Estrutura composta termoplástica substitui metais em pedais de freio de segurança crítica
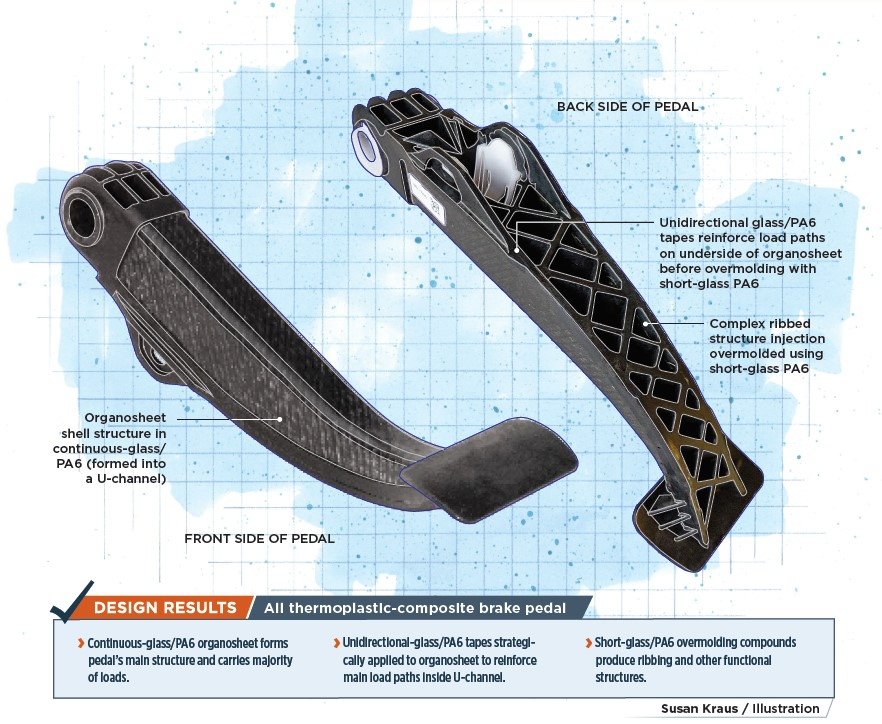
A indústria automotiva converteu os pedais do acelerador de metais em termoplásticos de vidro curto moldados por injeção na década de 1990. No entanto, os pedais de freio - sendo componentes essenciais para a segurança com requisitos desafiadores de rigidez, resistência e carga de torção - demoraram muito mais para serem convertidos. O fornecedor automotivo de nível 1 Boge Rubber &Plastics Group (Damme, Alemanha) diz que é o primeiro fornecedor a atender às exigentes metas de desempenho e custo de OEM para pedais de freio em compostos termoplásticos. O design exclusivo, três materiais diferentes e um processo de produção sob medida permitem que a empresa produza pedais mais fortes, mais rígidos, com menor peso e menor custo.
Encontrando um nicho que conta
Boge é um desenvolvedor e produtor de produtos para amortecimento de vibração e montagem de trem de força / chassi, bem como módulos de plástico leves e caixas de pedal (incluindo combinações de pedais de freio, embreagem e acelerador) para a indústria automotiva. Ela produz componentes automotivos em folha orgânica de fibra contínua com compostos de sobremoldagem de vidro curto desde 2008. Ela adicionou fitas termoplásticas unidirecionais (UD) à mistura em 2018. Por meio da inovação de processo contínua, o tempo de ciclo e os custos foram reduzidos e os negócios aumentaram.
“Em 2015, meu chefe veio até mim e disse:'Essas mudanças que você fez são boas, Daniel, mas seria bom se você pudesse encontrar um mercado maior com volumes de produção que realmente contam'”, lembra o Dr.-Ing . Daniel Häffelin, gerente sênior / chefe da equipe leve do Boge Global Innovation Center. Uma equipe de engenheiros de Boge aceitou o desafio e pensou em como aumentar a eficiência da fibra para reduzir custos e ganhar mais negócios.
