de até 6 metros de comprimento, que também podem incluir outros painéis ou vigas.
O sistema de controle de processo é fundamental no processamento de termoplásticos. Os termoplásticos derretem em temperaturas mais altas do que os termofixos e devem ser resfriados em um processo consistente e controlado para minimizar o empenamento e maximizar a cristalinidade. “É muito importante controlar o processo exato do início ao fim”, diz Offringa. “A gestão térmica do ciclo de aquecimento é muito importante.” (consulte a barra lateral “Problemas de formação de termoplásticos (TP)” neste artigo para obter mais detalhes sobre os problemas e a importância do controle do processo ao usar termoplásticos).
Recursos especiais de ferramentas são usados para permitir que os reforçadores integrados e finos se soltem facilmente da ferramenta. A peça desmoldada está quase em forma líquida e, em seguida, é aparada para formar a peça acabada. Da ferramenta de entrada à ferramenta de saída, todo o processo leva cerca de 45 minutos. Isso significa que, com uma prensa, cerca de 15 nervuras de asa podem ser fabricadas em um turno de oito horas.
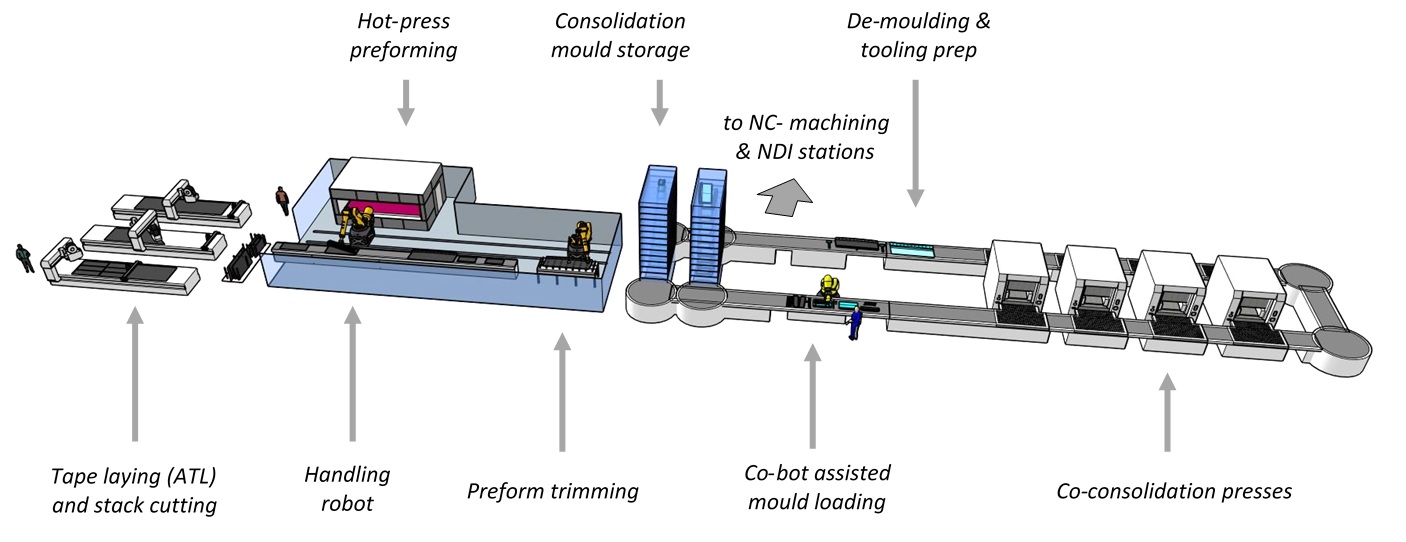
