Impressão em 3D magnético da próxima geração de compostos personalizados
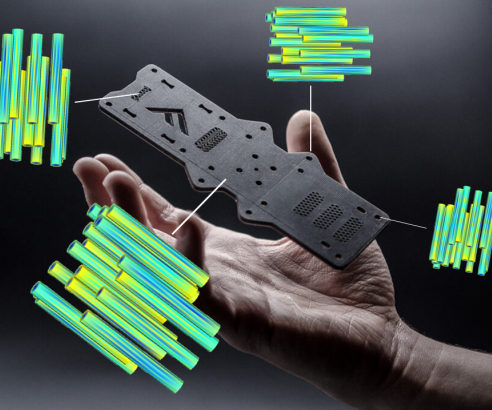
Fortify (Boston, Ma., EUA) foi fundada em 2016, com base na pesquisa de impressão 3D composta por Josh Martin (CEO da Fortify) e Randall Erb, diretor do DAPS Lab da Northeastern University em Boston. (Erb também é cofundador da Boston Materials e da Fortify.) Seu objetivo era permitir a produção rápida de compósitos com microestruturas otimizadas. A tecnologia patenteada Fluxprint que desenvolveram usa campos magnéticos e processamento digital de luz (DLP) - mas com sistemas de resina altamente preenchidos - para produzir microestruturas personalizadas em peças compostas impressas em 3D de alta resolução.
Fluxprint vs. DLP
Tanto o DLP quanto a estereolitografia (SLA) são vistos atualmente como as tecnologias de impressão 3D que oferecem a maior complexidade e precisão de peças. Ambos contam com o uso de luz - normalmente ultravioleta (UV) - para curar uma resina fotossensível que geralmente compreende epóxi ou acrílico e monômeros metacrílicos. A luz é direcionada digitalmente para brilhar na resina no tanque do sistema para criar as formas ou padrões para cada camada. A plataforma de fabricação é movida após cada camada, permitindo que a próxima camada seja impressa e prossiga para uma peça sólida acabada.
Os projetores DLP e SLA datam do início da impressão 3D na década de 1980. As impressoras DLP tendem a ser maiores porque abrigam o projetor de luz real. A maioria das máquinas SLA e DLP usa polímeros termofixos, mas a EnvisionTEC fabrica uma impressora que também pode usar termoplásticos. Ambos usam tradicionalmente polímeros puros sem reforço.
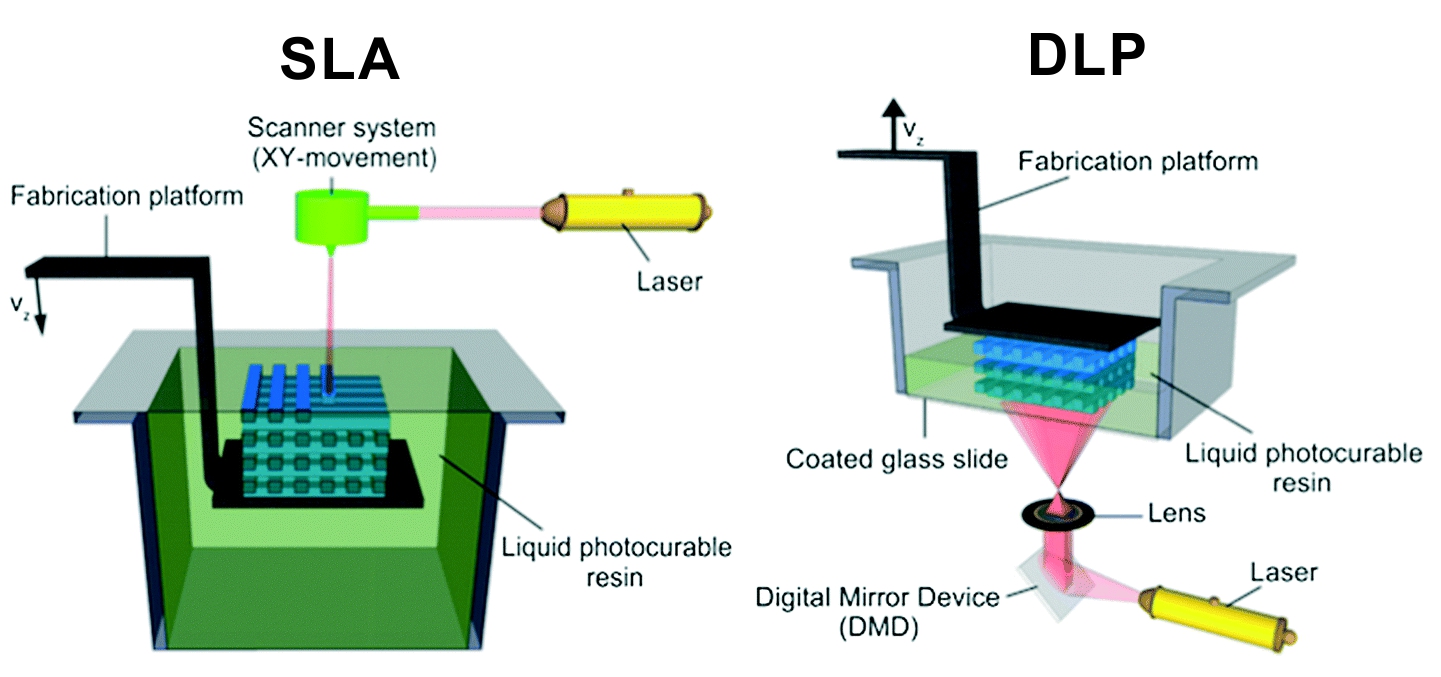
“As plataformas DLP são capazes de taxas de produção e qualidade suficientes”, diz o CEO da Fortify Josh Martin, “mas as propriedades mecânicas sempre foram um desafio. Nossa tese central é que uma mudança radical no desempenho não será realizada apenas pela química do polímero. No entanto, explorar as propriedades exclusivas dos compostos na indústria de aditivos de alta resolução será uma virada de jogo. ”
Ele explica que a Fortify é especializada na cura por UV de resinas técnicas altamente preenchidas usando aditivos exclusivos e controlando a orientação desses aditivos de aprimoramento de propriedades na impressão. Os enchimentos incluem fibras de vidro, carbono e cerâmica, bem como partículas. As resinas técnicas incluem à base de acrilato e metacrilato (PMMA) ou à base de epóxi, de base catiônica - que Martin explica serem mais convencionais para a indústria de tintas. Os principais fabricantes de resinas em todo o mundo (BASF, DSM, Dupont e outros) estão investindo pesadamente para aprimorar as propriedades de seus materiais aditivos. Fortify é capaz de selecionar o melhor desses avanços para adicionar sua tecnologia de reforço.