“Organosheet é um ótimo produto, mas você deve usá-lo da maneira certa, apenas quando necessário”, explica Häffelin. “Já havíamos tornado nosso processo de produção muito enxuto, então não ganharíamos muito tentando reduzir ainda mais os tempos de ciclo. Raciocinamos que a melhor maneira de reduzir custos era reduzir a quantidade de fibra sem fim que usamos usando essa fibra de forma mais eficiente. ”
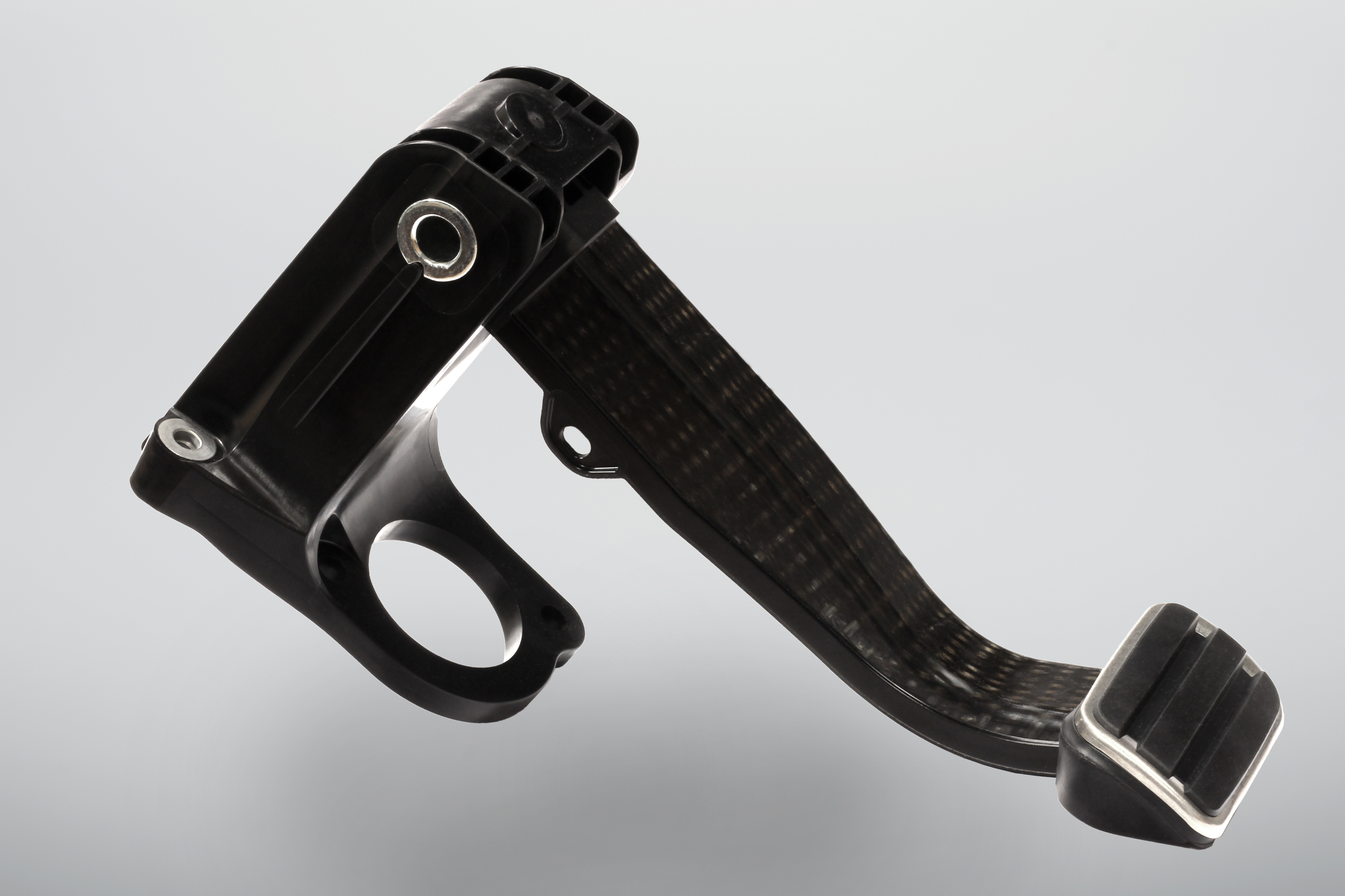
Simplesmente tornar os pedais menores ou mais finos também não funcionaria porque existem restrições práticas no tamanho e forma do pedal de freio, para não mencionar as especificações de desempenho desafiadoras devido à sua natureza crítica para a segurança. O que fez mais sentido foi encontrar maneiras de controlar melhor a orientação da fibra para otimizar as propriedades locais nas áreas da peça que tiveram os picos de carga mais elevados, oferecendo oportunidades para reduzir a espessura da parede em áreas menos críticas.