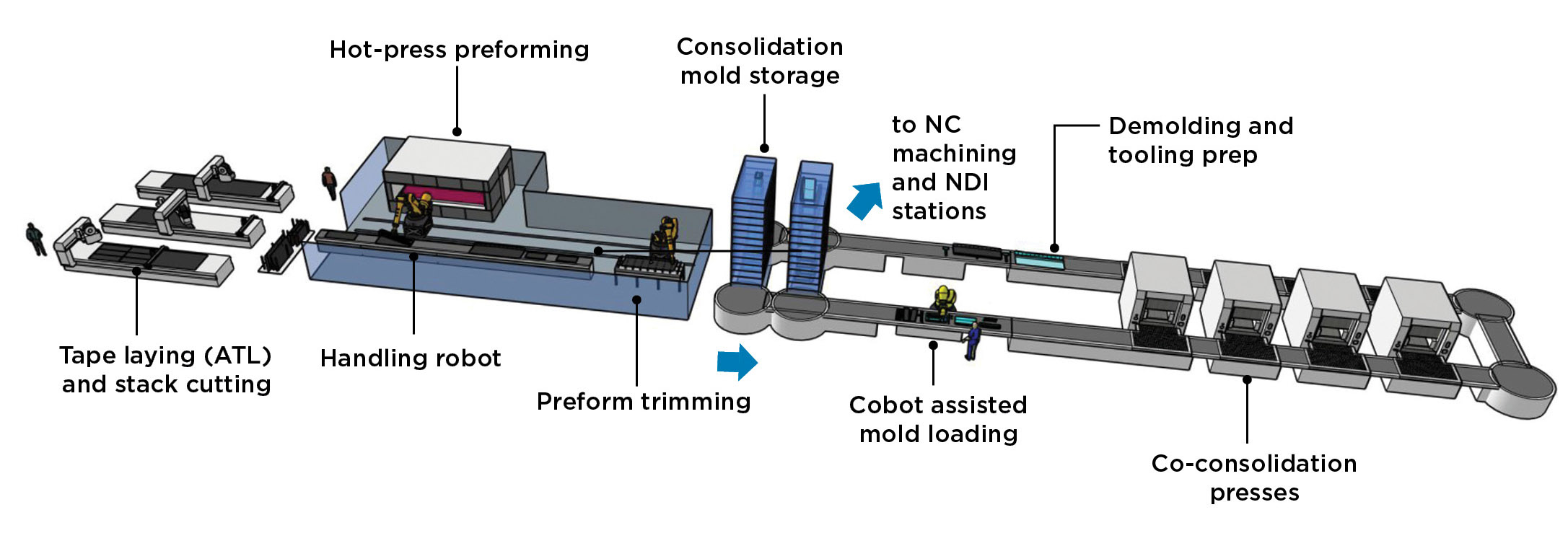
“Acaba sendo um processo de fabricação simples”, observa Offringa. “Estamos fazendo muitas coisas ao mesmo tempo:co-consolidando pré-formas com diferentes formatos, criando a parte inferior da nervura para ter um flange bidirecional e, ao mesmo tempo, endurecendo a teia com a tecnologia de junta de topo. No final das contas, porém, pegamos todos os elementos do material, os colocamos em uma ferramenta e criamos uma peça homogênea em uma etapa de processamento ”.
Teste, entrega e além
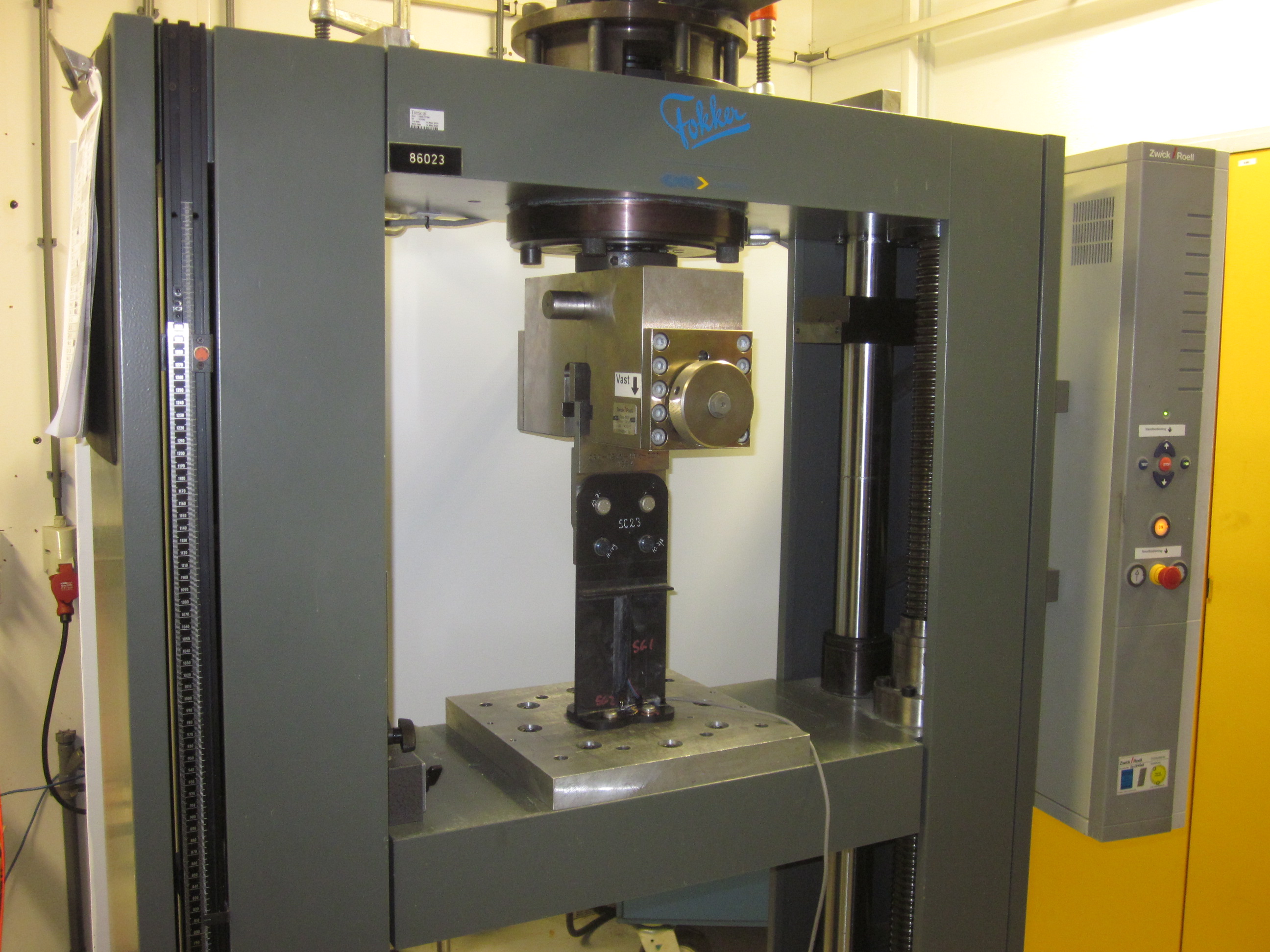
Testando. Os subcomponentes foram testados para atender aos requisitos de tensão e resistência à compressão nas instalações da Ilha de Wight e Hoogeveen da GKN.
No final de 2019, os subcomponentes de costela foram testados nas instalações da Ilha de Wight e Hoogeveen da GKN Aerospace, e Offringa diz que eles passaram nos requisitos de carga de tensão e compressão "por uma ampla margem". Ele acrescenta:“É forte, é difícil, é fácil de fabricar. Este é um conceito que saiu exatamente como esperávamos. ” Em comparação com uma versão de alumínio, Offringa diz que a versão de composto termoplástico oferece uma economia de peso significativa e é competitiva em termos de custos.
A empresa entregou três costelas para a Airbus, uma das quais será montada e testada no demonstrador WOT. A GKN Aerospace continua a trabalhar na otimização de seu processo e materiais para reforços aeroespaciais comerciais, tanto para a Wing of Tomorrow como além.
Resina
- Composto termoplástico reforçado com fibra contínua feito inteiramente de recursos naturais
- Solvay Expande a Capacidade do Composto Termoplástico
- Fraunhofer encomenda células de produção Engel automatizadas para P&D de compósitos termoplásticos
- Instituto de Estruturas e Projeto DLR aumenta a maturidade de estruturas de fuselagem de compósito termoplástico
- Solvay conclui a instalação da instalação na Carolina do Sul, aumenta a capacidade de composto termoplástico dos EUA
- INEOS Styrolution para construir local de produção para compósito termoplástico StyLight
- Xenia apresenta compostos termoplásticos de CF / PP
- Tubo composto termoplástico em ascensão no fundo do mar
- Composto termoplástico TenCate qualificado NIARs NCAMP
- TenCate celebra montagem de consórcio de compósitos termoplásticos no Brasil