O controle da orientação da fibra é obtido por meio de um campo magnético. Como o Fortify 3D imprime uma peça usando sua tecnologia Fluxprint, as fibras são alinhadas magneticamente voxel a voxel para atender aos requisitos de carga da peça. (Veja o processo em ação no vídeo acima.) Para materiais de reforço não magnéticos, como partículas de cerâmica e vidro e fibras, técnicas proprietárias de rotulagem magnética são usadas para revestir os enchimentos de uma forma que os torna magneticamente responsivos e compatíveis com a resina.
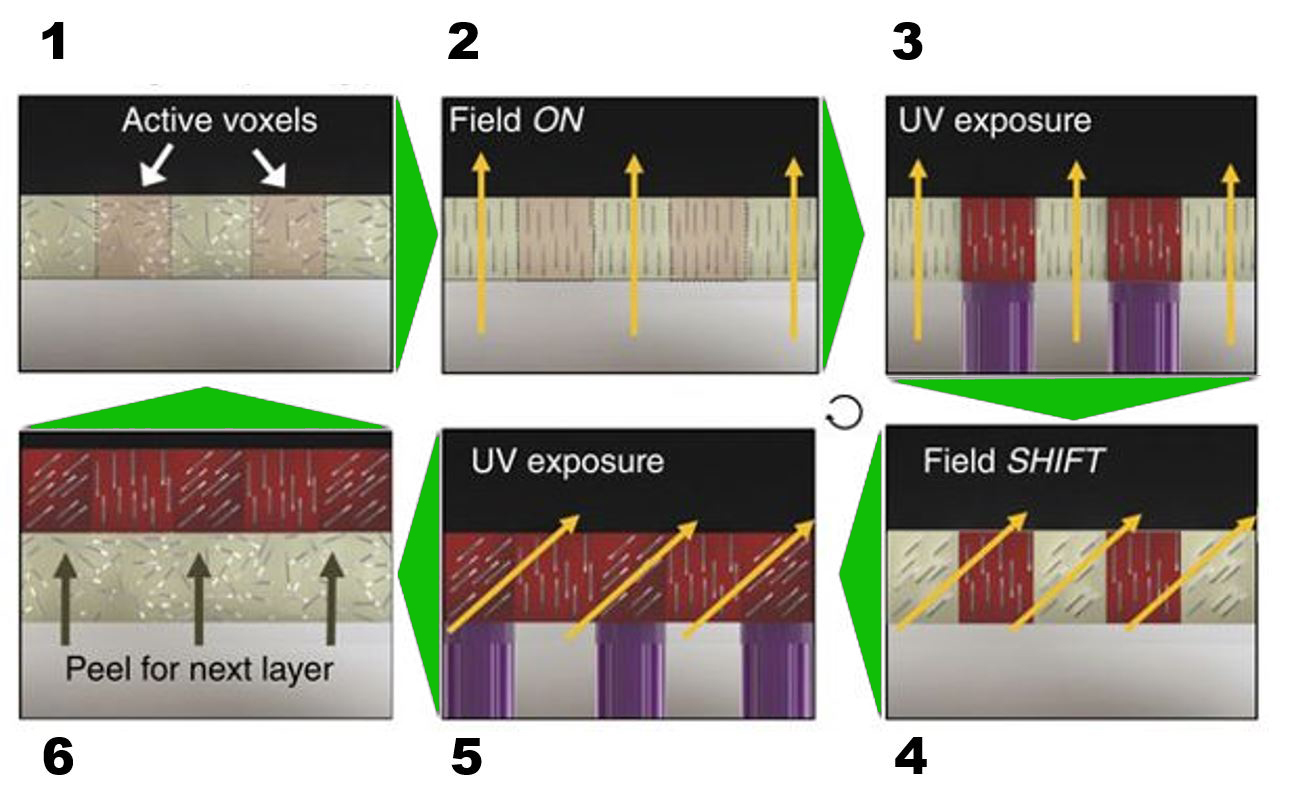
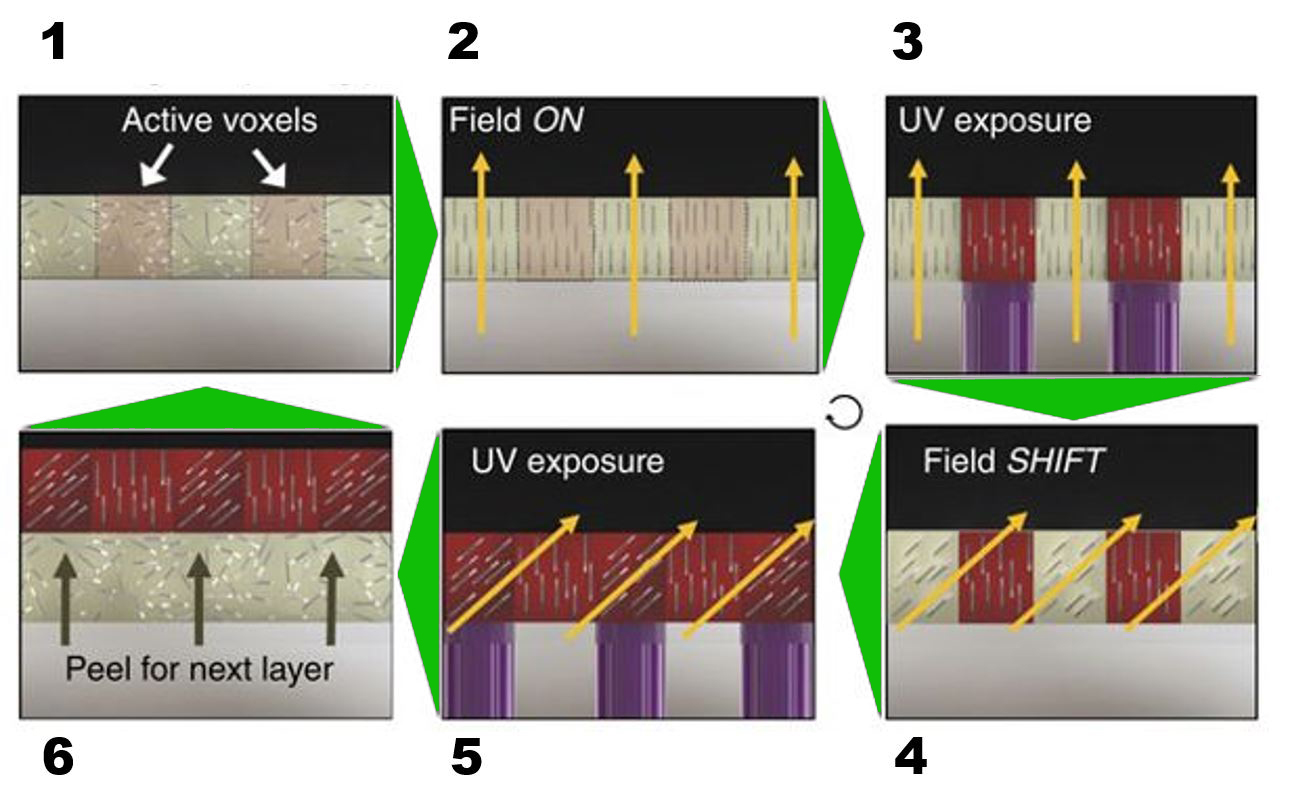
O processo do Fluxprint é mostrado na imagem acima e descrito a seguir:
- Uma camada de material de alimentação é fornecida à área de construção com reforço alinhado aleatoriamente.