“Buscamos uma maneira de‘ direcionar ’as fibras localmente para que pudéssemos colocá-las exatamente onde precisávamos para manter a rigidez e a resistência”, acrescenta o Dr. Torsten Bremer, diretor executivo do Boge Rubber &Plastics Group. “Sabíamos, em princípio, que isso era possível porque já havíamos considerado as máquinas pick-and-place usadas em artigos esportivos e médicos, mas eram muito caras. Foi quando decidimos que precisávamos de um novo processo. ”
“Já estávamos trabalhando com um OEM alemão para encontrar maneiras de fazer pedais de freio totalmente compostos que atendessem aos requisitos de desempenho e custo”, lembra Burkhard Tiemann, vice-presidente executivo do Boge Plastics &Rubber Group, líder da linha de produtos - Plásticos. “Dissemos ao nosso cliente:‘ Iremos desenvolver um novo processo usando fitas UD e organosheet ’. Eles nos disseram:‘ Se você puder reduzir a massa e os custos ainda mais, nós o faremos ’. Esse foi nosso ponto de partida. Fizemos uma grande promessa em 2015 de que poderíamos entregar um pedal de freio totalmente composto que fosse mais barato, mais leve e pudesse ser produzido em grandes quantidades. Demorou três anos para resolver os detalhes e entregar nossos primeiros produtos. ”
Direção de fibra
Os pedais de freio compostos devem atender às mesmas especificações de desempenho dos pedais de aço ou alumínio. Isso inclui requisitos de modo de falha especial com cargas de até 3.000 newtons e deflexão semelhante a aço na carga máxima. Dados esses requisitos e o espaço restrito do pacote disponível, a estrutura principal do invólucro do pedal, que suporta as cargas máximas, requer reforço de fibra contínuo. Portanto, a equipe decidiu usar organosheet para formar a espinha dorsal do pedal. As fitas UD seriam então usadas para aumentar localmente a rigidez / resistência e reforçar as paredes internas durante os picos de tensão na área da peça que seria subsequentemente dobrada em um canal em U durante a pré-formação. E em áreas onde a geometria funcional, como nervuras, era necessária, o composto de sobremoldagem de vidro picado foi especificado. A equipe sentiu que essa abordagem híbrida aumentaria a eficiência da fibra enquanto reduzia o uso de material, a espessura média da parede e o tempo de ciclo.

A equipe começou um trabalho intensivo de simulação para otimizar os locais de fibra durante a produção. A base para o trabalho de Boge foi baseada em um programa de pesquisa alemão com financiamento público de 2011-2014 chamado SoWeMa (Software, Ferramentas e Desenvolvimento de Máquina para uma Cadeia de Fabricação Totalmente Automática e Leve).