- O campo magnético é aplicado para alinhar o reforço.
- Os voxels ativos são expostos à luz ultravioleta, fixando a orientação do reforço nesses voxels (agora mostrados em vermelho).
- O campo magnético é alterado para definir uma nova orientação de reforço.
- Repita a etapa de exposição aos raios ultravioleta para corrigir a orientação para o próximo conjunto de voxels (repita conforme necessário).
- A placa de montagem se ajusta para trazer a matriz do material de alimentação não curado para a próxima camada de impressão.
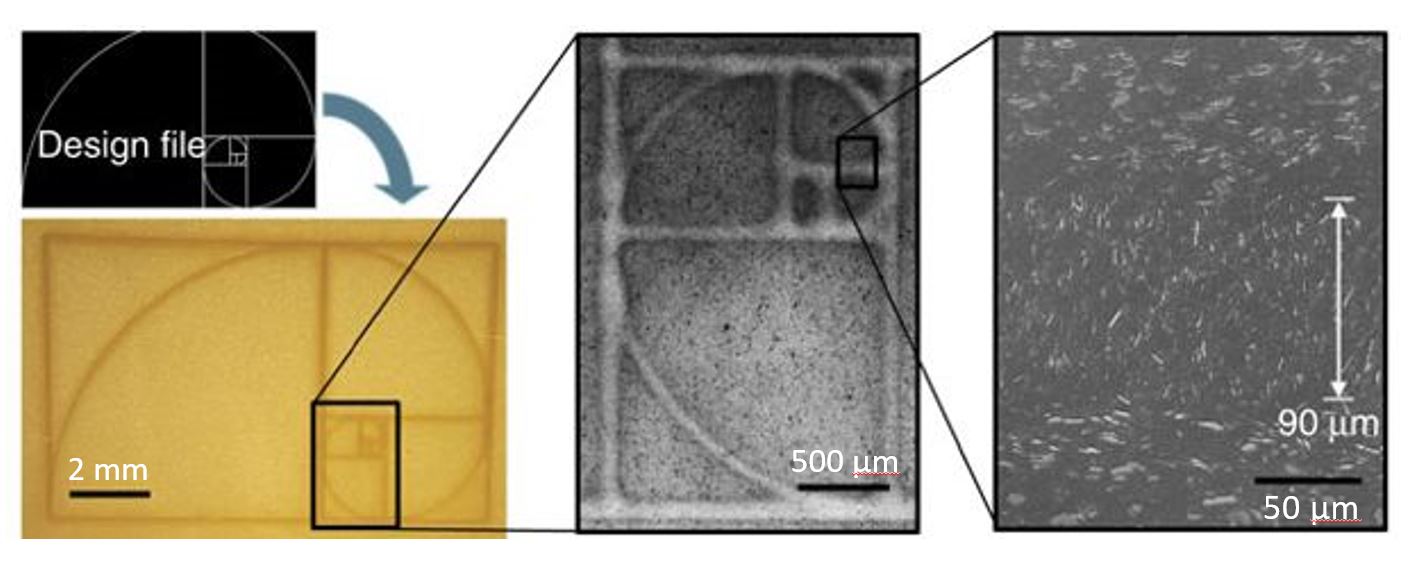
A tecnologia Fluxprint permite o controle do nível de voxel sobre a orientação da fibra durante o processo de impressão. Fonte | “Projetando arquiteturas de reforço composto bioinspirado via impressão magnética 3D” por Joshua J. Martin, Brad E. Fiore e Randall M. Erb, Nature Communications volume6, número do artigo:8641 (2015).
Por que usar voxel por voxel?
“Cada geometria tem deformações e estados de tensão exclusivos”, explica Martin. “A maioria dos compostos são fabricados à mão para dar conta disso. Estamos digitalizando o processo. Por exemplo, se você puder reforçar adequadamente uma estrutura de UAV, poderá usar menos material. Qualquer aplicativo que trabalhe contra a gravidade irá se beneficiar fundamentalmente com isso. ”
A impressão de voxel por voxel também é inerentemente de alta resolução. “Este é o processo de fabricação de compósito de mais alta resolução até hoje”, diz Martin, observando que a modelagem de deposição fundida (FDM) - onde o filamento de plástico reforçado com fibra não reforçado ou fresado é derretido e depositado em uma cama de impressão - tem uma resolução na casa das centenas de micrômetros, enquanto o do Fluxprint está dentro de dezenas de micrômetros. “Então, essa é uma melhoria de ordem de magnitude, que entra no território além do que é percebido a olho nu. Este tipo de resolução é muito importante para uma ampla variedade de peças de uso final. ”
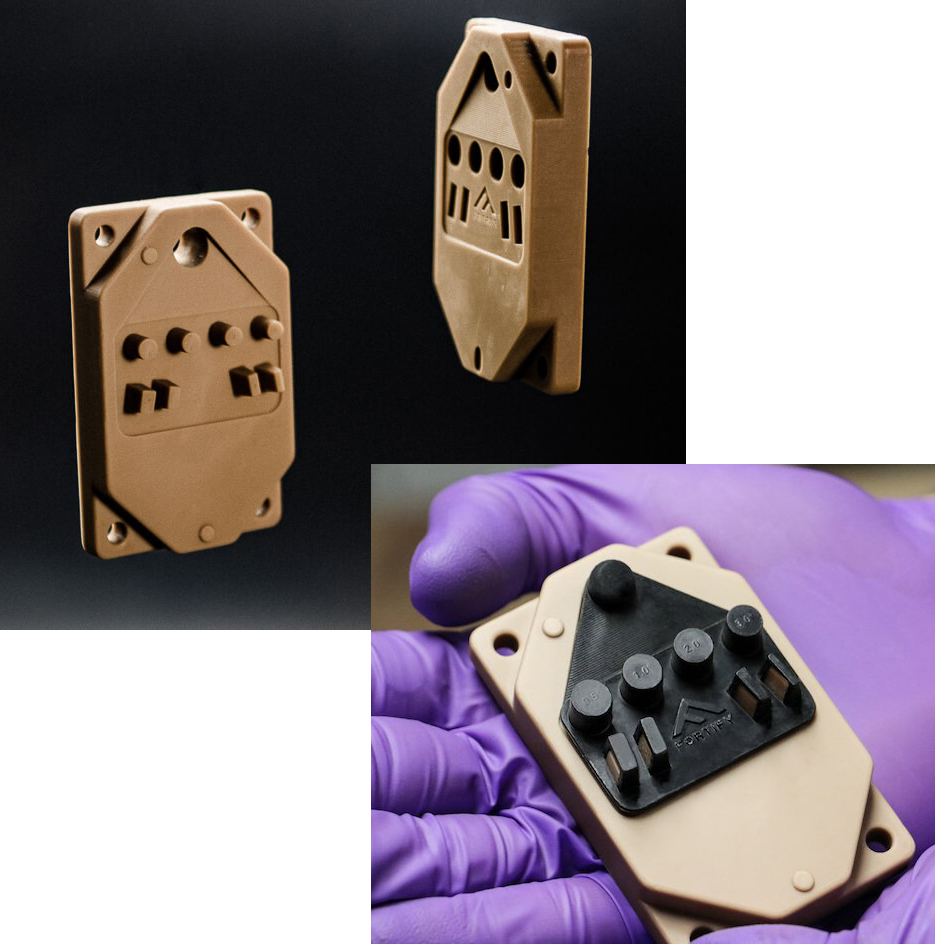
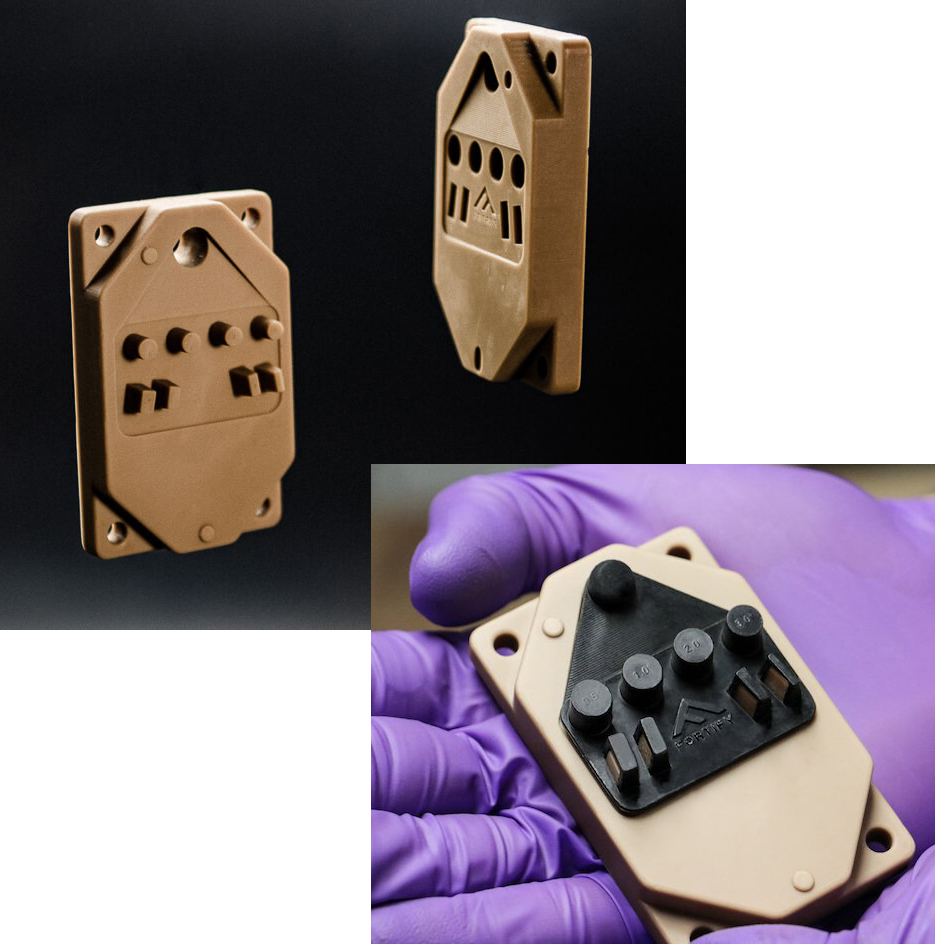
A tecnologia de impressão 3D magnética Fluxprint da Fortify pode orientar as fibras para reforçar as projeções "peg" nas ferramentas de moldagem por injeção. Fonte | Fortalecer.
“Oferecemos ferramentas de moldagem por injeção que são significativamente mais baratas do que o metal usinado tradicionalmente, podem ser entregues em uma fração do tempo e oferecem recursos que as práticas de usinagem convencionais não seriam capazes de alcançar”, continua Martin. “Um cliente iria iterar 12 designs diferentes por ano, usinados em alumínio. Reduzimos o tempo de chegada ao mercado significativamente, produzindo mais de uma dúzia de projetos em vários meses. Eles agora podem passar do design às peças na prateleira em questão de semanas. ” Outro benefício é a capacidade de reforçar as projeções, conhecidas como ‘pinos’. Essas extrusões de alta proporção geralmente se retraem. O reforço evita isso, mantendo tolerâncias apertadas.
Leia mais sobre os benefícios do Fortify em ferramentas de moldagem por injeção na revista irmã da CW, Additive Manufacturing.
Materiais abertos, novos desenvolvimentos
O Fortify busca uma abordagem de materiais abertos. “Não queremos limitar a capacidade de nossos clientes de crescimento e exploração de aditivos”, explica o vice-presidente de aplicações do Fortify, Karlo Delos Reyes. “Garantimos aos nossos clientes flexibilidade e os melhores materiais disponíveis ao abraçar a inovação aberta.”