“A pesquisa do SoWeMa cobriu muitas das perguntas que faríamos um ano depois para nosso próprio empreendimento”, explica Häffelin. “Como o design é parte do know-how central de Boge, começamos com os fundamentos do programa SoWeMa e construímos nossos próprios recursos de simulação FE (elementos finitos) para estruturas anisotrópicas de layup.”
Uma área de foco foi a otimização da topologia combinada para o layup de fita e a estrutura de nervuras. “Criamos um ciclo de iteração para otimizar a colocação das fitas e adaptar a estrutura das costelas de acordo, uma vez que ambas estão interligadas pela rigidez e resistência da peça”, continua K. Siebe, engenheiro da FEA, Centro de Inovação CRRC. “Uma vez que a combinação de materiais de fitas UD, organosheet e materiais de fibra curta é única e sua aplicação é limitada a uma janela específica de umidade e temperatura, construímos nossos próprios cartões de material para caracterizar com mais precisão como esses materiais se comportariam durante o teste físico. ”
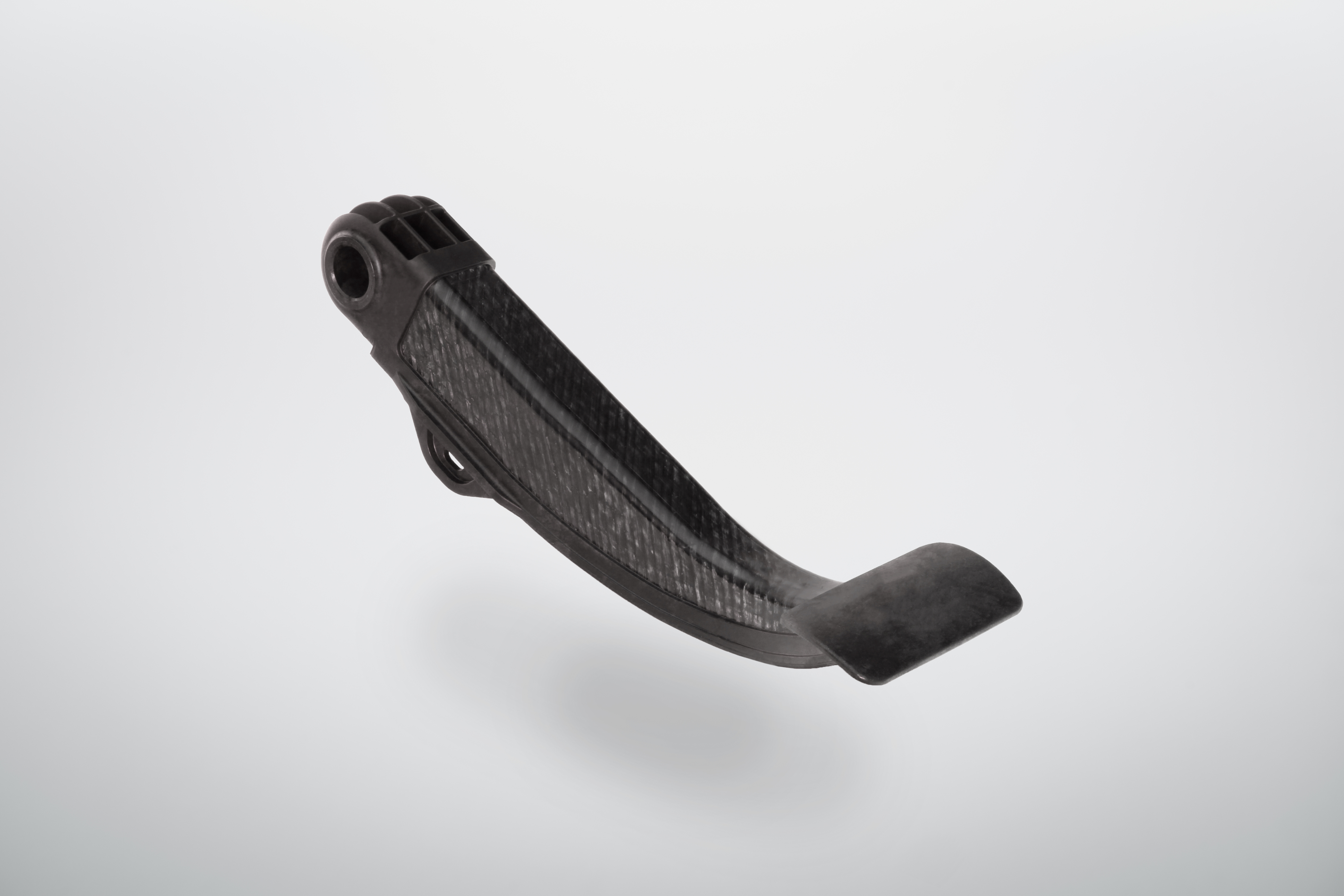
Boge especificou a estrutura da camada e a arquitetura da fibra para cada material com base nos resultados da simulação e um determinado projeto de pedal. Lanxess Deutschland GmbH (Cologne, Germany) fornece organosheet em frações de volume de fibra (FVFs) de 45-50%. As fitas termoplásticas UD com FVFs de 55-60% foram fornecidas pela Celanese Corp. (Irving, Texas, U.S.). Compostos de injeção de vidro curto para esta aplicação, na fração de peso da fibra de 40-60% (FWF), foram fornecidos por várias fontes. Todos os materiais são pretos e apresentam uma matriz de poliamida 6 ou 6/6 (PA6, PA6 / 6). Para atender às especificações do cliente, PA6 é a resina padrão para todos os três tipos de compostos. No entanto, dependendo dos níveis de umidade e temperatura durante a fabricação, bem como das restrições de espaço e geometria do pedal, Boge também pode usar PA6 / 6 para a resina de sobremoldagem, uma vez que os dois polímeros são semelhantes o suficiente para se ligarem bem.
Produção em três etapas
Paralelamente ao design, a equipe trabalhou em um processo de produção de três etapas. Na primeira etapa, um blank de fibra sob medida é criado usando folha orgânica pré-cortada e pré-consolidada como uma base estável na qual prender estrategicamente tiras de fita UD alinhadas aos caminhos de carga para reforçar a estrutura do invólucro da peça. Na segunda etapa, a placa é movida e sequencialmente aquecida, consolidada e moldada / drapeada. Na terceira etapa, ele é sobremoldado com um composto de vidro curto para criar a estrutura nervurada.