“Fazemos parceria com grandes fabricantes de polímeros e personalizamos a química de superfície dos aditivos”, diz Martin. Ele observa que cada enchimento tem suas próprias vantagens e desvantagens em relação à resistência ao desgaste, desempenho em temperatura etc. “Para fibras, o comprimento varia de alguns µm a alguns mm, dependendo da aplicação. Onde precisamos de resolução de superfície, usamos uma porcentagem maior de aditivos de menor comprimento. Onde podemos pagar uma superfície mais áspera, mas queremos otimizar a resistência à tração, por exemplo, usamos aditivos de fibra mais longos. ”
Uma das estratégias do Fortify é fazer parceria com líderes da indústria e fornecedores para alavancar a experiência e permitir a polinização cruzada de ideias. A Fortify anunciou recentemente uma parceria com a DSM Additive Manufacturing (Hoek van Holland, Holanda e Elgin, Illinois, EUA) para desenvolver materiais compostos de alto desempenho que serão usados nos sistemas de impressão da Fortify para alcançar desempenho mecânico e de temperatura expandido. “Eles vão expandir nossa paleta de resinas”, diz Martin, “e estamos entusiasmados em trabalhar com eles para desenvolver resinas de ponta”.
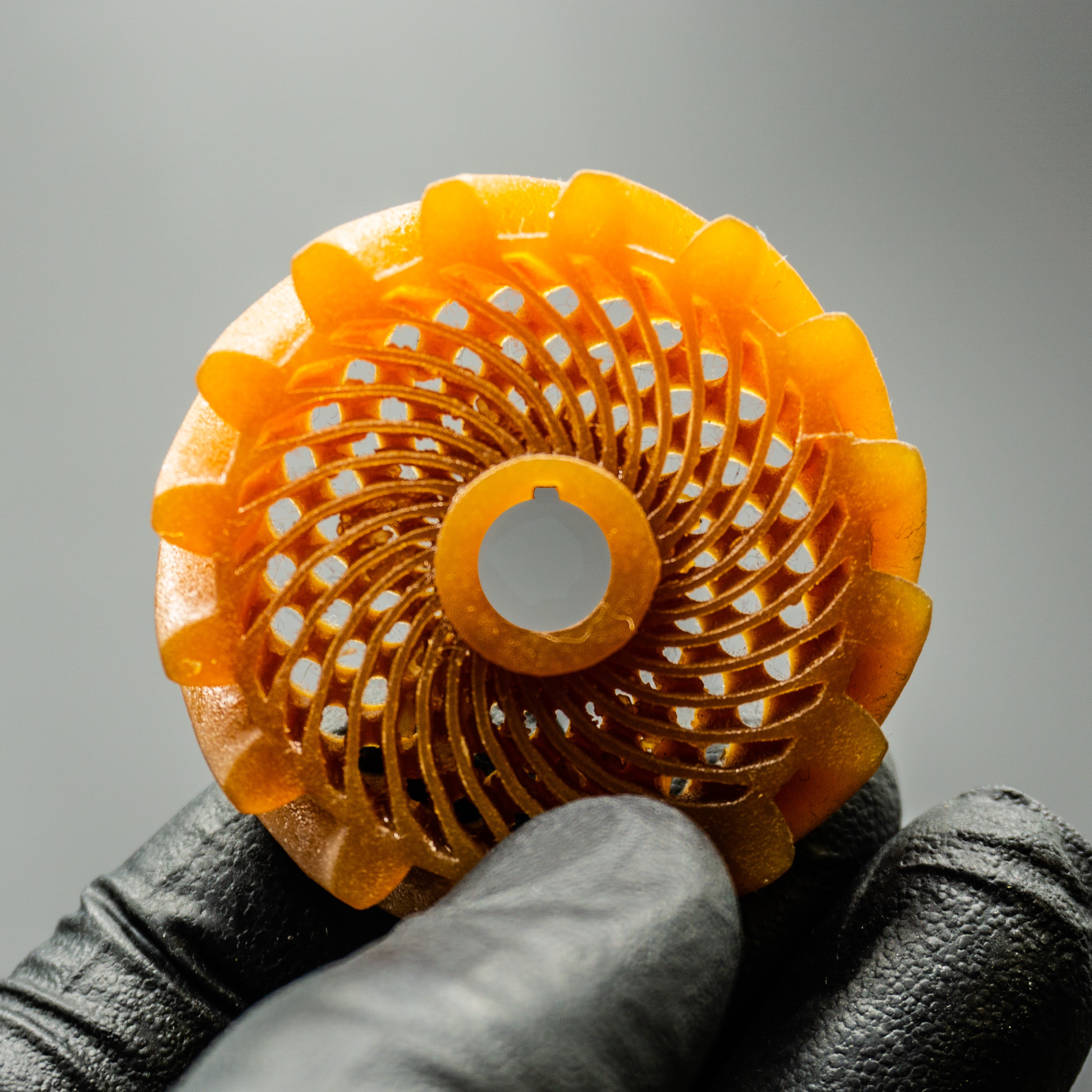
Parte composta reforçada com fibra de vidro feita com Fluxprint. FONTE | Fortalecer.
Reforço e aplicações na direção Z
O Fluxprint ainda está imprimindo por camadas. Então, é possível obter reforço na direção z? “Se você está imprimindo fibras de 2 milímetros de comprimento, não pode colocá-las na direção z”, diz Martin. “Mas você pode ficar mais curto fibras na orientação z. Estamos analisando várias escalas de comprimento e vemos isso no futuro para uma transferência de carga otimizada. ”
A Fortify já está produzindo peças para UAVs, incluindo hélices, e vê muito mais aplicações desse tipo na indústria aeroespacial. “Temos uma pequena área construída, então estamos nos concentrando em aplicações onde podemos facilmente atender a volumes menores de peças”, diz Martin. “Este é um ecossistema maduro, mas oferecemos um novo nível de desempenho em propriedades mecânicas em altas temperaturas e tolerâncias.” Ele cita a capacidade de melhorar a temperatura de deflexão térmica de uma peça e explica que há dezenas de peças sob o capô no setor automotivo que precisam fornecer resistência e rigidez quando expostas a temperaturas de 160 ° C. “Essas peças com geometrias complexas Eles se prestam bem à impressão 3D com nossa tecnologia. Em comparação com o método atual de moldagem e usinagem de peças de PEI (polieterimida), oferecemos maior desempenho, menor prazo de entrega e alto potencial de menor custo . ”
O ferramental também é um mercado atual, incluindo matrizes, gabaritos e acessórios para moldagem por injeção. “Novamente, nossas peças são mais rígidas, mais fortes e têm maior resistência à temperatura, mantendo a precisão dimensional em serviço”, diz Martin. “Mas seu valor real está em não exigindo pós-processamento significativo, como o que é necessário ao usar máquinas EDM, e ainda assim eles correspondem à qualidade dos acessórios feitos com esses métodos tradicionais, incluindo fresamento CNC. ”
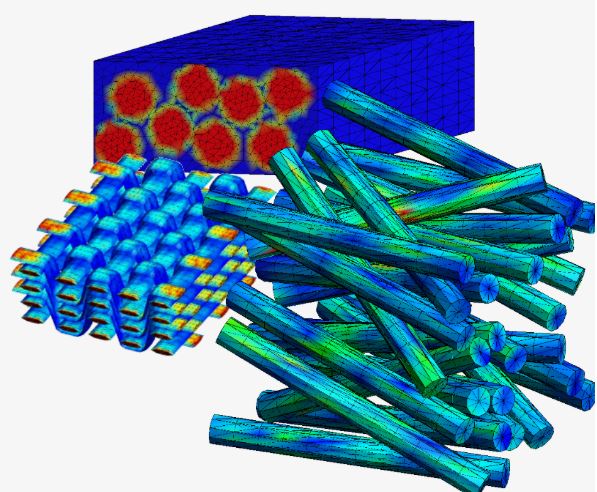
Fonte | MultiMecânica
Avançando para a próxima geração de composições multiescala e multifuncionais
Fortify fez parceria com MultiMechanics (Omaha, Neb., EUA), um desenvolvedor de modelagem multiescala e software de simulação para materiais avançados. Esta parceria é interessante por vários motivos. Primeiro, o Fortify usará o produto carro-chefe da MultiMechanics, MultiMech, para prever o desempenho das peças e otimizar seu design e orientação de fibra antes de serem impressos. Assim, MultiMech atuará para fornecer o feedback para design iterativo de circuito fechado , permitindo que os usuários personalizem e otimizem mais rapidamente as peças compostas com impressão em fluxo contínuo. Fortify e MultiMechanics também planejam integrar MultiMech no INFORM do Fortify design generativo e software de controle de impressão. Assim, desde o design até o teste virtual e a impressão - todas as funções serão controladas em um único fluxo digital.
Para o segundo ponto, é importante entender o que a MultiMechanics está oferecendo por meio de seu software MultiMech:
- Análise multiescala de elementos finitos , incluindo a modelagem de um número praticamente ilimitado de escalas (por exemplo, nano, micro, camada, laminado, peça).
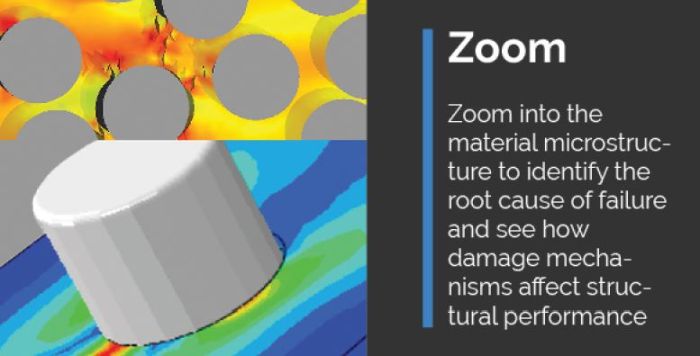
- Geração automática de microestruturas de elemento finito 3D complexas e modelagem de quase qualquer microestrutura de material, incluindo fibra contínua e cortada, partículas, vazios, espumas, tecidos, etc.
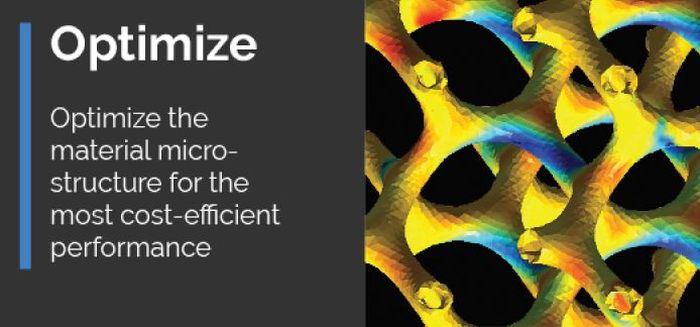
- Efeitos do modelo de constituintes em microescala, incluindo interações , frações de volume, distribuição e orientação, além de importação p variação induzida por roces de programas (por exemplo, Moldex3D, Moldflow).
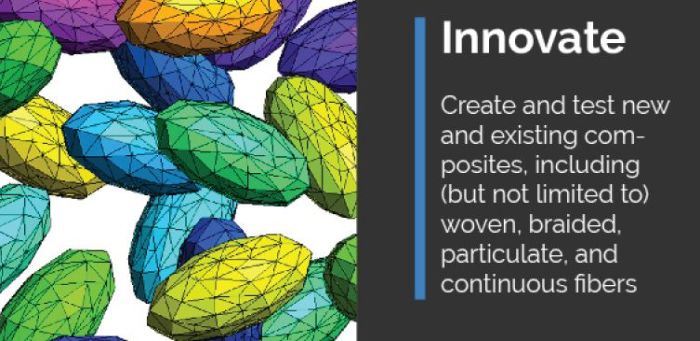
- Analise como a variação de fabricação afeta o desempenho da peça e realizar da modelagem de mago incluindo a transição multiescala de micro-fissuras em macro-fissuras.
Isso remonta ao motivo pelo qual Martin e Erb começaram o Fortify em primeiro lugar. Em seu artigo de 2015, "Projetando arquiteturas de reforço composto bioinspiradas por meio de impressão magnética 3D", eles afirmam:
Martin e Erb discutem compostos naturais que utilizam fibras descontínuas e partículas de reforço organizadas em arquiteturas complexas em várias escalas para alcançar propriedades superiores em relação aos seus constituintes. Um exemplo dado por Qunfeng Cheng em 2017 Materiais Hoje o artigo é nácar em conchas de abalone. Compreendendo 95 vol% de aragonita inorgânica e 5 vol% de matriz de proteína orgânica, a tenacidade à fratura do nácar é 3.000 vezes maior do que a de aragonita. Cheng observa que isso mostra um "efeito de amplificação" nas propriedades mecânicas que vai muito além da regra de misturas em compósitos tradicionais .