Para alcançar tempos de ciclo rápidos, o manuseio robótico foi um dado para este sistema. Um recurso importante do processo que a equipe queria incluir era a flexibilidade de colocar fitas de qualquer comprimento, em qualquer orientação e em qualquer posição em um lado da estrutura da organosheet e pregar a laser essas fitas na estrutura para que não se movessem nas etapas subsequentes.
Outra decisão que a equipe tomou foi não pré-consolidar a peça em branco sob medida imediatamente após o layup, mas logo antes da cobertura / pré-formação e sobremoldagem. A equipe concluiu que o material teria que ser reaquecido durante o drapejamento / pré-formação de qualquer maneira e, para ser econômico, eles deveriam manter o tempo total de ciclo próximo a 1 minuto. Conseqüentemente, Boge aquece e consolida a peça bruta pouco antes de drapejar / pré-formar, usando um rápido aumento de temperatura combinado com alta pressão para criar uma forte ligação mecânica entre a fita e a folha orgânica. O aquecimento para e a temperatura da peça começa a cair conforme a peça bruta consolidada ainda quente se move para a cavidade de drapejamento antes de ser movida novamente e sobremoldada com nervuras e outros recursos funcionais em uma segunda cavidade. Fortes ligações mecânicas, com penetração verificada na cadeia de polímero, são obtidas entre os três materiais. Nenhum acabamento pós-molde é necessário.
Para atender aos requisitos de qualidade dessas peças essenciais para a segurança, a equipe também desenvolveu um sistema rápido, preciso e compatível com a Indústria 4.0 que usa sensores de visão, força, tempo, pressão e temperatura que verificam o material em cada etapa do processo de fabricação. O sistema então armazena esses dados e os vincula ao número de identificação exclusivo de cada pedal. Isso garante 100% de rastreabilidade de todos os materiais, turnos e configurações de processo envolvidos.
Realizações até o momento
O processo sob medida, totalmente automatizado e controlado de qualidade de Boge passou do protótipo à produção em série de alto volume em 2018. Produzindo um novo pedal a cada minuto, a célula de fabricação atual pode fabricar até 1 milhão de peças por ano. Os pedais totalmente compostos usam 33% menos organosheet do que os designs anteriores e a espessura nominal da parede caiu de 3 para 2 milímetros. Os pedais também são 50-55% mais leves, mas atendem ou excedem os requisitos de resistência do aço. Os pedais mais leves melhoram a sensação ao toque para os consumidores e todo o sistema é 100% reciclável no final da vida. Com o processo atual, os pedais compostos estão em paridade de custo com o alumínio e um custo ligeiramente superior ao do aço. Outras aplicações automotivas e esportivas estão em desenvolvimento.
O que o futuro reserva à medida que as montadoras transferem recursos para a eletrificação da frota? “À medida que o drive-by-wire [sistemas de atuação eletromecânica] e a eletrificação do trem de força se tornam mais comuns, os pedais de gás podem desaparecer, mas os pedais de freio permanecerão”, diz Häffelin. “No entanto, provavelmente veremos uma maior integração eletrônica, incluindo sensores, nos pedais de freio. Isso aumentará substancialmente a complexidade da peça, tornando as composições ainda mais competitivo do que metais. ”
Uso de material, etapas de processo e critérios de equipamento são explicados em mais detalhes em CW Artigo de acompanhamento de janeiro de 2021, "O processo personalizado produz pedal de freio composto a cada minuto."
Resina
- Composto de nylon reforçado com fibra longa substitui a carcaça do motor de alumínio
- Composto termoplástico reforçado com fibra contínua feito inteiramente de recursos naturais
- Solvay Expande a Capacidade do Composto Termoplástico
- Oribi Composites, parceiro de desempenho da Packard para rodas motorizadas off-road de composto termoplástico
- Consórcio visa soluções para estruturas compostas termoplásticas de fibra de carbono
- INEOS Styrolution para construir local de produção para compósito termoplástico StyLight
- Xenia apresenta compostos termoplásticos de CF / PP
- Tubo composto termoplástico em ascensão no fundo do mar
- Composto termoplástico TenCate qualificado NIARs NCAMP
- TenCate celebra montagem de consórcio de compósitos termoplásticos no Brasil