Em 2018 Materiais Avançados artigo, “Manufatura aditiva como método para projetar e otimizar estruturas bioinspiradas”, os autores Audrey Velasco-Hogan, Jun Xu e Marc A. Meyers afirmam que a estrutura hierárquica de materiais como conchas de nácar, osso, bambu e crustáceos permitem sua combinação impressionante de força, módulo, leveza, dureza e resistência à fadiga. Suas partículas / filamentos constituintes e matriz são organizados de maneira diferente em cada nível (por exemplo, nano-, micro-, meso-, macro-), variando as propriedades em cada nível (isto é, um composto multiescala). Quando combinado com interfaces eficientes entre os níveis, esta estrutura hierárquica funciona sinergicamente para mitigar a propagação de fissuras e aumentar a tenacidade ao mesmo tempo que mantém a dureza - algo que ainda não foi alcançado na cerâmica depois de quase um século de tentativas.
Futuro dos compostos e INFORMAR
Este é o futuro dos compostos:projetar compostos hierárquicos com propriedades exclusivas adaptado para aplicações precisas. E já está avançando, rapidamente. Por exemplo, o Instituto de Estruturas e Design do Centro Aeroespacial Alemão (DLR) em Stuttgart também fez parceria com a MultiMechanics para entender como a mudança de temperatura afeta a microestrutura e o comportamento do material de compósitos de matriz cerâmica (CMCs) . Esta análise é considerada crucial para a futura produção de componentes CMC da DLR, incluindo bicos para foguetes e sistemas de proteção térmica para veículos de reentrada, entre outros. “Nosso trabalho na MultiMechanics nos últimos dez anos tem se dedicado a conectar o comportamento microestrutural com precisão de materiais avançados para o desempenho geral da peça e sua fabricação ”, Afirma o Dr. Flavio Souza, presidente e CTO da MultiMechanics. “O MultiMech nos permite modelar trincas microestruturais e determinar como elas afetariam a parte geral do compósito”, afirma Neraj Jain, líder do grupo no Departamento de Compósitos e Estruturas Cerâmicas da DLR. “A integração eficiente da MultiMech com nossas outras ferramentas FEA, como Abaqus e ANSYS, aumenta nossa produtividade e nos aproxima de nosso objetivo de otimizar materiais CMC virtualmente . ”
Uma vez que esses compostos tenham sido otimizados virtualmente, eles são então impressos, com MultiMech embutido no software INFORM da Fortify, que já é voltado para arquiteturas orgânicas otimizadas para carga por meio de seu backbone de design generativo . (Observe que a unidade de negócios de Materiais Compósitos da Solvay também investiu em tecnologia de impressão 3D e MultiMecânica.)
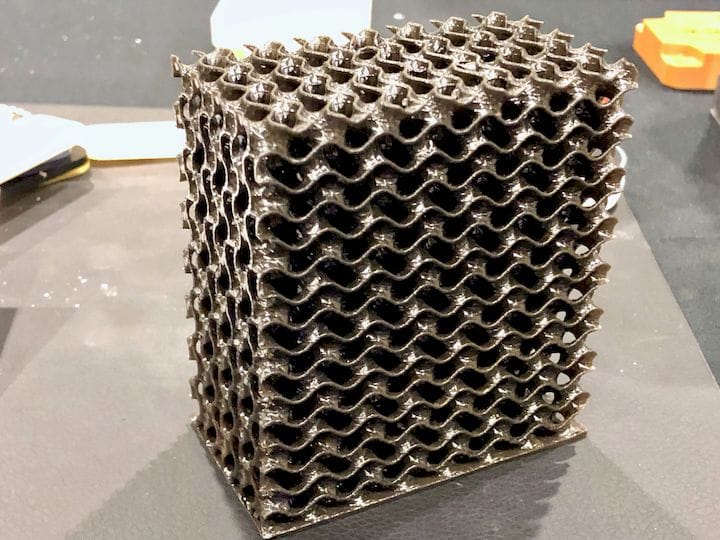
Estrutura reforçada com fibra, design fornecido por nTopology. Fonte | Fortalecer.
“INFORM usa algoritmos avançados para otimizar a orientação da fibra para cada parte ”, explica Martin. “Onde, tradicionalmente, o fluxo de trabalho de impressão 3D começa com STL para cortar o design, o nosso começa com FEA (um modelo com tensão e deformação) e, em seguida, decide em quais voxels separar o design modelado e como orientar as fibras. Progredimos por meio de iterações, alinhando as fibras com vetores de campo de tensão / deformação e, em seguida, simulamos como essa impressão se comportará e usaremos esses dados para refinar e otimizar o design, alcançando o design microestrutural gerador . ”
Apenas o começo
Observe que esses futuros compostos incluem uma variedade de materiais. O Naval Research Laboratory (NRL, Arlington, Va., U.S.) está desenvolvendo CMCs usando uma matriz cerâmica com um reforço cerâmico secundário via nanopartículas e / ou filamentos. Esses CMCs também podem usar reforço de fibra contínua. Em outras palavras, diferentes constituintes e arquiteturas podem ser usados em cada nível para a resistência aprimorada e propriedades elétricas e térmicas personalizadas necessárias (por exemplo, em hipersônica, leia mais em meu artigo de julho de 2019 sobre nanocompósitos).
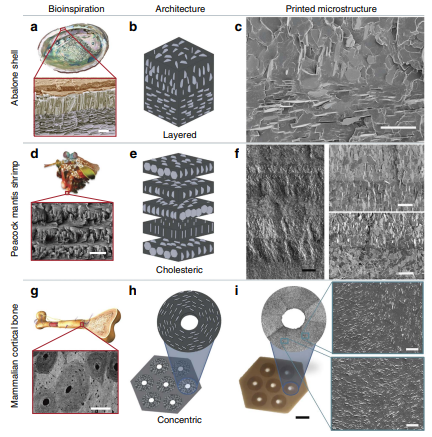
FONTE | Figura 3, "Projetando arquiteturas de reforço composto bioinspiradas via impressão magnética 3D" por Joshua J. Martin, Brad E. Fiore e Randall M. Erb, Nature Communications, volume 6 (2015).
Compósitos hierárquicos também estão sendo impressos e testados usando tintas epóxi reforçadas e matrizes poliméricas termoplásticas. Esta é talvez a maior vantagem do Fortify como uma startup. Não está apenas se preparando para os compósitos do futuro, ela já os está projetando e produzindo. E embora o que já conquistou seja impressionante - é apenas o começo.
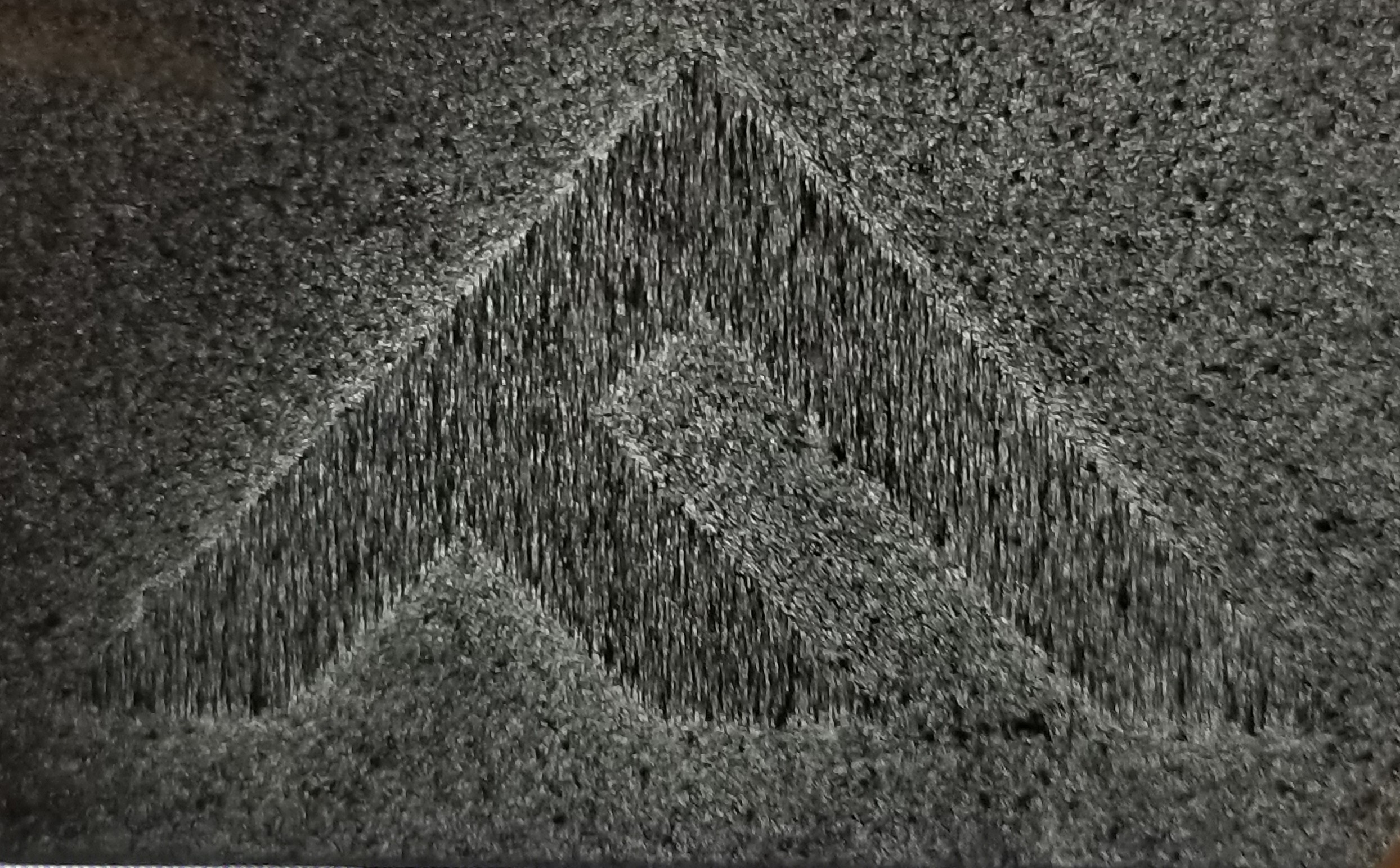
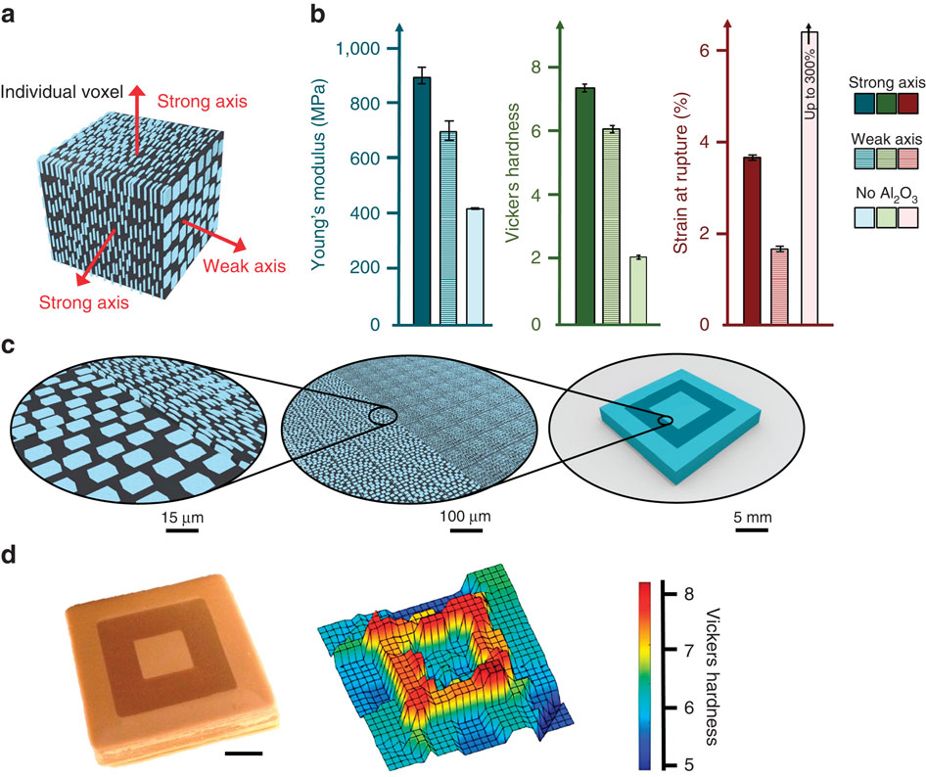
Resina
- As 3 etapas básicas da impressão 3D
- A impressão 3D multimaterial pode ser o próximo passo para AM?
- O ABC da impressão 3D
- A evolução da impressão 3D
- Community Colleges:Treinamento da Próxima Geração de Fabricantes
- Dia da Fabricação 2017:Educando a Próxima Geração de Trabalhadores
- Compósitos para impressão 3D com fibra contínua
- Material para a próxima geração de sensores inteligentes
- Fonte de Terahertz ultrafina abre caminho para a próxima geração de tecnologia de comunicação
- COVID-19:Demanda pela próxima geração de fábrica inteligente